高强度钢和超高强度钢的切削加工
机械行业难加工材料与结构的加工技术(ppt 80页)

外型面难加工结构件主要有:薄壁件、叶片、涡轮盘 、微小微细零件外型面及其它特殊复杂的型面。
内型面难加工结构主要有:蜂窝结构、阵列孔、有特 殊要求的小孔、窄缝及其它特殊复杂的形腔结构。
南京航空航天大学机电学院052系
难加工材料的加工技术
南京航空航天大学机电学院052系
难加工材料与结构概述-分类
(4)低温性能好 钛合金在低温和超低温下能保 持力学性能。
(5)化学活性大 钛的化学活性大,与大气中的 O2、N2、H2、CO、CO2、水蒸气、氨气等均产 生剧烈的化学反应。
(6)导热性差 钛的导热系数低,约为Ni的1/4, Fe的1/5,Al的1/14
(1)钛合金具有密度小、强度高、能耐各种酸、碱、 海水、大气等介质的腐蚀等一系列优良的力学、物理 性能,因此在航空、航天、核能、船舶、化工、冶金 、医疗器械等工业中得到了越来越广泛的应用。
南京航空航天大学机电学院052系
难加工材料与结构概述-应用
1.钛合金
记忆钛合金镜架
钛合金刀具
南京航空航天大学机电学院052系
2.主要内容:
1)难加工材料
1)难加工材料的分类
2)难加工材料的应用
2) 难加工结构
南京航空航天大学机电学院052系
难加工材料与结构概述-分类
1.钛合金 2.高温合金 3.不锈钢 4.高强度钢与超高强度钢 5.复合材料 6.硬脆性材料
南京航空航天大学机电学院052系
难加工材料与结构概述-应用
2.高温合金
低膨胀、恒弹性、高弹 性高温合金
精密合金高温合金不锈钢棒
南京航空航天大学机电学院052系
高强钢和超高强度钢定义

高强钢和超高强度钢的定义及特点1. 引言高强钢和超高强度钢是现代材料科学和工程领域中的两个重要概念。
随着工业技术的不断发展,对材料强度和性能的要求也越来越高。
高强钢和超高强度钢以其卓越的力学性能和广泛的应用领域而备受关注。
本文将对高强钢和超高强度钢的定义、特点和应用进行详细介绍。
2. 高强钢的定义和特点高强钢是指抗拉强度大于等于540MPa的钢材。
相对于普通碳素钢,高强钢具有以下特点:2.1 强度高高强钢的抗拉强度大于等于540MPa,远高于普通碳素钢的抗拉强度。
这使得高强钢在承受大的外力时能够更好地抵抗变形和破坏,提高了结构的安全性和可靠性。
2.2 韧性好高强钢不仅具有高强度,而且具有较好的韧性。
在承受外力时,高强钢能够发生一定程度的塑性变形,从而吸收外力的冲击能量,减少结构的破坏。
这使得高强钢在工程结构中能够更好地应对地震、风载等复杂环境的作用。
2.3 可焊接性好高强钢通常具有良好的可焊接性,可以通过常规的焊接工艺进行连接。
这使得高强钢在工程施工中更加方便快捷,降低了施工难度和成本。
2.4 重量轻相对于普通碳素钢,高强钢的强度更高,但密度相对较低,因此具有较轻的重量。
这使得高强钢在汽车、航空航天等领域得到广泛应用,可以减轻结构自重,提高载荷能力和燃油效率。
3. 超高强度钢的定义和特点超高强度钢是指抗拉强度大于等于980MPa的钢材。
相对于高强钢,超高强度钢具有以下特点:3.1 极高的强度超高强度钢的抗拉强度远远超过普通钢材,达到甚至超过980MPa。
这使得超高强度钢在工程中可以承受更大的荷载,应用于更为苛刻的环境中。
3.2 卓越的韧性超高强度钢在具有极高强度的同时,韧性也相对较好。
这是通过合理的化学成分设计和热处理工艺实现的。
超高强度钢能够在承受外力时发生较大的塑性变形,从而吸收更多的冲击能量,提高结构的抗震性能。
3.3 优异的耐蚀性超高强度钢通常具有良好的耐蚀性,能够在恶劣的环境中长期使用而不受腐蚀的影响。
难加工材料

难加工材料绪论:1.难加工材料分类?特点?2.难切削材料有哪些特点?3.改善难切削材料切削加工性的基本途径有哪些?第一章淬火钢的切削加工1.1 什么是淬火钢?它有哪些切削特点?1.2怎样选择切削淬火钢的刀具材料?1.3切削淬火钢的实例有哪些?第二章不锈钢的切削加工第三章高强度钢和超高强度钢的切削加工第四章高锰钢的切削加工第五章冷硬铸铁和耐磨铸铁的切削加工第六章钛合金的切削加工第七章高温合金的切削加工第八章热喷涂材料的切削加工第九章难熔金属和纯金属的切削加工第十章其他难加工材料绪论:1.难切削材料分哪几类?各有什么特点?难加工材料,科学地说,就是切削加工性差的材料,即硬度>HB250,强度σb>1000MPa,延伸率>80%,冲击值αK>0.98MJ/m2,导热系数K<41.8W(m·K)。
难加工材料种类很多,从金属到非金属材料的范围也很广泛,初步可分为以下八大类:(1)微观高硬度材料:如玻璃钢、岩石、可加工陶瓷、碳棒、碳纤维、各种塑料、胶木、树脂、合成材料、硅橡胶、铸铁等。
这类材料的特点是含有硬质点相,其中有的研磨性很强。
由于这些材料的耐磨性很好,切削时起磨料作用,故刀具主要承受磨料磨损,在高速切削时也同时伴随着物理、化学磨损。
(2)宏观高硬度材料:如淬火钢、硬质合金、陶瓷、冷硬铸铁、合金铸铁、喷涂材料(镍基、钴基)等。
这类材料的主要特点是硬度高。
切削这类材料时,由于切削力大,切削温度高,刀具主要是磨料磨损和崩刃。
(3)加工时硬化倾向严重的材料,如不锈钢、高锰钢、耐热钢、高温合金等。
这类材料的塑性高、韧性好、强度高,强化系数高。
切削加工时的切削表面和已加工表面硬化现象严重。
由于这类材料的强度高,导热系数低,切削温度高,切削力大,刀具主要承受磨料磨损、粘结磨损和热烈磨损。
(4)切削温度高的材料:如合成树脂、木材、硬质橡胶、石棉、酚醛塑料、高温合金、钛合金等。
GBT9943-1998高速钢化学成分表与性能特点用途
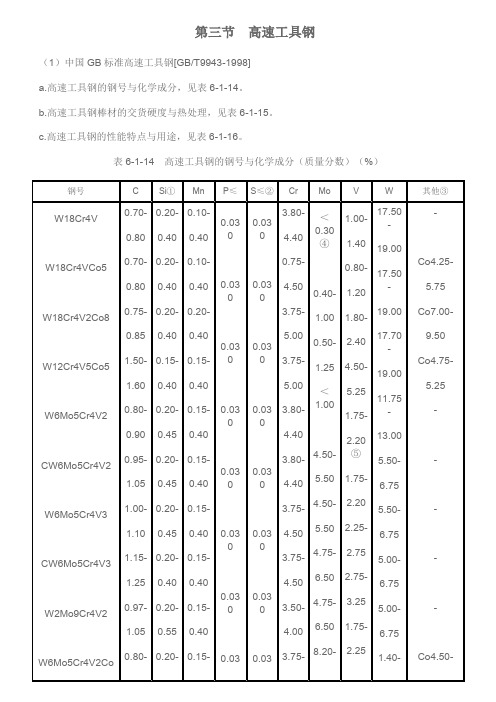
3.50- 3.25- 2.25 6.25-
5.75 Co7.75-
0.15 0.65 0.40
4.25 4.75 0.95- 7.00
8.75
W2MoqCr4VCo8
0.03 0.03
0.77- 0.20- 0.15- 0
0 3.80- 9.00- 1.35 1.15-
-
W9Mo3Cr4V W6Mo5CrV2Al
4.50 6.50 2.75- 6.75
0.03 0
3.50-
4.75-
3.25
5.00-
4.00 6.50 1.75- 6.75
0.03 3.75- 8.20- 2.25 1.40-
其他③
-
Co4.255.75
Co7.009.50
Co4.755.25 -
-
-
-
-
Co4.50-
5
0.90 0.45 0.40 0
3.804.40
< 0.30 ④
1.001.40
17.50 -
19.00
0.75-
0.80- 17.50
0.03 0
4.50
0.40-
1.20
-
3.75- 1.00 1.80- 19.00
0.03
5.00
0.50-
2.40
17.70 -
0 3.75- 1.25 4.50- 19.00
5.00 < 5.25
能稍差,钢的过热和脱碳敏感性较大
时,接近含钴高速钢的使用寿命
(2)中国 YB 标准机器锯条用高速工具钢热轧钢带[YB/T084-1996](表 6-1-17) 表 6-1-17 机器锯条用高速工具钢热轧钢带
高强度钢的定义和分类

高强度钢的定义和分类
佚名
【期刊名称】《涟钢科技与管理》
【年(卷),期】2012(000)005
【摘要】按照国际钢铁协会ULSAB(ulrtaLightSteelAutoBody)项目组的定义,将屈服强度在210~550MPa范围内的钢定义为高强度钢(HSS),屈服强度在550MPa以上的钢定义为超高强度钢(uHss)。
根据强化机理的不同又把高强度
钢板分为普通高强度钢板和先进高强度钢板。
【总页数】1页(P62-62)
【正文语种】中文
【中图分类】U465.11
【相关文献】
1.高强度钢:奥氏体——马氏体高强度耐腐蚀钢 [J],
N.M.Voznesenskaya;E.N.Kablov;A.F.Petrakov;A.B.Shalkevich;张建光
2.Si对低合金高强度钢和超高强度钢抗延迟断裂性能的影响 [J], 刘东雨;白秉哲;方鸿生
3.高强度汽车用钢发展与第3代汽车高强度钢的研究 [J], 罗振轩;荣建;杨可;刘国军;戚文;于婷;徐虹
4.高强度钢和超高强度钢的切削加工 [J], 徐少红
5.心肌病分子水平的定义和分类——2006年美国心脏病学会心肌病定义和分类专家建议 [J], 杜忠东
因版权原因,仅展示原文概要,查看原文内容请购买。
高强度钢和超高强度钢的切削加工

FZ =σsapf ( 1.4 ξ+c) 式中: ξ 为切削工程中的变形系数 ; c 为与刀具前角有关
的常数。
σ s 大 , 故主切削 力 Fz 加大。但是 , 这些钢材的塑性较低 , 故 ξ 减小 , 因而 Fz
不与
由于高强度钢、 超高强度钢的强度高 , 即
W18 Cr 4V 、 W6Mo5 Cr4 V2 等
工件材料强度 G 1 : HIJK6&%-."/ 切削速度 转速 孔径 /mm 10~15 20~30 30~80
σb/M Pa
1 130 1 250 1 324 1 425 1 520 1 668
P
类合金、 TiC
2 !":%&!":()*+,2.1 34@A、 34CБайду номын сангаасEF、 *+9G
P 类涂 层合金 的切削 效果将优 于普 P 类合金加工时 , 可根据粗、 精加工及加 工条件的差异 , 选定其级别和牌号。而 TiC 基和 Ti ( C、 N) 基
基合金及 通硬质合金。在使用 合金主要用于精加工和半精加工。 涂层合金则可用于精加工和 半精加工及负荷较轻的粗加工。 ⑤陶瓷刀具材料。陶瓷刀具的硬度和耐热性高于硬质合
Ti ( C、 N)
fghi: 200 6- 12- 02 jklm: 徐少红 ( 19 65- ) , 女, 江苏扬州人 , 广东工贸职业技术学院 , 高级讲师 , 在职硕士 , 现从事机械类的教学、 技术工作。
72
《装备 制造 技术》 2007 年第 2 期
金 , 允许的切削 速度比硬质合金高 1~2 倍。在高强 度钢、 超高 强度钢的切削中 , 主要用于车削和平面铣削的精加工和半精加 工 , 而不能应用于粗加工或有冲击载荷的断续切削。所以必须 采用
刀具__常用及新牌号硬质合金的使用范围
度较低
YG8C
粗晶粒合金,使用强度较高
YG6A (YG6X)
YG8N
K10
细晶粒合金,耐磨性和使用强度与YG6X 相似
中晶粒合金,其抗弯强度与YG8相同, 硬度和YG6相同,高温切削时热稳定性好
YT5 YT14 YT15 YT30 YW1 YW2
P30
在YT合金中强度最高,抗冲击和抗振动 最好,不易崩刀,但耐磨性较差
是一个重力粗加工切削用合金牌号。较 粗晶粒合金。韧性高、抗冲击、抗振动性 能好
细晶粒合金。具有较高的硬度和韧性, 有较好的耐磨性和抗粘结性能
耐磨性和允许切削速度较YT30高,热稳 定性较高,使用强度和抗冲击性比YT30 好,对冲击和振动敏感,必须按正确工艺 焊接
韧性比YD03好,热稳定性好,耐磨性比 YT15、YW!都高
适于碳钢、合金钢(包括钢锻件、冲压件、铸件的表皮加工),不平整断面和间断 切削时的粗车、粗刨、不连续的粗铣、钻孔
适于碳钢 、合金钢不平整断面和连续切削的粗加工,间断切削时的半精加工和精 加工,连续面的粗铣,铸孔的扩钻、孔的粗扩
适于碳钢、合金钢连续切形式的粗车、半精车和精车,间断切削时的小断面精车, 旋风铣削螺纹,连续断面的半精铣和精铣
专用于各种镍基、钴基、铁及含碳化物自熔性喷涂合金材料的车、铣、刨加工
适于小模数齿轮滚刀、铣刀、所有成型刀具、自动机床刀具、最适于切削易切削钢 及有色金属
适合于加工耐热合金、钛合金及耐热不锈钢,可粗车和断续车削
加工石油管螺纹的梳刀用
用于高强度合金钢的精、半精加工,以及螺纹加工
适于高强度合金钢、高速钢、弹簧钢的精加工和半精加工。适于加工螺纹,对高速 钢与45钢的对焊件加工最为理想
铸铁铣削专用合金,适于各种铸铁粗铣或精铣,也可铣削高锰钢,特别是高效铣削 合金白口耐磨铸铁
高强度钢的概念
高强度钢的概念
一、引言
高强度钢是一种具有优异力学性能的钢材,广泛应用于建筑、汽车、航空航天、船舶等各个领域。
本文档旨在介绍高强度钢的概念,包括抗拉强度、屈服强度、韧性、耐腐蚀性以及加工性能等方面。
二、抗拉强度
抗拉强度是高强度钢的主要力学性能指标之一,它表示钢材在拉伸过程中所能承受的最大拉力。
高强度钢的抗拉强度通常高于普通钢材,能够承受更大的拉伸应力。
三、屈服强度
屈服强度是钢材在受力过程中发生屈服现象时的应力值。
高强度钢的屈服强度也高于普通钢材,能够承受更大的变形和应力。
四、韧性
韧性是钢材在冲击或变形过程中吸收能量的能力。
高强度钢具有良好的韧性,能够承受大的变形和冲击而不发生断裂。
五、耐腐蚀性
高强度钢通常具有较好的耐腐蚀性,能够抵抗大气、海水等环境中的腐蚀介质。
这主要得益于钢材表面的氧化膜和内部合金元素的防腐作用。
六、加工性能
高强度钢的加工性能较好,易于进行切割、弯曲、焊接等加工操作。
同时,高强度钢还具有良好的可焊性和可塑性,能够满足各种复杂形状的加工需求。
七、结论
高强度钢具有优异的力学性能和良好的耐腐蚀性,广泛应用于各个领域。
在选择和使用高强度钢时,需要根据具体的应用场景和需求,综合考虑其抗拉强度、屈服强度、韧性、耐腐蚀性以及加工性能等因素。
工件切削加工性
刃和刀尖的强度,一般取γ。=-4—0º,主偏角kr适当减小,刀
尖圆弧半径rε适当加大。
淬硬钢的组织为回火马氏体,硬度达HRC60以上,塑性
和导热系数都很低。其加工性及刀具材料、刀具几何参数的 选择基本上与冷硬铸铁同。对它们进行精加工,可采用CBN 刀具。
κr= 45° ~ 75°、λs= -10 °
6.钛合金切削加工性分析
1).钛合金特点和分类
a)密度小(约为 4.5g / cm3 ),比钢约小一倍。
b)强度极限高(可达σb=0.981~1.37GPa), 钛合金的比强度(单位重量强度)很高,尤其在高温下比强度仍 很高,这一点对航空、航天工业尤为重要。
工件切削加工性
表 7– 1 材料可加工性分级
分级
名称及种类
Kv
1 很容易切削材料 一般有色金属
> 3.0
2
易切削钢
容易切削材料
3
较易切削钢
2.5 ~ 3.0 1.6 ~ 2.5
4
一般钢及铸铁
1.0 ~ 1.6
普通材料
5
稍难切削材料 0.65 ~ 1.0
6
较难切削材料 0.5 ~ 0.65
7
难切削材料
理 ;对镍基高温合金可采用固溶处理(淬火)
b)、首选一足够的vc以保证加工质量,再选f 、ap
c)、选择合适的刀具材料和角度 连续切:YG6X、YW1 断续切:M42、501、B201
高速钢刀具:γo=15 ° ~20°、αo=12 ° 、κr=45 ° 硬质合金刀具:γo=5° ~ 10°、αo= 8° ~ 15° 、
在自动机床或自动生产线上,常常以切屑
《超高强度钢》课件
详细描述
通过特殊的表面处理技术,如喷涂防腐涂层 或进行渗碳处理,超高强度钢能够有效地抵 抗各种腐蚀介质,如空气、水、酸碱等。这 种优良的耐腐蚀性使得超高强度钢在海洋工 程、化工设备等领域具有广泛的应用前景。
03 超高强度钢的生产技术
热处理技术
退火
通过加热至一定温度并保温,使钢软化,以便进一步加工。
详细描述:铝合金具有较好的强度与重量比,比超高强 度钢更轻,适合用于需要减轻重量的场合,但在承受高 应力方面不如超高强度钢。
详细描述:铝合金在某些环境下也容易受到腐蚀,但其 耐腐蚀性能优于普通钢材,与超高强度钢相当。
详细描述:铝合金的加工性能较好,易于切割、焊接和 加工,与超高强度钢相比,其加工性能更优。
汽车工业应用
汽车工业是超高强度钢的重要应用领域,主要用于制造汽车底盘、悬挂系统、安全装置等关键部件。随着节能减 排和轻量化需求的增加,超高强度钢在汽车工业的应用将更加广泛。
环境友好性的考虑
绿色生产技术
在超高强度钢的生产过程中,采用绿色生产技术,降低能耗和减少废弃物排放。例如,采用节能环保 的冶炼和连铸技术,减少废气、废水和固废的产生。
制造工艺
总结词
超高强度钢的制造工艺主要包括冶炼、轧制、热处理等环节,其制造工艺复杂 ,技术要求高。
详细描述
超高强度钢的制造需要经过严格的冶炼、轧制、热处理等环节,确保钢材的纯 净度和组织结构均匀性。同时,制造过程中还需采用先进的合金元素添加技术 和精密的加工工艺,以满足钢材的高性能要求。
02 超高强度钢的性能特点
可回收利用
超高强度钢应具有良好的可回收利用性,以便在产品生命周期结束后进行再生利用。通过合理的材料 设计和技术创新,实现超高强度钢的环保和可持续发展。
- 1、下载文档前请自行甄别文档内容的完整性,平台不提供额外的编辑、内容补充、找答案等附加服务。
- 2、"仅部分预览"的文档,不可在线预览部分如存在完整性等问题,可反馈申请退款(可完整预览的文档不适用该条件!)。
- 3、如文档侵犯您的权益,请联系客服反馈,我们会尽快为您处理(人工客服工作时间:9:00-18:30)。
简介:1 什么是高强度钢和超高强度钢?所谓高强度钢,是指那些在强度和韧性方面结合很好的钢种。
低合金结构钢,经调质处理后,具有很好的综合力学性能。
其抗拉强度sb>1 200MPa时,叫高强度钢;其抗拉强度sb>1500MPa时,称为超高强度钢。
超高强度钢,视其合金含量的多少,可分为低合金超高强度钢(合金含量不大于6%)、中合金超高强度钢和高合金超高强度钢。
含一种合金元素的高强度合金钢有铬钢、关键字:刀具夹具切削铣削车削机床测量1 什么是高强度钢和超高强度钢?所谓高强度钢,是指那些在强度和韧性方面结合很好的钢种。
低合金结构钢,经调质处理后,具有很好的综合力学性能。
其抗拉强度σb>1200MPa时,叫高强度钢;其抗拉强度σb>1500MPa时,称为超高强度钢。
超高强度钢,视其合金含量的多少,可分为低合金超高强度钢(合金含量不大于6%)、中合金超高强度钢和高合金超高强度钢。
含一种合金元素的高强度合金钢有铬钢、镍钢、锰钢等;含两种合金元素的合金钢有铬镍钢、铬锰钢、铬钼钢等;含三种以上合金元素的高强度合金钢有铬锰硅钢、铬镍钨钢、铬镍钼钢、铬锰钛钢、铬锰钼钒钢等。
高强度钢和超高强度钢的原始强度和硬度并不高,但是经过调质处理后可获得较高的强度,硬度在HRC30~50之间。
钢的抗拉强度与硬度之间存在一定的关系。
一般来说,硬度提高强度也随之增高,但不能说高强度钢就是高硬度钢。
所谓高强度钢和超高强度钢,是指综合性能而言的。
淬火钢的硬度很高,但不能称为高强度钢和超高强度钢,其原因是它的综合性能不好,几乎没有塑性,韧性也很差,只能作耐磨零件和工具。
2 高强度钢和超高强度钢有哪些切削特点?高强度钢和超高强度钢,由于加入不同量的合金元素,经热处理后,Si、Mo、Ni 等元素使固溶体强化,金相组织多为马氏体,具有很高的强度(最高可达1960MPa)和较高的硬度(HRC>35),冲击韧性高于45号钢,切削时具有以下特点:1.刀具易磨损、耐用度低:高强度钢和超高强度钢,调质后的硬度一般在HRC50以下,但抗拉强度高,韧性也好。
在切削过程中,刀具与切屑的接触长度小,切削区的应力和热量集中,易造成前刀面月牙洼磨损,增加后刀面的磨损,导致刃口崩缺或烧伤,刀具的耐用度低。
2.切削力大:高强度钢和超高强度钢的剪切强度高,变形困难,切削力在同等的切削条件下,比切45号钢的单位切削力大1.17~1.49倍。
3.切削温度高:这两种钢的导热性差,切削时切屑集中于刃口附近很小的接触面内,使切削温度增高。
如45号钢的导热系数为50.2 W/(m·K),而38CrNi3MoVA的导热系数为29.3 W/(m·K),仅为45号钢的60%,切削38CrNi3MoVA时的切削温度比切削45号钢的切削温度高100℃左右。
切削温度高,刀具磨损加剧。
4.断屑困难:由于高强度钢和超高强度钢具有良好的塑性和韧性,所以切削时切屑不易拳曲和折断。
切屑常缠绕在工件和刀具上,影响切削的顺利进行。
3 切削高强度钢和超高强度钢时怎样选择刀具材料?高强度钢和超高强度钢具有很高的强度和硬度,切削时要求刀具应具有较高的红硬性、耐磨性及冲击韧性,而且不易产生粘结磨损和扩散磨损。
粗加工和断续切削时,要求刀具具有抗热冲击性能。
除金刚石刀具外,各种刀具材料均可以切削,在选择刀具材料时,应根据切削条件合理选择。
1.高速钢:选用高性能高速钢切削高强度钢和超高强度钢,应根据工件材料的性能、形状、加工方法和工艺系统刚性等特点,全面考虑刀具材料的耐热性、耐磨性和韧性等。
当工艺系统刚性较好、刀具型面简单时,可采用钨系、钨钼系高钒高钴高速钢;型面复杂时,可采用钨钼系、高碳低钒含铝高速钢或钨钼系高碳低钒高钴高速钢;当工艺系统刚性较差时,可采用钨钼系低钒含铝高速钢及钨钼系低钒高钴高速钢;在冲击切削条件下,宜采用钨钼系高钒高速钢、钨钼系含铌高速钢或钨钼系含铝高速钢。
不同的切削方式切削高强度钢和超高强度钢时,高速钢牌号的选择见表1。
2.粉末冶金高速钢和TiN涂层高速钢:粉末冶金高速钢,是由高速钢粉末在高温(1100℃)、高压(100MPa)下直接压制,再锻造成所需要的刀具形状,加工淬火后刃磨而成。
它具有硬度高、高温硬度好、耐磨性好的特点,适用于高强度钢和超高强度钢的切削。
如原冶金部钢铁研究总院生产的FW12Cr4V5C05(FT15)和FW 10Mo5Cr4V2Co12等。
高速钢刀具TiN涂层,可以延长刀具耐用度2~3倍,提高切削速度25%。
常用的涂层高速钢刀具有:麻花钻、立铣刀、丝锥、齿轮滚刀、铰刀和插齿刀等。
3.硬质合金:根据硬质合金的性能,它是切削高强度和超高强度钢的主要刀具材料。
一般应选新型高性能硬质合金或涂层硬质合金。
4.陶瓷刀具:它的硬度和耐热性高于硬质合金,允许的切削速度比硬质合金高1~2倍。
在高强度钢和超高强度钢的切削中,陶瓷刀具主要用于车削和平面铣削的半精加工和精加工中。
推荐选用Al2O3~TiC系列陶瓷,如AT6、AG2、T8、LT35、LT55等。
5.立方氮化硼(CBN、PCBN):这种刀具的硬度、耐磨性及耐热性很高,PCBN的强度也很高,达1500 MPa,适用于高强度钢和超高强度钢的车削和铣削,主要用于半精加工和精加工。
简介:陶瓷刀具车5 切削高强度钢和超高强度钢时怎样选择切削用量?各种高强度钢和超高强度钢中的合金元素种类与含量不同,热处理后的力学物理性能差异也很大,因此应根据不同的切削对象合理选择切削用量。
选择切削用量的基本原则与一般切削相同。
切削高强度钢时的切削速度应比加工一般钢材低些,为切削45号钢的切削速度的50%左右。
加工超高强度钢应更低一些,为切削45号钢的切削速度的30%。
采用高关键字:刀具夹具切削铣削车削机床测量5 切削高强度钢和超高强度钢时怎样选择切削用量?各种高强度钢和超高强度钢中的合金元素种类与含量不同,热处理后的力学物理性能差异也很大,因此应根据不同的切削对象合理选择切削用量。
选择切削用量的基本原则与一般切削相同。
切削高强度钢时的切削速度应比加工一般钢材低些,为切削45号钢的切削速度的50%左右。
加工超高强度钢应更低一些,为切削45号钢的切削速度的30%。
采用高速钢刀具时,V c =3~11m/min ,f=0.03~0.3mm/r ,a p =0.3~2mm ;采用陶瓷刀具切削时,V c =70~210m/min ,f=0.05~1mm/r ,a p =0.1~4mm ;采用CBN(或PCBN)切削时,V c =40~220m/min ,f=0.03~0.3mm/r ,a p ≤0.8 mm 。
采用硬质合金刀具车削时,粗车或荒车时,V c =10~90m/min ,f=0.3~1.2mm/r ,a p =4~20 mm ;半精车时,V c =30~140m/min ,f=0.15~0.4mm/r ,a p =1~4pmm ;精车时,V c =70~120m/min ,f=0.05~0.2mm/r ,a c =0.05~1.5mm 。
在选择切削速度时,应考虑材料的强度,一般σb =1000~1500MPa 时,V c =85~40m/min ,σb =1500~1700MPa 时,V c =58~35m/min ;σb =2000~2150MPa 时,V c =35~10m/mi n 。
6 怎样解决切削高强度钢和超高强度钢时的断屑问题?陶瓷刀具车切削高强度钢和超高强度钢时的断屑问题,是影响加工效率和生产自动化的重要问题。
同时,解决好断屑问题,也是提高加工质量和刀具耐用度的重要手段。
因此必须根据切削的条件和加工方式,选择有效的断屑措施。
1.利用刀片断屑槽断屑:这种方法是最常用而比较简单的断屑方法。
常用的刀具都可以磨出一定的槽型,但一般一种槽型只能针对一种或几种工件材料,在一定的切削用量范围内断屑。
焊接式硬质合金刀具,可以磨成槽底为圆弧槽,前宽深后窄浅的锥形槽、弧形槽、腰鼓形槽、棱形凸面槽等,见图1和图2。
锥形断屑槽刃磨起来比较容易,其几何参数见表5。
图1 锥形断屑槽弧形槽腰鼓形槽凸棱面槽图2 弧形槽、腰鼓形槽、凸棱面槽3.障碍式(或导屑器)断屑:采用可调式断屑压板或弹性断屑板强迫断屑,也是常采用的方法。
钻削、镗削时可采用导屑器,防止切屑缠绕,见图3。
4. 改变刀具几何参数断屑:在切削高强度钢和超高强度钢时,可以通过改变一个或几个刀具几何参数达到断屑的目的。
如加大主偏角、加大负倒棱宽度、减小前角等。
但应注意的是,改变刀具几何参数时,必须综合考虑工艺系统刚性和刀具耐用度。
当机床刚性较差或弱刚性工件时,如加大倒棱宽度、减小前角,会使切削力增加,容易引起工件振动,影响加工质量。
而加大主偏角,会使刀尖强度降低,散热面积减小,影响刀具耐用度。
一般只在半精车和精车时采用。
5. 改变切削用量断屑:当切削深度不很大时,可以通过增加进给量、降低切削速度来达到断屑的目的。
当切削深度已经较大时,必须考虑刀具的强度、工艺系统的刚性和机床功率,以免造成“闷车”,使刀具损坏。
6. 工件预切槽断屑法:切削高强度钢和超高强度钢时,可以在工件的被加工表面上,预先加工1~2条直槽或螺旋槽,深度不得超过切削深度,一般为0.6~0.8a p 。
使切削深度在切削过程中不停的变化,可以取得稳定的断屑效果。
7. 间断进给断屑:在切削过程中,周期性瞬时停止进给,也可以达到良好断屑的目的。
8. 外力强迫断屑:在切削过程中,可以采用辅助装置或能量,使切屑被迫折断。
如喷射高压流体等。
7 对高强度钢和超高强度钢铰孔时怎样选择铰刀?图3 钻头导屑器对高强度钢和超高强度钢铰孔时,可选用高性能高速钢和硬质合金作为刀具材料。
高性能高速钢中的高钒、高钴、含钴或含铝的超硬高速钢,非常适于加工这种钢材。
如用含钴超硬高速钢W12Mo5Cr4V3Co5Si制作的铰刀,直径Ø18 mm,铰削高强度钢(σb =1200~1300 MPa)的孔时,每把铰刀可铰孔60~70个。
铰时n=140r/m in,f=0.05mm/r,粗糙度Ra为1.6µm。
用于高强度钢的硬质合金铰刀,如图4-4所示,刀具材料为YT15硬质合金。
此铰刀适用于L/D≤5及D=6~80mm的孔。
使用时要充分加乳化液。
如使用钻套,必须使用旋转钻套,以避免铰刀刃口与钻套摩擦。
操作时,先将刀具与工件接触后再开车,退刀时最好先停车。
8 铰削高强度钢和超高强度钢孔时怎样选择切削用量?高强度钢和超高强度钢一般铰孔时,切削余量不宜过大,否则会影响加工效率和刀具耐用度。
当孔径小于等于15 mm时,余量约为0.1~0.15 mm;孔径大于15 m m时,余量为0.2~0.3 mm。
在选择切削速度时,要充分考虑工件材料的强度和硬度。