钢铁智能 自动化篇
钢铁制造中的自动化技术有哪些

钢铁制造中的自动化技术有哪些钢铁制造是一个复杂且高度工业化的过程,涉及到从原材料开采、加工到成品生产的多个环节。
在现代钢铁制造业中,自动化技术的应用极大地提高了生产效率、产品质量和安全性。
以下将详细介绍钢铁制造中常见的自动化技术。
首先是自动化控制系统。
这一系统犹如钢铁生产的“大脑”,负责协调和管理整个生产流程。
通过传感器收集各种数据,如温度、压力、流量等,并将这些数据传输到中央控制系统。
控制系统会根据预设的参数和算法,对生产设备进行实时调整和控制,以确保生产过程的稳定和优化。
例如,在高炉炼铁过程中,自动化控制系统可以精确控制炉内的温度、风量和原料的添加量,从而提高铁水的质量和产量。
机器人技术在钢铁制造中也发挥着重要作用。
在一些危险、重复且劳动强度大的工作环节,机器人能够替代人工操作。
比如在炼钢车间,机器人可以进行钢水取样、炉渣清理等工作。
在钢材的搬运和包装环节,机器人能够高效准确地完成任务,减少人力成本和劳动强度,同时降低了因人为失误导致的质量问题和安全事故的发生概率。
智能检测技术也是不可或缺的一部分。
通过使用各种先进的检测设备和传感器,如光学检测、超声波检测、X 射线检测等,可以对钢铁产品的质量进行实时监测和评估。
在生产过程中,能够及时发现产品的缺陷和瑕疵,从而采取相应的措施进行调整和改进,保证产品质量的稳定性和一致性。
例如,在钢板轧制过程中,通过在线检测技术可以实时监测钢板的厚度、平整度等参数,确保产品符合标准要求。
自动化物流系统在钢铁制造中也扮演着重要角色。
通过使用自动化的输送设备、起重机和仓储系统,可以实现原材料、半成品和成品的高效运输和存储。
这不仅提高了物流效率,减少了库存成本,还能够确保生产的连续性和稳定性。
例如,在大型钢铁企业中,采用自动化的铁路运输系统和智能仓储管理系统,可以实现原材料的快速供应和成品的及时发货。
另外,工业互联网技术的应用使得钢铁制造实现了更广泛的互联互通。
通过将生产设备、控制系统和企业管理系统连接到一个网络平台上,可以实现数据的共享和协同工作。
人工智能在冶金自动化中的应用

人工智能在冶金自动化中的应用引言概述:随着科技的不断发展,人工智能(Artificial Intelligence,简称AI)已经成为各个领域的热门话题。
冶金行业作为重要的工业领域之一,也开始广泛应用人工智能技术。
本文将探讨人工智能在冶金自动化中的应用,从优化冶金工艺、提高生产效率、保障安全环境等方面进行详细阐述。
一、优化冶金工艺1.1 智能化炼铁过程控制人工智能技术可以通过分析大量历史数据,建立模型来预测和优化炼铁过程中的各项参数。
通过智能化的控制系统,可以实现对温度、压力、氧含量等关键参数的精确控制,提高炼铁过程的稳定性和效率。
1.2 智能化炼钢过程控制类似于炼铁过程,人工智能技术可以应用于炼钢过程中的自动化控制。
通过对炉温、合金成分、氧含量等关键参数进行实时监测和调整,可以提高炼钢过程的质量和效率,减少能源消耗和排放。
1.3 智能化冶炼设备设计人工智能技术可以应用于冶炼设备的设计和优化。
通过对冶炼过程的模拟和分析,可以提前预测和解决潜在的问题,减少设备的故障和维修时间,提高设备的可靠性和寿命。
二、提高生产效率2.1 智能化生产计划调度人工智能技术可以应用于冶金生产计划的优化和调度。
通过对生产过程中的各项参数进行实时监测和分析,可以实现生产计划的动态调整,提高生产效率和资源利用率。
2.2 智能化物料配送在冶金生产中,物料的配送和搬运是一个重要的环节。
人工智能技术可以应用于物料配送系统的自动化控制,通过智能化的路径规划和调度,可以减少人力成本和运输时间,提高物料配送的效率。
2.3 智能化质量检测人工智能技术可以应用于冶金产品的质量检测。
通过对产品的外观、尺寸、成分等关键参数进行自动化检测和分析,可以提高产品的质量稳定性和一致性,减少人工操作的误差和成本。
三、保障安全环境3.1 智能化安全监测人工智能技术可以应用于冶金生产过程中的安全监测。
通过对温度、压力、气体浓度等关键参数进行实时监测和预警,可以提前发现和防止潜在的安全隐患,保障生产环境的安全性。
钢铁行业智能化生产方案

钢铁行业智能化生产方案随着科技的高速发展,智能化生产在各个行业都得到了广泛应用,钢铁行业也不例外。
本文将探讨钢铁行业智能化生产方案,并分析其对行业发展的影响。
一、智能设备的应用智能设备是智能化生产的核心。
在钢铁生产中,智能设备可以用于炼钢、炼铁、轧钢等各个环节。
比如,智能感应设备可以用于实时监测生产过程中的温度、浓度等参数,提高生产效率和产品质量。
智能机器人可以取代一些重复性劳动,减少人力成本。
智能控制系统可以集成各个设备,实现全自动化生产过程。
二、大数据分析与优化钢铁行业生产数据庞大,对于数据的处理和分析是一项艰巨的任务。
然而,通过大数据分析,可以发现一些潜在的问题和优化空间。
比如,通过分析生产数据,可以找到生产效率低下的环节,进行技术改进和流程优化;还可以基于客户需求和市场趋势,制定更准确的生产计划,避免库存积压和产能闲置。
三、物联网在钢铁行业中的应用物联网技术是智能化生产的重要组成部分。
在钢铁行业中,物联网技术可以实现设备之间的互联互通,实现设备的远程监控和控制。
通过物联网技术,可以实现生产数据的实时传输和分析,及时发现生产过程中的异常情况。
此外,物联网技术还可以实现供应链的智能化管理,提高物流效率和准确性。
四、人工智能技术的应用人工智能技术在钢铁行业中也有广泛的应用。
比如,通过机器学习算法,可以对钢铁生产中的瑕疵进行准确的检测和分类;通过深度学习算法,可以实现对生产过程中的各种异常情况的预测和预警。
人工智能技术的应用可以提高产品质量、降低生产成本,进一步推动钢铁行业的智能化进程。
五、智能化生产带来的益处钢铁行业的智能化生产方案可以带来多方面的益处。
首先,智能化生产可以提高生产效率和产品质量,降低生产成本。
其次,智能化生产可以减少人力投入,改善工作环境,提高工作安全性。
此外,智能化生产还可以提供更详细和准确的数据,有助于企业管理和决策。
六、智能化生产面临的挑战虽然智能化生产在钢铁行业中有着广阔的应用前景,但也面临一些挑战。
钢铁行业的人工智能应用案例智能生产和分析

钢铁行业的人工智能应用案例智能生产和分析近年来,人工智能技术的快速发展不仅在科技领域引起了广泛关注,也在各行各业掀起了一股智能化革命的浪潮。
钢铁行业作为传统的重工业,也在不断探索人工智能技术的应用案例,尤其是在智能生产和分析方面取得了显著的成果。
一、智能生产在钢铁行业中,智能生产主要体现在智能化的设备和机器人系统的应用上。
通过引入人工智能技术,可以实现设备的自动化、智能化管理和协同工作,大大提高生产效率和产品质量。
首先是钢铁行业中高温炉的智能化生产。
传统的高温炉监测和控制依赖于操作员的经验和测量仪器,但这种方法存在着误差和不稳定性。
而引入人工智能技术后,可以通过各种传感器和智能算法实时监测和控制高温炉的温度、压力等参数,同时结合大数据分析和预测模型优化生产过程。
这种智能化的高温炉生产模式不仅提高了钢铁行业的生产效率,还大大降低了能源消耗。
其次是智能机器人在钢铁行业中的应用。
传统的钢铁生产过程中,往往需要操作员长时间地在高温环境下进行重复劳动,不仅容易疲劳,还存在一定的安全隐患。
而引入智能机器人后,可以实现自动化的物料搬运、焊接等工作,减少了人工劳动的参与,提高了生产效率,并且降低了工伤事故的风险。
二、智能分析除了在智能生产方面的应用,人工智能技术在钢铁行业的数据分析方面也发挥了重要作用。
通过智能分析,可以对大量的数据进行挖掘和分析,帮助企业实现智能决策和优化资源配置。
钢铁行业的数据集包含了众多的生产数据、设备状态数据和质检数据等。
而借助人工智能技术,可以对这些数据进行深度学习和模型训练,从而实现对生产过程和设备状态的预测和智能分析。
通过分析数据,钢铁企业可以了解生产过程中存在的问题,及时调整生产计划,提高生产效率和产品质量。
此外,智能分析还可以帮助钢铁企业进行供应链管理和市场预测。
通过对市场数据和需求预测模型的分析,企业可以准确预测市场需求,并合理调整生产计划,避免过量或过少的生产,提高资源利用率和市场竞争力。
钢铁生产过程的智能化控制技术

钢铁生产过程的智能化控制技术随着时代的进步,钢铁行业也在不断发展。
在钢铁生产过程中,智能化控制技术正发挥着越来越重要的作用。
这些技术将传感器、计算机、网络通信和控制器等先进技术集成在一起,使生产过程更加精准、高效、稳定和安全。
钢铁生产过程的智能化控制技术包括自动化控制、物联网技术、智能监控和工业互联网等。
其中,自动化控制是核心技术。
在传统的钢铁生产过程中,许多环节都需要人工干预。
例如,在热轧过程中,操作工需要根据规定的程序控制轧机的开关,这种方式存在人工误差和操作不便捷等问题。
而自动化控制技术的应用,则能够完全解决这些问题。
自动化控制系统利用传感器对生产过程进行实时监测,通过计算机进行数据处理和控制,实现对钢铁生产过程全自动控制,提高生产效率,降低生产成本。
而在物联网技术和智能监控方面,它们的应用则主要体现在设备自我检测和维修管理方面。
物联网技术能够实现对设备的实时监测和数据采集,并将数据传输到云端进行分析和处理。
在智能监控方面,通过分析设备运行状态的异常信息,提前发现故障等问题,并及时进行维修处理,从而大大提高设备的使用寿命和工作效率。
而在工业互联网领域,钢铁生产企业的数字化转型已经取得了明显的成果。
通过构建物联网平台、应用云计算、大数据分析等先进计算技术,将生产过程中的工序串联起来,为企业带来了无限的机遇和优势。
企业可以在生产、管理、设备维修等方面实现信息化、智能化、数字化,提高生产效率和管理水平。
同时,钢铁企业还可借助工业互联网的技术,实现与供应链的深度合作和优化,降低生产成本,提高市场竞争力。
总的来说,钢铁生产过程的智能化控制技术在提高生产效率、降低生产成本、安全性等方面发挥了巨大作用。
未来随着技术的进一步升级和发展,将会在钢铁行业带来更多的创新和科技成果。
钢铁行业的人工智能应用与自动化生产
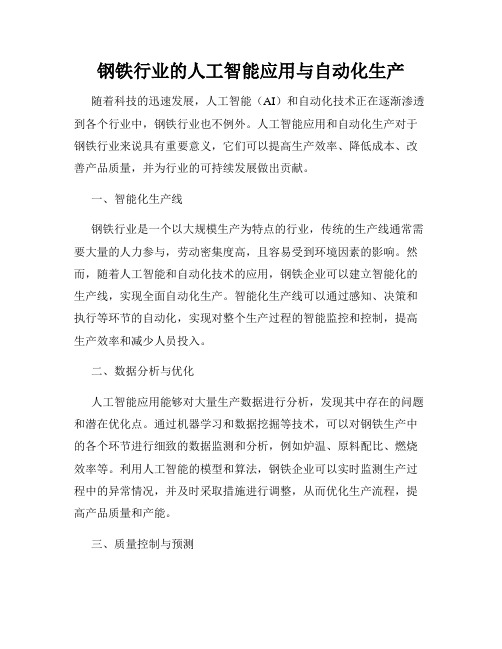
钢铁行业的人工智能应用与自动化生产随着科技的迅速发展,人工智能(AI)和自动化技术正在逐渐渗透到各个行业中,钢铁行业也不例外。
人工智能应用和自动化生产对于钢铁行业来说具有重要意义,它们可以提高生产效率、降低成本、改善产品质量,并为行业的可持续发展做出贡献。
一、智能化生产线钢铁行业是一个以大规模生产为特点的行业,传统的生产线通常需要大量的人力参与,劳动密集度高,且容易受到环境因素的影响。
然而,随着人工智能和自动化技术的应用,钢铁企业可以建立智能化的生产线,实现全面自动化生产。
智能化生产线可以通过感知、决策和执行等环节的自动化,实现对整个生产过程的智能监控和控制,提高生产效率和减少人员投入。
二、数据分析与优化人工智能应用能够对大量生产数据进行分析,发现其中存在的问题和潜在优化点。
通过机器学习和数据挖掘等技术,可以对钢铁生产中的各个环节进行细致的数据监测和分析,例如炉温、原料配比、燃烧效率等。
利用人工智能的模型和算法,钢铁企业可以实时监测生产过程中的异常情况,并及时采取措施进行调整,从而优化生产流程,提高产品质量和产能。
三、质量控制与预测在传统的钢铁生产中,产品质量受到许多因素的影响,如原料含量、加热温度、冷却速度等,人工控制存在一定的局限性。
而借助人工智能技术,钢铁企业可以建立起对产品质量的智能控制系统。
通过对生产数据的实时监测和分析,可以预测产品品质的趋势和变化,及时调整生产参数来保持产品质量的稳定和一致性。
四、智能物流与仓储管理在钢铁行业中,物流和仓储管理是非常重要的环节。
借助人工智能技术,钢铁企业可以实现物流过程的智能化管理,提高物流效率和减少物流成本。
例如,利用智能设备和传感器,可以实时监测货物的运输状况,并根据实时数据进行优化调整。
同时,通过构建智能的仓储系统,可以实现对原材料和成品的智能管理和追溯,提高仓储效率和产品溯源的可追溯性。
五、环境监测与安全管理钢铁生产涉及大量的能源消耗和环境排放问题,因此环境监测和安全管理尤为重要。
钢铁行业智能化钢铁生产控制方案
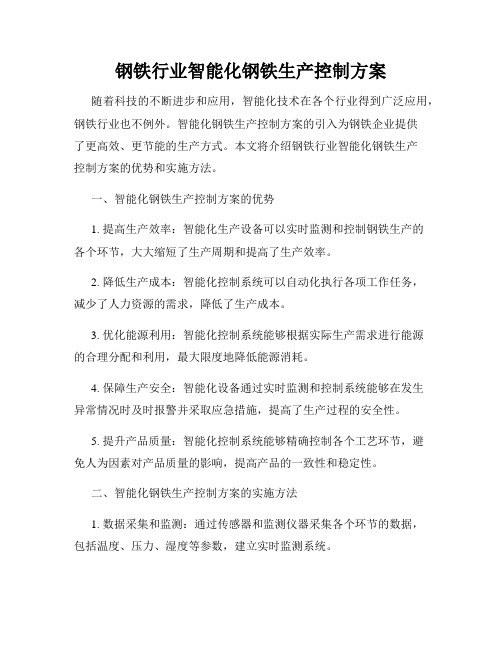
钢铁行业智能化钢铁生产控制方案随着科技的不断进步和应用,智能化技术在各个行业得到广泛应用,钢铁行业也不例外。
智能化钢铁生产控制方案的引入为钢铁企业提供了更高效、更节能的生产方式。
本文将介绍钢铁行业智能化钢铁生产控制方案的优势和实施方法。
一、智能化钢铁生产控制方案的优势1. 提高生产效率:智能化生产设备可以实时监测和控制钢铁生产的各个环节,大大缩短了生产周期和提高了生产效率。
2. 降低生产成本:智能化控制系统可以自动化执行各项工作任务,减少了人力资源的需求,降低了生产成本。
3. 优化能源利用:智能化控制系统能够根据实际生产需求进行能源的合理分配和利用,最大限度地降低能源消耗。
4. 保障生产安全:智能化设备通过实时监测和控制系统能够在发生异常情况时及时报警并采取应急措施,提高了生产过程的安全性。
5. 提升产品质量:智能化控制系统能够精确控制各个工艺环节,避免人为因素对产品质量的影响,提高产品的一致性和稳定性。
二、智能化钢铁生产控制方案的实施方法1. 数据采集和监测:通过传感器和监测仪器采集各个环节的数据,包括温度、压力、湿度等参数,建立实时监测系统。
2. 数据分析和决策:通过分析采集到的数据,运用数据挖掘和人工智能算法,得出生产过程中的优化方案和决策支持。
3. 自动化控制和执行:根据生产过程中的优化方案,通过自动化控制设备和智能化机器人完成各项工作任务,提高生产效率。
4. 人机协同:在智能化钢铁生产过程中,人员需要与系统进行紧密协作,对设备运行状况进行监控和管理,及时处理异常情况。
5. 安全保障:智能化钢铁生产控制方案需要考虑安全性,包括数据的保密性和系统的防护措施,确保生产过程安全可靠。
三、智能化钢铁生产控制方案的应用案例以某钢铁企业为例,该企业引入智能化钢铁生产控制方案后,生产效率提高了30%,生产成本降低了20%,产品质量得到了大幅度提升。
通过数据分析和决策支持系统,该企业能够更好地预测市场需求和制定生产计划,最大程度地减少了生产浪费。
钢铁行业的智能制造案例实现数字化和自动化的转型

钢铁行业的智能制造案例实现数字化和自动化的转型随着科技的进步和制造业的发展,智能制造成为了各个行业转型升级的关键。
尤其是在钢铁行业,数字化和自动化已经成为实现高效生产和持续发展的重要手段。
本文将介绍一些钢铁行业的智能制造案例,展示数字化和自动化技术在转型中的应用。
一、智能化生产线钢铁行业是一个工序繁杂、劳动强度大的行业,传统的生产方式已经无法满足市场需求。
钢铁企业纷纷引入智能化生产线,通过数字化控制和自动化技术实现生产过程的优化和高效。
例如,某钢铁企业引进了大数据分析和物联网技术,通过在生产线上安装传感器和智能设备,实现原材料进程的实时监测和控制,大大提高了生产效率和质量稳定性。
二、智能仓储和物流钢铁产品的仓储和物流过程对于生产和销售的顺利进行非常重要。
一些钢铁企业开始引入智能仓储系统,通过机器人和自动化设备实现货物的分拣、储存和装卸。
此外,利用物联网技术和智能传感器,企业可以实时掌握各环节的运输状态和货物位置,提高了物流效率和可追溯性。
数字化的监控系统也可以提供实时数据分析,帮助企业预测需求和优化仓储布局,从而降低成本和提高效益。
三、智能质检和维护钢铁产品的质量对于企业的声誉和市场竞争力至关重要。
传统的质检方式往往需要大量的人力和时间投入,而且存在一定的主观因素。
智能质检技术的引入可以高效地实现大规模数据的检测和分析,减少人力工作量和提高准确度。
例如,利用机器视觉技术和人工智能,可以对钢铁产品表面缺陷进行精确检测和分析,大大提高了质检效率和产品质量。
另外,智能化的维护系统也成为钢铁企业转型的重要环节。
通过传感器和监控设备,可以实时监测设备的状态和运行情况,实现设备故障的预测和预防维护,有效减少了停机时间和维修成本。
四、数字化管理和优化数字化管理是钢铁企业转型的核心。
传统的人工管理和决策往往存在信息不及时、准确性差等问题。
引入数字化管理系统,可以实现数据的集中存储和分析,提供实时的决策支持和业务优化。
- 1、下载文档前请自行甄别文档内容的完整性,平台不提供额外的编辑、内容补充、找答案等附加服务。
- 2、"仅部分预览"的文档,不可在线预览部分如存在完整性等问题,可反馈申请退款(可完整预览的文档不适用该条件!)。
- 3、如文档侵犯您的权益,请联系客服反馈,我们会尽快为您处理(人工客服工作时间:9:00-18:30)。
大功率电气传动系统的集成与调试电气传动系统特别是大功率调速传动系统是大中型企业物流及工艺处理的重要能量转换单元和核心设备,经过20多年的积累,我公司在以下关键技术上,取得了重大突破:•全数字直流传动的系统集成•各类通用变频器传动的系统集成•氧枪、焦罐、矿井提升等位势负载传动的系统集成•大型风机、压缩机等LCI(软启动)系统调试、运维•采用西门子、ABB主流系统集成轧机主传动中压交直交变频系统典型案例:• 4.3米宽厚板生产线全线辅传动系统(2009年);•炼钢120t、210t转炉倾动和氧枪传动控制;•大型焦炉四大机车传动控制;•70t、100t、150t干熄焦提升系统传动控制;•济钢中厚板厂精轧机主传动;•济钢1750高炉的simovert s 软启动系统;•双机架冷轧轧机、卷取机主传动;•中厚板、热连轧粗轧机、精轧机等。
焦化生产清洁高效集中管控技术基于济钢9座焦炉自动化控制系统建设及改造的成功经验,完全具备制定各类焦炉、化工、干熄焦等焦化行业整套自动化解决方案的能力。
并可延伸至石油、煤化工等非冶金行业的自动化的设计、开发及实施。
核心技术• 《煤的气流调湿与分级技术的自动控制方法》专利号:0.0 • 《一种稳定取得焦炉烟气用于煤调湿分级的方法》专利号:5.X • 大型焦炉全工序集中管控技术 • 干法熄焦智能化控制技术 • 焦炉模型控制技术 • 焦化生产自动排产技术• 焦炉四大机车自动定位、三车联锁控制技术 • 复式焦炉加热模型集成技术 技术创新《干法熄焦技术研究与应用》获国家科学技术二等奖,《炼焦煤气流调湿分级一体化工艺技术》获中国冶金科学技术一等奖等8项科技进步成果奖。
三、典型案例• 济钢焦化厂1-5号焦炉控制系统• 济钢焦化厂6-9号焦炉集中管控系统• 济钢焦化厂2X75t 、2X150t 、 100t 干熄焦智能化控制系统各种能源和副产废气得到了有效的就地治理和循环复用,产线综合能耗降低3%,操作人员减少了2/3。
冶金原料生产自动化技术在冶金原料生产领域,采用集中管控、模型优化等先进控制理念,致力于冶金原料准备、烧结等工艺济钢焦化厂新老系统效果对比5001000单炉年产量/操作工数的全自动化,充分发挥烧结矿的生产能力按生产的需要来控制能源消耗,稳定烧结矿质量,降低生产成本。
核心技术• 球团竖炉控制技术 • 烧结总量模型 • 烧结燃料模型• 烧结水分模型 • 烧结返矿模型 • 烧结点火模型 • 烧结布料模型 • 烧透点控制模型典型案例• 济钢球团厂3号球团竖炉控制系统(2002年) • 济钢球团厂4号球团竖炉控制系统(2005年) • 济钢第一炼铁厂1号--3号120m2烧结机及原料场控制系统(2002年-2007年) • 济钢第一炼铁厂1号、2号70m2烧结机控制系统(2004年)• 济钢第二炼铁厂320m2烧结机及原料场控制系统(2006年)• 济钢400m2烧结机整体控制系统(2009年)加热炉智能控制技术蓄热式加模型投用前后技术经济指标对比89.2192.0472.29959879.81.77813.792.1098.64利用系数(t/m 2h) 筛分指数% R稳定率% TFe稳定率% 转鼓指数%改造前改造后热炉自动控制系统是集钢坯信息管理、加热过程信息监测、加热目标温度控制等功能的过程控制系统,它的应用将使黑匣子式的加热炉生产转变为可观、可控、可预测的现代化生产工艺。
核心技术• 炉膛温度智能控制技术; • 加热炉汽化冷却自动调节; • 液压控制系统连锁控制 • 风机连锁控制、自动调节 • 钢坯全过程信息跟踪及自动输送;• 三维温度场结果分析控制系统结构框架图技术创新《厚板加热炉钢坯三维温度场在线数模系统的开发与应用》获XX 省科学进步一等奖;典型案例济钢中厚板厂3#加热炉智能控制炼铁生产自动化技术在大中型高炉实现了槽下配料过程自动化,上料、布料过程自动化,热风炉燃烧过程自动化,煤粉喷吹自动化,炉前出铁机械化、大型高炉零返矿等,我公司完全具备炼铁自动化系统的自主开发及系统集成能力。
核心技术• 高炉原燃料自动配料、自动上料技术 • 大型高炉高精度返矿自动入炉技术MES 系统L2级系统L1级系统生产过程数据采集监控坯料分布及动态跟踪出入炉记录查询三维结果分析炉温设定L1、MES 、轧机L2接口•热风炉自动燃烧、切换控制•布料器a、β、γ角自动校正模型•炉顶设备全自动连锁布料模型•自动补偿式炉顶布料模型•煤粉自动喷吹控制•变料计算、高炉操作参数、数据趋势查询及电子报表的功能•生产核心数据采集与分析,实现高炉操作在线指导技术创新我公司通过在炼铁领域近20年的潜心研究与经验积累,硕果累累,《炼铁生产计算机控制与管理系统》等四项成果获得XX省冶金科技进步奖。
典型案例•济钢1--6号350m3高炉•济钢1750m3高炉及高炉零返矿•济钢3200m3高炉自动化控制系统(2010)炼钢生产自动化技术将变频传动、PLC控制、大型网络管理、计算机模型技术等集成在转炉、精炼、连铸等复杂工况的工艺,实现了炼钢生产的全自动化,并具备了自动化系统的硬件设计、软件开发、现场调试全过程的集成能力。
核心技术•倾动氧枪控制技术•高效加料控制技术•安全稳定的炼钢余能回收控制技术•顶底复吹控制技术•智能炼钢系统集成•全自动连铸控制技术技术创新•《大型连铸机自控系统的研究开发》获中国冶金科学技术二等奖•《静动态炼钢模型在济钢120t转炉上的研究与应用》获XX省科学技术三等奖;•《济钢120吨转炉高效除尘技术的研究与应用》等三项成果获得XX省冶金科技进步奖典型案例•济钢1-4号40吨转炉•济钢1-5号连铸机控制系统•济钢1-3号120吨转炉、210吨转炉控制系统LF钢包精炼炉自动化控制技术LF钢包精炼炉作为炼钢和连铸的中间环节,在现代钢铁企业中得到广泛应用。
它可以显著提高合金收得率和钢水成份控制精度,方便进行温度调节。
由我公司自主开发的LF精炼炉自动化控制技术可以有效的减少LF精炼炉电极的加热时间,提供优化的合金配料单,大大降低生产电耗以及原料成本。
核心技术PLC基础控制:•钢包吹氩控制;•钢水升温控制;•合金加料控制。
模型控制:•炉次计划管理模型•能量平衡计算•钢包出站时间预估模型•钢包温度预报模型•合金优化配料模型•钢包成分预报模型•钢渣成分预报及渣料配料模型系统特点•提高了系统升温准确性,缩短了精炼加热时间,降低了电耗和电极消耗。
•通过实施合金加料优化计算,提高了钢水的窄成分控制率。
•提高钢水精炼的温度和成分准确率,稳定了铸机拉速,减少了铸坯的裂纹和夹杂。
技术创新《一炼钢2#LF精炼炉数学模型系统的开发与应用》获XX省冶金科技进步成果奖典型案例炼钢厂LF精炼炉(40t)应用。
连铸坯凝固壳厚度测试核心技术采用“射钉法”测定连铸坯在二冷区不同位置的凝固坯壳厚度。
射钉法是将带有示踪材料的钢钉击入正在凝固的坯壳,钢钉的液相线温度低于测试钢种的液相线温度,在液相区的钉子完全熔化,两相区钉子部分熔化,在固相区钉子未熔化。
切取带射钉的铸坯就可以直接测出凝固坯壳厚度,然后在铸坯相应位置取样进行硫印、低倍检验、结果分析、参数计算。
系统功能通过对连铸坯冷却过程中凝固壳厚度的测试,确切了解连铸坯在凝固冷却过程中不同部位的凝固变化规律。
通过测试,可以计算铸机的综合凝固系数,液芯长度或凝固终点位置,校验连铸机引进的凝固预测专家系统的可靠性,评价连铸机综合冷却能力,优化二冷制度,准确控制高拉速条件下的凝固终点位置,为实现高效连铸提供重要依据。
典型案例•济钢第一炼钢厂4#、5#铸机坯壳厚度测试;•济钢第三炼钢厂1#铸机坯壳厚度测试。
未射钉研究和参数调整以前射钉研究和参数调整以后轧钢生产自动化技术采用交交、交直交等先进传动技术和复杂精确的模型控制技术,快速稳定的数据处理系统,实现了从厚板到薄板、从线材到板材各种工艺的轧钢全自动生产。
核心技术•加热炉优化燃烧、炉内轧件跟踪、全自动装炉出炉控制•黑匣子测试技术、数模系统•零速下变频器失控电机电流增大抑制技术•公用直流母线变频控制技术•十二相整流技术、变频器矢量控制•脉冲放大、隔离及干扰抑制技术•变频器网络化控制技术•三轴传动滚切式双边剪自动控制技术•负荷平衡技术、“Δ-Y”组电流均衡技术•级联控制、四辊轧机自动换辊控制技术•剪切、精整全自动控制技术创新《三轴传动滚切式双边剪自动控制系统》获XX省科学技术三等奖。
《中板主传动数字化改造》等三项成果获XX省冶金科技进步奖。
典型案例•济钢中厚板厂矫直机、加热炉、双边剪、冷床控制系统•济钢中板厂主传动数字化改造项目、四辊粗轧机辅传动系统•济钢冷轧厂1700冷轧平整机辅传动控制系统•济钢一小型轧机主传动控制系统•济钢中轧厂加热炉控制系统•酒钢加热炉控制系统•济钢4300新厚板轧机自动化系统基于统一平台的智能化能源管控技术2007年,我公司自主研发的能源管控中心投用后,成为国内第一批能源中心项目,参与了行业规X的制定。
项目涵盖了企业能源全流程管控一体的解决之道,可在确保企业生产用能稳定供应的前提下,实现能源资源配置的最优化。
可与OA、ERP、MES等信息系统无缝连接,为企业高层提供客观富有价值的能源管理信息。
核心技术• 能源输配与平衡控制全过程管控一体化• 《基于柜位预测的钢铁企业煤气动态平衡实时控制方法》,国家发明专利申请号:2.5• 《变电站智能电子设备接入方法》国家发明专利申请号:1.0• 《多区域冶金变电所不停电升级改造系统 》国家发明专利申请号:0.6 • 电力系统的在线预测分析与变电所四遥控制• 超大规模多种类能源介质SCADA 采集平台技术创新《基于统一平台的济钢能源智能管理控制中心的研制》获2007年度中国冶金科学技术二等奖,XX 冶金科技进步一等奖。
典型案例济钢能源管理控制中心项目一、二、三期多机组联合循环发电安全高效集中管控技术通过高精度煤气混合、集中管控、机组冗余控制等技术,有效化解副产煤气资源高效转化带来的工艺创新风险。
实现了多机组联合循环发电安全高效集中管控。
做到工序能耗的考核,能源的考核有理、有力、实时、快捷能源趋势的科学预测和能源计划的结合,实现能源高效利用 集中、管控结合、安全稳定的生产保障60000点能源数据的支撑决策参考能耗统计、成本分析科学预测、优化调度集中监控、安全生产煤气、电力、水、气体的数据采集为公司高层提供真实、实时的能源产生、利用等决策信息核心技术•混合燃气的热值稳定控制系统及计算机控制模型专利号:ZL3.7•混合燃气大扰动压力稳定系统及计算机控制模型专利号:ZL2.2•多机组冗余备用控制•可靠性信号处理设计•多扰动变量的解耦控制•本质安全的计算机控制保证•高精度容错信号处理•智能故障诊断技术创新《冶金煤气多机组联合循环发电安全高效集中管控系统》等三项成果获得冶金科技进步奖典型案例•济钢燃气发电一期项目(2005)。