发动机凸轮轴检测方法综述
摩托车凸轮轴珠光体含量的电磁法检测技术

摩托车凸轮轴珠光体含量的电磁法检测技术
1 简介
摩托车发动机凸轮轴是发动机中的一个关键部件,它通过不断运动带动摩托车发动。
凸轮轴材质一般是高强度的合金钢,它在长时间的高速摩擦下,表面易产生疲劳、龟裂等微结构损伤,因此需要定期检测凸轮轴表面是否存在问题。
2 检测方法
传统的检测方法一般采用人工外观观察和超声波检测,然而这些方法都有一定的缺陷。
人工外观观察难以发现微小的龟裂,而超声波只能检测到表面伤痕,无法检测到深层缺陷。
因此,采用电磁法检测凸轮轴表面珠光体的含量可以成为一种更高效、准确的方法。
3 原理
在摩托车凸轮轴表面压制珠光体时,由于其电导率和磁导率的差异,凸轮轴表面和珠光体之间会产生不同的磁场响应。
通过加热凸轮轴,使珠光体断裂后释放出的磁场信号被接收,通过信号的强度和时间来判断凸轮轴表面上珠光体的含量和深度。
4 应用
电磁法检测技术已经广泛应用于汽车、飞机、铁路等交通运输工具的零件检测中。
在摩托车凸轮轴的检测中,电磁法检测技术可以快
速准确地检测出凸轮轴表面的微小损伤,有助于及早排除安全隐患和故障,提高摩托车性能和使用寿命。
5 结论
电磁法检测技术是一种可靠、高效、非破坏性的检测方法,可以用于检测摩托车凸轮轴表面珠光体含量,有效避免了传统检测方法的缺陷。
同时,电磁法检测技术的推广应用将有助于提高摩托车的安全性和可靠性。
凸轮轴检测步骤

凸轮轴检测步骤
1、准备
1.1检测准备
1.1.1准备检测仪器仪表
(1)量角仪。
(2)游标卡尺。
(3)棱角投影仪。
(4)抛光机。
1.1.2准备相关材料
(1)检测螺杆、螺母及凸轮,应符合图纸条件。
(2)准备清洗、抛光及其他检测用料。
2、检测
2.1外观检验
检查轴承外观质量,应没有变形、氧化、污损等缺陷,尤其是轴承滚动体和内外圈的表面无焊接、裂痕等缺陷。
2.2游标卡尺检测
游标卡尺检测凸轮轴是否设计尺寸正确,如外径、内径、深度和齿廓等尺寸,应符合图纸要求。
2.3量角仪检测
量角仪检测凸轮轴的轴向跳动、轴向振动及螺纹的螺距,应符合图纸要求,并且超限值不要超过公差范围。
2.4棱角投影检测
棱角投影检测凸轮轴的滚动面和轴线的相对位置,应符合图纸要求,并且超限值不要超过公差范围。
3、清洗及抛光
检测完毕后,应使用清洗剂清洗凸轮轴表面,然后将其抛光,以保证滚动体和螺纹等的良好检测。
4、结束
完成凸轮轴的检测后,根据检测结果确定凸轮轴的质量是否符合要求,如果均符合要求,则可以结束检测,准备进行其他检测与装配。
发动机凸轮轴检测方法综述2
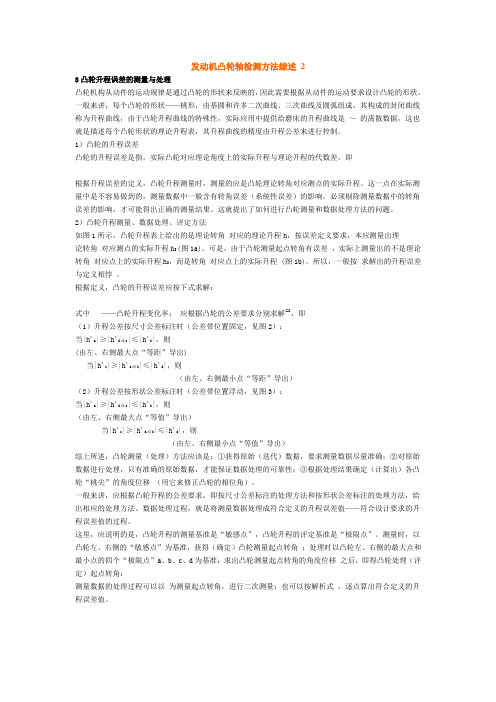
发动机凸轮轴检测方法综述 23凸轮升程误差的测量与处理凸轮机构从动件的运动规律是通过凸轮的形状来反映的,因此需要根据从动件的运动要求设计凸轮的形状。
一般来讲,每个凸轮的形状——桃形,由基圆和许多二次曲线、三次曲线及圆弧组成,其构成的封闭曲线称为升程曲线,由于凸轮升程曲线的特殊性,实际应用中提供给磨床的升程曲线是~的离散数据,这也就是描述每个凸轮形状的理论升程表,其升程曲线的精度由升程公差来进行控制。
1)凸轮的升程误差凸轮的升程误差是指,实际凸轮对应理论角度上的实际升程与理论升程的代数差。
即根据升程误差的定义,凸轮升程测量时,测量的应是凸轮理论转角对应测点的实际升程。
这一点在实际测量中是不容易做到的,测量数据中一般含有转角误差(系统性误差)的影响,必须剔除测量数据中的转角误差的影响,才可能得出正确的测量结果。
这就提出了如何进行凸轮测量和数据处理方法的问题。
2)凸轮升程测量、数据处理、评定方法如图1所示,凸轮升程表上给出的是理论转角对应的理论升程h,按误差定义要求,本应测量出理论转角对应测点的实际升程h S (图1a)。
可是,由于凸轮测量起点转角有误差,实际上测量出的不是理论转角对应点上的实际升程h S,而是转角对应点上的实际升程 (图1b)。
所以,一般按求解出的升程误差与定义相悖。
根据定义,凸轮的升程误差应按下式求解:式中——凸轮升程变化率;应根据凸轮的公差要求分别求解[2],即(1)升程公差按尺寸公差标注时(公差带位置固定,见图2):当|h'a|≥|h'd或c|≤|h'b|,则(由左、右侧最大点“等距”导出)当|h'c|≥|h'a或b|≤|h'd|,则(由左、右侧最小点“等距”导出)(2)升程公差按形状公差标注时(公差带位置浮动,见图3):当|h'a|≥|h'd或c|≤|h'b|,则(由左、右侧最大点“等值”导出)当|h'c|≥|h'a或b|≤|h'd|,则(由左、右侧最小点“等值”导出)综上所述,凸轮测量(处理)方法应该是:①获得原始(迭代)数据,要求测量数据尽量准确;②对原始数据进行处理,只有准确的原始数据,才能保证数据处理的可靠性;③根据处理结果确定(计算出)各凸轮“桃尖”的角度位移(用它来修正凸轮的相位角)。
浅谈凸轮轴的制造与检测
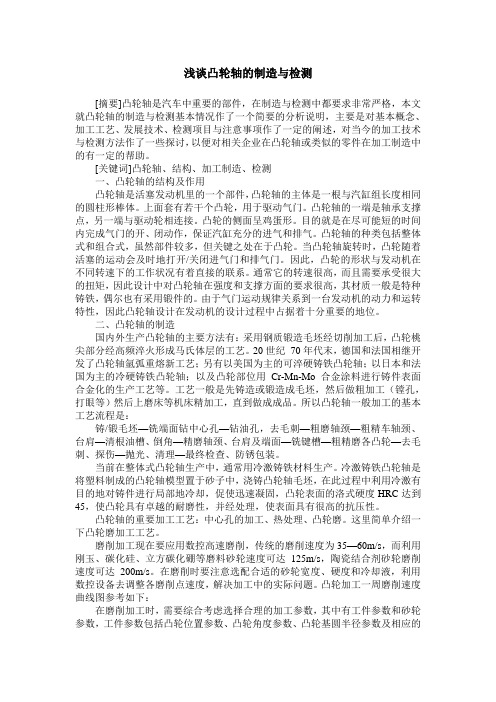
浅谈凸轮轴的制造与检测[摘要]凸轮轴是汽车中重要的部件,在制造与检测中都要求非常严格,本文就凸轮轴的制造与检测基本情况作了一个简要的分析说明,主要是对基本概念、加工工艺、发展技术、检测项目与注意事项作了一定的阐述,对当今的加工技术与检测方法作了一些探讨,以便对相关企业在凸轮轴或类似的零件在加工制造中的有一定的帮助。
[关键词]凸轮轴、结构、加工制造、检测一、凸轮轴的结构及作用凸轮轴是活塞发动机里的一个部件,凸轮轴的主体是一根与汽缸组长度相同的圆柱形棒体。
上面套有若干个凸轮,用于驱动气门。
凸轮轴的一端是轴承支撑点,另一端与驱动轮相连接。
凸轮的侧面呈鸡蛋形。
目的就是在尽可能短的时间内完成气门的开、闭动作,保证汽缸充分的进气和排气。
凸轮轴的种类包括整体式和组合式,虽然部件较多,但关键之处在于凸轮。
当凸轮轴旋转时,凸轮随着活塞的运动会及时地打开/关闭进气门和排气门。
因此,凸轮的形状与发动机在不同转速下的工作状况有着直接的联系。
通常它的转速很高,而且需要承受很大的扭矩,因此设计中对凸轮轴在强度和支撑方面的要求很高,其材质一般是特种铸铁,偶尔也有采用锻件的。
由于气门运动规律关系到一台发动机的动力和运转特性,因此凸轮轴设计在发动机的设计过程中占据着十分重要的地位。
二、凸轮轴的制造国内外生产凸轮轴的主要方法有:采用钢质锻造毛坯经切削加工后,凸轮桃尖部分经高频淬火形成马氏体层的工艺。
20世纪70年代末,德国和法国相继开发了凸轮轴氩弧重熔新工艺;另有以美国为主的可淬硬铸铁凸轮轴;以日本和法国为主的冷硬铸铁凸轮轴;以及凸轮部位用Cr-Mn-Mo 合金涂料进行铸件表面合金化的生产工艺等。
工艺一般是先铸造或锻造成毛坯,然后做粗加工(镗孔,打眼等)然后上磨床等机床精加工,直到做成成品。
所以凸轮轴一般加工的基本工艺流程是:铸/锻毛坯—铣端面钻中心孔—钻油孔,去毛刺—粗磨轴颈—粗精车轴颈、台肩—清根油槽、倒角—精磨轴颈、台肩及端面—铣键槽—粗精磨各凸轮—去毛刺、探伤—抛光、清理—最终检查、防锈包装。
凸轮轴凸轮表面测量方法
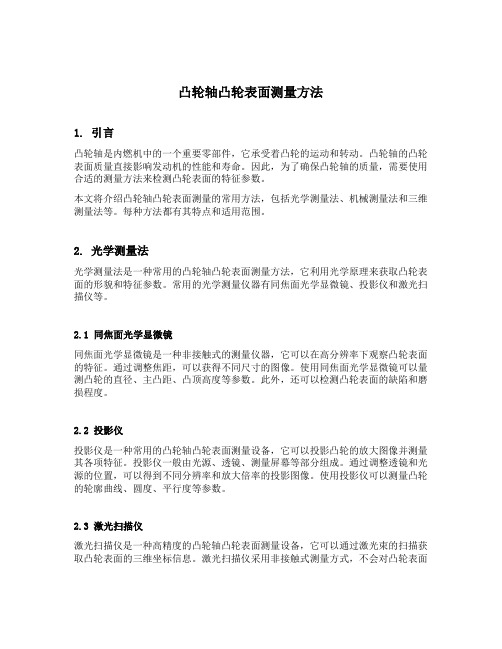
凸轮轴凸轮表面测量方法1. 引言凸轮轴是内燃机中的一个重要零部件,它承受着凸轮的运动和转动。
凸轮轴的凸轮表面质量直接影响发动机的性能和寿命。
因此,为了确保凸轮轴的质量,需要使用合适的测量方法来检测凸轮表面的特征参数。
本文将介绍凸轮轴凸轮表面测量的常用方法,包括光学测量法、机械测量法和三维测量法等。
每种方法都有其特点和适用范围。
2. 光学测量法光学测量法是一种常用的凸轮轴凸轮表面测量方法,它利用光学原理来获取凸轮表面的形貌和特征参数。
常用的光学测量仪器有同焦面光学显微镜、投影仪和激光扫描仪等。
2.1 同焦面光学显微镜同焦面光学显微镜是一种非接触式的测量仪器,它可以在高分辨率下观察凸轮表面的特征。
通过调整焦距,可以获得不同尺寸的图像。
使用同焦面光学显微镜可以量测凸轮的直径、主凸距、凸顶高度等参数。
此外,还可以检测凸轮表面的缺陷和磨损程度。
2.2 投影仪投影仪是一种常用的凸轮轴凸轮表面测量设备,它可以投影凸轮的放大图像并测量其各项特征。
投影仪一般由光源、透镜、测量屏幕等部分组成。
通过调整透镜和光源的位置,可以得到不同分辨率和放大倍率的投影图像。
使用投影仪可以测量凸轮的轮廓曲线、圆度、平行度等参数。
2.3 激光扫描仪激光扫描仪是一种高精度的凸轮轴凸轮表面测量设备,它可以通过激光束的扫描获取凸轮表面的三维坐标信息。
激光扫描仪采用非接触式测量方式,不会对凸轮表面造成损伤。
通过后期处理,可以得到凸轮表面的三维模型,并进一步提取凸轮的特征参数,如凸轮高度、凸轮面积等。
3. 机械测量法机械测量法是一种传统的凸轮轴凸轮表面测量方法,主要依靠机械测量工具来获取凸轮表面的特征参数。
常用的机械测量工具有表面测量仪、千分尺、外径卡规等。
3.1 表面测量仪表面测量仪是一种用于测量凸轮表面粗糙度和形状的机械测量工具。
它由测量头、测量刀、测量系统等部分组成。
通过将测量头沿着凸轮表面滑动,可以得到凸轮的表面粗糙度参数,如Ra、Rz等。
凸轮轴的检测方法

凸轮轴的检测方法
凸轮轴是发动机的重要零部件,其工作状态直接影响着发动机的性能和寿命。
为了确保凸轮轴的质量和使用效果,需要进行检测。
以下是几种凸轮轴的检测方法:
1. 直接测量法:采用游标卡尺等工具对凸轮轴上凸起的部分进行直接测量,以检查其直径、凸高度和凸角等基本参数。
该方法简单易行,但精度受测量工具和测量人员的水平影响较大。
2. 光学比对法:将一个标准的凸轮轴放到检测仪器中,通过检测仪器的光学系统测量出凸轮的轮廓信息,然后将要检测的凸轮轴与标准凸轮轴进行比对,以判断其质量和尺寸是否符合要求。
该方法精度高,但需要专业仪器和技术。
3. 磁粉检测法:在凸轮轴表面涂覆一层磁粉,然后将其放入磁场中,磁粉的特性可以表现出凸轮轴表面的缺陷和裂纹等问题。
该方法适用于检测表面缺陷和裂纹等问题。
4. 声波检测法:通过将凸轮轴表面进行超声波探测,可以检测出隐蔽缺陷和裂纹。
该方法检测速度快,但需要专业设备和技术。
总的来说,不同的凸轮轴检测方法各有优劣,应根据具体情况选择合适的检测方式,确保凸轮轴的质量和可靠性。
凸轮轴凸轮表面测量方法

凸轮轴凸轮表面测量方法一、前言凸轮轴是发动机的重要部件之一,它的设计和制造质量直接影响发动机的性能和寿命。
凸轮轴上的凸轮表面是传递运动和力量的关键部位,因此对于凸轮表面的测量尤为重要。
本文将介绍几种常见的凸轮轴凸轮表面测量方法。
二、工具和设备1. 数字显微镜2. 表面粗糙度仪3. 比较显微镜4. 电子高度计5. CMM(三坐标测量机)三、数字显微镜法测量凸轮表面形状误差数字显微镜法是一种常用的测量方法,它可以快速、精确地测量出凸轮表面形状误差。
具体步骤如下:1. 准备数字显微镜,并根据实际需要选择相应的放大倍数。
2. 将待测凸轮放置在支架上,并调整好位置。
3. 打开数字显微镜并对焦,然后开始进行测量。
4. 依次在不同位置进行测量,并记录下每个位置的数据。
5. 根据所得数据计算出凸轮表面形状误差,并进行分析和判断。
四、表面粗糙度仪法测量凸轮表面粗糙度表面粗糙度是一个重要的技术指标,它直接影响着凸轮轴的使用寿命和性能。
利用表面粗糙度仪可以快速测量出凸轮表面的粗糙度。
具体步骤如下:1. 准备好表面粗糙度仪,并根据实际需要选择相应的探头。
2. 将待测凸轮放置在支架上,并调整好位置。
3. 打开表面粗糙度仪并对焦,然后开始进行测量。
4. 依次在不同位置进行测量,并记录下每个位置的数据。
5. 根据所得数据计算出凸轮表面的平均粗糙度和最大峰值高度。
五、比较显微镜法测量凸轮表面形位误差比较显微镜法是一种常用的测量方法,它可以快速、直观地测量出凸轮表面形位误差。
具体步骤如下:1. 准备好比较显微镜,并根据实际需要选择相应的放大倍数。
2. 将待测凸轮放置在支架上,并调整好位置。
3. 打开比较显微镜并对焦,然后开始进行测量。
4. 依次在不同位置进行测量,并记录下每个位置的数据。
5. 根据所得数据计算出凸轮表面的形位误差,并进行分析和判断。
六、电子高度计法测量凸轮表面高度误差电子高度计法是一种常用的测量方法,它可以快速、精确地测量出凸轮表面高度误差。
发动机凸轮轴检测方法综述
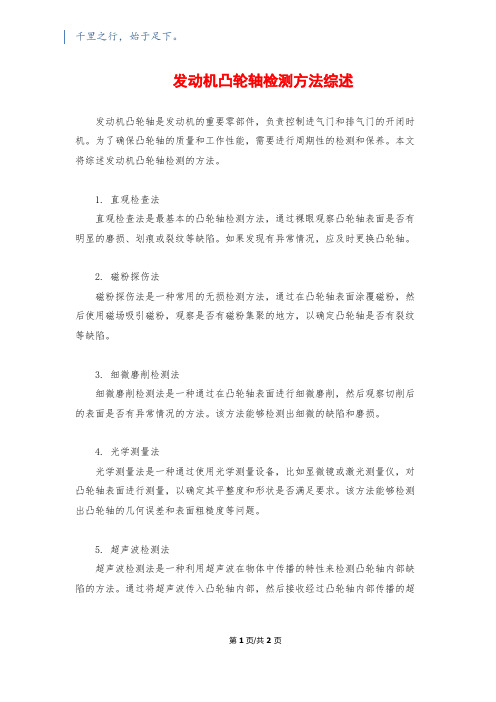
千里之行,始于足下。
发动机凸轮轴检测方法综述发动机凸轮轴是发动机的重要零部件,负责控制进气门和排气门的开闭时机。
为了确保凸轮轴的质量和工作性能,需要进行周期性的检测和保养。
本文将综述发动机凸轮轴检测的方法。
1. 直观检查法直观检查法是最基本的凸轮轴检测方法,通过裸眼观察凸轮轴表面是否有明显的磨损、划痕或裂纹等缺陷。
如果发现有异常情况,应及时更换凸轮轴。
2. 磁粉探伤法磁粉探伤法是一种常用的无损检测方法,通过在凸轮轴表面涂覆磁粉,然后使用磁场吸引磁粉,观察是否有磁粉集聚的地方,以确定凸轮轴是否有裂纹等缺陷。
3. 细微磨削检测法细微磨削检测法是一种通过在凸轮轴表面进行细微磨削,然后观察切削后的表面是否有异常情况的方法。
该方法能够检测出细微的缺陷和磨损。
4. 光学测量法光学测量法是一种通过使用光学测量设备,比如显微镜或激光测量仪,对凸轮轴表面进行测量,以确定其平整度和形状是否满足要求。
该方法能够检测出凸轮轴的几何误差和表面粗糙度等问题。
5. 超声波检测法超声波检测法是一种利用超声波在物体中传播的特性来检测凸轮轴内部缺陷的方法。
通过将超声波传入凸轮轴内部,然后接收经过凸轮轴内部传播的超第1页/共2页锲而不舍,金石可镂。
声波信号,通过分析超声波信号的变化来确定凸轮轴内部是否有裂纹或其他缺陷。
综上所述,发动机凸轮轴的检测方法主要包括直观检查法、磁粉探伤法、细微磨削检测法、光学测量法和超声波检测法等。
这些方法可以综合应用,以确保凸轮轴的质量和工作性能,从而保证发动机的正常运行。
同时,需要注意定期检测和保养凸轮轴,及时更换有问题的凸轮轴,以避免发生意外故障。
- 1、下载文档前请自行甄别文档内容的完整性,平台不提供额外的编辑、内容补充、找答案等附加服务。
- 2、"仅部分预览"的文档,不可在线预览部分如存在完整性等问题,可反馈申请退款(可完整预览的文档不适用该条件!)。
- 3、如文档侵犯您的权益,请联系客服反馈,我们会尽快为您处理(人工客服工作时间:9:00-18:30)。
发动机凸轮轴检测方法综述Summarize to The Measure Method of Engine Cam Shaft摘要论述了凸轮轴测量仪的测量原理和凸轮测量数据的处理与评定方法。
Abstract: The article mainly introduces the principle of the cam shaft measuring system and the method of data processing and assess in cam shaft measuring system.关键词凸轮轴测量数据处理评定keywords: cam shaft ,measure, data processing , assess.1概述凸轮机构广泛应用于自动化机械、精密仪器、自动化控制系统中,作为发动机的关键部件,凸轮轴是影响发动机气门开闭间隙大小和配气效率的主要因素。
随着凸轮轴自动化加工水平的不断提高,为了高精度、高效率地检测凸轮轴,并正确处理、评定它的各项工艺误差,及时快速地反馈凸轮轴的质量信息,传统的光学机械量仪以及采用人工数据处理的方法,已不能适应凸轮轴工艺质量管理的实际检测需要。
为此广州威而信精密仪器有限公司研制了基于计算机为检测、处理核心的L系列凸轮轴测量仪,它可以实现对凸轮轴加工质量的高效、高精度检测,从而对凸轮轴磨床的磨削工艺进行实时监控,以保证产品质量和提高生产效率。
发动机凸轮轴的测量包括与设计有关因素的测量项目和与质量管理有关因素的测量项目。
L-2000型凸轮轴测量仪的主要功能有:(1)检测凸轮轴的轴颈(凸轮轴的装配基准)误差(圆度,跳动);(2)检测凸轮轴的桃型(包括基圆段,爬行段,升程段等)误差;(3)检测凸轮轴的键槽(或定位销)与参考桃的相位角度;(4)检测凸轮轴的各个桃型与参考桃的相位角度;(5)计算凸轮轴的各个桃型轮廓的相邻误差;(6)计算凸轮轴的各个桃型轮廓最大升程和高度;(7)具有偏心修正功能,可以最大限度的减少由于凸轮轴各个桃型轮廓不同心而引起的附加测量误差;(8)具有灵活的参数设置功能和方便的桃型升程表修改功能,被检凸轮轴的轴颈和桃型轮廓的个数可自由设定,可以适应不同厂家的使用需要;(9)具有测试数据自动备份功能,以方便建立工艺质量的过程控制和统计分析;(10)提供有完善的数据分析报告。
打印升程误差曲线,桃型轮廓的极坐标误差图,每个桃型的升程误差数据、理论升程表以及实际升程表等。
本文对凸轮轴测量仪中涉及的主要检测功能、处理方法予以介绍。
2 定位基准的检测在凸轮轴加工过程中,通常借助凸轮轴端面的键槽或定位孔作为角度基准来完成后续的加工工序,因此在凸轮轴测量时需要确定凸轮轴端面的键槽或定位孔的中心位置——定位基准。
键槽的中心位置可以通过测量柱形键销(要求与键槽紧密配合)的中心位置获得;当定位基准是凸轮轴端面的定位孔时,可以通过测量定位销(要求与定位孔紧密配合)的中心位置获得定位孔的中心位置。
按设计要求,应当选用测头为球型测头,由于测头(球)与定位销(圆柱)是点与线的接触,其中心位置不易找准,致使测量中出现了数据不稳定,重复性不好的情况。
通过多种方法试验,也没有取得满意的效果。
定位销中心位置的测量,一度成为凸轮相位角度测量中的棘手问题。
通过进一步的分析可知,定位销虽不在凸轮轴的旋转中心,但当被测凸轮轴以其旋转中心转动时,定位销的运动轨迹是凸轮轴的同心圆,这样,随着测头与定位销接触点位置的不断改变,测头将产生相应位移(升降),因此,可以把定位销看成是凸轮轴上的一个凸轮,这个凸轮的“桃尖”——定位销中心的位置,则可按求解凸轮测量起点转角类似的数据处理方法,用“敏感点法”[1] 予以求解,从而解决了定位销中心位置的测量问题。
3凸轮升程误差的测量与处理凸轮机构从动件的运动规律是通过凸轮的形状来反映的,因此需要根据从动件的运动要求设计凸轮的形状。
一般来讲,每个凸轮的形状——桃形,由基圆和许多二次曲线、三次曲线及圆弧组成,其构成的封闭曲线称为升程曲线,由于凸轮升程曲线的特殊性,实际应用中提供给磨床的升程曲线是~的离散数据,这也就是描述每个凸轮形状的理论升程表,其升程曲线的精度由升程公差来进行控制。
1)凸轮的升程误差凸轮的升程误差是指,实际凸轮对应理论角度上的实际升程与理论升程的代数差。
即根据升程误差的定义,凸轮升程测量时,测量的应是凸轮理论转角对应测点的实际升程。
这一点在实际测量中是不容易做到的,测量数据中一般含有转角误差(系统性误差)的影响,必须剔除测量数据中的转角误差的影响,才可能得出正确的测量结果。
这就提出了如何进行凸轮测量和数据处理方法的问题。
2)凸轮升程测量、数据处理、评定方法如图1所示,凸轮升程表上给出的是理论转角对应的理论升程h,按误差定义要求,本应测量出理论转角对应测点的实际升程h S (图1a)。
可是,由于凸轮测量起点转角有误差,实际上测量出的不是理论转角对应点上的实际升程h S,而是转角对应点上的实际升程(图1b)。
所以,一般按求解出的升程误差与定义相悖。
根据定义,凸轮的升程误差应按下式求解:式中——凸轮升程变化率;应根据凸轮的公差要求分别求解[2],即(1)升程公差按尺寸公差标注时(公差带位置固定,见图2):当|h'a|≥|h'd或c|≤|h'b|,则(由左、右侧最大点“等距”导出)图1 凸轮升程的测量方法当|h'c|≥|h'a或b|≤|h'd|,则(由左、右侧最小点“等距”导出)(2)升程公差按形状公差标注时(公差带位置浮动,见图3):当|h'a|≥|h'd或c|≤|h'b|,则(由左、右侧最大点“等值”导出)当|h'c|≥|h'a或b|≤|h'd|,则(由左、右侧最小点“等值”导出)综上所述,凸轮测量(处理)方法应该是:①获得原始(迭代)数据,要求测量数据尽量准确;②对原始数据进行处理,只有准确的原始数据,才能保证数据处理的可靠性;③根据处理结果确定(计算出)各凸轮“桃尖”的角度位移(用它来修正凸轮的相位角)。
一般来讲,应根据凸轮升程的公差要求,即按尺寸公差标注的处理方法和按形状公差标注的处理方法,给出相应的处理方法。
数据处理过程,就是将测量数据处理成符合定义的升程误差值——符合设计要求的升程误差值的过程。
这里,应说明的是,凸轮升程的测量基准是“敏感点”,凸轮升程的评定基准是“极限点”。
测量时,以凸轮左、右侧的“敏感点”为基准,获得(确定)凸轮测量起点转角;处理时以凸轮左、右侧的最大点和最小点的四个“极限点”a、b、c、d为基准,求出凸轮测量起点转角的角度位移之后,即得凸轮处理(评定)起点转角:测量数据的处理过程可以以为测量起点转角,进行二次测量;也可以按解析式,逐点算出符合定义的升程误差值。
4 关于升程误差测量数据处理方法的说明凸轮的升程公差,常用的有两种标注方法:①标注的是带正负号的公差值,公差带的位置由凸轮升程的理论正确尺寸确定,且公差带位置是固定的,升程公差控制的仅是实际凸轮的轮廓尺寸。
这时,凸轮的升程误差应按尺寸公差来处理:凸轮的升程公差要求,设定了两个极限尺寸——最大实体尺寸(MMS)和最小实体尺寸(LMS)来限制升程的实际尺寸,要求凸轮升程的任一局部尺寸不得超出两个极限尺寸;②标注的是不带正负号的公差值,公差带的方向随凸轮的实际形状而定(变动),公差带的位置是浮动的,升程公差控制要素是实际凸轮的轮廓形状。
这时,凸轮的升程误差应按形位公差来处理(升程误差的测量数据,应按“最小条件”要求进行评定):凸轮的升程公差要求,设定了两个平行(或等距)的界面或界线,构成形状公差带来限制实际被测要素。
凸轮测量数据按尺寸公差要求处理时,应把升程误差与升程公差联系起来,最大限度的保证凸轮升程的合格(图2);凸轮测量数据按形位公差要求处理时,应把升程误差与“最小条件”联系起来,保证凸轮升程误差(包容区域的宽度)的最大值为最小(图3)。
处理时可根据设计要求,选择相应的处理方法。
在此应强调指出:当凸轮异侧(左、右侧)升程公差相等时,“等距”误差点也是“等值”误差点。
尺寸误差和形位误差数据的处理方法相一致。
所不同的只是,形位公差带位置浮动,尺寸公差带位置固定。
5 凸轮轴测量仪的工作原理凸轮轴的测量是二维测量系统。
目前凸轮轴测量仪的分度装置大都采用圆光栅编码器测量系统,线值装置采用直线光栅测量系统。
凸轮轴测量仪的原理框图[3] 如图4所示:由计算机发出的控制信号启动直流同步电机旋转,由驱动机构带动被测凸轮轴转动,通过Y轴圆光栅传感器,X轴直线光栅传感器分别将凸轮轴的角位移、径向、轴向位移转换成明暗条纹的光强变化信号,经光电转换电路转换成电压信号,再经前置放大和整形滤波,形成角度脉冲和径向位移脉冲经T/C计数板送入计算机。
经计算机处理后,就获得了每个凸轮轮廓对应于各个转角的径向测量值(升程)。
应用计算机控制技术,凸轮测量仪的机械运动、测量数据的采集和处理均可由计算机自动控制完成。
这里,应特别强调:凸轮测量时,测头的形状应与凸轮机构中的从动件的形状一致,这样才能更好的模拟凸轮机构的实际工作情况,使测量出的凸轮升程值准确反映凸轮机构从动件的工作位移和运动规律。
图2 尺寸公差标注(公差带固定)图3 形位公差标注(公差带浮动)图4凸轮轴测量仪原理框图6 凸轮轴各项参数的自动测量以广州威而信精密仪器有限公司L系列凸轮轴测量仪为例:仪器结构采用立式安装和测量方式,旋转轴系由精密气浮主轴与气浮顶尖构成,双气浮直线导轨为直线运动基准,由进口电机驱动;电器部分由高级计算机及德国海德汉(HEIDEHAIN)公司精密圆光栅传感器、精密光栅位移传感器组成。
测量软件采用基于中文版WINDOWS操作系统平台的WILSON测量软件,完成参数输入、测量选择、数据采集、处理及测量数据管理和测量结果打印输出等工作。
它可以准确、快速地完成凸轮轴各项参数的测量、处理、管理、打印输出等,达到了高精度、高效率地检测凸轮轴的目的。
(1)定位销中心位置的确定如图5,设测头(球)的半径为SR C,定位销(圆柱)的半径为R X,定位销中心运动轨迹圆的半径为R Z,定位销(凸轮)的虚拟基圆半径为,轴的转角为,测头(球)中心到轴的旋转中心的距离L(O C O),则可由O C OO X依据余弦定理求出:L=R Z cos+式中的取值范围为定位销(凸轮)的升程、升程变化率:=L-(R0+R C)=R Z cos+-(R0+R C)式中虚拟基圆半径图5 定位基准—定位销中心位置的确定因为定位销(凸轮)是对称形,升程变化率曲线是正弦曲线,可知其左、右侧“敏感点”(升程变化率的绝对值最大的点)m、n位于定位销(凸轮)正、负绝对值最大的转角处。