太阳能跟踪器中英文对照外文翻译文献
外文翻译

Advancements in Solar based LED Street lightNupur 1 Neha 1 Sangya gugri 1 Srishti mishra 1 Gulshan kr. dubey 2UG Student, Dept. of EIE, Galgotia‟s College of engineering & technology, Uttar Pradesh India 1 Associate professor, Dept. of EIE, Galgotia‟s College of engineering & technology, Uttar Pradesh,India 2ABSTRACT: We are in the time where energy conservation & use of renewable resourceshas become a necessity. Thus requirement of methods which are not only highly efficient but also low in energy consumption has greatly increased to keep a check on pollution factor. Keeping this in mind this paper focuses on solar based LED street light that uses automatic intensity controller with a solar tracker. This type of LED street light not only adjust itself according to the varying darkness but also keeps a track on overcharging, deep discharging, automatic restoration of charging ,protecting the battery from the over/under voltage. It comprised of solar cell and electric energy stored from battery. The LED street lamp is lit at night automatically and changed into pulsed lighting in low power after the setting time and then turns off in daytime. Since only 20% of the total sun‟s energy falls on earth and also the trajectory of sun keeps changing thus a solar tracker is used so as to track maximum sun‟s energy.Keywords:Solar panel, charge controller, Intensity regulator, Solar tracker.I.INTRODUCTIONThesurface of the Sun has a temperature of about 5,800 Kelvin (about 5,500 degrees Celsius, or about 10,000 degrees Fahrenheit),as per the say of NASA, At that temperature, most of the energy the Sun radiates is visible and near- infrared light. At Earth‟s average distance from the Sun (about 150 million kilometres), the average intensity of solar energy reaching the top of the atmosphere directly facing the Sun is about 1,360 watts per square meter, according to measurements made by the most recent NASA satellite missions. This amount of power is known as the total solar irradiance. (Before scientists discovered that it varies by a small amount during the sunspot cycle, total solar irradiance was sometimes called “the solar constant.”Averaged over the entire planet, the amount of sunlight arriving at the top of Earth‟s atmosphere is only one-fourth of the total solar irradiance, or approximately 340 watts per square meter.II. SOLAR TRACKERSolar tracking system[1] is the most appropriate technology to enhance the efficiency of the solar cells by tracking the sun. A microcontroller based design methodology of an automatic solar tracker is presented in thispaper. Light dependent resistors are used as the sensors of the solar tracker.The sun is the prime source of energy, directly or indirectly, which is also the fuel for most renewable systems. Among all renewable systems, photovoltaic system is the one which has a great chance to replace the conventional energy resources. Solar panel directly converts solar radiation into electrical energy. Solar panelis mainly made from semiconductor materials. Si used as the major component of solar panels, which ismaximum 24.5% efficient [2]. Unless high efficient solar panels are invented, the only way to enhance the performance of a solar panel is to increase the intensity of light falling on it. Solar trackers are the most appropriate and proven technology to increase the efficiency of solar panels through keeping the panels aligned with the sun‟s position. Solar trackers get popularized around the world in recent days to harness solar energy in most efficient way. This is far more cost effective solution than purchasing additional solar panels [3].III. TECHNOLOGY TO ENHANCE POWER OUTPUT FROM SOLAR PANELIncreasing the cell efficiency, maximizing the power output and employing a tracking system with solar panel are three ways to increase the overall efficiency of the solar panel[4]. Improvement of solar cell efficiency is an ongoing research work and people throughout the world are actively doing research on this. Maximizing the output power from solar panel and integrating solar tracking system are the twoways where electronic design methodology can bring success.Maximum power point tracking (MPPT) is the process to maximize the output power from solar panel by keeping the solar panel‟s operation on the knee point of P-V characteristics.A number of MPPT algorithms have been developed and employed around the world [5]. MPPT technology only offers the maximum power that can be received from a stationary array of solar panels at a particular time; it cannot, however, increase the power generation when the sun is not aligned with the system. Automatic solar tracker increases the efficiency of the solar panel by keeping the solar panel aligned with the rotating sun.Solar tracking is a mechanized system to track the sun‟s position that increases power output of solar panel 30% to 60% than the stationary system [6]. A few design methodology of solar tracking system has been proposed in recent days [7]-[9]. LED (Light Emitting Diode), light-emitting Diode, is a kind of ability to electric energy into visible Light solid state semiconductor devices, it can be directly put DianZhuan into Light. The heart of the LED is a semiconductor chip, chip attached on a bracket, at the end of the end is negative, the other end connected to the power of the anode, the whole chip is encapsulated by epoxy resin. Semiconductor chip consists of two parts, one part is a p-type semiconductor, dominated by holes in it, the other end is n-type semiconductor, here is mainly electronic. But this two kinds of semiconductor connected, forming a p-n junction between them. When a current flows through a wire to the chip, the electron will be pushed P area, electron and holes in the P zone compound, then will be issued in the form of photon energy, this is the principle of LED light. And the wavelength of light was the color of the light, is determined by the formation of p-n junction material.Initially LED is used as the indicator light instrument and then all kinds of light color of LED traffic light and display screen has been widely applied in large area, produced good economic and social benefits. 12-inch red traffic lights, for example, in the United States could have been used long life, low light efficiency of 140 - watt incandescent lamp as light source, it produces 2000 lumens of white light.After the red filter, light loss 90%, only 200 lumens of red light. And in the light of the new design, Lumileds companies adopted 18 red LED light source, including circuit loss, total power consumption of 14 watts, can produce the same light. Car light is also an important field of LED light source.For general lighting, people need more white light sources. Hair white light LED successful development in 1998. This LED to GaN chip and yttrium aluminum garnet (YAG) packaging together. GaN hair blue chip (lambda p = 465 nm, Wd = 30 nm), high temperature sintering of YAG phosphors containing Ce3 + yellow light shot after the blue light excitation, peak 550 m nled lamp. Blue LED substrate is installed in the bowl reflection cavity, covered with thin layer of resin mixed with YAG, about 200-500 nm. LED substrate from the blue part is absorbed phosphor to another part of the mix blue with yellow light from fluorescent powder, we can get more white light. For InGaN/YAG white leds, by changing the chemical composition of YAG phosphors and adjust the thickness of phosphor layer, can obtain a variety of white light color temperature 3500-10000 k. This by the method of blue leds for white light, simple structure, low cost, high technical maturity, so use the most.Compared with the traditional glow of light, LED light source is low pressure microelectronics products, successfully combines computer technology, network communication technology, image processing technology and the embedded control technology, etc. Traditional LED lights used in the chip size is 0.25 mmX0.25 nm, and the size of the LED lighting is typically mmX1.0 in 1.0 mm and above. LED bare chip forming work table structure, the inverted pyramid structure and flip chip design can improve the luminous efficiency, thus more light. LED packaging innovation including the design of high conductivity metal base, flip chip design and bare plate casting type lead frame and so on, these methods can design a high power, low thermal resistance of the device, and the device of the illumination intensity of illumination is greater than traditional LED products.A typical high flux LED device can produce several lumens to dozens of lumen flux, update the design can be integrated in a device more leds, or multiple devices can be installed in a single assembly, so that the number of lumen output is equal to the small bulb. For example, a high power 12 monochromatic LED chip light energy device can output 200 lm, the consumed power between 10 ~ 15 w.The application of LED light source is very flexible, used as the dot, line, face various forms of lightweight products; LED control is extremely convenient, as long as adjust current, can be arbitrarily adjusted light; A combination of different light color changing, the sequential control circuit, can achieve more dynamic change of rich and colorful effect. LED has been widely applied in all kinds of lighting equipment, such as a battery-powered flashlight, mini voice control lamp, security lighting, outdoor and indoor stair floodlight roads and buildings and tag continuous lighting.The emergence of white LED is LED from the identification to the illumination function across a substantive step. White LED closest to the sun, more can wellreflect the reality of the irradiation object color, so from a technical perspective, white LED is undoubtedly the most cutting-edge LED technology. White LED has began to enter some application field, emergency lights, flashlights, flash and other products appeared, but because the price is very expensive, so hard to popularize. White LED popularization is the premise of price decline, and prices must be formed in the white leds is possible after a certain market scale, integration of the two end depends on technology progress.IV. MICROCONTROLLERThe ATMEGA32 microcontroller has been used in the prototype. Microcontroller is the heart of overall system.ATMEGA32 microcontroller requires a 5 volt regulated voltage supply. …7805‟ voltage regulator is used to providefixed 5 volts supply to the microcontroller .ATMEGA32 has some features such as analoge comparator (AC), analog to digital converter (ADC), universal synchronous asynchronous receiver transmitter (USART), times etc. [13]. Utilization procedure of these features is given below 1)Analog comparator:There are two pins which are known as analog input 0 (AIN0) and analog input 1 (AIN1). Two analog voltage signals coming from two junctions of photo resistor circuit are fed to these pins. There is a bit called analog comparator output (ACO) which is set to either …1‟or …0‟.ACO = 01 VAIN0 > V AIN1VAINI> VAIN02) Analog to digital converter:Among 8 analog to digital converter input pins ADC0 and ADC1 have been used; where VVt ,is expected. Differential input is converted into digital value and the most 8 significant bits are defined 10 ADCADC asADC_result to compare with threshold. ADC_result= [V ADC0 – V ADC1 ] digitalThis threshold value, set according to the photo resistor response against the solar radiation intensity, is provided, sinceADC_result alone might be insufficient for rotation of motor. And if ADC_result> Threshold; motor rotates one step.3) Timers:Built-in timer of ATMEGA32 is utilized to create delay. The Earth rotates on its own axis, with respectto the sun 360°in a day and so it rotates, (360°/24=) 15° an hour or 3.75° in 15 minutes. Delay for 1.5 minutes and 15 minutes are required. These delays are mentioned as short delay and moderate delay respectively. The lasthour before sunset will provide additional energy to rotate thepanel in the initial position and so the tracker no more rotatesto the west rather it will rotate reversely. As 2 hours in day time are not considered for tracking, (2Ҳ15°=) 30° of rotationis not required to be done by the solar tracker. Half stepping of stepper motor is considered which gives 3.75° rotation ineach stepping; approximately ((180°-30°)/3.75°=) 40 rotations are required in each day to track the sun atdaylight. Count is used for counting the number of …wait‟ states when weather is cloudy and ADC does not permit to rotate the motor.V.CHARGE CONTROLLERA charge controller monitors the state-of-battery to insure that when the battery needs charge-current it gets it, and also insures the battery isn't overcharged. Connecting a solar panel to a battery without a regulator seriously risks damagingthe battery and potentially causing a safety concern.Charge controllers (or often called charge regulator) are rated based on the amount of amperage they can process from a solar array. If a controller is rated at 20 amps it means that you can connect up to 20 amps of solar panel output current to this one controller. The most advanced charge controllers utilize a charging principal referred to as Pulse-Width-Modulation (PWM) - which insures the most efficient battery charging and extends the life of the battery. Even more advanced controllers also include Maximum Power Point Tracking (MPPT) which maximizes the amount of current going into the battery from the solar array by lowering the panel's output voltage, which increases the charging amps to the battery - because if a panel can produce 60 watts with 17.2 volts and 3.5 amps, then if the voltage is lowered to say 14 volts then the amperage increases to 4.28 (14v X 4.28 amps = 60 watts) resulting in a 19% increase in charging amps for this example.Charge controllers also offer Low Voltage Disconnect (LVD) and Battery Temperature Compensation (BTC) as an optional feature. The LVD feature permits connecting loads to the LVD terminals which are then voltage sensitive.If the battery voltage drops too far the loads are disconnected - preventing potential damage to both the battery and the loads. BTC adjusts the charge rate based on the temperature of the battery since batteries are sensitive to temperature variations above and below about 75 F degrees.1)Battery:The Deep Cycle batteries used are designed to be discharged and then re-charged hundreds or thousands of times.These batteries are rated in Amp Hours (ah) - usually at 20 hours and 100 hours. Simply stated, amp hours refers to the amount of current - in amps - which can be supplied by the battery over the period of hours. For example, a 350ah battery could supply 17.5 continuous amps over 20 hours or 35 continuous amps for 10 hours. To quickly express the total watts potentially available in a 6 volt 360ah battery; 360ah times the nominal 6 volts equals 2160 watts or 2.16kWh (kilowatt-hours). Like solar panels, batteries are wired in series and/or parallel to increase voltage to the desired level and increase amp hours.The battery should have sufficient amp hour capacity to supply needed power during the longest expected period "no sun" or extremely cloudy conditions. A lead-acid battery should be sized at least 20% larger than this amount..If there is a source of back-up power, such as a standby generator along with a battery charger, the battery bank does not have to be sized for worst case weather conditions.The size of the battery bank required will depend on the storage capacity required, the maximum discharge rate, the maximum charge rate, and the minimum temperature at which the batteries will be used. During planning, all of these factors are looked at, and the one requiring the largest capacity will dictate the battery size.In this specific application, and taking into account thechanges of solar radiation during the day and, consequently, the energy available, the battery bank charge algorithm willpresent three different modes:• If the panel available current is lower than 0.1CAh, the converter will find the maximum power point (MPPT)in order to provide the highest current possible for thebattery bank (area under the current level, see figure 2).• If the panel available current is higher than 0.1CAh, theconverter limits the current to 0.1CAh, and disables thesearch for the maximum power point.• If the batteries are already charged, the control algorithmwill apply a constant voltage level, in order to keep thebatteries charged. Lead-acid batteries are the most common in PV systems because their initial cost is lower and because they are readily available nearly everywhere in the world. There are many different sizes and designs of lead-acid batteries, but the most important designation is that they are deep cycle batteries. Lead-acid batteries are available in both wet-cell (requires maintenance) and sealed no-maintenance versions. AGM andGel-cell deep-cycle batteries are also popular because they are maintenance free and they last a lot longer.VI. CONCLUSIONThis paper has studied about various advancements in the field of solar based LED street light. the use of solar tracking system has greatly increased the system and has helped to increase its overall output.Whereas the use of charge control circuit in the solar based LED street light has not only helped in saving the battery power but also in preventing the battery from getting deep discharged, overcharged, thereby conserving a lot of energy.R EFERENCES[1] Design and Construction of an Automatic SolarTracking System Md. Tanvir Arafat Khan, S.M. ShahrearTanzil, RifatRahman, S M ShafiulAlam*, Member, IEEE Department of Electrical and Electronic Engineering,[2] M. A. Green, “Clean Electricity from Photovoltaics,” Ed. Mary D.Archer and R. Hill, Series on Photoconversion of Solar Energy, V. 1,Imperial College Press, UK.[3] M.A. Panait and T Tudorache, “A Simple Neural Network SolarTracker for Optimizing Conversion Efficiency in Off-Grid Solar Generato r”Intl. Conf. on Renewable Energy and Power quality, no.278, March, 2008.[4] Piao, Z.G. Park, J. M. Kim, J. H. Cho, G. B. Baek, H. L, “ A study on the tracking photovoltaic system by program type,” Intl. Conf. on Electrical Machines and Systems, vol. 2, pp. 971-973, Sept. 27-29, 2005.[5] C. Hua and C. Shen, “Comparative study of peak power tracking techniques forsolar storage system,‟‟Applied Power Electronics Conference and Exposition, vol. 2, pp. 679-685, Feb. 15-19, 1998.[6] A. K. Saxena and V. D utta, “A versatile microprocessor based controller for solar tracking,‟‟ Photovoltaic Specialists Conference, vol. 2, pp. 1105-1109, 1990.[7] B. Koyuncu and K. Balasubramanian, “A microprocessor controlled automatic sun tracker,‟‟ IEEE Transactions on Consumer Electronics,vol.37, no. 4, pp. 913-917, 1991.[8] Design and Construction of an Automatic SolarTracking System Md. Tanvir Arafat Khan, S.M. ShahrearTanzil, RifatRahman, S M ShafiulAlam*, Member, IEEE太阳能LED路灯摘要:我们是在节约能源可再生资源和利用已经成为一种必然的时间。
太阳能双轴跟踪英语文献

Design of Track Control System in PVJun-ming Xiao , Ling-yun Jiao , Hai-ming Zhu, Rui ZhangSchool of Electronic and Information EngineeringZhongyuan University of TechnologyZhengzhou, P.R. Chinaxiaojunming528@(1. M .Xiao) jiaolingyun@(L. Y. Jiao)Abstract-Solar energy has an enormous developing applicationcapacity as one kind of green renewable energy source which canbe continuously used forever. The track control system in PVadapts automatic tracking light techniques to make solar panelsalways perpendicular to sunlight. This way can greatly improvethe generated energy of PV array, add solar energy utilizationratio, reduces the cost of photovoltaic power. This paper mainlyintroduces the basic structure and hardware and software designprocess of track control system in PV, gives the hardware circuit,parameter test methods and software control process of thissystem, analysis the advantages and disadvantages of suntrajectory tracking mode and electro-optical tracking mode,choose the method that electro-optical tracking as the majortracking mode while the sun trajectory tracking mode asadditional tracking mode on unusual weather conditions.Keywords-photovoltaic power; automatic track control;controller; sun trajectory tracking; electro-optical trackingI.In the energy crisis and environmental pollution highlightof today ,states have adopted a series of significant measures toand support the development of solar energy.Photovoltaic power is one of the main ways of solar energyutilization, has the characteristics of environmentally-friendlyand non-polluting, application range is very wide, has nowbeen used in co mmun ication, transportation and other fields,has a place in the national economy energy system [1]. Atpresent, the cost of photovoltaic power generation is too high,can not be compared with the traditional forms of powergeneration, influenced the development of domestic PV power978-1-4244-6055-7/10/$26.00 ©2010 IEEEIn order to reduce the cost of PV power, countriesaround the world are constantly exploring, at this stage themore mature approach are mainly tracking method and thelight-gathering method. Tracking method that is usingmodel, keep light vertical irradiate photovoltaicarray surface to improve solar panels' ability of absorb solarradiation. Track control system in PV using automatic trackingsolar power generation equipment can enhance the powergeneration efficiency 35%, decrease cost by 25% [2].II. T HE STRUCTURE OF TRACK CONTROL SYSTEM PVFig.l The block diagram of track control system in PYSolar energy as one kind of clean and non-pollution energy,has very broad prospects for development, however, there isthe problem of low density, intermittent and space distributionchanges [3], which put forward higher requirements for thecollection and use of solar energy. At present, solar panels ofphotovoltaic power generation system are basically fixed, cannot make full use of solar energy resources and generationefficiency is lower. Track control system in PV canautomatically adjust the orientation of solar panels according to the altitude angle and azimuth angle of sun, make the sun light always perpendicular incident the surface of photo v oltaic array to obtain the maximum power generation efficiency.As figureIshow is the block diagram of track controlsystem in PV , system uses modular design, mainly composed by photovoltaic array, tracker, sensors, controller, inverter and other components. Sensors can accurately receive sunshine within a certain angle and transform it into a measurable error signal; tracker can handle the error signal which is measured by sensors, then output motor triggered signals according to the control algorithm; controller can control the motor's running and stop according to the motor triggered signals. III.TRACKING METHOD AND CONTROL STRATEGY DESIGNPRINCIPLESA.The calculation a/sun angleThe sun path changes as the season changes, the sunposition tracking method can be divided into horizon coordinates tracking and equatorial coordinates tracking, horizon coordinate tracking method track the sun's altitude angle and azimuth angle, equatorial coordinate tracking method track the sun's declination angle and solar hour angle. Since the change range of solar declination angle is no more than ±23°27', its changes slowly so choose horizon coordinate tracing method.The calculation formula of sun altitude angle a and azimuth angle r s [4]:sin a =sin lj? sin 5 + cos lj? cos 5 cos Bh ( 1 )cos r s=(sin a sin lj? -sin 5) / (cos a cos lj?)Or, sin r s=cos 5 sin Bh / cos aWhere, declination angle5 =23.45 sin (360 x284 + n)365( 2 )lj? is installation site latitude;Bh is solar hour angle;nis thedays of year.According to the geographical latitude, the declination Angle and observation time, using equation (1) and (2) can calculate the sun's altitude angle and azimuth angle at any moment, any area.B.Tracking modeThe tracking mode that adopts at home and abroadis very much, it can be divided into sun trajectory tracking mode and electro-optical tracking according to the different forms of tracking [5], can be divided into uniaxial tracking method and biaxial tracking method according to the different forms of exercise [6].trajectory tracking mode and electro-optical tracking mode have some limitations, sun trajectory tracking mode need to accurate positioning before running, can not carry on automatic adjustment when sun angle calculation has errors. Electro-optical tracking mode under the influence of the weather greatly, usually appear not to track or wrong track of the situation because of the weather problem, especially in weather conditions may occur motor reciprocating motion situation, result in the waste of energy. This paper selected the biaxial tracking method of sun trajectory tracking mode combined with electro-optical tracking mode. In the of strong light using light intensity detect circuit detect ray deviation to electro-optical tracking, In case of weather changes the system automatically turns into sun trajectory tracking mode.C.Control modeIn photovoltaic power tracking system, control mode canbe divided into three types of open loop, closed loop and hybrid control according to whether exist feedback while the control system control the quantity control. Although the open loop control mode is uncomplicated and easy to realize, has the problem of tracking inaccurate, when the continuous overcast and rainy days, system will consume large amountsof power. Therefore, this article selected the closed loop control mode. Closed loop control mode schematic diagram is shown as Fig.2.As the figure shown, closed loop control mode is using sensor detect the deviation of the incident light rays of sun and system optical axis, when the deviation over the threshold, drive machine part tum to move through motor, reduce the deviation until the sun ray and system optical axis afresh parallelism, realize the tracking of the solar altitude angles and azimuth Angle.Fig.2 Closed loop control schematic diagram IV.DESIGN OF SYSTEM HARDWAREA.The basic composition of h ardwarePV tracking controller is a power plant that can make thesolar panel track the orientation of sunshine at any time and the sun light vertical irradiates to the solar panel. It's mainly compose with sensor, light intensity detect temperature detect circuit, current/voltage detect circuit, stepping motor, motor driver and other until, the hardware Fig.3 Controller hardware block diagramB.Light intensity detect circuitThe 14 parameters that PV tracking system can detect arethe output voltage/current of PV arrays, battery charging electric current/voltage, output AC current and AC voltage of inverter, environment temperature, battery temperature, PV arrays temperature, environment light intensity, tracking light intensity, sun altitude angle, azimuth angle and wind velocity.Light intensity detect circuit schematic is shown as FigA, operational amplifier, triode, resistance, capacitance and otherelements. PhototransistorDlandD2tum on after acceptsunshine, triode amplify the electrical signals. The voltage across the voltage follower is equal, avoid the mutual influence of front and back electric circuit, differential amplifieramplifytwovoltage'sdifferencevalue.Comparator's output voltage V DID 2 compared with reference voltage Vref, if the co-rotating input voltage larger than the reverse input voltage, the output is high-level, else is low-level. The motor run while the compare result V I islow-level.FigA Light intensity detect circuit schematicC.Stepping motor driver circuitStepping motor is one kind of actuator that convertselectric pulse into angular displacement, in the tracking control system using the controller's output signal as steppingmotor driver's input control signal, in order to control stepping motor's positive inversion of longitudinal direction and horizontal direction. As Fig.5 shown is one of the stepping motor drive circuits, the system totally have four stepping motor drive circuits, respectively drive stepping motor's positive inversion of longitudinal direction and horizontal direction.Control pulse goes into transistor after 74LS14 reverse phase, the pulse amplified by the transistor, then control photoelectric switch. After photoelectric isolation, carry on the voltage and current amplification by power tube, then drive each phase windings of stepping motor, make steppingmotor do forward, backward, speed up, slow down or stop movement. As Fig.5 shown L is one phase winding of stepping motor, RL is winding internal resistance, RISexternal resistors, has the function of limit current and improves the circuit time constant, the shunt capacitance across the external resistors can enhance the high frequency performance of stepping motor, D is fly-wheel diode, avoid power tuber's damage because of the back electromotive force that produced by motor winding.+25VFig.S Stepping motor driver circuitV.SYSTEM SOFTWARE DESIGNFig.6 System operating proceduresThe software part of PV tracking control system mainly includemamprogram,dataacquisitionmonitoring subroutine, electro-optical tracking subroutine, trajectory tracking battery charge and discharge subroutine, and so on, control flow is shown as Fig.6. The system can multiple detect signal acquisition, display, query, etc, can carry on real-time or historical data's graphics image processing and print for theinformation stored in the database, has the function of self-calibration, self-diagnosis and self-test. At the same time, the system can automatically adjust the position of PV array according to test results, in order to achieve real-time tracking target.VI.effective solutions of human energy crisis and the effective means of reducing environmental pollution, solar photo v oltaic cell array's power generation has relation with the incidence angle of sunlight, the generation is the largest when ray using light automatic tracking mode to make solar battery always perpendicular to sunlight, this method can greatly enhance the capacity of solar array, reduce the overall cost of PV power generation, create high economic efficiency, meet the request of setting up the environmental protection economy energy type social, has the theory research meaning and application prospect of promotion.REFERENCESX.K.Li. "Photovoltaic power development and policy analysis", Sun[2] F. Yang and P. Wang. "Design of controller for full automatic tracking solar", Foreign electronic components, volA, pp. 4-6, 2007. [3] J. L. Li and S. B. Zhou. "Design of a new kind of solar photovoltaic power tracking system", Electrical applications, vo1.28, pp.68-71, 2009. [4]P. C. Yu and Y. F. Chen. "A FPPY power system based on intelligent sun tracking with low power cost", Measurement and control technology, vo1.27, pp.36-39, 2008.[5] X. H. Wang. "Design and research of multiple plane mirror condensation solar tracking system", Hefei, Hefei university, 2007.[6]B. X. Zhang. "Research of solar energy utilization tracking and gather system", Hefei, Hefei university, 2006.。
太阳能相关英文文献翻译

Solar Tracker for Solar Water Heater AbstractThe Solar Tracker team was formed in the fall of 2005 from five students in an ME design team, and a Smart House liaison. We continued the work of a previous solar tracker group. The task was to design a prototype tracking device to align solar panels optimally to the sun as it moves over the course of the day. The implementation of such a system dramatically increases the efficiency of solar panels used to power the Smart House. This report examines the process of designing and constructing the prototype, the experiences and problems encountered, and suggestions for continuing the project. 1.IntroductionSolar tracking is the process of varying the angle of solar panels and collectors to take advantage of the full amount of the sun’s energy. This is done by rotating panels to be perpendicular to the sun’s angle of incidence. Initial tests in industry suggest that this process can increase the efficiency of a solar power system by up to 50%. Given those gains, it is an attractive way to enhance an existing solar power system. The goal is to build a rig that will accomplish the solar tracking and realize the maximum increase in efficiency. The ultimate goal is that the project will be cost effective – that is, the gains received by increased efficiency will more than offset the one time cost of developing the rig over time. In addition to the functional goals, the Smart House set forth the other following goals for our project: it must not draw external power (self-sustaining), it must be aesthetically pleasing, and it must be weatherproof.The design of our solar tracker consists of three components: the frame, the sensor, and the drive system. Each was carefully reviewed and tested, instituting changes and improvements along the design process. The frame forthe tracker is an aluminum prismatic frame supplied by the previous solar tracking group. It utilizes an ‘A-frame’ design with the rotating axle in the middle. Attached to the bottom of this square channel axle is the platform which will house the main solar collecting panels. The frame itself is at an angle to direct the panels toward the sun (along with the inclination of the roof). Its rotation tracks the sun from east to west during the day.The sensor design for the system uses two small solar panels that lie on the same plane as the collecting panels. These sensor panels have mirrors vertically attached between them so that, unless the mirror faces do not receive any sun, they are shading one of the panels, while the other is receiving full sunlight. Our sensor relies on this difference in light, which results in a large impedance difference across the panels, to drive the motor in the proper direction until again, the mirrors are not seeing any sunlight, at which point both solar panels on the sensor receive equal sunlight and no power difference is seen.After evaluation of the previous direct drive system for the tracker, we designed a belt system that would be easier to maintain in the case of a failure. On one end of the frame is a motor that has the drive pulley attached to its output shaft. The motor rotates the drive belt which then rotates the pulley on the axle. This system is simple and easily disassembled. It is easy to interchange motors as needed for further testing and also allows for optimization of the final gear ratio for response of the tracker.As with any design process there were several setbacks to our progress. The first and foremost was inclement weather which denied us of valuable testing time. Despite the setbacks, we believe this design and prototype to be a very valuable proof-of-principle. During our testing we have eliminated many of the repetitive problems with the motorand wiring so that future work on the project will go more smoothly. We also have achieved our goal of tracking the sun in a ‘hands-off’demo. We were able to have the tracker rotate under its own power to the angle of the sun and stop without any assistance. This was the main goal set forth to us by the Smart House so we believe our sensed motion prototype for solar tracking will be the foundation as they move forward in the future development and implementation of this technology to the house.2. Defining the ProblemThe project was to complete the “REV 2” design phase of the solar tracker to be used on the Smart House. While the team was comprised of members from the ME160 senior design course, the customer for this project was to be the Smart House organization. Jeff Schwane, a representative from the Smart House, was our liaison and communicated to our group the direction Smart House leadership wished us to proceed.At our first meeting with Jeff and Tom Rose, the following needs were identified:1.Track the sun during the daye no external power source3.Weather proof4.Cost effective power gain5.Must look good6.Solar panel versatile i.e. can fit different types ofpanelsWith these needs in hand, we constructed a Quality Function Deployment chart. This chart can be found in Appendix A. The QFD showed the major areas of concern might have been: number of panels/size of panels, internal power requirements, motor torque required.At our first meeting we were also able to set up our goals for the semester. Having a working prototype capable oftracking the sun was to be the main goal for the end of the semester, but we soon found that in order to accomplish this, we would be forced to omit portions of the design criteria in hopes they would be worked out later. This would result in the optimization of platform space on the roof to be irrelevant, with our goal being to have one platform track. It also led to the assumption that our base would not need to be tested for stability or required to be fastened to the roof. With an idea of where we were to begin, from scratch with the possibility of using the frame from the “REV 1” design, and an idea of where we were to finish, with a moving prototype, we constructed the Gantt chart that can be found in Appendix B. Our group planned to meet with Jeff once a week to make sure we were on track with the needs of the Smart House. Jeff would also meet with Tom Rose, the director of Smart House, at least once a week in order to keep everyone on the same page. With our goals in mind we embarked on the process of idea generation.3. Concepts and Research3.1 Tracking TypeOur group used a brainstorming approach to concept generation. We thought of ideas for different solar tracking devices, which proved difficult at times due to the existing frame and concept presented to us by Smart House. Other concepts were generated through research of pre-existing solar tracking devices. Originally our concept generation was geared towards creating a completely new solar tracker outside of the constraints of the previous structure given to us by Smart House. This initial brainstorming generated many concepts. The first one was a uni-axial tracking system that would track the sun east to west across the sky during the course of a day and return at the end of the day. This concept presented the advantage of simplicity and presented us with the option to use materials from the previous structure (whichwas also intended to be a uni-axial tracker) in construction. Another more complex concept was to track the sun bi-axially which would involve tracking the sun both east to west and throughout the seasons. The advantage of this concept was a more efficient harvesting of solar energy. The third concept was to only track throughout the seasons. This would provide small efficiency gains but nowhere near the gain provided by tracking east to west.The different structures we came up with to accomplish tracking motion included a rotating center axle with attached panels, hydraulic or motorized lifts which would move the main panel in the direction of the sun, and a robotic arm which would turn to face the sun. The clear efficiency gains coupled with the simplicity of design of the uni-axial tracking system and the existence of usable parts (i.e. motor and axle) for the rotating center axle structure, led us to the choice of the East to West tracking, rotating center axle concept.3.2 StructureOnce the method of motion was chosen, it was necessary to generate concepts for the structural support of the axle. Support could be provided by the triangular prismatic structure which was attempted by the previous Smart House solar tracker group or through the use of columns which would support the axis on either side. While the prismatic structure presented the advantage of mobility and an existing frame, the columns would have provided us with ease of construction, simple geometric considerations, and ease of prospective mounting on the roof. Due to the heightened intensity of time considerations, the previous financial commitment to the prismatic structure by Smart House, and our limited budget, the presence of the pre-existing frame proved to be the most important factor in deciding on a structure. Due to these factors we decided to work within the frame which was provided to us from the previous SolarTracker group.3.2 Tracking MotionOnce the structural support was finalized we needed to decide on a means to actualize this motion. We decided between sensed motion, which would sense the sun’s position and move to follow it, and continuous clock type motion, which would track the sun based on its pre-determined position in the sky. We chose the concept of continuous motion based on its perceived accuracy and the existence of known timing technology. During the evaluation stage, however, we realized that continuous motion would prove difficult. One reason was the inability to draw constant voltage and current from the solar panels necessary to sustain consistent motion, resulting in the necessity for sensing the rotation position to compensate. Continuous motion also required nearly constant power throughout the day, which would require a mechanism to store power. Aside from these considerations, the implementation of a timing circuit and location sensing device seemed daunting. After consulting Dr. Rhett George, we decided on a device using two panels and shading for sensed motion.4. Analysis and Embodiment4.1 Structure GeometryThe geometry of the frame was created in order to allow the solar panels to absorb light efficiently. This was done by allowing rotation in the east-west direction for tracking the sun daily and a 36° inclination (Durham’s latitude) towards the south. Because this frame was designed to be placed on a roof with a slope of 25°, the actual incline of the frame was made to be 11°.The geometry of the existing platform structure was modified. This was done in order to incorporate the results from the Clear Day Model supplied to us by Dr. Knight. This model led to the conclusion that the platform should track toup to 60°in both directions of horizontal. Thus, the angle range of the frame had to be increased. The sides of the frame were brought in to increase the allowable angle of rotation, and they were brought in proportionally to maintain the inclination angle of 11°. Also, crosspieces were moved to the inside of the frame to allow greater rotation of the platform before it came into contact with the support structure.The panels used for sensing and powering rotation were placed on the plane of the platform. Mirrors were placed perpendicular to and in between the panels to shade one and amplify the other in order to produce a difference to power the motor. The sensing panels were placed outside the platform area to maintain the largest area possible for collecting panels. A third sensing panel was mounted nearly vertical and facing east to aid rotation back towards the sun in the morning. This panel was attached to the frame under the platform, so that during most of the day, it’s shaded with minimal effects on sensed rotation.Minimizing the torques on the motor was a main concern in order to minimize the motor power needed. The platform designed for the placement of the collecting solar panels was placed under the rotational shaft so that the panels would be aligned with it the rotational axis. Since the main panels comprise the majority of the weight putting these in the plane of the rotational axis reduces torque on the shaft. The sensing panels were placed symmetrically about the axis of rotation in order to prevent additional torque on the motor. The third panel was attached to the frame instead of the platform or rotational shaft so as to also avoid any torque.4.2 MaterialsMaterials selection for most of the frame was simple because it had already been constructed. The mirrors used for the amplification and shading of the sensing panels were also already purchased and available for use. Additional parts forattachment of the panels and mirrors to the frame were taken from the scrap pieces available in the machine shop. In our selection of sensing panels, size and power needed to be balanced effectively. The panels were to be as small as possible in order to add minimal stress and weight to the frame but also needed to be powerful enough to power the rotation of the platform. Therefore, the most powerful of the intermediate sized panels available were selected. The panels purchased also appeared to be the most reliable of our options.4.3 Drive MechanismAfter designing a prototype and testing it, the motor purchased and used by the previous solar tracker group was slipping. It was removed, and the installation of a gear system with another simple motor was suggested and attempted. Professor Knight supplied some gears as well as some belts and pulleys. One end of the shaft was lathed so that one of the pulleys could be set on it, and spacers were bought so that a 6V motor we had available could power another pulley. These pulleys were to be connected by a belt. This motor demonstrated insufficient strength to turn the rotational shaft. The original motor, once detached, was taken apart and examined. Itappeared to be working again so a new pulley was purchased to fit it and was attached in the place of the 6V motor.5. Detailed Design5.1 FrameThe frame was designed from one inch square aluminum tubing, and a five foot long, two inch square tube for the axle. It is constructed with a rigid base and triangular prismatic frame with side supporting bars that provide stability. The end of the axle is attached to a system of pulleys which are driven by the motor. It is easily transported by removing the sides of the base and folding the structure.5.2 SensorOur sensing panels are bolted to the bottom of the main solar panel frame and braced underneath with half inch L-brackets. The mirrors are attached to the inside of the sensing panels and braced by L-brackets as well. The whole structure attaches easily to the main panel frame which is attached to the main axle using four 2-inch U-bolts. A third panel is bolted to the structure to return the main panels direction towards the horizon of sunrise.5.3 How the Sensor WorksOur sensor creates movement of the motor by shading one of the panels and amplifying the other when the system is not directly facing the sun. The two sensing panels are mounted parallel to the main panels symmetrically about the center axle with two mirrors in between them. The shading on one of the panels creates high impedance, while the amplified panel powers the motor. This happens until the panels receive the same amount of sunlight and balance each other out (i.e. when the sensing panels and main panels are facing the sun.). We initially attempted using a series configuration to take advantage of the voltage difference when one of the panels was shaded (Appendix C). This difference, however, was not large enough to drive the motor. We subsequently attempted a parallel configuration which would take advantage of the impedance of the shaded panel (Appendix C) and provide the current needed to drive the motor. Once the sensing mechanism has rotated from sunrise to sunset, the third panel, which is usually shaded, uses sunlight from the sunrise of the next day to power the motor to return the panels towards the direction of the sun.6. Prototype TestingInitial testing was done using just the sensing component and a 6V motor. The panels were tilted by hand to create shading and amplification. A series configuration of the sensing panels was initially tested and proved ineffective. Dataacquisition showed a maximum of a 2V difference across the motor, which was insufficient to power it. Upon testing the panels individually, it was discovered that the open voltage across each individual panel would only vary between 21.5V and 19.5V when fully amplified and fully shaded, respectively. The current running through each panel, however, was seen to fluctuate between nearly 0 amps when shaded, up to 0.65 amps when fully amplified. Therefore, in order to take advantage of the increase in impedance of the solar panels due to shading, we chose to put our sensing panels in parallel with each other and the motor. Tests with this configuration turned the motor in one direction, stopped when the sensing panels were nearly perpendicular to the sun, and reversed direction as the panels rotated past perpendicular. We found the angle range necessary to stop the motor to be very small. It was also observed that the panels rotated to slightly past perpendicular when they ceased motion. This error may be due to a difference in the innate resistance in each individual sensing panel. When tested it was found that one panel had a resistance of 52 kΩ, and the other panel resistance was 53 kΩ. Other testing found the voltage and current provided by the sensing solar panels to the motor to be consistent at all points, excluding when the solar panels are directly facing the sun. Through testing it was concluded that resistance may need to be added to one of the panels to compensate for the differences in the internal resistances of the individual panels, and a voltage regulator needs to be added to decrease the voltage seen across the motor. The original motor was prone to failure as its slippage caused the breakdown of our initial prototype after testing. This led to the institution of the pulley and belt driven system which would allow for easier maintenance given motor failure or slippage. The success of our initial testing and prototype proved to us the efficacy of our solar tracker design.7. ConclusionThroughout this project we enlisted the support of multiple resources (i.e. ME and EE professors, previous Smart House teams). We learned early on that a clear problem definition was essential to efficient design and progress. We struggled initially as we tried to design a tracking device that was different from the previous solar tracker group’s attempt, without fully weighing the size of their investment and the advantages of using the existing frame for our purposes. As we worked with the fixed frame construction from the previous group we learned that variability of design is key, especially when in the initial phases of prototyping. After many setbacks in testing of the solar panels, we learned that when working with solar panels, much time needs to be set aside for testing due to the unpredictability of the weather.The actual implementation of using the prototype in its intended location on the Smart House roof requires weather-proofing to protect the wiring and electrical connections from the elements, housing for the motor, a bracing system to attach the structure to the roof, and possible redesign to eliminate excess height and simplify overall geometry. The efficiency of the sensor system could be improved by widening the mirrors or by placing blinders along the sides of the panels to decrease the effects of reflected and refracted light incident on the shaded sensing panel.适用于太阳能热水器的太阳能跟踪器摘要太阳能跟踪器设计团队成立于2005年秋季,设计团队由五名队员组成,我们还负责与智能家居的联络工作。
自动化太阳能发电系统英文文献翻译

在混合光伏阵列中采用滑模技术的电源控制发电系统
摘要
变结构控制器来调节输出功率的一个独立的混合发电系统。 该系统包括光伏 发电和风力发电, 存储电池组和一个变量的单相负载。控制律承认两种操作模式 。 第一条用在当日晒度足够满足对电力的需求的情况下。第二运作模式应用在 日晒度不足的时候。后者致使系统在最大功率操作点(MPOP)操作下存储尽可能 多的能量。根据IncCond算法开发的一种新方法。滑模控制用于技术设计的控制 律。这些技术提供了一个简单的控制律设计框架,并有助于它们自带的鲁棒性。 最后,指导方针根据考虑为实际系统的设计。
1引言
可再生能源, 如风力和太阳能被认为是非常前途的能源。它们拥有可以满足 不断增加的世界能源需求的特点。另一方面,他们是基于无公害转换流程,它们 需要的主要资源是取之不尽,用之不竭,并且免费的。对于远程、远离电网的地 方,它往往是比用输电线路[1] 提供一个独立的电力来源拥有可行性。在这些电 网中, 在混合动力系统结合模块的基础上, 可再生能源发电以柴油为动力的备用 发电机已考虑ERED等效为一个可行的选择[2, 3]。然而,柴油发电机在孤立的燃 料供应和其运作领域是相当麻烦,相比较可再生能源,显得不划算[4]。为了取 代柴油备用发电机,独立的混合动力系统经常采用结合可再生能源来源的TARY 型材,如风力和光伏发电,合适的存储设备,如电池。自存储成本仍然是一个重 大的经济约束,通常光伏/风能/电池系统是用“适当”的大小以减少资本成本。 本文提出了一种控制策略,以规范的混合动力系统,包括光伏发电和风力 发电,蓄电池组和可变负载的输出功率作为研究。控制可调整的光伏发电、风力 发电, 以满足负载和电池充电的电源要求。系统以在独立控制下的最大发电的主 要目标。该控制器的设计开发,在之前的文献[5]中提过。因此,根据不同的大 气条件,不同的光伏阵列控制律使用的范围不同。第一条用在暴晒的地方,运作 模式足以提供的总功率需求,和风力发电一起适用。另一条控制律是在曝晒度不 足情况下跟踪最大功率操作点(MPOP),使系统保持尽可能多的储存的能量。 跟踪MPOP的方法是一个新的扩展版本下的IncCond算法[6]。 对于这两种操作模式设计控制律均使用滑模方法。这种技术很有吸引力,它 简化了设计任务,并使控制器具有鲁棒性。此外,根据第二次的运作模式,这种 技术提供的MPOP收敛速度最快。
太阳能跟踪系统毕业论文外文翻译
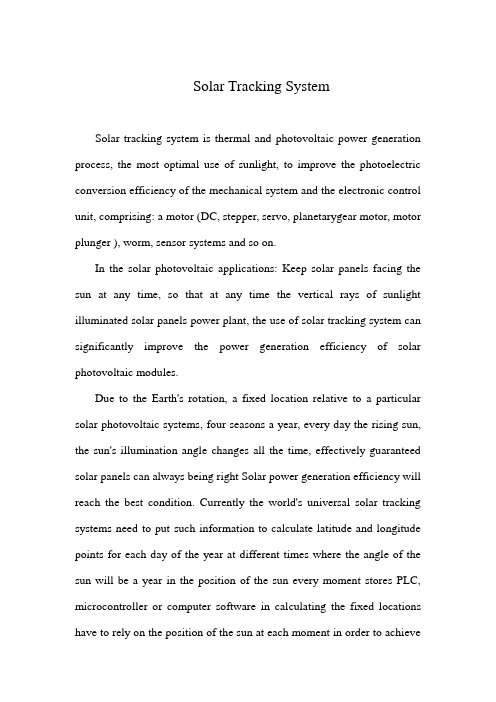
Solar Tracking SystemSolar tracking system is thermal and photovoltaic power generation process, the most optimal use of sunlight, to improve the photoelectric conversion efficiency of the mechanical system and the electronic control unit, comprising: a motor (DC, stepper, servo, planetarygear motor, motor plunger ), worm, sensor systems and so on.In the solar photovoltaic applications: Keep solar panels facing the sun at any time, so that at any time the vertical rays of sunlight illuminated solar panels power plant, the use of solar tracking system can significantly improve the power generation efficiency of solar photovoltaic modules.Due to the Earth's rotation, a fixed location relative to a particular solar photovoltaic systems, four seasons a year, every day the rising sun, the sun's illumination angle changes all the time, effectively guaranteed solar panels can always being right Solar power generation efficiency will reach the best condition. Currently the world's universal solar tracking systems need to put such information to calculate latitude and longitude points for each day of the year at different times where the angle of the sun will be a year in the position of the sun every moment stores PLC, microcontroller or computer software in calculating the fixed locations have to rely on the position of the sun at each moment in order to achievetracking. Uses the theory of computer data, needs to Earth coordinates regional data and settings, once installed, it inconvenient to move or dismantle, finished on each move must be recalculated parameter setting data and adjust various parameters; principle, circuit, technology, equipment is very complexMiscellaneous, non-professionals can not easily operate. Hebei, a solar photovoltaic power generation companies exclusively developed with world-leading level, do not calculate the position of the sun around the data, free software, not afraid cloudy, thunderstorms, cloudy and other inclement weather, has been the default system device saver, dustproof effect strong wind resistance, easy to use, low cost, anytime, anywhere on your mobile device can accurately track the sun's intelligent solar tracking system. The solar tracking system in the company's first-generation tracker technology based on integrated use of a variety of environments around the situation, the solar tracking system was fully upgraded and improved, so that the solar tracking system has become all-weather, full-featured, Super energy saving, intelligent solar tracking system. The solar tracking system has a normal (good weather conditions) under the Japanese track status and harsh climatic conditions and the state of the system of self-protection equipment to protect themselves from the normal state automatically and quickly converted to the Japanese track three cases.Adds a GPS positioning system, the solar tracking system is the first fully computer software without spatial orientation of the sun tracker, a leading international level, it is possible without geographical, weather conditions and external conditions, can be -50 ℃to 70 ℃ambient temperature range of normal use; tracking precision can reach ± 0.001 °, to maximize solar tracking accuracy, the perfect track to achieve timely and maximize solar energy utilization. The solar tracking system can be widely used in various types of equipment requires the use of solar tracking where the solar tracking system, affordable, stable performance, reasonable structure, precise tracking, easy to use. The installation of a solar tracking system solar power systems installed in high-speed car, train, and communications emergency vehicles, special military vehicles, warships or ships, and whether the system is running to where and how to turn around, turn the solar tracking system equipment requirements to ensure the site is tracking the sun! The solar tracking control technology with our own intellectual property rights belonging to national invention patent product, patent application number: 200610146201.8, has mass production.The solar tracking system has four operating state:1 Normal (good weather conditions) under the Japanese track status;2 intermittent tracking. If there is a period of time of day is cloudy or cloudy or inclement weather, the system will be screened out asunsuitable track, the entire system will be in a suspended state. Until light and track conditions are suitable, the system will be a fast-track instruction, so that roughly aligned with the sun tracker. , The program will conduct another set of signal acquisition and processing, complete the fine tracking;3 automatic back. Sunset, the system will automatically enter the sleep state, and automatically return to the position of the rising sun. The next day and then automatically enters a new round of running.4 inclement weather state protection: When the environment is not suitable for such factors as wind or precipitation system work, tracker will automatically stop working, and the whole big system receiving surface state and the ground plane parallel or vertical to prevent the system being to destruction.The solar tracking system main application areas:(1) a flat photovoltaic photovoltaic field and 500 times the CPV systems;(2) the field of solar thermal parabolic track (such as solar cookers, solar heating temperature, solar thermal and chemical);(3) solar trough collector;(4) solar thermal power tower and so on.太阳能跟踪系统太阳能跟踪系统是光热和光伏发电过程中,最优化太阳光使用,达到提高光电转换效率的机械及电控单元系统,包括:电机(直流、步进、伺服、行星减速电机、推杆电机等)、涡轮蜗杆、传感器系统等等。
太阳能光伏系统蓄电池充电毕业论文中英文资料对照外文翻译文献综述

中英文资料对照外文翻译文献综述Design of a Lead-Acid Battery Charging and Protecting IC in Photovoltaic System1.IntroductionSolar energy as an inexhaustible, inexhaustible source of energy more and more attention. Solar power has become popular in many countries and regions, solar lighting has also been put into use in many cities in China. As a key part of the solar lighting, battery charging and protection is particularly important. Sealed maintenance-free lead-acid battery has a sealed, leak-free, pollution-free, maintenance-free, low-cost, reliable power supply during the entire life of the battery voltage is stable and no maintenance, the need for uninterrupted for the various types of has wide application in power electronic equipment, and portable instrumentation. Appropriate float voltage, in normal use (to prevent over-discharge, overcharge, over-current), maintenance-free lead-acid battery float life of up to 12 ~ 16 years float voltage deviation of 5% shorten the life of 1/2. Thus, the charge has a major impact on this type of battery life. Photovoltaic, battery does not need regular maintenance, the correct charge and reasonable protection, can effectively extend battery life. Charging and protection IC is the separation of the occupied area and the peripheral circuit complexity. Currently, the market has not yet real, charged with the protection function is integrated on a single chip. For this problem, design a set of battery charging and protection functions in one IC is very necessary.2.System design and considerationsThe system mainly includes two parts: the battery charger module and the protection module. Of great significance for the battery as standby power use of the occasion, It can ensure that the external power supply to the battery-powered, but also in the battery overcharge, over-current and an external power supply is disconnected the battery is to put the state to provide protection, the charge and protection rolled into one to make the circuit to simplify and reduce valuable product waste of resources. Figure 1 is a specific application of this Ic in the photovoltaic powergeneration system, but also the source of this design.Figure1 Photovoltaic circuit system block diagramMaintenance-free lead-acid battery life is usually the cycle life and float life factors affecting the life of the battery charge rate, discharge rate, and float voltage. Some manufacturers said that if the overcharge protection circuit, the charging rate can be achieved even more than 2C (C is the rated capacity of the battery), battery manufacturers recommend charging rate of C/20 ~ C/3. Battery voltage and temperature, the temperature is increased by 1 °C, single cell battery voltage drops 4 mV , negative temperature coefficient of -4 mV / ° C means that the battery float voltage. Ordinary charger for the best working condition at 25 °C; charge less than the ambient temperature of 0 °C; at 45 °C may shorten the battery life due to severe overcharge. To make the battery to extend the working life, have a certain understanding and analysis of the working status of the battery, in order to achieve the purpose of protection of the battery. Battery, there are four states: normal state, over-current state over the state of charge, over discharge state. However, due to the impact of the different discharge current over-capacity and lifetime of the battery is not the same, so the battery over discharge current detection should be treated separately. When the battery is charging the state a long time, would severely reduce the capacity of the battery and shorten battery life. When the battery is the time of discharge status exceeds the allotted time, the battery, the battery voltage is too low may not be able to recharge, making the battery life is lower.Based on the above, the charge on the life of maintenance-free lead-acid batteries have a significant impact, while the battery is always in good working condition, battery protection circuit must be able to detect the normal working condition of the battery and make the action the battery can never normal working state back to normal operation, in order to achieve the protection of the battery.3.Units modular design3.1The charging module Chip, charging module block diagram shown in Figure 2. The circuitry includes solar battery array Charge controller controller Discharge controller DC load accumulatorcurrent limiting, current sensing comparator, reference voltage source, under-voltage detection circuit, voltage sampling circuit and logic control circuit.Figure2 Charging module block diagramThe module contains a stand-alone limiting amplifier and voltage control circuit, it can control off-chip drive, 20 ~30 mA, provided by the drive output current can directly drive an external series of adjustment tube, so as to adjust the charger output voltage and current . V oltage and current detection comparator detects the battery charge status, and control the state of the input signal of the logic circuit. When the battery voltage or current is too low, the charge to start the comparator control the charging. Appliances into the trickle charge state when the cut-off of the drive, the comparator can output about 20 mA into the trickle charge current. Thus, when the battery short-circuit or reverse, the charger can only charge a small current, to avoid damage to the battery charging current is too large. This module constitutes a charging circuit charging process is divided into two charging status: high-current constant-current charge state, high-voltage charge status and low-voltage constant voltage floating state. The charging process from the constant current charging status, the constant charging current of the charger output in this state. And the charger continuously monitors the voltage across the battery pack, the battery power has been restored to 70% to 90% of the released capacity when the battery voltage reaches the switching voltage to charge conversion voltage Vsam charger moves to the state of charge. In this state, the charger output voltage is increased to overcharge pressure driverV oltage amplifierV oltage sampling comparatorStart amplifier State level control Charging indicator Logical module Undervoltage detection circuit R- powerCurrent sampling comparator Limiting amplifier Power indicatorV oc is due to the charger output voltage remains constant, so the charging current is a continuous decline. Current down to charge and suspend the current Ioct, the battery capacity has reached 100% of rated capacity, the charger output voltage drops to a lower float voltage VF.3.2 Protection ModuleChip block diagram of the internal protection circuit shown in Figure 3. The circuit includes control logic circuit, sampling circuit, overcharge detection circuit, over-discharge detection comparator, overcurrent detection comparator, load short-circuit detection circuit, level-shifting circuit and reference circuit (BGR).Figure3 Block diagram of battery protectionThis module constitutes a protection circuit shown in Figure 4. Under the chip supply voltage within the normal scope of work, and the VM pin voltage at the overcurrent detection voltage, the battery is in normal operation, the charge and discharge control of the chip high power end of the CO and DO are level, when the chip is in normal working mode. Larger when the battery discharge current will cause voltage rise of the VM pin at the VM pin voltage at above the current detection voltage Viov, then the battery is the current status, if this state to maintain the tiov overcurrent delay time, the chip ban on battery discharge, then the charge to control the end of CO is high, the discharge control side DO is low, the chip is in the current mode, general in order to play on the battery safer and more reasonable protection, the chip will battery over-discharge current to take over the discharge current delay time protection. The general rule is that the over-discharge current is larger, over the Sampling circuitOver discharge detection comparator Control logic circuitLevel conversion circuit Overcharge detection comparator Over-current detection comparator2 Over-current detection comparator1Over-current detection circuitLoad short detection circuitshorter the discharge current delay time. Above Overcharge detection voltage, the chip supply voltage (Vdd> Vcu), the battery is in overcharge state, this state is to maintain the corresponding overcharge delay time tcu chip will be prohibited from charging the battery, then discharge control end DO is high, and charging control terminal CO is low, the chip is in charging mode. When the supply voltage of the chip under the overdischarge detection voltage (Vdd <Vdl,), then the battery is discharged state, this state remains the overdischarge delay time tdl chip will be prohibited to discharge the battery at this time The charge control side CO is high, while the discharge control terminal DO is low, the chip is in discharge mode.ProtectionmoduleFigure4 Protection circuit application schematic diagram4.Circuit DesignTwo charge protection module structure diagram, the circuit can be divided into four parts: the power detection circuit (under-voltage detection circuit), part of the bias circuit (sampling circuit, the reference circuit and bias circuit), the comparator (including the overcharge detection /overdischarge detection comparator, over-current detection and load short-circuit detection circuit) and the logic control part.This paper describes the under-voltage detection circuit (Figure 5), and gives the bandgap reference circuit (Figure 6).Figure5 Under-voltage detection circuitFigure6 A reference power supply circuit diagramBattery charging, voltage stability is particularly important, undervoltage, overvoltage protection is essential, therefore integrated overvoltage, undervoltage protection circuit inside the chip, to improve power supply reliability and security. And protection circuit design should be simple, practical, here designed a CMOS process, the undervoltage protection circuit, this simple circuit structure, process and easy to implement and can be used as high-voltage power integrated circuits and other power protection circuit.Undervoltage protection circuit schematic shown in Figure 5, a total of five components: the bias circuit, reference voltage, the voltage divider circuit, differential amplifier, the output circuit. The circuit supply voltage is 10V; the M0, M1, M2, R0 is the offset portion of the circuit to provide bias to the post-stage circuit, the resistance, Ro, determine the circuit's operating point, the M0, M1, M2 form a current mirror; R1 M14 is the feedback loop of the undervoltage signal; the rest of the M3, M4 and M5, M6, M7, M8, M9, M10, M11, M12, M13, M14, composed of four amplification comparator; M15, DO, a reference voltage, the comparator input with the inverting Biasing circuit Reference circuit Bleeder circuit difference amplifier Output circuitAmplifierAmplifierinput is fixed (V+), partial pressure of the resistance R1, R2, R3, the input to the inverting input of the comparator, when the normal working of the power supply voltage, the inverting terminal of the voltage detection is lost to the inverting terminal voltage of the comparator is greater than V+. Comparator output is low, M14 cutoff, feedback circuit does not work; undervoltage occurs, the voltage divider of R1, R2, R3, reaction is more sensitive, lost to the inverting input voltage is less than V when the resistor divider, the comparator the output voltage is high, this signal will be M14 open, the voltage across R into M at both ends of the saturation voltage close to 0V, thereby further driving down the R1> R2, the partial pressure of the output voltage, the formation of the undervoltage positive feedback. Output, undervoltage lockout, and plays a protective role.5. Simulation results and analysisThe design of the circuit in CSMC 0.6 μm in digital CMOS process simulation and analysis of the circuit. In the overall simulation of the circuit, the main observation is that the protection module on the battery charge and discharge process by monitoring Vdd potential and Vm potential leaving chip CO side and DO-side changes accordingly. The simulation waveform diagram shown in Figure 7, the overall protection module with the battery voltage changes from the usual mode conversion into overcharge mode, and then return to normal working mode, and then into the discharge mode, and finally back to normal working mode. As the design in the early stages of the various parameters to be optimized, but to provide a preliminary simulation results.Figure7 Overvoltage and under-voltage protection circuit simulation waveform6.ConclusionDesigned a set of battery charging and protection functions in one IC. This design not only can reduce the product, they can reduce the peripheral circuit components. The circuit uses the low-power design. This project is underway to design optimization stage, a complete simulation can not meet the requirements, but also need to optimize the design of each module circuit.光伏系统中蓄电池的充电保护IC电路设计1.引言太阳能作为一种取之不尽、用之不竭的能源越来越受到重视。
外文翻译_太阳跟踪系统

外文翻译_太阳跟踪系统毕业设计,论文,译文及原稿译文题目双轴太阳跟踪器的设计与实现光学传感器基于单电机的光伏系统原稿题目 Design and Implementation of a Sun Tracker with a Dual-AxisSingle Motor for an Optical Sensor-BasedPhotovoltaic System原稿出处 Department of Electrical Engineering双轴太阳跟踪器的设计与实现光学传感器基于单电机的光伏系统摘要:能源耗竭和全球气候变暖是地方发展的双重威胁,解决方法的公共利益中心是利用可再生的能源资源。
太阳能源是一种最有前途的可再生能源。
太阳跟踪器可以大幅度提高电力生产。
本文提出了一种新颖的利用的双轴太阳跟踪光伏系统的设计反馈控制理论以及四象限光电阻(LDR)传感器和简单的电子电路提供强健的系统性能。
拟议的系统采用独特的双轴交流电机和一个独立的光伏逆变器完成太阳能跟踪。
控制执行是一种简单而有效的技术创新设计。
此外构造了一个按比例缩小的实验室原型来验证该计划的可行性。
实验证实了太阳跟踪器的有效性。
最后,本研究结果可以作为未来太阳能应用的参考。
关键词:双轴太阳跟踪器;太阳能光伏板;反馈控制理论的光依赖电阻器;独立光伏逆变器;能量增益1、介绍随着人口和经济的发展,能源危机的问题的快速增加和全球变暖影响今天是一个令人日益感到关切。
可再生能源资源的利用是解决这些问题的关键。
太阳能是的主要来源之一清洁、丰富和取之不尽,用之不竭的能源,这不仅提供了可替代能源资源,但也提高了环境污染。
最直接的和技术上有吸引力地利用太阳能是通过光伏转换。
(也称为太阳能电池) 在 PV 电池的物理是非常类似于经典的 p — n结型二极管。
光伏电池将阳光直接转化为直流电 (DC) 电力由光伏效应 [1,2]。
光伏面板或模块是光伏电池封装互连的大会。
在为了最大限度地从太阳能电池板,一个需要保留小组在最佳的输出功率位置垂直于白天的太阳辐射。
太阳能发电-中英文翻译Solarelectricalenergygeneration文献翻译
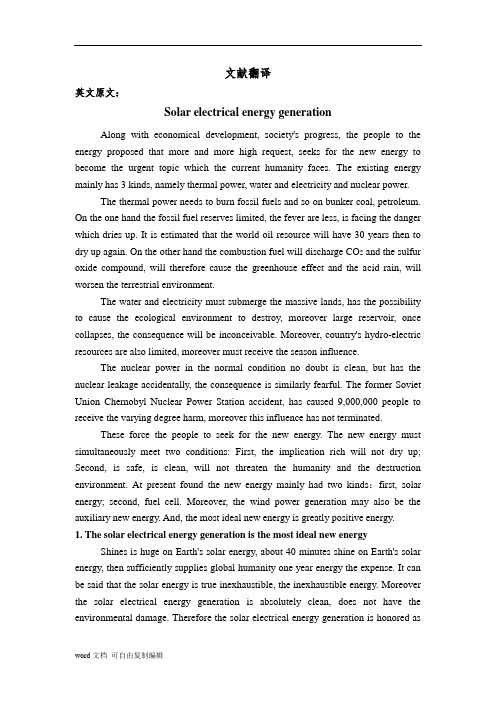
文献翻译英文原文:Solar electrical energy generationAlong with economical development, society's progress, the people to the energy proposed that more and more high request, seeks for the new energy to become the urgent topic which the current humanity faces. The existing energy mainly has 3 kinds, namely thermal power, water and electricity and nuclear power.The thermal power needs to burn fossil fuels and so on bunker coal, petroleum. On the one hand the fossil fuel reserves limited, the fever are less, is facing the danger which dries up. It is estimated that the world oil resource will have 30 years then to dry up again. On the other hand the combustion fuel will discharge CO2 and the sulfur oxide compound, will therefore cause the greenhouse effect and the acid rain, will worsen the terrestrial environment.The water and electricity must submerge the massive lands, has the possibility to cause the ecological environment to destroy, moreover large reservoir, once collapses, the consequence will be inconceivable. Moreover, country's hydro-electric resources are also limited, moreover must receive the season influence.The nuclear power in the normal condition no doubt is clean, but has the nuclear leakage accidentally, the consequence is similarly fearful. The former Soviet Union Chernobyl Nuclear Power Station accident, has caused 9,000,000 people to receive the varying degree harm, moreover this influence has not terminated.These force the people to seek for the new energy. The new energy must simultaneously meet two conditions: First, the implication rich will not dry up; Second, is safe, is clean, will not threaten the humanity and the destruction environment. At present found the new energy mainly had two kinds:first, solar energy; second, fuel cell. Moreover, the wind power generation may also be the auxiliary new energy. And, the most ideal new energy is greatly positive energy.1. The solar electrical energy generation is the most ideal new energyShines is huge on Earth's solar energy, about 40 minutes shine on Earth's solar energy, then sufficiently supplies global humanity one year energy the expense. It can be said that the solar energy is true inexhaustible, the inexhaustible energy. Moreover the solar electrical energy generation is absolutely clean, does not have the environmental damage. Therefore the solar electrical energy generation is honored asis the ideal energy.Obtains the electric power from the solar energy, must carry on the electro-optical transformation through the greatly positive battery to realize. It completely was formerly different with other power source electricity generation principle, has the following characteristic: ①Non-depletion danger; ②Clean (does not have environmental damage) absolutely; ③It is not distributed the resources the region the limit; ④But is using electricity place nearby generates electricity; ⑤The energy quality is high; ⑥The user easy to accept from the sentiment; ⑦The gain energy expenditure's time is short. The deficiency is:①The illumination energy distribution density is small, namely must take the huge area; ②Obtains the energy with four seasons, the day and nights and cloudy clear and so on meteorological conditions concerns. But generally speaking, the flaw does not cover the fine jade, takes the new energy, the solar energy has the enormous merit, therefore receives various countries the value.Must enable the solar electrical energy generation to achieve the practical level truly; first, must raise the solar energy electro-optic conversion efficiency and reduce its cost; second, must realize the solar electrical energy generation with present's electrical network networking.At present, solar panels mainly has the mono-crystalline silicon, the polycrystalline silicon, the amorphous state silicon three kinds. The mono-crystalline silicon solar cell conversion efficiency is highest, has reached above 20%, but the price is also the most expensive. The amorphous state silicon solar cell conversion efficiency is lowest, but the price is the cheapest, from now on most will be hopeful uses in generally generating electricity will be this kind of battery. Once its big area module electro-optic conversion efficiency achieves 10%, each watt generating set price falls to 1-2 US dollars, then sufficiently compete with present's electricity generation way. It is estimated that at the end of this century it may achieve this level.Certainly, in the special use and the laboratory uses the solar cell efficiency must be much higher, if the US Boeing develops by the gallium arsenic semiconductor with the positive electricity place which too the stibium gallium semiconductor overlaps becomes, the electro-optic conversion efficiency may reach 36%, has caught up with the coal-burning electricity generation efficiency quickly. But because it is too expensive, at present can only be restricted on the satellite uses.2. Solar electrical energy generation applicationAlthough solar electrical energy generation day and nights, clear and rain, season influence, but may carry on scattered, therefore it is suitable for various each household minute to carry on the electricity generation severally, moreover must join in the power supply network, causes each family when the electric power is wealthy may sold it to the Electricity company, when the insufficiency be possible from the Electricity company to buy up. Realizes this point’s technology not to be difficult to solve, the key lies in must have the corresponding legal safeguard. Now the US, Japan and so on developed country has made the corresponding law, guaranteed that carries on the solar electrical energy generation the family benefit, encourages the family to carry on the solar electrical energy generation.Japan has realized the solar electrical energy generation system the same electricity company electrical network's networking in April, 1992, had some families to start to install the solar electrical energy generation equipment. The Japanese Ministry of International Trade and Industry started from 1994 take individual housing as an object, implemented to purchases the solar electrical energy generation equipment's expense to subsidize 2/3 systems. Requests the first year had 1000 households families, when 2000 to have 70,000 households families to install the solar electrical energy generation equipment.According to the Japanese Department concerned estimates in the Japanese 21,000,000 households individual housing, if has 80% to install the solar electrical energy generation equipment, then may satisfy 14% which the national total power needs, if units and so on factory and office building also carry on the solar electrical energy generation with the room, then the solar electrical energy generation will occupy the national electric power 30%-40%. The current hindrance solar electrical energy generation popular most primary factor is the expense is expensive In order to satisfy the general family power requirement 3 kilowatt generating system, needs 6,000,000 to 7,000,000 Japanese Yen, has not included the installment wages. The concerned expert believed that when must fall at least to 1,000,000 to 2,000,000 Japanese Yen, the solar electrical energy generation only then can popularize truly. The key to reduce the expense lie in the solar cell to raise the conversion efficiency and to reduce the cost.Some time ago, the US Texas Instruments Company and SCE Corporation announced that they develop one kind of new solar cell, each unit is the diameter less than 1 millimeter bead, they distribute regularly densely and numerously on the softaluminum foil, looks like many silkworm eggs to cling on the paper is the same. Then distributes in about 50 square centimeters area has 1,700 such units. This kind of new battery's characteristic is, although the conversion efficiency has 8%-10%, but the price is cheap. Moreover aluminum foil bottom bush soft solid, may look like the cloth to fold equally at will, and durable, hangs in toward the sun place then may generate electricity, is convenient. It is said that uses this kind of new solar cell, so long as each watt power capacity equipment 1.5 to 2 US dollars, moreover each round of once electricity's expense might also fall to 14 cents about, definitely may compete with the ordinary power plant. Each family hangs this kind of battery on the roof, the wall toward the sun, every year may obtain 1,000-2,000 degrees electric powers.3. Solar electrical energy generation prospectThe solar electrical energy generation has a more exciting plan. First, Japan proposes creates the century plan. Prepares the desert and the sea area carries on the electricity generation using the ground, and through superconducting cable whole world solar power station connection unification electrical network in order to global. According to reckoning, to 2000, in 2050, in 2100, even if all uses the solar electrical energy generation supplies the whole world energy, the occupying land area is also 651,100 square kilometer, 1,867,900 square kilometer, 8,291,900 square kilometers. 8,291,900 square kilometers only occupy the complete sea area 2.3% or the complete desert area 51.4%, even is the Sahara area 91.5%. Therefore this plan has the possibility to realize.Another one is the space electricity generation plan. As early as in 1980 the NASA and Department of Energy proposed that in the spatial construction solar power station tentative plan, prepares on the synchronous orbit to put one long 10 kilometers, to extend 5 kilometer big plates, above covers entirely the solar cell, like this then may provide 5,000,000 kilowatts electric powers. But this needs to solve to the ground wireless electric transmission question. Already proposed with the micro wave beam, the laser beam and so on each kind of plan. At present although has realized the short distance, the short time, the low power microwave wireless electric transmission with the mockup, but to true practical also has the long distance.Along with our country technology's development, in 2006, China had three enterprises to enter global first ten, symbolizes that China will become one of global new energy science and technology central, in the world the solar energy light bends down widespread application, what caused present to be deficient was raw materialsupply and the price rise, we needed dissemination of technology at the same time, to use the new technology, with the aim of reducing the cost large scale, was this new energy long-term development provides the driving force!The solar energy use mainly divides into several aspects: The family with the small solar energy power plant, the large-scale incorporation power plant, the building integration light bends down the glass curtain wall, the solar energy street light, the scenery supplementary street light, the scenery supplementary power supply system and so on, now main application way for construction integration and scenery supplementary system.The world present had the nearly 200 companies to produce the solar cell, but produces the plants mainly hand in the Japanese business.Recent years the South Korean Tri-star, LG expressed the positive participation's desire, China two sides across the Taiwan Strait are similarly very warm-hearted. It is reported that our country Taiwan in 2008 crystallizes the silicon solar cell productivity to reach 2.2GW, later will expand by every year 1GW productivity in the past and started to produce the thin film solar cell, this year will strengthen vigorously, Taiwan anticipated that “the solar cell great nation” emulated to Europe. in 2010 various countries and the area have above 1GW the productive plan solar cell manufacturer to have Japanese Sharp, German Q-Cells, Scho~Solar, turns 5 prestige RWE Solar, Chinese Suntech Power and so on 5 companies, above other 7 500MW productivity company.Recent years the world solar cell market advanced triumphantly, an excellence, but the rare financial storm brought the economic crisis, was similarly presses in solar cell market on dark clouds, the Major enterprise like Germany Q-Cells achievement declined accordingly, because pre-year the world too positive electricity market also the demand will be this year worn out, the petroleum price dropped, but the competitive power counter-promotion and so on disadvantage factor lowered But at the same time, the people also see the US. After the Obama comes on stage, soon applies the Green New Deal policy, may have 150,000,000,000 US dollar subsidy funds including the among them green energy program, Japan will also carry out the subsidy system to continue to popularize solar cell's application4. Solar cell electricity generation principle:The solar cell is pair of light has the response and can transform the energy of light the electric power the component. Many kinds of materials can produce the lightto bend down the effect, for example: Mono-crystalline silicon, polycrystalline silicon, amorphous silicon, gallium arsenic, selenium indium copper and so on. Their electricity generation principle basic same, presently take crystal as example description light electricity generation process. The P crystalline silicon may result in the N silicon after the doping phosphorus, forms the P-N knot.When light illumination solar cell surface, part of photons by silicon material absorption; The photon energy transfer has given the silicon atom, caused the electron to occur more moved, becomes the free electron to tie the both sides in P-N to gather has formed the potential difference, when exterior key-on, under this voltage's function, will have the electric current to wind through the exterior electric circuit to have certain output. This process's essence is: The photon energy transforms the electrical energy the process.5. Crystalline silicon solar cell's manufacture process:The silicon is on our star preserves one of most abundant quantity materials. Had discovered after the 19th century scientists crystalline silicon semiconductor characteristic, it changed all nearly, even humanity's thought. 20 century's ends, in our life everywhere obviously “silicon” the f orm and the function, the crystalline silicon solar cell is in the recent 15 years forms the industrial production to be quickest. The production process may divide into five steps approximately: a、depuration process.b、pulls good process.c、slice process.d、system battery process.e、and the seal process.6. Solar cell's application:In the 1960s, the scientists already applied the solar cells in the spatial technology-communication satellite power supply, on the century's end, in the human self-introspection's process, bends down unceasingly regarding the light generates electricity this kind so clean and the direct energy form already even more kind, not only in the spatial application, but also gives full play in the numerous domains.For example: The solar energy garden lamp, the solar electrical energy generation household with the system, the stockaded village power supply's independent system, the light bends down the water pump (potable water or irrigation), the correspondence power source, the petroleum oil pipeline cathodic protection, the fiber optic cable communications pumping station power source, in the seawater desalination system, the cities the guidepost, the highway guidepost and so on. Europe and America and so on advanced countries bend down the electricitygeneration the light to merge the city to use electricity the system and the remote border district nature village power supply system integrate the development direction. The solar cell and the building system's union already formed the industrial production tendency.参考译文:太阳能发电随着经济的发展、社会的进步,人们对能源提出越来越高的要求,寻找新能源成为当前人类面临的迫切课题。
- 1、下载文档前请自行甄别文档内容的完整性,平台不提供额外的编辑、内容补充、找答案等附加服务。
- 2、"仅部分预览"的文档,不可在线预览部分如存在完整性等问题,可反馈申请退款(可完整预览的文档不适用该条件!)。
- 3、如文档侵犯您的权益,请联系客服反馈,我们会尽快为您处理(人工客服工作时间:9:00-18:30)。
(文档含英文原文和中文翻译)中英文对照外文翻译英文原文Solar TrackerThe Solar Tracker team was formed in the fall of 2005 from five students in an ME design team, and a Smart House liaison. We continued the work of a previous solar tracker group. The task was to design a prototype tracking device to align solar panels optimally to the sun as it moves over the course of the day. The implementation of such a system dramatically increases the efficiency of solar panels used to power the Smart House. This report examines the process of designing and constructing the prototype, the experiences and problems encountered, and suggestions for continuing the project.1.IntroductionSolar tracking is the process of varying the angle of solar panels and collectors to take advantage of the full amount of the sun‟s energy. This is done by rotating panels to be perpendicular to the sun‟s angle of incidence. Initial tests in industry suggest that this process can increase the efficiency of a solar power system by up to 50%. Given those gains, it is an attractive way to enhance an existing solar power system. The goal is to build a rig that will accomplish the solar tracking and realize the maximum increase in efficiency. The ultimate goal is that the project will be cost effective – that is, the gains received by increased efficiency will more than offset the one time cost of developing the rig over time. In addition to the functional goals, the Smart House set forth the other following goals for our project: it must not draw external power (self-sustaining), it must be aesthetically pleasing, and it must be weatherproof.The design of our solar tracker consists of three components: the frame, the sensor, and the drive system. Each was carefully reviewed and tested, instituting changes and improvements along the design process. The frame for the tracker is an aluminum prismatic frame supplied by the previous solar tracking group. It utilizes an …A-frame‟ design with the rotating axle in the middle. Attached to the bottom of this square channel axle is the platform which will house the main solar collecting panels. The frame itself is at an angle to direct the panels toward the sun (along with the inclination of the roof). Its rotation tracks the sun from east to west during the day.The sensor design for the system uses two small solar panels that lie on the same plane as the collecting panels. These sensor panels have mirrors vertically attached between them so that, unless the mirror faces do not receive any sun, they are shading one of the panels, while the other is receiving full sunlight. Our sensor relies on this difference in light, which results in a large impedance difference across the panels, to drive the motor in the proper direction until again, the mirrors are not seeing any sunlight, at which point both solar panels on the sensor receive equal sunlight and no power difference is seen.After evaluation of the previous direct drive system for the tracker, we designed a belt system that would be easier to maintain in the case of a failure. On one end of the frame is a motor that has the drive pulley attached to its output shaft. The motor rotates the drive belt which then rotates the pulley on the axle. This system is simple and easily disassembled. It is easy tointerchange motors as needed for further testing and also allows for optimization of the final gear ratio for response of the tracker.As with any design process there were several setbacks to our progress. The first and foremost was inclement weather which denied us of valuable testing time. Despite the setbacks, we believe this design and prototype to be a very valuable proof-of-principle. During our testing we have eliminated many of the repetitive problems with the motor and wiring so that future work on the project will go more smoothly. We also have achieved our goal of tracking the sun in a …hands-off‟demo. We were able to have the tracker rotate under its own power to the angle of the sun and stop without any assistance. This was the main goal set forth to us by the Smart House so we believe our sensed motion prototype for solar tracking will be the foundation as they move forward in the future development and implementation of this technology to the house.2. Defining the ProblemT he project was to complete the “REV 2” design phase of the solar tracker to be used on the Smart House. While the team was comprised of members from the ME160 senior design course, the customer for this project was to be the Smart House organization. Jeff Schwane, a representative from the Smart House, was our liaison and communicated to our group the direction Smart House leadership wished us to proceed.At our first meeting with Jeff and Tom Rose, the following needs were identified:1.Track the sun during the daye no external power source3.Weather proof4.Cost effective power gain5.Must look good6.Solar panel versatile i.e. can fit different types of panelsWith these needs in hand, we constructed a Quality Function Deployment chart. This chart can be found in Appendix A. The QFD showed the major areas of concern might have been: number of panels/size of panels, internal power requirements, motor torque required.At our first meeting we were also able to set up our goals for the semester. Having a working prototype capable of tracking the sun was to be the main goal for the end of the semester, but we soon found that in order to accomplish this, we would be forced to omit portions of the design criteria in hopes they would be worked out later. This would result in the optimization of platform space on the roof to be irrelevant, with our goal being to have one platform track. It also led to the assumption that our base would not need to be tested for stability or required to be fastened to the roof. With an idea of where we were to begin, from scratch with the possibility of using the frame from the “REV 1” design, and an idea of where we were to finish, with a moving prototype, we constructed the Gantt chart that can be found in Appendix B. Our group planned to meet with Jeff once a week to make sure we were on track with the needs of the Smart House. Jeff would also meet with Tom Rose, the director of Smart House, at least once a week in order to keep everyone on the same page. With our goals in mind we embarked on the process of idea generation.3. Concepts and Research3.1 Tracking TypeOur group used a brainstorming approach to concept generation. We thought of ideas for different solar tracking devices, which proved difficult at times due to the existing frame and concept presented to us by Smart House. Other concepts were generated through research of pre-existing solar tracking devices. Originally our concept generation was geared towards creating a completely new solar tracker outside of the constraints of the previous structure given to us by Smart House. This initial brainstorming generated many concepts. The first one was a uni-axial tracking system that would track the sun east to west across the sky during the course of a day and return at the end of the day. This concept presented the advantage of simplicity and presented us with the option to use materials from the previous structure (which was also intended to be a uni-axial tracker) in construction. Another more complex concept was to track the sun bi-axially which would involve tracking the sun both east to west and throughout the seasons. The advantage of this concept was a more efficient harvesting of solar energy. The third concept was to only track throughout the seasons. This would provide small efficiency gains but nowhere near the gain provided by tracking east to west.The different structures we came up with to accomplish tracking motion included a rotating center axle with attached panels, hydraulic or motorized lifts which would move the main panel in the direction of the sun, and a robotic arm which would turn to face the sun. The clear efficiency gains coupled with the simplicity of design of the uni-axial tracking system and the existence of usable parts (i.e. motor and axle) for the rotating center axle structure, led us to the choice of the East to West tracking, rotating center axle concept.3.2 StructureOnce the method of motion was chosen, it was necessary to generate concepts for the structural support of the axle. Support could be provided by the triangular prismatic structure which was attempted by the previous Smart House solar tracker group or through the use of columns which would support the axis on either side. While the prismatic structure presented the advantage of mobility and an existing frame, the columns would have provided us with ease of construction, simple geometric considerations, and ease of prospective mounting on the roof. Due to the heightened intensity of time considerations, the previous financial commitment to the prismatic structure by Smart House, and our limited budget, the presence of the pre-existing frame proved to be the most important factor in deciding on a structure. Due to these factors we decided to work within the frame which was provided to us from the previous Solar Tracker group.3.2 Tracking MotionOnce the structural support was finalized we needed to decide on a means to actualize this motion. We decided between sensed motion, which would sense the sun‟s position and move t o follow it, and continuous clock type motion, which would track the sun based on its pre-determinedposition in the sky. We chose the concept of continuous motion based on its perceived accuracy and the existence of known timing technology. During the evaluation stage, however, we realized that continuous motion would prove difficult. One reason was the inability to draw constant voltage and current from the solar panels necessary to sustain consistent motion, resulting in the necessity for sensing the rotation position to compensate. Continuous motion also required nearly constant power throughout the day, which would require a mechanism to store power. Aside from these considerations, the implementation of a timing circuit and location sensing device seemed daunting. After consulting Dr. Rhett George, we decided on a device using two panels and shading for sensed motion.4. Analysis and Embodiment4.1 Structure GeometryThe geometry of the frame was created in order to allow the solar panels to absorb light efficiently. This was done by allowing rotation in the east-west direction for tracking the sun daily and a 36° inclination (Durham‟s latitude) towards the south. Because this frame was designed to be placed on a roof with a slope of 25°, the actual incline of the frame was made to be 11°.The geometry of the existing platform structure was modified. This was done in order to incorporate the results from the Clear Day Model supplied to us by Dr. Knight. This model led to the conclusion that the platform should track to up to 60° in both directions of horizontal. Thus, the angle range of the frame had to be increased. The sides of the frame were brought in to increase the allowable angle of rotation, and they were brought in proportionally to maintain the inclination angle of 11°. Also, crosspieces were moved to the inside of the frame to allow greater rotation of the platform before it came into contact with the support structure.The panels used for sensing and powering rotation were placed on the plane of the platform. Mirrors were placed perpendicular to and in between the panels to shade one and amplify the other in order to produce a difference to power the motor. The sensing panels were placed outside the platform area to maintain the largest area possible for collecting panels. A third sensing panel was mounted nearly vertical and facing east to aid rotation back towards the sun in the morning. This panel was attached to the frame under the platform, so that during most of the day, it‟s shaded with mi nimal effects on sensed rotation.Minimizing the torques on the motor was a main concern in order to minimize the motor power needed. The platform designed for the placement of the collecting solar panels was placed under the rotational shaft so that the panels would be aligned with it the rotational axis. Since the main panels comprise the majority of the weight putting these in the plane of the rotational axis reduces torque on the shaft. The sensing panels were placed symmetrically about the axis of rotation in order to preventadditional torque on the motor. The third panel was attached to the frame instead of the platform or rotational shaft so as to also avoid any torque.4.2 MaterialsMaterials selection for most of the frame was simple because it had already been constructed. The mirrors used for the amplification and shading of the sensing panels were also already purchased and available for use. Additional parts for attachment of the panels and mirrors to the frame were taken from the scrap pieces available in the machine shop. In our selection of sensing panels, size and power needed to be balanced effectively. The panels were to be as small as possible in order to add minimal stress and weight to the frame but also needed to be powerful enough to power the rotation of the platform. Therefore, the most powerful of the intermediate sized panels available were selected. The panels purchased also appeared to be the most reliable of our options.4.3 Drive MechanismAfter designing a prototype and testing it, the motor purchased and used by the previous solar tracker group was slipping. It was removed, and the installation of a gear system with another simple motor was suggested and attempted. Professor Knight supplied some gears as well as some belts and pulleys. One end of the shaft was lathed so that one of the pulleys could be set on it, and spacers were bought so that a 6V motor we had available could power another pulley. These pulleys were to be connected by a belt. This motor demonstrated insufficient strength to turn the rotational shaft. The original motor, once detached, was taken apart and examined. Itappeared to be working again so a new pulley was purchased to fit it and was attached in the place of the 6V motor.5. Detailed Design5.1 FrameThe frame was designed from one inch square aluminum tubing, and a five foot long, two inch square tube for the axle. It is constructed with a rigid base and triangular prismatic frame with side supporting bars that provide stability. The end of the axle is attached to a system of pulleys which are driven by the motor. It is easily transported by removing the sides of the base and folding the structure.5.2 SensorOur sensing panels are bolted to the bottom of the main solar panel frame and braced underneath with half inch L-brackets. The mirrors are attached to the inside of the sensing panels and braced by L-brackets as well. The whole structure attaches easily to the main panel frame which is attached to the main axle using four 2-inch U-bolts. A third panel is bolted to the structure to return the main panels direction towards the horizon of sunrise.5.3 How the Sensor WorksOur sensor creates movement of the motor by shading one of the panels and amplifying the other when the system is not directly facing the sun. The two sensing panels are mounted parallel to the main panels symmetrically about the center axle with two mirrors in between them. The shading on one of the panels creates high impedance, while the amplified panel powers the motor. This happens until the panels receive the same amount of sunlight and balance each other out (i.e. when the sensing panels and main panels are facing the sun.). We initially attempted using a series configuration to take advantage of the voltage difference when one of the panels was shaded (Appendix C). This difference, however, was not large enough to drive the motor. We subsequently attempted a parallel configuration which would take advantage of the impedance of the shaded panel (Appendix C) and provide the current needed to drive the motor. Once the sensing mechanism has rotated from sunrise to sunset, the third panel, which is usually shaded, uses sunlight from the sunrise of the next day to power the motor to return the panels towards the direction of the sun.6. Prototype TestingInitial testing was done using just the sensing component and a 6V motor. The panels were tilted by hand to create shading and amplification. A series configuration of the sensing panels was initially tested and proved ineffective. Data acquisition showed a maximum of a 2V difference across the motor, which was insufficient to power it. Upon testing the panels individually, it was discovered that the open voltage across each individual panel would only vary between 21.5V and 19.5V when fully amplified and fully shaded, respectively. The current running through each panel, however, was seen to fluctuate between nearly 0 amps when shaded, up to 0.65 amps when fully amplified. Therefore, in order to take advantage of the increase in impedance of the solar panels due to shading, we chose to put our sensing panels in parallel with each other and the motor. Tests with this configuration turned the motor in one direction, stopped when the sensing panels were nearly perpendicular to the sun, and reversed direction as the panels rotated past perpendicular. We found the angle range necessary to stop the motor to be very small. It was also observed that the panels rotated to slightly past perpendicular when they ceased motion. This error may be due to a difference in the innate resistance in each individual sensing panel. When tested it was found that one panel had a resistance of 52 kΩ, and the other panel resistance was 53 kΩ. Other testing found the voltage and current provided by the sensing solar panels to the motor to be consistent at all points, excluding when the solar panels are directly facing the sun. Through testing it was concluded that resistance may need to be added to one of the panels to compensate for the differences in the internal resistances of the individual panels, and a voltage regulator needs to be added to decrease the voltage seen across the motor. The original motor was prone to failure as its slippage caused the breakdown of our initial prototype after testing. This led to the institution of the pulley and belt driven system which would allow for easier maintenance givenmotor failure or slippage. The success of our initial testing and prototype proved to us the efficacy of our solar tracker design.7. ConclusionThroughout this project we enlisted the support of multiple resources (i.e. ME and EE professors, previous Smart House teams). We learned early on that a clear problem definition was essential to efficient design and progress. We struggled initially as we tried to design a tracking device that was different from the previous solar tracker group‟s attempt, without fully weighing the size of their investment and the advantages of using the existing frame for our purposes. As we worked with the fixed frame construction from the previous group we learned that variability of design is key, especially when in the initial phases of prototyping. After many setbacks in testing of the solar panels, we learned that when working with solar panels, much time needs to be set aside for testing due to the unpredictability of the weather.The actual implementation of using the prototype in its intended location on the Smart House roof requires weather-proofing to protect the wiring and electrical connections from the elements, housing for the motor, a bracing system to attach the structure to the roof, and possible redesign to eliminate excess height and simplify overall geometry. The efficiency of the sensor system could be improved by widening the mirrors or by placing blinders along the sides of the panels to decrease the effects of reflected and refracted light incident on the shaded sensing panel.中文译文太阳能跟踪器简介太阳能跟踪队成立于2005年秋季,设计团队由五名队员组成,我们还负责与智能家居的联络工作。