刹车盘毕业设计
轿车盘式制动器毕业设计

摘要轿车的设计与生产涉及到了很多的领域,其安全性、经济性、动力性的相关指标,对设计提出了较高要求。
轿车制动系统是轿车正常行驶的重要主动安全系统,其性能的好坏对轿车的正常行驶安全有着重要影响。
伴随着轿车行驶速度和路面复杂程度的变化,迫切需要更高性能的制动器。
由于制动系统的重要性,本次设计的主要目的是轿车制动器的结构类型设计。
本文从制动系统的作用和设计的要求出发,对各种样式制动器的优缺点进行了比较,并依据已给的设计参数,进行方案分析验证及校核。
得出,轿车的前后轮均采用浮钳盘式制动器。
在此基础上,选择了真空助力式伺服制动系统和双管路系统,选用了间隙自动调节装置。
依据设计和计算出的数据,分别用AUTO CAD和CATIA软件绘制出了该制动器的二维图和三维建模。
关键词:制动器;设计;建模ABSTRACTThe design and production of cars involved a lot of fields, the safety, economy and power of the relevant indicators, the design of a higher demand. Car braking system is an important active safety system, and its performance has important influence on the normal running safety of the car. Along with the change of the speed of the car and the complexity of the road surface, it is urgent to need a better performance of the brake.Due to the importance of the braking system, the main purpose of this design is to design the structure type of the car brake. In this paper, the advantages and disadvantages of various styles of brake are compared, based on the function and design requirements of the braking system, and the design parameters are given. It is concluded that the floating caliper disc brake is used in the front and back wheels of the car. On this basis, the selection of vacuum assisted brake servo system and dual system, use the automatic clearance adjustment device. According to the design and calculation of the data, respectively, using CAD AUTO and CATIA software to draw the two-dimensional map and three-dimensional modeling of the brake.Key words: brake; design; modeling目录摘要 (I)1 绪论 (1)1.1课题研究的目的及意义 (1)1.2轿车制动器的发展状况 (1)2 研究课题简介 (3)2.1课题主要内容 (3)2.2课题研究方案 (3)2.3本章小结 (4)3 制动器的结构形式 (5)3.1制动系统的基本概念 (5)3.2鼓式制动器结构形式简介 (6)3.3盘式制动器结构形式简介 (8)3.4盘式制动器的优缺点 (9)3.5该轿车制动器结构的最终选择 (9)3.6本章小结 (10)4 制动器主要参数及其选择 (11)4.1制动力与制动力分配系数 (11)4.2同步附着系数 (15)4.3制动强度和附着系数利用率 (16)4.4制动器最大制动力矩 (17)4.5制动器因数 (19)4.6盘式制动器主要参数的确定 (19)4.7本章小结 (20)5 制动器的设计计算 (21)5.1摩擦衬块的磨损特性计算 (21)5.2制动器的热容量和温升核算 (22)5.3盘式制动器制动力矩的计算 (23)5.4驻车制动计算 (24)5.5本章小结 (25)6 制动器主要零部件的结构设计 (26)6.1制动盘 (26)6.2制动钳 (26)6.3制动块 (27)6.4摩擦材料 (27)6.5制动轮缸 (28)6.6制动器间隙 (28)6.7本章小结 (29)7 制动驱动机构的结构形式选择与设计计算 (30)7.1 制动驱动机构的结构型式选择 (30)7.2 制动管路的多回路系统 (32)7.3 液压制动驱动机构的设计计算 (33)7.3.1制动轮缸直径与工作容积 (33)7.3.2制动主缸直径与工作容积 (35)7.3.3制动踏板力与踏板行程 (35)7.3.4制动主缸 (36)7.4 本章小结 (36)8 CATIA建模 (37)8.1CATIA软件 (37)8.2绘制的主要CATIA零件图 (38)结论 (40)参考文献 (41)致谢 (43)附录A (44)附录B (53)1绪论1.1课题研究的目的及意义轿车的构设和产出涉及到许多范围,对构设提出了更高的要求。
盘式制动器毕业设计

毕业设计(论文、作业)毕业设计(论文、作业)题目:盘式制动器设计分校(点):浦东分校年级、专业:12 机电一体化教育层次:大学专科学生姓名:乔倪杰学号:128041103指导教师:诸杭完成日期:目录Abstract (II)1 绪论 (1)1.1 制动器的作用 (1)1.2 制动器的种类 (1)1.3 制动器的组成 (1)1.4 对制动器的要求 (3)1.5 制动器的新发展 (4)2 制动器的结构形式及选择 (5)2.1 制动器的种类 (5)2.2 盘式制动器的结构型式及选择 (6)3 盘式制动器的设计 (7)3.1 盘式制动器的结构参数与摩擦系数的确定 (8)3.2 制动衬块的设计计算 (9)3.3 摩擦衬块磨损特性的计算 (10)3.4 制动器主要零件的结构设计 (11)4 制动驱动机构的结构型式选择与设计计算 (12)4.1 制动驱动机构的结构型式选择 (13)4.2制动管路的选择 (14)4.3 液压制动驱动机构的设计计算 (15)5 盘式制动器的优化设计 (17)5.1 优化设计概述 (17)5.2 解决优化设计问题的一般步骤及几何解释 (17)5.3 常用优化方法 (18)5.4 制动系参数的优化 (18)6 结论 (19)致谢 (21)参考文献 (22)附录................................................. 错误!未定义书签。
摘要汽车的制动系是汽车行车安全的保证,许多制动法规对制动系提出了许多详细而具体的要求,这是我们设计的出发点。
从制动器的功用及设计的要求出发,依据给定的设计参数,进行了方案论证。
对各种形式的制动器的优缺点进行了比较后,选择了前盘的形式。
这样,制动系有较高的制动效能和较高的效能因素稳定性。
随后,对盘式制动器的具体结构的设计过程进行了详尽的阐述。
选择了简单液压驱动机构和双管路系统,选用了间隙自动调节装置。
在设计计算部分,选择了几个结构参数,计算了制动系的主要参数,盘式制动器相关零件以及驱动机构的设计计算。
盘式制动器_毕业设计说明书参考

盘式制动器_毕业设计说明书参考(以下是机械设计专业的毕业设计说明书范例,供参考)毕业设计题目:盘式制动器设计一、题目来源及背景盘式制动器是用于汽车、摩托车等机动车辆的制动装置之一,具有制动力矩大、耐磨损、散热快等优点。
本毕业设计项目充分利用机械设计、材料学等方面知识,对盘式制动器的制动器件进行设计。
二、设计要求1. 主要技术指标:(1)制动力矩:大于100 N·m(2)使用寿命:大于2×10⁴次(3)材料:盘式制动器盘采用GCr15;制动蹄采用40Cr;制动片采用半金属材料。
2. 设计思路(1)整体结构设计:盘式制动器的整体结构以制动盘、制动蹄、制动片、制动器液压缸等组成。
其中,制动盘为主动件,制动蹄和制动片为被动件,液压缸提供制动力。
(2)制动盘设计:制动盘是盘式制动器的核心部件,由于需要承受制动力矩,因此采用GCr15高强度材料。
制动盘的直径和厚度由制动力矩、车辆重量等因素决定。
(3)制动片设计:制动片采用半金属材料,能够在制动过程中承受高温、高压。
制动片的表面采用刻花纹路,以增加摩擦面积和摩擦系数。
(4)制动蹄设计:制动蹄采用40Cr合金钢,具有足够的强度和硬度。
制动蹄的设计应考虑制动片与制动盘之间的间隙,以确保能够实现完整制动。
(5)液压缸设计:液压缸的设计应考虑到制动盘的直径和轮轴间隙,能够提供足够的制动力矩。
液压缸的设计也应考虑到防泄漏、稳定等因素。
三、设计过程1. 制动盘设计(1)根据制动力矩、车辆重量等因素确定制动盘的直径和厚度。
(2)采用CAD软件进行3D建模,并进行有限元分析,得出制动盘在制动力矩作用下的应力分布情况和变形情况。
(3)结合分析结果,调整制动盘的厚度和结构。
(4)根据制动盘的设计尺寸和结构参数,进行加工和表面处理,确保制动片和制动盘之间具有充分的接触面积和摩擦力。
2. 制动片设计(1)选择半金属材料作为制动片材料。
根据制动盘的直径和表面处理情况,设计制动片的形状和尺寸。
毕业设计浮钳盘式制动器

原始数据:整车质量:空载:1550kg ;满载:2000kg质心位置:a=L 1=1.35m ;b=L 2=1.25m质心高度:空载:hg=0.95m ;满载:hg=0.85m轴 距:L=2.6m轮 距: L 0=1.8m最高车速:160km/h车轮工作半径:370mm轮毂直径:140mm轮缸直径:54mm轮 胎:195/60R14 85H1.同步附着系数的分析(1)当0φφ<时:制动时总是前轮先抱死,这是一种稳定工况,但丧失了转向能力;(2)当0φφ>时:制动时总是后轮先抱死,这时容易发生后轴侧滑而使汽车失去方向稳定性;(3)当0φφ=时:制动时汽车前、后轮同时抱死,是一种稳定工况,但也丧失了转向能力。
分析表明,汽车在同步附着系数为0φ的路面上制动(前、后车轮同时抱死)时,其制动减速度为g qg dt du 0φ==,即0φ=q ,q 为制动强度。
而在其他附着系数φ的路面上制动时,达到前轮或后轮即将抱死的制动强度φ<q ,这表明只有在0φφ=的路面上,地面的附着条件才可以得到充分利用。
根据相关资料查出轿车≥0φ0.6,故取6.00=φ.同步附着系数:=0φ0.62.确定前后轴制动力矩分配系数β常用前制动器制动力与汽车总制动力之比来表明分配的比例,称为制动器制动力分配系数,用β表示,即:u F Fu 1=β,21u u u F F F +=式中,1u F :前制动器制动力;2u F :后制动器制动力;u F :制动器总制动力。
由于已经确定同步附着系数,则分配系数可由下式得到: 根据公式:L h L g02φβ+= 得:68.06.285.06.025.1=⨯+=β 3.制动器制动力矩的确定为了保证汽车有良好的制动效能,要求合理地确定前,后轮制动器的制动力矩。
根据汽车满载在沥青,混凝土路面上紧急制动到前轮抱死拖滑,计算出后轮制动器的最大制动力矩2M μ由轮胎与路面附着系数所决定的前后轴最大附着力矩:e g r qh L LG M ϕυ)(1max 2-= 式中:ϕ:该车所能遇到的最大附着系数;q :制动强度;e r :车轮有效半径;max 2μM :后轴最大制动力矩;G :汽车满载质量;L :汽车轴距;其中q=g h a a ⨯-+)(0ϕϕϕ=85.0)6.07.0(35.17.035.1⨯-+⨯=0.66 故后轴max 2μM =3707.0)85.066.035.1(6.220000⨯⨯⨯-=1.57610⨯Nmm 后轮的制动力矩为2/1057.16⨯=0.785610⨯Nmm前轴max 1μM = T max 1f =max 21f T ββ-=0.67/(1-0.67)⨯1.57610⨯=3.2610⨯Nmm前轮的制动力矩为3.2610⨯/2=1.6610⨯Nmm2.浮钳盘式制动器主要结构参数的确定2.1制动盘直径D制动盘直径D 希望尽量大些,这时制动盘的有效半径得以增大,就可以降低制动钳的夹紧力,降低摩擦衬块的单位压力和工作温度。
本科毕业设计_盘式制动器设计说明
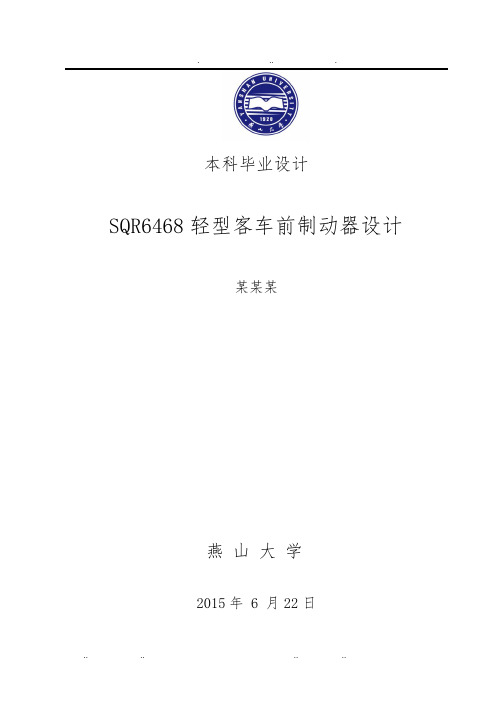
本科毕业设计SQR6468轻型客车前制动器设计某某某燕山大学2015年 6 月22日本科毕业设计SQR6468轻型客车前制动器设计学院:专业:车辆工程学生:某某某学号: 3指导教师:某某某答辩日期: 2015.6.22燕山大学毕业设计任务书摘要本文首先对汽车制动器原理和对各种各样的制动器进行分析,详细地阐述了各类制动器的结构,工作原理和优缺点.再根据轻型客车的车型和结构选择了适合的方案.根据市场上同系列车型的车大多数是滑钳盘式制动器,而且滑动钳式盘式制动器结构简单,性能居中,设计规,所以我选择滑动钳式盘式制动器.本文探讨的是一种结构简单的滑动钳式盘式制动器,对这种制动器的制动力,制动力分配系数,制动器因数等进行计算.对制动器的主要零件如制动盘、制动钳、支架、摩擦衬片、活塞等进行结构设计和设计计算,从而比较设计出一种比较精确的制动器.本文所采用的设计计算公式均来自参考资料。
本设计主要针对轻型客车前制动器设计,首先计算数据,完成二维装配图和二维零件图绘制,然后利用CATIA软件进行三维建模。
以更清楚的表达盘式制动器结构。
关键词盘式制动器;制动力;制动力分配系数;制动器因数;CATIA软件AbstractThis paper first principle of the car brake and brake on a wide range of analysis,a detailed exposition of the structure of various types of brake, and the advantages and disadvantages of working principle. Accordance with Minibus models and structure chosen for the program Under series models on the market with most of the cars leading trailing, and leading trailing simple structure, performance, middling, design specifications, so I chose to receive from the Sliding Disc brake. This paper is a simple structure recipients from the Disc brake, the brake system of this power, braking force distribution coefficient, such as brake factor calculation. brake on the main parts such as brake pan, brake caliper, bracket, friction linings, piston for structural design and design, design and comparison A more precise brake used in the design of this formula are calculated from the reference.This design mainly in view of the light bus front brake design, calculation data first, finish 2 d assembly drawing and 2 d part drawing, And then using CATIA software for 3 d modeling, to more clearly express the structure of disc brake.Key words Disc brakes;Power system;Power distribution coefficient systemBrake factor CATIA software目录摘要 (II)Abstract (II)第1章绪论 (1)1.1 课题背景 (1)1.2 研究目的及意义 (1)1.3 盘式制动器结构形式及其选择 (3)1.3.1 盘式制动器的结构形式 (3)1.3.2 盘式制动器的优缺点 (4)1.3.3 本设计盘式制动器的选择 (5)1.4 浮钳盘式制动器 (5)1.4.1 浮钳盘式制动器的结构 (5)1.4.2 浮钳盘式制动器的工作原理 (6)1.4.3 制动间隙调整原理 (7)1.5 本文研究容 (8)第2章制动系的主要参数及其选择 (9)2.1 任务书给定设计基本参数 (9)2.2 受力分析 (9)2.3 同步附着系数的确定及计算 (13)2.4 制动力、制动强度、附着系数利用率的计算 (15)2.4.1 满载时的情况 (15)2.4.2 空载的情况 (17)2.5 制动器最大制动力矩的计算 (19)2.6 本章小结 (19)第3章盘式制动器的结构设计 (20)3.1 盘式制动器结构设计的任务和步骤 (20)3.2 盘式制动器的主要零部件设计和三维造型 (20)3.2.1 制动盘 (21)3.2.2 制动衬块 (22)3.2.3 制动钳 (23)3.2.4 制动钳支架 (24)3.2.5 盘式制动器总成装配图 (26)3.3 本章小结 (26)第4章盘式制动器的校核计算 (27)4.1 摩擦衬块的磨损特性计算 (27)4.2制动器的热容量和温升的核算 (28)4.3 盘式制动器制动力矩的校核 (29)4.4 本章小结 (32)结论 (33)参考文献 (34)致 (36)附录1 (38)附录2 (364)附录3 (48)第1章绪论1.1 课题背景对制动器的早期研究侧重于试验研究其摩擦特性,随着用户对其制动性能和使用寿命要求的不断提高,有关其基础理论与应用方面的研究也在深入进行。
毕业设计浮钳盘式制动器

原始数据:整车质量:空载:1550kg;满载:2000kg质心位置:a=L1=1.35m;b=L2=1.25m 质心高度:空载:hg=0.95m;满载:hg=0.85m 轴距:L=2.6m轮距: L 0=1.8m最高车速:160km/h车轮工作半径:370mm轮毂直径:140mm轮缸直径:54mm轮胎:195/60R14 85H1.同步附着系数的分析(1)当0 时:制动时总是前轮先抱死,这是一种稳定工况,但丧失了转向能力;(2)当0 时:制动时总是后轮先抱死,这时容易发生后轴侧滑而使汽车失去方向稳定性;(3)当0 时:制动时汽车前、后轮同时抱死,是一种稳定工况,但也丧失了转向能力。
分析表明,汽车在同步附着系数为0的路面上制动( 前、后车轮同时抱死)时,其制动减速度为du dt qg 0g ,即q 0,q为制动强度。
而在其他附着系数的路面上制动时,达到前轮或后轮即将抱死的制动强度q , 这表明只有在0的路面上,地面的附着条件才可以得到充分利用。
根据相关资料查出轿车 0 0.6 ,故取 0 0.6. 同步附着系数: 0 0.62. 确定前后轴制动力矩分配系数常用前制动器制动力与汽车总制动力之比来表明分配的比例,称为制动器制动 F 力分配系数,用 表示,即:u1, F u F u1 F u2u式中, F u 1 :前制动器制动力; F u2 :后制动器制动力; F u :制动器总制动力3. 制动器制动力矩的确定 为了保证汽车有良好的制动效能,要求合理地确定前,后轮制动器的制动力矩 根据汽车满载在沥青,混凝土路面上紧急制动到前轮抱死拖滑,计算出后轮制 动器的最大制动力矩 M 2由轮胎与路面附着系数所决定的前后轴最大附着力矩:GM2max(L1 qh g) re2max L 1 g e式中: :该车所能遇到的最大附着系数;q :制动强度; r e :车轮有效半径;M 2max :后轴最大制动力矩;根据公式:L 2 0hgL由于已经确定同步附着系数,则分配系数可由下式得到: 1.25 0.6 0.852.6 得:后轮的制动力矩为 1.57 106/ 2 =0.785 106Nmm前轴 M 1max = T f1max = T f2max =0.67/(1-0.67) 1.57 10 6=3.2 10 6Nmm 1 前轮的制动力矩为 3.2 106/2=1.6 106Nmm2. 浮钳盘式制动器主要结构参数的确定 2.1 制动盘直径 D制动盘直径 D 希望尽量大些,这时制动盘的有效半径得以增大,就可以降低制 动钳的夹紧力,降低摩擦衬块的单位压力和工作温度。
毕业设计论文轿车盘式制动器设计及优化

行车制动装置和驻车制动装置,都由制动器和制动驱动机构两部分组成。
任何制动系都是由以下4个部分组成:
(1)供能装置。包括供给、调节制动所需能量以及改善传能介质的各个部件。
(3)制动稳定性好。由于盘式制动器的制动力矩与其制动油缸的活塞推力及摩擦系数成线性关系,还由于无自行增势作用,因此在制动过程中制动力矩增长较缓和,与鼓式制动器相比,能保证高的制动稳定性。
(4)制动力矩与汽车前进和后退的行驶状态无关。
(5)在输出同样大小的制动力矩条件下,盘式制动器的结构尺寸和质量比鼓式的要小。
摩擦式制动器按其旋转元件的形状又可分为鼓式和盘式两大类。
鼓式制动器又分为内张型鼓式制动器和外束型鼓式制动器。由于外束型鼓式制动器通常简称为带式制动器,而且在汽车上已很少采用,所以内张型鼓式制动器通常简称为鼓式制动器,而通常所说的鼓式制动器即是内张型鼓式结构。
盘式制动器的旋转元件是一个垂向安放且以两侧面为工作面的制动盘,其固定摩擦元件一般是位于制动盘两侧并带有摩擦片的制动块。当制动盘被两侧的制动块夹紧时,摩擦表面便产生作用于制动盘上的摩擦力矩。盘式制动器常用作轿车的车轮制动器,也可用作各种汽车的中央制动器。
(2)控制装置。包括产生制动作用和控制制动效能的各个部件。
(3)传动装置。包括将制动能量传到制动器的各个部件及管路,如制动主缸、轮缸及连接管路。
(4)制动器。产生阻碍车辆运动或运动趋势的力的部件。一般通过固定元件与旋转元件工作表面之间的摩擦作用来实现。
较完善的制动系还应具有制动力调节装置、报警装置、压力保护装置等附加装置。
汽车盘式制动分析毕业设计论文

3
制动器刚体模型分析........................................................................................................15 3.1 多刚体系统动力学................................................................................................. 15 3.1.1 3.1.2 3.1.3 3.1.4 3.2 多刚体系统的坐标系...................................................................................15 多刚体系统组成成分...................................................................................15 多刚体系统的自由度...................................................................................16 多刚体系统的动力学方程...........................................................................16
关键词:盘式制动器;虚拟样机;振动;多柔体模型
I
沈阳理工大学学士学位论文
Abstract
With the development of the economy,the vehicles have been one of the best means of transportation in modern time.Because the brakes play an important part in the vehicles’Safety and Comfort,how to reduce the cars’brake vibration and noise has become an important research topic. First the paper introduced the history of brakes.the research status of brake vibration,then introduced a multi-body dynamic model of the basic theory and self-excited vibration theoretical of the disc brake vibration.All these theories provide a feasible means for further develop.Next,introduced how to build the flexible multi-body of the brake system using the FEA technology and the multi-body dynamic technology.Including hhow to get the model neutral file(MNF)of the brake disc and brake pad by utilizing the FEA technology.In the process of building the MNF,the free model analysis of the brake disc and pads were studied.Introduced the process of the multi-body dynamics modeling:import flexible bodies and rigid bodies,in order to calculate accurately,should gave the rigid bodies a certain material properties,add the constraints between the disc and brake pads were achieved by the contact command. The brake angular velocity and acceleration curves can be carried out by dynamical simulation and analysis.The flexible multi-body model not only concerned the flexibility deformation of the components of the brake system,but also concerned the influence of moment of inertia of the rotating components of the automobile,so the simulation was more reasonable.The method of building the flexible multi-body model is universal and it can be useful for future disk brake noise analysis and structural optimization design.
- 1、下载文档前请自行甄别文档内容的完整性,平台不提供额外的编辑、内容补充、找答案等附加服务。
- 2、"仅部分预览"的文档,不可在线预览部分如存在完整性等问题,可反馈申请退款(可完整预览的文档不适用该条件!)。
- 3、如文档侵犯您的权益,请联系客服反馈,我们会尽快为您处理(人工客服工作时间:9:00-18:30)。
河南工业职业技术学院机械加工技术课程设计说明书设计题目:设计“刹车盘”零件的机械加工工艺规程及工艺装备班级设计者沉默指导教师机械制造工艺学课程设计任务书题目:汽车刹车盘零件的加工工艺规程生产纲领: 5000件生产类型:批量生产内容:1.产品零件图 1张2.产品毛坯图 1张3.机械加工工艺过程卡片 1套4.机械加工工序卡片 1套5. 课程设计说明书(5000~8000字) 1份班级学生沉默指导教师目录前言……………………………………………………………………………………………课程设计说明书正文…………………………………………………………………………一、零件的分析……………………………………………………………………………(一)、零件的作用………………………………………………………………………(二)、零件的工艺性分析………………………………………………………………二、确定生产类型…………………………………………………………………………三、确定毛坯………………………………………………………………………………(一)、确定毛坯的种类………………………………………………………………(二)、绘制铸造件毛坯图……………………………………………………………四、工艺规程设计…………………………………………………………………………(一)定位基准的选择……………………………………………………………………(二)工艺路线的拟定……………………………………………………………………(三),机械加工余量、工序尺寸及毛坯尺寸的确定…………………………………`五、工装设计分析提设计任务书……………………………………………………………六、小结…………………………………………………………………………………………七、主要参考文献………………………………………………………………………………前言机械制造工艺学课程是在学完了机械制造工艺学包括机床夹具设计和大部分专业课,并进行了生产实习的基础上的一个教学环节。
这是我们在进行毕业设计之前对所学课程的一次深入的全面的总复习,也是一次理论联系实际的训练。
因此,它在今年的学习中占有重要的地位。
我个人的感想是,希望经历了这次课程的设计,对自己的将来所从事的工作,进行一次适应性的训练,通过这次课程设计锻炼自己的分析问题,解决问题的能力,为毕业后的工作打下一个良好的基础。
由于自己的理论知识的不完善,实践能力的缺乏,设计之中不免有一些不合理的地方,学生我肺腑的恳请各位老师能够给予指教批评。
一零件的分析(一)零件的作用刹车目前有盘刹和鼓刹,老一些的车很多都是前盘后鼓的。
现在的车很多前后都是盘刹的。
因为盘刹较鼓刹的散热好,在高速制动状态下,不容易产生热衰退,所以其高速制动效果好。
但在低速冷闸时,制动效果不如鼓刹。
价格比鼓刹贵。
所以现在很多中高级轿车采用全盘刹,而普通轿车采用前盘后鼓,而相对低速,且需要制动力大的卡车、巴士,仍采用鼓刹。
(二)零件的工艺分析该零件为汽车刹车盘,安装在轴上,形状一般,精度要求并不高,零件的主要技术要求分析如下:(参阅附图1)(1)由零件图可知,零件的左右端面有粗糙度要求,其余的表面精度要求并不高,只需按照铸造时的精度即可。
铸件要求不能有砂眼、疏松等缺陷,以保证零件的强度、硬度及疲劳度,在静力的作用下,不至于发生意外事故。
(2)零件的端面的安装孔位置精度要求较高。
二、确定生产类型已知此刹车盘零件的生产纲领为50000件/年,零件的质量不到5Kg,查《机械制造工艺与夹具》第7页表1.1-3,可确定该零件生产类型为大批量批生产,所以初步确定工艺安排为:加工过程划分阶段;工序适当集中;加工设备以通用设备和专用夹具为主,采用专用工装。
三确定毛坯(1)确定毛坏种类零件材料为HT200,考虑零件在机床运行过程中所受冲击不大,零件结构又比较简单,生产类型为大批量生产,故选择木摸手工砂型铸件毛坯。
查《机械制造工艺设计简明手册》第41页表2.2-5,选用铸件尺寸公差等级为CT-9。
这对提高生产率,保证产品质量有帮助。
此外为消除残余应力还应安排人工时效。
(2)绘制铸造件零件图四、工艺规程的设计(一)定位基准的选择根据零件图纸及零件的使用情况分析及毛坯的铸造情况,应用卡槽作定位基准,然后加工出左端面用作精基准。
故对基准的选择应予以分析。
(1)粗基准的选择按照粗基准的选择原则为保证不加工表面和加工表面的位置要求,毛坯选择铸造卡槽作为粗基准。
根据零件图所示,毛坯的散热卡槽。
(2 )精基准的选择考虑要保证零件的加工精度和装夹准确方便,依“基准重合”原则和“基准统一”原则,以粗加工后的右端面为主要的定位精基准,用卡盘卡紧,进行切削。
(二)工艺路线的拟定根据零件的几何形状、尺寸精度及位置精度等技术要求,以及加工方法所能达到的经济精度,在生产纲领已确定的情况下,可以考虑采用数控车床、通用转床配以专用工卡检具,并尽量使工序集中来提高生产率。
除此之外,还应当考虑经济效果,以便使生产成本尽量下降。
选择零件的加工方法及工艺路线方案如下:方案一:工序一:以散热卡槽为粗基准粗车刹车盘的大端面,内圆面及内外圆倒角。
采用CA6150卧式车床加工。
工序二:以刹车盘大端面为基准粗车零件小端面、装配孔及外圆面及所要求倒角。
采用CA6150卧式车床加工。
工序三:再次以散热卡槽为粗基准半精车刹车盘的大端面,内圆面及内外圆倒角。
为了提高精度和提高效率,此序采用CAk6150N卧式数控车床加工。
工序四:再以三序刹车盘大端面为基准半精车零件小端面、装配孔及外圆面及所要求倒角。
采用CA6150卧式车床加工。
工序五:以大端面为水平基准,小端面内孔为定位基准,转削凸圆面的4个定位装配孔。
采用Z3040转床。
工序六:以小端面内孔壁厚为定位精基准,对工件大外圆两平行端面进行磨削精加工。
采用改装后的砂轮CAK6150N进行加工。
根据工序方案制定出详细的工序划分如下所示:毛坯为精铸件,清理后,退火处理,以消除铸件的内应力及改善机械加工性能,在毛坯车间车削去浇冒口,达到毛坯的技术要求,然后送到机械加工车间来加工。
根据工序安排,编出机械加工工艺过程卡及工序卡片。
见附表:机械加工工艺过程卡;附表;机械加工工序卡。
(三)机械加工余量、工序尺寸及毛坯尺寸的确定。
1 .毛坯尺寸的确定,画毛坯图。
刹车盘材料为HT230。
由于产品的精度要求不高,生产纲领为中批生产,所以毛坯选用砂型铸造。
毛坯铸出后进行退火处理,以消除铸件在铸造过程中产生的内应力。
由文献(1)表2-2,该种铸件的尺寸公差等级为IT9级。
由文献(1)表2-2,可查出铸件主要尺寸的公差,现将主要毛坯尺寸及公差所示:由此,可绘出其零件的毛坯图(见附图2)2.粗车刹车盘的两端面面两端面由粗车和精车两次加工完成,采用6换多次使用圆弧车刀(高速钢)。
刀具:YG6硬质合金圆弧右偏车刀。
由于车刀在工作时,是断续切削,背吃刀量大,刀齿受很大的机械冲击,在选择几何角度时,应保证刀齿具有足够的强度。
由金属切削原理与刀具可取γo =50~λs=-100κr=600=100。
加工要求:粗车刹车盘的两端面。
a)确定加工余量由毛坯图可知:总加工余量为2mm,文献)2(表8-30可知精加工余量为1mm,由于两脚底面较小,根据实际情况,调整为0.2mm ,故其粗加工余量为(2-0.2)=1.8mm 。
b )确定进给量由《切削加工简明实用手册》表8-95 ,取每分钟进给量为0.2mm/min,取精加工每齿的进给量为1.5mm/min.粗车走刀一次a p =1.8mm ,精车走刀一次a p = 0.2mm 。
c)计算切削用量由表8-56,取粗车、精车的主轴转速分别为150r/min 和300r/min ,由前面选择的刀具圆弧R0.2mm ,以及工件直径确定相应的切削速度分别为:V 粗=πdn/1000=1000150120πx =56.52m/min V 精=πdn/1000=1000300120πx m/min=113m/mind) 校核该机床功率(只需校核粗加工即可)。
由文献)2(表2.4-96得切削功率为P m =92.4x10-514.00D 86.0e a 72.0fa p a ZnK m p 取Z=16 n=60150=2.5r/s e a =10mm f a =0.2mm p a =1.8mm而K m p =K v KF 2 由文献)2(表2.4-94可知K v =1KF 2=1 故K m p =1故m p =92.4x 510-x 14.0120x 86.010x 72.02.0x1.8x16x2.5x1=0.35KW 其所消耗量功率远小于机床功率,故可用。
3.两端面的加工两端面的加工由车削来完成,此时,刀具:YG6硬质合金端车刀,刀具不变,机床不变。
工序单边总余量由毛坯图与零件图可知为2mm ,由于本工序为粗加工,尺寸精度和表面质量可不考虑,从而可采用不对称端车,以提高进给量提高加工效率。
由表8-95可得:p a =2mm f=2mm/r 由文献)2(表8-56可得n=600r/min 则就可确定相应的切削的速度:故V=1000dn π=1000600120πx =226.08m/min4.钻定位孔孔该孔可选由高速钢钻头钻出定位孔后,为了装配方便,再由锪钻钻出倒角。
由文献)2(表8-81得锪孔时的倒角余量为1.5mm ,根据实际情况可取为2mm,故锪孔的角度为90°。
由文献)2(表8-69,锪孔的进给量在不破坏精度的情况下自行确定。
由文献)2(表8-71求得钻孔时的切削速度v=0.35m/s=21m/min 由此算出转速为:n=Dv π1000=10211000x x π=668.8r/min按钻床的实际转速取n=600r/min ,则实际切削速度为:v=πdn/1000=10006.11x π=21.85m/min由表8-78得F=CFd x 0Ff y FK F =588.6xd 0xf 8.0xK f M=C m d x 0mf ym K m x103-=225.63x d 9.10xf 8.0x K m x03- 因为加工灰铸铁时K M =K f 由文献)3(表8-78,可查的K f =1,故F=588.6x11.6x0.28.0x1=1884.1N M=225.63x11.69.1x0.28.0x1x103-=6.6N.m它们均小于机床所能提供的进给率和扭转力矩,故机床刚度足够。
8.时间定额计算根据设计要求,只计算一道工序的工时,下面计算加工Ф12孔的工时定额。
(1) 机动时间由文献《机械加工工艺手册》表2.5-7得钻孔时的计算公式为:t=fnl l l 21++式中l 1=2D cotK y +(1~2)l 2=1~4,钻定位孔孔时,l 2=0 l=30 l 2=2 f=0.3 n=600 l 1=212cot(2118)+1.5=5.1因此,t=3.060021.530x ++=0.206min 所以t b =4t=0.824min(2)辅助时间由机械加工工艺手册表2.5-41确定 开停车 0.015min 刀架定位0.015min 主轴运转0.02min 清除铁屑0.04min 卡尺检验0.1min装卸工件时间由机械加工工艺手册表2.5-42取1min 故辅助时间ta=(0.015+0.015+0.02+0.04+0.1+1)=1.19min(3)作业时间TB=ta +tb=(1.19+0.824)=2.014min(4)常量工作场地时间T s由机械制造工艺学取α=3%则T s=TB xα=2.014x3%=0.06。