管壳式换热器传热机理
壳管式换热器传热系数
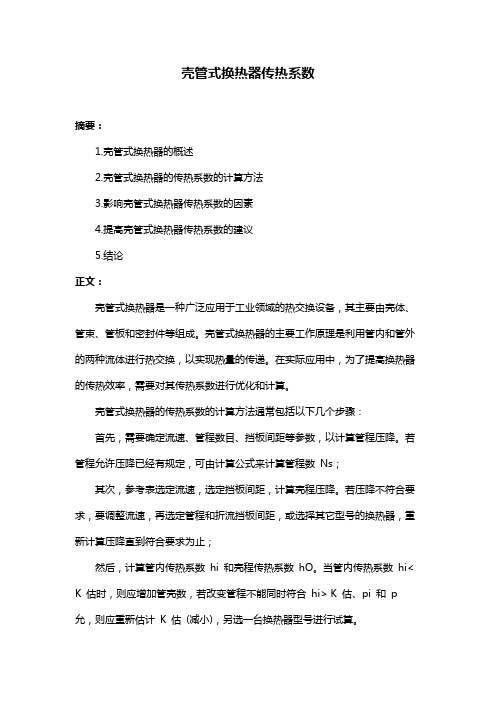
壳管式换热器传热系数摘要:1.壳管式换热器的概述2.壳管式换热器的传热系数的计算方法3.影响壳管式换热器传热系数的因素4.提高壳管式换热器传热系数的建议5.结论正文:壳管式换热器是一种广泛应用于工业领域的热交换设备,其主要由壳体、管束、管板和密封件等组成。
壳管式换热器的主要工作原理是利用管内和管外的两种流体进行热交换,以实现热量的传递。
在实际应用中,为了提高换热器的传热效率,需要对其传热系数进行优化和计算。
壳管式换热器的传热系数的计算方法通常包括以下几个步骤:首先,需要确定流速、管程数目、挡板间距等参数,以计算管程压降。
若管程允许压降已经有规定,可由计算公式来计算管程数Ns;其次,参考表选定流速,选定挡板间距,计算壳程压降。
若压降不符合要求,要调整流速,再选定管程和折流挡板间距,或选择其它型号的换热器,重新计算压降直到符合要求为止;然后,计算管内传热系数hi 和壳程传热系数hO。
当管内传热系数hi< K 估时,则应增加管壳数,若改变管程不能同时符合hi> K 估、pi 和p 允,则应重新估计K 估(减小),另选一台换热器型号进行试算。
影响壳管式换热器传热系数的因素有很多,主要包括以下几点:1.流体的性质:不同的流体具有不同的热传导性能,因此流体的性质对传热系数有很大影响。
2.流速:流速越大,传热系数越大,但流速过高会增加压力损失,影响换热器的工作效率。
3.管径和管间距:管径和管间距的增大会降低传热系数,因此需要根据实际工况选择合适的管径和管间距。
4.换热器的结构:换热器的结构设计直接影响传热系数,如管束的排列方式、管壁的厚度等。
为了提高壳管式换热器的传热系数,可以采取以下措施:1.优化换热器的结构设计,提高管壁的导热性能。
2.选择合适的流速和管程数目,以降低压力损失。
3.调整挡板间距,以增加壳程传热系数。
4.选择具有高传热性能的材料制作换热器。
总之,壳管式换热器的传热系数受多种因素影响,需要根据实际工况进行优化和计算。
管壳式换热器工作原理

管壳式换热器工作原理
管壳式换热器是一种常见的热交换设备,广泛应用于化工、电力、石油、冶金等工业领域。
它通过管壳两侧流体的热量传递,实现了热能的高效利用。
下面我们将详细介绍管壳式换热器的工作原理。
首先,管壳式换热器由壳体、管束、管板、管箱、管支撑、法兰、密封件等部件组成。
工作时,热源流体通过换热器的壳侧流动,被传热管束中的传热介质吸收热量,而冷却介质则通过管束内部流动,从而实现热量的传递。
其次,管壳式换热器的工作原理主要包括传热、流体运动和传热管束结构。
在传热过程中,热源流体和冷却介质在管束内外形成对流传热,同时通过管壁实现了传导传热。
流体的运动状态对传热效果也有着重要影响,合理的流体速度和流动方式能够提高传热效率。
此外,传热管束的结构设计也是影响换热器工作效果的重要因素,合理的管束布局和管子材质选择都能够影响传热效果。
最后,管壳式换热器在工作中需要注意一些问题。
首先是流体的流动状态,要保证流体在换热器内部的均匀分布,避免出现死角和局部过热。
其次是管束的清洁和维护,定期清洗管束表面的污垢,保持传热管的清洁度,以确保换热器的正常工作。
最后是对换热器的运行参数进行监测和调整,根据实际工况对换热器的进出口温度、压力等参数进行调整,以保证换热器的高效运行。
总之,管壳式换热器通过管束内外流体的热量传递,实现了热能的高效利用。
在工作中,合理的结构设计和运行参数调整都能够提高换热器的工作效率。
希望本文能够对大家对管壳式换热器的工作原理有所帮助。
管壳式换热器的工作原理及结构
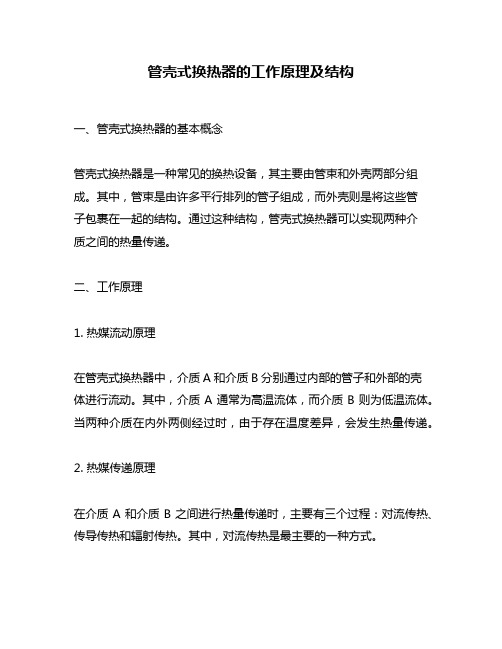
管壳式换热器的工作原理及结构一、管壳式换热器的基本概念管壳式换热器是一种常见的换热设备,其主要由管束和外壳两部分组成。
其中,管束是由许多平行排列的管子组成,而外壳则是将这些管子包裹在一起的结构。
通过这种结构,管壳式换热器可以实现两种介质之间的热量传递。
二、工作原理1. 热媒流动原理在管壳式换热器中,介质A和介质B分别通过内部的管子和外部的壳体进行流动。
其中,介质A通常为高温流体,而介质B则为低温流体。
当两种介质在内外两侧经过时,由于存在温度差异,会发生热量传递。
2. 热媒传递原理在介质A和介质B之间进行热量传递时,主要有三个过程:对流传热、传导传热和辐射传热。
其中,对流传热是最主要的一种方式。
3. 工作过程在工作过程中,高温流体通过内部的管子进入到换热器中,并沿着管子表面流动。
同时,低温流体从外部的壳体进入到换热器中,并沿着管子外表面流动。
在这个过程中,高温流体和低温流体之间进行了热量传递,使得高温流体的温度降低,而低温流体的温度升高。
三、结构特点1. 管束结构管束是管壳式换热器的主要组成部分之一。
在管束中,许多平行排列的管子被固定在两个端盖板上,并通过密封垫圈与外壳连接。
由于管子间距离较小,因此可以有效地增加热量传递面积。
2. 壳体结构外壳是管壳式换热器的另一个重要组成部分。
它通常由两个半球形或长方形壳体组成,并通过法兰连接。
在使用过程中,外壳起到保护内部管束不受损坏的作用。
3. 密封结构为了保证介质A和介质B之间不发生混合,在管壳式换热器中需要设置密封结构。
这种密封结构通常采用密封垫圈或波纹垫片等材料制成,可以有效地防止介质泄漏。
4. 清洗结构由于管壳式换热器在使用过程中会产生一定的污垢和腐蚀物,因此需要定期进行清洗。
为了方便清洗,管壳式换热器通常设置有进出口和排污口等结构。
四、应用领域管壳式换热器广泛应用于化工、石油、制药、食品等领域中。
在这些领域中,管壳式换热器可以实现高效的热量传递,提高生产效率,并减少能源消耗。
十三种类型换热器结构原理及特点(图文并茂)

十三种类型换热器结构原理及特点(图文并茂)一、板式换热器的构造原理、特点:板式换热器由高效传热波纹板片及框架组成。
板片由螺栓夹紧在固定压紧板及活动压紧板之间,在换热器内部就构成了许多流道,板与板之间用橡胶密封。
压紧板上有本设备与外部连接的接管。
板片用优质耐腐蚀金属薄板压制而成,四角冲有供介质进出的角孔,上下有挂孔。
人字形波纹能增加对流体的扰动,使流体在低速下能达到湍流状态,获得高的传热效果。
并采用特殊结构,保证两种流体介质不会串漏。
板式换热器结构图二、螺旋板式换热器的构造原理、特点:螺旋板式换热器是一种高效换热器设备,适用汽-汽、汽-液、液-液,对液传热。
它适用于化学、石油、溶剂、医药、食品、轻工、纺织、冶金、轧钢、焦化等行业。
结构形式可分为不可拆式(Ⅰ型)螺旋板式及可拆式(Ⅱ型、Ⅲ型)螺旋板式换热器。
螺旋板式换热器结构图三、列管式换热器的构造原理、特点:列管式换热器(又名列管式冷凝器),按材质分为碳钢列管式换热器,不锈钢列管式换热器和碳钢与不锈钢混合列管式换热器三种,按形式分为固定管板式、浮头式、U型管式换热器,按结构分为单管程、双管程和多管程,传热面积1~500m2,可根据用户需要定制。
列管式换热器结构图四、管壳式换热器的构造原理、特点:管壳式换热器是进行热交换操作的通用工艺设备。
广泛应用于化工、石油、石油化工、电力、轻工、冶金、原子能、造船、航空、供热等工业部门中。
特别是在石油炼制和化学加工装置中,占有极其重要的地位。
换热器的型式。
管壳式换热器结构图五、容积式换热器的构造原理、特点:钢衬铜热交换器比不锈钢热交换器经济,并且技术上有保证。
它利用了钢的强度和铜的耐腐蚀性,即保证热交换器能承受一定工作压力,又使热交换器出水质量好。
钢壳内衬铜的厚度一般为1.0mm。
钢衬铜热交换器必须防止在罐内形成部分真空,因此产品出厂时均设有防真空阀。
此阀除非定期检修是绝对不能取消的。
部分真空的形成原因可能是排出不当,低水位时从热交换器,或者排水系统不良。
换热器工作原理

换热器工作原理换热器是一种用于传递热量的设备,它能够将热量从一个流体传递到另一个流体,实现热能的高效利用。
换热器广泛应用于工业生产、能源系统、航空航天等领域,在提高能源利用率和节能减排方面起到重要作用。
本文将详细介绍换热器的工作原理,以及常见的换热器类型和应用。
1. 工作原理换热器的工作原理基于热传导和对流传热的基本原理。
当两个流体在换热器内部流经相邻的管道时,通过管壁的传热,使得热量从一个流体传递到另一个流体。
换热器的设计目的是最大限度地增加传热面积和热传导效率,以实现高效的热量传递。
2. 换热器类型根据换热过程中流体的流动方式和传热方式的不同,换热器可以分为多种类型,包括:(1) 管壳式换热器:管壳式换热器是最常见的一种换热器类型。
它由一个外壳和多个内部管子组成。
热传导通过管壁进行,流体在管内外分别流动,实现热量的传递。
(2) 板式换热器:板式换热器由多个平行排列的金属板组成,板间形成多个流体通道。
热量通过板间的传热表面进行传递,流体在板间交替流动。
(3) 管束式换热器:管束式换热器由多个小管子束缚在一个大管壳内,形成多个流体通道。
热量通过小管子的传热表面进行传递,流体在管内外分别流动。
(4) 螺旋板式换热器:螺旋板式换热器由两个螺旋形的金属板组成,形成多个螺旋通道。
热量通过螺旋通道的传热表面进行传递,流体在通道内旋转流动。
(5) 气冷式换热器:气冷式换热器主要用于冷却气体。
它通过气体与冷却介质的对流传热,将气体的热量散发到周围环境中。
3. 换热器应用换热器广泛应用于各个领域,包括工业生产、能源系统和航空航天等。
以下是一些常见的应用示例:(1) 工业生产:在化工、石油、制药等行业中,换热器被用于加热、冷却、蒸发、浓缩等过程,实现能源的高效利用和产品质量的提高。
(2) 能源系统:在火力发电、核电站、太阳能和风能发电等能源系统中,换热器用于热能的回收和利用,提高能源利用效率。
(3) 航空航天:在航空航天领域,换热器被用于飞机发动机的冷却、燃气轮机的热回收等应用,确保设备的正常运行和性能的提升。
管壳式换热器壳侧气液两相流动和传热的数值模拟研究

管壳式换热器壳侧气液两相流动和传热的数值模拟研究一、本文概述本文旨在通过数值模拟的方法,深入研究管壳式换热器壳侧气液两相流动和传热的过程。
管壳式换热器作为一种常见的热交换设备,广泛应用于化工、能源、环保等多个领域。
在实际应用中,壳侧气液两相流动和传热过程的复杂性往往导致设计优化和运行控制的困难。
本文的研究对于提高管壳式换热器的性能,提升工业生产效率具有重要的理论和实践价值。
在数值模拟研究中,我们将首先建立管壳式换热器的数学模型,考虑壳侧气液两相流动的流动特性、传热过程、相间作用等因素,利用计算流体力学(CFD)等先进方法,进行求解和模拟。
通过对比实验结果,验证数学模型的准确性和可靠性。
在此基础上,我们将对管壳式换热器壳侧气液两相流动和传热过程进行深入分析,探讨不同操作条件、结构参数对流动和传热性能的影响,揭示其中的流动和传热机理。
同时,我们还将探索优化设计方案,提高换热器的传热效率和稳定性,为实际工业应用提供有益的参考和指导。
本文将通过数值模拟的方法,全面研究管壳式换热器壳侧气液两相流动和传热的过程,为换热器的设计优化和运行控制提供理论支持和实践指导。
二、管壳式换热器的结构与工作原理管壳式换热器是一种常见的热交换设备,广泛应用于化工、石油、能源、制冷等工业领域。
其基本结构由管束、壳体和管板等几部分组成。
管束由多根管子平行排列组成,管子内部为流体通道,用于传递热量。
壳体则包围在管束外部,形成一个封闭的空间,壳体内也有流体流动,与管内的流体进行热量交换。
管板则起到固定管束和密封的作用,同时也作为流体进出口的连接部分。
管壳式换热器的工作原理基于热传导和对流传热两种基本传热方式。
当两种不同温度的流体分别流过管内和管外时,由于温度差异,热量会从高温流体传递到低温流体。
管内流体通过对流传热将热量传递给管壁,然后通过热传导方式将热量传递给管外流体,最终实现两种流体之间的热量交换。
在管壳式换热器中,流体的流动状态对传热效果有重要影响。
管壳式换热器结构设计
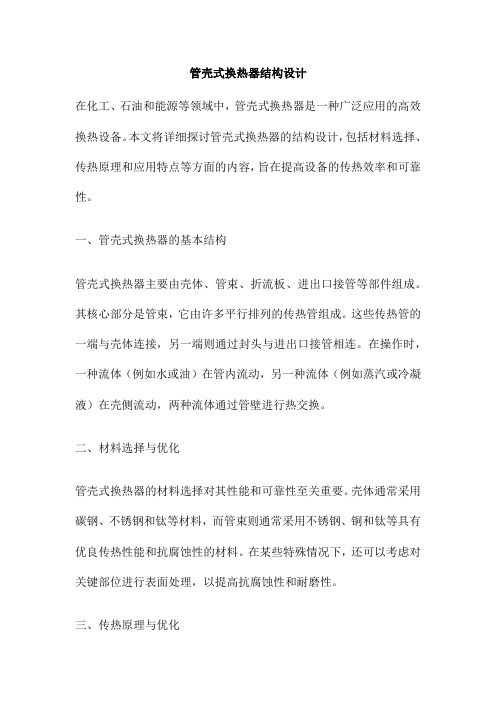
管壳式换热器结构设计在化工、石油和能源等领域中,管壳式换热器是一种广泛应用的高效换热设备。
本文将详细探讨管壳式换热器的结构设计,包括材料选择、传热原理和应用特点等方面的内容,旨在提高设备的传热效率和可靠性。
一、管壳式换热器的基本结构管壳式换热器主要由壳体、管束、折流板、进出口接管等部件组成。
其核心部分是管束,它由许多平行排列的传热管组成。
这些传热管的一端与壳体连接,另一端则通过封头与进出口接管相连。
在操作时,一种流体(例如水或油)在管内流动,另一种流体(例如蒸汽或冷凝液)在壳侧流动,两种流体通过管壁进行热交换。
二、材料选择与优化管壳式换热器的材料选择对其性能和可靠性至关重要。
壳体通常采用碳钢、不锈钢和钛等材料,而管束则通常采用不锈钢、铜和钛等具有优良传热性能和抗腐蚀性的材料。
在某些特殊情况下,还可以考虑对关键部位进行表面处理,以提高抗腐蚀性和耐磨性。
三、传热原理与优化管壳式换热器的传热原理主要是通过对流传热和热传导的组合来实现的。
为了提高设备的传热效率,可以采用以下措施:1、改变折流板的形状和布置,以增加壳侧流体的湍流度。
2、选择具有高导热系数的材料,以提高管壁的热传导性能。
3、适当增加管束数量和布置密度,以增加传热面积。
四、应用特点与优势管壳式换热器在各种工业领域中得到了广泛应用,主要特点有:1、结构紧凑,占地面积小,易于布置。
2、材料选择广泛,适用于各种不同的工艺条件和腐蚀性介质。
3、传热效率高,能够实现两种流体的有效热交换。
4、制造工艺成熟,操作维护方便,使用寿命较长。
五、结论本文对管壳式换热器的结构设计进行了全面分析,包括材料选择、传热原理和应用特点等方面的内容。
通过合理的结构设计,可以显著提高管壳式换热器的传热效率和可靠性,使其在各种工业领域中发挥更加重要的作用。
随着技术的不断进步,管壳式换热器的设计和制造水平也将不断提升,为工业生产带来更大的价值。
六、展望随着工业生产的不断发展和能源紧缺的压力日益增大,管壳式换热器的应用前景更加广阔。
管壳式换热器结构介绍

3、管壳程流体的确定
主要根据流体的操作压力和温度、可以利用的压力降、结构和腐蚀 特性,以及所需设备材料的选择等方面,考虑流体适宜走哪一程。下面 的因素可供选择时考虑:
适于走管程的流体有水和水蒸气或强腐蚀性流体;有毒性流体;容易 结构的流体;高温或高压操作的流体等。
1、管壳式换热器结构介绍
管壳式换热器:是以封闭在壳体中管束的壁面作为传热面的间 壁式换热器,这种换热器结构较简单、操作可靠,可用各种结构材 料(主要是金属材料)制造,能在高温、高压下使用,是目前应用 最广的类型。(设计制造遵循标准:国外 TEMA ASME 国内 GB151、GB150)
换热器封头选取原则
换热器折流板
单弓形折流板:优点是可以达到最大的错流,缺点是压降较高,且窗口 的管束容易发生振动;设计要点是折流板圆缺率在17%-35%之间,折流 板间距在0.2-1.0倍的壳径。此种类型折流板适用于大部分场合。
NITW:该折流板窗口不布管,管少,需要的壳体直径大。设计要点:15%的 折流板圆缺率。适合的场合是气体振动和压降受限。
谢谢!
K型壳体:主要用于管程热介质,壳侧蒸发的工况,在废热回收条件下使 用。
X型壳体:冷热流体属于错流流动,其优点是压降非常小,当采用其他壳 体发生振动,且通过调整换热器参数无法消除该振动时可以使用此壳体 形式,其不足之处是流体分布不均匀,X型壳体并不经常使用。
在化工工艺手册中,I型壳体类型可EDR软件中的不是同一种壳体, 其形式见I1,它的使用方式仅有一种搭配,就是BIU,U型管换热器。
螺纹管性能特点
在管子类型中,螺纹管属于管外扩展表面的类型,在普通换热管外 壁轧制成螺纹状的低翅片,用以增加外侧的传热面积。螺纹管表面积比 光管可扩展1.6-2.7倍,与光管相比,当管外流速一样时,壳程传热热阻 可以缩小相应的倍数,而管内流体因管径的减小,则压力降会略有增大。 螺纹管比较适宜于壳程传热系数相当于管程传热系数1/3-3/5的工况。
- 1、下载文档前请自行甄别文档内容的完整性,平台不提供额外的编辑、内容补充、找答案等附加服务。
- 2、"仅部分预览"的文档,不可在线预览部分如存在完整性等问题,可反馈申请退款(可完整预览的文档不适用该条件!)。
- 3、如文档侵犯您的权益,请联系客服反馈,我们会尽快为您处理(人工客服工作时间:9:00-18:30)。
换热器折流板
单弓形折流板:优点是可以达到最大的错流,缺点是压降较高,且窗口 的管束容易发生振动;设计要点是折流板圆缺率在17%-35%之间,折流 板间距在0.2-1.0倍的壳径。此种类型折流板适用于大部分场合。 NITW:该折流板窗口不布管,管子支撑完美,不引起管束振动,缺点是 相同的壳径大小,布管数较少,需要的壳体直径大。设计要点:15%的 折流板圆缺率。适合的场合是气体振动和压降受限。 双弓形折流板:优点是压降低,更好的规避振动的问题;缺点是大的窗 口流动面积;设计要点:5%-30%的圆缺率,默认两排管重叠;适合场合 时振动和压力受限的换热器(相对于单弓形折流板来说)。 螺旋折流板:分为单螺旋折流板和双螺旋折流板优点是换热好,压降低, 流动均匀;缺点是制造困难;设计要点是螺旋角度5-45°,适合的场合 时压降受限,容易结垢的场合。 折流杆:优点是支撑优,流动均匀,压降低基本无振动问题;缺点是低 的换热效果;管子布置只能为45°和90°;适合场合是低压降气体冷凝 和换热。 窝巢型:支撑优,流动均匀,压降低;缺点是比换热效果不好,设计基 本无要求。 蛋框型:支撑好,制造经济;缺点是高温应力下发生变形;设计基本无 要求。
螺纹管性能特点
在管子类型中,螺纹管属于管外扩展表面的类型,在普通换热管外 壁轧制成螺纹状的低翅片,用以增加外侧的传热面积。螺纹管表面积比 光管可扩展1.6-2.7倍,与光管相比,当管外流速一样时,壳程传热热阻 可以缩小相应的倍数,而管内流体因管径的减小,则压力降会略有增大。 螺纹管比较适宜于壳程传热系数相当于管程传热系数1/3-3/5的工况。
下表为壳程气体的最大允许速度与气体成分的分子量和气体压力的关系:
2、允许压力降的选择 选择较大的压力降可以提高流速,从而增强传热效果减少换热面积。 但是较大的压力降也使得泵的操作费用增加。合适的压力降值需要以换 热器年总费用为目标,反复调整设备尺寸,进行优化计算而得出。 在大多数设备中,可能会发现一侧的热阻明显的高于另一侧,此侧的 热阻成为控制热阻。可壳程的热阻是控制侧时,可以用增加折流板块数 或者缩小壳径的方法,来增加壳侧流体流速、减少传热热阻,但是减少 折流板间距是有限制的,一般不能小于壳径的1/5或50mm。当管程的热 阻是控制侧时,则依靠增加管成熟来增加流体流速。 在处理粘稠物料时,如果流体处于层流流动则将此物料走壳程。由于 在壳程的流体流动易达到湍流状态,这样可以得到较高的传热速率,还 可以改进对压力降的控制。
4、换热终温 的确定 换热终温一般由工艺过程的需要确定。当换热终温可以选择时,其 数值对换热器是否经济合理有很大的影响。在热流体出口温度与冷流体 出口温度相等的情况下,热量利用效率最高,但是有效传热温差最小, 换热面积最大。 另外,在确定物流出口温度时,不希望出现温度交叉现象,即热流 体出口温度低于冷流体出口温度。 5、设备结构的选择 对于一定的工艺条件,首先应确定设备的形式,例如选择固定管板 形式还是浮头形式等。参照下表1-7. 在换热器设计过程中,强化传热总的目标概括有:在给定换热量下 减少换热器的尺寸;提高现有换热器的性能;减小流动工质的温差;或 者降低泵的功率。 传热过程是指两种流体通过硬设备的壁面进行热交换的过程,按照 流体的传热方式基本上可以分为无相变和有相变两种类型。无相变过程 强化传热技术的研究,一般依据控制热阻侧而采取相应的措施:如采用 扩展管内或者管外表面;采用管内插异物;改变管束支撑件形式;加入 不互溶的低沸点添加剂等方法,以增强传热效果。
管壳式换热器传热机理
培训课件1 王亚乐
简介
一般来说,管壳式换热器制造容易,生产成本低,选 材范围广,清洗方便,适应性强,处理量大,工作可靠, 且能适应高温高压。虽然它在结构紧凑性、传热轻度和 单位金属消耗量方面无法与板式和板翅式换热器相比, 但它由于具有前述的一些优点,因而在化工、石油能源 等行业的应用中仍处于主导地位。 管壳式换热器是把管子与管板连接,再用壳体固定。 它的型式大致分为固定管板式、釜式浮头式、U型管式、 滑动管板式、填料函式及套管式等几种。根据介质的种 类、压力、温度、污垢和其他条件,管板与壳体的连接 的各种结构型式特点,传热管的形状和传热条件,造价, 维修检查方便等情况来选择设计制造各种管壳式换热器。
2、管壳式换热器设计所需考虑的因素
换热设备的类型很多,对每种特定的传热工况,通过优化选型都会 得到一种最合适的设备型号,如果将这个型号的设备使用到其他工况, 则传热的效果可能有很大的改变。因此,针对具体工况选择换热器类型, 是很重要和复杂的工作。对管壳式换热器的设计,有以下因素值得考虑。 1、流速的选择 流速是换热器设计的重要变量,提高流速则提高传热系数,同时压 力降与功耗也会随之增加,如果采用泵送流体,应考虑将压力降尽量消 耗在换热器上而不是调节阀上,这样可依靠提高流速来提高传热效果。 采用较高的流速有两个好处:一是提高总传热系数,从而减小换热 面积;二是减少在管子表面生成污垢的可能性。但是也相应的增加了阻 力和动力的消耗,所以需要进行经济比较才能最后确定适宜的流速。 此外在选择流速上,还必须考虑结构上的要求。为了避免设备的严 重磨损,所算出的流速不应超过最大允许的经验流速。 以下的三个表格分别表示了介质的流速范围和水在管内的流速余材质的 关系等。
Байду номын сангаас
1、管壳式换热器结构介绍
管壳式换热器:是以封闭在壳体中管束的壁面作为传热面的间 壁式换热器,这种换热器结构较简单、操作可靠,可用各种结构材 料(主要是金属材料)制造,能在高温、高压下使用,是目前应用 最广的类型。(设计制造遵循标准:国外 TEMA ASME 国内 GB151、GB150)
换热器封头选取原则
后封头
L型后封头:和A型前封头相同 M型后封头:和B型前封头相同 N型后封头:和N型前封头相同 U型:U型管束,管束可移动,壳侧容易清洗;热膨胀处理优秀,经济 (无法兰);缺点是管侧无法清洗,更换管束困难,弯头部位容易冲刷 损伤。 P型封头和W型封头已经被淘汰,不在使用。 S型封头:其尺寸特点是其后封头要比壳体的直径大,优点是可以解决换 热器设计过程中的两个问题,一是可以消除换热器的热应力,二是换热 器的管壳侧都可以进行清洗。 T型封头和S型封头相似,但其后封头尺寸和壳体直径相同,且其内封头 和管束可以直接抽出,但T型封头和S型封头相比,受力情况没有S型封头好, 唯一的好处是抽芯方便,在工程设计中一般不选用T。
G型壳体:属于平行流换热器,该换热器的热流体出口温度可以比冷流体 出口温度低,适用于需要做壳侧强化的卧式热虹吸再沸器、冷凝器等。 H型壳体:双平行流换热器,主要用于冷凝和蒸发的工况下,而且壳体中 不使用折流板。G/H型壳体的优点是传热温差大,比E型要高。 J型壳体:分流壳体,一是适用于壳体气相压降较大,振动解决不了的情 况;二是用于再沸器,相对于E型使得传热的效果比较稳定;三是用于部 分冷凝的工况,其缺点则是传热温差较小,传热系数也不大。 K型壳体:主要用于管程热介质,壳侧蒸发的工况,在废热回收条件下使 用。 X型壳体:冷热流体属于错流流动,其优点是压降非常小,当采用其他壳 体发生振动,且通过调整换热器参数无法消除该振动时可以使用此壳体 形式,其不足之处是流体分布不均匀,X型壳体并不经常使用。 在化工工艺手册中,I型壳体类型可EDR软件中的不是同一种壳体, 其形式见I1,它的使用方式仅有一种搭配,就是BIU,U型管换热器。
谢谢!
冷凝器介绍
1、冷凝机理分析
当蒸汽与低于其饱和温度的壁面接触时会冷凝成液体,同时放出汽化 潜热并传递给壁面,这种热交换过程称为冷凝传热。一般来说,单组份 的冷凝传热是一种高效传热过程,它的传热系数高于同种流体的单相对 流传热系数,但对含不凝气的混合物冷凝,因不凝气的存在使冷凝传热 系数大大降低。 冷凝传热过程大致分为以下几种类型: 按冷凝面的基本几何参数,可分为管内冷凝和管外冷凝。管内冷凝 包括水平管、垂直管和倾斜管;管外冷凝包括垂直单管及管束、水平单 管及管束。 按管子类型可分为光管、螺纹管(低翅片管)、沟槽管等。 按蒸汽的流体动力学可分为:低速(重力控制)和高速(剪力控制) 两种动力学状态。 按组分的数目和性质可分为:单组分、多组分混合物(冷凝液互溶 和不互溶两种)、含不凝气的混合物。 按冷凝方式可分为:膜状冷凝、滴状冷凝、直接接触冷凝、均相流 冷凝等。
下图为不同介质在不同设备类型中的允许压力降参考值:
3、管壳程流体的确定 主要根据流体的操作压力和温度、可以利用的压力降、结构和腐蚀 特性,以及所需设备材料的选择等方面,考虑流体适宜走哪一程。下面 的因素可供选择时考虑: 适于走管程的流体有水和水蒸气或强腐蚀性流体;有毒性流体;容易 结构的流体;高温或高压操作的流体等。 适于走壳程的流体有塔顶馏出物的冷凝;烃类的冷凝和再沸;管件压 力降控制的流体;粘度大的流体等。 当上述情况排除后,介质走哪一程的选择,应着眼于提高传热系数和 最充分的利用压力降上。由于介质在壳程的流动容易达到湍流 (Re≥100),因而将粘度大的或流量小的流体,即雷诺数低的流体走壳 程一般是有利的。反之,如果流体在管程能够达到湍流时,则安排走管 程较合理。若从压力降的角度考虑,一般是雷诺数低的走壳程合理。
换热器壳体
E型壳体:为单程壳体,在设计过程中一般优先选择,它适用于所有的情 况,单相换热更优,缺点是压降较大。 F型壳体:适用于场地受限,需要双壳程的情况,比较适合于单相换热, 纯逆流换热,传热温差大;缺点是F型壳体有分程隔板,此处会发生漏流, 而且壳程进口与出口处的压差和温差都是最大的,会发生漏温且分程隔 板也容易发生变形。所以F型壳体适用于压差和温差都不大的情况下。
1、管壳侧是否需要清洗; 2、是否需要移动管束; 3、是否需要考虑热膨胀; 前封头类型:A、B、C、D、N 后封头类型:L、M、N、P、S、T、W 后封头又分为固定式、浮头式以及U型管,相对于固定式,浮头式造 价更高、需要更大的壳径、低的换热效果(由于泄漏流C的存在),优点 则是一端具有自由度可以处理好热膨胀问题。
前封头
A型封头:适应于管程流体较脏,需要经常清洗的情况。 B型封头:单法兰经济型最好,由于易于采购,是最常用的封头 C型封头:带管板和可拆盖,管侧清洗方便,可以处理管程高压和高危介 质(适当),适于壳侧管束较重以及壳侧需要清洗的情况。 D型封头:特种高压型,适用于特殊高压的工况(管箱焊在管板上) N型封头:带管板和可拆盖,管束不可拆,此种封头经济性最好,接近管 板容易;可以处理壳侧高危介质。 A型封头与B型封头相比多了一片法兰,其耐压性没有B型封头好, 其优点是换热器检修时不许将封头拿掉,相对于B型封头来说更加方便。 C型封头、N型封头换热器中的管束是可抽出的,其中C型封头的换热器中 的管板和管箱是焊在一起的。