锅炉温度控制系统设计
锅炉温度PID控制系统设计
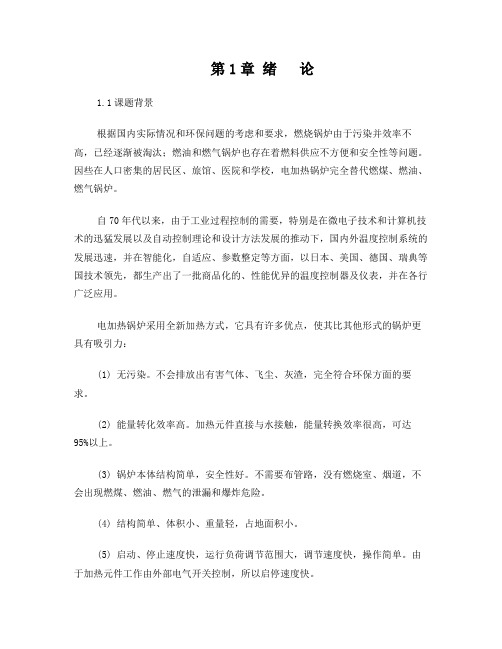
第1章绪论1.1课题背景根据国内实际情况和环保问题的考虑和要求,燃烧锅炉由于污染并效率不高,已经逐渐被淘汰;燃油和燃气锅炉也存在着燃料供应不方便和安全性等问题。
因些在人口密集的居民区、旅馆、医院和学校,电加热锅炉完全替代燃煤、燃油、燃气锅炉。
自70年代以来,由于工业过程控制的需要,特别是在微电子技术和计算机技术的迅猛发展以及自动控制理论和设计方法发展的推动下,国内外温度控制系统的发展迅速,并在智能化,自适应、参数整定等方面,以日本、美国、德国、瑞典等国技术领先,都生产出了一批商品化的、性能优异的温度控制器及仪表,并在各行广泛应用。
电加热锅炉采用全新加热方式,它具有许多优点,使其比其他形式的锅炉更具有吸引力:(1) 无污染。
不会排放出有害气体、飞尘、灰渣,完全符合环保方面的要求。
(2) 能量转化效率高。
加热元件直接与水接触,能量转换效率很高,可达95%以上。
(3) 锅炉本体结构简单,安全性好。
不需要布管路,没有燃烧室、烟道,不会出现燃煤、燃油、燃气的泄漏和爆炸危险。
(4) 结构简单、体积小、重量轻,占地面积小。
(5) 启动、停止速度快,运行负荷调节范围大,调节速度快,操作简单。
由于加热元件工作由外部电气开关控制,所以启停速度快。
(6) 可采用计算机监控,完全实现自动化。
其温度的控制都能通过微控制芯片完成,使锅炉的运行完全实现自动化,最大程度地将控制器应用于传统的锅炉行业。
本课题主要研究锅炉温度的过程控制。
新型锅炉是机电一体化的产品,可将电能直接转化成热能,具有效率高,体积小,无污染,运行安全可靠,供热稳定,自动化程度高的优点,是理想的节能环保的供暖设备。
加上目前人们的环保意识的提高,电热锅炉越来越受人们的重视,在工业生产和民用生活用水中应用越来越普及。
电热锅炉目前主要用于供暖和提供生活用水。
主要是控制水的温度,保证恒温供水。
随着计算机和信息技术的高速发展,单片机广泛的应用于工业控制中。
工业控制也越来越多的采用计算机控制,在这里我们采用51系列单片机来做控制器。
蒸汽锅炉PID温度控制系统设计

目旳:
对锅炉过热蒸汽温度控制系统进行分析和设计,而对 锅炉过热蒸汽旳良好控制是确保系统输出蒸汽温度稳 定旳前提。所以本设计采用串级控制系统,这么能够 极大地消除控制系统工作中旳多种干扰原因,使系统 能在一种较为良好旳状态下工作,同步锅炉过热器出 口蒸汽温度在允许旳范围内变化,并保护过热器管壁 温度不超出允许旳工作温度。
调整器接受过热器出口蒸汽温度t变化后,调整器才开始动作, 去控制减温水流量W ,W旳变化又要经过一段时间才干影响到 蒸汽温度t,这么既不能及早发觉扰动,又不能及时反应控制旳 效果,将使蒸汽温度t发生很大旳动态偏差,影响锅炉生产旳安 全和经济运营。
燃烧工况
温度设定值
控制信号
喷水流量
控制器
执行器
过热器
温度变送器
在本设计用到串级控制系统中,主对象为送入负荷设 备旳出口温度,副对象为减温器和过热器之间旳蒸汽 温度,经过控制减温水旳流量来实现控制过热蒸汽温 度旳目旳。
蒸汽锅炉工艺流程及控制要求
蒸汽锅炉工艺流程及控制要求
锅炉是一种具有多输入、多输出且变量之间相互关联 旳被控对象。 过热蒸汽温度控制系统:主要使过热器出口温度保持 在允许范围内,并确保管壁温度不超出工艺允许范围;
被控对象建模
根据在减温水量扰动时,过热蒸汽温度有较大旳容积迟延, 而减温器出口蒸汽温度却有明显旳导前作用,完全能够构成 以减温器出口蒸汽温度为副参数,过热蒸汽温度为主参数旳 串级控制系统
温度设定值
温度主调节器
副调节器
减温水流量
蒸汽流量或者烟
扰动
气热量扰动
阀 门
减温器 2
过热蒸汽温度
过热器 1
温度变送器 温度变送器
毕业设计18锅炉温度串级控制系统
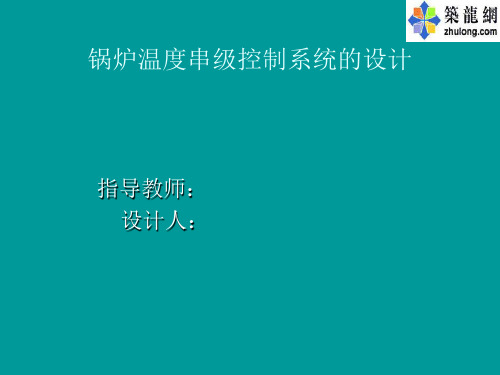
由于本次设计选用的是电阻丝加热炉,属于电加热形式, 应该选择温度控制器作为执行机构,选用对应的MJYD-JL20型单相交流模块。 PLC控制器输出的数字量经过D/A转换成温度控制器可识 别的模拟电压信号后,根据不同的电流值,MJYD-JL-20型 单相交流模块输出相应的电压值从而控制电阻丝两端的电 压值,达到调节温度的目的。
致谢
这次毕业设计是我在大学里过得最充实、 最有意义、最开心的一段经历,让我为大 学画出了一个圆满的句号。感谢老师,感 谢同学,感谢在设计过程中所有帮助过我 的人!
MADO2接线图
输出接线图
CPM1A-MAD02-CH 屏 蔽 电 缆 + V+ 电 压 输 出 电压输入 屏蔽电缆
输入接线图
CPM1A-MAD02-CH V+ 250E I+
+
I+ 电 流 输 出
_ COM 10K 0V
COM
+
V+
0V
电流输入 _ FG
I+
COM
250E
FG
10K 0V
执行器的选择
系统硬件的设计
温度检测电路单元
PLC及其配套的MAD02
执行器的选择 系统电气原理图
温度检测电路单元
JCJ100G接线示意图
PLC及其配套的MAD02
在本次设计中选用的是日本OMRON(立石)公司推出的 CPM2A型可编程控制器,型号为CPM2A-40CDR-A 。
在本次设计中,需要进行温度信号的采集,但采集过来的 信号为模拟信号,而PLC所能存储并进行处理的信号为数 字信号,因此,需要对采集到的温度信号,进行相应的模 数转换,以便实现锅炉温度的串级控制。相应地,PLC输 出的为数字信号,必须进行D/A转换形成模拟量才能实现 对执行器的控制。由于本次设计选用PLC作为控制工具, 所以应选择转换模块或与所选用PLC相配套的器件。因此 本次设计选用CPM2A—MAD02作为本设计中的A/D、D/A 转换器件。
锅炉温度定值S7--300控制系统设计 - 副本

锅炉温度定值S7-300控制系统设计摘要:锅炉温度定值S7--300 控制系统采用PLC作为控制系统的核心,使用西门子公司的S7--300 系列PLC编程软件中的PID功能块来实现控制算法,通过和计算机的通信实现数据的自动处理和操作的远程控制。
监控画面采用西门子公司的Wincc组态软件来制作,从而实现对Kp、Ti、Td三个参数的在线修改,以及实时监视被控对象的运行状态。
关键词:PID 可编程控制器组态软件1 引言锅炉的水温控制在一些场合仍然采用传统的继电器、接触器控制方式,没有控制算法,自动化程度不高,运行稳定性较差,操作维护部方便。
针对这些问题,本文采用S7--300 PLC 作为主控制单元,配合外围检测电路、执行单元、人机界面等技术,引入PID算法控制程序,设计出一种新的锅炉定值水温控制系统,以获得良好的控制效果。
在工业控制领域,基于运行稳定性考虑,大多采用PLC控制器作为控制核心。
特别是对生产过程中的各种物理量的检测和控制,PID控制仍然占据着非常重要的地位,在冶金、机械、化工等行业中获得了广泛应用。
PID算法简单、实用,容易为现场工程技术人员所掌握,它不需要求出被控系统的数学模型,通过调节比列(P)、积分(I)、微分(D)三个参数的大小就可以获得较好的控制效果。
对于比较复杂的控制系统,例如具有大惯性、纯滞后系统,可以在传统PID调节器的基础上,融入相应的智能控制算法衍生出各种实用可行的改进PID算法,因此,它具有较强的灵活性和应用性。
西门子中可编程控制器自带有两路模拟量输入和一路模拟量输出,具有较好的数值运算能力和处理模拟信号量的功能,可以设计出各种PID调节器,运用于具有连续量控制的闭环系统;还可根据被控对象的具体特点和要求来调整必要的控制参数,利用组态软件Wincc还具有监控功能,并可以在运行中调整参数。
2 锅炉温度定值控制系统结构2.1 PLC控制柜的组成(1)电源部分(2)CPU模块西门子S7--300PLC,型号为CPU315--2 DP,它集成了MPI 接口,可以很方便的在PLC站点、操作站OS、编程器PG、操作员面板建立较小规模的通讯。
锅炉过热蒸汽温度控制系统设计研究毕业设计开题报告
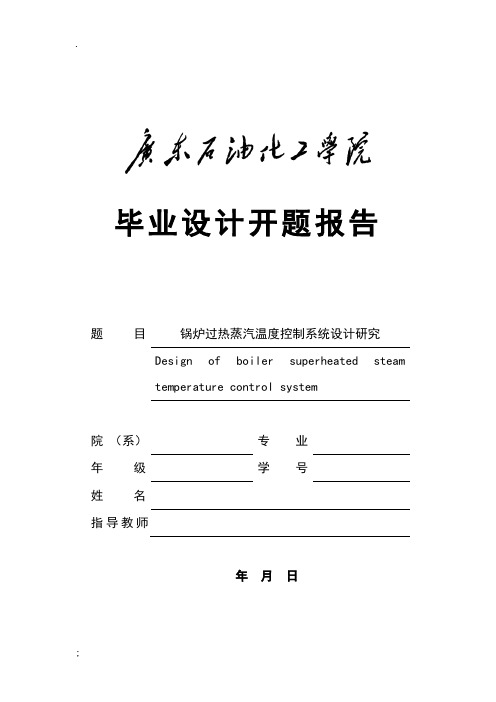
重点解决的问题
主要内容:
1、建立被控对象数学模型。
2、基于单片机设计总体方案,进行PID控制规律的选用与数字化。
3、硬件设计,包括单片机输入信号接口电路、外围电路等。
4、软件设计,包括初始化及主程序、控制程序、A/D和D/A转换程序及其他处理程序。
5利用PROTUES仿真。
重点解决的问题:
锅炉是我国工业生产和生活上应用面最广、数量最多的热力设备,是石油化工、发电等工业过程必不可少的重要动力设备,其产物蒸汽不但可以作为蒸馏、干燥、反应、加热等过程的热源,而且还可以作为驱动设备的动力源。
过热蒸汽温度控制是锅炉控制系统不可缺少的重要组成部分,其性能和可靠性已成为保证锅炉安全性和经济性的重要因素。由于锅炉往往负荷变化大,起停频繁,依靠人工操作很难保证其安全、稳定地在经济工况下长期运行。温度过高,会使蒸汽带水过多,汽水分离差,使后续的过热器管壁结垢,影响了生产安全;温度过低又将破坏部分水冷壁的水循环不能满足工艺要求,严重时会发生锅炉爆炸,从而造成重大事故。因此,工业过程对锅炉控制系统都有很高的要求,在锅炉运行中,保证过热蒸汽的温度在正常的范围内具有非常重要的意义。
完成论文的初稿;
修改、完善毕业设计并送指导老师审阅;
完成论文的PPT文件,准备毕业答辩。
指
导
教
师
意
见
***同学查阅了大量与课题相关的文献资料,对设计意图和课题意义清
楚明确,设计了初步的研究方案,预见了难点和关键问题,并拟定了工作计划,
为开题做了充分准备。目前已达到开题要求,同意开题。
指导教师签名:
年 月 日
1、了解锅炉过热蒸汽的工艺过程,对被控对象进行分析,设计控制方案。
火电厂锅炉温度控制系统设计

火电厂锅炉温度控制系统设计课程设计任务书学生姓名专业班级指导教师工作单位题目火电厂锅炉温度控制系统设计初始条件锅炉温度的控制效果直接影响着产品的质量温度低于或高于要求时要么不能达到生产质量指标有时甚至会发生生产事故采用双交叉燃烧控制以锅炉炉膛温度为主控参数燃料和空气并列为副被控变量设计火电厂锅炉温度控制系统以达到精度在℃范围内要求完成的主要任务包括课程设计工作量及其技术要求以及说明书撰写等具体要求1选择控制方案2绘制锅炉温度控制系统方案图3确定系统传感与变送器的选择数据采集系统控制电路等4说明系统工作原理时间安排1月21日选题理解课题任务要求1月22日方案设计1月2324日参数计算撰写说明书1月25日答辩指导教师签名 2008 年 1 月 9 日系主任或责任教师签名 2008 年 1 月 12 日目录1绪论 12锅炉的工艺流程及控制要求 221锅炉的工艺流程222锅炉的控制要求33锅炉炉膛温度的动态特性分析 34方案设计541炉膛温度控制的理论数学模型 542炉膛温度控制方法的选择 543 系统单元元件的选择 6com测变送器的选择 6com测变送器的选择8com副控制器正反作用的选择10com的PID调节器和副回路的PI调节器10com仪表的选择10com的选择125控制系统的工作原理 146设计心得157参考文献161绪论工程控制是工业自动化的重要分支几十年来工业过程控制获得了惊人的发展无论是在大规模的结构复杂的工业生产过程中还是在传统工业过程改造中过程控制技术对于提高产品质量以及能源的节约都起着重要的作用生产过程是指物料经过若干加工步骤而成为产品的过程该过程中通常会发生物理化学反应生化反应物质能量的转换与传递等等或者说生产过程表现为物流过变化的过程伴随物流变化的信息包括物流性质的信息和操作条件的信息生产过程的总目标应该是在可能获得的原料和能源条件下以最经济的途径将原物料加工成预期的合格产品为了打到目标必须对生产过程进行监视和控制因此过程控制的任务是在了解生产过程的工艺流程和动静态特性的基础上应用理论对系统进行分析与综合以生产过程中物流变化信息量作为被控量选用适宜的技术手段实现生产过程的控制目标生产过程总目标具体表现为生产过程的安全性稳定性和经济性1安全性在整个生产过程中确保人身和设备的安全是最重要和最基本的要求在过程控制系统中采用越限报警事故报警和连锁保护等措施来保证生产过程的安全性另外在线故障预测与诊断容错控制等可以进一步提高生产过程的安全性2稳定性指系统抑制外部干扰保持生产过程运行稳定的能力变化的工业运行环境原料成分的变化能源系统的波动等均有可能影响生产过程的稳定运行在外部干扰下过程控制系统应该使生产过程参数与状态产生的变化尽可能小以消除或者减少外部干扰可能造成的不良影响3经济性在满足以上两个基本要求的基础上低成本高效益是过程控制的另外一个重要目标为了打到这个目标不进需要对过程控制系统进行优化设计还需要管控一体化即一经济效益为目标的整体优化工业过程控制可以分为连续过程工业离散过程工业和间隙过程工业其中连续过程工业占的比重最大涉及石油化工冶金电力轻工纺织医药建材食品等工业部门连续过程工业的发展对我国国民经济意义最大过程控制主要指的就是连续过程工业的过程控制锅炉是工业生产中不可缺少的动力设备它多产生的蒸汽不仅能够为蒸馏化学反应干燥蒸发等过程提供热源而且还可以作为风机压缩机泵类驱动透平的动力源随着石油化学工业规模的不断扩大生产过程不断强化生产设备不断革新作为全厂动力和热源的锅炉亦向着大容量高参数高效率的方向发展为确保安全稳定生产对过路设备的自动控制就显得尤为重要2锅炉的工艺流程及控制要求21锅炉的工艺流程由于锅炉设备使用的燃料燃烧设备炉体形式锅炉功用和运行要求的不同锅炉有各种各样的流程常见流程如图21所示由图可知蒸汽发生系统由给水泵给水调节阀省煤器汽包及循环管组成燃料和热空气按照一定的比例进入燃烧室燃烧产生的热量传递给蒸汽发生系统产生饱和蒸汽然后经过热器形成一定汽温的过热蒸汽汇集至蒸汽母管压力为的过热蒸汽经负荷设备调节阀供给生产负荷使用与此同时燃烧过程中产生的烟气将饱和蒸汽变成过热蒸汽后经省煤器预热锅炉给水和空气预热器预热空气最后经引风机送往烟囱排入大气22锅炉的控制要求根据生产负荷的不同需要锅炉需要提供不同规格压力和温度的蒸汽同时根据安全性和经济性的要求是锅炉安全运行和完全燃烧锅炉设备的主要控制要求如下1供给蒸汽量适应负荷变化需要或者保持给定负荷2锅炉供给用汽设备的蒸汽压力应当保持在一定的范围内3 过热蒸汽温度保持在一定范围4汽包水位保持在一定范围5保持锅炉燃烧的经济性和安全性6 炉膛负压保持在一定的范围内根据上述要求锅炉设备的主要控制系统见表21表21 锅炉设备的主要控制系统控制系统被控变量操纵变量控制目的锅炉给水控制系统锅炉汽包水位给水流量锅炉内产生的蒸汽和给水的无聊平衡过路燃烧控制系统蒸汽压力烟气成分炉膛负压燃料流量送风流量引风流量蒸汽负荷的平衡燃烧的完全和经济性锅炉运行的安全性过热蒸汽控制系统过热蒸汽温度喷水流量过热蒸汽的温度和安全性3锅炉炉膛温度的动态特性分析火电厂的锅炉炉膛由于采用的燃料为煤粉在燃烧过程中炉膛和汽包之间的传热过程是一个相当复杂的过程炉膛的温度的动态特性具有一般的大滞后时变非线性和不对称性等特点在过程控制中为了方便设计同时又在一定的要求范围内我们通常把锅炉炉膛的温度的动态特性看作是一个线性的系统可以用以下传递函数描述具有时滞的一阶环节具有时滞的二阶环节在现场环境中炉膛内的温度变化是时时刻刻的很难用一个固定的数学公式将炉温的变化规律总结出来但是我们要对炉膛内的温度进行控制就必须要对炉膛内的温度变化进行一个规律的总结所以在规定的要求范围内对一些情况进行近似处理是很合理和必要的在通常情况下我们给定炉膛一个温度值作为系统的给定使锅炉炉膛在这个给定的温度状态下工作这个温度的变化又是和炉内的燃料燃烧量和炉体的总散热量相关的对于火电厂锅炉来说炉体的容量结构检测元件及其安放位置等都影响着滞后的大小它不是一个单一的问题是一个系统问题容积滞后时间就是级联的各个惯性环节的时间常数之和纯滞后产生的根源也要从整个测量系统来考虑并且与温度的高低有关热量从热源传到温度传感器要经过多个热阻与热容相串联的热惯性环节而串联的多容对象会产生等效纯时滞后随着温度的升高辐射传热的比例增大辐射具有穿透性使传热路径缩短传热速度加快所以纯滞后的时间会随温度升高而减小由于火电厂锅炉使用的燃料是煤粉即锅炉能量的来源方式是通过化学燃料的燃烧获得能量的同时炉膛内能量的散发形式又是以炉膛的炉体热量散失对汽包进行热量传导进行散失等多种途径进行的所以炉膛内的温度的变化是一个相当复杂的过程是一个非线性变化的过程从模型参数上看在锅炉炉膛的整个温度调节范围内对象的增益容积滞后时间和纯滞后时间通常是与工作温度与负载变化有关的变参数而且参数变化量与温度变化量之间是非线性关系由于锅炉炉膛内的温度是高温段的在高温段温度变化的纯滞后时间和过程增益将比低温段有显著减少而时间常数则显著增大锅炉作为一种高负荷运转的设备特别是火电厂内的锅炉长期处于高负荷运转下随着运行时间的变化其各项性能都会逐渐发生变化特别是随着使用时间的增长炉子的保温隔热材料会逐渐老化炉膛内部由于长期处于高温环境中炉体的保温密封性能变差通过炉体向外散失的热量增大此外锅炉初次使用和久停后再用时由于绝热保温材料中的水分大炉膛温度的特性差别也是很大的另外随着季节的变换锅炉运行的外部环境温度也是经常变化的冬天外部环境相对较冷炉体的散热较快夏天气温炎热炉体的散热相对会较慢如此种种因素都会引起炉膛温度特性的变化但变化的速度十分缓慢而不明显火电厂锅炉炉膛温度具有大惯性大滞后特性在炉膛的整个温度范围内对象的增益容积滞后时间纯滞后时间都是与工作温度有关的变参数从传热原理可知这些参数也与负荷变化有关在锅炉设计的工作温区在工作点附近的小范围内其动特性接近于线性较容易控制用常规的PID调节器也能控制得很好但不能经受太大的扰动也不能够大范围地跟踪变化较快的给定信号对于常规仪表大范围地改变温度要靠手动仅当温度接近给定值时方可投入自动根据以上分析可以认为火电厂锅炉炉膛温度是一种具有大容积滞后和大纯滞后的对象在整个炉膛的温区内其动态参数随锅炉的工作温度变化在工作点附近的小温度范围内炉膛的动态特性近似线性的4方案设计41炉膛温度控制的理论数学模型根据以上分析可知炉膛温度问题是比较复杂的对炉膛温度动态特性进行分段线性化则在每个较小的温度区间锅炉炉膛的燃料流量炉膛温度系统的动态特性可近似地用一个惯性环节和一个纯滞后环节串联的简化模型来表征即1其中K为过程的增益为过程的纯滞后时间To为过程的等效容积滞后时间在锅炉炉膛的整个温度范围内对象的增益容积滞后时间和纯滞后时间都是炉膛温度和负载的非线性函数K随锅炉炉膛内温度升高而减小To随锅炉炉膛内的温度升高而增大机理建模和计算机仿真分析以及实验辨识等也证明了这一模型的可行性42炉膛温度控制方法的选择双交叉燃烧控制是以锅炉炉膛温度为主被控量燃料和空气并列为副被控变量的串级控制系统其中两个并列的副环具有逻辑比值功能使该控制系统在稳定工作的情况下保证空气和燃料的最佳比值也能在动态过程中尽量维持空气燃料在最佳比值附近因此具有良好的经济效益和社会效益在煤粉流量调节回路中炉温PID的输出A1与根据实测空气流量折算成需要的煤粉流量之后分别乘以一个偏置系数K3得到信号A2乘以一个偏置系数K4得到信号A3A1A2A3三者经过高低选择器比较选中者作为煤粉流量PID的设定值空气流量调节回路中炉温PID的输出B1与根据实测煤粉流量折算成所须空气流量之后分别乘上一个偏置系数K1得到信号B2乘上偏置系数K2得到信号B3B1B2B3三者经高低选择器比较选中者乘上流量补偿系数送到空气PID作为设定值其系统组成原理图如图41所示43 系统单元元件的选择com测变送器的选择在本次设计中选用热电阻温度变送器它的量程单元的原理图如图42图42热电偶温度变送器量程单元原理图热电偶温度变送器与各种测温热电偶配合使用可将温度信号线性地转换成为4~20mADC电流信号或1~5VDC电压信号输出它是由量程单元和放大单元两部分组成的热电偶温度变送器的主要特点是采用非线性负反馈回路来实现线性变化这个特殊的性质反馈回路能按照热电偶温度-毫伏信号间的非线性关系调整反馈电压以保证输入温度t与整机输出或间的线性关系由图可见热电偶温度变送器的量程单元由信号输入回路A零点调整及冷端补偿回路B以及非线性反馈回路C等部分组成输入信号为热电偶产生的热电势输入回路中限流电阻和限压稳压管为安全火花防爆元件电阻还与电容组成低通滤波器零点调整量程调整电路的工作原理与直流毫伏变送器大致相仿所不同的是在热电偶温度变送器的输入回路中增加了由铜电阻等元件组成的热电偶冷端温度补偿电路同时把调零电位器移动到了反馈回路的支路上在反馈回路中增加了运算放大器等组成的线性化电路起线性化作用由于锅炉炉膛内的温度值较高所以选用的热电偶变送器的温度测量值必须达到要求这里我选用的是DBW-1150型热电偶温度变送器DBW-1150型热电偶温度变送器是DDZ-III系列仪表的主要品种本温度变送器用热电偶作为测温元件将被测温度线性地转换成标准信号1-5VDC或4-20mADC 输出供给指示记录凋节器计算机等自动化监控系统技术参数◆输入标准热电偶◆输出输出电流4~20mADC输出电压1~5VDC输出电阻250Ω允许负载变化范围100Ω◆量程0~1600℃◆冷端补偿误差≤1℃◆温度漂移≤01×基本误差1℃◆绝缘电阻电源输入与输出端子间≤100MΩ◆绝缘强度电源输入输山端子间1500VAC分钟◆工作条件环境温度0~50℃相对湿度≤90RH◆电源电压24VDC±5◆功耗<2W◆防爆等级 ib IICT6◆重量<2Kg com测变送器的选择由于流量变送的对象是煤粉和热空气所以在选择流量变送装置的时候必须是能够检测气体流量和和粉末混合气体的流量的另外由于空气是热空气所以还要求变送装置能够在一定的高温下工作所以这里选用的流量变送器为LUGB型涡街流量计LUGB型涡街流量计根据卡门karman涡街原理测量气体蒸汽或液体的体积流量标况的体积流量或质量流量的体积流量计广泛用于各种行业气体液体蒸汽流量的计量也可测量含有微小颗料杂质的混浊液体并可作为流量变送器用于自动化控制系统中LUGB型涡街流量传感器防爆型符合GB3836-2000《爆炸性环境用防爆电气设备》有关规定防爆标志为ExiaIICT6该仪表适用于工厂C级T6组及其以下的爆炸场所在本次设计中选用LUGB型涡街流量传感器其精度等级完全可以满足火电厂锅炉温度控制系统的精度要求产品特点◆可测量蒸汽气体液体的体积流量和质量流量◆无机械运动部件测量精度高结构紧凑维护方便◆压力损失小量程范围宽量程比达10-40倍◆采用消扰电路和抗振传感头仪表具有抗环境振动性能◆可测介质温度达350℃450℃技术参数◆公称口径 DN10~DN500◆测量介质气体液体蒸气◆可测介质温度 -40℃~150℃-40℃~280℃-40℃~350℃-40℃~450℃◆公称压力 25MPa 25 MPa协商供货◆精度等级 1级05级注05级量程范围≥17◆输出信号①电压脉冲低电平≤1V高电平≥6V脉冲宽04ms负载电阻 150Ω② 420mA转换精度±05满度值负载电阻19V350Ω24V500Ω30V750Ω③现场液晶显示瞬时流量6位显示m3h或kghth转换精度±01累计流量8位显示m3kgt转换精度±01◆供电电源①电压脉冲输出12VDC或24VDC② 420mA输出19VDC30VDC③现场液晶显示电池供电36V1节1号锂电池使用寿命大于3年外部供电12VDC或24VDC可实现带背光的液晶显示订货注明环境温度①电压脉冲输出-30℃65℃② 420mA输出-10℃55℃③现场液晶显示 -25℃55℃◆防爆标志 ExiaIIBT6◆表体材料 1Cr18Ni9Ti 其它材料协议供货 45号钢法兰连接型◆全智能型仪表①输出信号标态的体积流量或质量流量②现场液晶显示循环显示6位瞬时流量压力温度8位显示累积量com副控制器正反作用的选择副控制器的正反作用要根据副回路的具体情况决定而与主回路无关副环可以按照单回路控制系统确定正反作用的方法来确定副控制器的正反作用主控制器的正反作用根据主回路所包括的各环节来确定副回路的放大倍数可视为正因变送器一般为正这样主控制器的正负特性与主对象的正负特性一致本设计中主控制器和副控制器都要反作用com的PID调节器和副回路的PI调节器因为主回路是一个定制系统主控制器起着定制控制作用保持主变量的稳定是首要任务主控制器必须有积分作用在这里采用的是PID调节器它综合了比例控制积分控制和微分控制三种规律的优点又克服了各自的缺点比例部分能够迅速响应控制作用积分部分则最终消除稳态偏差微分部分可以稳定调节精度因为副回路是一个随动系统其给定值随主控制器输出的变化而变化同时两个并列的副环具有逻辑比值关系其变化是双交叉的为了能快速跟踪同时比例调节应该采用PI调节com仪表的选择采用模拟控制器DDZ-III型调节器DDZ―Ⅲ基型控制器框图如图43由控制单元和指示单元两部分组成控制单元包括输入电路比例积分微分电路手动电路保持电路指示单元有两种因此基型控制器也分两种即全刻度指示控制器和偏差指示控制器控制器的输入信号为1~5V的测量信号设定信号有内设定和外设定两种内设定信号为1~5V外设定信号为4~20mA测量信号和设定信号通过输入电路进行减法运算输出偏差到比例积分微分电路进行比例积分微分运算后由输出电路转换为4~20mA信号输出手动电路和保持电路附于比例积分微分电路之中手动电路可实现软手动和硬手动两种操作当处于软手动状态时用手指按下软手动操作键使控制器输出积分式上升或下降当手指离开操作键时控制器的输出值保持在手指离开前瞬间的数值上当控制器处于硬手动状态时移动硬手动操作杆能使控制器的输出快速改变到需要的数值只要操作杆不动就保持这一数值不变由于有保持电路使自动与软手动相互切换硬手动只能切换到软手动都是无平衡无扰动切换只有软手动和自动切换到硬手动需要事先平衡才能实现无扰动切换如果是全刻度指示控制器测量信号的指示电路和设定信号的指示电路分别把1~5V电压信号转化为1~5mA电流信号用双针指示器分别指示测量信号和设定信号当控制器出现故障需要把控制器从壳体中取出检查时可以把便携式手动操作器插入手动操作插孔以实现手动操作图43中的4~20mA输出信号通过精密电阻转化为1~5V电压反馈到控制器的输入端使控制器形成了自闭系统提高了控制器的运算精度根据火电厂生产设计要求采用WHSPL型调节器技术参数◆调节器输入通道5路信号标准4-20mA1-5VDC或0-10 mA0-25VDC◆调节器输出通道1路信号标准4-20mA或0-10 mA◆跟踪输入通道1路信号标准1-5VDCDDZ-III型或0-25VDCDDZ-II型◆模拟输入通道的输入阻抗为250Ω◆故障接点输出1路晶体管集电极开路输出◆手自接点输入1路无电压开关接点接点容量05A手动ON自动OFF◆电源220±10AC02A◆每个通道都可以用拨码开关设定为是否进行开方运算阻尼时间可通过面板修改◆PID参数范围 1给定值-691069 2比例带007999 3积分时间00999分 4微分时间00999分 5采样周期200毫秒◆安装方式表盘安装仪表自带悬挂装置◆仪表外尺寸80×160×260mm com的选择按所用能源形式的不同执行器分为电动气动和液动三类本设计主要是采用气动执行器为了安全考虑采用气开式它由气动执行机构和控制机构两部分组成气动执行机构又分为薄膜式和活塞式它们都是以压缩空气为能源具有控制性好结构简单动作可靠维修方便防活防爆和价廉等优点并可以方便地与气动仪表配套使用气动执行器也称为气动调节阀介绍典型产品气动薄膜调节阀地结构和工作原理气动薄膜调节阀的结构可以分为两部分上面是执行机构下面是调节机构从所学的知识可以了解到它主要由膜片弹簧推杆阀芯阀座等零部件组成当来自控制器的信号压力通入到薄膜气室时在膜片上产生一个推力并推动推杆部件向下移动使阀芯和阀座之间的空隙减小流体受到的阻力增大流量减小推杆下移的同时弹簧受压产生反作用力直到弹簧的反作用力与信号压力在膜片上产生的推力相平衡为止此时阀芯与阀座之间的流通面积不再改变流体的流量稳定可见调节阀是根据信号压力的大小通过改变阀芯的行程来改变阀的阻力大小达到控制流量的目的为了满足火电厂的安全生产要求在此次设计中使用VBD气动端面密封蝶阀VBD气动端面密封蝶阀是一种重量轻结构简单的后座式端面密封蝶阀阀体阀板均用钢板焊接或铸造加工而成适用于低压状态的空气或其他气体的流量压力控制本产品符合GBT4213-92标准技术参数◆型式扁平式焊接或铸造阀体◆公称通径 125~2000mm5〃~80〃◆公称压力PN025061016MPa JIS2K JIS5KJIS10K ANSI 150◆连接型式法兰式125~2000mm8〃~80〃密封面型式RF◆材料 25SUS304SUS316高温耐热钢Ni25Mo等◆标准型适用-5~200℃公称通径DN550以下◆外部轴承型公称通径DN600以上公称通径DN550以下温度200~600℃◆压盖形式螺栓压紧式◆填料聚四氟乙烯聚四氟乙烯石棉常温用柔性石墨中温高温用阀内组件◆额定行程全开60°或全开90°◆阀板材料 25SUS304SUS316等◆旋转轴材料SUS630SUS304SUS316◆阀体阀板密封形式端面密封型执行机构◆型式气缸活塞执行机构◆供气压力500kPa◆气源接口G18"G14"G38"G12"◆环境温度0~+70℃◆阀作用型式根据执行机构与旋转轴之间键连接位置不同可实现阀的气关式或气开式◆阀门安装方式阀杆应水平地安装在配管上若安装方式发生变化请予以注明附件◆定位器空气过滤减压器保位阀行程开关阀位传送器手轮机构等5控制系统的工作原理目前在火力发电厂中锅炉炉膛温度的控制虽然已经普遍采用了计算机控制但最常用的控制方法仍是普通PID控制包括单回路串级回路和分程控制等都是由PID作为基本的控制算法在此次设计中我们采用串级回路控制方法串级调节系统多用于燃料源受频繁扰动的锅炉炉膛该系统由主回路和副回路组成主回路根据实际值与给定值的偏差由PID调节规律对燃料流量进行调节副回路根据燃料流量实际值与主回路温度调节器输出的燃料流量的偏差对流量进行调节以避免扰动对燃料流量的影响在系统稳定状态时温度PID的输出以A1送到煤粉流量调节回路PID作为设定值以B1送到空气流量调节回路PID作为设定值在负荷剧增温测温给时温度PID的输出剧增对于空气流量调节回路随着B1开始增加时B1 B2低选器选中B1空气流量增加当B1正跳变到B1 B2时低选器选中B2B1被中断同时B3 B2高选器选B2B2作为该回路PID的设定值使空气流。
工业锅炉温度控制系统设计与实现

五、结论
本次演示对工业锅炉温度控制系统的设计与实现进行了详细的阐述。通过合理 地设计硬件和软件架构,以及精心的现场实施,我们成功地构建了一个高效、 稳定、安全的温度控制系统。该系统可以显著提高工业锅炉的温度控制精度和 生产效率,同时降低了能源消耗和安全隐患,为工业生产带来了积极的影响。
参考内容
5、适应性广:能够适应不同的锅炉型号和工作环境。
三、系统设计
基于以上的需求分析,我们设计出以下的温度控制系统:
1、硬件部分:采用以微处理器为核心的控制器,搭配热电偶、变送器等传感 器设备,以及电动调节阀等执行器设备。微处理器可以根据传感器采集的温度 数据,通过PID(比例-积分-微分)算法计算出调节量,控制执行器动作,以 实现对锅炉温度的精确控制。
参考内容二
摘要:
本次演示介绍了一种基于PLC(可编程逻辑控制器)的车载锅炉温度自动控制 系统,该系统的设计与实现旨在提高车载锅炉的温度控制精度和节能性能。通 过采用PLC控制器、传感器模块和显示模块等组件,实现了对车载锅炉温度的 实时监测与控制,并取得了良好的实验结果。本次演示的研究成果对于优化车 载锅炉温度控制具有一定的实用价值。
引言:
车载锅炉作为一种重要的能源设备,广泛应用于各种工业领域。然而,传统的 手动控制方式存在一定的局限性,如控制精度不高、节能性能不佳等。因此, 研究一种基于PLC的车载锅炉温度自动控制系统具有重要的现实意义。本次演 示旨在设计并实现一种具有高精度、节能性能优异的温度自动控制系统,从而 提高车载锅炉的整体运行性能。
5、通信功能:系统应具备与上位机或其它设备进行数据通信的功能,实现数 据的远程监控和管理。
四、系统实现
在系统实现阶段,我们需要完成以下几个步骤:
1、硬件选型和搭建:根据系统设计的要求,选择合适的微处理器、传感器、 执行器等硬件设备,并进行搭建。
锅炉温度控制系统设计
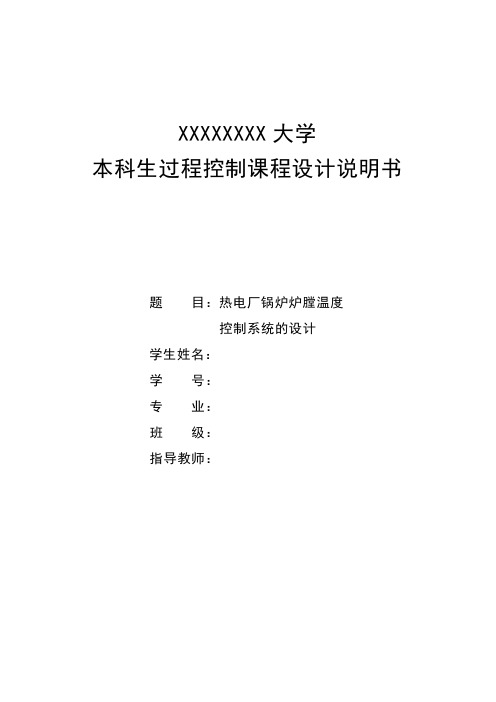
XXXXXXXX大学本科生过程控制课程设计说明书题目:热电厂锅炉炉膛温度控制系统的设计学生姓名:学号:专业:班级:指导教师:摘要锅炉是热电厂重要且基本的设备 ,其最主要的输出变量之一就是主蒸汽温度。
主汽温度自动调节的任务是维持过热器出口汽温在允许范围内 ,以确保机组运行的安全性和经济性。
如果该温度过高 ,会使锅炉受热面及蒸汽管道金属材料的蠕变速度加快 ,降低使用寿命。
若长期超温 ,则会导致过热器爆管 ,在汽机侧还会导致汽轮机的汽缸、汽阀、前几级喷嘴和叶片、高压缸前轴承等部件的寿命缩短 ,甚至损坏;假如该汽温过低 ,会降低机组的循环热效率 ,一般汽温每降低5 ℃~10 ℃,效率约降低1 % ,同时会使通过汽轮机最后几级的蒸汽湿度增加 ,引起叶片磨损;当汽温变化过大时 ,将导致锅炉和汽轮机金属管材及部件的疲劳 ,还将引起汽轮机汽缸和转子的胀差变化 ,甚至产生剧烈振动 ,危及机组的安全 ,所以有效精准的控制策略是十分必要的锅炉炉膛温度的控制效果直接影响着产品的质量,温度低于或者高于要求时都不能达到生产质量指标,有时甚至会发生生产事故,此设计控制以锅炉炉膛温度为主控参数、燃料和空气并列为副被控变量设计热电厂锅炉温度控制系统,以达到精度在正负5 ℃范围内。
关键词:热电厂;锅炉;炉膛温度;串级控制目录引言 (4)第一章热电厂的工艺流程及要求 (5)第二章锅炉的工艺流程及控制要求 (7)2.1锅炉的工艺流程 (7)2.2锅炉的控制要求 (8)第三章锅炉炉膛温度的分析 (8)第四章锅炉炉膛温度控制系统的设计 (12)4.1炉膛温度控制的理论数学模型 (12)4.2炉膛温度控制方法的选择 (12)4.3 系统单元元件的选择 (12)4.3.1温度检测变送器的选择 (12)4.3.2流量检测变送器的选择 (14)4.3.3主、副调节器正反作用的选择 (15)4.3.4主、副回路调节器调节规律的选择 (16)4.3.5控制器仪表的选择 (16)4.3.6控制阀的选择 (18)第五章锅炉炉膛温度控制系统的工作原理 (19)第六章总结 (20)参考文献 (21)引言随着现代工业生产的迅速发展,对工艺操作条件的要求更加严格,对安全运行及对控制质量的要求也更高。
- 1、下载文档前请自行甄别文档内容的完整性,平台不提供额外的编辑、内容补充、找答案等附加服务。
- 2、"仅部分预览"的文档,不可在线预览部分如存在完整性等问题,可反馈申请退款(可完整预览的文档不适用该条件!)。
- 3、如文档侵犯您的权益,请联系客服反馈,我们会尽快为您处理(人工客服工作时间:9:00-18:30)。
淮海工学院课程设计报告书课程名称:专业综合课程设计题目:锅炉温度控制系统设计系(院):电子工程学院学期:2011-2012-1专业班级:自动化081姓名:学号:评语:成绩:签名:日期:1 引言锅炉参数控制,是过程控制的典型实例。
锅炉微计算机控制,是近年来开发的一项新技术,它是微型计算机软、硬件、自动控制、锅炉节能等几项技术紧密结合的产物,我国现有中、小型锅炉30多万台,每年耗煤量占我国原煤产量的1/3,目前大多数工业锅炉仍处于能耗高、浪费大、环境污染等严重的生产状态。
提高热效率,降低耗煤量,用微机进行控制是一件具有深远意义的工作。
工业生产过程中,用模拟控制来控制电加热炉温已经取得了较为成熟的经验,但他的控制精度较低,显示操作不方便,为此引入了计算机控制系统对温度进行数字算法控制。
由于锅炉加热的时间常数相对于采样周期来说很大,所以锅炉加热控制系统的动态特性可以看作一阶滞后环节来近似,在控制算法上可采用最小拍无纹波控制或其他纯滞后补偿算法。
根据控制系统要求,设计控制方案和主电路及各检测控制模块电路,然后针对温度控制要求计算电路元件所需参数,应用最小拍无纹波控制算法,实现锅炉温度控制。
进而了解温度控制系统特点及运用计算机设计控制程序实现计算机自动控制温度的方法。
2 设计电路图及工作原理控制系统原理图如图1所示,炉温控制的基本原理是:改变可控硅的导通角即改变电热炉加热丝两端的有效电压,有效电压可在0~140V 内变化。
可控硅的导通角为0~5bH 。
温度传感器是通过一只热敏电阻及其放大电路组成,温度越高其输出电压越小。
外部LED 灯的亮灭表示可控硅的导通与关断的占空比时间,如果炉温低于设定值则可控硅导通,系统加热,否则系统停止加热,炉温自然冷却到设定值。
设炉温的给定值为450oC,广义被控对象的传递函数为10()(1)sd eW s s s-=+。
图1 系统的基本原理单片机D/A执行机构被控对象反馈环节A/D 广义被控对象给定值-—3 系统硬件设计3.1 输入通道扩展如图2所示的是输入通道的扩展图,利用8051单片机和ADC0809以及74LS373芯片组成的中断控制方式的电路图,在图2中,由于ADC0809正在转换是EOC =0,转换结束时EOC=1,而如果设单片机的外部中断0为下降沿触发的话,则EOC 需要经过反相器后才能连接至0INT 。
图2中采用5.2P 和WR 启动A/D 转换器,在单片机的振荡频率不太高的情况下,若ALE 引脚的输出频率范围满足ADC0809的要求的话,可以直接作为ADC0809的时钟输入。
图2 输入通道扩展电路图3.2输出通道扩展图3 输出通道扩展电路图图3所示的是单片机与DAC0832组成的输出通道的扩展,图中单片机与DAC0832采用的是单缓冲方式的接口电路,采用单缓冲方式的接口电路,DAC0832不能同步输出,图中DAC0832的CS和XFER都与地址线P相连,当地址线选通DAC0832后,只要输出2.2WR控制信号,DAC0832就能一步完成数字量的输入所存和D/A转换成输出,图3中采用的输出方式为单极性输出方式。
3.3 A/D转换电路设计A/D转换器的作用就是把模拟量转换为数字量,是模拟量输入通道必不可少的器件。
常用的A/D转换器从转换原理上可分为逐次逼近型、计数比较型和双积分型;从分辨率上可分为8位、12位、16位等。
A/D转换器与单片机的硬件接口有3种方式:查询方式、延时方式和中断方式。
查询方式就是首先由CPU向A/D转换器发出启动脉冲,然后读取转换结束信号,根据转换结束信号的状态,判断A/D转换是否结束。
如果结束,可以读取A/D转换结果,否则继续查询,直到A/D转换结束。
转换结束引脚通常连接到数据线或I/O口线上。
这种方法程序设计简单,且可靠性高,但实时性差,大多数控制系统对于这点都是允许的,这种方法用的最多。
该系统采用查询方式。
A/D转换电路图如图4所示:图4 A/D转换电路图3.4 D/A转换电路设计D/A转换器就是一种把数字信号转换为模拟电信号的器件,是模拟量输出通道必不可少的器件。
D/A转换器与计算机的连接方式可有3种:直接连接、采用可编程并行接口和采用锁存器连接。
DAC0832是电流型输出器件,根据运放和DAC0832的连接方法不同,可以分为单极性输出和单极性输出。
其控制方式可以分为双缓冲和单缓冲方式。
本系统采用了双缓冲单极性输出方式的接口电路如图5所示:图5 D/A转换电路图3.5报警电路电路原理图如图6所示:图6 报警电路图其中使用光耦TLP521-1进行单片机隔离,当加热水温超过预设值时,单片机口P2.4输出高电平,光耦导通,继电器开始动作,其长弊端闭合,+5V电源接入,声光报警功能启动。
音乐芯片采用市场上常用的警笛报警芯片,价格便宜,同时发出声音比蜂鸣器大许多。
3.6 键盘电路设计图7所示的为独立联接式无编码键盘电路。
当键盘数较少时, 采用独立联接式键盘可以使系统简单有效。
独立式键盘是最简单的键盘结构形式,每个按键的电路是独立的,都有单独一根I/O 口线采集键的通断状态。
当某键按下时,对应口线被下拉到地;断开时,口线被电阻上拉到+5V 。
显然,通过检测各I/O 口线的状态,就能知道有无键闭合以及哪个键闭合。
图7 键盘电路图3.7 LED 显示电路设计如图8所示的是LED 动态扫描接口电路,图中WR P LE +=7.2,片选信号是从8051单片机的4.1P 至7.1P 经过反相器连接至LED 显示管上的,而位选信号则是8051单片机经过74LS373连接至4个LED 的显示管上。
图8 LED 显示电路图4 最少拍无纹波计算机控制系统设计已知被控对象的传递函数为10()(1)sd eW s s s-=+,取采样周期5.0=T s用零阶保持器沟通数字控制器与被控对象联系时,该系统广义对象的脉冲传递函数])1(101[)(+⋅-=-s s ese Z z G sTs)6065.01)(1(065.19025.0)1)(1()]5.0()5.11([]1111)1(15.0)[1(10)1111)(1(10112315.015.05.01215.012111211---------------------+=---+-=-+-----=++--=z z zzz e z eez zzezz z z z s ssz z再确定闭环脉冲传递函数和误差脉冲传递函数)1)(1()(09025.0)(2211132-----++-=+=zf zf z z W azazz e φ 联立求解上式得通过)(1)(z W z e -=φ11=f ,8474.02=f , 1526.0=a328474.01526.01)(----=zzz W e因此控制器的脉冲传递函数)()()()(z W z G z z D e φ=654325432322332217648.00402.11625.09025.0065.10784.01152.01159.01526.0)8474.01526.01)(0652.19025.0()1293.01526.0)(6065.06065.11(--------------------++--=--+++-=z z z z z zz z z zzz zz zzz5 MATLAB 仿真5.1 Simulink 仿真图如图9所示:图9 Simulink 仿真图5.2 MATLAB 仿真波形如图10所示:图10 MATLAB仿真波形6 软件设计控制系统的软件主要包括:温度的采样和处理、控制计算、中断、显示、调节参数修改、温度设定及修改。
其中控制算法采用最小拍无纹波控制算法,以达到更好的控制效果。
系统的软件流程图如图11所示:开始系统初始化键盘输入给定温度值温度采集温度显示与给定值相比较计算差值N|e(k)|>0Y最小拍无纹波控制求出输出控制量图11 程序总体流程图7 说明书该系统是锅炉温度控制系统,首先用键盘输入给定的温度值,温度传感器进行温度的采集,通过A/D转换器转换得到二进制温度数据,并对其进行、标度变换并与输入的参照温度相比较,得出误差,根据最小拍无纹波控制算法求出控制温度达到期望值所需要的控制量控制可控硅的导通角即改变电热炉加热丝两端的有效电压,从而改变电路的输出功率,达到调温作用。
8 参考文献[1] 范立南,李雪飞.计算机控制技术.北京:机械工业出版社.2009[2] 陈夕松,汪木兰.过程控制系统.北京:科学出版社,2005[3] 潘新民.微型计算机与传感器技术. 北京:人民邮电出版社,1996[4] 刘玉强,刘晓为等.高温扩散炉恒温区温度的自动控制.哈尔滨工业大学学报,1999[5] 黄胜军.微机控制应用实验与实例. 第一版. 北京:清华大学出版社,1999[6] 曹天汗.单片机原理与接口技术.第一版.北京:电子工业出版社,2003[7] 胡汉才.单片机原理及其接口技术.第二版.北京:清华大学出版社,2003[8] 胡寿松.自动控制原理.北京:国防工业出版社,1990第页共10 页10。