标准范本-KAIZEN改善
NIKE KAIZEN REPORT(改善报告)
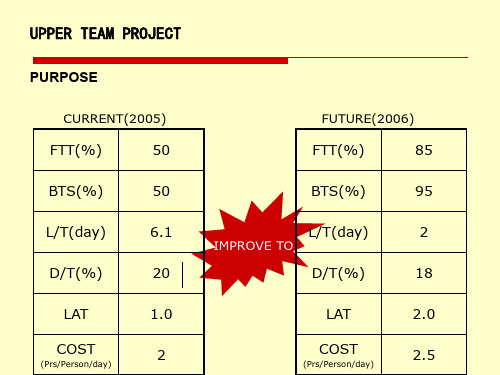
Schedule
Select the proper T/Ls&G/Ls for Value Stream Organization
Nov,2005 Set rules& Responsibilities /training
Dec,2005 Coaching in workshop
Jan,2006 Coaching in workshop
Schedule
No. 1 2 3 4 항목 시험운영 1차 정리보고 2차안 정리 본시행 준비 내용 파이롯트 라인(제조1반)에 대해서 시험 운영함 시험운영에 대한 결과 정리 및 문제점 공유 문제점에 대한 대책방안 강구 본실시를 위한 방안 강구 레이아웃 작성 및 이동 일정확정 인원 선정 및 인원교육, 배치 이동 작업 실시 일정 '~08월31일 9월 5일 9월5일~7일 '~9월10일
◎ 용진에 재단기를 전진 배치함으로써 보다 효율적인 물류 관리 시스템 구축 ◎ 공순 마무리에 보다 신속한 대응 가능 ◎ 자재 수령 후 자체 생산계획에 의해서 생산을 함으로써 공정간 재공재고 최소화 가능 ◎ 라우팅 단순화로 리더타임 감소 가능 (최소한 1일 리더타임 감소)
Upper Cell Lean Layout Change
Current Future
Purpose
bine stitching,cutting,HFW to become a Upper Cell Value Steam 2.Utilize kanban to change from push system to pull system 3. Daily based production paln change to hourly based plan 4. Set up standard WIP and build system
Kaizen Advisor kaizen format

改善前後平衡率對比
改善前 14 12 10 8 6 4 2 0 Assy1
有價時間 必要時間 浪費時間
4.72S Assy2
5.88S
Assy3 Assy4 Assy5
有價時間
Assy6
必要時間 浪費時間
改善后
14 12 10 8 6 4 2 0 Assy1 Assy2 Assy3 Assy4 Assy5
Kaizen Format
By: hua.zhao 2012/9/20
改善線狀況調查
生產機種:GES380W12V0481 目前產線線速:12S(有出現推拉狀況) 組長訴求:1.提升產能,達到300PCS/H設定標準 2.節省人力1人以上. 根據組長訴求設定改善目標:
改善前
人數 產出(PCS/H) Takt time 線體面積(㎡) 6 276 12 26
Assy6
根據改善後的平衡率可以看出,目前所有站別作業時間已經全部低於 takt time,第2站與第5站作業時間加起來低於takt time,且此兩站都分 別為獨立的製程,可以合併.
The end!
TKS!
鎖螺絲作業方式改善
Before After
自動供 料機台
問題: 行動: 鎖螺絲作業需要拿一顆螺絲,鎖一顆 改為自動供料式電鎖,無須取放螺絲,只 螺絲,存在動作浪費. 要將電鎖下壓就可以完成鎖附動作,節省
效益評估: 改善後鎖螺絲站別作業時間下降為5.88S,可以於改善後的焊散熱片站別合併,節省一 人
第五站 第六站 第六站
10月30日 節省 0.38S/PCS 節省 8月26日 1.74S/PCS 8月12日
CASE包装更改入料方式改善
Before After
Kaizen Format Kaizen格式改善格式
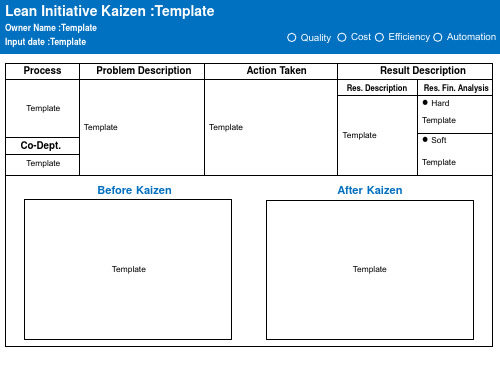
Template
Hard
Template
Template
Template
Template Soft Template
Co-Dept.
Template
Before Kaizen
After Kaizen
Template
Template
Action Taken
Result Description
Res. Description Res. Fin. Analysis
7、Black color, Arial font, 12 size, left Try to quantization your description 8、Black color, Arial font, 12 size, left Template Template Try to quantization your description 5、Black color, Arial font, 12 size, center Template Template
Lean Initiative Kaizen :Template
Owner Name :Template Input date :Template
Quality
Cost
Efficiency
Automation
Process
Problem Description
Action Taken
Result Description
Lean Initiative Kaizen :Template
Owner Name :Template Input date :Template
KAIZEN基本知识【范本模板】

持续改善(KAIZEN)—能让员工的生产力变得更高的战略如果你只学一个日语词,那么就学“KAlZEN"!KAlZEN “持续改善”的策略是日本管理部门中最重要的理念,KAlZEN是日本人竞争成功的关键,KAlZEN 意味着改进,KAIZEN 意味着涉及每一个人、每一环节等的连续不断的改进:从最高的管理部门、管理人员到工人。
Kaizen[改善]管理者论坛[ www.onlyit。
cn ] 收藏本站什么是Kaizen?释义Kaizen法最初是日本企业界的一个管理概念,用于渐进的、持续(增加)的变革或提高. Kaizen实际上是一种生活哲学。
它假设我们生活的方方面面都应该持续不断地得以改变和提高。
Kaizen哲学的背后包含着许多日本管理理念,如: Total Quality Control[全面质量控制]、品质圈、小组活动、劳资关系。
Kaizen哲学的关注要点是:质量、努力、全员投入、变革意愿、沟通。
日本公司相互区别之处就在于:是完完全全的创新,还是大刀阔斧的变革,还是通过Kaizen实现持续提高的变革. Kaizen的字面意义就是:通过改(Kai),而变好(Zen).Kaizen的五个基本要素1. 团队工作(Teamwork)2。
自律性(Personal Discipline)3。
高昂士气(Improved Morale)4. 质量圈(Quality Circles)5. 改良建议(Suggestions for Improvement)在此基础之上,Kaizen的三项核心要务•降低废料、排除低效。
•做好生厂区管理的5个S•1。
Seiri —整理•2。
Seiton - 整顿•3。
Seiso —清洁•4。
Seiketsu - 清扫• 5. Shitsuke - 修养•实现标准化.何时应用Kaizen法?尽管较难给出一个普遍适用的建议,但有一点是清楚的,Kaizen非常适用于需要长期过程的渐进变革,这种变革最好是在浓厚的集体主义环境下进行。
精益生产7.Kaizen_Training (改善)

Who execute Kaizen? 谁来执行改善?
• 一般情况下(80%),谁提出谁负责实施。(当然是在批准后) • 有些情况下(15%),需要部门主管协调其他员工实施。 • 最少状况下(5%),需要部门主管向上协调其他部门员工实施。
Normally, how long time to close a Kaizen? 一般多长时间关闭改善建议? • 《=3 个月
•
我可以写其他部门的Kaizen吗?
– 可以,但我们鼓励你先从自己的工作领域入手。如果写其他部门的Kaizen实施起 来需要的协调较多。所以还是鼓励写你的工作岗位或环境中的改善。
Questions 常见问题和回答
• • 我可以写过去已经发生或正在实施的Kaizen吗?
– 不可以,我们鼓励员工去想新的Kaizen。
某些Kaizen做起来容易,但审批程序造足够的判断力前必要的审批是为 了保证改善不会对质量、安全或其他方面产生意想不到的负面影响。 – 随着经验的积累,我们可审批的授权人将会逐步授权,例如,QA的审批可能会授 权给部门内某些经过充分培训过的主管或质量负责人等。
What’s Kaizen? 什么是改善?
• • • • “Kaizen”来自日文,就是改善的意思。 “Kaizen”最初来自于质量领域,目的是持续改进。它鼓励员工在自己的工作 领域不断改进和提高。 “Kaizen”是一种工具,用于快速解决简单的问题,主要解决那些原因已经很 明了且不需要数据分析的问题。 任何对安全、质量、生产效率/产量、设备稳定性、客户服务、成本、士气等 有帮助的合理化建议都是合格的改善建议。
– 判断是否属于变更控制范围,如果是,走变更控制。 – 判断是否需要其他专家评审,如生产技术,研发,EHS、电气工程师、产品专家 或外部专家等。
现场改善Kaizen Workshop001
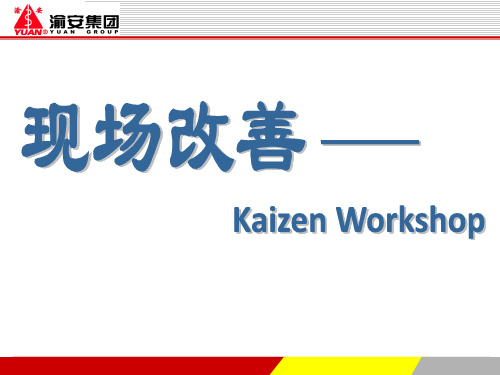
现场观察表(1)
目标:安全
编号 要素名称
基本安全措施 ·安全人 1.1 ·安全主题 ·区域责任制 ·疏散图
危险危害
1.2
·化学品 ·高风险作业
·安全隐患
人机工程
1.3
·灯光 ·负重
·疲劳
编号
目标:质量 要素名称
现场观察要素表
目标:效率
编号
要素名称
编号
目标:成本 要素名称
目标:组织发展 编号 要素名称
·数量
3.2 ·包装
·一物一位
·先进先出
生产计划与控制
3.3
·发布过程 ·发布载体
·变更
暗灯系统
3.4
·问题响应 ·停线数据
·问题交流报告
全员生产维修
·点检SOS
3.5 ·点检表
·预维修计划
·维修记录
成本分析与成本控制
4.1
·报废记录 ·劳保用品
·办公费用
5.1
宗旨 ·团队目标
工作平衡与工作分配 4.2 ·工作负荷量
现场改善日程
涂装车间面漆间现场改善活动日程
组织部门 精益生产办公室
活动时间 2005-11-28 至 2005-12-3
组长
冯彬
改善小组成员
改善区域 会议集中点
涂装车间面漆间 涂装车间办公室
杨北川、张涛、刘洪、卢传风、毛清华、廖志林、林杰
日期 时间
活动内容
方法/工具
AM 9:00-9:30 改善培训
改善材料
11 月 30 日 全天
改善小组成员完成各自负责的《问题清单》中的问题,问题 每天下午 5:00-5:
12 月 1 日 全天
清单责任人原则上是小组成员
(精品)改善Kaizen(免费版)

什么是改善 (Kaizen) ?
• 改善是关注于使用精益生产的工具来迅速地减少浪费以降低成本、 提高质量、缩短交货期、提高速度、增加弹性及快速响应内外部 客户的需求
• 改善关注递增变化, 是采用丰田生产系统来进行持续改进的工具 • 改善是通过全员参与推行“立刻行动” 的方法, 快速获得利益的
工具. (过程 X 接受能力 = 结果)
小组规则
• 保持一个准备变革的开放心态 • 保持一个积极的态度 • 从不僵持在无声的反对状态 • 创造一个无过失的环境 • 实行每天互相尊重 • 用希望别人对待自己的方式对待他人 • 一个人, 一个观点—没有好坏及排列 • 这儿没有愚蠢的问题 • 理解过程并执行它!
改善结果的取得
•# 操作员人数 / 天( 所有班次) •全面生产运转时间 •产量 ( 台数 / 天) •生产力 (台数 / 天/操作员) •在线库存量 •车间空间 •设置时间 •质量 ( # 拒收数量/天) •订户至交货时间 •安全 •人机工程
管理层 walk through
改善培训
1. 浏览6 Sigma 和 Lean 2. 精益生产系统 3. 操作规程标准 4. 标准操作工具 5. 5-S 6. 可视控制工具 7. 在线 Supermarket / 水蜘蛛 8. 减少设置时间 9. TBM
改善工具
• 事件通知函 • Takt Time 计算 • 时间观察表 • Takt Time/ Cycle Time Bar Cart • 流程图 ( Spaghetti Diagram) • 优化表 (采用收益VS. 支出矩阵) • 标准工作组合表 •标准工作分布 • 改善报纸 •改善执行 • 改善结果获得 • 改善30天跟踪
改善跟踪
• 确定第一周现场计划 • 在区域内执行跟踪表且每日监督 • 由小组组长或副组长每周向高层管理者汇报 • 进行30天的区域巡回 (小组组长和高层管理者) • 计划90天审核 (和财务及制造部门)
KAIZEN工作改善之道课件

达标是一种封闭式管理,只要求按标准、规定的去做就可以,容易束缚人的思维;改善是一种开放式管理,追求比现状更好 :成本更低、效率更高、质量更好、交货期更短,至于如何达到的方法没有规定,需要每个人贡献出自己的智慧 。
与达标思想不同,改善思想所强调的是越来越好,“标”固然重要,需要的“标”当然要去达到。但更重要的是持续不断的改善意识,追求更好的意识!
防错法的应用原理(一)
2. 保险原理 藉用二个以上的动作必需共同或依序执行才能完成工作。 (1) 藉“共同”动作必须同时执行来完成 例 :开银行保险箱时,须以顾客之钥匙与银行之钥匙, 同时插入钥匙孔,才能将保险箱打开。 例 :操作冲床之工作,为预防操作人员不小心被手夹 伤,所以设计一双手必须同时按操作钮下去,才能 执行工作。
2. 使作业不要技能与直觉 需要高度技能与直觉的作业,容易发生失误。 考虑冶具及工具,进行机械化,使新进人员或 支持人员也能做不出错的作业。
3. 使作业不会有危险 因不安全或不安定而会给人或产品带来危险 时,加以改善使之不会有危险。又,马虎行之 或勉强行之而发生危险时,设法装设无法马虎 或无法勉强的装置。
防错法的应用原理(三)
(5) 以“方向”控制的方式来完成 例 :超级市场内进口及出口之单向栏栅,只能进 不能出,只能出不能进。 (6) 以“电流”用量的方式来完成 例 :家庭的电源开关皆装置保险丝,用电过量 时,保险丝就熔断,造成断电。 (7) 以“温度”控制的方式来完成 例 :家庭内冷气机之温度控制,冷度够时,自动 停止,温度上升时,自动开启。 (8) 以“压力”控制的方式来完成 例 :厨房内之快锅内压力过大时,则“液压阀”就 开启,使锅内之压力外泻以免造成爆炸之危 机。
防错法的应用原理(十)
- 1、下载文档前请自行甄别文档内容的完整性,平台不提供额外的编辑、内容补充、找答案等附加服务。
- 2、"仅部分预览"的文档,不可在线预览部分如存在完整性等问题,可反馈申请退款(可完整预览的文档不适用该条件!)。
- 3、如文档侵犯您的权益,请联系客服反馈,我们会尽快为您处理(人工客服工作时间:9:00-18:30)。
人 物,人,机器 物,人,机器 人,机器,质量
人 人 质量 人 人 机器 人,物,机器 人,物,机器
识别和消除浪费的方法
头脑风暴
对照浪 费特征 寻找浪
费
问5个为 什么分析 根本原因
流程化标准化
改善效 果确认
找到对付消 除这些原因
的方法
展开改 良改善
❖ 识别浪费是改善的 基础!
❖ 任何工作的着眼点 都是消除浪费!
6、工序间的距离尽可能的短。
如何改善?
改善步骤:
和理想状态的差距
发现问题
付诸行动
想出对策
寻找改 善目标
不合理 测定
不合理原 因分析
Point
别忘了PDCA。
流程化 标准化
改善效 果确认
展开改 良改善
如何发现问题
➢ 从数据(准确的,详实的数据,ICQ) ➢ 从观察 ➢ 从汇报 ➢ 从抱怨 ➢ 从交谈 ➢ 从实际经历
ZEN善 更好
通过不断地改变(方法、手段等)让事情变得更好(更有
效率…)。
一系列小的改变的累积!
持续不断!!
持续改善! Continuous Improvement!
➢ 把地板打扫干净是不是改善?
把地板打扫干净不是改善,但是改进扫把的使用方法就是改 善。
➢ 把东西放回原位是不是改善?
把东西放回原位不是改善,但是改进放置东西的方式就是改 善。
需要清理的收集板
收集板
定位杆
➢ 改进前的做法
A. 将定位杆拆下,收集板散开
B. 将收集板逐一拿出
C. 清洗,晾干
D. 然后,需要5个人合作,将收集板放 入,并依次将定位杆穿入,因定位杆 及收集板都失去原位,所以张 民,一起研究改进方案
减少
使用削去一部分螺 纹的螺钉和螺母, 可以只拧四分之一 圈
改变
资料来源:Fujita-Kaizen Museum
其他例子-1
资料来源:Fujita-Kaizen Museum
其他例子-2
资料来源:Fujita-Kaizen Museum
其他例子-3
其他例子-3
资料来源:Fujita-Kaizen Museum
•重物搬运 •拖拽 •不安全动作
等
例:消灭搬运的浪费
多余搬运
原则
方法
布局的改善 车辆使用、转活规则
的完善
标准作业的制定
1、彻底消灭反复装车,卸车,倒车, 换车的作业。
2、各作业点必要的搬运工作必须以不 停机工作为原则。
3、所搬运的物料应该是立即可以使用 的状态。
4、定量搬运,避免数数。
5、现场尽可能不要存货(材料、 半成 品)。
12种浪费的特征
浪费种类
浪费特征
浪费对象
搬运 库存 过量生产 不当加工
等待 动作 不良品 人力资源 污染 能源 额外消耗 产品设计
重复装卸;搬运路途过长;忙碌的传送者 超出规定的库存量;原料变质过期;难以取得部件或原料 货物不能顺利流动;在制品的堆积;存储时间过长 操作员(编程员,设计员)的方法之间存在差异;标准加工和实际加工 之间存在差异;不能统计加工 操作员等待,物品等待,操作员照看设备和操作 眼、手、脚、物、身体动作 顾客投诉,返工,废品,检查 人员没有改善建议或建议没有得到重视,人员没有合适的工作 恶臭… 没加工时机器电灯开着,电脑显示器开着… 过大的工厂,过多的机器,过多的监督人员… 产品加工困难,使用困难
➢ 不一致,不协调 产能不均
如何改善?
消除
-废除 -中止 -移除
改
-简化
善
-集中
方
减少
-同步 -标准化
法
-异常处理
-整合
改变
-变更 -多样化 -交换
消除
需要马桶盖吗?
资料来源:the slide of Fujita Sensei
消除
巴黎 法兰克福
资料来源:the slide of Fujita Sensai
➢ 将气枪加一圆盘挡板 ➢ 各种工装夹具的制作使用
LTA 空气过滤器定期清理维护的改 进工作
➢ LTA 是为ANCA 及JUNKER机 ➢ LTA 3001 床过滤排出空气,去除油雾的一 类专用设备,它应用的是静电吸 附原理。 经过一段时间的使用, 在电离及收集板上会沉积一些 粉尘,所以需定期清理。
5 个为什么
找到根本原因 表面划痕 工件碰撞 没有合适的容器 缺乏改善精神 缺乏激励机制
表面划痕 工件碰撞 没有合适的容器 缺乏改善精神 缺乏激励机制
为什么要改善?
➢ 不足、勉强 设备不足、条件不够
➢ 浪费 换线,换型时间的浪费 辅助工时(搬运、等待)的浪费 最终发现不良的浪费 机械设备不良的浪费 。。。
➢ 大家集思广益,怎么做?
➢ 改进收集器的框架结构
去处一端面的 铆钉
如此,可自由拆卸一个端面,并使 定位杆位置保持不变,
收集板可从该侧端面拿出, 同样可按次序依次安装
改进前后比较
➢ 改进前 需要五人2.5小时做一个收集器
的维护 维护周期一个月
由于维护频繁,机床利用率相对 降低
➢ 改进后
仅需三人45分钟做一个收集器 的维护
❖ 所有不创造价值的 工作都是浪费!
例:发现动作浪费的着眼点
•上下、左右 •重复
•单手的持有 •拿取困难
•保持
•难操作
•持有更换 •放开的瞬间
•空行 •半步回返 •半步踏进 •站立等待 等
•上下、左右 •反转 •方向转换 •取放 等
•寻找 •选 •确认 •难看见
•瞄 •费劲 •烦
等
•回身 •弯腰 •伸背 •大的移动
由于清洗质量的提高,使维护周 期延长为两个月
由于降低了维护次数,相对提高 了机床的利用率
整顿 – 物品放置在方便使用的地方
改善前
改善后
• 桌子太宽 • 零件太远 • 零件水平放置,不容易看到和拿来到。
• 桌子变小了(省下2/3) • 零件靠近了,容易拿到。 • 零件倾斜放置,更容易看到和拿到。
KAIZEN 改善
改善的态度与能力
高
II
I
能力
III
IV
低
消极
态度
积极
何谓KAIZEN改善?
KAIZEN改善
改变 KAI改
ZEN善 更好
通过改变让事情变得更好(更有效率…)。
练习
➢ 把地板打扫干净是不是改善? ➢ 把东西放回原位是不是改善?
何谓KAIZEN改善?
KAIZEN改善
改变 KAI改
改善的目的
➢ 让事情变得更好,更有效率… 消除浪费 ➢ 改善可用于我们所要做的所有精益项目都是一种改善
减少准备时间 消除浪费
Set up time reduction
多余搬运 多余动作
12种浪费
多余库存
仓库
过度生产
停工待料 不良品
不当加工
热量和能源,废物和污染 人力资源,不必要额外消耗 产品设计不良