钢铁工业主要工序能耗指标
3能耗指标体系的分类计算

能耗指标体系的分类钢铁企业能耗指标主要有吨钢综合能耗、吨钢可比能耗、主要产品的工序能耗、主要产品的实物单耗(如炼铁焦比、炼焦煤耗等)以及产值能耗、增加值能耗等等。
能源分析评价指标中,包括企业内部能源加工转换指标和企业损失指标。
按钢铁企业能耗经济技术指标体系可分为:(1)企业级能源技术经济指标:如吨钢综合能耗、万元产值能耗、吨钢耗新水、吨钢电耗、损失率等。
(2)工序级能源技术经济指标:如炼钢工序能耗、炼铁工序能耗等。
(3)耗能设备级能源技术经济指标:加热炉燃耗、高炉焦比、制氧机电耗等。
按钢铁企业能效对标指南中能耗指标体系可分为:(1)综合性指标:如企业级能源消耗总量、工序级能源消耗总量、各类能源介质消耗总量、企业能源亏损量等指标。
(2)单耗性指标:如吨钢综合能耗、企业吨钢可比能耗、工序单位产品能耗。
(3)经济性指标:万元产值能耗、万元增加值能耗等。
2.能耗指标的范围及计算钢铁制造流程是由多个不同的生产工序组成的,前一道工序的产品为下一道工序的原料,这是钢铁工业的特点,由于其复杂性,因此,统计范围和指标定义必须规范,以便于对标,找出节能潜力,提升企业效益。
(1)吨钢综合能耗范围及计算综合能耗是规定的耗能体系在一段时间内实际消耗的各种能源实物量按规定的计算方法和单位分别折算为标准煤后的总和。
吨钢综合能耗(comprehensive energy consumption ):吨钢综合能耗是企业生产每吨粗钢所综合消耗的各种能源自耗总量;也就是每生产一吨钢,企业消耗的净能源量。
其计算公式为:吨钢综合能耗=企业钢产量企业自耗能源量(吨标准煤/吨钢,千克标准煤/吨;tce/t ,kgce/t )式中,企业自耗能源量即报告期内企业自耗的全部能源量。
统计上报按企业全部耗能量。
企业自耗能源量= 企业购入能源量 ± 库存能源增减量 - 外销能源量= 企业各部位耗能量之和 + 企业能源亏损量作为行业对标,吨钢综合能耗的统计范围可按照企业生产流程的主体生产工序(包括原料储存、焦化、烧结、球团、炼铁、炼钢、连铸、轧钢、自备电厂、制氧等动力厂)、厂内运输、燃料加工及输送、企业亏损等消耗能源总量,不包括矿石的采、选工序,也不包含炭素、耐火材料、机修、石灰、精制及铁合金等非钢生产工序的能源消耗量。
国内外高炉炼铁系统的能耗分析
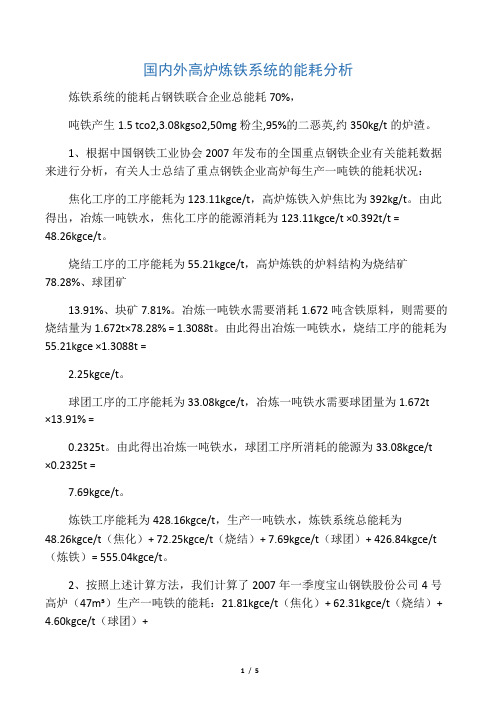
表12005年浦项制铁盒光阳厂炼铁有关能耗指标
项目工序能耗Kgce/t
烧结
66
57.4焦化
129.7
131.9炼铁
462.5
441.1入炉焦比Kgce/t炉料结构%
烧结比
76.4
70.9球团比
7.8
11.1块矿比
15.8
18.0xx
光阳494.7
492.1
表2全国重点钢铁企业能耗对比(单位Kgce/t)
高热值煤气回收利用率低是非高炉炼铁能耗高的“瓶颈”
2007年,我国重点钢铁企业的烧结、炼铁工序能耗与2006年相比进一步降低,炼铁生产部分工序能耗指标见表2。
2007年,全国重点钢铁企业高炉炼铁燃料比是529kg/t,浦项FINEX燃料比是740kg/t~750kg/t,澳大利亚Hismelt的煤耗在900kg/t(尚需1200℃风温和350kWh/t的电力)。这说明目前非高炉炼铁的能耗高于高炉冶炼生产工艺。
国内外高炉炼铁系统的能耗分析
炼铁系统的能耗占钢铁联合企业总能耗70%,
吨铁产生1.5 tco2,3.08kgso2,50mg粉尘,95%的二恶英,约350kg/t的炉渣。
1、根据中国钢铁工业协会2007年发布的全国重点钢铁企业有关能耗数据来进行分析,有关人士总结了重点钢铁企业高炉每生产一吨铁的能耗状况:
钢铁工艺流程废热利用分析
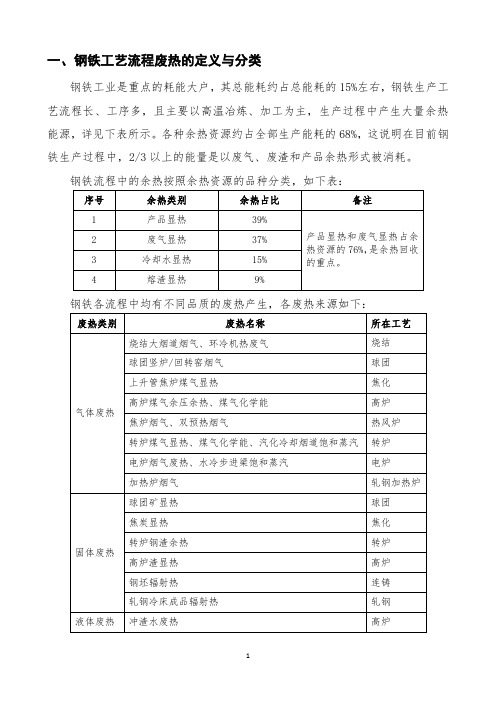
一、钢铁工艺流程废热的定义与分类钢铁工业是重点的耗能大户,其总能耗约占总能耗的15%左右,钢铁生产工艺流程长、工序多,且主要以高温冶炼、加工为主,生产过程中产生大量余热能源,详见下表所示。
各种余热资源约占全部生产能耗的68%,这说明在目前钢铁生产过程中,2/3以上的能量是以废气、废渣和产品余热形式被消耗。
钢铁流程中的余热按照余热资源的品种分类,如下表:钢铁各流程中均有不同品质的废热产生,各废热来源如下:二、钢铁工艺流程废热利用技术现状(一)常规废热利用方式钢铁流程的废热利用中,废热回收发电是经济性比较高的一种废热回收方式,因此钢铁行业的废热回收主要以废热回收发电方式为主,在余热发电技术的研发应用方面,与发达国家钢铁工业相比,我们钢铁行业的余热发电技术起步较晚。
目前,钢铁工业余热发电主要有以下几种方式,一是利用焦化、烧结工序烟气余热换热产生过热蒸汽发电;二是利用炼钢、轧钢工序烟气余热换热产生饱和蒸汽发电;第三种是煤气-蒸汽联合循环发电。
另外目前有人提出利用高炉的冲渣热水余热进行ORC发电,此技术目前尚在论证中,市场未有应用案例。
1、过热蒸汽发电(1)干熄焦余热发电炼焦生产中,高温红焦冷却有两种熄焦工艺:一种是传统的采用水熄灭炽热红焦的工艺,简称湿熄焦,另一种是采用循环惰性气体与红焦进行热交换冷却焦炭,简称干熄焦。
干熄焦余热发电技术是指利用与红焦热交换产生的高温烟气驱动汽轮发电机组进行发电,其主要工艺流程为:焦炉生产出来的约1000℃赤热焦炭运送入干熄炉,在冷却室内与循环风机鼓入的冷惰性气体进行热交换。
惰性气体吸收红焦的显热,温度上升至800℃左右,经余热锅炉生产中高压过热蒸汽,驱动汽轮发电机组发电,同时汽轮机还可产生低压蒸汽用于供热。
随着干熄焦技术所产生的社会和节能环保效益得到普遍认可,干熄焦余热发电技术也得到了国内钢铁企业越来越广泛的应用。
该项发电技术已十分成熟,目前的发展趋势集中在进一步提高余热的回收利用效率上,正逐步由传统的小型中压参数系统向系列化、大型化、高参数发展。
钢铁工业主要工序能耗指标2015解析

1.1
南京
1.0
5
吨坯氩气消耗
Nm3/t
/
0.6
南京
1.0
天铁
18.22/110
汽动鼓风/电动鼓风
6
吨铁新水耗
m3/t
1.5
0.12
南昌钢厂
0.12
7
吨铁蒸汽消耗
kg/t
/
13.32
莱钢
13.32
8
高炉热风炉吨铁燃料消耗
GJ/t
/
1. 89
宝钢
1.89
二
能源回收指标
1
吨铁TRT发电量
湿法除尘
kWh/t
≥30
28
首钢
30
干法除尘
kWh/t
≥35
52
太钢
52
四
10
25
AOD炉吨钢水氧气消耗
Nm3/t
32
26
AOD炉吨钢水氮气消耗
Nm3/t
25
27
AOD炉吨钢水燃气消耗
GJ/t
0.05
四
连铸
(一)
方坯连铸
1
工序能耗
kgce/t
6.0
3.6
莱钢
5.5
2
吨坯电耗
kWh/t
/
10
南京
11/9
有/电磁搅拌
3
吨坯新水消耗
t/t
/
0.15
莱钢
0.2
4
吨坯氧气消耗
Nm3/t
序号
指标名称
单位
国家标准先进值[2]
近年行业先进值
标杆指标
备注
指标
企业名称
一
钢铁行业铁合金单位产品能源消耗限额标准

外,其它铁合金(几乎全部)征收20%的出口关税。
注:*为估测值.其它铁合金中的2009年镍铁产量约为350万吨.
2009* 2209.4 ~520 ~800 ~160
~95 ~128 ~506.4
6
我国铁合金发展现状
近年部分铁合金的出口数量 单位:万吨
年度 出口总量 铬系铁合金 锰系铁合金 硅铁合金
电解锰 金属硅
2005 254.73
9.12 54.84 71.78 27.53 53.61
目前铁合金生产中约有30~40%的设备属于国家淘汰范围的落后产 能,新建项目中也存在落后工艺、落后设备的建设,铁合金能耗 限额标准的制定对于推进铁合金行业的结构调整,淘汰落后和制 止新建容量较大、技术装备水平偏低的电炉设备重复建设具有重 要的意义。
我国铁合金发展现状
亿吨 6
5
4
3
2
1.24
1
379.4
限额值(淘汰落后)
本标准中对铁合金单位产品能耗限额值的取值大致是按照淘汰现有产能 约2400万吨(2007年前未含工业硅和电解锰的产能)、3500万吨(2010 年前的产能)中30%35%左右的落后产能考虑的 。
准入值(新建设备准入门槛)
铁合金单位产品能耗限额的准入值是根据较大容量(12.5MVA电炉) 装备规模、按照较好的水平来确定的。
7.4 12.7 4.5 8.1 32.56 50049
钢铁工业主要工序能耗指标

1-1粗钢综合性指标标杆值
4
号
指标名称
单住
国内先进木平
标杆指标
备注
1
全厂壽炉煤气放散率
%
“0”
2
全厂焦炉煤气放散率
%
0
0
3
转炉煤气放散率
%
“0”
4
全厂回收余热蒸九放散
率
%
0
5
全厂吨钢二次能嫄回收
量
kgce/t
440
500
包括:回收的各种煤气、
煤化工产品、各种余热
(包括TRT丿等。
6全Βιβλιοθήκη 吨钢二次能嫄利用6066
宝钢
70
该指标只有7.63m焦炉,采用爲温爲 压干熄焦装置才能 达到。
2
煤调谡吨焦节能量
kgce/t
/
5
宝钢、
济钢
6
只有采用烟遒气预
热技术才能达到。
四
其它重要指标
1
干熄焦配备率
%
100
100
宝钢
100
1-3
序
号
指标名称
单佞
国家标准先
u [2]
近年行业先进值
标杆
指标
备注
指标
企业名
称
能耗指标
1
工序能耗
钢铁工业重要能源消耗指标参考表(行业平均值、国际先进值)

钢加工 热轧 冷轧 镀涂 钢丝 铁合金 耐材 工序能耗(kgce/t) 90.07 81.30 120.10 71.79 101.1 1703.16 164.32 电耗(千瓦时/吨) 99.32 82.80 165.30 115.61 310.1 4514.4 123.07 工序水耗 20.33 17.60 27.46 12.3 48.18 46.22 11.66 耗新水 2.02 1.81 1.53 0.5 12.28 4.78 8.80 备注:数据来源于2005年钢铁工业统计年报(中国钢铁工业协会信息统计部)
吨刚综合能耗:741kgce/t 吨刚可比能耗:714kgce/t 2005年全国重点归钢铁企业工序能耗、水耗 采矿 工序能耗(kgce/t) 电耗(千瓦时/吨) 工序水耗 耗新水 露天 1.11 1.39 地下 7.59 14.89 选矿 14.59 29.61 6.97 1.02 焦化 142.21 33.5 58.0 3.0 烧结 65.09 36.64 0.54 0.26 球团 39.62 34.62 1.44 0.48 炼铁 440.6 66.65 34.48 1.19
2005年全国重点钢铁企业及国际各工序能耗情况(等价值) 吨钢综 合能耗 吨钢可比 能耗 烧结 球团 焦化 炼铁 转炉
Kgce/t Kgce/t
行业平均值 韩国光阳 德国蒂森 国际先进 747.05 714.12 711.9
Kgce/t Kgce/t Kgce/t Kgce/t Kgce/t
64.83 57.4 58 51 40.5 142.21 131.9 75.1 95 456.79 441.1 426 438 36.34 -2.3 -4.5 -8.8
655
炼钢 49.43 76.93 15.35 1.66
5钢铁企业能源综合平衡

5钢铁企业能源综合平衡钢铁企业能源综合平衡一、钢铁企业能源综合平衡概述(一)钢铁企业能源综合平衡的定义钢铁企业能源综合平衡是以钢铁企业为对象的能源平衡,包括各种能源收入与支出的平衡,消耗与有效利用及损失的能源数量平衡。
钢铁企业能源综合平衡所指的能量平衡范围,是指在生产活动中消耗的一次能源和二次能源所提供的能量,工质和物料所携带的能量,以及在企业内部进行能源转换和传输过程中损失能量的综合系统平衡。
在平衡计算中,都是将各种形式的能量按它们的等价热量值折合成热能这一主要利用形式,所以往往又将钢铁企业能源综合平衡称为钢铁企业热平衡。
钢铁企业能源综合平衡并不是只限于能源和能量的统计分析和数量平衡这一狭义的技术经济范围,而是通过这方面的工作,广义地对钢铁企业能源管理的组织体制,用能方针和政策,企业的耗能设备乃至生产工艺流程等进行分析,提出企业近期技术改进措施和远景规划。
钢铁能源综合平衡统计是综合平衡统计的重要组成部分,是一项综合性很强的系统工程。
从微观到宏观,从单项到综合,从局部到整体,从个别能源流转环节到全部能源系统流程,形成了一个完整的能源平衡体系。
(二)钢铁企业能源综合平衡的意义钢铁企业能源综合平衡遵循输入能量等于输出能量这一基本法则,就一定时期内企业能源的购入、加工转换、输送、分配、储备、使用等整个能源系统流程进行平衡分析,就能源系统内各运行环节的特征和相互之间的联系,以及能源经济运行中所形成的总量、效益之间的制约和平衡状况。
(三)能量平衡体系能量收、支的项目是随着所选体系不同而异的,所以在进行能量平衡时必须首先确定研究的体系,它可以是一个设备,也可以是一个工序,还可以是一个分厂,乃至整个企业。
在选好体系之后,用框图代表所选的体系,而将进入和排出体系的所有各项能量用箭头标在方框的四周,这就构成了我们所研究的能量平衡模型,绘制模型图的习惯方法一般是:1.由工质(工艺流体、物料或半成品)所带入能量Q带入画在方框的左侧。
- 1、下载文档前请自行甄别文档内容的完整性,平台不提供额外的编辑、内容补充、找答案等附加服务。
- 2、"仅部分预览"的文档,不可在线预览部分如存在完整性等问题,可反馈申请退款(可完整预览的文档不适用该条件!)。
- 3、如文档侵犯您的权益,请联系客服反馈,我们会尽快为您处理(人工客服工作时间:9:00-18:30)。
附件1 钢铁行业主要生产工序能耗指标标杆值
表1-1 粗钢综合性指标标杆值
表1-2 焦化工序标杆值
表1-3 烧结工序标杆值
表1-4 球团工序标杆值
表1-5 炼铁工序标杆值
表1-6 转炉炼钢工序标杆值
表1-7 电炉炼钢工序标杆值
表1-8 轧钢工序标杆值
注[1]:国家标准指《焦炭单位产品能源消耗限额》(GB21342-2008)
注[2]:国家标准指《粗钢生产主要工序单位产品能源消耗限额》(GB21256-2007)、《清洁生产标准钢铁行业(烧结)》(HJ/T426-2008)、《清洁生产标准钢铁行业(高炉炼铁)》(HJ/T427-2008)、《清洁生产标准钢铁行业(炼钢)》(HJ/T428-2008)、国标《钢铁企业节能设计规范》(2010年送审稿)。