PCB焊接工艺
PCB电路板焊接工艺及要求

6)元器件在PCB板上的插装应分布均匀,排列整齐美观,不允许斜排、立体交叉和重叠排列,不允许一边高,一边低,也不允许引脚一边长,一边短。
7)做好防静电措施,手工焊接电烙铁一定要接地。
8)部分特殊原件பைடு நூலகம்接要求,如下表:
a:晶振XT1:焊接时需要加绝缘垫片,外壳要接地用焊锡把晶振外壳和旁边的焊盘短接。
2)用喷涂的方法涂覆三防漆时,喷涂面积应比器件所占面积大,以保证全部覆盖器件和焊盘;
3)原则上喷涂三防漆一次,喷涂厚度为0.1—0.3mm之间。喷涂时线路板尽量平放,电路板的顶层和底层均应喷涂,喷涂后不应有滴露,也不能有裸露的部分。
4)电路板做喷涂三防漆前,对电路板标号J1,J2,J3,J4端子做相应防护;底层标号AD_L,AD_R,AD_M,VDD,VCC,GND做相应防护;红外对管D1,D2接收、发送的表面做相应防护。
b:红外对管D1,D2:焊接时整体高度要求8.8mm±0.2mm。如下图:
注:晶振、红外对管在电路板清洗后焊接。
器件
项目
SMD贴片器件
DIP直插器件
焊接时烙铁头温度
320±10℃
330±5℃
焊接时间
每个焊点1—3秒
2—3秒
拆除时烙铁头温度
310—350℃
330±5℃
备注
波峰焊,浸焊最高温度260℃。
波峰焊,浸焊时间≤5S。
当焊接大功率或焊点与大铜箔相连,上述温度无法焊接时,烙铁温度可升高至360℃。当焊接敏感怕热零件(LED、传感器、晶振)温度控制在200—300℃,使用免清洗焊锡丝焊接。
PCB板
1)焊点的机械强度要足够
2)焊接可靠,保证导电性能
PCB板焊接工艺设计流程

PCB板焊接工艺设计流程一、前期准备工作1.收集相关信息:包括电路板设计图纸、元器件清单和组装工艺要求等。
2.熟悉电路板结构和设计:了解电路板的层数、线宽线距和孔径等关键参数,了解元器件的安装方式和焊接要求。
二、工艺参数确定1.焊接方式选择:根据电路板结构和元器件类型,选择合适的焊接方式,如表面贴装(SMT)、插件焊接或混合焊接等。
2.焊接温度曲线确定:根据元器件的封装类型和焊接要求,确定适当的预热温度、焊接温度和冷却速率等工艺参数。
3.焊接材料选择:选择合适的焊接材料,包括焊膏、焊锡丝和助焊剂等,根据元器件类型和焊接方式进行搭配。
4.焊接设备选择:根据焊接工艺要求和产能需求,选择合适的焊接设备,包括回流焊炉、波峰焊机和烙铁等。
三、工艺规程编制1.制定焊接规程:根据前期准备工作和工艺参数确定的结果,编制详细的焊接工艺规程,包括焊接步骤、参数设定和操作要求等。
2.制定检测方法:根据元器件的焊接要求,制定相应的检测方法和标准,包括焊点质量检测、焊接强度测试和引脚间电阻测量等。
3.制定操作指导书:编写详细的操作指导书,包括焊接步骤、工艺参数设定和检测方法等,用于指导焊接工艺过程中的操作人员。
四、实施调试1.验证焊接工艺:根据制定的焊接工艺规程,进行焊接试验并验证焊点质量和电气性能等,根据测试结果进行必要的调整和优化。
2.调试设备和工艺参数:根据实际焊接效果,调试焊接设备和工艺参数,以达到最佳的焊接质量和稳定性。
3.培训操作人员:对焊接操作人员进行培训,确保他们理解并能正确操作焊接工艺,提高焊接质量和效率。
在整个PCB板焊接工艺设计流程中,需要密切与相关部门协作,如PCB设计人员、元器件供应商和设备厂商等,以确保焊接工艺的合理性和可行性。
此外,在实际实施中还要时刻注意产品质量和工艺稳定性的监控,及时调整和改进焊接工艺,以及做好相关文档和记录的管理。
只有这样,才能保证焊接工艺的高效性和可靠性,为最终产品的质量提供保障。
pcb飞线焊接工艺
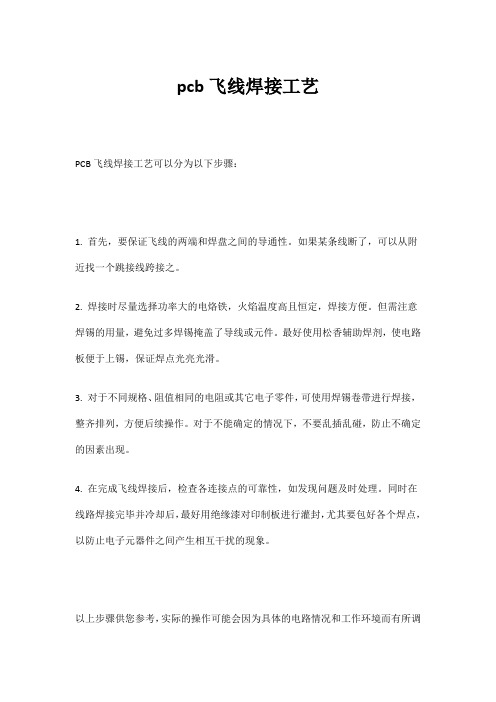
pcb飞线焊接工艺
PCB飞线焊接工艺可以分为以下步骤:
1. 首先,要保证飞线的两端和焊盘之间的导通性。
如果某条线断了,可以从附近找一个跳接线跨接之。
2. 焊接时尽量选择功率大的电烙铁,火焰温度高且恒定,焊接方便。
但需注意焊锡的用量,避免过多焊锡掩盖了导线或元件。
最好使用松香辅助焊剂,使电路板便于上锡,保证焊点光亮光滑。
3. 对于不同规格、阻值相同的电阻或其它电子零件,可使用焊锡卷带进行焊接,整齐排列,方便后续操作。
对于不能确定的情况下,不要乱插乱碰,防止不确定的因素出现。
4. 在完成飞线焊接后,检查各连接点的可靠性,如发现问题及时处理。
同时在线路焊接完毕并冷却后,最好用绝缘漆对印制板进行灌封,尤其要包好各个焊点,以防止电子元器件之间产生相互干扰的现象。
以上步骤供您参考,实际的操作可能会因为具体的电路情况和工作环境而有所调
整。
PCB电路板的手工焊接技术
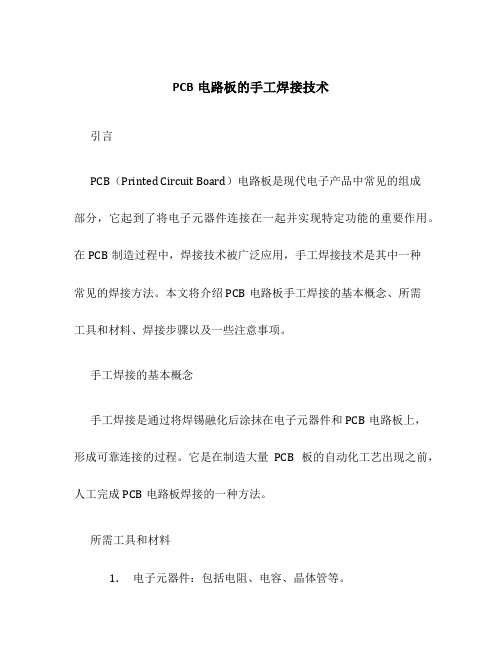
PCB电路板的手工焊接技术引言PCB(Printed Circuit Board)电路板是现代电子产品中常见的组成部分,它起到了将电子元器件连接在一起并实现特定功能的重要作用。
在PCB制造过程中,焊接技术被广泛应用,手工焊接技术是其中一种常见的焊接方法。
本文将介绍PCB电路板手工焊接的基本概念、所需工具和材料、焊接步骤以及一些注意事项。
手工焊接的基本概念手工焊接是通过将焊锡融化后涂抹在电子元器件和PCB电路板上,形成可靠连接的过程。
它是在制造大量PCB板的自动化工艺出现之前,人工完成PCB电路板焊接的一种方法。
所需工具和材料1.电子元器件:包括电阻、电容、晶体管等。
2.PCB电路板:可以自行设计并打印,也可以购买现成的PCB板。
3.焊锡:选择适宜的焊锡线,通常使用的是60/40的焊锡线。
4.电烙铁:选择功率适中的电烙铁,常见的是30W-50W的电烙铁。
5.磁吸台:用于固定PCB板,保持稳定。
6.镊子:用于握取和调整元器件的位置。
7.酒精棉:用于清洁焊接区域表面。
焊接步骤1.准备工作:将所有所需的工具和材料整理好,清洁工作台,并确保所有元器件和PCB板没有损坏。
2.安装元器件:根据PCB板设计图纸,将各个元器件按照对应位置插入PCB板。
可以使用镊子帮助握取和调整元器件位置。
3.固定PCB板:将PCB板放在磁吸台上,使其保持水平并固定在一个位置上。
4.烙铁预热:将电烙铁插入插座并预热至适宜的温度,通常为250-350°C。
5.准备焊锡:将焊锡线从卷上拉出适量,剪断并插入焊锡台。
将焊锡台放在磁吸台旁边,以便操作时能方便取用。
6.焊接元器件:首先将烙铁端放在焊锡台上擦拭干净,然后用烙铁加热所需焊接的元器件脚和PCB板焊盘。
一般情况下,将烙铁加热焊盘上的焊锡,等到焊锡完全融化时再将焊锡线与焊盘交汇处接触,使焊锡覆盖整个焊盘。
7.清洁和整理:完成焊接后,用酒精棉或棉签清洁焊接区域,确保焊接处干净无杂质。
pcb线路板阻焊工艺流程
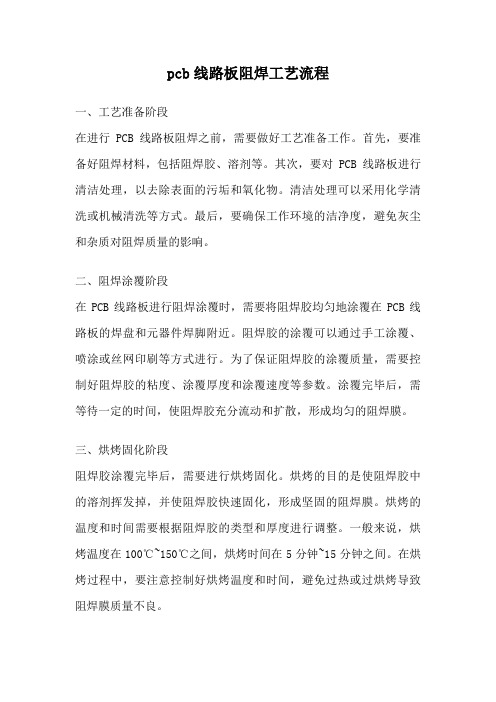
pcb线路板阻焊工艺流程一、工艺准备阶段在进行PCB线路板阻焊之前,需要做好工艺准备工作。
首先,要准备好阻焊材料,包括阻焊胶、溶剂等。
其次,要对PCB线路板进行清洁处理,以去除表面的污垢和氧化物。
清洁处理可以采用化学清洗或机械清洗等方式。
最后,要确保工作环境的洁净度,避免灰尘和杂质对阻焊质量的影响。
二、阻焊涂覆阶段在PCB线路板进行阻焊涂覆时,需要将阻焊胶均匀地涂覆在PCB线路板的焊盘和元器件焊脚附近。
阻焊胶的涂覆可以通过手工涂覆、喷涂或丝网印刷等方式进行。
为了保证阻焊胶的涂覆质量,需要控制好阻焊胶的粘度、涂覆厚度和涂覆速度等参数。
涂覆完毕后,需等待一定的时间,使阻焊胶充分流动和扩散,形成均匀的阻焊膜。
三、烘烤固化阶段阻焊胶涂覆完毕后,需要进行烘烤固化。
烘烤的目的是使阻焊胶中的溶剂挥发掉,并使阻焊胶快速固化,形成坚固的阻焊膜。
烘烤的温度和时间需要根据阻焊胶的类型和厚度进行调整。
一般来说,烘烤温度在100℃~150℃之间,烘烤时间在5分钟~15分钟之间。
在烘烤过程中,要注意控制好烘烤温度和时间,避免过热或过烘烤导致阻焊膜质量不良。
四、表面处理阶段阻焊工艺的最后一步是进行表面处理。
主要是通过去除阻焊膜覆盖的焊盘和元器件焊脚,以便进行后续的焊接操作。
表面处理可以采用化学溶解或机械刮除等方式进行。
化学溶解可以使用特定的溶剂,将阻焊膜溶解掉;机械刮除可以使用专用的刮刀或刮刷,将阻焊膜刮除掉。
表面处理完毕后,需要进行清洗和干燥,以确保PCB线路板表面的干净和无残留。
PCB线路板阻焊的工艺流程包括工艺准备、阻焊涂覆、烘烤固化和表面处理等步骤。
在每个步骤中,都需要控制好工艺参数和操作要点,以保证阻焊质量和工艺稳定性。
同时,还需要进行严格的质量检查和测试,以确保PCB线路板的可靠性和稳定性。
阻焊工艺的优化和改进,可以提高PCB线路板的耐久性和抗干扰能力,从而提高整个电子产品的品质和性能。
pcb 板焊锡工艺定义
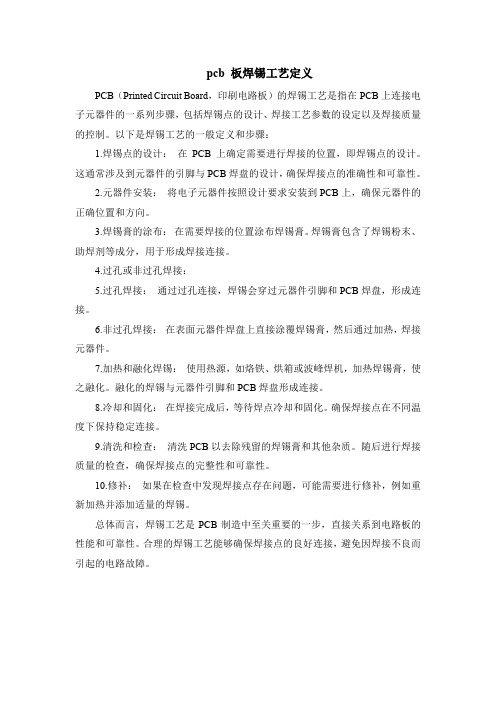
pcb 板焊锡工艺定义
PCB(Printed Circuit Board,印刷电路板)的焊锡工艺是指在PCB上连接电子元器件的一系列步骤,包括焊锡点的设计、焊接工艺参数的设定以及焊接质量的控制。
以下是焊锡工艺的一般定义和步骤:
1.焊锡点的设计:在PCB上确定需要进行焊接的位置,即焊锡点的设计。
这通常涉及到元器件的引脚与PCB焊盘的设计,确保焊接点的准确性和可靠性。
2.元器件安装:将电子元器件按照设计要求安装到PCB上,确保元器件的正确位置和方向。
3.焊锡膏的涂布:在需要焊接的位置涂布焊锡膏。
焊锡膏包含了焊锡粉末、助焊剂等成分,用于形成焊接连接。
4.过孔或非过孔焊接:
5.过孔焊接:通过过孔连接,焊锡会穿过元器件引脚和PCB焊盘,形成连接。
6.非过孔焊接:在表面元器件焊盘上直接涂覆焊锡膏,然后通过加热,焊接元器件。
7.加热和融化焊锡:使用热源,如烙铁、烘箱或波峰焊机,加热焊锡膏,使之融化。
融化的焊锡与元器件引脚和PCB焊盘形成连接。
8.冷却和固化:在焊接完成后,等待焊点冷却和固化。
确保焊接点在不同温度下保持稳定连接。
9.清洗和检查:清洗PCB以去除残留的焊锡膏和其他杂质。
随后进行焊接质量的检查,确保焊接点的完整性和可靠性。
10.修补:如果在检查中发现焊接点存在问题,可能需要进行修补,例如重新加热并添加适量的焊锡。
总体而言,焊锡工艺是PCB制造中至关重要的一步,直接关系到电路板的性能和可靠性。
合理的焊锡工艺能够确保焊接点的良好连接,避免因焊接不良而引起的电路故障。
电路板焊接工艺模板

资料内容仅供您学习参考,如有不当或者侵权,请联系改正或者删除。
PCB板焊接工艺1.PCB板焊接的工艺流程1.1PCB板焊接工艺流程介绍PCB板焊接过程中需手工插件、手工焊接、修理和检验。
1.2PCB板焊接的工艺流程按清单归类元器件—插件—焊接—剪脚—检查—修整。
2.PCB板焊接的工艺要求2.1元器件加工处理的工艺要求2.1.1元器件在插装之前, 必须对元器件的可焊接性进行处理, 若可焊性差的要先对元器件引脚镀锡。
2.1.2元器件引脚整形后, 其引脚间距要求与PCB板对应的焊盘孔间距一致。
2.1.3元器件引脚加工的形状应有利于元器件焊接时的散热和焊接后的机械强度。
2.2元器件在PCB板插装的工艺要求2.2.1元器件在PCB板插装的顺序是先低后高, 先小后大, 先轻后重, 先易后难, 先一般元器件后特殊元器件, 且上道工序安装后不能影响下道工序的安装。
2.2.2元器件插装后, 其标志应向着易于认读的方向, 并尽可能从左到右的顺序读出。
2.2.3有极性的元器件极性应严格按照图纸上的要求安装, 不能错装。
2.2.4元器件在PCB板上的插装应分布均匀, 排列整齐美观, 不允许斜排、立体交叉和重叠排列; 不允许一边高, 一边低; 也不允许引脚一边长, 一边短。
2.3PCB板焊点的工艺要求2.3.1焊点的机械强度要足够2.3.2焊接可靠, 保证导电性能2.3.3焊点表面要光滑、清洁3.PCB板焊接过程的静电防护3.1静电防护原理3.1.1对可能产生静电的地方要防止静电积累, 采取措施使之控制在安全范围内。
3.1.2对已经存在的静电积累应迅速消除掉, 即时释放。
3.2静电防护方法3.2.1泄漏与接地。
对可能产生或已经产生静电的部位进行接地, 提供静电释放通道。
采用埋地线的方法建立”独立”地线。
3.2.2非导体带静电的消除: 用离子风机产生正、负离子, 能够中和静电源的静电。
常使用的防静电器材4.电子元器件的插装电子元器件插装要求做到整齐、美观、稳固。
电路板板焊接工艺和流程
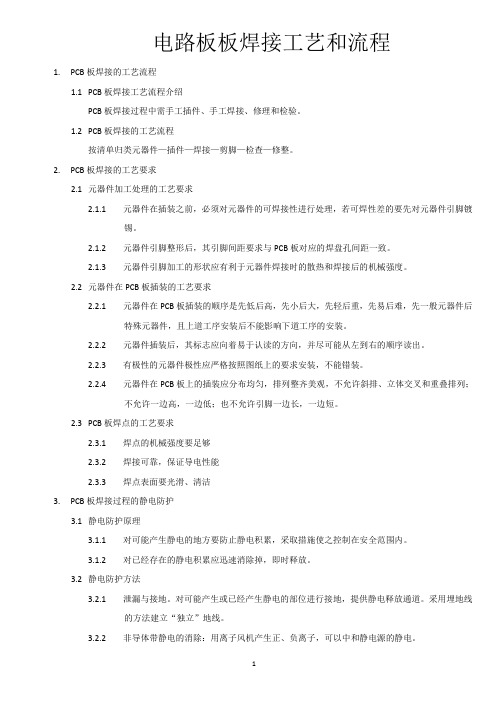
电路板板焊接工艺和流程1.PCB板焊接的工艺流程1.1PCB板焊接工艺流程介绍PCB板焊接过程中需手工插件、手工焊接、修理和检验。
1.2PCB板焊接的工艺流程按清单归类元器件—插件—焊接—剪脚—检查—修整。
2.PCB板焊接的工艺要求2.1元器件加工处理的工艺要求2.1.1元器件在插装之前,必须对元器件的可焊接性进行处理,若可焊性差的要先对元器件引脚镀锡。
2.1.2元器件引脚整形后,其引脚间距要求与PCB板对应的焊盘孔间距一致。
2.1.3元器件引脚加工的形状应有利于元器件焊接时的散热和焊接后的机械强度。
2.2元器件在PCB板插装的工艺要求2.2.1元器件在PCB板插装的顺序是先低后高,先小后大,先轻后重,先易后难,先一般元器件后特殊元器件,且上道工序安装后不能影响下道工序的安装。
2.2.2元器件插装后,其标志应向着易于认读的方向,并尽可能从左到右的顺序读出。
2.2.3有极性的元器件极性应严格按照图纸上的要求安装,不能错装。
2.2.4元器件在PCB板上的插装应分布均匀,排列整齐美观,不允许斜排、立体交叉和重叠排列;不允许一边高,一边低;也不允许引脚一边长,一边短。
2.3PCB板焊点的工艺要求2.3.1焊点的机械强度要足够2.3.2焊接可靠,保证导电性能2.3.3焊点表面要光滑、清洁3.PCB板焊接过程的静电防护3.1静电防护原理3.1.1对可能产生静电的地方要防止静电积累,采取措施使之控制在安全范围内。
3.1.2对已经存在的静电积累应迅速消除掉,即时释放。
3.2静电防护方法3.2.1泄漏与接地。
对可能产生或已经产生静电的部位进行接地,提供静电释放通道。
采用埋地线的方法建立“独立”地线。
3.2.2非导体带静电的消除:用离子风机产生正、负离子,可以中和静电源的静电。
常使用的防静电器材4.电子元器件的插装电子元器件插装要求做到整齐、美观、稳固。
同时应方便焊接和有利于元器件焊接时的散热。
4.1元器件分类按电路图或清单将电阻、电容、二极管、三极管,变压器,插排线、座,导线,紧固件等归类。
- 1、下载文档前请自行甄别文档内容的完整性,平台不提供额外的编辑、内容补充、找答案等附加服务。
- 2、"仅部分预览"的文档,不可在线预览部分如存在完整性等问题,可反馈申请退款(可完整预览的文档不适用该条件!)。
- 3、如文档侵犯您的权益,请联系客服反馈,我们会尽快为您处理(人工客服工作时间:9:00-18:30)。
PCB焊接工艺1、PCB板焊接的工艺流程1.1 PCB焊接工艺流程介绍PCB焊接过程中需要手工插件、手工焊接、修理和检验1.2 PCB焊接的工艺流程按清单归类器件—插件—焊接—剪脚—检查—修正2、PCB板焊接的工艺要求2.1 元器件加工处理的工艺要求2.1.1 元器件在插装之前,必须对元器件的可焊接性进行处理,若可焊性差的要先对元器件引脚镀锡2.1.2 元器件引脚整形后,其引脚间距要求与PCB板对应的焊盘孔间距一致。
2.1.3 元器件引脚的加工形状应有利于元器件焊接时的散热和焊接后的机械强度2.2 元器件在PCB板插装的工艺要求2.2.1 元器件在PCB插装的顺序是先低后高,小小后大,先轻后重,先一般元器件后特殊元器件,且上道工序安装后补能影响下道工序的安装。
2.2.2 元器件插装后,其标志应向着易于认读的方向,并尽可能从左到右的顺序读出。
2.2.3 有极性的元器件极性应严格按照图纸上的要求安装,不能错装。
2.2.4 元器件在PCB板上的插装应分步均匀,排列整齐美观,不允许斜排、立体交叉和重叠排列;不允许一边高,一边低;也不允许一边引脚长,一边短。
2.3 PCB板焊接的工艺要求2.3.1 焊点的机械强度要足够2.3.2 焊接可靠,保证导电性能2.3.3 焊点表面要光滑、清洁3、PCB焊接过程的静电防护3.1 静电防护原理3.1.1 对可能产生静电的地方要防止静电积累,采取措施使之控制在安全范围内。
,即时释放。
3.2 静电防护方法3.2.1 泄露与接地。
对可能产生或已经产生的部位进行接地,提供静电释放通道。
采用埋底线的方法建立“独立”底线。
3.2.2 非导体带静电的消除:用离子风机产生正负离子,可以中和静电源的静电。
常使用的防静电器材。
4、电子元器件的插装电子元器件插装要求做到整齐、美观、稳固。
同时应方便焊接和有利于元器件焊接时的散热。
4.1 元器件分类按电路图或清淡将电阻、电容、二极管、三极管,变压器,插件先、座,导线,紧固件等归类。
4.2.1 元器件整形的基本要求所有元器件引脚均不得从根部弯曲,一般应留1.5MM以上。
要尽量将有字符的元器件面置于易观察的位置。
4.2.2 元器件的引脚成形手工加工的元器件整形,弯引脚可以借助镊子或小螺丝刀对引脚整形。
4.3 插件顺序手工插装元器件,应满足工艺要求。
插装时不要用手直接碰元器件引脚和印刷版铜箔。
4.4 元器件插装的方式二极管、电容器、电阻器等元器件军事俯卧式安装在印刷PCB上的。
5、焊接主要工具手工焊接是每一个电子装配工得必须掌握的技术,正确选用焊料和焊剂,根据实际情况喧杂焊接工具,是保证焊接质量的必备条件。
5.1 焊料与焊剂5.1.1 焊料能熔合两种或两种以上的金属,使之成为一个整体的易熔金属或合金都叫焊料。
通常用的焊料中,喜占62.7%,铅占37.3%。
这种配比的焊锡熔点和凝固点都是183℃,可以有液态直接冷却为固态,不经过半液态,焊点可迅速凝固,缩短焊接时间,减少虚焊,该点温度称为共品点,该成分配比的焊锡称为共品焊锡。
共品焊锡具有低熔点,熔点与凝固点一致,流动性好,表面张力小,润湿性好,机械强度高,焊点能承受较大的拉力和剪力,导电性能好的特点。
5.1.2 助焊剂助焊剂是一种焊接辅助材料,其作用如下:去除氧化膜防止氧化减少表面张力使焊点美观常用的助焊剂有松香、松香酒精助焊剂、焊膏、氧化锌助焊剂、氧化胺助焊剂等。
焊接中常采用中心夹有松香助焊剂、含锡量为61%的39锡铅焊锡丝,也成为松香焊锡丝。
5.2 焊接工具的选用5.2.1 普通电烙铁普通电烙铁只适合焊接要求不高的场合使用。
如焊接导线、连接线等。
5.2.2 恒温电烙铁恒温电烙铁的重要特点是有一个恒温控制装置,使得焊接温度稳定,用来焊接较精细的PCB板。
5.2.3 吸锡器吸锡器实际是一个小型手动空气泵,压下吸锡器的压杆,就排除了吸锡器腔内的空气:释放吸锡器的压杆的锁钮,弹簧推动压杆迅速回到原位,在吸锡器腔内形成空气的负压力,就能够吧熔融的焊料吸走。
5.2.4 热风枪热风枪又称贴片电子元器件拆焊台。
它专门用于表面贴片安装电子元器件(特别是多引脚的SMD集成电路)的焊接和拆卸。
5.2.5 烙铁头当焊接焊盘较大的可选用截面式烙铁头当焊接焊盘较小的可选用尖嘴式烙铁头。
当和焊接多脚贴片IC是可以选用刀型烙铁头。
当焊接元器件高低变化的电路是,可以使用弯型电烙铁。
6、手工焊接的流程和方法6.1手工焊接的条件被焊件必须具备可焊性被焊金属表面应保持清洁使用合适的助焊剂具有适当的焊接温度具有合适的焊接时间6.2 手工焊接的方法6.2.1 电烙铁与焊锡丝的握法手工焊接握电烙铁的方法有反握、正握及握笔式有三种:下图是两种焊锡丝的拿法6.2.2 手工焊接的步骤准备焊接:清洁焊接部位的积尘及污渍、元器件的插装、导线与接线端钩连,为焊接做好前期的预准备工作。
加热焊接:将沾有少许焊锡的电烙铁头接触被焊元器件约几秒钟。
若是要拆下PCB板上的元器件,则待烙铁头加热后,用手或镊子轻轻拉动元器件,看是否可以取下。
清理焊接面:若所焊部位焊锡过多,可将烙铁头上的焊锡甩掉(注意不要烫伤皮肤,也不要甩到PCB 上),然后用烙铁头“沾”些焊锡出来,若焊点焊锡过少、不圆滑时,可以用点烙铁头“蘸”些焊锡对焊点进行补焊。
检查焊点:看焊点是否圆润、光泽、牢固,是否有雨周围元器件连焊的现象。
6.2.3 手工焊接的方法加热焊件:恒温烙铁温度一般控制在280至360℃之间,焊接时间控制在4秒以内部分元器件的特殊焊接要求:焊接时烙铁头与PVB板成45°角,电烙铁头顶住焊盘和元器件引脚然后给元器件和焊盘均匀预热。
移入焊锡丝焊锡丝从元器件脚和烙铁接触面处引入,焊锡丝应靠在元器件脚与烙铁头之间。
加热焊件移入焊锡移开焊锡当焊锡丝熔化(要掌握进锡速度)焊锡散满整个焊盘时,即可以45角方向拿开焊锡丝。
移开电烙铁焊锡丝拿开后,烙铁继续放在焊盘上持续1~2秒,当焊锡只有轻微烟雾冒出时,即可拿开烙铁,拿开烙铁时,不要过于迅速或者用力往上挑,以免溅落锡珠、锡点、或使焊点拉尖等,同时要保证被焊元器件在焊锡凝固之前不要移动或受到震动,否则极易造成焊点结构疏松、虚焊等现象。
移开焊锡移开电烙铁6.3 导线和接线端子的焊接6.3.1 常用连接导线单股导线多股导线屏蔽线6.3.2 导线焊前处理剥绝缘层导线焊接前要除去末端绝缘层。
拔出绝缘层可用普通工具或专用工具。
用剥线钳或普通偏口钳剥线时要注意对单股线不应伤及导线,多股先及屏蔽线不断线,否则将影响接头质量。
对多股线剥除绝缘层是注意将线芯拧成螺旋状,一般采用边拽边拧的方式。
预焊预焊是导线焊接的关键步骤。
导线的预又称为挂锡,但注意导线挂锡时要边上锡边旋转,旋转方向与拧合方向一致,多股导线挂锡要注意“烛芯效应”,即焊锡浸入绝缘层内,造成软线变硬,容易导致接头故障。
6.3.3 导线和接线端子的焊接绕焊绕焊把经过上锡的导线端头在接线端子上缠一圈,用钳子拉紧缠牢后进行焊接,绝缘层不要接触端子,导线一定要留1~3MM为宜。
钩焊钩焊是将导线端子弯成钩行,钩在接线端子上并用钳子夹紧后施焊。
搭焊搭焊把经过镀锡的导线搭到接线端子上施焊。
绕焊钩焊搭焊7、PCB板上的焊接7.1 PCB板焊接的注意事项7.1.1 电烙铁一般应选择内热式20-35W或调温式,烙铁的温度不超过400℃的为宜。
烙铁头形状应根据PCB板焊盘大小采用截面或者尖嘴式,目前PCB板发展是小型密集化,因此一般常用尖嘴是烙铁头。
7.1.2 加热是应尽量使烙铁头同时接触印刷版上铜箔和元器件引脚,对较大的焊盘(直径大于5MM)焊接时可移动烙铁,即烙铁绕焊盘转动,以免长时间停留一点导致局部过热。
7.1.3 金属化孔的焊接,焊接时不仅要让焊料润湿焊盘,而且孔内也要润湿填充。
因此金属化孔加热时间应长于单面板。
(A)单面板(B)双面板7.1.4 焊接时不要用烙铁头摩擦焊盘的方法增强焊料润湿性能,而要靠表面清理和预焊。
7.2 PCB板子的焊接工艺7.2.1 焊前准备按照元器件清单检查元器件型号、规格及数量是否符合要求。
焊接人员戴防静电手腕,确认恒温烙铁接地。
7.2.2 焊接顺序元器件的装焊顺序依次是电阻器、电容器、二极管、三极管、集成电路、大功率管,其它元器件是先小后大。
7.2.3 对元器件焊接的要求电阻器的焊接。
按元器件清单将电阻器准确地装入规定位置,并要求标记向上,字向一致。
装完一种规格再装另一种规格,尽量是电阻器的高低一致。
焊接后将露在PCB板表面上多余的引脚齐根剪去。
电容器的焊接。
将电容器按元器件清单装入规定位置,并注意有极性的电容器其“+”与“-”极性不能接错。
电容器上的标记方向要易看得见。
先装玻璃鍒电容器、金属膜电容器、瓷介电容器,最后装电解电容。
二极管的焊接。
正确辨认正负极后按要求装入规定位置,型号及标记要易看得见。
焊接立式二极管时,对最短的引脚焊接时,时间不要超过2秒钟。
三极管的焊接。
按照要求e、b、c三根引脚装入规定位置。
焊接时间应尽可能的短些,焊接时用镊子夹住引脚,以帮助散热。
焊接大功率三极管时,若需要加装散热片,应将接触面平整、光滑后再紧固。
集成电路的焊接。
将集成电路插装在线路板上,按元器件清单要求,检查集成电路的型号、引脚位置是否符合要求。
焊接时先焊集成电路边沿的二只引脚,以使其定位,然后再从左到右或从上至下进行逐个焊接。
焊接时,烙铁一次沾取锡量为焊接2~3引脚的量,烙铁头先接触印刷电路的铜箔,待焊锡进入集成电路引脚底部时,烙铁头再接触引脚,接触时间以不超过3秒钟未宜,而且不要使焊锡均匀包住引脚。
焊接完毕后要检查一下,是否有漏焊、碰焊、虚焊之处,并清理焊点处得焊料。
7.3 焊接质量的分析及拆焊7.3.1 焊接的质量分析构成焊点虚焊主要有下列几种原因:被焊件引脚受氧化;被焊件引脚表面有污垢;焊锡的质量差;焊接质量部过关,焊接是焊锡用量太少;电烙铁温度太低或太高,焊接时间过长或太短;焊接时焊锡未凝固前焊件抖动。
7.3.2 手工焊接质量分析手工焊接常见的不良现象过热7.3.3 拆焊工具在拆卸过程中,主要用的工具有:电烙铁、吸锡器、镊子等。
7.3.4 拆卸方法引脚较少的元器件拆法:一手拿着电烙铁加热待拆元器件引脚焊点,一手用镊子夹找元器件,待焊点焊锡熔化时,用夹子将元器件轻轻往外拉。
多焊点元器件且引脚较硬的元器件拆法:采用吸锡器逐个将引脚焊锡洗干净后,再用夹子取出元器件,如图:用吸锡器拆卸元器件双列或四列IC的引脚用热风枪拆焊,温度控制在350℃,风量控制在3~4格,对着引脚垂直、均匀的来回吹热风,同时用镊子的尖端靠在集成电路的一个角上,待所有引脚焊锡熔化时,用镊子尖轻轻将IC挑起。