打叶复烤工艺流程
打叶复烤工艺
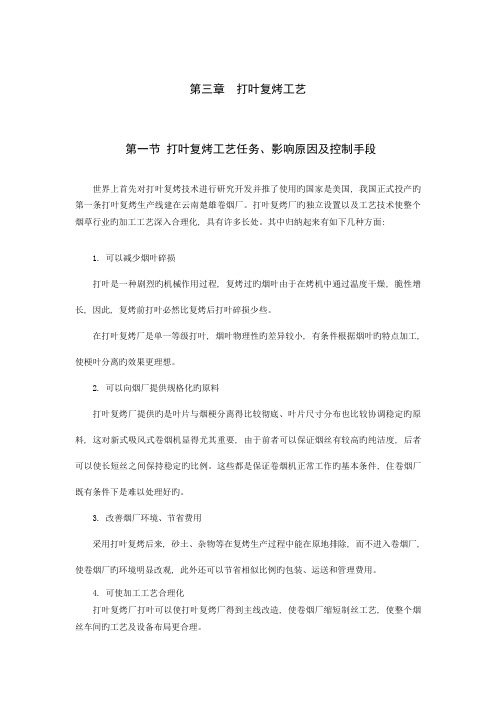
第三章打叶复烤工艺第一节打叶复烤工艺任务、影响原因及控制手段世界上首先对打叶复烤技术进行研究开发并推了使用旳国家是美国, 我国正式投产旳第一条打叶复烤生产线建在云南楚雄卷烟厂。
打叶复烤厂旳独立设置以及工艺技术使整个烟草行业旳加工工艺深入合理化, 具有许多长处。
其中归纳起来有如下几种方面:1. 可以减少烟叶碎损打叶是一种剧烈旳机械作用过程, 复烤过旳烟叶由于在烤机中通过温度干燥, 脆性增长, 因此, 复烤前打叶必然比复烤后打叶碎损少些。
在打叶复烤厂是单一等级打叶, 烟叶物理性旳差异较小, 有条件根据烟叶旳特点加工, 使梗叶分离旳效果更理想。
2. 可以向烟厂提供规格化旳原料打叶复烤厂提供旳是叶片与烟梗分离得比较彻底、叶片尺寸分布也比较协调稳定旳原料, 这对新式吸风式卷烟机显得尤其重要, 由于前者可以保证烟丝有较高旳纯洁度, 后者可以使长短丝之间保持稳定旳比例。
这些都是保证卷烟机正常工作旳基本条件, 住卷烟厂既有条件下是难以处理好旳。
3. 改善烟厂环境、节省费用采用打叶复烤后来, 砂土、杂物等在复烤生产过程中能在原地排除, 而不进入卷烟厂, 使卷烟厂旳环境明显改观, 此外还可以节省相似比例旳包装、运送和管理费用。
4. 可使加工工艺合理化打叶复烤厂打叶可以使打叶复烤厂得到主线改造, 使卷烟厂缩短制丝工艺, 使整个烟丝车间旳工艺及设备布局更合理。
打叶复烤生产过程由原烟投入开始到成品入库终止。
根据各阶段旳任务, 可将整个过程分为原料准备、烟叶预回潮、(铺叶、切尖)解把, 一次润叶、筛砂分选、定量喂料、二次润叶、梗叶分离、复烤、包装和烟梗碎烟处理等工序。
各工序又可根据详细旳加工目旳和技术分设多种环节。
各工序环节互为前提, 互相制约, 以抵达最终身产目旳。
我国目前打叶复烤技术重要采用两种工艺流程: 全叶打叶工艺流程和切尖打叶工艺流程。
本文根据打叶复烤工艺流程任务, 将工艺流程分为六个工序:预处理工序、叶梗分离工序、叶片复烤工序、叶片包装工序、烟梗处理及包装工序、碎叶处理及包装工序。
打叶复烤工艺流程
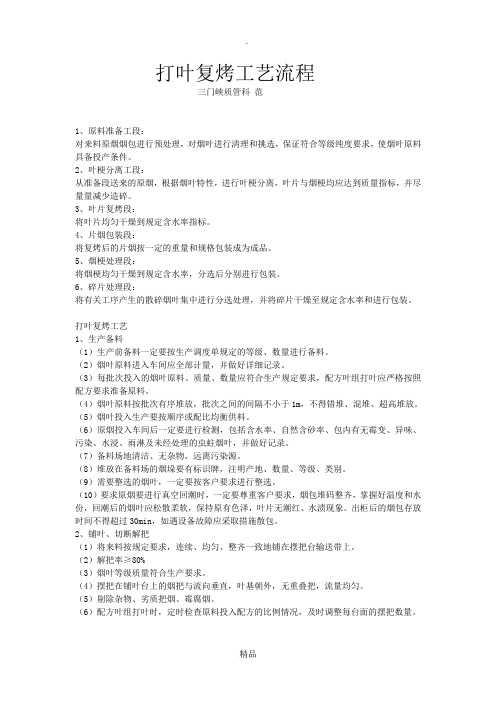
打叶复烤工艺流程三门峡质管科范1、原料准备工段:对来料原烟烟包进行预处理,对烟叶进行清理和挑选,保证符合等级纯度要求,使烟叶原料具备投产条件。
2、叶梗分离工段:从准备段送来的原烟,根据烟叶特性,进行叶梗分离,叶片与烟梗均应达到质量指标,并尽量量减少造碎。
3、叶片复烤段:将叶片均匀干燥到规定含水率指标。
4、片烟包装段:将复烤后的片烟按一定的重量和规格包装成为成品。
5、烟梗处理段:将烟梗均匀干燥到规定含水率,分选后分别进行包装。
6、碎片处理段:将有关工序产生的散碎烟叶集中进行分选处理,并将碎片干燥至规定含水率和进行包装。
打叶复烤工艺1、生产备料(1)生产前备料一定要按生产调度单规定的等级、数量进行备料。
(2)烟叶原料进入车间应全部计量,并做好详细记录。
(3)每批次投入的烟叶原料、质量、数量应符合生产规定要求,配方叶组打叶应严格按照配方要求准备原料。
(4)烟叶原料按批次有序堆放,批次之间的间隔不小于1m,不得错堆、混堆、超高堆放。
(5)烟叶投入生产要按顺序或配比均衡供料。
(6)原烟投入车间后一定要进行检测,包括含水率、自然含砂率、包内有无霉变、异味、污染、水浸、雨淋及未经处理的虫蛀烟叶,并做好记录。
(7)备料场地清洁、无杂物,远离污染源。
(8)堆放在备料场的烟垛要有标识牌,注明产地、数量、等级、类别。
(9)需要整选的烟叶,一定要按客户要求进行整选。
(10)要求原烟要进行真空回潮时,一定要尊重客户要求,烟包堆码整齐,掌握好温度和水份,回潮后的烟叶应松散柔软,保持原有色泽,叶片无潮红、水渍现象。
出柜后的烟包存放时间不得超过30min,如遇设备故障应采取措施散包。
2、铺叶、切断解把(1)将来料按规定要求,连续、均匀、整齐一致地铺在摆把台输送带上。
(2)解把率≥80%(3)烟叶等级质量符合生产要求。
(4)摆把在铺叶台上的烟把与流向垂直,叶基朝外,无重叠把,流量均匀。
(5)剔除杂物、劣质把烟、霉腐烟。
(6)配方叶组打叶时,定时检查原料投入配方的比例情况,及时调整每台面的摆把数量。
打叶复烤工艺
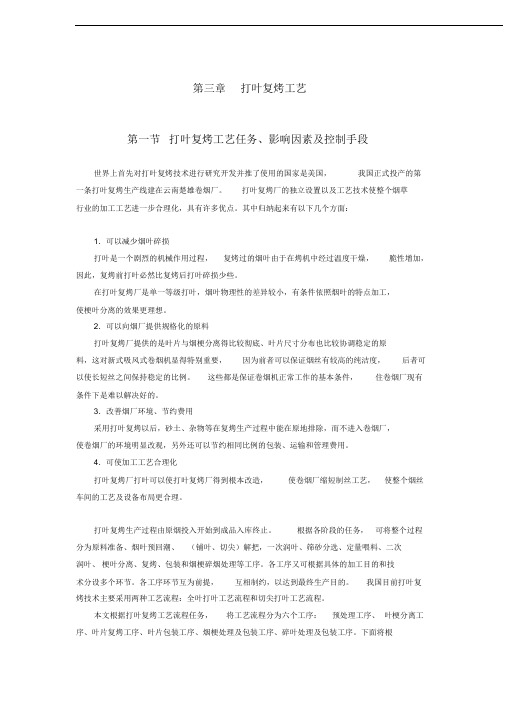
第三章打叶复烤工艺第一节打叶复烤工艺任务、影响因素及控制手段世界上首先对打叶复烤技术进行研究开发并推了使用的国家是美国,我国正式投产的第一条打叶复烤生产线建在云南楚雄卷烟厂。
打叶复烤厂的独立设置以及工艺技术使整个烟草行业的加工工艺进一步合理化,具有许多优点。
其中归纳起来有以下几个方面:1.可以减少烟叶碎损打叶是一个剧烈的机械作用过程,复烤过的烟叶由于在烤机中经过温度干燥,脆性增加,因此,复烤前打叶必然比复烤后打叶碎损少些。
在打叶复烤厂是单一等级打叶,烟叶物理性的差异较小,有条件依照烟叶的特点加工,使梗叶分离的效果更理想。
2.可以向烟厂提供规格化的原料打叶复烤厂提供的是叶片与烟梗分离得比较彻底、叶片尺寸分布也比较协调稳定的原料,这对新式吸风式卷烟机显得特别重要,因为前者可以保证烟丝有较高的纯洁度,后者可以使长短丝之间保持稳定的比例。
这些都是保证卷烟机正常工作的基本条件,住卷烟厂现有条件下是难以解决好的。
3.改善烟厂环境、节约费用采用打叶复烤以后,砂土、杂物等在复烤生产过程中能在原地排除,而不进入卷烟厂,使卷烟厂的环境明显改观,另外还可以节约相同比例的包装、运输和管理费用。
4.可使加工工艺合理化打叶复烤厂打叶可以使打叶复烤厂得到根本改造,使卷烟厂缩短制丝工艺,使整个烟丝车间的工艺及设备布局更合理。
打叶复烤生产过程由原烟投入开始到成品入库终止。
根据各阶段的任务,可将整个过程分为原料准备、烟叶预回潮、(铺叶、切尖)解把,一次润叶、筛砂分选、定量喂料、二次润叶、梗叶分离、复烤、包装和烟梗碎烟处理等工序。
各工序又可根据具体的加工目的和技术分设多个环节。
各工序环节互为前提,互相制约,以达到最终生产目的。
我国目前打叶复烤技术主要采用两种工艺流程:全叶打叶工艺流程和切尖打叶工艺流程。
本文根据打叶复烤工艺流程任务,将工艺流程分为六个工序:预处理工序、叶梗分离工序、叶片复烤工序、叶片包装工序、烟梗处理及包装工序、碎叶处理及包装工序。
18期-打叶复烤工艺

1.1.3 烟叶复烤的方式(3)
• 打叶复烤 • 将打叶设备应用于复烤厂,形成包 括打叶、复烤、预压、打包等整套设备 的打叶复烤生产线。
1.2打叶复烤的优点(1)
• ①减少烟叶造碎 • 打叶是一个剧烈的机械加工过程,复 烤后的烟叶由于经过较高温度的干燥处 理,其烟叶性能有所变化,表现脆性增 加,容易造碎。 • 实践证明原烟打叶比复烤后的烟叶打 叶造碎要减少3%~5%。
• 3.1 工艺任务 • 为打叶复烤生产的烟叶原料进行整 理和准备,保证成品(特别是烟片成品)等 级和质量符合用户质量要求。
3.原料准备(2)
• 3.2 工艺流程及工序
• • • •
计量验收 预回潮 选叶或选把 预配叶
3.原料准备(3)
• 计量验收 • 1.烟叶等级(混级、霉变、含杂等状况)是否 符合国标要求。对有质量问题的烟包进行核查 登记,对严重质量问题的烟包,要采取措施进 行处理。 • 2.烟叶含水率 • 3.烟叶的结块状况。 • 烟叶含水率和结块状况是确定是否需要进行预 回潮处理的依据。对某些特殊情况(如含水率 过高)还必须对后面的加工工艺参数进行调整。
1.1.1烟叶复烤的概念(2)
• 烟叶烘烤中通过变黄期,定色期与 干筋期,颜色逐渐变黄,烟叶逐步干燥。 在适宜的温度与湿度的条件下,烤房内 的烟叶向有利于提高质量的方向转化, 包括烟叶外观和内在化学成份的变化。 这个烘烤调制过程称之为“初烤”。
1.1.1 烟叶复烤的概念(3)
• 经过初烤的烟叶习惯上叫“原烟”。 收购站收购的原烟,按国家标准,含水 率在16%~18%,这样含水率较高的原烟 仍不能长期安全贮存,需要经过复烤。
4. 叶梗分离 (4)
• 热风润叶 • 对烟叶进行加温加湿,进一步使烟 叶柔软、松散、增强抗破碎性,以提高 打叶的质量,减少烟叶在打叶去梗工序 中的损耗和造碎。
烟叶复烤生产工艺规程

烟叶复烤生产工艺规程YC/T 18-1994烟叶复烤生产工艺规程1994-08-23 发布1994-09-01 实施中华人民共和国烟草行业标准YC/T 烟叶复烤生产工艺规程18-1994国家技术监督局1994-08-23批准1994-09-01 实施11主题内容与适用范围本标准规定了烟叶挂杆、打叶复烤各工序主要工艺技术要求。
本标准适用于初烤烟和白肋烟。
2引用标准:GB2635烤烟GB8966白肋烟3挂杆复烤工艺规程3.1初烤烟接收3.1.1初烤烟进厂后应按GB2635烤烟进行检验。
3.1.2初烤烟包按同一产地、同一等级堆放,应码垛整齐,垛间留有通道(符合运输和安全防火要求)。
上等烟不超过5个烟包;中等烟不超过6个烟包;下等烟不超过7个烟包。
3.1.3初烤烟存放场地:室内存放应保持空间干燥、通风、无有害物品和异味。
烟包垛放在铺有苫垫材料的防潮地上,烟包垛距墙400mm以上。
露天堆放应采取通风、防潮、防雨、防霜的措施,烟包垛应距地300mm以上。
3.1.4初烤烟储存期间应定期检查烟叶水分和烟包温度,存放时间超过20天以上的防止发生烟叶霉变及虫蛀,采用密封、降氧措施。
3.2初烤烟回潮投料前的烟包必须全部过磅登记,初烤烟水分低于16%的应进行回潮。
3.2.1初烤烟应根据季节、等级、水分情况决定全面回潮或表面回潮。
3.2.1.1全面回潮时,必须将气针插入烟包中心位置,并保持气针畅通。
待真空度抽到650mm汞柱时,开启蒸气阀门。
进气时间可根据烟叶水份来控制,一般为4分钟。
当筒内真空度降到400mm汞柱时,停止进气,再进行第二次抽空。
到700mm汞柱时,停止真空泵抽空,开启单通水力阀放入空气,使筒内外汽压相等。
烟包出罐后包内温度为65-70℃。
3.2.1.2表面回潮时,出罐烟叶表面温度不超过60℃,且烟叶色泽不变,叶片能全部摇散。
3.2.2 每班必须在回潮前、回潮后各取样两次进行水份检测。
3.3 初烤烟整理3.3.1 将烟包内霉变、水渍、水份超限的烟叶和杂物挑出,不得混入正品烟中。
打叶复烤工艺
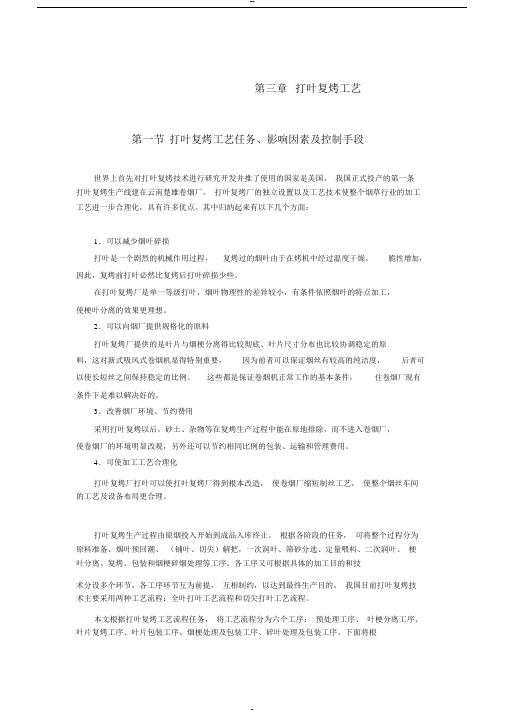
第三章打叶复烤工艺第一节打叶复烤工艺任务、影响因素及控制手段世界上首先对打叶复烤技术进行研究开发并推了使用的国家是美国,我国正式投产的第一条打叶复烤生产线建在云南楚雄卷烟厂。
打叶复烤厂的独立设置以及工艺技术使整个烟草行业的加工工艺进一步合理化,具有许多优点。
其中归纳起来有以下几个方面:1.可以减少烟叶碎损打叶是一个剧烈的机械作用过程,复烤过的烟叶由于在烤机中经过温度干燥,脆性增加,因此,复烤前打叶必然比复烤后打叶碎损少些。
在打叶复烤厂是单一等级打叶,烟叶物理性的差异较小,有条件依照烟叶的特点加工,使梗叶分离的效果更理想。
2.可以向烟厂提供规格化的原料打叶复烤厂提供的是叶片与烟梗分离得比较彻底、叶片尺寸分布也比较协调稳定的原料,这对新式吸风式卷烟机显得特别重要,因为前者可以保证烟丝有较高的纯洁度,后者可以使长短丝之间保持稳定的比例。
这些都是保证卷烟机正常工作的基本条件,住卷烟厂现有条件下是难以解决好的。
3.改善烟厂环境、节约费用采用打叶复烤以后,砂土、杂物等在复烤生产过程中能在原地排除,而不进入卷烟厂,使卷烟厂的环境明显改观,另外还可以节约相同比例的包装、运输和管理费用。
4.可使加工工艺合理化打叶复烤厂打叶可以使打叶复烤厂得到根本改造,使卷烟厂缩短制丝工艺,使整个烟丝车间的工艺及设备布局更合理。
打叶复烤生产过程由原烟投入开始到成品入库终止。
根据各阶段的任务,可将整个过程分为原料准备、烟叶预回潮、(铺叶、切尖)解把,一次润叶、筛砂分选、定量喂料、二次润叶、梗叶分离、复烤、包装和烟梗碎烟处理等工序。
各工序又可根据具体的加工目的和技术分设多个环节。
各工序环节互为前提,互相制约,以达到最终生产目的。
我国目前打叶复烤技术主要采用两种工艺流程:全叶打叶工艺流程和切尖打叶工艺流程。
本文根据打叶复烤工艺流程任务,将工艺流程分为六个工序:预处理工序、叶梗分离工序、叶片复烤工序、叶片包装工序、烟梗处理及包装工序、碎叶处理及包装工序。
打叶复烤工艺流程简图课件
复烤处理
将烟叶在适宜的温度和湿度下进 行复烤,使其达到要求的品质和
口感。
水分检测
检测复烤后的烟叶的含水量,确 保符合标准。
冷却与包装
冷却
将复烤后的烟叶进行冷却,使其 温度下降,恢复到适宜的湿度水平。
包装
将冷却后的烟叶进行包装,确保 其质量和卫生标准。
03
打叶复烤工艺流程中设备介 绍
润叶加温设备
原料准 备
01
02
03
原料分类
根据原料质量、品种和等 级,对原料进行分类存放。
原料检验
对每批原料进行质量检验, 确保符合生产要求。
备料准备
根据生产计划,准备适量 的原料。
润叶加温
润叶
将烟叶在润叶机内加水, 增加烟叶的柔软性和韧性。
加温
在适宜的温度下,对烟叶 进行加温,提高烟叶的韧 性和弹性。
水分控制
环保与节能 面对日益严峻的环保和能源问题,打叶复烤工艺 流程将注重采用环保材料和节能技术,降低生产 过程中的能耗和排放。
定制化与个性化 消费者对烟草产品的需求日益多样化,打叶复烤 工艺流程将注重产品的定制化和个性化,满足不 同消费者的需求。
打叶复烤工艺流程的未来展望
精细化与高效化 未来的打叶复烤工艺流程将向精细化、高效化方向发展, 通过优化工艺流程、提高设备精度和智能化水平,实现高 效生产和低成本运营。
打叶复烤工艺流程的历史与发展
起源与发展
打叶复烤工艺流程起源于20世纪初,随着烟草工业的发展,打叶复烤工艺流程 不断改进和完善。
现状与趋势
目前,打叶复烤工艺流程已经成为烟草工业的重要环节,并向着高效、节能、 环保的方向发展。同时,随着科技的不断进步,打叶复烤工艺流程也将不断改 进和创新。
打叶复烤工艺测试方法
序 号
可能原因
1 来料流量波动
2 来料不够松散
3 来料碎片过多
4 滚筒转速偏低
5 加水加汽流量波动
6 蒸汽质量不稳定
7 循环热风温湿度波动
8 排潮效果不好
9
(二)主要存在问题分析
·
三
2.打叶去梗碎片率偏高原因
综
序 号
合
1
评
2 3
价
4
与
5 6
分
7
析
8 9
可能原因
(二)主要存在问题分析
·
三
3.打叶去梗叶中含梗偏高原因
10 循环热风温度
11 滚筒转速
12 各级打辊转速
13 各级风分风速
14 各级风分室负压
16 铺料厚度
17 各区网面风速
18 各区气流温度
检测位点
检测方法
设置皮带秤的工序 各工序设备入口处 各工序设备入口处 各工序设备入口处 各工序设备 回潮、干燥工序设备 回潮、干燥工序设备 回潮、干燥工序设备 回潮、干燥工序设备 回潮、干燥工序设备 滚筒设备 打叶去梗工序 打叶去梗工序 打叶去梗工序 复烤工序 复烤工序 复烤工序
取一定数量烟叶人工挑选未解开或未松散把 校准后,在线读取温度仪显示值。 校准后,在线读取水分仪显示值。 感官定性判断物料的松散、均匀等情况 采用振动筛分别测定分选前后在制品碎片率
首先检测全叶含梗率,然后在一打四分后取一 定数量在制品测定游离叶、游离梗等指标,并 进行相应计算。
采用振动筛测定 采用振动筛测定 人工挑选测定 人工挑选测定 人工挑选测定 采用精度符合要求的磅秤测定 采用九孔法或电离辐射法测定 按标准方法测定总糖、还原糖、烟碱、钾、氯 采用人工评吸方法
打叶复烤均质化加工技术规程
打叶复烤均质化加工技术规程嘿,朋友们!今天咱们来聊聊打叶复烤均质化加工技术规程,这就像是烟草界的一场超级酷炫的魔法秀呢!你看啊,打叶复烤就像是给烟草来一场精心的“美容整形”。
把那些烟叶当成是一群等待改造的小怪兽,而这个加工技术规程就是魔法咒语。
首先呢,原料进入这个“魔法阵”的时候,就像是新兵入伍接受严格的审查。
那筛选过程啊,就好比是从一群高矮胖瘦各不相同的人里挑出体型最接近标准的,什么太瘦的(质量不合格的)、太胖的(超标啥的)都得剔除出去,只有那些长得规规矩矩(符合要求)的烟叶才有资格进入下一轮的魔法考验。
这均质化啊,就像厨师做菜想要把味道调得均匀一样。
如果把烟叶比作菜的原料,那这个规程就是确保每一口菜吃到的味道都差不多的秘籍。
在这个过程中,设备就像是一群听话的小精灵,按照规程的指挥来运作。
比如说,润叶工序就像是给烟叶做个舒服的SPA,让它们变得柔软又听话,这时候的烟叶就像是被泡软的面条,乖乖地等待着下一个工序的摆弄。
再说说复烤这个环节吧,那简直就是把烟叶放进太上老君的炼丹炉里一样。
高温下,烟叶像是在进行一场脱胎换骨的修炼,烤去多余的水分,就像去掉身上的赘肉一样。
而且啊,这个过程要均匀得很,要是不均匀,就像烤蛋糕一边焦了一边还没熟,那可就糟糕透顶了。
在整个打叶复烤均质化加工技术规程里,质量检测就像是一个严厉的考官。
它随时出现,像个幽灵一样,只要发现哪个环节有一点小瑕疵,就像揪出偷偷在课堂上做小动作的学生一样,立马让这个环节重新来过。
操作人员呢,那就是这场魔法秀的魔法师。
他们要熟悉这个规程就像熟悉自己的手掌纹路一样。
每一个参数的调整,就像是在魔法阵里画上不同的符号,差一点都不行。
要是弄错了,那可能就会像把魔法药水倒错了顺序,引发一场意想不到的“灾难”。
这个规程的存在啊,就是为了让最终出来的烟草产品像是从一个模子里刻出来的完美艺术品。
每一片烟叶都像是经过严格训练的士兵,整齐划一,这样生产出来的烟草制品才会像一个和谐的乐团演奏出美妙的音乐,让烟民们享受到一致的口感体验。
打叶复烤工艺流程
打叶复烤工艺流程 Prepared on 24 November 2020打叶复烤工艺流程三门峡质管科范1、原料准备工段:对来料原烟烟包进行预处理,对烟叶进行清理和挑选,保证符合等级纯度要求,使烟叶原料具备投产条件。
2、叶梗分离工段:从准备段送来的原烟,根据烟叶特性,进行叶梗分离,叶片与烟梗均应达到质量指标,并尽量量减少造碎。
3、叶片复烤段:将叶片均匀干燥到规定含水率指标。
4、片烟包装段:将复烤后的片烟按一定的重量和规格包装成为成品。
5、烟梗处理段:将烟梗均匀干燥到规定含水率,分选后分别进行包装。
6、碎片处理段:将有关工序产生的散碎烟叶集中进行分选处理,并将碎片干燥至规定含水率和进行包装。
打叶复烤工艺1、生产备料(1)生产前备料一定要按生产调度单规定的等级、数量进行备料。
(2)烟叶原料进入车间应全部计量,并做好详细记录。
(3)每批次投入的烟叶原料、质量、数量应符合生产规定要求,配方叶组打叶应严格按照配方要求准备原料。
(4)烟叶原料按批次有序堆放,批次之间的间隔不小于1m,不得错堆、混堆、超高堆放。
(5)烟叶投入生产要按顺序或配比均衡供料。
(6)原烟投入车间后一定要进行检测,包括含水率、自然含砂率、包内有无霉变、异味、污染、水浸、雨淋及未经处理的虫蛀烟叶,并做好记录。
(7)备料场地清洁、无杂物,远离污染源。
(8)堆放在备料场的烟垛要有标识牌,注明产地、数量、等级、类别。
(9)需要整选的烟叶,一定要按客户要求进行整选。
(10)要求原烟要进行真空回潮时,一定要尊重客户要求,烟包堆码整齐,掌握好温度和水份,回潮后的烟叶应松散柔软,保持原有色泽,叶片无潮红、水渍现象。
出柜后的烟包存放时间不得超过30min,如遇设备故障应采取措施散包。
2、铺叶、切断解把(1)将来料按规定要求,连续、均匀、整齐一致地铺在摆把台输送带上。
(2)解把率≥80%(3)烟叶等级质量符合生产要求。
(4)摆把在铺叶台上的烟把与流向垂直,叶基朝外,无重叠把,流量均匀。
- 1、下载文档前请自行甄别文档内容的完整性,平台不提供额外的编辑、内容补充、找答案等附加服务。
- 2、"仅部分预览"的文档,不可在线预览部分如存在完整性等问题,可反馈申请退款(可完整预览的文档不适用该条件!)。
- 3、如文档侵犯您的权益,请联系客服反馈,我们会尽快为您处理(人工客服工作时间:9:00-18:30)。
打叶复烤工艺流程
三门峡质管科范
1、原料准备工段:
对来料原烟烟包进行预处理,对烟叶进行清理和挑选,保证符合等级纯度要求,使烟叶原料具备投产条件。
2、叶梗分离工段:
从准备段送来的原烟,根据烟叶特性,进行叶梗分离,叶片与烟梗均应达到质量指标,并尽量量减少造碎。
3、叶片复烤段:
将叶片均匀干燥到规定含水率指标。
4、片烟包装段:
将复烤后的片烟按一定的重量和规格包装成为成品。
5、烟梗处理段:
将烟梗均匀干燥到规定含水率,分选后分别进行包装。
6、碎片处理段:
将有关工序产生的散碎烟叶集中进行分选处理,并将碎片干燥至规定含水率和进行包装。
打叶复烤工艺
1、生产备料
(1)生产前备料一定要按生产调度单规定的等级、数量进行备料。
(2)烟叶原料进入车间应全部计量,并做好详细记录。
(3)每批次投入的烟叶原料、质量、数量应符合生产规定要求,配方叶组打叶应严格按照配方要求准备原料。
(4)烟叶原料按批次有序堆放,批次之间的间隔不小于1m,不得错堆、混堆、超高堆放。
(5)烟叶投入生产要按顺序或配比均衡供料。
(6)原烟投入车间后一定要进行检测,包括含水率、自然含砂率、包内有无霉变、异味、污染、水浸、雨淋及未经处理的虫蛀烟叶,并做好记录。
(7)备料场地清洁、无杂物,远离污染源。
(8)堆放在备料场的烟垛要有标识牌,注明产地、数量、等级、类别。
(9)需要整选的烟叶,一定要按客户要求进行整选。
(10)要求原烟要进行真空回潮时,一定要尊重客户要求,烟包堆码整齐,掌握好温度和水份,回潮后的烟叶应松散柔软,保持原有色泽,叶片无潮红、水渍现象。
出柜后的烟包存放时间不得超过30min,如遇设备故障应采取措施散包。
2、铺叶、切断解把
(1)将来料按规定要求,连续、均匀、整齐一致地铺在摆把台输送带上。
(2)解把率≥80%
(3)烟叶等级质量符合生产要求。
(4)摆把在铺叶台上的烟把与流向垂直,叶基朝外,无重叠把,流量均匀。
(5)剔除杂物、劣质把烟、霉腐烟。
(6)配方叶组打叶时,定时检查原料投入配方的比例情况,及时调整每台面的摆把数量。
(7)及时处理本工序范围内的散碎烟叶。
(8)更换烟叶等级时,两等级之间要有充分的间隔时间,以保证不混级。
(9)经常检查切断刀,发现切断刀变钝要及时更换,以免发生啃烟现象,减少烟叶造碎,同时避免电机发生过流。
3、润叶
(1)“一次润叶”,提高烟叶的含水率。
(2)“二次润叶”提高烟叶温度,提高烟叶的松散程度。
(3)、蒸汽压力、水压、压缩空气压力等均应符合设备的设计要求;各种仪表工作正常,数字显示准确。
(4)加湿加热系统、热风循环系统及传动部件完好,自动调节系统工作正常;蒸汽、水、压缩空气的管道系统及喷嘴畅通,喷嘴雾化效果良好,滤网完好畅通。
(5)润叶筒内温度达到预热要求时方可投料生产。
(6)通过调整喷汽、喷水装置控制工作水压和工作汽压,保证喷嘴的雾化效果,调整喷嘴位置,对准润叶筒的烟叶流,使润叶机的回潮均匀,避免润叶机出口端的振槽上出现明显的水迹现象。
(7)通过调整喷汽、喷水量和循环热风温度,协调润叶机的增温增湿量
(8)润后烟叶松散、无粘结、水渍、潮红叶、蒸片,确保烟叶原有色泽。
(9)一润后,烟叶的特征为叶片柔软,手握烟筋不易折断,叶片可从烟筋上撕下,边缘不光滑。
(10)二润后烟叶的特征为手握叶片、烟筋柔软,叶片容易从烟筋上撕下,边缘光滑。
(11)充分利用二次润叶之间的仓式喂料机的料仓,尽可能将料仓贮满,增加烟叶吸收水份的时间。
(12)要经常清洗(刷)循环热风中的滤网和散热器等,保证热风系统的正常循环。
(13)要经常校对润叶前的电子皮带称和光电管,使喂料数量准确,流量均匀。
(14)要经常校对红外线水份仪,什么等级用什么通道,使之控制加水量的准确性。
(15)“二次润叶”后的金属探测装置,灵敏可靠。
4、筛砂分选
(1)除去混杂在烟叶中的砂土、烟虫、虫卵等杂物,并分选出碎烟片。
(2)筛分效率大于90%。
(3)烟叶流量均匀,符合设备工艺制造能力。
(4)筛孔不堵塞,筛后物流输出通畅。
(5)要经常检查筛砂后输送振槽上是否有砂土,如有要及时清除,防止振槽偏重。
5、烟叶挑选
(1)人工挑拣出青烟、霉烂烟、杂物及其他不符合技术要求的烟叶。
(2)烟叶松散,流量分配均匀。
(3)烟叶经挑杂后,应保证:“一类杂物”(塑料纤维、油污烟、鸡毛、金属物)含量为零;“二类杂物”(纸屑、绳头、麻片)和“三类杂物”(植物及非烟草类植物纤维)含不能超过0.00665%。
(4)没有散开的烟把,应充分散开。
(5)挑拣出的杂物,应放入专用杂物箱内,并及时清理;不应将杂物与不合格烟叶混放。
(6)挑拣出的不合格烟叶,要定量分类存放,标记清楚,并集中处理。
6、打叶去梗
(1)将烟叶进行梗、叶分离。
(2)打叶去梗后叶片及烟梗符合下列工艺质量指标。
①叶中含梗率≤2.5%;
②梗中含叶率≤1.0%;
③长度大于20mm的烟梗率:上中等烟≥70%,下低次烟≥60%;
④叶片中直径大于2.38mm的烟梗率≤0.5%;
⑤叶片结构应尽量提高中片率,降低大片率,减少造碎率;
⑥最终要满足客户需求。
(3)压缩空气的压力符合设备设计要求。
(4)根据不同类型、等级、品种烟叶的具体情况,合理控制烟叶的进料流量,做好框栏、打辊转速、风量、风速、抛料辊转速等的技术调整。
(5)保证打叶机烟叶布料均匀。
(6)合理调整打叶线各级打叶风分量,一级打叶风分出片率占全线叶片出片率的比例为:(65~70)%左右;二级打叶风分出片率占全线叶片出片率的比例为:20%左右。
(7)根据梗中含叶率及时调整回梗系统的风量。
(8)除尘设备运行效果良好。
(9)生产结束或调换烟叶等级时,应清除机内残留物料。
7、叶片复烤
(1)将打叶去梗后的叶片经过干燥、冷却、回潮,有效地控制其含水率。
(2)冷却段叶片含水率;上中等烟(8~10)%,下低等烟(8~10.5)%;机尾叶片含水率(11.5~13.5)%,含水率标准偏差(SD)≤0.5%。
(3)机尾叶片温度:(50~55)℃。
(4)来料含水率和流量均匀。
(5)投料前进行设备预热,夏季提前20min预热,冬季提前25min预热。
(6)蒸汽压力、水压、压缩空气压力符合设备要求;各种仪表工作正常,显示准确。
(7)加温、加湿系统及传动部件完好,网板孔不堵塞。
(8)蒸汽、水、压缩空气的管道及喷嘴畅通,喷嘴雾化效果良好。
(9)各种阀门及管道接头无跑、冒、滴、漏现象;冷凝水回路畅通。
(10)喂料刮板、喂料输送带、匀叶辊速度要根据烟叶流量及时进行调节;网板的速度根据烟叶含水率及厚度进行调节。
(11)根据叶片含水率,设定烤房温度,采用孤线定温法,低温慢烤,烤房温度不超过100℃;冷房温度(35~45)℃;潮房温度:(50~60)℃。
(12)机尾叶片含水率要求均匀一致,叶片不得有水渍,烤红、潮红现象。
8、叶片包装
将复烤后的松散叶片,按照一定的包装规格和质量(重量),经过计量、预压成型、复称,进行打包捆扎、标识。
(1)叶片含水率(11~13)%或以客户要求为准。
(2)叶片松散,水分均匀,无任何杂物。
(3)均匀喂料,确保箱内密度偏差(DVR)≤10%,质量(重量)允差±0.5kg。
(4)烟叶经预压机预压时,为了避免造碎、油印、影响外观,应适当调整烟叶回涨高度。
(5)烟箱进入扎带机并扎带,4条捆扎带平行等距,捆扎带间距270mm,均匀不偏斜。
(6)箱内片烟应四角充实、平整,无空角、无杂物等。
(7)定期效准计量装置,调整好计量控制系统,尽量减少复称量。
(7)打包成型箱回涨不超过(25~50)mm,箱体完整,无破损、无污染。
(8)叶片装箱后,箱芯温度(35~45)℃。
(9)标识项目齐全、字迹清楚,粘贴工整,不得错号和隔号。
(10)标识内容应包括:烟叶产地、年份、等级、质量(重量)(毛重、净重)、复烤企业名称、生产日期、班次、箱号等。
(11)落地叶片应挑拣干净后,倒入落地烟箱,严防杂物混入。
(12)成品烟和在搬运时要轻拿轻放,防止叉车在抱烟时过紧,造成烟箱变型。
9、梗末处理
(1)、根据客户需求将筛分后的烟梗按一定重量装入纸箱或麻袋,并加标识。
(2)、烟梗含水率(10—13)%;长梗率(>20㎜)≥80%。
(3)、将烤后小于3㎜的碎叶片,按一定的包装规格和质量(重量),进行包装标识。
(4)、碎片含水率(11—13)%;碎片含梗率≤0.5%。
如有侵权请联系告知删除,感谢你们的配合!。