第七章 船体分(总)段的装焊
船体分(总)段的装焊

• 引言 • 船体分(总)段的装焊工艺流程 • 船体分(总)段的装焊设备与工具 • 船体分(总)段的装焊质量控制 • 船体分(总)段的装焊安全与环保 • 船体分(总)段的装焊实例分析
01
引言
船体分(总)段的装焊的定义
船体分(总)段的装焊是指将船体划分为若干个分段,然后按照一定的顺序和工艺要求 进行组装焊接的过程。
01
02
03
04
佩戴防护眼镜
在焊接操作过程中,焊接人员 需佩戴专业的防护眼镜,以防 止飞溅物对眼睛造成伤害。
穿戴防护服
焊接人员需穿着防烫、防火的 防护服,以保护身体免受高温
和火花飞溅的伤害。
使用防尘口罩
在焊接过程中,焊接人员需佩 戴防尘口罩,以减少吸入有害
烟尘和气体。
佩戴耳塞
长时间从事焊接工作的人员需 佩戴耳塞,以减轻噪声对听力
埋弧自动焊机
适用于长直焊缝和大面积 的平板对接焊接,具有焊 接速度快、质量稳定等优 点。
切割设备
火焰切割机
利用燃气和氧气燃烧产生的高温进行切割,适用 于厚板和不锈钢板的切割。
等离子切割机
利用高温等离子弧进行切割,具有切割速度快、 切口质量好等优点。
激光切割机
利用高能激光束进行精确切割,适用于薄板和复 杂形状的切割。
成本。
此外,合理的分段划分和装焊工 艺还可以提高船体的结构强度和 稳定性,从而提高船舶的安全性
和使用寿命。
船体分(总)段的装焊的历史与发展
早期的船体分(总)段的装焊主要采用 手工焊接的方式,效率低下,质量不 稳定。
同时,随着数字化技术和计算机技术 的发展,船体分(总)段的装焊也逐步 实现数字化和智能化,提高了装配的 精度和效率。
船体加工-分段装焊方法
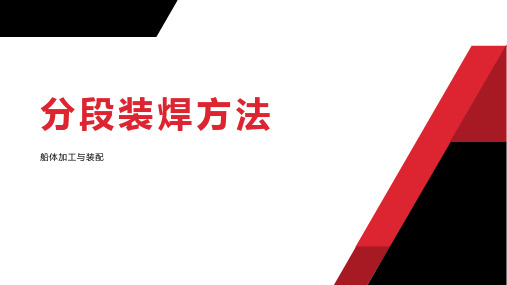
船体加工与装配
船体结构预装焊工艺
部、组件装焊 分段装押
组件装焊 大型分段或总段的组装
加工的船体构件绝大部分要经过此工艺过程, 再送往船台装焊成船体
船体结构预装焊工艺
船体结构预装程序的合理与否
船体建造质量的好坏 船体变形的大小
预装焊工艺水平的高低
装配作业的难易 制造周期的长短
• 船厂的生产能力 • 生产效事的高低
分段装焊工艺
分段的类型
分 段
• 由零、部件组装而成的船体局部结构
平面分段 平直板列上装有骨材的单层平面板架
舱壁分段
舱口围壁分段
平台甲板分段
平行中体处的舷侧分段
分段装焊工艺
分段的类型
分 段
• 由零、部件组装而成的船体局部结构
曲面分段 曲面板列上装有骨材的单层曲面板架
单底分段 甲板分段
舷侧分段
分段装焊工艺
分段装焊工艺
分段装焊工艺的基本内容
分段装焊顺序的合理与否
分段制造的质量 辅助材料的消耗量
装焊作业的难易程度 分段制造的周期
分段装焊工艺
分段装焊工艺的基本内容
同一分段 不同分段
不同的制造方法 不同的装焊顺序
分段装焊工艺
分段建造方法
按装配基面分类
正造法
反造法
侧(卧)造法
分段建造时的位置与其在 实船上的位置一致
分段装焊工艺
分段建造方法
放射法
按构件安装顺序分类
分段装焊工艺
分段建造方法
按构件安装顺序分类
插入法
在分段装配基准面的板列上
• 安装间断的纵向构件
• 再装插入的横向构件
• 将连续的纵向桁材插入横向构件中,然后再进行焊接
6-7 船舶总段的装配

6、总段接缝的焊接;
操作要求: ① ② ③ ④ 按焊接工艺规程进行焊接。 焊接舷侧板与舭板的对接缝; 焊接横舱壁与内底板、舷侧板、甲板的角焊缝; 焊接甲板与舷侧板的角焊缝; 焊接内部结构的接缝。
7、总段划线和结构性检验;
操作要求: 划安装定位线、轮廓线;焊缝和结构性检验。
8、总段舾装;
操作要求: 安装总段内的舾装单元、各种舾装件极其附件。
① 舷部肋骨检验线应与底部肋骨检验线对齐; ② 水平检验线应与舱壁水平检验线在同一水平面; ③ 肋骨检验线顶部半宽等于该号肋骨的船体半宽。
5、甲板分段的装配;
① ② ③ ④
操作要求: 甲板中心线应与内底中心线相吻合; 甲板肋骨检验线应与舷部肋骨检验线对齐; 甲板边高应与舷部所划甲板理论线吻合; 应保证梁拱高度。
8、外板的安装;
• 操作要求: 应保证肋骨间距的正确。
9、总段焊接;
焊接顺序: ① 焊接骨架间接缝,骨架与甲板间的接缝; ② 焊接外板的对接缝; ③ 焊接骨架与外板的接缝,骨架与托底骨架的接缝。
10、满档板的装配焊接;
11、 划出船台安装定位线; 12、总段翻身、甲板封底焊、满档板封底焊; 13、矫正变形; 14、焊缝和结构性检验; 15、总段舱面舾装。
1、各个分段的装配焊接; 2、底部分段定位固定; 3、横舱壁分段的装配;
操作要求: ① 安装位置应和内底板下横骨架一致,错开位移不得超过 舱壁板厚的一半; ② 水平检验线必须在同一水平面内,中心线应和内底板中 心线对齐; ③ 舱壁应保证与基线垂直,高度应符合图纸要求。
4、舷侧部分段的装配;
操作要求:
第八节 总段的装配
总段及其制造Biblioteka 法总段: 主船体沿船长方向划分的其深度和宽度等于该处型深和 型宽的环形立体分段。 总段的两种制造方法: 1、分段建造法
船体分段装焊设计 庄

船体分段装焊设计庄摘要:主要是了解船体预装配的工艺装备内容;理解船体部件装焊过程;掌握胎架设计方法。
扼要分析和阐述了船舶船体结构在装配过程中的缺陷,对难于采取返修的典型缺陷,关键词:部件装配,船体结构,结构强度,缺陷引言:船体装配工艺随着造船材料和连接技术的发展而变化,目前的钢质船舶焊接船体的装配过程,大致由下列4个步骤组成:1.将各个船体零件装配焊接成船体部件。
2.由船体零件和部件装配焊接成各种船体分段或总段。
3.由平面分段、曲面分段和零、部件装焊成大型立体分段或总段。
4.在船台上(或造船坞内)将分段、大型立体分段和总段组装成整个船体。
前3个步骤通常称为船体结构预装配工艺。
所谓船体零件是指经号料、加工后可供装配的船体构件,如肋骨、横梁、肋板、外板等。
船体部件是指两个或两个以上的船体零件装焊成的组合件。
如各种焊接T型梁、肋骨框架、尾柱、舵、带缆桩等。
船体分段是由船体部件和零件组合而成的一部分船体,它又可分为平面分段、曲面分段、半立体分段、立体分段和大型立体分段。
平面分段有隔舱壁、甲板、围壁等分段;曲面分段有舷侧、单层底、舭部等分段;立体分段有双层底、上层建筑、甲板室、边水舱、首部、尾部等分段;半立体分段则介于平面、曲面分段和立体分段之间,如舷侧带甲板边板、舷侧带部分隔舱壁、甲板带半高围壁等分段。
船体总段是由船体分段、部件和零件组合而成的具有一定长度的船体环形封闭体;大型立体分段类似于船体总段。
1 船体预装配的工艺装备船体结构预装配焊接主要指船体部件、分段和总段的制造。
在制造时,除了装配操作时需要使用的工具与设备外,还必须配置便于进行画线、装配定位、焊接和检验的专用工艺装备,才能顺利地进行装配工作并保证装配质量。
这些工艺装备,根据其工作面的不同,可分为平台和胎架两大类。
1.1 平台的种类和用途平台是一个大而平坦的工作台。
一般由型钢和钢板组成,并固定在专门的水泥基础上。
它主要用于装配焊接船体部件、平面分段和带有平面基面的立体分段等的一种工作台,也可作为设置胎架的基础。
船体装配讲义

第一章船舶分段的划分第一节船舶装配概述零件部件分段(总段)船台、船坞散装件1)部件装配:将加工好的零件装焊成小组件或大组件。
2)分段装配:将加工好的部件进行组装,形成分段的过程。
方箱子分段平面分段流水线3)分段总组:曲面分段、曲面分段进行组装,形成形成主体结构的分段。
4)总装大合拢:将总组好的分段到船台或船坞进行焊接的的过程。
1 分段建造装配顺序:铺板划线定位安装构件盖面2 分段制造方法1)放射法:先装纵骨,再装中间的肋板和间断桁材,交叉进行,最后吊中桁材。
2)插入法:先装间断桁材,再装肋板,最后吊中桁材,适用于中型船、横骨架式。
3)分离法:先装纵骨、间断桁材、中桁材,再插入肋板,适用于平直纵骨结构分段。
4)框架法:分段铺板焊接和划线在分段场地进行,而构架在专用胎架上进行制造,最后将构架所形成的框架整体吊上分段进行焊接。
分段构架装配采用那几种方法,这些方法的主要工序如何?船体装焊工艺路线,归纳起来有几条部序,四大部序。
第二节分段划分及编码方法一、分段划分的原则1)分段重量的选择受船厂起重能力和运输能力的限制。
2)生产负荷的均衡性分段数量的位置要于船台(船坞)装焊顺序和进度相符合。
3)船体结构的合理性分段划分的结构合理性,是船体结构特点对分段大接头的强度要求。
4)施工工艺的合理性A 扩大分段装配焊接的机械化、自动化范围。
B 分段大接缝布置的合理性,分段大接缝布置的合理不仅可以保证船体结构的合理,而且可以简化装配工作。
C 分段接头形式的合理性,单断面接头和阶梯形接头,板和骨架错开,错开距离在一档肋距内。
D 分段划分充分考虑钢材分段长度尽量与钢板规格或型才规格保持一致,我公司板材或型材长度一般为12m。
E 扩大预舾装。
二、分段编码横向位置代码数量顺序代码分段层次代码分段构造代码(这里表示底部)分段区域代码(这里表示货舱区)分段构造代码:底部 B Botton边底W Wing舷侧S Side上甲板 D Deck横隔舱T Transverse bulkhead纵隔舱L Longitudinal bulkhead半立体分段G特殊分段尾柱SF烟囱FU挂舵臂RH分段层次代码:0 底部分段1 上甲板及面层各分段2 二甲板3 三甲板1、请代入船体划分的原则2、说明CB05P/S、EG11P/S、FG21第二章分段与总段的制造(胎架部分)第一节胎架的划分一、胎架基准面的切取1 胎架的作用:作为制造分段的专用工装设备。
第七章 船体分(总)段的装焊

1) 激光经纬仪法:即把胎架中心线复画 到底板上后,用样棒或根据草图用钢卷尺 在分段中心线上标出每档肋骨点后,过每 一肋骨点架好激光经纬仪,校好水平,对 准分段中心线,读取水平度盘角度α,然 后旋转900,固定水平度盘,发射激光束, 转动竖直度盘求得许多激光点。
2)基准线对线法:即将胎架基准面上标出的 基准肋骨线用线锤复到底板上口边,以该点 为准,用肋骨间距在上口线的展开样棒来画 出上口线上的各肋骨点,打上标记,然后沿 对应点子拉出钢丝,用吊线锤的方法找出若 干点子,即可画出肋骨线。
双层底分段装焊工艺过程(正造法)
一、制作胎架
二、底板装焊
从K列板开始,当K行板吊上 胎架后,应使其中心线对准胎架 中心线;其纵向位置以K板伸出端 部胎架的长度对准胎架上标出的 端接缝线来确定。当K行板的纵横 位置确定后用马板固定于胎架上 并与胎模板贴紧。
其它底板装焊的注意要点:
1.基准边与余量边的规定:以前一行 已定位底板的纵缝为基准,与之相接 的后一行未定位底板的纵缝为有余量; 端接缝则以环缝线为准,画出切割线; 有奠基分段的,对于非奠基分段则与 奠基分段相近的一端留有余量,另一 端为基准边。
5.焊接
1)采用分离装配法安装纵横骨架:
➢纵向(主向)构件边装边焊; ➢中桁材、旁桁材、船底纵骨与船底外板的 角接焊缝用自动角焊机或半自动角焊机进行 单面连续焊;
纵向构件与船体外板的施焊顺序
➢外底板上安装肋板(交叉构件)后,则先焊肋板 与中桁材、旁桁材、船底纵骨间的连续立角焊缝。
➢再焊接肋板与船底外板的单面连续平角焊缝。
第一节 概 述
分段是由零、部件组装而成的船体局 部结构,是船体装配焊接工作中的重要 组成部分。
船体分段制作工艺流程

船体分段制作工艺流程船体分段现场制造工艺流程生产范围大组立是船舶制造的一种生产管理模式,是船体分段装配的一个生产阶段。
就是将零件和部件组成分段的生产过程。
人员搭配大组立生产以班为单位,一个班一般分为三到四个班组,一个班组的成员有一个组长、三个师傅、六个徒弟、两个电焊工、一个打磨工。
图纸资料大组立相关图纸有零件明细表、产品完工图、制作工艺、焊接工艺等。
工具割枪、米尺、线垂、千斤顶、水平尺、水平管、花兰螺丝、铁锤、铁楔、角尺、电焊机、自动二氧化碳焊接、打磨机机舱双层底大组立机舱双层底工艺流程胎架或平台准备——铺内底板——构件安装位置划线——构件安装——焊接——管铁舾装安装焊接——外板安装——焊前检查——构件与外板焊接——打磨——密性实验——交验装配作业标准分段长:L <±4mm分段宽: B <±4mm分段高:H <±4mm分段方正度:(内底板四角水平)<±8mm(加测机座内底板水平)货舱双层底大组立工艺流程胎架或平台准备——内底板拼装——自动二氧化碳焊接——构件安装位置划线——内底纵骨安装焊接——构件小组(肋板)安装焊接——舾装——补漆¬外底板拼装——焊接——构件安装位置划线——外底纵骨装焊——组装完成——焊接——打磨——舾装——完工检查——报验装配作业标准分段长:L <±4mm分段宽:B <±4mm分段高:H <±3mm分段方正度:<4mm (内、外底板对角线差值)分段扭曲度:<±8mm (内底板四角水平)纵骨端平面度:<±4mm内、外底板中心线偏差<±3mm内、外底板肋位线偏差<±3mm货舱顶边水舱大组立货舱顶边水舱分段工艺流程胎架或平台准备——斜板拼装——焊接——构件安装位置划线——斜板纵骨安装焊接——构件(肋板)安装焊接——舾装——补漆¬甲板拼装——焊接——纵骨装焊——组装完成——焊接——打磨——舾装——完工检查——报验装配作业标准分段长: L <±4mm分段宽: B <±4mm分段高: H <±4mm分段方正度:(测上甲板)<4mm分段扭曲度:(上甲班)<±8mm纵骨端平面:<±4mm货舱舭部大组立工艺流程胎架或平台准备——斜底板拼装——焊接——构件安装位置划线——斜底纵骨安装焊接——构件小组(肋板)安装焊接——舾装——补漆¬外底板拼装——焊接——构件安装位置划线——外底纵骨装焊——组装完成——焊接——打磨——舾装——完工检查——报验装配作业标准分段长: L <±4mm分段宽: B <±4mm内底高:H1±3mm舭部尖顶高:H2±4mm分段方正度:(测斜板)<4mm分段扭曲度:(测斜板)<±8mm。
船体修造工艺复习资料

船体修造工艺复习资料船体修造工艺复习资料第六章钢材预处理和号料一.钢材变形的主要原因是什么?答:1.钢板轧制引起的变形。
2.运输,存放引起的变形。
二.钢材表面清理的方法有哪几种?各有什么特点?答:1.原材料抛丸法特点:抛丸除锈的效率很高,可达8002m/h,但不适于清理厚度在4mm以下的薄钢板,因其容易引起薄板变形。
2.原材料酸洗法特点:酸洗除锈法除用于薄板外,主要用于处理管子,舾装件和形状复杂的零部件。
3.分段喷丸法特点:喷丸除锈法的生产效率比手工敲铲法高,与抛丸除锈法相比,具有设备简单,维修方便的优点。
问题是劳动条件仍然差,生产效率也不高,辅助工作量较大,属于半机械式生产,难于实现半自动化,尤其是需除锈分段的大小受到喷丸房主尺度的限制。
4.带锈底漆特点:带锈底漆一般用于二次除锈,对小型船舶也可作一次除锈防护用。
使用带锈底漆可以免掉钢材表面的除锈工作,减少许多除锈的专用设备,节省大量工时,大大简化钢材的除锈与防护工艺,尤其是对于二次除锈,其效果更为显著。
虽然它要在锈蚀存在的情况下才起作用,而且对氧化皮的清理还有困难,但是它在船体钢材的清理与防护工艺中是一项较有发展前途的新技术。
5.覆盖层保护法特点;在金属表面上使用覆盖层保护是防止金属腐蚀的最普通而又重要的方法,它的作用在于是金属与外界隔绝,以阻碍金属表面形成微电池,从外界创造条件来避免腐蚀的发生,故称为消极防护。
覆盖层一般应满足下列基本要求:结构紧密,完整无孔,不透电解质,附着力强,高强度,耐磨,分布均匀。
三.什么叫钢材的预处理?答:号料前的钢材矫正和表面清理与防护便称为钢材的预处理。
四.什么叫钢材的号料?号料方法有哪几种?答:号料:所谓号料就是在进行过预处理的钢材上,按照实际形状与大小画出船体零件的图形,并标注其船名,构件名称,有关结构线,加工符号,装配符号,施工余量等。
号料方法:1.普通号料(样板号料,草图号料)2.光学号料法3.自动号料法五.什么是二次号料?答:二次号料是在构件经过加工,装配,焊接后成为正确的构件和组成部件或分段是,再一次画出的切割线,故又称为装配画线。
- 1、下载文档前请自行甄别文档内容的完整性,平台不提供额外的编辑、内容补充、找答案等附加服务。
- 2、"仅部分预览"的文档,不可在线预览部分如存在完整性等问题,可反馈申请退款(可完整预览的文档不适用该条件!)。
- 3、如文档侵犯您的权益,请联系客服反馈,我们会尽快为您处理(人工客服工作时间:9:00-18:30)。
1.平面分段:平直板列上装有骨材的单 层平面板架,如舱壁分段、舱口围壁分 段、平台甲板分段、平行中体处的舷侧 分段等。
3
2.曲面分段:曲面板列上装有骨 材的单层曲面板架。
如单底分段、甲板分段、舷 侧分段等。
3.半立体分段:两层或两层以
上板架所组成的非封闭分段,
或者是单层板架带有一列与
其成交角的板架所构成的分
23
2.拼板的套割:曲形外底板装配时尽量把刚吊上 胎架的后一列钢板插人已定位好的前一列底板 下面,以便于进行套割;当板材较厚不便插入 时,可将两板端边缘对平,以另一侧的定位边 为准画出余量边的余量线再予切割。
第七章 船体分(总)段的装焊
教学要求: 了解分段和总段的吊运和翻身; 理解分段的焊接变形及预防; 掌握船体分段、总段装焊过程。
重点:分段、总段装焊。 难点:分段的焊接变形及预防。
1
第一节 概 述
分段是由零、部件组装而成的船体局 部结构,是船体装配焊接工作中的重要 组成部分。
一、分段的类型 分段按其外形特征大致可分为五类。
9
3)侧(卧)造法:分段建造时的位置与其 在实船上的位置成一定的角度或垂直。 优点:改善施工条件; 缺点:胎架数量多。 通常用于舷侧分段、舱壁分段等。
10
2、构件装配方法
分段的装配程序一般是: 铺板 画线 安装构架。
分离装配法
散装法 放射装配法
构件装 配方法
插入装配法
框架法
11
(1)散装法 ①分离散装法:在分段装配基准面的板列上,先安
17
3、分段检验
(1)分段外形尺寸; (2)构件尺寸; (3)构架位置; (4)零件数量; (5)装配精度; (6)焊焊质量。
18
4、分段完工检验
(1)分段尺寸检验; (2)分段外形检验;
19
第三节 底部立体分段的装焊
底部分段从结构形式上分为双底和单底 两大类。
双底的内底边板可分为平直、向下折角、 向上折角、阶梯型4种形式,
如艏、艉尖舱总段、上层建筑总段 等。
5
二、分段装焊工艺的基本内容 1.选择分段装配基准面和工艺装 备(平台或胎架); 2.决定合理的装焊顺序; 3.提出施工技术要求。
6
衡量装焊工艺程序是否合理的标准:
(1)能否保证分段的型线与尺寸; (2)是否便于装配操作,辅助材料和工时消 耗是否少; (3)是否便于焊接操作,合理的工艺应是水 平焊缝和俯位焊缝数量多、长度长,有利于扩 大自动焊、半自动焊的范围; (4)是否缩短分段的制造周期; (5)是否有利于舾装工程与船体工程的平行 作业; (6)能否处理好单船、小批量及批量生产的 矛盾。
段。
如带舱壁的甲板分段、带
舷侧的甲板槽形(门形)分
段、甲板室分段等。
4
4.立体分段:两层或两层以上 的板架所组成的封闭分段,或 者是由平面(或曲面)板架所 组成的非环形立体分段。
如双层底分段、双层舷侧分 段、边水舱分段、艏立体段、 艉立体段等。
5.总段:主船体沿船长方向划分,其深 度和宽度等于划分处型深和型宽的环 形立体分段。
1、胎架检验
(1)胎架的基准面是否明确,水平,这是最基本的; (2)胎架的型值数据是否完整,准确,这是外板线 性光顺的保证; (3)胎架强度如何,需要保证安全; (4)拼板区是否有足够的胎架进行支撑,保证板缝 便于拼接。
16
2、划线检验
(1)各构件安装线; (2)开口线; (3)大接缝线; (4)端接缝与肋位距离; (5)列板宽度; (6)间断焊焊接尺寸。
21
双层底分段装焊工艺过程(正造法)
一、制作胎架
二、底板装焊
从K列板开始,当K行板吊上 胎架后,应使其中心线对准胎架 中心线;其纵向位置以K板伸出端 部胎架的长度对准胎架上标出的 端接缝线来确定。当K行板的纵横 位置确定后用马板固定于胎架上 并与胎模板贴紧。
22
其它底板装焊的注意要点:
1.基准边与余量边的规定:以前一行 已定位底板的纵缝为基准,与之相接 的后一行未定位底板的纵缝为有余量; 端接缝则以环缝线为准,画出切割线; 有奠基分段的,对于非奠基分段则与 奠基分段相近的一端留有余量,另一 端为基准边。
适合于钢板较厚且制造场地起重设备负荷 较大的中型船舶的分段制造。
14
(2)框架法 先将所有的纵、横构件组装成箱形框架并焊好,
再与列板组装在一起形成分段。 可变立焊为俯焊,便于框架焊接采用机械化,使
工作面得以扩展,有利于缩短分段制造周期,减小 焊接变形。
适用于大型平直分段制造。
15
四、分段制造过程中的检验项目
7
三、分段制造方法和装配方法
1、分段建造方法
1)正造法:分段建造时的 位置与其在实船上的位置一 致。 优点:施工条件好、型线易 保证; 缺点:胎架复杂、画线工作 量大。 常用于单底分段、机舱分段 及批量生产。
8
2)反造法:分段建造时的位置与其在实船上的位 置相反(成180度)。 优点:胎架简单、可一次翻身,可改仰焊为平焊。 缺点:施工条件稍差、型线易产生误差。 常用于双层底分段、以甲板为基面的分段及单船生 产。
20
底部装配方法有正装和倒装两种。
正装法是以外底板为基准面,一般在胎架 上装焊,因此能够保证底部的正确型线,但 胎架制作需耗费较多的辅助钢材和一定的工 时。适合于单底结构或壳板较薄的底部分段, 及成批生产这类结构的产品,
倒装法是以内底板为基准面,在型钢平台 或墩木上进行装焊的,利用肋板、龙骨等纵 横骨架来保证底部型线的,其型线的正确要 差些,但可省去胎架,适合于双底结构或单 船生产。
引起的分段变形小 适用于曲率变化大、钢板稍薄的小型船舶 分段制造,及高度在lm以上的双底结构。
13
③插入装配法 :在分段装配基准面的板列上, 先安装间断的纵向构件,再装插入的横向构 件,最后将连续的纵向构件插入横向构件中, 然后再进行焊接。
可使构件吊装的时间集中,不需吊求随 时配合,但插入安装难度较大
装布置较密的主向构件并进行焊接,再安装交叉构件 并进行焊接。
装配与焊接交替,有利于扩大自动焊、半自动爆的 范围,减少分段的总体变形。但装配工作不连续。
适用于平直、结构刚性大、钢板厚、以纵骨架式为 主的大、中型船舶的分段制造。`
12
②放射装配法 :在分段装配基准面的板列上, 按从中央向四周的放射状方向,依次交替装 配纵、横构件并焊接。