物料平衡与热平衡计算
化工中物料衡算和热量衡算公式
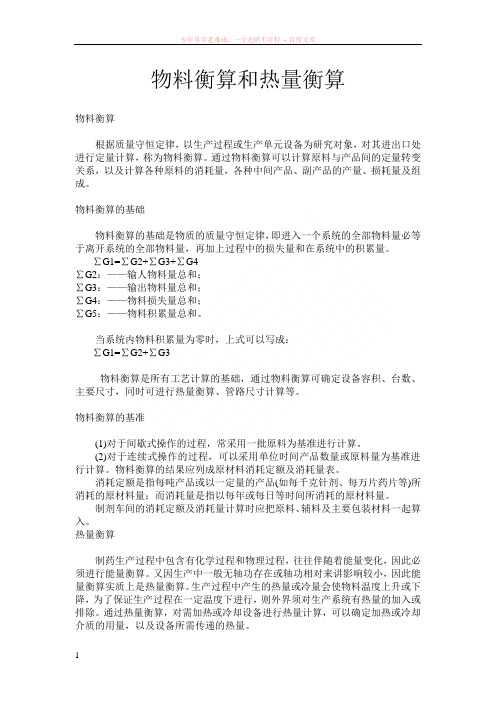
物料衡算和热量衡算物料衡算根据质量守恒定律,以生产过程或生产单元设备为研究对象,对其进出口处进行定量计算,称为物料衡算。
通过物料衡算可以计算原料与产品间的定量转变关系,以及计算各种原料的消耗量,各种中间产品、副产品的产量、损耗量及组成。
物料衡算的基础物料衡算的基础是物质的质量守恒定律,即进入一个系统的全部物料量必等于离开系统的全部物料量,再加上过程中的损失量和在系统中的积累量。
∑G1=∑G2+∑G3+∑G4∑G2:——输人物料量总和;∑G3:——输出物料量总和;∑G4:——物料损失量总和;∑G5:——物料积累量总和。
当系统内物料积累量为零时,上式可以写成:∑G1=∑G2+∑G3物料衡算是所有工艺计算的基础,通过物料衡算可确定设备容积、台数、主要尺寸,同时可进行热量衡算、管路尺寸计算等。
物料衡算的基准(1)对于间歇式操作的过程,常采用一批原料为基准进行计算。
(2)对于连续式操作的过程,可以采用单位时间产品数量或原料量为基准进行计算。
物料衡算的结果应列成原材料消耗定额及消耗量表。
消耗定额是指每吨产品或以一定量的产品(如每千克针剂、每万片药片等)所消耗的原材料量;而消耗量是指以每年或每日等时间所消耗的原材料量。
制剂车间的消耗定额及消耗量计算时应把原料、辅料及主要包装材料一起算入。
热量衡算制药生产过程中包含有化学过程和物理过程,往往伴随着能量变化,因此必须进行能量衡算。
又因生产中一般无轴功存在或轴功相对来讲影响较小,因此能量衡算实质上是热量衡算。
生产过程中产生的热量或冷量会使物料温度上升或下降,为了保证生产过程在一定温度下进行,则外界须对生产系统有热量的加入或排除。
通过热量衡算,对需加热或冷却设备进行热量计算,可以确定加热或冷却介质的用量,以及设备所需传递的热量。
热量衡算的基础热量衡算按能量守恒定律“在无轴功条件下,进入系统的热量与离开热量应该平衡”,在实际中对传热设备的衡算可由下式表示Q1+Q2+Q3=Q4+Q5+Q6(1—1)式中: Q1—所处理的物料带入设备总的热量,KJ;Q2—加热剂或冷却剂与设备和物料传递的热量(符号规定加热剂加入热量为“+”,冷却剂吸收热量为“-”),KJ;Q3—过程的热效率,(符号规定过程放热为“+”;过程吸热为“-”)Q4—反应终了时物料的焓(输出反应器的物料的焓)Q5—设备部件所消耗的热量,KJ;Q6—设备向四周散失的热量,又称热损失,KJ;热量衡算的基准可与物料衡算相同,即对间歇生产可以以每日或每批处理物料基准。
转炉炼钢物料平衡和热平衡计算 模板-
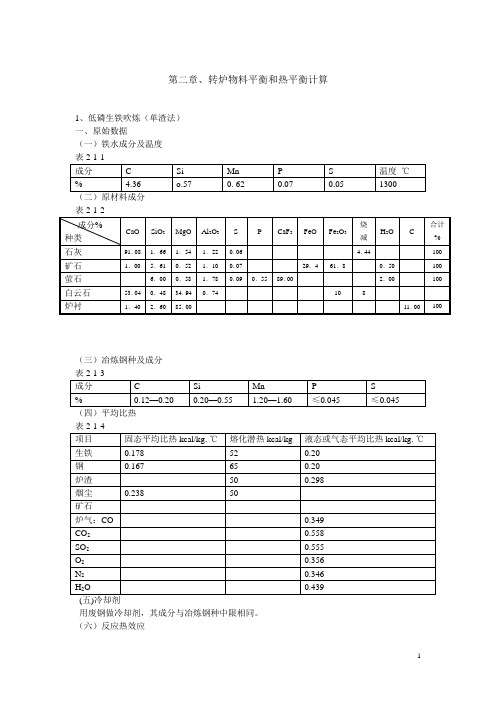
第二章、转炉物料平衡和热平衡计算1、低磷生铁吹炼(单渣法)一、原始数据(一)铁水成分及温度(二)原材料成分(三)冶炼钢种及成分(四)平均比热(五)冷却剂用废钢做冷却剂,其成分与冶炼钢种中限相同。
(六)反应热效应反应热效应通常采用25℃为参考温度,比较常用的反应数据见表2-1-5(七)根据国内转炉实测数据选取1、渣中铁珠量为渣量的2.5%;2、金属中[C]假定85%氧化成CO,15%氧化成CO2;3、喷溅铁损为铁水量的0.3%;4、取炉气平均温度1450℃,自由氧含量0.5%,烟尘量为铁水量的1.8%,其中FeO=75%,Fe203=22%;5、炉衬侵蚀量为铁水量的0.15%;6、氧气成分为98.9% O2,1.5% N2。
根据铁水成分,渣料质量,采用单渣不留渣操作。
先以100公斤铁水为计算基础。
(一)炉渣及其成分的计算1、铁水中各元素氧化量表2-1-6成分,kgC Si Mn P S 合计项目铁水 4.36 0.57 0.62 0.07 0.05终点钢水0.13 痕迹0.13 0.008 0.019氧化量 4.23 0.57 0.49 0.062 0.031 5.308 [C]:取终点钢水含碳量0.15%;[Si]:在碱性氧气转炉炼钢中,铁水中的Si几乎全部被氧化;[Mn]:顶底复吹转炉残锰量取60%;[P]:采用低磷铁水吹炼,铁水中磷90%进入炉渣,10%留在钢中;[S]:氧气转炉去硫率不高,取40%。
2、各元素氧化量,耗氧量及其氧化产物量见表2-1-73、造渣剂成分及数量根据国内同类转炉有关数据选取1)矿石加入量及成分矿石加入量为1.00公斤/100公斤铁水,成分及重量见表2-1-82)萤石加入量及成分萤石加入量为0.30kg/kg铁水,其成分及重量见表2-1-93)炉衬侵蚀量为0.200公斤/100公斤铁水,其成分及重量见2-1-104)生白云石加入量及成分加入的白云石后,须保证渣中(MgO)含量在6—8%之间,经试算后取轻烧白云石加入量为1.2公斤/100公斤铁水。
钢铁热平衡
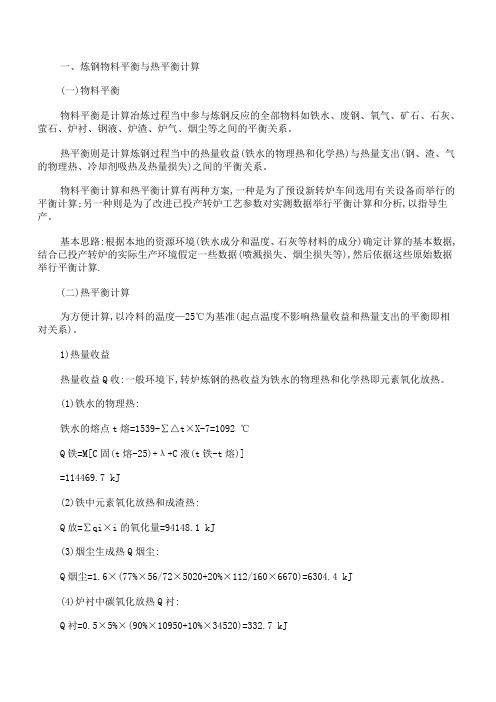
一、炼钢物料平衡与热平衡计算(一)物料平衡物料平衡是计算冶炼过程当中参与炼钢反应的全部物料如铁水、废钢、氧气、矿石、石灰、萤石、炉衬、钢液、炉渣、炉气、烟尘等之间的平衡关系。
热平衡则是计算炼钢过程当中的热量收益(铁水的物理热和化学热)与热量支出(钢、渣、气的物理热、冷却剂吸热及热量损失)之间的平衡关系。
物料平衡计算和热平衡计算有两种方案,一种是为了预设新转炉车间选用有关设备而举行的平衡计算;另一种则是为了改进已投产转炉工艺参数对实测数据举行平衡计算和分析,以指导生产。
基本思路:根据本地的资源环境(铁水成分和温度、石灰等材料的成分)确定计算的基本数据,结合已投产转炉的实际生产环境假定一些数据(喷溅损失、烟尘损失等),然后依据这些原始数据举行平衡计算.(二)热平衡计算为方便计算,以冷料的温度—25℃为基准(起点温度不影响热量收益和热量支出的平衡即相对关系)。
1)热量收益热量收益Q收:一般环境下,转炉炼钢的热收益为铁水的物理热和化学热即元素氧化放热。
(1)铁水的物理热:铁水的熔点t熔=1539-∑△t×X-7=1092 ℃Q铁=M[C固(t熔-25)+λ+C液(t铁-t熔)]=114469.7 kJ(2)铁中元素氧化放热和成渣热:Q放=∑qi×i的氧化量=94148.1 kJ(3)烟尘生成热Q烟尘:Q烟尘=1.6×(77%×56/72×5020+20%×112/160×6670)=6304.4 kJ(4)炉衬中碳氧化放热Q衬:Q衬=0.5×5%×(90%×10950+10%×34520)=332.7 kJ以是,Q收=114469.7+94148.1+6304.4+332.7=215254.9 kJ2)热量支出钢液物理热:(1)钢液的熔点t熔=1539-∑△t×X-7=1520℃Q铁=M[C固(t熔-25)+λ+C液(t终-t熔)]=130277.0 kJ2)熔渣物理热Q渣= M[ C液(t液-25)+λ]=31074.6kJ(炉渣温度比钢水低20℃)3)矿石分化吸热Q矿=1×(29.4%×56/72×5020+61.8%×112/160×6670+209.20)=4242.5kJ4)烟尘带走热Q尘=烟尘量1.6×[1.0(1450-25)+209.20]=2614.7 kJ5)炉气物理热Q气=10.71×1.136(1450-25)=17337.3 kJ6)渣中铁珠带走热量Q和=1.112[0.745(1520-25)+217.568+0.8368(1650-1520)=1601.4 kJ7)喷溅金属带走热量Q和=1.0[0.745(1520-25)+217.568+0.8368(1650-1520)=1440.1 kJ8)热损失吹炼过程当中的热量损失包括炉口和炉体的热辐射及冷却水带走的热量等,因炉容及炉口巨细、耐材厚度等不同而异,一般为热收益的3~8%,取5%。
改好的物料平衡及热平衡计算
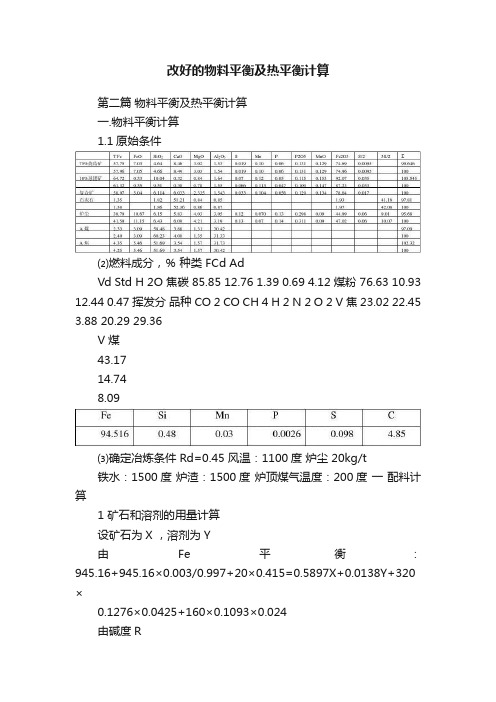
改好的物料平衡及热平衡计算第二篇物料平衡及热平衡计算一.物料平衡计算1.1原始条件⑵燃料成分,%种类 FCd AdVd Std H 2O 焦碳 85.85 12.76 1.39 0.69 4.12 煤粉 76.63 10.93 12.44 0.47 挥发分品种 CO 2 CO CH 4 H 2 N 2 O 2 V 焦 23.02 22.45 3.88 20.29 29.36V 煤43.1714.748.09⑶确定冶炼条件 Rd=0.45 风温:1100度炉尘 20kg/t铁水:1500度炉渣:1500度炉顶煤气温度:200度一配料计算1 矿石和溶剂的用量计算设矿石为X ,溶剂为Y由Fe 平衡:945.16+945.16×0.003/0.997+20×0.415=0.5897X+0.0138Y+320×0.1276×0.0425+160×0.1093×0.024由碱度R0.06030.52363200.12760.03541600.10930.04200.06091.14.80.061140.01863200.12760.51691600.10930.6023200.0643602.8X Y X Y ++??+??-?=++??+??-?-?由以上两式解,得 X=1617,Y=63.853 1.4.炉渣成分的计算⑴炉渣中CaO 的量: G CaO 渣=131.866kg/t ⑵炉渣中SiO 2的量:G SiO2=119.878kg/t ⑶炉渣中FeO 的量: G FeO 渣=945.16×0.00372* 3.66/0.99756kg t=⑷炉渣中MgO 的量:G MgO 渣=0.0235×1617+0.0086×63.853+320×0.1276×0.0157+160×0.10 93×0.0135-20×0.0421=38.584 kg/t ⑸炉渣中MnO 的量:G MnO 渣=0.0017×1617×71/55×50%=1.07kg/t式中: 50%—锰元素在炉渣中的分配率⑹炉渣中Al 2O 3的量:故G Al2O3渣=0.0154×1617+0.0087×563.853+320×0.1276×0.3773+160×0.1 093×0.3133-20×0.0019=45.714kg/t ⑺炉渣中S 的量: G S 渣原料﹑燃料带入的S 总量:S 1 =0.0033×1617+320×0.0069+160×0.0047=3.493 kg/t 进入生铁的S 量: S 2 =1000S%=1000×0.026%=0.26kg/t 进入煤气的S 量: S 3 = G S 5%=3.493×0.05=0.175kg/t 进入炉尘的S: S 4=20×0.0013=0.026kg/t进入炉渣的S:S= 3.493-0.175-0.26-0.026=3.032kg/t⑴生铁含磷[P]:[P]=(0.0056×1617-0.0013×20) ?1000100=0.088⑵生铁含锰[Mn]: 故[Mn]=1.07×7155×1000100=0.080⑶生铁含碳[C]:[C]= 100-94.516-0.48-0.08-0.026-0.088=4.81 2..物料平衡计算 2.1.风量的计算 C 直=2824×4.8+5512×2.16+6260×0.88+5612×0.45×948.74=96.57kg3200.85851600.766396.580.7%3200.85851600.7663200.214 446.74245.94.C K g =?+?--?+?-?-=燃()V O2=3245.94*22.4229.5424m=.2104.0015.05.0)015.01(21.02=?+-?=O2321071O V V mO ==风1386.75G V r K g=?=风风空气2.2炉顶煤气成分及数量的计算⑴甲烷的体积V CH4① 由燃料碳素生成的甲烷的量为:V CH4碳=2.78×322.4 5.1912m=② 焦炭挥发分中的甲烷的量为:V CH4焦=320×0.0139×0.0388×22.4/16=0.24 ③ 故V CH4=5.19+0.24=5.43m 3 ⑵氢的体积V H2① 风口燃烧生成:V H2=V 风×0.015=16.073m② 焦碳和煤粉中带入的:V H2=(320×0.0139×0.2029+160×0.1244×0.4317)×22.4/2=106.35 3m ③ 生成CH 4的H 2V H2=2.78×22.4/12×2=10.383m ④ 参加还原的H 2 V H2=(a+b)40%=48.973m 故V H2=①+②-③-④=63.073m⑶二氧化碳的体积V CO2 ①间接还原生成a:Fe 2O 3+CO →2FeO+CO 2V CO2 =(0.786×1617+0.0197×63.853-20×0.2144)=177.60m 3 ② FeO + H 2 → Fe + H 2O72 22.4γH ×945.16*725648.99 所以γH =0.1295V CO2=945.16×22.4/56×(1-0.45-γH 2)=158.98③石灰石分解产生的CO 2量为:V CO2分=G 熔CO 2%熔22.4/44=0.4208Y ×22.4/44=13.68 m 3④焦炭挥发分中CO 2的量为:V CO2挥= 380×0.0139×0.2302×22.4/44=0.62 m 3故V CO2=①+②+③+④=350.016 m 3⑷一氧化碳的体积V CO① 分口前碳素燃烧生成的CO 量为:V CO 燃=G C 燃22.4/12=245.94×22.4/12=459.09m 3② 间接还原消耗的CO 量为:V=336.58m 3③ 焦炭挥发分中的CO 量为:V CO 挥=320×0.0139×0.2245×24/28=0.799m 3 ④ 直接还原生成CO 量为:V CO 间=96.57×22.4/12=180.26m 3 故V CO = ①+④+③-②=303.35m 3 ⑸氮气体积V N2①鼓风带入的N 2量为:V N2风=1071×(1-0.015)×79%=833.4 m 3②焦炭和煤粉带入的N 2量为:V N2焦+煤=(320×0.0139×0.2936+160×0.1244×0.1474)×22.4/28=3.39 m 3故V N2= V N2风+ V N2焦+煤=836.79m 330.2246440.1946280.5369280.040520.0035161.36/22.4kg mρ?+?+?+?+?==煤气 1.361558.6562119.77G kg=?=煤气二.热平衡计算1热量收入Q 收⑴碳素氧化放热Q C① 碳素氧化为放出的热量Q CO2+COQ CO2+CO =(303.35-0.799)×5241.72+(177.60+158.98)×17869.5=7601347.45kJ式中 17869.5—C 氧化CO 2为放热,kJ/m 3 式中 5241.72—C 氧化CO 为放热,kJ/ m 3 ⑵鼓风带入的热量Q 风Q=(1071×98%×98.5%×1.4233+1071×98%×1.5%×1.7393)×1100=1648727.32kJ式中Q 空气—在11000C 下空气的热容量,其值为1.4233kJ/(m 3×0C) Q 水汽—在11000C 下水汽的热容量,其值为1.7393kJ/(m 3×0C)⑶氢氧化放出热:Q H2=(48.97+2.78×22.4/12)×10788.58=640302.22 kJ式中10788.58氢氧化水为放热,kJ/ m 3 ⑷成渣热Q 渣:石灰石分解产生的CaO 和MgO 与SiO 2反应热。
湖工大转炉物料平衡与热平衡计算
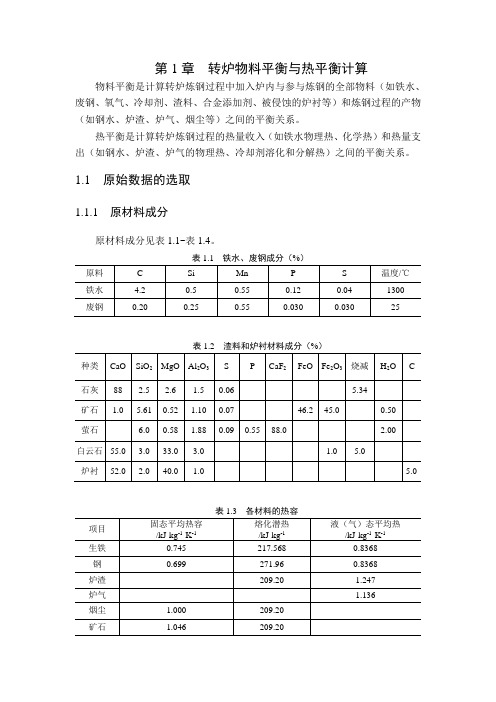
第1章转炉物料平衡与热平衡计算物料平衡是计算转炉炼钢过程中加入炉内与参与炼钢的全部物料(如铁水、废钢、氧气、冷却剂、渣料、合金添加剂、被侵蚀的炉衬等)和炼钢过程的产物(如钢水、炉渣、炉气、烟尘等)之间的平衡关系。
热平衡是计算转炉炼钢过程的热量收入(如铁水物理热、化学热)和热量支出(如钢水、炉渣、炉气的物理热、冷却剂溶化和分解热)之间的平衡关系。
1.1 原始数据的选取1.1.1 原材料成分原材料成分见表1.1~表1.4。
表1.1 铁水、废钢成分(%)原料 C Si Mn P S 温度/℃铁水 4.2 0.5 0.55 0.12 0.04 1300 废钢0.20 0.25 0.55 0.030 0.030 25表1.2 渣料和炉衬材料成分(%)种类CaO SiO2MgO Al2O3S P CaF2FeO Fe2O3烧减H2O C 石灰88 2.5 2.6 1.5 0.06 5.34矿石 1.0 5.61 0.52 1.10 0.07 46.2 45.0 0.50萤石 6.0 0.58 1.88 0.09 0.55 88.0 2.00白云石55.0 3.0 33.0 3.0 1.0 5.0炉衬52.0 2.0 40.0 1.0 5.0表1.3 各材料的热容项目固态平均热容/kJ·kg-1·K-1熔化潜热/kJ·kg-1液(气)态平均热/kJ·kg-1·K-1生铁0.745 217.568 0.8368 钢0.699 271.96 0.8368 炉渣209.20 1.247 炉气 1.136 烟尘 1.000 209.20矿石 1.046 209.20表1.4 反应热效应(25℃)元素反应反应热/kJ·kg-1元素[C]+1/2O2=CO10950C[C]+O2=CO234520Si [Si]+O2=SiO228314P 2[P]+5/2O2=P2O518923Mn [Mn]+1/2O2=MnO 7020[Fe]+1/2O2=FeO 5020Fe[Fe]+3/2O2=Fe2O36670SiO2SiO2+2CaO=2CaOSiO22070P2O5P2O5+4CaO=4CaO P2O550201.1.2 假设条件根据各类转炉生产实际过程假设:(1)渣中铁珠量为渣量的8%;(2)喷溅损失为铁水量的1%;(3)熔池中碳的氧化生成90%CO,10% CO2;(4)烟尘量为铁水量的1.6%,其中wFeO为77%,wFe2O3=20%;(5)炉衬侵蚀量为铁水量的0.5%;(6)炉气温度取1450℃,炉气中自由氧含量为总炉气量的0.5%;(7)氧气成分:98.5%氧气,1.5%氮气。
物料平衡与热平衡计算
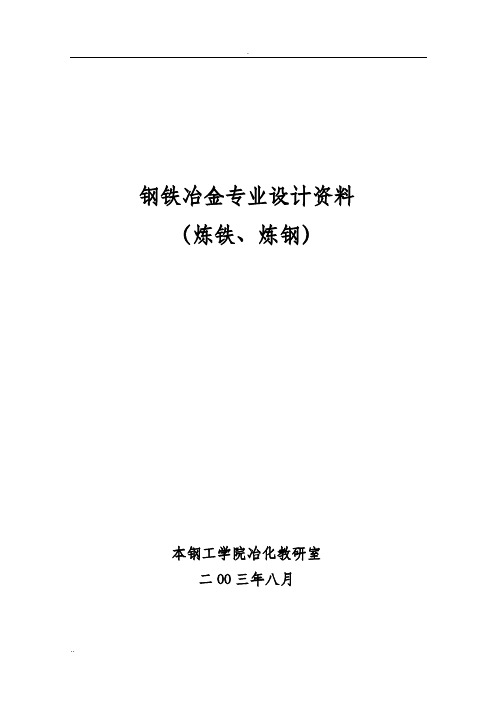
钢铁冶金专业设计资料(炼铁、炼钢)本钢工学院冶化教研室二00三年八月第一章物料平衡与热平衡计算物料平衡和热平衡计算是氧气顶吹转炉冶炼工艺设计的一项基本的计算,它是建立在物质和能量不灭定律的基础上的。
它以转炉作为考察对象,根据装入转炉内或参与炼钢过程的全部物料数据和炼钢过程的全部产物数据,如图1-1-1所示的收入项数据和支出项数据,来进行物料的重量和热平衡计算。
通过计算,可以定量地掌握冶炼工重要参数,做到“胸中有数”。
对指导生产和分析研究改进冶炼工艺,设计转炉炼钢车间等均有其重要意义。
由于转炉炼钢过程是一个十分复杂的物理化学过程,很显然,要求进行精确的计算较为困难,特别是热平衡,只能是近似计算,但它仍然有十分重要的指导意义。
物料平衡和热平衡计算,一般可分为两面种方案。
第一种方案是为了设计转炉及其氧枪设备以及相应的转炉炼钢车间而进行的计算,通常侧重于理论计算,特别是新设计转炉而无实际炉型可以参考的情况下;另一种方案是为了校核和改善已投产的转炉冶炼工艺参数及其设备参数或者采用新工艺新技术等,而由实测数据进行的计算,后者侧重于实测。
本计算是采用第一种方案。
目前,我国顶吹转炉所采用的生铁基本上为低磷的(0.10~0.40%)和中磷的(0.40~1.00%)两种,对这两种不同含磷量生铁的冶炼工艺制度也不相同。
因此,下面以50吨转炉为例,分别就低磷生铁和高磷生铁两种情况,进行物料平衡和热平衡计算。
1.1原始数据1.1.1铁水成分及温度表1-1-11.1.2原材料成分表1-1-2 原材料成分..表2-1-1铁水成分与温度转炉冶炼钢种常为普通碳素钢和低合金钢,在此以要求冶炼BD3钢考虑,其成分见表2-1-3..1.1.4平均比热表1-1-41.1.5冷却剂用废钢作冷却剂,其成份与冶炼钢种成份的中限相同。
(见表1-1-3) 1.1.6反应热效应虽然炉内化学反应,实际上是在炉料温度和炉内上部气相温度之间的任一温度发生的,但反应热效应通常仍采用25℃作为参考温度,值得指出的是,反应热还与组分在铁水中存在形态有关,至今对参与化学反应有关的实际组成物还有不同的看法。
干燥过程的物料平衡与热平衡计算

干燥过程的物料与热平衡计算1、湿物料的含水率湿物料的含水率通常用两种方法表示。
(1)湿基含水率:水分质量占湿物料质量的百分数,用ω表示。
100%⨯=湿物料的总质量水分质量ω(2)干基含水率:由于干燥过程中,绝干物料的质量不变,故常取绝干物料为基准定义水分含量。
把水分质量与绝干物料的质量之比定义为干基含水率,用χ表示。
100%⨯=量湿物料中绝干物料的质水分质量χ(3)两种含水率的换算关系: χχω+=1 ωωχ-=1 2、湿物料的比热与焓(1)湿物料的比热m C湿物料的比热可用加和法写成如下形式:w s m C C C χ+=式中:m C —湿物料的比热,()C kg J ⋅绝干物料/k ; s C —绝干物料的比热,()C kg J ⋅绝干物料/k ; w C —物料中所含水分的比热,取值4.186()C kg J ⋅水/k (2)湿物料的焓I '湿物料的焓I '包括单位质量绝干物料的焓和物料中所含水分的焓。
(都是以0C 为基准)。
()θθχθχθm s w s C C C C I =+=+='186.4式中:θ为湿物料的温度,C 。
3、空气的焓I空气中的焓值是指空气中含有的总热量。
通常以干空气中的单位质量为基准称作比焓,工程中简称为焓。
它是指1kg 干空气的焓和它相对应的水蒸汽的焓的总和。
空气的焓值计算公式为:()χ1.88t 24901.01t I ++= 或()χχ2490t 1.881.01I ++=式中;I —空气(含湿)的焓,绝干空气kg/kg ;χ—空气的干基含湿量,绝干空气kg/kg ;1.01—干空气的平均定压比热,K ⋅kJ/kg ; 1.88—水蒸汽的定压比热,K ⋅kJ/kg ; 2490—0C 水的汽化潜热,kJ/kg 。
由上式可以看出,()t 1.881.01χ+是随温度变化的热量即显热。
而χ2490则是0C 时kg χ水的汽化潜热。
它是随含湿量而变化的,与温度无关,即“潜热”。
转炉物料平衡与热平衡计算.
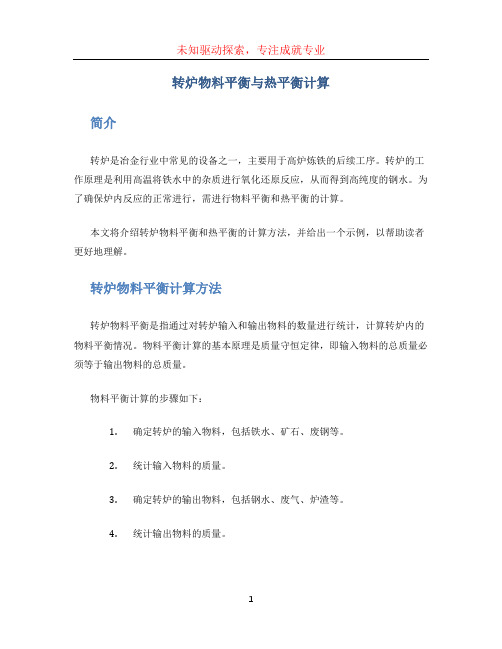
转炉物料平衡与热平衡计算简介转炉是冶金行业中常见的设备之一,主要用于高炉炼铁的后续工序。
转炉的工作原理是利用高温将铁水中的杂质进行氧化还原反应,从而得到高纯度的钢水。
为了确保炉内反应的正常进行,需进行物料平衡和热平衡的计算。
本文将介绍转炉物料平衡和热平衡的计算方法,并给出一个示例,以帮助读者更好地理解。
转炉物料平衡计算方法转炉物料平衡是指通过对转炉输入和输出物料的数量进行统计,计算转炉内的物料平衡情况。
物料平衡计算的基本原理是质量守恒定律,即输入物料的总质量必须等于输出物料的总质量。
物料平衡计算的步骤如下:1.确定转炉的输入物料,包括铁水、矿石、废钢等。
2.统计输入物料的质量。
3.确定转炉的输出物料,包括钢水、废气、炉渣等。
4.统计输出物料的质量。
5.比较输入物料的总质量和输出物料的总质量,若两者相等,则物料平衡成立;若不相等,则存在物料的损失或增加。
下面以一个具体的例子来说明转炉物料平衡的计算过程。
假设一个转炉的输入物料包括1000kg的铁水、200kg的矿石和100kg的废钢。
经过转炉反应后,得到800kg的钢水、400kg的废气和100kg的炉渣。
通过统计计算,我们可以得到输入物料的总质量为1000kg + 200kg + 100kg = 1300kg,输出物料的总质量为800kg + 400kg + 100kg = 1300kg。
两者相等,说明物料平衡成立。
转炉热平衡计算方法转炉热平衡是指通过对转炉内的能量输入和输出进行统计,计算转炉的热平衡情况。
热平衡计算的基本原理是能量守恒定律,即输入能量的总量必须等于输出能量的总量。
热平衡计算的步骤如下:1.确定转炉的输入能量,包括燃料的热值、还原剂的热值等。
2.统计输入能量的总量。
3.确定转炉的输出能量,包括钢水的热值、废气的热值等。
4.统计输出能量的总量。
5.比较输入能量的总量和输出能量的总量,若两者相等,则热平衡成立;若不相等,则存在能量的损失或增加。
- 1、下载文档前请自行甄别文档内容的完整性,平台不提供额外的编辑、内容补充、找答案等附加服务。
- 2、"仅部分预览"的文档,不可在线预览部分如存在完整性等问题,可反馈申请退款(可完整预览的文档不适用该条件!)。
- 3、如文档侵犯您的权益,请联系客服反馈,我们会尽快为您处理(人工客服工作时间:9:00-18:30)。
文档来源为:从网络收集整理.word版本可编辑.欢迎下载支持.钢铁冶金专业设计资料(炼铁、炼钢)本钢工学院冶化教研室二00三年八月第一章物料平衡与热平衡计算物料平衡和热平衡计算是氧气顶吹转炉冶炼工艺设计的一项基本的计算,它是建立在物质和能量不灭定律的基础上的。
它以转炉作为考察对象,根据装入转炉内或参与炼钢过程的全部物料数据和炼钢过程的全部产物数据,如图1-1-1所示的收入项数据和支出项数据,来进行物料的重量和热平衡计算。
通过计算,可以定量地掌握冶炼工重要参数,做到“胸中有数”。
对指导生产和分析研究改进冶炼工艺,设计转炉炼钢车间等均有其重要意义。
由于转炉炼钢过程是一个十分复杂的物理化学过程,很显然,要求进行精确的计算较为困难,特别是热平衡,只能是近似计算,但它仍然有十分重要的指导意义。
物料平衡和热平衡计算,一般可分为两面种方案。
第一种方案是为了设计转炉及其氧枪设备以及相应的转炉炼钢车间而进行的计算,通常侧重于理论计算,特别是新设计转炉而无实际炉型可以参考的情况下;另一种方案是为了校核和改善已投产的转炉冶炼工艺参数及其设备参数或者采用新工艺新技术等,而由实测数据进行的计算,后者侧重于实测。
本计算是采用第一种方案。
目前,我国顶吹转炉所采用的生铁基本上为低磷的(0.10〜0.40%)和中磷的(0.40〜1.00%)两种,对这两种不同含磷量生铁的冶炼工艺制度也不相同。
因此,下面以50吨转炉为例,分别就低磷生铁和高磷生铁两种情况,进行物料平衡和热平衡计算。
1.1原始数据表 1-1-1表1-1-2原材料成分表2-1-1铁水成分与温度转炉冶炼钢种常为普通碳素钢和低合金钢,在此以要求冶炼BD3钢考虑,其成分见表2-1-31-1-4用废钢作冷却剂,其成份与冶炼钢种成份的中限相同。
(见表1-1-3)虽然炉内化学反应,实际上是在炉料温度和炉内上部气相温度之间的任一温度发生的,但反应热效应通常仍采用25 C作为参考温度,值得指出的是,反应热还与组分在铁水中存在形态有关,至今对参与化学反应有关的实际组成物还有不同的看法。
但是,比较常用的反应热数据见表1-1-5。
表1-1-5*通常近似认为是Fe+- O2=FeO21.1.7其它数据的选取(根据国内同类转炉的实测数据选取)1. 渣中铁珠量为渣量的5%-8%本设计取8%2. 金属中碳的氧化假定为:80%-90%勺碳氧化成CO, 20%-10%的碳氧化成CO2。
3. 喷溅铁损为铁水量的0.7%〜1.0%,本设计取1.0%。
4 .取炉气平均温度1450C,炉气中自由氧含量为 0.5%,烟尘量铁珠量的 1.6%,其中 FeO=77% F Q O3=20%5. 氧气成分为 98.5%02,1.5%N2。
6. 炉衬侵蚀量为铁水量的0.5%。
1.2物料平衡计算根据铁水成份,渣料质量以及冶炼钢种,采用单渣不留渣操作,通常首先以100公斤铁水为计算基础,然后再折算成100公斤金属料。
炉渣来自金属中元素的氧化产物,渣料以及炉衬侵蚀等。
1. 铁水中各元素氧化量(见表2-2-1)表1-2-1终点钢水成份是根据同类转炉冶炼钢种的实际数据选取,其中:[C]:应根据冶炼钢种含碳量的中限和预估计的脱氧剂的增碳量(0.2~0.3)之差来确定终点钢水含碳量,取 0.150%。
[Si]:在碱性转炉炼钢法中,铁水中的硅几乎全部被氧化,随同加入的其它材料带入的SiO2一起进入炉渣中,故终点钢水硅的含量为痕迹。
[Mn]:终点钢水残锰量,一般为铁水中锰含量的 30%-40%取30%[P]:采用低磷铁水操作,铁水中磷约 85〜95%进入炉渣,在此取铁水中磷的 90%进入炉渣, 10%留在钢中。
同时要考虑钢包中回磷的因素[S]:氧气转炉内去硫率不高,一般在 30〜50%勺范围,取40%2.各元素氧化量、耗氧量及其氧化产物量见表 1-2-2 。
表 1-2-2C C Si Mn PSS Fe Fe4.100 x 90%=3 3.690 x 兰=4.92012.690 0.410 x 弩=1.093124.100 x 10%=0 0.850 x =0.971[C]+ 281 410 0.406 x 兰=0.1182{O 2}={CO} 550 0.135 x 聖=0.174[C]+{O 2}={CO2} 62850 0.005 x =0.005[Si]+{O 2}=(SiO 2) 32[Mn ]+ 0. 0.010 x(-兰)=-032」{O 2}=(MnO)406 .0052 0 1.056 x 兰=2[P]+ 56|{O 2}=(P 2O5)135 0.3022 0.015 x 1 = 0.575 x 48=[S]+{O 2}={SO 2} 3 1120.005 0.204[S]+(CaO)=(CaS)+[O]0.015-0.005=[Fe]+{O 2}=(FeO) 0.012[Fe]+{O 2}=(Fe 2 1. 9O3) 0563.690 x 28=8.61120.410 x 44=1.501230.850 x 60=281.8210.406 x 71=550.5240.135 x 142=620.3090.005 x 64=320.0100.010 x 72=320.023 *假定气化硫率占总去硫率的一1。
-0.0053表示还原出的氧量,消耗CaO量为0.010 x 56=0.01832见表2-2-8见表2-2-8*指生成的CaS量0.001 X 72= 0.002 公斤,消耗 CaO 量为 0.001 X 56 3232 0.001 X I 6= 0.001 公斤3 •造渣剂成分及数量50吨氧气转炉加入造渣剂数量,是根据国内同类转炉有关数据选取: 1)矿石加入量及成分322)萤石加入量及成分萤石加入量为0.50公斤/ 100公斤铁水,其成分及重量见表2-2-4表 1-2-4* P 以2[P]+ - {O 2}= ( P 2O 5 )的形式进行反应,其中生成P 2O 5量为矿石加入量为1.00公斤/ 100公斤铁水,其成分及重量见表1-2-3表 1-2-3* S 以]S]+ (CaO )= (CaO )+ [O]的形式反应,其中生成 CaS 量为 =0.002公斤,生成微量氧2142 800.003 X =0.007公斤,消耗氧量为0.003 X =0.004公斤。
62 62** S微量,忽略之。
3)炉衬侵蚀量为0.50公斤/100公斤铁水,其成分及重量见表1-2-5被浸蚀的炉衬中碳的氧化,同金属中碳的氧化成 CO, CO2的比例相同,即: ■ 28 :0.053公斤C 1CO 0.025 X 90%X =12___ 44=0.009公斤C CO2 0.025 X 10%X =1216其消耗氧气量为:0.053 X =0.030公斤0.009 X生=0.007公斤28 44共消耗氧气量为0.03+0.007=0.037 公斤4)生白云石加入量及成份为了提高转炉炉衬寿命,在加入石灰造渣的同时,添加一部分白云作造渣剂,其目的是提高炉渣中MgO的含量。
初期渣中(MgO)含量增高,使炉渣的熔点和粘度明显降低,减缓或阻碍石灰颗粒表面的硅酸二钙层(2CaO・ SiO2)的形成,从而加速石灰的熔解。
同时,能减少初期渣中的(FeO)含量或者中和一部分氧化铁,因此降低了炉渣的有效氧化能力。
这样就使得焦油白云石炉衬中碳的氧化作用减慢,有利于提高炉衬浸蚀能力。
另外,提高炉渣中的(MgO)含量,降低了炉渣对炉衬的浸蚀能力,在吹炼后期随着炉渣碱度的提高,其粘度相应提高,使石灰加入量严囂O )有效®RX (SiO 2) (CaO)%CaO 石灰 RX%SiO 2石灰得炉壁容易挂渣,从而保护避免受浸蚀,也有利于提高炉衬寿命。
生产实践表明, 渣中(MgO )含量为6〜8%时,其效果较好。
为此,必须保证渣中(MgO )含量 在6〜8%之间来计算白云石加入量。
经试算后取生白云石加入量为 2.0〜3.0 / 100 公斤铁水,本设计取3.0,其成份及重量见表1-2-6表 1-2-6烧减是指生白云石(MgCO 3 • CaCO 3)分解后而生产的CO 2气体。
5)炉渣碱度和石灰加入量(%CaO )取终渣碱度R==2.8〜4.0 取3.5(%SiO 2)首先计算由上述造渣剂以及铁水中各元素氧化产物而进入炉渣中的 SiO 2和CaO 的重量,然后再计算石灰加入量。
渣中已存在的刀(SiO 2)量=铁水中Si 氧化生成的SiO 2量+炉衬带入的SiO 2量+ 矿石带入的SiO 2量+萤石带入的SiO 2量+白云石带入的SiO 2量 =1.821+0.010+0.056+0.030+0.014=1.931 公斤。
渣中已存在的刀(CaO )量=白云石带入的CaO 量+炉衬带入的CaO 量+矿石带 入的CaO 量-铁水中S 成渣消耗的 CaO 量-矿石中S 成渣消耗的 CaO 量=0.925+0.27+0.010-0.018-0.002=1.185 公斤。
3.5X1.931 1.185 门厂八匕 = =6.537 公斤91.08% 3.5X1.66%加入石灰所代入的各成份及重量见表 1-2-7。
720.004 x 72=0.009,生成氧量为320.004 X 32 =0.002公斤;消耗(CaO )量为0.004 X 56=0.007 公斤* S 以[S]+ ( CaO ) = ( CaS ) +[O]的形式反应,其中生成( CaS )量为32烧减是指未烧透的CaCO 3经受热分解所产生的CO 2气体量。
6) 终点氧化铁的确定终渣中氧化铁的含量与钢水的终点含碳量和终渣的碱度有关,根据生产实践 数据,终点钢水含碳量为0.15%和终渣碱度为3.5时,终渣中(Fe 2O 3)= 5%和(FeQ =10%。
7) 终渣量及其成份表1-2-8中不计(FeO )和(Fe 2O 3)在内的炉渣重量为: (CaO+MgO+SiO 2+P 2O 5+MnO+AI 2O 3+CaF 2+CaS ) =7.152+0.904+2.039+0.316+0.524+0.127+0.445+0.034 =11.541 公斤已知渣中氧化铁量为15%则渣中其它成份之和为100%- 15%=85%11 541故炉渣总重量为 一=13.578公斤由此可知:85%(FeO )的重量=13.578 X 10%=1.358公斤,其中铁重=1.358 X 56=1.056 公斤72112(Fe 2O 3)的重量=13.578 X 5%=0.679公斤,其中铁重量=0.679 X =0.474 公斤160将(FeO )和(Fe 2O 3)的值分别填入表2-3-2中。