汽车设计中的多目标优化过程研究
汽车动力总成的模糊多目标优化

4
技 术纵横
轻 型汽 车技 术
20 ( 总 19 0 6 3) 9
汽车动力总成的模糊多 目标优化
张 斌 翁建 生 汪 洋
( 南京航空航天大学车辆工程系 )
摘
要
在研究发动机动力总成时, 考虑 系统参数的稳健 区间, 结合能量解耦 , 系统固有频率
维普资讯
2 0 ( 总 19 轻 型 汽车技 术 0 6 3) 9
技 术纵横
●’
5
有隔振效果 , 以固有频率上限为 1H , 所 8 z又为了避 免悬置系统太软而造成位移过大 ,固有频率下限设
f1)mn (1 i( :
=
P 一i ) 刀x
2 k
般是通过橡胶悬置连接在车架上的,因此必须对
橡胶悬置系统进行合理的设计来控制发动机干扰力 对整车的影响。现行的设计方法主要是通过系统各
阶模态能量解耦 , 悬置处动反力 、 力矩最小 , 系统 固
有频率的合理配置为指标 。在实现优化的时候一般
B(, : L : — Jn 10 i ) ( k k. 0 %  ̄ r
1
( 2) 1
定为 5 H 。本文把频率固定在一定的范围, . z 5 在优化 程序 中为作 为约束处理。
23动 反力 、 . 力矩 最小 :
1
f1)mi( X -l ) (2= n i Y
=1
( 3 1)
动力总成系统 工作状态下受追振动微分方程 ,
可 以表示成如下 的形式 :
f 0 4 入t2 s £ b i20t } O mr oc 2 9 n o 0 s 9 00
来:
所以, 系统质心处的振动响应为
《多目标优化的若干问题研究》范文
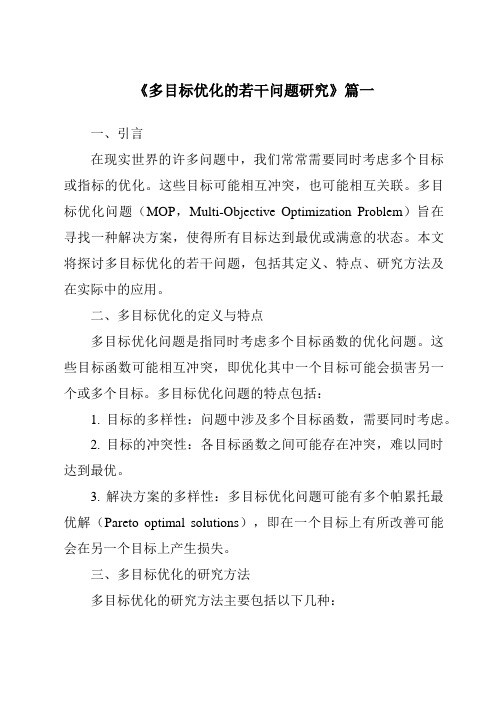
《多目标优化的若干问题研究》篇一一、引言在现实世界的许多问题中,我们常常需要同时考虑多个目标或指标的优化。
这些目标可能相互冲突,也可能相互关联。
多目标优化问题(MOP,Multi-Objective Optimization Problem)旨在寻找一种解决方案,使得所有目标达到最优或满意的状态。
本文将探讨多目标优化的若干问题,包括其定义、特点、研究方法及在实际中的应用。
二、多目标优化的定义与特点多目标优化问题是指同时考虑多个目标函数的优化问题。
这些目标函数可能相互冲突,即优化其中一个目标可能会损害另一个或多个目标。
多目标优化问题的特点包括:1. 目标的多样性:问题中涉及多个目标函数,需要同时考虑。
2. 目标的冲突性:各目标函数之间可能存在冲突,难以同时达到最优。
3. 解决方案的多样性:多目标优化问题可能有多个帕累托最优解(Pareto optimal solutions),即在一个目标上有所改善可能会在另一个目标上产生损失。
三、多目标优化的研究方法多目标优化的研究方法主要包括以下几种:1. 线性加权法:通过给各个目标函数赋予不同的权重,将多目标优化问题转化为单目标优化问题。
2. 约束法:将部分目标转化为约束条件,只对剩余的目标进行优化。
3. 交互式决策法:通过与决策者进行交互,逐步调整各目标的权重和约束条件,以获得满意的解决方案。
4. 进化算法:利用进化算法(如遗传算法、粒子群算法等)在搜索空间中寻找帕累托最优解。
四、多目标优化的应用多目标优化在实际应用中具有广泛的应用领域,如工程设计、经济管理、生物医学等。
以下以工程设计为例,介绍多目标优化的应用:在机械设计中,我们可能需要同时考虑零件的重量、强度、成本等多个因素。
这些因素可以转化为多个目标函数,通过多目标优化方法寻找满足所有目标的最佳设计方案。
例如,在汽车制造中,可以通过多目标优化方法降低汽车重量、提高燃油效率、减少制造成本等。
五、多目标优化的挑战与展望尽管多目标优化在许多领域取得了显著的成果,但仍面临一些挑战和问题。
车辆动力系统的多目标优化与设计

车辆动力系统的多目标优化与设计关键信息项:1、车辆动力系统优化与设计的目标和要求性能提升指标:____________________________节能减排目标:____________________________成本控制范围:____________________________2、优化与设计的范围和内容发动机类型与技术:____________________________传动系统配置:____________________________能源管理策略:____________________________3、时间节点和交付成果初步方案提交时间:____________________________测试与验证阶段完成时间:____________________________最终优化设计成果交付时间:____________________________ 4、费用及支付方式总费用预算:____________________________阶段性付款比例:____________________________支付条件和时间:____________________________5、质量保证与售后服务质量保证期限:____________________________售后服务内容和响应时间:____________________________1、引言本协议旨在明确双方在车辆动力系统的多目标优化与设计项目中的权利、义务和责任,确保项目的顺利进行和达成预期目标。
11 背景随着汽车行业的快速发展和市场需求的不断变化,车辆动力系统的优化与设计成为提高车辆性能、降低能耗和排放的关键。
为了满足市场竞争和法规要求,需要对车辆动力系统进行多目标的优化和创新设计。
2、项目目标和要求21 性能提升指标车辆的加速性能、最高车速、爬坡能力等方面应达到或超过特定的标准和要求。
211 具体的加速时间指标:从 0 到 100 公里/小时的加速时间应不超过 X 秒。
汽车车架结构多目标拓扑优化方法研究

=λ0
+
s
(
i
f
∑= 1λi
wi - λ0
)
-1
式中 ,Λ(ρ) 为平均频率 ;λi 为第 i 阶特征频率 ;λ0 、s 为给定
的参数 ,用来调整目标函数 ; w i 为第 i 阶频率的权重系
数 ; f 为需要优化的低阶频率的阶次 。
平均频率公式定义了一个光滑的目标函数 。
在优化过程中 , 当平均频率公式中的几个低阶模
E(ρ) = ρp E 0 < ρmin ≤ρ ≤1 式中 , E 为弹性模量 ; p 为惩罚因子 , p > 1 ;ρmin 为材料为 空的最小密度值 ;ρ为材料密度 。
SIM P 法的缺点是 : 虽然能有效地压缩中间 密度 ,但是依然存在棋盘格现象和数值不稳定性 现象 ,而且最终得到的拓扑结构不仅与惩罚因子 p 有关 , 还与初始有限元网格有关 (即网格依赖 性) 。该缺点可以通过与其他方法结合使用来克 服 , 如周长约束法 (perimeter co nt rol) 、密度斜率 法 (densit y slope) 、下 限 约 束 方 法 (minimum member size co nt rol) 等 。
基于应力优化的大客车结构多目标优化

主题 词 : 车 客
全 承载式
有 限元
结构 优化
中图分 类号 :4 2 文 献标识码 : 文章 编号 :00 30 (000 —0 4 0 U 6. 2 A 10" 73 2 1 )4 00— 4
Mut o jcieOpi z t no u tu tr ae n l- bet t ai nB sSr cu eb sdo i v mi o
和 2 9 48 3个焊点
刚度满 足设计 要求但 应力 较大 、 度储备 不足 , 动 强 振
模 态频率 与车身 骨架 质量可 进一步 优化 .因此有 必 要 对其结 构进行 优化设 计 为此 .采用优 化结构 最
s o h tt e si n s ft e i i a e in mo e ft e b s me t d s n r q i me t,b tt e sr s s v r ih a d h wst a h tf e s o h n t ld sg d lo h u es e i e u r f i g e n s u h te s i e y h g n te s e gh r s re i rl t ey p o , h r fr ,te o t z t n me h d w ih o t z st e ma i m t s fsr c ue h t n t e e v s eai l o r t e eo e h p i ai t o h c p i e h xmu sr so tu t r r v mi o mi e i a o td s d p e .Af rt e o t l d sg ft o s g s t e ma i m t cu a te s i sg i c n l e u e .te f t o d r t h p i e i n o w t e . h xmu s t r lsr s s in f a t r d c d h r — r e e ma a u r i y i s trin l f q e c s i r v d h ih f b d r me i e u e ,a d t e sr c u a e in o h u s o so a r u n y i mp o e ,t e weg t o o y f e a s d c d n h t t r l d sg f t e b s i r u mo e r
基于多目标优化的汽车底盘车架设计
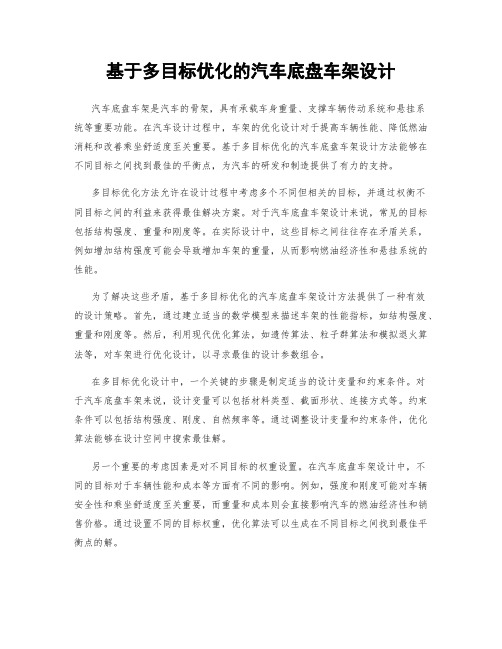
基于多目标优化的汽车底盘车架设计汽车底盘车架是汽车的骨架,具有承载车身重量、支撑车辆传动系统和悬挂系统等重要功能。
在汽车设计过程中,车架的优化设计对于提高车辆性能、降低燃油消耗和改善乘坐舒适度至关重要。
基于多目标优化的汽车底盘车架设计方法能够在不同目标之间找到最佳的平衡点,为汽车的研发和制造提供了有力的支持。
多目标优化方法允许在设计过程中考虑多个不同但相关的目标,并通过权衡不同目标之间的利益来获得最佳解决方案。
对于汽车底盘车架设计来说,常见的目标包括结构强度、重量和刚度等。
在实际设计中,这些目标之间往往存在矛盾关系,例如增加结构强度可能会导致增加车架的重量,从而影响燃油经济性和悬挂系统的性能。
为了解决这些矛盾,基于多目标优化的汽车底盘车架设计方法提供了一种有效的设计策略。
首先,通过建立适当的数学模型来描述车架的性能指标,如结构强度、重量和刚度等。
然后,利用现代优化算法,如遗传算法、粒子群算法和模拟退火算法等,对车架进行优化设计,以寻求最佳的设计参数组合。
在多目标优化设计中,一个关键的步骤是制定适当的设计变量和约束条件。
对于汽车底盘车架来说,设计变量可以包括材料类型、截面形状、连接方式等。
约束条件可以包括结构强度、刚度、自然频率等。
通过调整设计变量和约束条件,优化算法能够在设计空间中搜索最佳解。
另一个重要的考虑因素是对不同目标的权重设置。
在汽车底盘车架设计中,不同的目标对于车辆性能和成本等方面有不同的影响。
例如,强度和刚度可能对车辆安全性和乘坐舒适度至关重要,而重量和成本则会直接影响汽车的燃油经济性和销售价格。
通过设置不同的目标权重,优化算法可以生成在不同目标之间找到最佳平衡点的解。
多目标优化的汽车底盘车架设计方法具有许多优点。
首先,它可以提供多种解决方案,使设计师能够在不同的设计空间中选择最佳方案。
其次,它可以显著提高车辆性能和综合效益。
通过优化设计,可以提高车架的结构强度和刚度,减轻车身重量,降低燃油消耗,提高行驶稳定性和乘坐舒适度。
多目标优化方法在汽车前悬架设计中的应用

LI U Ya—k u n, ZHANG J i n—r ai n
( La n z h o u J i a o t o n g Un i v e r s i t y S c h o o l o f Me c h a t r o n i c En g i n e e r i n g, La n z h o u 7 3 0 0 7 0, Ch i n a )
多 目标优化方法在 汽车前悬架设 计中的应 用
刘亚 坤 , 张金敏 ( 兰 州交通 大 学机 电工程 学院 , 甘 肃 兰州 7 3 0 0 7 0 )
Mu l t i p l e Ta r ge t Op t i mi z a t i o n Me t ho d f o r a n Aut o mo bi l e Fr o n t S us p e n s i o n Sy s t e m De s i g n
1 ADAMS模 型 的 建 立及 仿 真
1 . 1 悬 架 数 学 模 型 的 建 立
a n a l y z e d t o d e t e r mi n e t h e o p t i mi z a t i o n o b j e c t i v e s .
中图分 类号 : TH1 2 2 ; U4 6 3 .3 3
文献 标识 码 : A
优化 设计 。用 虚 拟 样 机 平 台对 轿 车 前 悬 架 进 行 优
车体结构多目标拓扑优化设计探讨
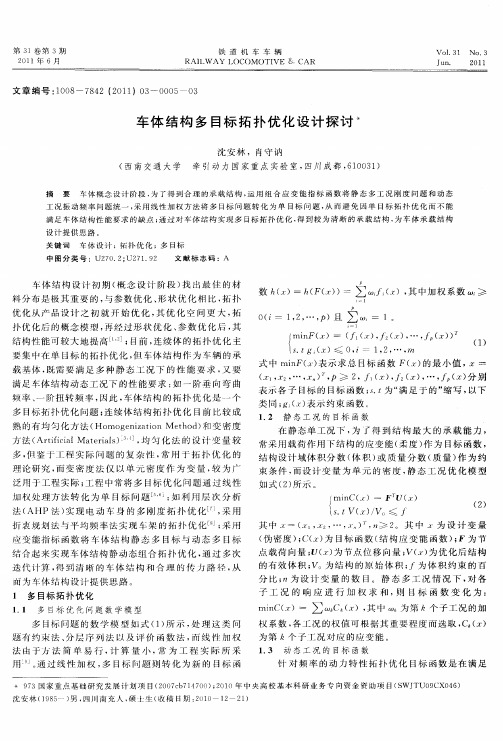
结 构性能 可较 大地提 高u ] 目前 , ; 连续 体 的拓 扑优 化 主
要 集 中在 单 日标 的拓 扑 优 化 , 车体 结 构 作 为 车 辆 的 承 但 载 基 体 , 需 要 满 足 多 种 静 态 工 况 下 的 性 能 要 求 , 要 既 又 满 足 车 体 结 构 动 态 工 况 下 的 性 能 要 求 : 一 阶 垂 向 弯 曲 如
位, 即有 相 同的数量 级 , 车体 结构 应 变 能与 频 率之 间 但 的数 量级 之 间存 在 较 大差 异 _ 如 果 不 引用 一 个值 来 】 ,
平 衡两 者之问 的差异 , 计算 结果将 受数量 级高 的 目标 则 所支 配 , 一般 来说 , 结构 的应变 能 数量 级在 1 0 0 ~ . ×1 t0 0 . ×1 之 问 , 结 果 特 征 值 倒 数 的 数 量 级 为 1 0× 而 .
而为 车 体 结 构 没 汁 提 供 思 路 。
1 多 目标 拓 扑 优 化 1 1 多 目标 优 化 问题 数 学模 型 .
点 载 荷 向 量 ; ( 为 节 点 位 移 向 量 ; ) 优 化 后 结 构 【 ) , V( 为 的有 效 体 积 ; 。为 结 构 的 原 始 体 积 ; 为 体 积 约 束 的 百 V f
图 2 车体 拓 扑 优 化
设 计 域 有 限 元 模 型
设 计 域 有 限 元模 型 ( 部 ) 局
∑
( 4 )
【.V( / s t z) 。≤ 厂
其 中 : 一( 1z , , ,≥ 2 w 为第 J阶特征值 倒 z z ,2 … - ) z ,j 数 的加权 系数 。 14 静 动态工 况 总 目标 函数 . 采用权 系数方 法 , 目标 函数 间必须有 相 同的度量单
- 1、下载文档前请自行甄别文档内容的完整性,平台不提供额外的编辑、内容补充、找答案等附加服务。
- 2、"仅部分预览"的文档,不可在线预览部分如存在完整性等问题,可反馈申请退款(可完整预览的文档不适用该条件!)。
- 3、如文档侵犯您的权益,请联系客服反馈,我们会尽快为您处理(人工客服工作时间:9:00-18:30)。
图 4 高精度近似模型的误差分析结果
Convergence of Percent Contributions 25%
图 5 低精度近似模型的误差分析结果
Conve rge nce of Pe rce nt Contributions 25% Sub_Frame-1 * Rear_rails_rear_end
Predicted vs Actual Output Variable = "Mass"
2.39E+03
Predicted vs Actual Output Variable = "R MD B _C radle4B arC rush_lhs"
5.50E+01
2.38E+03
4.78E+01
Predicted
5 10 4
图 2 发动机舱盖变量贡献量 3 近似模型
图 3 100%正撞有效加速度主效应图
在整车分析中,对于一些计算时间较短并且变量形式单一的优化设计问题,比如白车身刚度的 板厚优化,可以直接用分析软件进行优化循环而不需建立近似模型。但计算时间较长的多目标优化 问题,需要借助近似模型来完成优化设计工作。最新的 Isight4.5 软件提供了多项式近似模型、径向 基函数神经网络和克里格插值模型三种近似模型,三种模型都可以用来进行设计空间的模拟。在建 立好近似模型之后必须验证模型的精度。验证模型精度通常有三种方法,包括误差分析、随机采样 点计算对比和贡献量收敛性分析。图 4-图 7 分别列出了两个汽车子系统优化过程中的近似模型的 误差分析结果和贡献量收敛性分析结果,从图中可以看出,精度高的模型误差分布接近 45 度对角 线,贡献量收敛性曲线后半部分相对较平稳,反之精度差的模型样本点误差分散,贡献量曲线波动 也较大。提高近似模型精度的方法主要有两种,一是在误差较大的区域附近增加 DOE 样本点,二 是选择精度更高的近似模型。
(Case1)
(Case2)
表 2 不同优化目标配置下的优化结果对比
速度为 0 时间(ms) 动态压溃(mm) 有效压溃(mm) 有效加速度(g’s) 效率(%) Case1 Case2 82.6 80.9 700 651 903 787 19.7 19.3 96.00 100.57
质量(kg) 1.48 3.91
优化循环
通过优化算法进行新方案与当前最佳方案的对比 目标间的权衡分析 基于权衡分析结果获得备选设计方案 通过计算确认备选方案 图 1 优化设计流程
优化循环
2. 试验设计 2.1 定义设计目标 在进行优化设计之前必须明确设计目标,通常情况下在一个大的优化任务中会有多个优化设计 方向的组合。整车开发中最常见的设计目标是性能和重量。为使得这两个目标达到最佳水平,在优 化设计过程中通常的做法是分两步,首先是通过优化使性能达标,第二步是研究设计余量,在满足 性能的条件下减重。 2.2 定义设计变量和区间 从数学角度看,汽车设计中的变量分连续变量和离散变量两种。其中连续变量通常是各结构参 数的位置、角度等;离散变量主要包括零件的材料、厚度等。基于试验设计的绝大多数变量水平通 常不超过 20。 对于一个新的优化设计过程, 首先应基于工程师对优化任务的理解和设计经验以及设 计可行性对需要优化的变量进行初步的筛选。这样做的目的一是理清设计思路,二是减少试验样本 个数,从而缩短试验设计的计算时间。表 1 所示为某仪表盘骨架系统优化设计变量,通过筛选,将 最初定义的 18 个变量精简为 15 个设计变量。如果采用正交试验,DOE 样本数量可以减少 20 个以 上。
引言
在整车开发过程中,无论是前期架构还是在子系统开发中,应用优化设计来提高开发质量和缩 短开发周期都是必不可少的一个环节。但面对复杂的优化设计过程,如何合理的定义多目标优化设 计问题,之后又如何通过合理的手段完成优化设计并给出工程指导方向,是每个工程师非常关心的 话题。本文就此作了一些总结性的研究,并结合部分实际案例提出了一些在优化设计过程中需要注 意的事项以及应用 Isight 软件进行优化设计的一些经验。旨在对汽车优化设计工作有一定的参考价 值。 1. 优化设计流程简介 对于一个完整的优化设计过程,可以用图 1 所示流程图的形式来简单描述。图中左半部分适用 于解决单次计算耗时较长的优化问题,比如被动安全性问题和空气动力学问题等;右半部分适用于 单次计算耗时较短的问题,比如子系统结构刚度和模态优化问题等。单次计算时间主要取决于工程 师面对的计算机软硬件条件。其主要区别在于左半部分问题需要借助试验设计和近似模型,而右半 部分可以直接采用优化算法进行解决。随着计算机水平的发展,能够直接进行优化计算的问题将越 来越多。
Predicted
2.37E+03
4.05E+01
2.36E+03
3.33E+01
2.35E+03 2.35E+03
2.36E+03
2.37E+03 Actual
2.38E+03
2.39E+03
2.60E+01 2.60E+01
3.33E+01
4.05E+01 Actua l
4.78E+01
5.50E+01
5%
0% 0 50 Number Runs Used 100
0% 0 50 N u m b e r R u n s U se d 100 Fore_A ft
4.
图 6 高精度近似模型贡献量变化结果 建立优化问题
图 5 低精度近似模型贡献量变化结果
优化问题必须建立在合适的目标和约束条件下才能获得最佳的设计结果。如果目标和约束条件 不合适甚至可能会对工程更改方向产生误导。在早期对优化设计任务不清晰的情况下,需要对比不 同的约束条件和目标配置下获得的优化结果,从中选择最适合工程需求的方案。常用的多目标优化 算法有遗传算法和模拟退火算法等。在近似模型上的优化相当于在一系列数学方程式之间寻求最优 解,不需要借助求解器软件计算,同时这种优化设计可以在短时间内进行多次优化迭代,并且寻找 全局最优解,因此可以迅速的找到最佳设计方案。对于可以直接使用有限元求解器进行优化计算的 问题,虽然单个工况计算耗时较短,但直接优化需要进行多次的优化循环,执行一个优化过程同样 需要耗费相当长的时间,因此选择一个恰当的目标和约束条件将显得更加重要。表 2 对比了某车型 100%正撞工况采用不同优化目标配置获得的结果。 其中配置 1 和配置 2 的约束条件相同, 但配置 1 的目标是包括质量在内的所有设计指标极值化,配置 2 定义的是将质量差值最小化,两种方案同时 采用模拟退火算法,获得的优化结果如表 2 所示。
表 1 仪表盘骨架系统优化设计变量清单
横梁左侧支架形式 横梁右侧支架形式 管柱下支架减重孔形式 H 梁 5 号板材料 左侧横梁管径 左侧横梁板厚 右侧横梁板厚 H 梁 1 号板厚度 H 梁 2 号板厚度 H 梁 5 号板厚度 地板支架板厚 管柱下支架板厚 管柱上支架板厚 Hinge pillar 支架板厚 Hinge pillar 支架板厚
Percent Contributions
Rear_rails _front _end 20% Rocker S ub_Frame-1 * Rear_rails _front _end Rocker * Rear_rails_rear_end 10% Rear_rails_rear_end Rear_rails_rear_end * Rear_rails _front _end 5% crush_can B_pillar_LHS-SHP
对于设计区间, 需要根据设计变量的实际情况, 分水平定义每个变量。 例如某车身零件的板厚, 在参考竞争车型和上一代车型的厚度之后,需要按照板厚成型要求,将其设计区间定义为 1.8,2.0, 2.2,2.4,2.5 五个离散的水平。这样既可以保证每个 DOE 样本是能够反映设计可行性的样本,同 时也将会使得后期基于近似模型获得的设计方案响应预测值更加准确。 2.3 定义试验设计矩阵 设计变量的个数和水平数决定试验设计矩阵的大小。从设计要求角度,必须在保证后期能够建 立精确近似模型的情况下,尽可能的减少计算样本数量。为了保证能够建立精确的近似模型,需要 试验设计矩阵满足任意变量个数和任意水平数的需求,但目前还没有商业软件能够满足这样的设计 需求。Isight 软件配备了很多标准试验设计方法,包括正交试验和优化的拉丁超立方试验等,但通 常情况下需要工程师根据工程要求采用自定义方式建立试验设计矩阵。以某车型发动机舱盖结构优 化为例,其设计变量有 19 个,其中 2 水平变量 5 个,4 水平变量 10 个,8 水平变量 4 个,需要工 程师定制的 DOE 矩阵则为 L64 (2 *4 *8 )。 2.4 生成设计样本和样本计算 通过 Isight 软件驱动配置文件和前处理软件,可以生成每个工况的样本文件。通常情况下一个 样本的生成需要 5 个配置文件,包括模型文件、变量参数文件、计算文件、批处理程序文件和 DOE 矩阵文件。模型文件主要包括需要参与 DOE 计算的整车或子系统结构,并可以通过计算文件的调 用进行有限元计算;变量参数文件包含了参与 DOE 计算的所有设计变量名和变量值;批处理程序 文件可以通过后台运行的方式单独进行某个样本的运算设置和计算; DOE 矩阵文件以列表的形式定 义了所有样本的变量取值。在通过并行计算获得所有样本的计算结果之后,通过 Isight 提供的开放 式 JAV A 编辑平台,借助 Loop 等组件集成 JAVA 后处理程序可以计算获得所需要的响应。 2.5 DOE 数据分析 通过 DOE 数据分析可以获得各设计参数对于设计指标的贡献量百分比, 同时还可以获得指标随 设计变量的变化趋势曲线,即主效应图。基于贡献量百分比分析可以判断对设计指标有重要影响的 设计参数,制作主效应图的目的是发掘设计目标随设计变量的变化趋势。图 2 为某车型发动机舱盖 各设计参数对某设计指标的贡献量百分比,图 3 为某车型 100%正撞加速度随白车身各设计参数变 化的主效应图。