基于ANSYS的叶片模态分析与创新设计
某机高压涡轮叶片振动模态分析

某机高压涡轮叶片振动模态分析摘要:以某机高压涡轮工作叶片为研究对象,讨论其模态振动理论,采用UG建立叶片实体模型,利用有限元软件ANSYS Workbench对其进行模态分析,并与电动振动台测量结果进行对比,得到有限元分析结果具有一定的可靠性,为数值模拟振动测试数据提供一定的可信度依据,尤其对一些科研机种叶片的数值振动模态仿真分析提供了参考价值。
关键字:振动测试;模态分析;叶片;ANSYS Workbench引言叶片是航空发动机重要组成部分,工作时主要承受离心载荷、气动载荷、热载荷以及工况环境变化导致的交变载荷,工作中很容易发生故障,据统计振动故障占发动机总故障的15%,而叶片振动故障又占振动故障的75%。
而据粗略统计,我国现役航空发动机发生的重大事故中,涡轮叶片的断裂高达80%以上[1]。
因此叶片工作时的可靠性直接关系到整个发动机的运行安全性及使用寿命,为避免叶片振动故障的出现,在设计、制造及维修过程中对叶片进行振动模态分析,得到其固有频率、振型以及振动应力分析就显得尤其重要。
然而,高压涡轮叶片在发动机工作状态下直接对叶片进行频率及振动形态的观察及测试是比较困难甚至是不可能的。
在生产及制造中,一般只对叶片进行自由振动分析,测得其固有频率及振动形态。
单从使用角度来看,仅仅对叶片进行自由模态分析是不精确的,无法获得叶片全生命使用周期内的准确频率及振动形态。
本文首先在电动振动台ES-10-240上对高压涡轮叶片进行振动测试,得出其平均固有频率。
然后再UG中建立叶片实体模型,利用有限元软件ANSYS Workbench对其进行模态分析,对比有限元分析结果与试验结果。
在此基础上对高压涡轮叶片进行预应力模态分析,得到更准确的振动频率及振动形态,为高压涡轮叶片设计及加工提供一定的参考价值。
1 模态分析理论模态分析是结构动力学分析中最基础、也是最重的一种分析类型,其主要是用于计算结构的振动频率和振动形态,每一个模态都有特定的固有频率、阻尼比和模态阵型。
基于ANSYS的飞机发动机压气机叶片模态分析
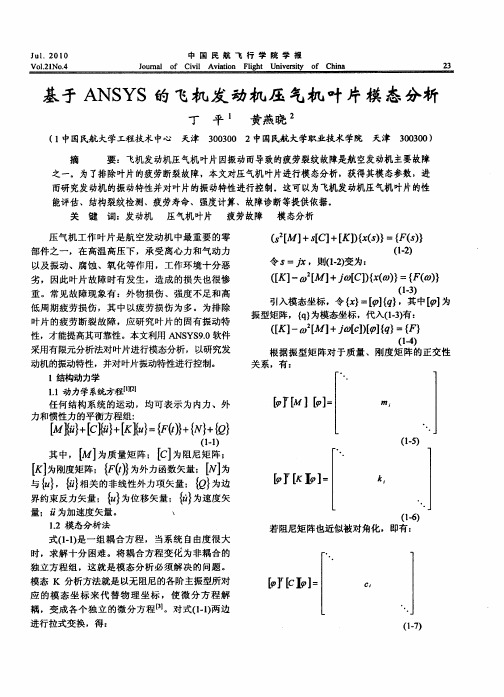
】【 】 『c =
(-) 1 7
中 国 民 航 飞 行 学 院 学 报
J u n l o Ci i Ava i n Fl h Un v ri o C ma o r a f vl it o i t g i est y f h
J .2OI u1 O
VO . . I I 4 2 No
J .2Ol uI O
中 国 民 航 飞 行 学 院 学 报
J u a o Cii Avain Fl h Unv ri o Chn or l f n vl it i t o g iest y f ia
VO _ 1 . l No 4 2
基 于 A YS的 飞机 发 动机 压 气机 叶 片 模 态 分析 NS
忽 略一些 对结 果影 响不 大 的结构 。
这样,相互耦合 的Ⅳ 自由度系统的方程组经 正交变换,成为在模态坐标下相互独立的 N 自由
度系统的方程组,解耦后的第 i 个方程为:
一
Mlj C f ∑ , =,… 以 + ( l = F( 1, , o , 2 )
=1
(-) 19 式中 , , 别 为模 态 刚度 、模 态 质 C分
( ^ 】 s 】 【 ) () ={ ( ) 【 + i + 】 ) F c { )
(-) 1 2
令 S= ,则( 2变为: 1) -
( 一 【 】 【 】 } F } I 』 + C ) ( )={ ( ) X】 {
(—) 13
重。常见故障现象有 :外物损伤 、强度不足和高
】 『
】 =
(- I 0 若阻尼矩阵也近似被对角化 ,即有:
模态 K分析方法就是以无阻尼的各阶主振型所对
应 的模 态 坐 标 来 代 替 物 理 坐 标 , 使 微 分 方 程 解 耦 ,变 成 各 个 独 立 的微 分 方 程 p。对 式 (一) J 11两边 进行 拉式 变换 ,得 :
机械设计制造及自动化毕业论文-风力机叶片的有限元分析

风力机叶片的有限元分析学生姓名:1111 专业班级:机械设计制造及其自动化2008级10班指导教师:朱仁胜指导单位:机械与汽车工程学院摘要:通过Solidworks软件对3MW风力机叶片进行建模,然后基于ANSYS 和Workbench分别对其进行模态分析和流固耦合分析,其中流固耦合分析中的结构静力分析部分也使用到了ANSYS Mechanical APDL。
其中模态分析结果表示:叶片的振型以摆振和弯曲为主,其一阶模态频率分别为 0.34Hz,能顺利的避开外在激励频率,避免了共振现象的发生。
流固耦合分析对额定风载进行了数值模拟仿真,通过结构静力分析,对叶片的受力,变形情况有了一个基本的了解,其中叶片在额定风载情况下的最大应力为56MPa,远远低于其实测拉伸强度的720MPa。
在11级风载下的应力云图显示其所受的最大应力为83.8MPa,满足其材料的强度要求。
该分析对进一步的疲劳分析和优化设计等提供了参考和依据。
关键词:叶片建模;模态分析;流固耦合分析;结构静力分析1Abstract:Through the Solidworks software build the blade model which power is 3 MW. Then based on the ANSYS and Workbench software,the analysis of modal and fluid-structure interaction.Andthe Static structural analysis is used the ANSYS Mechanical APDL too.The modal analysisresults show that the vibration modes of this blade are presented as Shimmy and bending,Thefirst modes frequency is 0.34Hz.And it can avoid the external excitation frequencywell,Avoid the resonance phenomenon occurs.The analysis of fluid-structure interaction havedo a numerical simulation about Rated wind load,through the Static structural analysis wehave a basic understanding of the stress and deformation about the blade. And the maximumstress of the blade is 56MPa under the rated wind load.Far lower than the Measured tensilestrength of 720MPa.And under the 11 rating wind load.The stress cloud show that maximumstress is 83.8MPa,Meet the strength of the material requirements.This analysis providesa reference and basis for further fatigue analysis and optimization design.Keywords:Blade modeling;Modal analysis;Fluid-structure interaction analysis;Static structural analysis31 概 述风能是地球表面大量空气流动所产生的动能,风能量具有取之不尽、用之不竭、就地可取、不需运输、广泛分布、不污染环境、不破坏生态、周而复始、可以再生等诸多优点。
基于ANSYS workbench六片斜叶圆盘涡轮搅拌器的模态分析
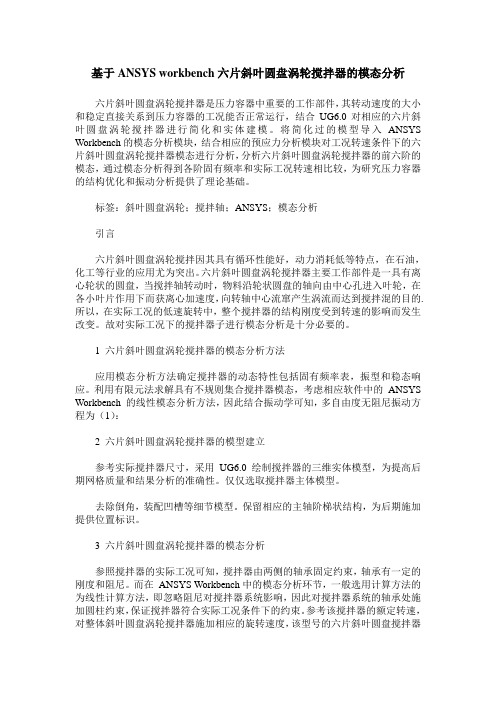
基于ANSYS workbench六片斜叶圆盘涡轮搅拌器的模态分析六片斜叶圆盘涡轮搅拌器是压力容器中重要的工作部件,其转动速度的大小和稳定直接关系到压力容器的工况能否正常运行,结合UG6.0对相应的六片斜叶圆盘涡轮搅拌器进行简化和实体建模。
将简化过的模型导入ANSYS Workbench的模态分析模块,结合相应的预应力分析模块对工况转速条件下的六片斜叶圆盘涡轮搅拌器模态进行分析,分析六片斜叶圆盘涡轮搅拌器的前六阶的模态,通过模态分析得到各阶固有频率和实际工况转速相比较,为研究压力容器的结构优化和振动分析提供了理论基础。
标签:斜叶圆盘涡轮;搅拌轴;ANSYS;模态分析引言六片斜叶圆盘涡轮搅拌因其具有循环性能好,动力消耗低等特点,在石油,化工等行业的应用尤为突出。
六片斜叶圆盘涡轮搅拌器主要工作部件是一具有离心轮状的圆盘,当搅拌轴转动时,物料沿轮状圆盘的轴向由中心孔进入叶轮,在各小叶片作用下而获离心加速度,向转轴中心流窜产生涡流而达到搅拌混的目的.所以,在实际工况的低速旋转中,整个搅拌器的结构刚度受到转速的影响而发生改变。
故对实际工况下的搅拌器子进行模态分析是十分必要的。
1 六片斜叶圆盘涡轮搅拌器的模态分析方法应用模态分析方法确定搅拌器的动态特性包括固有频率表,振型和稳态响应。
利用有限元法求解具有不规则集合搅拌器模态,考虑相应软件中的ANSYS Workbench 的线性模态分析方法,因此结合振动学可知,多自由度无阻尼振动方程为(1):2 六片斜叶圆盘涡轮搅拌器的模型建立参考实际搅拌器尺寸,采用UG6.0 绘制搅拌器的三维实体模型,为提高后期网格质量和结果分析的准确性。
仅仅选取搅拌器主体模型。
去除倒角,装配凹槽等细节模型。
保留相应的主轴阶梯状结构,为后期施加提供位置标识。
3 六片斜叶圆盘涡轮搅拌器的模态分析参照搅拌器的实际工况可知,搅拌器由两侧的轴承固定约束,轴承有一定的刚度和阻尼。
而在ANSYS Workbench中的模态分析环节,一般选用计算方法的为线性计算方法,即忽略阻尼对搅拌器系统影响,因此对搅拌器系统的轴承处施加圆柱约束,保证搅拌器符合实际工况条件下的约束。
基于ANSYS的叶片模态分析与创新设计

基于ANSYS的叶片模态分析与创新设计ANSYS是流体、结构、电磁等多物理场仿真分析的领导者,叶片模态分析是ANSYS在燃气轮机和风力发电领域的热点应用之一。
本文将从ANSYS叶片模态分析的基本流程,分析结果的意义以及基于模态分析的叶片创新设计加以介绍。
ANSYS叶片模态分析的基本流程主要包括建模、网格划分、边界条件定义、材料参数设定、求解器选择和结果分析。
在建模时,可以选择不同的叶片结构,如单普通叶片、单普通叶片带平台、双蒸汽冷却叶片等。
在网格划分时,要考虑叶片的形状、大小、复杂程度等因素,以保证计算效率和结果精度。
边界条件包括入口流量、出口压力等,根据不同的模拟场景选取。
在确定材料参数时,需要考虑材料弹性模量、材料密度、材料损伤参数等因素。
求解器选择应根据具体情况选取,如静态应力求解器、压缩流求解器等。
结果分析主要是对计算结果进行后处理,查看叶片的振动频率、振型、动态应力等信息,以确定叶片的任意振型和自由振动频率等数据。
叶片模态分析的结果对叶片的设计、优化和制造具有重要意义。
其中,叶片振动频率和振型是判定叶片的动态性能和稳定性的关键指标,可以直接影响叶片的寿命和可靠性。
动态应力分析可以判断叶片在工作过程中的应力强度和疲劳寿命等参数。
基于叶片模态分析进行的叶片创新设计,主要包括改变叶片几何形状、采用新型材料、改变叶片结构等方面。
比如,可以采用钛合金、高温合金等材料来提高叶片的抗热性能;可以在叶片上加装定位孔来提高抗振性能;可以增加叶片弯曲度、消声器等措施来改善叶片气动损失和减小噪音等。
总之,基于ANSYS的叶片模态分析是在叶片设计、制造和优化过程中不可或缺的工具,它可以帮助工程师查明叶片的动态性能和稳定性,辅助进行叶片的推进优化和改进。
未来,在燃气轮机和风力发电领域的应用前景广阔。
为了阐述相关数据的分析,本文以2021年中国6月份统计局公布的国民经济运行数据为例进行分析。
涉及到GDP、CPI、PPI、PMI、利率等数据。
原创的ANSYS教材10叶轮模态

第N章风机叶轮模态分析案例下面介绍某核电厂用空调风机叶轮模型使用ANSYS WOKBENCH 14.0 机械设模块模态分析功能进行分析,演示其基本操作过程。
1.5.1案例介绍模态分析的经典定义是:将线性定常系统振动微分方程组的物理坐标变换为模态坐标,使方程解耦成为一组以模态坐标及模态参数描述的独立方程以便求出系统的模态参数。
坐标变换的变化矩阵为模态矩阵其每列为模态阵型。
模态分析的最终目标在于改变机械结构系统由经验、类比和静态设计方法为动态、优化设计方法;在于借助于实验与理论分析相结合的方法对已有结构系统进行识别、分析和评价,从中找出结构系统在动态性能上所存在的问题,确保工程结构能安全可靠及有效的工作;在于根据现场测试的数据来诊断和预报振动故障和进行噪声控制。
通过这些方法为老产品的改进和新产品的设计提供可靠的依据。
系统各个阶模态对相应的贡献量或者权系数是不相同的,它与激励的频率结构有关。
一般低阶模态比高阶模态有较大的权系数。
对于实际结构而言,我们感兴趣的往往是它的前几阶或者十几阶模态,更高阶的模态常常被抛弃。
这样尽管会造成一定的误差,单频相应函数的矩阵阶数将大大减少,使计算量大为减少。
实践证明这是完全可取的,这也是模态分析的一大优点,这种处理方式成为模态截断。
可以使用质量点:质点在模态分析中是只有质量(无硬度)的存在,其会降低结构自由振动的频率。
材料属性:杨氏模量,泊松比,和密度是必需的。
由于在结构上没有激励作用,因此振型只是与自由振动相关的相对值。
此次我们使用某核电厂用空调风机的叶轮部件进行模态分析查看其前5阶阵型为结构改进与动力学分析做准备。
1.5.2导入模型(1) 我们使用实际生产图的模型进行分析。
在模型简化上仅仅删除了轮毂与轮盘连接用的铆钉,其他部分未经简化,其与实际模型完全相同。
首先打开SW,并打开模型文件。
如图-1以及图-2所示。
图-1 打开SW 图-2打开模型文件。
(2)打开ANSYS WORKBENCH 程序接口导入模型文件。
ANSYS模态分析

ANSYS模态分析ANSYS模态分析是一种用于计算和研究结构的振动和模态的仿真方法。
它可以帮助工程师和设计师了解结构在自由振动模态下的响应,从而优化设计和改进结构的性能。
本文将对ANSYS模态分析的原理和应用进行详细介绍。
ANSYS模态分析基于动力学理论和有限元分析。
在模态分析中,结构被建模为一个连续的弹性体,通过求解结构的固有频率和模态形状来研究其振动行为。
固有频率是结构在没有外力作用下自由振动的频率,而模态形状则是结构在每个固有频率下的振动形态。
模态分析可以帮助工程师了解结构在特定频率下的振动行为。
通过分析结构的固有频率,可以评估结构的动态稳定性。
如果结构的固有频率与外部激励频率非常接近,可能会导致共振现象,从而对结构造成破坏。
此外,模态分析还可以帮助识别结构的振动模态,并评估可能的振动问题和改进设计。
1.准备工作:首先,需要创建结构的几何模型,并进行必要的网格划分。
在几何模型上设置适当的约束条件和边界条件。
选择合适的材料属性和材料模型。
然后设置分析类型为模态分析。
2.计算固有频率:在模态分析中,需要计算结构的固有频率。
通过求解结构的特征值问题,可以得到结构的固有频率和模态形状。
通常使用特征值求解器来求解特征值问题。
3.分析结果:一旦得到结构的固有频率和模态形状,可以进行进一步的分析和评估。
在ANSYS中,可以通过模态形状的可视化来观察结构的振动模态。
此外,还可以对模态形状进行分析,如计算应力、变形和应变等。
ANSYS模态分析在许多领域都有广泛的应用。
在航空航天工程中,模态分析可以用于评估飞机结构的稳定性和航空器的振动特性。
在汽车工程中,可以使用模态分析来优化车身结构和减少共振噪音。
在建筑工程中,可以使用模态分析来评估楼房结构的稳定性和地震响应。
总之,ANSYS模态分析是一种重要的结构动力学仿真方法,可以帮助工程师和设计师了解结构的振动特性和改善设计。
通过模态分析,可以预测共振问题、优化结构设计、提高结构的稳定性和性能。
基于ANSYS的汽轮机扭曲叶片模态分析
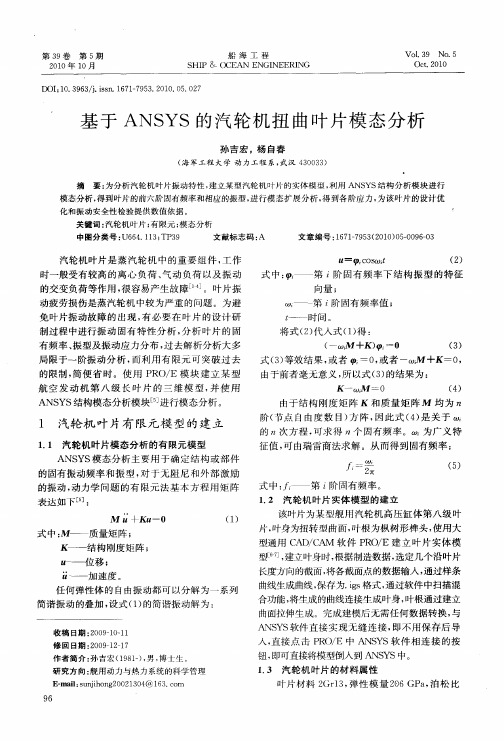
1 汽轮 机 叶 片有 限元模 型 的建 立
1 1 汽轮 机叶片模 态分 析的有 限元模 型 .
ANS YS模态 分析 主要 用 于确 定 结构 或 部件
征值 , 由瑞 雷商法求 解 。从而 得到 固有频率 : 可
f 一 i
兀
的固有 振动频 率 和振 型 , 于无 阻 尼 和外 部 激励 对 的振动 , 动力学 问题 的有 限元 法 基本 方 程 用矩 阵
关 键 词 : 轮 机 叶 片 ; 限 元 ; 态 分 析 汽 有 模
中图 分类 号 : 6 . 1 ; P 9 U64 13 T 3
文 献标 志码 : A
文 章 编 号 :6 17 5 (0 0 0—0 60 17 —93 2 1 ) 50 9—3
U ̄ #iOSot P C oi () 2
作 者 简 介 : 吉 宏 ( 9 1)男 , 士 生 。 孙 18一 , 博 研 究 方 向 : 用 动力 与 热 力 系 统 的 科 学 管理 舰
E mals nio g 0 2 3 4 1 3 c r - i:u j n 2 0 1 0 @ 6 . o h n
9 6
基于 ANS S的汽轮机扭 曲叶片模态分 析—— 孙吉宏 , 自春 Y 杨
汽轮机 叶片 是蒸 汽 轮 机 中 的重要 组 件 , 作 工 时一般 受有 较高 的离 心 负荷 、 动 负 荷 以及 振 动 气 的交变 负荷 等作用 , 容易产 生故 障l ] 很 】 。叶片振 。 动 疲劳损 伤是蒸 汽轮机 中较 为严重 的问题 。为避 免 叶片振 动故 障 的出 现 , 必 要 在 叶片 的设 计 研 有
一
将 式 () 2 代人 式 ( ) : 1得
局 限于一 阶振 动分 析 , 而利 用 有 限元 可 突破 过 去 的 限制 , 便 省 时 。使 用 P O/ 简 R E模 块 建 立 某 型 航 空 发 动 机 第 八 级 长 叶 片 的 三 维 模 型 , 使 用 并
- 1、下载文档前请自行甄别文档内容的完整性,平台不提供额外的编辑、内容补充、找答案等附加服务。
- 2、"仅部分预览"的文档,不可在线预览部分如存在完整性等问题,可反馈申请退款(可完整预览的文档不适用该条件!)。
- 3、如文档侵犯您的权益,请联系客服反馈,我们会尽快为您处理(人工客服工作时间:9:00-18:30)。
2 1传统叶片结构 如图 3所示, 传统叶片
结构简单, 制造加工方便, 此 外与叶片装配的定子结构也 简单, 装配简便, 应用中装配 图效果如图 1所示。但缺点 是叶片顶部与定子为滑动磨 擦, 接触面的受力性能较差,
基金项目: 浙江工商职业技术学院科研项目基金资助 (KYB0812)。 作者简介: 黄仕彪 (1979- ), 男, 福建龙岩人, 浙江工商职业技术学院工学院讲师, 硕士, 研究方向: 机电液技术、CAE, 发表论文 4篇。 收稿日期: 2010- 10- 13
K ey words: vane; ANSY S; moda l ana lysis; noise reduction
0 前言
在液压传动技术领域, 叶片泵是目前工业使用较多的液 压泵, 衡量叶片泵性能的重要指标主要是泵的振动和噪声高 低问题。近年来, 国内外的高校、科研院所在叶片泵降噪方面 的进行了大量的研究, 取得了一定的成果。随着叶片泵向高 压、高转速方向发展, 国产的叶片泵运转长时间运行后的噪声 和振动问题依然突出, 一直没有很好地解决, 振动和噪声导致 大量的能量损耗, 降低了液压系统效率。
50
现代机械 2010年第 6期
基于 ANSYS的叶片模态分与创新设计*
黄仕彪
(浙江工商职业技术学院 工学院, 浙江 宁波 315012)
摘要: 本文提出新型叶片结构, 使叶片与定子由传统的滑动磨擦改变为滚动磨擦, 有效减小叶片磨损。利用有限元软件 AN SYS 的模态分析技术, 通过对叶片结构进行优化设计可以得到合理结构的新型叶片, 达到节能降噪的目的。 关键词: 叶片 ANSY S 模态分析 降噪 中图分类号: TB123 文献标识码: A 文章编号: 1002- 6886( 2010) 06- 0050- 03
[ J]. 湖南工程学院学报, 2007, 17( 4): 31 34 [3]那焱青, 李少年, 王峥嵘, 那成烈. 关于子母叶片泵叶片的 受力分析
[ J]. 兰州理工大学学报, 2004, 30 ( 4) : 61 63 [4]雷亚勇, 吴晓明, 陈春明. 双作用叶片泵噪声的产生机理和降噪分析
[ J]. 机床与液压, 2007, 35( 1): 145 147 [5]张驰云, 沈双达, 金杨洁. 叶片式转向助力泵定子曲线优化设计 [ J]. 机
出现在第 29阶, 而新型叶片结构的纵向模态振型出现在第 34阶, 说明结构较复杂的新型叶片的模态比结构简单的传统 叶片更多, 即新型叶片比传统叶片的固有频率阶次更多, 在相 同条件下, 新型叶片比传统叶片更容易被激振源激励而引起 共振。但只要用有限元软件准确分析出新型叶片的各阶固 有频率, 并计算出激励源的激振频率, 只要能做到两者不相 等, 就完全能够避免共振的发生。
1 叶片的受力分析
传统叶片泵的结构如图 1所示, 主要由定子、转子、叶片、 配流盘等组成。叶片在定子曲线上划动时, 叶片顶部受到定 子内曲线的两个作用力, 如图 2所示, 叶片与定子为滑动磨 擦, F1 为定子对叶片的接触反作用力, 方向沿 A 点处定子曲
线的法线方向, F2 为定子对叶片的摩擦力, 方向沿 A 点处定 子曲线的切线方向, 且 F2 = f F1, f 为叶片与定子的摩擦系 数。由于工作中叶片高速旋转的惯性力、液压力的作用, 叶片 顶部 A点磨损较大, 叶片顶部逐渐被磨成一个平面, 导致叶 片与定子曲面的接触面增大, 进而引起摩擦力 F2 增大。
械设计与制造, 2007(1): 19 20 [6]郑开陆. 叶片泵制造的研究, 液压与气动 [ J]. 2006( 2): 21 23 [7] E iich i Kojmi a. Developm ent of a Qu ieter Variable dispacem ent Vane
pump for AutomotiveH ydrau lic pow er Steering sys tem [ J]. In ternational journal of F luid Pow er, 2003( 4). [8]雷天觉. 液压工程手册 [M ]. 北京: 机械工业出版社, 1990
叶片泵的噪声有机械噪声和流体噪声两部分构成[ 1- 3] , 机械噪声为其主要成份, 机械噪声与定子曲线形状、转子及叶 片的结构等相关, 机械噪声主要是叶片与定子内表面磨擦、撞 击产生的。叶片泵的技术难点在于解决叶片运动过程中对 定子的冲击, 以及如何进一步改善叶片的受力、减少磨损。虽 然定子高次曲线的应用在理论上保障了叶片运动的平稳性, 但由于叶片顶部结构为尖角状或圆弧廓状, 叶片在运动中与 定子仍然存在较大的磨擦, 引起噪声, 此外叶片在高速旋转过 程中, 当激振频率与叶片的某阶固有频率相等时, 会引起叶片 剧烈的振动。
M odal Analysis and Innovative Design for the Vane Based on ANYSY
HUANG Shibiao
Abstract: A new vane structure is d iscussed in this paper. T he abrasion of vane is e ffic iently reduced by chang ing sliding fr iction into ro lling friction. The freedom modal ana lysis techno logy of finite element analysis so ftwareANSYS is used, a rational new vane structure can be obtained by optmi a l design for the structura l o f van, then purpose o f energy sav ing and no ise reduction can be attained.
51
问题, 下面利用用有限元软 件对叶片进行模态分析, 求 解两种叶片的各阶固有频 率及相应模态振型, 为解决 新型叶片在工作中因共振 而引起的噪声问题, 提供参 考解决方法。
把叶片结构网格划分, 取 SOLID45单元, 叶片的有 限元网格图如图 10、11 所 示。材料属性输入杨氏模量 E = 2. 2 1011 Pa, 泊松比为 0. 31, 密度 r= 7 800 kg/m3。求解传统叶片结构前 30阶、新型叶片 结构前 35阶的固有频率, 各阶固有频率结果如图 12、13所 示。图中数据显示, 从第 7阶开始, 两种叶片都有固有频率, 且在相同阶次中, 传统叶片的固有频率比新型叶片的固有频 率数值更大些。
参考文献
[1]张晓黎, 雷波, 王六一, 陈静波. 模流分析在电动机护罩注塑模设计中 的应用 [ J]. 工程塑料应用, 2009(4): 67 69
[2]余玲, 陈忠桂, 张天柱. 基于 M oldFlow 技术优化塑件设计 [ J]. 模具制 造, 2009( 1): 8, 9, 54
[3]严志云, 谢鹏程, 丁玉梅等. 基于 M oldflow 塑料齿轮注射模浇注系统 设计 [ J]. 模具制造, 2009( 11): 14 16
前面设计了新型叶片结构, 以改善传统叶片结构的受力
通过逐一查找各阶模态振型, 其中可以找到传统叶片结 构的横向振型图如图 14 所示, 固有频率是第 18 阶 51. 604
52
现代机械 2010年第 6期
H z; 纵向振型图如图 15所示, 固有频率是第 29阶 83. 384 H z。 同理, 可以找到新型叶片结构的横向振型图如图 16所示, 固 有频率是第 19阶 43. 169 H z; 纵向振型图如图 17所示, 固有 频率是第 29阶 77. 893 H z。在谐振状态, 叶片的横向振型、纵 向振型分别对泵体的定子和侧盖能产生剧烈的冲击和噪声, 对叶片及相关泵体磨损较大。
(上接第 34页 ) 方案三的充填时间长且冷流道体积太多。从生产效率、
经济节约的角度考虑, 优先选用方案二。
3 结束语
注塑模具浇注系统选择的恰当与否, 直接决定着塑件的 性能、质量和生产效率。
本文针对两塑料制品的四腔 ( 2+ 2)注塑成型设计了三 套浇注系统, 并利用 M old flow 软件对其注塑成型过程进行了 模拟分析, 得出了最优浇注系统方案, 减少了设计中的盲目 性, 进而提高了一次试模的成功率。
参考文献
工作中叶片的激振频率取决于电机转速, 因此对应于电 机的不同转速, 激振频率也不同, 当激振频率达到叶片相应的 固有频率时, 会导致叶片共振, 引起叶片剧烈振动, 使叶片泵 产生噪声和振动。例如, 假设电机转速为 970 r/m in, 则激振 频率为 16. 667H z。从图 12、13可见, 设计的叶片有很多阶固 有频率, 因此在应用中为了有效避免叶片泵因共振引起的振 动和噪声, 有两种方法, 一是要避免叶片的激励频率等于叶片 任何一阶的固有频率。二是在已知激励频率的情况下, 通过 结构优化设计, 使叶片的固有频率不等于激励频率。
3 结论
通过总结前人关于叶片泵噪声的主要来源的研究结果, 指出传统叶片结构与定子的受力模型存在缺陷, 是引起叶片 泵机械噪声的原因之一。本文提出一种新型叶片结构, 能够 改善叶片与定子在运动中的磨损, 用有限元软件 ANSYS对新 型叶片进行模态分析, 求解它们的各阶固有频率的大小、模态 振型, 为叶片的结构优化设计提供参考依据。通过结构设计 与有限元分析, 理论上新型叶片结构具有可行性, 有一定的实 际应用价值, 能够避免叶片在工作中产生共振, 减小叶片泵的 噪声和振动, 从而能达到节能降噪的目的。
计算机应用
叶片运转时的摩擦力较大, 容易引起叶片与定子的剧烈磨损 和系统噪声。 2 2新型叶片结构
为了改善传统叶片受力 状况, 在传统叶片的基础上 改进, 设计一种新型叶片结 构, 新型叶片结构由叶片、滚 动体、销钉、螺钉四个部分组 成, 如图 4至 8所示。其中, 如图 4b 的叶片空间框架图 所示, 叶片的顶部开有滚动 体的滚槽, 滚槽左侧是滚动 体支撑孔, 滚槽右侧打螺纹 孔, 叶片底部设有一个方形 槽腔, 用于安装弹簧, 弹簧提 供叶片 与转子之间的弹簧 力, 使叶片运转时能够始终 压紧定子。