MSA测量系统分析与结果解释
MSA测量系统分析

MSA测量系统分析MSA(测量系统分析)是一种用于评估和改进测量系统稳定性、偏倚和线性性能的方法。
通过进行MSA,可以确定测量系统是否足够稳定和准确,以便在不同的情况下对产品进行正确的测量。
稳定性是指测量系统在相同的测量条件下的一系列测量结果是否一致。
稳定性是MSA中最基本的指标之一,因为如果测量系统不稳定,那么无论多么准确的测量工具都无法提供可靠的测量结果。
偏差是指测量结果与真实值之间的差异。
在MSA中,需要比较测量系统的平均偏差与零偏差之间的差异。
如果两者之间存在较大的差异,则说明测量系统存在系统性的偏离问题,需要进行校准或修正。
线性是指测量系统的输出是否与输入之间存在良好的线性关系。
在MSA中,需要绘制出测量系统的线性回归图,通过斜率和截距来评估测量系统的线性性能。
如果回归线接近理想的45度直线,则说明测量系统的线性性能较好。
在进行MSA时,一般采用以下步骤来评估测量系统的稳定性、偏差和线性性能:1.收集测量数据:使用相同的测量系统对一批样本进行测量,并记录测量结果。
2.统计分析:对于每个样本,计算测量结果的平均值和标准偏差。
然后,计算每个样本平均值之间的差异,并计算整体平均偏差和标准偏差。
3. 制作控制图:使用收集的测量结果,绘制测量系统稳定性的控制图。
通常使用X-bar图来监控平均值的稳定性,使用R或S图来监控标准偏差的稳定性。
4.比较平均偏差和零偏差:计算测量系统的平均偏差和零偏差之间的差异,并进行比较。
如果差异较大,则说明测量系统存在系统性的偏离问题。
5.绘制线性回归图:使用测量数据,绘制测量系统的线性回归图。
计算斜率和截距,并与理想的45度直线进行比较。
如果回归线接近理想线,则说明测量系统具有良好的线性性能。
通过以上步骤,可以对测量系统进行全面的评估,并确定是否需要采取措施来改善测量系统的稳定性、偏差和线性性能。
常用的改善方法包括校准测量工具、调整测量程序和培训操作人员等。
总之,MSA是一种重要的质量管理工具,能够帮助企业评估和改进测量系统的稳定性、偏差和线性性能。
测量系统分析报告MSA

测量系统分析报告MSA1. 引言测量系统分析(Measurement System Analysis,简称MSA)是指通过分析和评估测量系统的性能、稳定性和可靠性,来判断测量结果的准确性和可靠性的过程。
本报告旨在对某测量系统进行全面的分析和评估,以帮助提升测量系统的质量和可靠性。
2. 测量系统分析方法在进行测量系统分析时,常采用以下方法:2.1 重复性与再现性分析重复性和再现性是评估测量系统可靠性的重要指标。
通过对同一对象进行多次测量,可以评估测量结果的一致性和稳定性。
2.2 偏倚分析偏倚分析用于评估测量系统是否存在系统性的误差。
通过对测量系统进行校准,并比较校准前后的测量结果,可以判断测量系统的偏倚情况。
2.3 线性分析线性分析用于评估测量系统是否存在线性关系。
通过测量系统对一系列已知标准进行测量,并绘制测量结果与标准值之间的图表,可以判断测量系统的线性关系。
3. 案例分析本次测量系统分析以某电子元件测量系统为例进行分析。
3.1 重复性与再现性分析通过对同一电子元件进行连续十次测量,并记录测量结果,得到以下数据:测量次数测量结果1 12.32 12.43 12.14 12.35 12.26 12.47 12.58 12.29 12.610 12.3通过计算这十次测量结果的平均值和标准偏差,得到重复性和再现性的评估数据。
3.2 偏倚分析为了评估测量系统的偏倚情况,我们对测量系统进行了校准,并测量了一系列标准样本。
校准前后的测量结果如下:标准样本校准前测量结果校准后测量结果1 2.3 2.12 3.4 3.23 4.5 4.44 5.6 5.75 6.7 6.56 7.8 7.9通过比较校准前后的测量结果,可以评估测量系统的偏倚情况。
3.3 线性分析为了评估测量系统的线性关系,我们选择了一系列已知标准进行测量,并绘制了测量结果与标准值之间的图表。
图表显示测量系统的测量结果与标准值之间存在一定的线性关系。
测量系统分析报告MSA

测量系统分析报告MSA在现代制造业中,为了确保产品质量的稳定性和一致性,对测量系统进行准确的分析和评估是至关重要的。
测量系统分析(Measurement System Analysis,简称 MSA)就是一种用于评估测量过程的工具和方法,它可以帮助我们确定测量数据的可靠性、准确性以及可重复性。
测量系统通常由测量人员、测量设备、测量方法、测量环境和被测量对象等要素组成。
而 MSA 的目的就是要评估这些要素对测量结果的影响,并确定测量系统是否能够满足预期的测量要求。
MSA 主要包括以下几个方面的内容:一、测量系统的准确性准确性是指测量结果与真实值之间的接近程度。
在 MSA 中,通常通过与标准值进行比较来评估测量系统的准确性。
例如,如果我们要测量一个零件的长度,已知其标准长度为 100mm,而测量结果为98mm,那么就存在 2mm 的偏差。
为了提高准确性,我们需要对测量设备进行校准,并确保测量方法的正确性。
二、测量系统的重复性重复性是指在相同的测量条件下,对同一被测量对象进行多次测量时,测量结果的一致性。
如果一个测量系统具有良好的重复性,那么多次测量的结果应该非常接近。
例如,对同一个零件的同一尺寸进行10 次测量,如果测量结果的差异很小,说明测量系统的重复性较好。
三、测量系统的再现性再现性是指在不同的测量条件下,由不同的测量人员使用相同的测量设备和测量方法对同一被测量对象进行测量时,测量结果的一致性。
例如,不同的操作人员在不同的时间对同一个零件的同一尺寸进行测量,如果测量结果的差异较小,说明测量系统的再现性较好。
四、稳定性稳定性是指测量系统在一段时间内保持其性能的能力。
通过定期对测量系统进行监控和测量,可以评估其稳定性。
如果测量系统的稳定性较差,可能需要对其进行维护或更换。
为了进行有效的 MSA,我们通常采用以下几种方法:1、均值极差法(Average and Range Method)这是一种常用的评估测量系统重复性和再现性的方法。
MSA测量系统分析报告
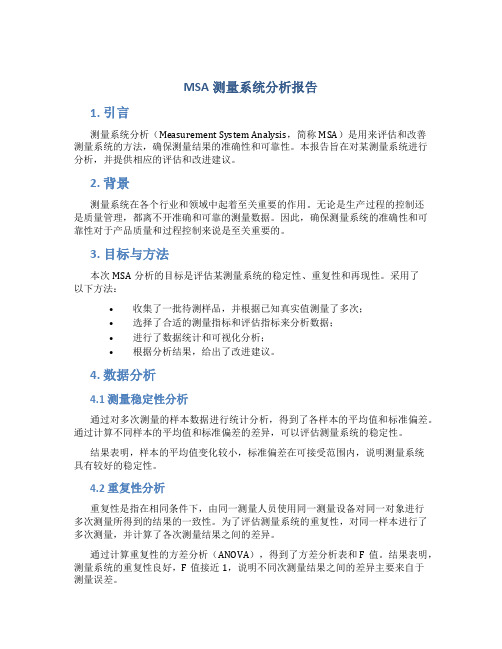
MSA测量系统分析报告1. 引言测量系统分析(Measurement System Analysis,简称MSA)是用来评估和改善测量系统的方法,确保测量结果的准确性和可靠性。
本报告旨在对某测量系统进行分析,并提供相应的评估和改进建议。
2. 背景测量系统在各个行业和领域中起着至关重要的作用。
无论是生产过程的控制还是质量管理,都离不开准确和可靠的测量数据。
因此,确保测量系统的准确性和可靠性对于产品质量和过程控制来说是至关重要的。
3. 目标与方法本次MSA分析的目标是评估某测量系统的稳定性、重复性和再现性。
采用了以下方法:•收集了一批待测样品,并根据已知真实值测量了多次;•选择了合适的测量指标和评估指标来分析数据;•进行了数据统计和可视化分析;•根据分析结果,给出了改进建议。
4. 数据分析4.1 测量稳定性分析通过对多次测量的样本数据进行统计分析,得到了各样本的平均值和标准偏差。
通过计算不同样本的平均值和标准偏差的差异,可以评估测量系统的稳定性。
结果表明,样本的平均值变化较小,标准偏差在可接受范围内,说明测量系统具有较好的稳定性。
4.2 重复性分析重复性是指在相同条件下,由同一测量人员使用同一测量设备对同一对象进行多次测量所得到的结果的一致性。
为了评估测量系统的重复性,对同一样本进行了多次测量,并计算了各次测量结果之间的差异。
通过计算重复性的方差分析(ANOVA),得到了方差分析表和F值。
结果表明,测量系统的重复性良好,F值接近1,说明不同次测量结果之间的差异主要来自于测量误差。
4.3 再现性分析再现性是指在相同条件下,由不同测量人员使用同一测量设备对同一对象进行测量所得到的结果的一致性。
为了评估测量系统的再现性,不同测量人员对同一样本进行了多次测量,并计算了各次测量结果之间的差异。
通过计算再现性的方差分析(ANOVA),得到了方差分析表和F值。
结果表明,测量系统的再现性良好,F值接近1,说明不同测量人员的差异对测量结果的影响较小。
超详细MSA测量系统分析讲解

2.线性的分析方法和接受准则
●回顾:
1.什么是线性?
●线性指南
1.在量具的操作范围内,选择g(子组数)≥5个零件 2.检验每个零件,以确定基准值 3.一个人测量每个零件m(子组容量)≥10次 4.计算每次测量的零件偏倚及零件偏倚的平均值。(偏倚i,j=Xi,j -基准值) 5.在线性图上画出单值偏倚和基准的偏倚值 6.计算并画出最佳拟合线和置信带 7.画出“偏倚=0”线,评审该图指出特殊原因和线性的可接受性 (即“偏倚=0”线必须完全在拟合线置信带以内)
MSA
课前思考
1.什么是MSA ? 2.什么时候做MSA? 3.谁做MSA? 4.哪些测量系统需要做MSA? 5.在哪里做MSA? 6.怎么做MSA?原理是什么?
MSA
第一单元
MSA的基本概念
MSA
二.MSA的基本概念
1.测量的定义
●测量:被定义为“对某具体事物赋予数字(或数值),以表示它们 对于特定特性之间的关系”。这定义由C.Eisenhart(1963)首次提出 。赋予数字的过程被定义为测量过程。而数值的指定被定义为测量值 。
3.MSA与FMEA(潜在失效模式及后果分析)
a. FMEA可以用来识别特殊特性,为SPC和MSA确定控制和分析的 对象
b.可以建立测量系统FMEA,管理测量系统的风险
MSA
一.MSA的概述介绍
(二)MSA 与汽车行业五大质量手册
4.MSA与SPC(统计过程控制)
测量系统对适当的数据分析来说是很关键的,在收集过 程数据之前就应很好地对它加以了解。这些测量系统缺少 统计控制,或它们的变差在过程总变差中占很大比例,就 可能做出不恰当的决定。
测量系统分析报告MSA

测量系统分析报告MSA概述测量系统分析(MSA)是一种用于评估和提高测量系统的准确性和稳定性的方法。
在制造和生产过程中,准确的测量是至关重要的,因为它对产品质量的监控和改进起着关键作用。
本文档将对测量系统进行分析,包括可重复性、再现性和稳定性等关键指标的评估,以及对所得数据的解释和建议。
测量系统简介测量系统是用来进行尺寸、重量、温度等物理量测量的设备和过程的总称。
测量系统可以包括测量仪器、传感器、仪表和操作方法等。
而测量系统分析是对这些测量系统进行评估和优化的过程。
测量系统的重要性测量系统是确保产品尺寸和规格准确的关键因素。
一个好的测量系统可以提供可靠的数据,帮助生产商识别潜在的质量问题,并做出正确的调整,以确保产品的一致性和合格性。
然而,一个不准确或不稳定的测量系统可能会导致误判,从而对产品的质量和性能产生负面影响。
MSA的关键指标可重复性(Repeatability)可重复性是指在相同测量条件下,测量系统对同一对象进行重复测量的结果间的一致性。
当一个测量系统具有良好的可重复性时,重复测量的结果应该接近。
在测量系统分析中,使用计算变异系数(CV)来评估测量数据的可重复性。
再现性(Reproducibility)再现性是指在不同测量条件下,不同测量系统或不同测量人员对同一对象进行测量所得结果的一致性。
一个良好的测量系统应该具有较高的再现性,即不同的测量设备和人员能够得到相似的测量结果。
在测量系统分析中,可以使用方差分析(ANOVA)来评估测量数据的再现性。
线性度(Linearity)线性度是指测量系统的输出值是否与被测量对象的实际值呈线性关系。
一个好的测量系统应该具有较好的线性度,即在不同测量范围内,测量结果与实际值之间应该存在一个良好的线性关系。
可以使用回归分析来评估测量数据的线性度。
稳定性(Stability)稳定性是指测量系统在一段时间内保持准确性和一致性的能力。
测量系统的稳定性对于长期生产过程的监控和控制非常重要。
MSA测量系统分析指标解读与评估方法
MSA测量系统的重要性
提高产品质量
通过评估测量系统的性能,可以减少因测量误差 导致的产品质量问题,提高产品质量水平。
降低生产成本
优化测量系统可以减少不必要的返工和浪费,降 低生产成本。
增强客户满意度
准确的测量结果有助于提高客户满意度,增强品 牌信誉。
MSA测量系统的应用领域
制造业
用于评估生产线上的测 量设备,确保产品质量
实施效果
优化后的测量系统在产品质量控制方面取得了显著成效。产品的合格率提高了15%,客户投诉率降低了 10%,为公司赢得了良好的市场声誉和经济效益。
06
MSA测量系统未来发展趋势 与展望
技术创新与发展趋势
智能化发展
随着人工智能技术的不断进步,MSA测量系统将更加智能化, 实现自动化测量、数据分析和处理。
实施效果
经过改进后的测量系统,在产品质量控制方面取得了显著成效。产品的 合格率提高了10%,客户投诉率降低了8%,为公司带来了可观的经济 效益。
案例二:某电子企业MSA测量系统改进实践
问题描述
某电子企业在生产过程中,发现测量系统存在较大的误差和不稳定性,导致产品质量波动 较大。
解决方案
该企业决定对测量系统进行改进,引入MSA方法进行全面的分析和评估。通过对测量设 备的校准、优化测量环境、改进测量方法等措施,提高了测量系统的精度和稳定性。
制定测量计划
制定详细的测量计划,包括测量时间、地点、人 员、设备、方法等。
实施测量
按照测量计划进行测量,记录测量数据,确保数据 的准确性和完整性。
数据分析
对测量数据进行统计分析,计算各项指标,评估 测量系统的性能。
结果报告
将分析结果以报告形式呈现,包括各项指标的计算结果 、评估结论和改进建议等。
测量系统分析报告MSA
测量系统分析报告MSA前言:测量系统是评估产品质量和过程稳定性的重要工具。
测量系统分析(MSA)是一种系统性的方法,用于评估和优化测量系统的准确性、精确度、稳定性和能力。
本报告旨在为读者提供关于测量系统的详细分析和评估结果。
一、背景介绍在任何生产或制造领域中,对产品进行准确的测量是确保质量控制的关键因素。
测量系统即测量工具、设备和人员的组合,用于定量评估产品的属性或特征。
可靠性和准确性的测量系统对于正确评估产品的一致性、稳定性以及满足客户要求至关重要。
二、测量系统分析的目的测量系统分析的主要目的是评估和改进测量系统的性能,确保测量结果准确可靠。
该分析有助于确定测量系统的误差来源,评估测量设备和工具的重复性和再现性,并为生产过程提供可靠的测量数据,帮助生产商做出正确的决策。
三、分析方法选择合适的分析方法对测量系统进行评估是至关重要的。
常用的MSA方法包括重复性和再现性分析、偏差和准确度分析、稳定性分析以及测量能力评估。
根据实际情况和需要,可以选择单因素方差分析、方差-方差分析或组件间方差分析等方法。
四、评估结果1. 重复性和再现性分析:通过对同一样本进行多次测量,计算重复性和再现性指标。
根据分析结果确定测量系统中存在的误差来源,以及测量设备和操作者之间的差异。
重复性和再现性分析结果对评估测量系统的稳定性和可靠性至关重要。
2. 偏差和准确度分析:通过与真实值进行比较,分析测量系统的偏差和准确度。
评估测量结果与实际情况之间的差异,并确定偏差的来源。
这有助于改进测量系统的精确性和准确性。
3. 稳定性分析:对测量系统的稳定性进行评估,查看测量结果是否随时间发生变化。
通过监测和控制稳定性,可以确保测量系统具有一致性和可靠性。
4. 测量能力评估:评估测量系统的能力,即判断测量系统是否满足产品质量控制的要求。
通过分析测量系统的变异性、精确度和准确度,评估其对于产品特性的测量能力。
五、结论与改进建议基于对测量系统的分析和评估,我们得出以下结论:1. 测量系统的稳定性较高,能够提供一致性和可靠的测量结果。
超详细MSA测量系统分析讲解
超详细MSA测量系统分析讲解MSA(Measurement System Analysis)是一种用于评估测量系统准确性和可重复性的方法。
它被广泛应用于各种工业领域,特别是质量管理和过程改进领域。
下面将详细介绍MSA的一些关键概念和测量过程。
首先,MSA的主要目标是确保测量系统能够准确地衡量一个过程或产品的特性。
测量系统可以是任何用于测量的工具、设备或方法,如卡尺、天平、人工测量等。
为了评估测量系统的准确性和可重复性,主要使用以下几个指标:1. 精确度(Accuracy): 指测量结果与真实值之间的接近程度。
通常通过与已知的标准进行比较来评估。
2. 可重复性(Repeatability): 指在重复测量同一样本时,测量系统的结果之间的一致性。
这可通过多次测量同一样本并比较结果来评估。
3. 重现性(Reproducibility): 指在不同的条件下,不同操作员使用相同的测量系统测量同一样本时,测量结果之间的一致性。
现在,我们将介绍MSA的几个主要步骤:1.选择适当的测量系统:首先需要确定要使用的测量系统,这取决于所需测量的特性以及资源和时间的限制。
为了选择合适的测量系统,需要考虑其测量范围、精度和可靠性等因素。
2.收集数据:在进行MSA时,需要收集足够的数据量以便对测量系统进行分析。
数据收集可以通过抽样、重复测量或使用模拟数据等方式进行。
3.分析数据:收集到数据后,需要对其进行统计分析。
常用的分析方法包括直方图、均值-方差图和相关性分析等。
通过这些分析,可以计算出测量系统的准确性和可重复性指标。
5.评估测量系统:通过上述步骤,可以评估测量系统的准确性和可重复性,并确定它是否符合要求。
如果发现测量系统存在问题,可以采取改进措施,如校准、调整或更换测量设备等。
需要注意的是,MSA不仅适用于新的测量系统,也适用于已经在使用的测量系统。
对于已经在使用的测量系统,MSA可以帮助识别潜在的问题并提出相应的改进建议。
MSA-测量系统分析解析
变化后。
实施测量系统分析的时期
二、在量产阶段:
已完成MSA分析的测量系统发生以下变更时, 应重新进展MSA分析。
操作人员; 计量器具经修理、更换、调整后 ; 待检产品或检测工程转变后 ; 操作方法 ; 作业场所。
测量系统分析的方法
计量型测量系统:
双性分析: 对测量系统进展
重复性和再现性分析,计算出重复性、再
测量系统分析
Measurement Systems Analysis
根底学问培训
内容
术语 测量系统分析的目的、意义 实施测量系统分析的时期 测量系统分析的方法 测量系统分析的具体过程 结果分析
术语
测量系统: 用来对被测特性赋值的操作、程序、测量设备、
软件以及有关人员的集合;或者可以说用以猎取 测量结果〔数据〕的整个过程。
0396
GO/NOGO
●
3 50 组装B03
13 10A2指针高度确认具1.0-2.0mm测量系统
0397
GO/NOGO
●
3 50 组装B03
14 锡膏厚度检测仪测量系统
0449
R&R
○
3 10 SMT
15 磁通计测磁钢磁通量61±4MX
0078
R&R
○
3 10 组装B40
16 CC30钢球压入高度2.8±0.03测量系统
测量系统分析的方法
CYM量具族系表:
参考:AIAG测量系统分析手册
序号类别ຫໍສະໝຸດ 明细1游标卡尺
2
外径千分尺
3
百分表
4
千分表
5
高度游标卡尺
6
膜厚计
7
小测头千分尺
- 1、下载文档前请自行甄别文档内容的完整性,平台不提供额外的编辑、内容补充、找答案等附加服务。
- 2、"仅部分预览"的文档,不可在线预览部分如存在完整性等问题,可反馈申请退款(可完整预览的文档不适用该条件!)。
- 3、如文档侵犯您的权益,请联系客服反馈,我们会尽快为您处理(人工客服工作时间:9:00-18:30)。
量具R&R 研究(交叉):摘要:每次测量过程结果时都会发现某些变异。
产生这样的变异的变异源有两个:一是任何按照过程制造的部件都会存在差别,二是任何测量方法都不是完美无缺的?因此,重复测量同一部件不一定会产生同样的测量结果。
使用量具R&R 可以确定测量产生的变异性中哪一部分是由测量系统本身引起的。
测量系统变异性包括由量具本身和操作员之间的变异性引起的变异。
此方法适用于非破坏性试验。
当满足下列假定条件时它也可用于进行破坏性实验:(1)同一批内的所有部件都极为相似,以至于可以认为是同一种部件;(2)所有操作员都测量同一批部件。
可使用方差分析法、均值和R 法进行交叉量具R&R 研究。
其中使用均值和R法时计算更为简单,而方差分析法则更为准确。
在进行量具R&R 研究时,测量应按随机顺序进行,所选部件在可能的响应范围内提供了代表性样本,这一点非常重要。
1.1.1 数据说明选择了十个表示过程变异预期极差的部件。
由三名操作员按照随机顺序测量每个部件的厚度,每个部件测量两次。
1.1.2 方差分析法与均值-R 法的比较由于利用控制图进行计算比较简单,因而首先产生了均值-R 法。
但是,在某些方面方差分析法更为准确:(1)利用方差分析法可以研究操作员和部件之间会产生哪些交互作用,而均值-R 法却不同。
(2)利用方差分析法所用的方差分量对变异性进行的估计比使用均值-R 法的极差进行估计更准确。
1.1.3 量具R&R 的破坏性实验量具R&R 研究的主要目的之一是要查看同一个操作员或多个操作员对同一个部件的重复测量结果是否相似。
如果要进行破坏性实验,则无法进行重复测量。
要对破坏性测试应用Minitab 的量具R&R 研究,则需要假定某些部件“完全相同”,可视为同一个部件。
如果假定是合理的,则可将同一批产品中的部件当作同一个部件。
如果上述情形满足该条件,则可以根据部件具体的测试方法选择使用交叉量具R&R 研究或嵌套量具R&R 研究。
如果每个操作员都要对每批部件进行检验,则使用交叉量具R&R 研究比较适合。
如果仅由一名操作员检验每批部件,则可使用嵌套量具R&R 研究。
2. 方差分析法包含交互作用的双因子方差分析通过双因子方差分析(方差分析)可以知道两个不同水平的因子是否可产生不同的响应变量平均值。
双因子方差分析表中列出了以下产生变异性的变异源:(1)部件,它表示由于测量不同的部件而产生的变异性。
(2)操作员,它表示由于进行测量的操作员不同而产生的变异性。
(3)操作员*部件,它表示测量过程中由于操作员和部件的不同组合而产生的变异性。
如果操作员*部件项的p 值大于0.25,方差分析将在无交互作用项的情况下重新运行。
(4)误差或重复性,它表示在测量过程中不是由部件、操作员或者操作员与部件交互作用产生的变异性。
您希望看到每一种变异源对应的p 值是否低于所选的显著性水平。
这说明该变异源是导致产生测量变异性的主要原因。
对于部件数据而言,当显著性水平 a = 0.05 时,通过操作员p 值(P = 0.033) 可以知道导致厚度平均值产生显著差异的原因在于三位不同的测量操作员。
此处,由于P = 0.000 小于0.25,因此包括操作员*部件项。
在量具R&R 中将考虑操作员和部件之间的交互作用。
量具R&R 研究(交叉):方差分析法:包含交互作用的双因子方差分析表来源自由度SS MS F P部件9 2.05871 0.228745 39.7178 0.000操作员 2 0.04800 0.024000 4.1672 0.033部件* 操作员18 0.10367 0.005759 4.4588 0.000重复性30 0.03875 0.001292合计59 2.24913删除交互作用项选定的Alpha = 0.252.1.1 数据说明选择了十个表示过程变异预期极差的部件。
由三名操作员按照随机顺序测量每个部件的厚度,每个部件测量两次。
2.1.2 方差分析法与均值-R 法的比较由于利用控制图进行计算比较简单,因而首先产生了均值-R 法。
但是,在某些方面方差分析法更为准确:(1)利用方差分析法可以研究操作员和部件之间会产生哪些交互作用,而均值-R 法却不同。
(2)利用方差分析法所用的方差分量对变异性进行的估计比使用均值-R 法的极差进行估计更准确。
2.1.3 自由度计算通常,DF 用于测量计算每个SS 时可用的“独立”信息数量。
(1)合计= n - 1,其中n = 观测值总数(2)DF 部件= a -1,其中 a = 部件数目(3)DF 操作员= b - 1,其中b = 操作员人数(4)DF 操作员*部件= (a-1)*(b-1)(5)DF 重复性= n - (a*b)注DF 合计= DF 部件+ DF 操作员+ DF 操作员*部件+ DF 重复性2.1.4 F 统计量计算F 统计量用于确定不同水平的因子是否会导致响应变量的值发生变化。
(1)F 部件= MS 部件/ MS 操作员*部件(2)F 操作员= MS 操作员/ MS 操作员*部件(3)F 操作员*部件= MS操作员*部件/ MS 重复性其中,MS 表示每个因子的均方(MS)。
F 统计量越大,该因子在响应或测量变量的变异性中所起的作用就越大。
2.2 变异性量具R&R 输出结果显示按以下变异源分析总变异性的情况:合计量具R&R,它可分为- 重复性,这是指同一操作员多次测量同一部件时产生的测量变异性。
- 再现性(可进一步分为操作员和操作员*部件分量),这是指由不同操作员测量同一部件产生的测量变异性。
-部件之间,这是指由于测量不同的部件而产生的变异性。
理想的情况是重复性与再现性几乎不产生变异性,绝大部分变异性应该由部件之间(部件之间)的测量差异引起。
具体表现为:(1)重复性与再现性变异源只占非常低的%贡献。
(2)由部件之间变异源导致的变异性占较大的%贡献。
%贡献、%研究变异、%公差和%过程等列可提供极为重要的信息。
通过这些列可以看出某一特定变异源在引起某种变异性中所起的作用百分比。
通常,合计量具R&R 在研究变异中所占的百分比应该低于30%,最好是低于10%。
对于部件数据,合计量具R&R 在研究变异中所占的百分比为32.66%。
此时就需要采取纠正措施。
具体措施包括对操作员进行培训或者使用更好的量具。
如果输入的是过程公差、规格上限或下限或者历史标准差,那么%公差或%过程列将比%研究变异更为重要。
2.2.1方差分量来源方差分量贡献率合计量具R&R 0.0044375 10.67重复性0.0012917 3.10再现性0.0031458 7.56操作员0.0009120 2.19操作员*部件0.0022338 5.37部件间0.0371644 89.33合计变异0.0416019 100.00过程公差= 1历史标准差= 0.174757研究变异%研究变%公差%过程来源标准差(SD) (6 * SD) 异(%SV) (SV/Toler) (SV/Proc)合计量具R&R 0.066615 0.39969 32.66 39.97 38.12重复性0.035940 0.21564 17.62 21.56 20.57再现性0.056088 0.33653 27.50 33.65 32.09操作员0.030200 0.18120 14.81 18.12 17.28操作员*部件0.047263 0.28358 23.17 28.36 27.04部件间0.192781 1.15668 94.52 115.67 110.31合计变异0.203965 1.22379 100.00 122.38 116.712.2.2 可区分类别数该数字指过程当前能够区分的部件的不同类别数目。
合计量具R&R 越低,该数字就越高。
如果某个过程不能区分至少 5 种类型的部件,则该过程不合格。
对于部件数据,测量系统只能区分 4 种不同部件。
这需要进行一些改进。
可区分的类别数= 42.2.2.1 数据说明选择了十个表示过程变异预期极差的部件。
由三名操作员按照随机顺序测量每个部件的厚度,每个部件测量两次。
2.2.2.2 方差分析法与-R 法的比较由于利用控制图进行计算比较简单,因而首先产生了均值-R 法。
但是,在某些方面方差分析法更为准确:(1)利用方差分析法可以研究操作员和部件之间会产生哪些交互作用,而均值-R法却不同。
(2)利用方差分析法所用的方差分量对变异性进行的估计比使用均值-R 法的极差进行估计更准确。
2.2.2.3 测量系统辨别力测量系统辨别力是指检测测量特征的变化的能力。
如果某个测量系统的辨别力不充分,它将无法准确测量过程变异或无法对单个部件的特征值(例如平均值)进行量化。
下表为会话窗口输出中列出的可区分类别数表,通过它可帮助确定测量系统的测量能力。
可区分类别数可提供:1 有关一致与不一致方面的信息2 - 4 不区分的控制图粗略估计过程参数和能力指数5 个或更多控制图、过程参数和能力指数2.2.3 变异性量具R&R 输出结果显示按以下变异源分析总变异性的情况:合计量具R&R,它可分为- 重复性,这是指同一操作员多次测量同一部件时产生的测量变异性。
- 再现性,这是指不同操作员测量同一部件时产生的测量变异性。
部件之间,这是指由于测量不同的部件而产生的变异性。
理想的情况是重复性与再现性几乎不产生变异性,绝大部分变异性应该由部件之间(部件之间)的测量差异引起。
具体表现为:(1)重复性与再现性变异源只占非常低的%贡献。
(2)由部件之间变异源导致的变异性占较大的%贡献。
%贡献、%研究变异、%公差和%过程等列可提供极为重要的信息。
通过这些列可以看出某一特定变异源在引起某种变异性中所起的作用百分比。
通常,合计量具R&R 在研究变异中所占的百分比应该低于30%,最好是低于10%。
对于部件数据,合计量具R&R 在研究变异中所占的百分比为25.16%。
该测量系统应该是合格的。
如果输入的是过程公差、规格上限或下限或者历史标准差,那么%公差或%过程列将比%研究变异更为重要。
2.2.3.1方差分量来源方差分量贡献率合计量具R&R 0.0020839 6.33重复性0.0011549 3.51再现性0.0009291 2.82部件间0.0308271 93.67合计变异0.0329111 100.00过程公差= 1历史标准差= 0.174757研究变异%研究变%公差%过程来源标准差(SD) (6 * SD) 异(%SV) (SV/Toler) (SV/Proc)合计量具R&R 0.045650 0.27390 25.16 27.39 26.12重复性0.033983 0.20390 18.73 20.39 19.45再现性0.030481 0.18288 16.80 18.29 17.44部件间0.175577 1.05346 96.78 105.35 100.47合计变异0.181414 1.08848 100.00 108.85 103.812.2.3.2 可区分类别数该数字指过程当前能够区分的部件的不同类别数目。