陶瓷材料烧结工艺和性能测试实验指导书模板
材料显微结构与性能实验指导书(1)

yl [1 3 1 yb /100] 100%
六.思考题
1.测定粘土或坯料的收缩率的目的是什么? 2.影响粘土或坯料收缩率的因素是什么? 3.如何降低收缩率? 4.干燥过程和烧成过程为什么会收缩?其动力是什么?
实验三
一.实验目的
吸水率测试
1.掌握陶瓷吸水率的概念、测定原理和测定方法; 2.了解陶瓷吸水率与显微结构之间的关系。
五.实验记录与计算
1.记录表 表3 试样名称 试样处理 试样编号 900℃烧成样品 1250℃烧成样品 2.计算 吸水率按下式计算: a 干试样质量 m1 饱和试样质量 m2 测定人 吸水率测试记录表 日期
m2 m1 ×100% m1
(式 3-1)
六.思考题
1.所测试样的吸水率是多少? 2.影响试样吸水率的因素有哪些?
二.实验原理
陶瓷制品或多或少含有大小不同、形状不一的气孔。浸渍时能被液体填充的气孔或和大气相 通的气孔称为开口气孔;浸渍时不能被液体填充的气孔或和大气相通的气孔称为闭口气孔。陶瓷 体中所有开口气孔所吸收的水的质量与其干燥材料的质量之比值称为吸水率。测定陶瓷制品的吸 水率是评价其致密程度的依据,可以确定其烧结温度和烧结范围,从而制定烧成曲线。
二、实验原理
硬度是材料的表面层抵抗小尺寸物体所传递的压缩力而不变形的能力。通常矿物 的宏观硬度是按十级标准用莫氏硬度计确定。莫氏硬度中,每一种硬度高的矿物,都 能用其尖刻伤前面的矿物。但因为莫氏硬度的等级极不均衡,通常除用莫氏硬度测定 陶瓷釉面外,常用显微硬度汁测定陶瓷硬度。显微硬度试验是一种微观的静态试验方 法。最常见的显微硬度有维氏和壳(努)氏两种。 用显微硬度计测定维氏显微硬度就是用一台立式反光显微镜测出在一定负荷下 由金刚石锥体压头,压入被测物后所残留的压痕的对角线长度来求出被测物的硬度。 显微硬度计算公式,维氏硬度计中金刚石为正方形锥体,相对夹角 α=136º(±20 ´),其硬度为
陶瓷的烧制实验报告

一、实验目的本次实验旨在了解陶瓷的烧制过程,掌握陶瓷烧制的基本技术,熟悉陶瓷原料的选取、制备、成型、装饰及烧成等各个环节,提高对陶瓷工艺的认识和操作技能。
二、实验原理陶瓷烧制是将陶瓷原料在高温下烧结成瓷的过程。
在烧制过程中,原料中的矿物质发生一系列物理和化学变化,形成具有一定强度和美观性的陶瓷制品。
三、实验材料与仪器1. 实验材料:高岭土、石英、长石、粘土、釉料等。
2. 实验仪器:陶瓷球磨机、陶瓷拉坯机、陶瓷成型模具、陶瓷窑炉、高温电炉、陶瓷喷枪、陶瓷颜料等。
四、实验步骤1. 原料选取与制备(1)选取高岭土、石英、长石、粘土等原料。
(2)将原料进行球磨,使其达到一定的细度。
(3)将球磨后的原料混合均匀,制成陶瓷泥料。
2. 成型(1)将陶瓷泥料放入陶瓷拉坯机,通过旋转拉坯机,用手和拉坯工具将泥料拉成瓷坯。
(2)将瓷坯放入陶瓷成型模具中,使其成型。
3. 装饰(1)用陶瓷喷枪在瓷坯表面喷洒釉料。
(2)用陶瓷颜料在瓷坯表面进行绘画。
4. 烧成(1)将装饰好的瓷坯放入匣钵中。
(2)将匣钵放入陶瓷窑炉中,进行低温预热。
(3)逐渐提高窑炉温度,使瓷坯达到烧结温度。
(4)保持烧结温度一段时间,使瓷坯充分烧结。
(5)逐渐降低窑炉温度,使瓷坯缓慢冷却。
五、实验结果与分析1. 原料选取与制备实验中选取的高岭土、石英、长石、粘土等原料,经过球磨、混合后制成的陶瓷泥料,具有良好的可塑性。
2. 成型通过陶瓷拉坯机和成型模具,成功地将陶瓷泥料拉成瓷坯,并使其成型。
3. 装饰用陶瓷喷枪喷洒釉料,使瓷坯表面光滑;用陶瓷颜料进行绘画,使瓷坯更具艺术性。
4. 烧成在陶瓷窑炉中,瓷坯经过烧结和冷却过程,最终成为具有一定强度和美观性的陶瓷制品。
六、实验总结通过本次实验,我们对陶瓷的烧制过程有了较为全面的了解,掌握了陶瓷烧制的基本技术。
在实验过程中,我们体会到以下几点:1. 陶瓷原料的选取与制备对陶瓷制品的质量有重要影响。
2. 成型、装饰、烧成等环节对陶瓷制品的美观性和实用性至关重要。
实验八 烧结实验

陶瓷的烧结实验
一、实验目的
了解陶瓷烧结的基本知识
二、实验原理
烧结(也叫烧成)是指在高温作用下,坯体发生一系列物理化学变化,由松散状态逐渐致密化,且机械强度大大提高的过程。
在烧结过程中包括有机物的挥发、坯体内应力的消除、气孔率的减少;在烧结气氛作用下,粉末颗粒表面氧化物的还原、原子的扩散、粘性流动和塑性流动;烧结后期还可能出现二次再结晶过程和晶粒长大过程。
烧结过程主要分为三个过程见烧结过程图:
初期烧结颈形成阶段,通过形核、长大等原子迁移过程,颗粒间的原始接触点或面转变成晶粒结合,形成烧结颈;中间烧结颈长大阶段,原子向颗粒粘结面的大量迁移使烧结颈扩大,颗粒间距缩小,孔隙的结构变得光滑,形成连续的空隙网络;最终烧结阶段:烧结的最终阶段是一个很缓慢的过程,借助于体积扩散机制将发生孔隙的孤立、球化及收缩。
三、实验步骤
(一)、实验材料、设备
试条6条、镊子、耐火板、烧结电炉、三点弯曲强度测试仪
1、将试条做2000Mpa的等静压。
2、测量每条试条的长宽高。
3、将等静压后的试条放在耐火板上,推进硅钼棒炉中,然后,再关上电路门。
4、设计升温曲线20℃/min,30min,40℃/min,到1500℃后恒温,4h。
5、关炉后,样品随炉冷却到室温。
6、取出样品,测量烧结后样品的长宽高。
7、测量试条的三点弯曲强度。
四、实验结果
1、计算试条的线形收缩率。
2、计算试条的平均弯曲强度。
结构陶瓷材料实验指导书

结构陶瓷材料实验指导书编者:张宝林桂林理工大学材料化学教研室2009年9月实验结构陶瓷基本制备工艺一、目的意义1.学习结构陶瓷原料处理设备及工艺2. 了解结构陶瓷配方、混料设备及工艺3. 学会使用成型压机、模具、冷等静压工艺4.烧结实验,了解烧结设备使用及功能5.陶瓷研磨、抛光技术6. 光学显微镜观察方法,显微硬度测量、断裂韧性计算二、基本原理及实验步骤1.结构陶瓷原料处理2. 结构陶瓷配制混料工艺称量:由基本原料、烧结助剂、性能改进添加剂等组成,采用不同称量范围或精度电子天平称量不同重量范围的原料。
干混工艺:不添加液体于原料中,将干粉原料直接混合,适合混料要求低的情况,如埋粉、燃烧合成原料混合等或原料不能接触液体、不能烘干的情况。
湿混工艺:添加水或有机液体如乙醇于原料中,适合混料要求高的情况,如陶瓷烧结料。
3. 使用成型压机、模具、冷等静压工艺1)用软布蘸酒精擦拭模具,着重清洁与样品接触部位,最后组装好模具;2)首先计算成型素坯需要量(以素坯密度40%TD估计),称量样品,倒入模具,轻微晃动模具,或使用丝状物拨平物料;3)计算模具合适的压力,杜绝超压力压模具,及使样品分层现象;4)用称料纸将样品规则地包好,用薄膜塑料袋封装样品,前后套三层,注意尽量排除气体;5)置入等静压机中在100MPa下等静压进一步增加密度;6)将样品取出,除去包装纸,放入干燥器中待烧。
4.烧结实验,了解烧结设备使用及功能1)调节智能控制仪调节烧结温度;2)将样品置入坩埚中,放入马弗炉中;3)开启加热电源,烧结样品,记录实验参数(烧结样品,温度、时间,现象等);4)烧结结束,待炉子彻底冷却,方可取出样品,观察样品状态,测量样品密度,测量收缩率、失重。
5)样品密度测试方法:样品开水煮2小时以上;(一)测出浸重G3=吊兰+样品-吊兰(在水中)(二)湿重G2=布擦干样品表面水分后称重(三)干重G1=湿样品120度烘2小时以上,然后置于干燥器中至室温(2-3小时)(四)密度=G1/(G2-G3)(五)显孔隙率=(G2-G1)/(G2-G3)收缩率、失重测试:收缩率=[(烧结前样品长度-烧结后样品长度)/烧结前样品长度]⨯100%失重=[(烧结前样品重量-烧结后样品重量)/烧结前样品重量] ⨯100%5. 陶瓷研磨、抛光技术1)粗磨:在铁研磨盘上水磨,100目金刚砂2)细磨:在铁研磨盘上水磨,3000目金刚砂3)抛光:绸布上用金刚石研磨膏,甘油做润滑剂4)100倍光学显微镜下观察抛光效果典型的氮化硅陶瓷轴承球切面抛光图(100倍光学显微镜)6. 光学显微镜观察方法,显微硬度测量、断裂韧性计算1)显微硬度测量:维氏硬度测试是用对角面为136度金刚石四棱锥体作压头,在0.4903~9.807N; 9.807~490.3N的载荷作用下,压入陶瓷表面,保持10~20s后卸除载荷,材料表面便留下一个压痕,在显微镜下测量对角线的长度,计算得到维氏硬度(或称显微硬度)P为载荷,如10kg。
某陶瓷公司原料试烧检测作业指导书
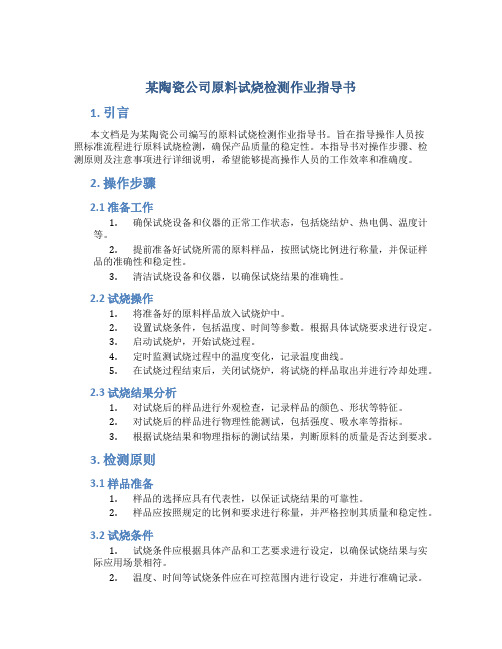
某陶瓷公司原料试烧检测作业指导书1. 引言本文档是为某陶瓷公司编写的原料试烧检测作业指导书。
旨在指导操作人员按照标准流程进行原料试烧检测,确保产品质量的稳定性。
本指导书对操作步骤、检测原则及注意事项进行详细说明,希望能够提高操作人员的工作效率和准确度。
2. 操作步骤2.1 准备工作1.确保试烧设备和仪器的正常工作状态,包括烧结炉、热电偶、温度计等。
2.提前准备好试烧所需的原料样品,按照试烧比例进行称量,并保证样品的准确性和稳定性。
3.清洁试烧设备和仪器,以确保试烧结果的准确性。
2.2 试烧操作1.将准备好的原料样品放入试烧炉中。
2.设置试烧条件,包括温度、时间等参数。
根据具体试烧要求进行设定。
3.启动试烧炉,开始试烧过程。
4.定时监测试烧过程中的温度变化,记录温度曲线。
5.在试烧过程结束后,关闭试烧炉,将试烧的样品取出并进行冷却处理。
2.3 试烧结果分析1.对试烧后的样品进行外观检查,记录样品的颜色、形状等特征。
2.对试烧后的样品进行物理性能测试,包括强度、吸水率等指标。
3.根据试烧结果和物理指标的测试结果,判断原料的质量是否达到要求。
3. 检测原则3.1 样品准备1.样品的选择应具有代表性,以保证试烧结果的可靠性。
2.样品应按照规定的比例和要求进行称量,并严格控制其质量和稳定性。
3.2 试烧条件1.试烧条件应根据具体产品和工艺要求进行设定,以确保试烧结果与实际应用场景相符。
2.温度、时间等试烧条件应在可控范围内进行设定,并进行准确记录。
3.3 检测指标1.外观检查应准确记录试烧后样品的颜色、形状等特征。
2.物理性能测试应根据产品要求进行选择,以保证产品的强度、吸水率等指标符合标准要求。
3.4 结果判断1.根据试烧结果和物理指标的测试结果进行综合判断,判断原料是否符合要求。
2.如有不达标情况,需要及时采取措施进行改进,以确保产品质量的稳定性。
4. 注意事项1.操作人员需要熟悉试烧设备和仪器的使用方法,以确保操作的准确性和安全性。
材料烧结实验报告

一、实验目的1. 了解材料烧结的基本原理和工艺过程;2. 掌握烧结实验的基本操作和数据处理方法;3. 熟悉烧结过程中的影响因素,为后续材料制备提供理论依据。
二、实验原理烧结是指将粉末材料加热到一定温度,使其颗粒表面熔融,通过冷却结晶和晶粒长大,使粉末材料转变为具有一定性能的致密材料的工艺过程。
烧结过程主要包括预热、烧结和冷却三个阶段。
三、实验材料与仪器1. 实验材料:金属粉末、陶瓷粉末等;2. 实验仪器:高温炉、电子天平、样品夹具、温度计、金相显微镜等。
四、实验方法1. 样品制备:将粉末材料按照一定比例混合均匀,压制成所需形状和尺寸的样品;2. 烧结:将样品放入高温炉中,按照预定温度和时间进行烧结;3. 冷却:烧结完成后,将样品从高温炉中取出,自然冷却至室温;4. 性能测试:对烧结后的样品进行力学性能、显微结构等性能测试。
五、实验步骤1. 样品制备:将金属粉末和陶瓷粉末按照一定比例混合均匀,压制成直径20mm、高10mm的圆柱形样品;2. 烧结:将样品放入高温炉中,以10℃/min的升温速率加热至1200℃,保温1小时,然后以10℃/min的降温速率冷却至室温;3. 性能测试:对烧结后的样品进行力学性能测试,包括抗拉强度、抗压强度和硬度测试;同时,利用金相显微镜观察样品的显微结构。
六、实验结果与分析1. 力学性能测试结果:抗拉强度:XX MPa;抗压强度:XX MPa;硬度:XX Hv。
2. 显微结构分析:通过金相显微镜观察,烧结后的样品表面光滑,内部组织致密,无明显气孔和裂纹。
3. 分析:(1)烧结温度对样品力学性能的影响:随着烧结温度的升高,样品的抗拉强度、抗压强度和硬度均有所提高。
这是由于高温下粉末颗粒表面熔融,使得晶粒生长更加充分,从而提高了材料的力学性能;(2)烧结时间对样品力学性能的影响:在一定范围内,烧结时间的延长有助于提高样品的力学性能。
这是由于烧结时间的延长使得晶粒生长更加充分,从而提高了材料的力学性能;(3)粉末材料配比对样品力学性能的影响:金属粉末和陶瓷粉末的配比对样品的力学性能有较大影响。
陶瓷材料烧结工艺和性能测试实验指导书模板
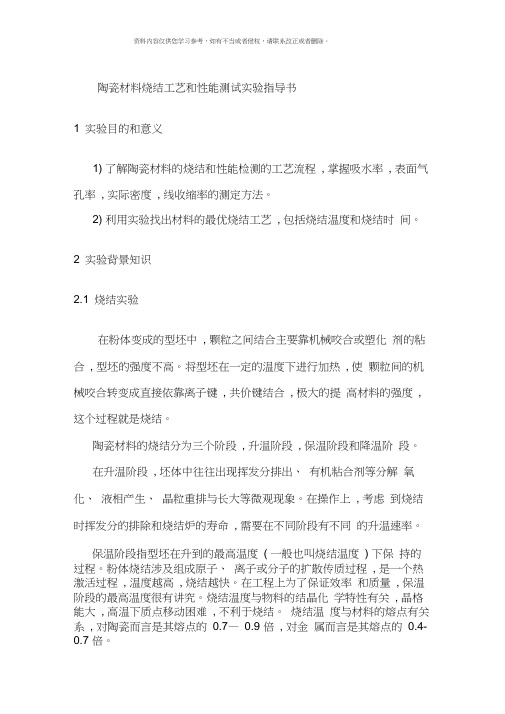
陶瓷材料烧结工艺和性能测试实验指导书1 实验目的和意义1) 了解陶瓷材料的烧结和性能检测的工艺流程, 掌握吸水率, 表面气孔率, 实际密度, 线收缩率的测定方法。
2) 利用实验找出材料的最优烧结工艺, 包括烧结温度和烧结时间。
2 实验背景知识2.1 烧结实验在粉体变成的型坯中, 颗粒之间结合主要靠机械咬合或塑化剂的粘合, 型坯的强度不高。
将型坯在一定的温度下进行加热, 使颗粒间的机械咬合转变成直接依靠离子键, 共价键结合, 极大的提高材料的强度, 这个过程就是烧结。
陶瓷材料的烧结分为三个阶段, 升温阶段, 保温阶段和降温阶段。
在升温阶段, 坯体中往往出现挥发分排出、有机粘合剂等分解氧化、液相产生、晶粒重排与长大等微观现象。
在操作上, 考虑到烧结时挥发分的排除和烧结炉的寿命, 需要在不同阶段有不同的升温速率。
保温阶段指型坯在升到的最高温度( 一般也叫烧结温度) 下保持的过程。
粉体烧结涉及组成原子、离子或分子的扩散传质过程, 是一个热激活过程, 温度越高, 烧结越快。
在工程上为了保证效率和质量, 保温阶段的最高温度很有讲究。
烧结温度与物料的结晶化学特性有关, 晶格能大, 高温下质点移动困难, 不利于烧结。
烧结温度与材料的熔点有关系, 对陶瓷而言是其熔点的0.7—0.9 倍, 对金属而言是其熔点的0.4-0.7 倍。
冷却阶段是陶瓷材料从最高温度到室温的过程, 冷却过程中伴随有液相凝固、析晶、相变等物理化学变化。
冷却方式、冷却速度快慢对陶瓷材料最终相的组成、结构和性能等都有很大的影响, 因此所有的烧结实验需要精心设计冷却工艺。
由于烧结的温度如果过高, 则可能出现材料颗粒尺寸大, 相变完全等严重影响材料性能的问题, 晶粒尺寸越大, 材料的韧性和强度就越差, 而这正是陶瓷材料的最大问题, 因此要提高陶瓷的韧性, 就必须降低晶粒的尺寸, 降低烧结温度和时间。
可是在烧结时, 如果烧结温度太低, 没有充分烧结, 材料颗粒间的结合不紧密, 颗粒间依然是靠机械力结合, 没有发生颗粒的重排, 原子的传递等过程, 那么材料就是不可用的。
实习报告:陶瓷烧结
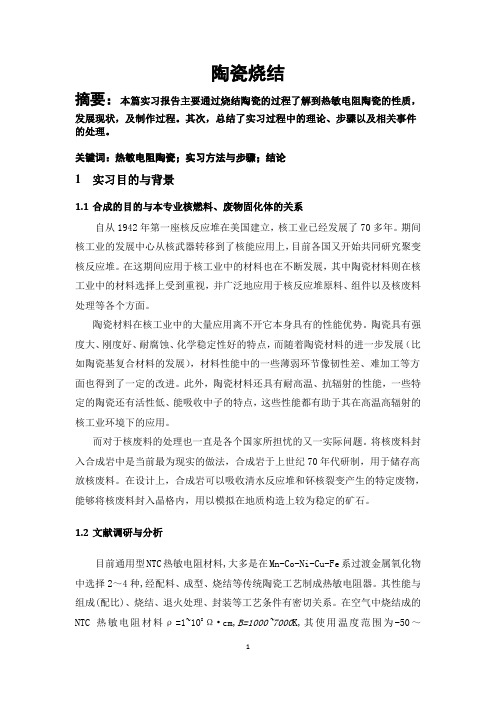
陶瓷烧结摘要:本篇实习报告主要通过烧结陶瓷的过程了解到热敏电阻陶瓷的性质,发展现状,及制作过程。
其次,总结了实习过程中的理论、步骤以及相关事件的处理。
关键词:热敏电阻陶瓷;实习方法与步骤;结论1 实习目的与背景1.1 合成的目的与本专业核燃料、废物固化体的关系自从1942年第一座核反应堆在美国建立,核工业已经发展了70多年。
期间核工业的发展中心从核武器转移到了核能应用上,目前各国又开始共同研究聚变核反应堆。
在这期间应用于核工业中的材料也在不断发展,其中陶瓷材料则在核工业中的材料选择上受到重视,并广泛地应用于核反应堆原料、组件以及核废料处理等各个方面。
陶瓷材料在核工业中的大量应用离不开它本身具有的性能优势。
陶瓷具有强度大、刚度好、耐腐蚀、化学稳定性好的特点,而随着陶瓷材料的进一步发展(比如陶瓷基复合材料的发展),材料性能中的一些薄弱环节像韧性差、难加工等方面也得到了一定的改进。
此外,陶瓷材料还具有耐高温、抗辐射的性能,一些特定的陶瓷还有活性低、能吸收中子的特点,这些性能都有助于其在高温高辐射的核工业环境下的应用。
而对于核废料的处理也一直是各个国家所担忧的又一实际问题。
将核废料封入合成岩中是当前最为现实的做法,合成岩于上世纪70年代研制,用于储存高放核废料。
在设计上,合成岩可以吸收清水反应堆和钚核裂变产生的特定废物,能够将核废料封入晶格内,用以模拟在地质构造上较为稳定的矿石。
1.2 文献调研与分析目前通用型NTC热敏电阻材料,大多是在Mn-Co-Ni-Cu-Fe系过渡金属氧化物中选择2~4种,经配料、成型、烧结等传统陶瓷工艺制成热敏电阻器。
其性能与组成(配比)、烧结、退火处理、封装等工艺条件有密切关系。
在空气中烧结成的NTC热敏电阻材料ρ=1~108Ω•cm,B=1000~7000K,其使用温度范围为-50~+300℃。
随着NTC热敏电阻器应用领域的扩大,对其性能的要求也日益提高。
就目前情形而言,对能在高温条件下使用的NTC元件,要求十分严格,例如在汽车发动机使用电子计算机控制系统后,为了限制尾气中有害气体的排放量(CO、NOx、CHx等有害气体),要求对排气口温度进行有效的测控。
- 1、下载文档前请自行甄别文档内容的完整性,平台不提供额外的编辑、内容补充、找答案等附加服务。
- 2、"仅部分预览"的文档,不可在线预览部分如存在完整性等问题,可反馈申请退款(可完整预览的文档不适用该条件!)。
- 3、如文档侵犯您的权益,请联系客服反馈,我们会尽快为您处理(人工客服工作时间:9:00-18:30)。
陶瓷材料烧结工艺和性能测试实验指导书
1实验目的和意义
1) 了解陶瓷材料的烧结和性能检测的工艺流程, 掌握吸水率, 表面气孔率, 实际密度, 线收缩率的测定方法。
2) 利用实验找出材料的最优烧结工艺, 包括烧结温度和烧结时间。
2 实验背景知识
2.1 烧结实验
在粉体变成的型坯中, 颗粒之间结合主要靠机械咬合或塑化剂的粘合, 型坯的强度不高。
将型坯在一定的温度下进行加热, 使颗粒间的机械咬合转变成直接依靠离子键, 共价键结合, 极大的提高材料的强度, 这个过程就是烧结。
陶瓷材料的烧结分为三个阶段, 升温阶段, 保温阶段和降温阶段。
在升温阶段, 坯体中往往出现挥发分排出、有机粘合剂等分解氧化、液相产生、晶粒重排与长大等微观现象。
在操作上, 考虑到烧结时挥发分的排除和烧结炉的寿命, 需要在不同阶段有不同的升温速率。
保温阶段指型坯在升到的最高温度( 一般也叫烧结温度) 下保
持的过程。
粉体烧结涉及组成原子、离子或分子的扩散传质过程, 是一个热激活过程, 温度越高, 烧结越快。
在工程上为了保证效率和质量, 保温阶段的最高温度很有讲究。
烧结温度与物料的结晶化学特性有关, 晶格能大, 高温下质点移动困难, 不利于烧结。
烧结温度与材料的熔点有关系, 对陶瓷而言是其熔点的0.7—0.9倍, 对金属而言是其熔点的0.4-0.7倍。
冷却阶段是陶瓷材料从最高温度到室温的过程, 冷却过程中伴随有液相凝固、析晶、相变等物理化学变化。
冷却方式、冷却速度快慢对陶瓷材料最终相的组成、结构和性能等都有很大的影响, 因此所有的烧结实验需要精心设计冷却工艺。
由于烧结的温度如果过高, 则可能出现材料颗粒尺寸大, 相变完全等严重影响材料性能的问题, 晶粒尺寸越大, 材料的韧性和强度就越差, 而这正是陶瓷材料的最大问题, 因此要提高陶瓷的韧性, 就必须降低晶粒的尺寸, 降低烧结温度和时间。
可是在烧结时, 如果烧结温度太低, 没有充分烧结, 材料颗粒间的结合不紧密, 颗粒间依然是靠机械力结合, 没有发生颗粒的重排, 原子的传递等过程, 那么材料就是不可用的。
2.2 性能检测
材料是否烧结良好, 需要一定的检测手段。
烧结的致密程度一般表现在密度是否高、材料内部的气孔的多少、表面的气孔多少和大小以及吸水能力的强弱。
在本实验中, 主要考察材料表面气孔
率、相对密度、吸水率以及线收缩率。
2.2.1 目测
很多的实验, 在烧结的过程中, 可能由于很多的原因而出现表面裂纹, 有些会出现表面的凹陷, 因此, 烧结后检测的第一步就是目测试样。
如果出现以上的问题, 则试样肯定是不合格的, 其它的实验能够不用做了。
目测的项目有是否出现表面裂纹、是否有变形现象, 是否表面出现凹陷或者突出。
2.2.2 密度测试
试样经110C°干燥之后之重量与试样总体积之比, 用g/cm3表示。
材料烧结好坏的一个重要方面就是密度是否接近理论密度。
在烧结过程中, 随着晶界的不断移动, 伴随着液相和固相传质的进行, 颗粒间的空隙会逐渐在表面消失, 其中会有些气孔保留, 大多数的气孔会逐渐缩小甚至消失。
达到良好烧结的标准就是气孔率小, 密度接近理论密度。
例如原料采用99%的氧化铝, 则理论密度为3.9g/cm3 (全部按照α-Al2O3来计算)。
2.2.3 线收缩率
在烧结后, 最直观, 最明显的变化就是尺寸的巨大收缩, 如果在变形量很小的情况下, 线收缩率越大, 说明样品烧结得越致密。
一般的收缩率有体积收缩率和线收缩率两种, 由于工具简便, 准确度较高, 因此线收缩率是比较常见的测试方法。
取几个比较具有代表性的尺寸( 对圆片状的样品来说, 取直径d和高度h) , 计算每一个尺寸的缩小尺寸和原尺寸的百分比, 然后平均。
2.2.4 表面气孔率
和密度相关的量, 如果气孔率越大, 则密度就越小。
而表面气孔率能够在很程度上反映材料的致密程度。
如表面有很多的开口气孔, 则材料的烧结就是不致密的。
其定义是一定表面的气孔的体积和材料的总体积的比, 用百分数来表示。
2.2.5 吸水率
吸水率——试样孔隙可吸收水的重量, 与试样经110C°干燥之后之重量之比, 用百分率表示。
和表面气孔率相似, 如果表面气孔越多, 吸取水的能力就越强。
和表面气孔率一起更加准确的表示材料的致密程度。
3 实验内容
3.1 烧结实验
实验仪器
烧结炉( 1300℃硅钼棒炉, 1600℃硅碳棒炉) 、精确度为0.01g
天平、承烧板若干、游标卡尺。
3.1.1原料的选用
原料有很多种, 各有不同的烧结温度, 有的材料中有掺杂, 则烧结温度又会发生变化。
制定一个合适的烧结温度, 首先要根据实际的材料, 查阅有关文献, 了解大致的温度范围, 然后制定合适的方案。
例如采用纯度为99%的氧化铝材料, 则烧结温度大约在1600℃。
则能够设计烧结温度为1500℃、1600℃、1700℃这三个温度。
如果在原料中有MgO, CaO这些帮助烧结的掺杂物, 则烧结温度能够适当降低。
如纯度为75%的氧化铝, 则烧结温度可能只有1200℃。
这种材料具有烧结温度低, 材料较致密, 一定温度下产生很多液相很容易促进烧结的优点。
一般来说, 材料选用能够有一定比较的选择。
比如选择氧化铝作为主要的原料, 则能够在其中掺杂CaO、MgO、SiO2等, 制成几种不同的原料的坯体, 考察原料的成分变化对于材料烧结性能的影响。
3.1.2 成型
烧结实验用的试样能够由各种成型方法制得。
在本实验室的其它实验中, 能够选择的方法有流延成型, 丝网印刷, 模压成型, 热压注成型四种。
除开模压成型, 其它成型方法均需要脱脂步骤。
将每一种不同原料配方的坯体根据方案制备一定数量( 比如有三个烧结温度, 则能够做12个左右的试样, 每一个温度有4个完全相同原料的试样) 。