循环流化床锅炉热力计算
曾小强260吨时循环流化床锅炉设计-热力计算 OK汇总
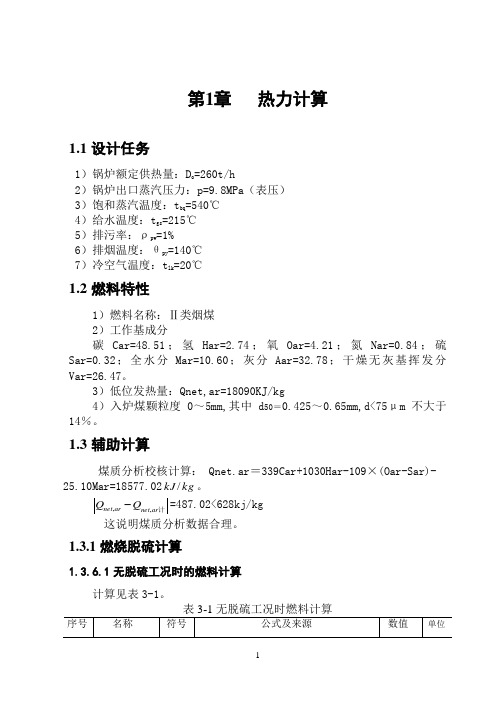
第1章 热力计算1.1 设计任务1)锅炉额定供热量:D o =260t/h2)锅炉出口蒸汽压力:p=9.8MPa (表压) 3)饱和蒸汽温度:t bq =540℃ 4)给水温度:t gs =215℃ 5)排污率:ρpw =1%6)排烟温度:θpy =140℃ 7)冷空气温度:t lk =20℃1.2 燃料特性1)燃料名称:Ⅱ类烟煤 2)工作基成分碳Car=48.51;氢Har=2.74;氧Oar=4.21;氮Nar=0.84;硫Sar=0.32;全水分Mar=10.60;灰分Aar=32.78;干燥无灰基挥发分Var=26.47。
3)低位发热量:Qnet,ar=18090KJ/kg4)入炉煤颗粒度0~5mm,其中d 50=0.425~0.65mm,d<75μm 不大于14%。
1.3 辅助计算煤质分析校核计算: Qnet.ar =339Car+1030Har-109×(Oar-Sar)-25.10Mar=18577.02kg kJ /。
计ar net ar net Q Q ,, =487.02<628kj/kg这说明煤质分析数据合理。
1.3.1 燃烧脱硫计算1.3.6.1 无脱硫工况时的燃料计算计算见表3-1。
1.3.6.2无脱硫工况时得烟气体积计算计算见表3-2。
1.3.6.3脱硫计算计算见表3-3。
1.3.2脱硫工况时燃烧产物平均特性计算1.3.6.1不同过量空气系数下燃烧产物的容积及成分不同过量空气系数下燃烧产物的容积及成分见表3-4。
1.3.6.2不同过量空气系数燃烧产物的焓温表不同过量空气系数下燃烧产物的焓温表见表3-5。
1.3.3锅炉热平衡及燃烧和石灰石消耗量计算锅炉热平衡及燃料的计算见表3-6。
表3-6锅炉热平衡及燃料和石灰石的计算1.4炉膛设计及热力计算1.4.1炉膛结构特性计算炉膛结构如图3-1所示。
炉膛结构计算见表3-7。
1.15.5炉膛膜式水冷壁计算受热面积图1-1.炉膛膜式水冷壁计算简图表3-7炉膛结构计算1.25.6炉膛汽冷屏计算受热面积炉膛汽冷屏受热面积计算如表3-8图1-2汽冷屏计算简图表3-8炉膛汽冷屏受热面积计算1.35.7汽冷旋风分离器计算受热面积汽冷旋风分离器受热面积计算如表3-9图1-3汽冷旋风分离器受热面积计算简图本设计中,旋风分离器汽冷壁是由135根φ38mm⨯5mm管子和鳍片组成1.3.1炉膛热力计算炉膛传热计算见表3-10。
循环流化床锅炉热力计算通用程序编制
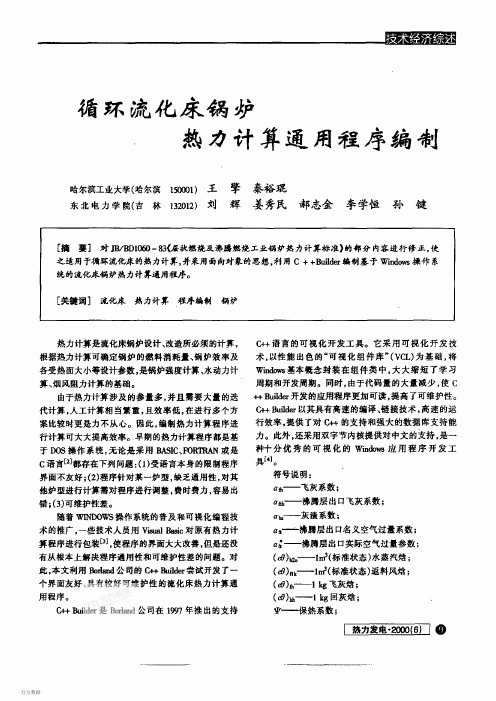
,(。0 。,・ 0 = )0a o' B_ a 1 A
10 0 1 0一 。 0 ,
0 1 0 0 田 1 0 + "c) K (6a 一c 10 4 a 一9 0
尹 ‘
勺 ‘
产 ‘1
将() 2做如下变换
l(a0 10一几 a '' 0 = C0 B1 )
出的工作 。
面向 对象的程序设计方法将数据和对数据的操作 放在一起, 作为一个相互依存、 不可分离的整体来处 理。它采用数据抽象和信息隐藏技术, 将对象及对象 的操作抽象成一种新的数据类型— 类, 并且考虑了 不同对象之间的联系和对象类的可重用性。 本程序采用面向对象的设计方法, 实现界面、 数据 和相应计算的有机结合, 例如: 建立类 ToNr Fr , 1 O 其成 员变量包括煤种的元素成分、 煤种的低位发热蚤及煤 种分类。成员函数包括空气盘、 烟气量、 烟气熔及锅炉 箱人热盆的 计算, 及保存数据文件及打印拾出, 对于旧 工程还包括读取数据文件。 将数据和与数据有关的 操 作放在一起, 实现了 数据封装。以窗体为分隔对象, 程 序各组成部分界面清晰, 便于检查和修改。
() 6
K — 循环倍率;
2 面向对象的程序设计思想
以往的热力计算程序是采用结构化的设计原则,
I 理论空气熔; t —
I 理 烟 治; 0 论 气 —
I I I - k计算嫩煤量产生的飞灰烩; g
程序设计人员采取自 上而下、 逐步求精的 设计方法[ 6 ]
采用这种方法, 可以把复杂的问题分解为不同层次的 具有不同功能的计算模块, 再把模块逐步分解为一系 列具体的处理步骤或高级语言的语句。首先将锅炉热 力计算划分为以下几个部分: () 1烟气特性计算; () 2锅炉热平衡计算; () 3辐射受热面( 膛) 炉 热力计算; () 4半辐射受热面( 后屏) 热力计算; () 5对流受热面热力计算。 然后逐步将 个部分展开。例如: 5 对() 对流受热面热力计算” 5部分“ 展开为 () 知烟气绪, 1已 计算烟气侧放热量; () 2计算对流放热系数; ( 计算辐射放热系数; 3 ) () 4计算温压; () 5计算传热系 数; () 6计算传热to 再进一步展开直到真体的语句。分析上述步骤, 可以发现, 上5 以 大部分中 有些计算内容是相同的, 如 已 知烟温求烟治, 计算对流放热系致, 辐射放热系数, 温压计算以及水和水燕汽参数计算, 因此可将其编制 成函数供使用时调用。每个函数的 设计也按自 上而下 的原则进行。 结 构化程序设计方法虽然有许多优点, 但它仍是
循环流化床锅炉炉膛热力计算

循环流化床锅炉炉膛热力计算引言循环流化床锅炉燃烧效率高,污染排放低,燃料适应性广,被广泛应用于蒸汽生产中。
随着循环流化床锅炉的发展,其容量和规模都在增大。
目前美国在建的300 MWe循环流化床锅炉即将投入运行,600 MWe容量的循环流化床锅炉也已在设计中。
利用国内技术生产的35 t/h、75 t/h循环流化床锅炉有大量运行,目前国内投入运行的最大循环流化床锅炉是高温高压420 t/h容量的锅炉,高温高压450 t/h循环流化床锅炉也已在建,但运用的是国外技术。
在循环流化床锅炉的开发与发展过程中,各设计单位和锅炉制造厂家开发出各种炉型,针对各自不同的炉型采用各自的热力计算方法,即使是相同的炉型设计方法也可能不同,各有特点。
这与煤粉锅炉和鼓泡流化床锅炉在设计过程中有统一的热力计算方法[1]可供参考不同。
有关循环流化床锅炉热力计算方法在文献中也少见发表。
本文结合作者在循环流化床锅炉传热和设计理论研究及实践的基础上,建立了一种简单的循环流化床锅炉炉膛热力计算方法[2-9]。
与一般沸腾燃烧鼓泡流化床锅炉不同,循环流化床锅炉类型较多,炉型不同,其热力计算方法有所不同。
本方法针对采用高温分离装置的循环流化床锅炉,提出的计算方法可用于一般高温分离的循环流化床锅炉的设计计算,其余炉型可在此基础上根据具体炉型特点修改使用。
典型的高温分离器型循环流化床锅炉采用高温立式旋风分离器,安置在锅炉炉膛上部烟气出口处。
离开炉膛的大部分颗粒,由高温分离器所捕集并通过固体物料再循环系统从靠近炉膛底部的物料回送口送回炉膛。
经高温分离器分离后的高温烟气则进入尾部烟道,与布置在尾部烟道中的受热面进行换热后排出。
计算中未考虑添加石灰石的影响,若添加石灰石,则入炉热量、灰浓度和烟气量等有变化,需修正。
2 循环流化床锅炉炉膛几何尺寸的确定2.1 炉膛横截面积循环流化床锅炉炉膛一般由膜式水冷璧构成,其传热面积以通过水冷璧管中心面的面积计算。
若炉膛由轻型炉墙或敷管炉墙构成,则需考虑角系数的影响。
清华大学热力计算

12稀相段水冷壁面积Hxx m2包括出口展开面积428.63 13分离器进口宽度B m#VALUE! 14分离器进口高度H m#VALUE! 15分离器进口面积Ac m2#VALUE! 16分离器进口涂层面积H m13.76 5 水冷屏结构计算
1水冷屏横向管排数zsl-0.00 2横向节距s1mm6830.00 3水冷屏管径d mm60.00 4水冷屏管厚度d mm 5.00 5水冷屏管节距s mm80.00 6鳍片厚度dd1mm 5.00 7水冷屏深度方向管数l12 8水冷屏高度12.00 9受热面积H m20.00 10屏区水冷壁涂层面积H m20.00 11水冷屏平均高度Hhh m12.35 6 分离器结构计算
1分离器数量n-2 2分离器直径D mm#VALUE!
3分离器前进口宽度b1mm#VALUE!
4分离器后进口宽度b2mm#VALUE!
5分离器进口高度a mm#VALUE!
6分离器上升速度V0m/s 5.65 7分离器竖直段高度h mm#VALUE!
8分离器总高度H mm#VALUE!
9分离器锥段高度b6mm#VALUE! 10分离器锥角a o18 11分离器锥段长度LBN mm#VALUE!。
330MW循环流化床锅炉热力计算表格程序

表1 表1 分离器占16% 包墙占16% 低过占16% 屏过、高过各占26% 表1 表1 低再、屏再各占50% 表1
计算 计算 计算 计算 计算 表28 计算 表29 表1 计算 表30 计算 表31 表1
0.23632 3.33688 5.62448 0.51755 是 是 否
结果
red —
Ared,ar %
Mred,ar %
Sred,ar %
—
—
—
—
—
—
符号 单位
P'sm MPa
Pgt
MPa
P''cyc MPa
P''bq MPa
P''dg MPa
P''pg MPa
P''gg MPa
P'dz MPa
P''dz MPa
P''pz MPa
Dsm
kg/s
Dpw
kg/s
Dcyc kg/s
bCaCO3(1-β fj/100)XCaCO3/100
0.07368 0.0463
0.00274
XzzbCaCO3
0.52349
Aar+ACaSO4+ACaO+Awfj +Azz
14.7662
bCaCO3Bj
7.38888
计算公式或数据来源 结 果
给定
7.38888
表1
94.39
给定
51.4758
kg/kg
kg/kg烟 气
8.510510383 8.51051 8.51051 0.009577767 0.00958 0.00958
CFB循环流化床锅炉效率计算公式

CFB循环流化床锅炉效率计算公式循环流化床锅炉是一种高效、低污染的锅炉,采用循环流化床燃烧技术,通过循环流化床锅炉效率计算公式可以评估锅炉的能源利用效率。
下面我们将详细介绍循环流化床锅炉效率计算的相关内容。
循环流化床锅炉的效率主要是指锅炉能够将燃料中的化学能转化为热能的比例,即锅炉的热效率。
具体而言,热效率是指燃料转化为热量后在循环流化床中通过传热辐射、传导和对流的方式传递给工质(水蒸汽)的比例。
循环流化床锅炉的效率计算公式可分为直接测定法和间接测定法两种。
直接测定法是通过测量锅炉的输入和输出参数,如燃料的热值、燃料的用量、工质的进口温度和出口温度等,计算得到锅炉的效率。
计算公式如下:η = (Q_output / Q_input) × 100%其中,η表示锅炉的效率,Q_output表示锅炉输出的热量,Q_input表示锅炉输入的燃料热量。
这种方法比较简单,但需要准确测量和监测各项参数。
间接测定法是通过锅炉运行过程中的参数数据推算得出锅炉效率的计算公式。
典型的间接测定方法有燃煤量法、燃烧空气量法和热损失法。
燃煤量法是通过测量燃煤的质量和热值,以及工质进口温度和出口温度等参数,计算锅炉效率。
计算公式如下:η = (Q_output / (m_coal × Q_coal)) × 100%其中,η表示锅炉的效率,Q_output表示锅炉输出的热量,m_coal 表示煤的质量,Q_coal表示煤的热值。
燃烧空气量法是通过测量燃料的用量以及燃烧过程中的空气过剩系数等参数,计算锅炉效率。
热损失法是通过测量锅炉的散热损失、烟气的含氧量、烟气温度等参数,计算锅炉效率。
需要注意的是,循环流化床锅炉存在多种热损失方式,包括炉内未完全燃烧、烟气中的水蒸汽、烟气的散热等。
因此,在实际计算循环流化床锅炉效率时,需要综合考虑这些热损失。
循环流化床锅炉效率的计算公式可以根据具体情况进行调整和修正,以提高计算结果的准确性。
循环流化床锅炉燃烧系统热力计算探讨

・电源建设・循环流化床锅炉燃烧系统热力计算探讨崔 敏(国电华北电力设计院工程有限公司,北京市,100011)[摘 要] CFB 锅炉有2大突出特点:一是流化状态燃烧;二是可燃烧劣质煤。
压力高是循环流化床风机的特点,压力高使风机温升高。
因此,风机温升和石灰石脱硫是CFB 锅炉燃烧系统热力计算的2个基本特点。
在对风机温升的计算公式进行推导后,结合考虑石灰石脱硫,产生2种热力计算方法,即混合燃料计算法和燃煤修正计算法。
根据推导的风机温升计算公式,将理论计算结果与风机生产厂提供的技术数据进行比较,两者误差较小。
并用2种计算方法对CFB 锅炉燃烧系统进行了热力计算。
[关键词] CFB 锅炉 燃烧系统 热力计算 风机温升 石灰石脱硫中图分类号:TK 212 文献标识码:A 文章编号:1000-7229(2002)09-0008-05Inquire into Thermal Calculation of Combustion System for CFB BoilersCui Min(SP North China Electric Power Design Engineering Limited Company ,Beijing ,100011)[K eyw ords] CFB boiler ;combustion system ;thermal calculation ;temperature rise of fans ;limestone desulfurization 目前,循环流化床(CFB )燃烧技术发展非常迅速,在国内得到了广泛的应用。
CFB 锅炉有2大突出特点:流化状态燃烧;燃料适应性好,能燃用泥煤、褐煤、低热值烟煤和煤矸石等劣质煤。
上述2个特点使得CFB 锅炉燃烧系统的热力计算与普通煤粉炉存在差异。
因此,有必要对CFB 锅炉燃烧系统热力计算进行探讨。
1 高压力风机对热力计算的影响1.1 CFB 锅炉风机压力的特点CFB 锅炉的燃烧特点是炉膛内的物料成流化状态燃烧。
第四章 循环流化床锅炉炉内传热计算讲解

第四章循环流化床锅炉炉内传热计算循环流化床锅炉炉膛中的传热是一个复杂的过程,传热系数的计算精度直接影响了受热面设计时的布置数量,从而影响锅炉的实际出力、蒸汽参数和燃烧温度。
正确计算燃烧室受热面传热系数是循环流化床锅炉设计的关键之一,也是区别于煤粉炉的重要方面。
随着循环流化床燃烧技术的日益成熟,有关循环流化床锅炉的炉膛传热计算思想和方法的研究也在迅速发展。
许多著名的循环流化床制造公司和研究部门在此方面也做了大量的工作,有的已经形成商业化产品使用的设计导则。
但由于技术保密的原因,目前国内外还没有公开的可以用于工程使用的循环流化床锅炉炉膛传热计算方法,因此对它的研究具有重要的学术价值和实践意义。
清华大学对CFB锅炉炉膛传热作了深入的研究,长江动力公司、华中理工大学、浙江大学等单位也对CFB锅炉炉膛中的传热过程进行了有益的探索。
根据已公开发表的文献报导,考虑工程上的方便和可行,本章根椐清华大学提出的方法,进一步分析整理,作为我们研究的基础。
为了了解CFB锅炉传热计算发展过程,也参看了巴苏的传热理论和计算方法,浙江大学和华中理工大学的传热计算与巴苏的相近似。
4.1 清华的传热理论及计算方法4.1.1 循环流化床传热分析CFB锅炉与煤粉锅炉的显著不同是CFB锅炉中的物料(包括煤灰、脱硫添加剂等)浓度C p 大大高于煤粉炉,而且炉内各处的浓度也不一样,它对炉内传热起着重要作用。
为此首先需要计算出炉膛出口处的物料浓度C p,此处浓度可由外循环倍率求出。
而炉膛不同高度的物料浓度则由内循环流率决定,它沿炉膛高度是逐渐变化的,底部高、上部低。
近壁区贴壁下降流的温度比中心区温度低的趋势,使边壁下降流减少了辐射换热系数;水平截面方向上的横向搅混形成良好的近壁区物料与中心区物料的质交换,同时近壁区与中心区的对流和辐射的热交换使截面方向的温度趋于一致,综合作用的结果近壁区物料向壁面的辐射加强,总辐射换热系数明显提高。
在计算水冷壁、双面水冷壁、屏式过热器和屏式再热器时需采用不同的计算式。
- 1、下载文档前请自行甄别文档内容的完整性,平台不提供额外的编辑、内容补充、找答案等附加服务。
- 2、"仅部分预览"的文档,不可在线预览部分如存在完整性等问题,可反馈申请退款(可完整预览的文档不适用该条件!)。
- 3、如文档侵犯您的权益,请联系客服反馈,我们会尽快为您处理(人工客服工作时间:9:00-18:30)。
循环流化床锅炉热力计算
循环流化床锅炉热效率计算
我公司75t/h循环流化床锅炉,型号为UG75/3.82-M35,它的热效率计算为:
三、锅炉在稳定状态下,相对于1Kg燃煤的热平衡方程式如下:
Q r=Q1+Q2+Q3+Q4+Q5+Q6 (KJ/Kg),相应的百分比热平衡方程式为:
100%=q1+q2+q3+q4+q5+q6 (%)
其中
1、Q r是伴随1Kg燃煤输入锅炉的总热量,KJ/Kg。
Q r= Q ar+h rm+h rs+Q wl
式中Q ar--燃煤的低位发热量,KJ/Kg;是输入锅炉中热量的主要来源。
Q ar=12127 KJ/KgJ
h rm--燃煤的物理显热量,KJ/Kg;燃煤温度一般低于30℃,这一项热量相对较小。
h rs--相对于1Kg燃煤的入炉石灰石的物理显热量,KJ/Kg;这一项热量相对更小。
Q wl--伴随1Kg燃煤输入锅炉的空气在炉外被加热的热量,KJ/Kg;如果一、二次风入口暖风器未投入,这一部分热量也可不计算在内。
2、Q1是锅炉的有效利用热量,KJ/Kg;在反平衡热效率计算中,是利用其它热损失来求出它的。
3、Q4是机械不完全燃烧热损失量,KJ/Kg。
Q4= Q cc(M hz C hz+M fh C fh+M dh C dh)/M coal
式中Q cc--灰渣中残余碳的发热量,为622 KJ/Kg。
M hz、M fh、M dh--分别为每小时锅炉冷渣器的排渣量、飞灰量和底灰量,分别为15、7、2t/h。
C hz、C fh、C dh--分别每小时锅炉冷渣器的排渣、飞灰和底灰中残余碳含量占冷渣器的排渣、飞灰和底灰量的质量百分比,按2.4%左右。
M coal--锅炉每小时的入炉煤量,为20.125t/h。
所以Q4= Q cc(M hz C hz+M fh C fh+M dh C dh)/M coal
=622(15*2.4+7*2+3.5*2.4)/20.125
=1694 KJ/Kg
q4= 100Q4/Q r(%)
=100*1694/12127=13.9%
4、Q2是排烟热损失量,KJ/Kg。
Q2=(H py-H lk)(1-q4/100)
式中H py--排烟焓值,由排烟温度θpy (135℃)、排烟处的过量空气系数αpy(αpy =21.0/(21.0 - O2py))=1.24和排烟容积比热容C py=1.33 (KJ/(Nm3℃))计算得出,KJ/Kg。
H py=αpy (V gy C gy+ V H2O C H2O)θpy+I fh 由于I fh比较小可忽略不计
=1.24*( 5.05*1.33+0.615*1.51) *135
=1229
H lk--入炉冷空气焓值,由排烟处的过量空气系数αpy、冷空气容积比热容C lk (1.31KJ/(Nm3℃))、冷空气的温度θlk (20℃)和理论空气量
V o(V o=0.0889(C ar+0.375 S ar)+0.265H ar-0.0333O ar, Nm3/ Kg)计算得出,KJ/Kg。
V o=0.0889(C ar+0.375 S ar)+0.265H ar-0.0333O ar,
=0.0889(42.97+0.375*0.34)+0.265*4.08-0.0333*9.63
=4.59
H lk= V o C kθlk
= 4.59 *1.31*20
=120
Q2=(H py-H lk)(1-q4/100)
=(1229-120)(1-13.9/100)
=953.74
q2=100Q2/Q r(%)
=100*953.74/12127
=7.86%
5、Q3是化学不完全燃烧热损失量,KJ/Kg。
Q3=236(C ar+0.375S ar)(M co/28)/(M so2/64+M nox/46)(1- q4/100)
=236(42.97+0.375*0.34)(5.6/28)/(619.8/64+656.6/46)(1-15.6%)=71.36
式中M co、M so2、M nox--分别为排烟烟气中CO、SO2、NO X所含的质量,mg/ Nm3。
分别为:5.6、619.8、656.6
q3=100Q3/Q r(%)
=100*71.36/12127
=0.58%
6、Q5是锅炉散热损失量,KJ/Kg。
q5=(0.28*75.0)/H %
=(0.28*75)/64.4
=0.32
式中H--锅炉的实际运行时的蒸发量,t/h。
7、Q6是锅炉的灰渣物理热损失量,KJ/Kg。
Q6=(H hz M hz*100/(100-C hz)+H fh M fh*100/(100-C fh)+ H dh M dh*100/(100-C dh)) / M coal
=(608*15*100/(100-2.4)+77*7*100/(100-2.4)+608*2*100/(100-2.4))/20.125
=553.7
式中H hz、H fh、H dh--分别为锅炉冷渣器的排渣、飞灰和底灰的焓值,KJ/Kg,,由各自对应的平均比热容c h (1.185、1.0048),温度900℃、65℃计算得出,分别为:H hz=A ar a hz c hzθhz
=0.5703*1.185*900=608 KJ/Kg
H fh=A ar a fh c fhθfh
=0.5703*1.0048*135=77KJ/Kg
q6=100Q6/Q r(%)
=100*553.7/12127=4.56%
8、η是锅炉的反平衡热效率,%。
η=100-(q2+q3+q4+q5+q6)
4、理论耗标煤量计算
B=100/ηQr*[D gr(h″gr-h gs)+D pw(h pw-h gs)]
=100/(72.78*29310)*[64.4(3297-440)+1*(1042-440)]
=8.65t/h
为了降低各项热损失指标,提高锅炉热效率,建议做如下改进:1、根据循环流化床锅炉的燃烧机理,一定要保证床内物料的充分流化。
最主要的两方面就是,首先要保证稳定的床压波动范围,根据入炉煤质的变化,及时投入相应数量的冷渣器,避免床压上升过高;同时在床压下降到较低时,也要及时停运冷渣器进行吹扫。
其次要保证一次流化风量大于最小流化风量,并根据床温情况,适当加大。
只有保证
了床内物料的充分流化,才能避免发生床内局部结焦、床温偏差大和局部产生流化死区等不良现象,使入炉煤在炉膛得到充分的燃烧,以此减少锅炉冷渣器排渣中残余碳的质量含量C hz,降低机械不完全燃烧热损失。
2、对冷渣器的投入运行要足够重视。
一方面,冷渣器能够控制炉膛床压;另一方面,要控制冷渣器的运行参数,降低排渣温度,以此减少灰渣物理热损失。
3、对炉膛内一、二次风的配比做进一步调整。
一次流化风在保证物料充分流化的同时,也要保证炉膛密相区有一定的燃烧份额,使密相区的实际过量空气系数接近1,在欠氧燃烧状态。
二次风从炉膛密相区和稀相区的分界处进入,根据O2%控制燃烧所需的总风量,保证细颗粒在稀相区的充分燃烧。
另外,一、二次风共同作用,保证物料在炉内的循环倍率,提高细颗粒再燃烧的机率,降低飞灰中的残余碳含量
C fh,进一步减少机械不完全燃烧热损失。
4、加强对锅炉外部保温材料的完善,发现缺陷及时检修,减少锅炉的散热损失。