车工实训教学中梯形螺纹车削论文
梯形螺纹的数控车削加工

梯形螺纹的数控车削加工摘要:梯形螺纹的加工是数控车削的一个难点, 针对在数控车床加工梯形螺纹时容易出现扎刀等现象,本文介绍使用GSK980TDa系统的数控车床,运用调用子程序和编制宏程序两种编程方法,对梯形螺纹进行分层切削加工,较好的解决了加工过程中梯形螺纹车刀各切削刃的受力分配问题,有效避免了扎刀现象,为数控车削梯形螺纹提供一个实用的加工方法。
关键词:梯形螺纹;数控车削;宏程序;调用子程序;分层切削法一、前言梯形螺纹在传动中应用越来越广泛, 精度要求越来越高, 这就对梯形螺纹提出了高精度高效率的制造要求。
在车床上加工梯形螺纹是一项技术难度较高的工作, 梯形螺纹的车削在普通车床上应用比较广泛, 但要求工人要有比较熟练的操作技巧, 劳动强度大,螺纹加工的精度和效率受人为因素影响比较大,废品率较高。
数控车床稳定的高精度加工性能为梯形螺纹的车削提供了良好的加工基础, 但在数车上加工梯形螺纹编程与控制比较困难, 因此有人错误地认为数车不适合用来车削梯形螺纹, 实际上如果所编制的梯形螺纹加工程序工艺合理, 在数车上车削梯形螺纹也会取得很好的效果。
二、数控车加工梯形螺纹的难点1.数控车不能直接使用普通车床的梯形螺纹加工方法普通车床所使用的梯形螺纹加工方法如左右切削法、直槽法、阶梯槽法等都不能直接用于数控车。
因为数控车取消了普通车床上的机械传动链,通过装在主轴末端的同步传动带与主轴脉冲编码器连接,从而构成了主轴与大滑板传动丝杆之间的传动链。
主轴脉冲编码器在车螺纹时,同时输出两路信号:一路是按编程人员在加工程序中给定的主轴转速和螺距值,确定伺服电机的转速,保证主轴和伺服电机两种转速形成严格的传动比;另一路是控制彳轴的定位,保证螺纹车刀在多次循环切削过程中,车刀刀尖始终在螺旋槽内而不乱牙。
如果在加工过程中因出现扎刀或刀具损坏需要更换螺纹车刀而使数控车床停止旋转时,主轴脉冲编码器停止工作,上述两路信号停止输出,此时重新安装的螺纹车刀就很难准确地落在前一把螺纹车刀车出的螺旋槽内,从而加大对刀难度,甚至出现乱牙现象。
浅谈中职普车实习教学中的梯形螺纹加工

2012年·12月·下期学术·理论现代企业教育现代企业教育MODERN ENTERPRISE EDUCATION 浅谈中职普车实习教学中的梯形螺纹加工蒋金虎(淮阴区职教中心江苏淮安223300)摘要:在中等职业学校的普车教学中,车削梯形螺纹对于学生是一个难点,也是一个比较重要的课题,能否加工出一个合格的梯形螺纹能够反映一个人车工水平的高低。
分层车削法加工梯形螺纹对于中职学生来说是简单易懂,且安全有效的方法。
关键词:中职梯形螺纹分层在车工生产实习中,无论中级工和高级工都会学到梯形螺纹这些内容,梯形螺纹是应用很广泛的传动螺纹,它们的工作长度较长,使用精度要求较高,在车削梯形螺纹时,吃刀深,走刀快,切削力大,等因素决定了梯形螺纹的加工是一个难点。
凭借多年的车工专业技术及教学实践经验,笔者谈谈在车工实习教学指导中,如何使学生快速掌握车削梯形螺纹的方法。
在切削梯形螺纹前,一定要保证学生对三角螺纹的车削非常熟悉,知道螺纹的车削原理、思路及退刀、正反车的熟练操作。
一、传统车削方法的弊端传统的车削方法有左右切削法、车直槽法等,但车削过程中存在的弊端较多,且较为难懂,学生车削时容易因为操作方法或刀具质量较差,车床间隙等原因造成切削失败。
1.左右切削法。
在每次横向进给时,都必须把车刀向左或向右作微量移动,特别是小滑板空行程较大时,移动量不易掌握,车削很不方便,且只能用于螺纹的粗车。
2.车直槽法。
先用主切削刃宽度等于牙槽底宽的矩形螺纹车刀车出螺旋槽,使槽底直径等于梯形螺纹小径,然后用梯形螺纹精车刀精车牙型两侧。
由于梯形螺纹牙槽底宽较窄,车刀的刀头宽度很窄,刚性较差,特别是双线或多线梯形螺纹,螺纹升角大,左侧后角也大,致使刀头刚性和散热条件更差,车削过程中车刀容易磨损或造成打刀,给车削造成较大困难。
传统方法对于学生来说比较难懂,操作繁琐,综合机床本身间隙等客观原因则可能会导致车削失败,影响学生学习的积极性,造成实践教学效率的低下。
扎刀论文分层切削法论文:分层切削法车削梯形螺纹在数控车床中的应用

扎刀论文分层切削法论文:分层切削法车削梯形螺纹在数控车床中的应用[摘要] 本文对梯形螺纹加工时,采用分层切削法进刀的优越性进行了详细的分析,并就数控车床中应用分层切削法车削梯形螺纹时,编程指令的应用和宏程序编程方法进行了详细的阐述。
[关键词] 扎刀分层切削法三面切削宏程序前言梯形螺纹的螺距大、切入深,粗车中容易出现扎刀现象,而且,因切削力大、切削热高、刀具散热条件差,限制了切削速度,加工效率也不高。
因此,梯形螺纹的粗加工是车削加工中一个较难的课题。
分层切削法能有效的解决传统加工方法存在的不足,避免了因排屑不畅引起的扎刀现象和提高了加工功效;但在数控车床中应用分层切削法,编程繁琐、易出错。
本人通过在实践中不断尝试和探索,使用宏指令编程,实现了在数控车床中实施分层切削法车削梯形螺纹。
现将其方法阐述如下,以求得大家的指正与共识。
一、梯形螺纹传统的粗加工方法1.1 切直槽法此方法粗车时先用矩形螺纹车刀采用直进法车出螺旋直槽,然后用梯形螺纹精车刀车两侧。
如图2.1所示。
此方法在切螺旋直槽时,所用的刀具类似于切槽刀,而切槽刀本身就存在刀头强度差、排屑困难的缺陷;而且,由于在螺纹加工中螺纹升角的存在,螺纹旋向一侧的刃磨后角应等于工作后角加上螺纹升角(ψ)。
即α。
=(3~5)+ψ这样一来,刀头强度就更差了,在加工中极易出现扎刀现象,导致刀头折短、工件弯曲变形甚至报废。
要避免扎刀,只能减小吃刀深度,这样一来,进刀次数增多,而且,切完直槽后还要用梯形螺纹或蜗杆精车刀去除两侧余量,所以,加工效率很低。
图1.1 切直槽法1.2 左右切削法此方法在横向进刀时,同时进行左右少量进刀(又称赶刀),以避免三个切削刃同时参与切削,如图1.2.1a所示。
此方法加工时,既有横向进刀又有纵向赶刀,车刀对牙侧必须重复切削,切削面积较大(如图1.2.2b所示),因而,加工中切削力较大、切削热高、排屑困难。
加工时对纵向赶刀量不好控制,赶刀量太大,切削面积更大,会因切削力过大而扎刀;赶刀量太小,容易造成三面切削,此时切削面积最大(如图1.2.3c所示),而且排屑困难,更加容易扎刀。
浅谈梯形螺纹的车削

浅谈梯形螺纹的车削【摘要】梯形螺纹是应用十分广泛的螺纹,有米制和英制两种。
英制螺纹在我国采用较少,我国主要采用米制梯形螺纹。
本文就梯形螺纹车刀的选用、车刀的安装、工件的安装、车床的调整、车削方法的选用及螺纹的检测加以阐述如何又快又好的车削梯形螺纹。
【关键词】车削;梯形螺纹;方法车床上长丝杠和中、小滑板的丝杠都是梯形螺纹,他们的工作长度较长,传动中精度要求高,同时梯形螺纹牙型两侧面表面粗糙度值较小,致使梯形螺纹车削时,难度较大。
在车削中如果采用较大的吃刀深度,较快的走刀速度,在一定程度上可以提高梯形螺纹的车削速度,但对于初学者较难掌握。
在实际操作中容易造成扎刀,甚至刀头折断,从而使得初学着产生畏惧心理,使得初学者再次车削时不敢进刀,甚至不敢再次车削。
针对上述情况,在长期的教学中通过不断的教学实践,总结了一套切实有效的车削梯形螺纹的方法,现加以阐述。
1.梯形螺纹车刀的选用1.1粗车刀的选用为了提高梯形螺纹的加工效率,采用硬质合金梯形螺纹粗车刀(以车Tr50×6-7h螺纹为例)。
车刀的刀尖角应小于牙型角30°,取29°为宜。
刀尖宽度小于牙槽底宽,刀头宽度可刃磨为1.6mm左右。
为了增强刀头的刚性、耐磨性,可将梯形螺纹车刀刀头刃磨成圆弧形,并可适当的刃磨出前角,前角10°以内为宜,使切削更加顺畅。
在粗车螺纹时,由于受到螺纹螺旋线的影响,螺纹升角Ψ较大,其影响不可忽略,因此在刃磨梯形螺纹车刀时,必须考虑。
车削右旋螺纹时,左侧后角应为(3°-5°)+Ψ,右侧后角应为(3°-5°)-Ψ。
1.2精车刀的选用为了提高螺纹两侧面以及底面的表面粗糙度,梯形螺纹精车刀可选用高速钢梯形螺纹车刀。
螺纹车刀的径向前角为0°,两侧切削刃之间的夹角等于牙型角,刃磨成30°,同时两侧切削刃沿着刀柄轴线方向对称分布。
为了保证车削加工的顺畅,也可在两侧磨出较大前角(10°~15°)的卷屑槽,在车削时,车刀的前端不能参与切削,只能用于精车牙型两侧面。
基于普车加工梯形螺纹的方法研究
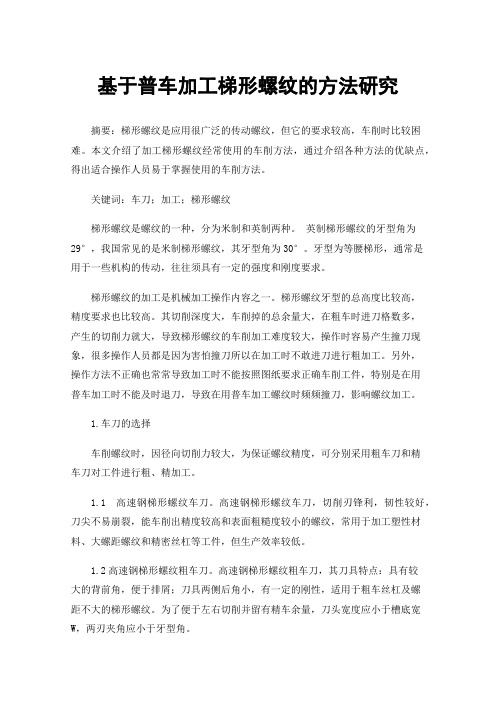
基于普车加工梯形螺纹的方法研究摘要:梯形螺纹是应用很广泛的传动螺纹,但它的要求较高,车削时比较困难。
本文介绍了加工梯形螺纹经常使用的车削方法,通过介绍各种方法的优缺点,得出适合操作人员易于掌握使用的车削方法。
关键词:车刀;加工;梯形螺纹梯形螺纹是螺纹的一种,分为米制和英制两种。
英制梯形螺纹的牙型角为29°,我国常见的是米制梯形螺纹,其牙型角为30°。
牙型为等腰梯形,通常是用于一些机构的传动,往往须具有一定的强度和刚度要求。
梯形螺纹的加工是机械加工操作内容之一。
梯形螺纹牙型的总高度比较高,精度要求也比较高。
其切削深度大,车削掉的总余量大,在粗车时进刀格数多,产生的切削力就大,导致梯形螺纹的车削加工难度较大,操作时容易产生撞刀现象,很多操作人员都是因为害怕撞刀所以在加工时不敢进刀进行粗加工。
另外,操作方法不正确也常常导致加工时不能按照图纸要求正确车削工件,特别是在用普车加工时不能及时退刀,导致在用普车加工螺纹时频频撞刀,影响螺纹加工。
1.车刀的选择车削螺纹时,因径向切削力较大,为保证螺纹精度,可分别采用粗车刀和精车刀对工件进行粗、精加工。
1.1 高速钢梯形螺纹车刀。
高速钢梯形螺纹车刀,切削刃锋利,韧性较好,刀尖不易崩裂,能车削出精度较高和表面粗糙度较小的螺纹,常用于加工塑性材料、大螺距螺纹和精密丝杠等工件,但生产效率较低。
1.2高速钢梯形螺纹粗车刀。
高速钢梯形螺纹粗车刀,其刀具特点:具有较大的背前角,便于排屑;刀具两侧后角小,有一定的刚性,适用于粗车丝杠及螺距不大的梯形螺纹。
为了便于左右切削并留有精车余量,刀头宽度应小于槽底宽W,两刃夹角应小于牙型角。
1.3高速钢梯形螺纹精车刀。
高速钢梯形螺纹精车刀车刀几何形状及刀具特点:车刀前面沿两侧切削刃磨有 R2~R3mm 的分屑槽,并磨有较大的前角、使切屑排出顺利。
车刀纵向前角γp=0°,两侧切削刃之间的夹角等于牙型角。
为了保证两测切削刃切削顺利,都磨有较大前角(γo=10°~20°)的卷屑槽。
螺纹加工论文车床加工论文
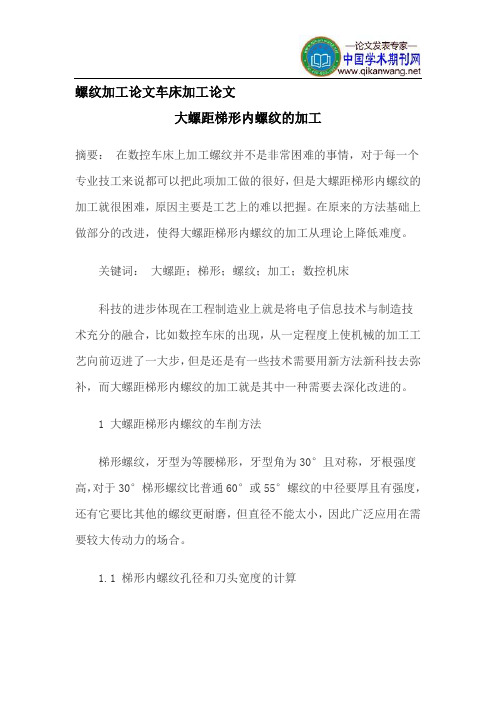
螺纹加工论文车床加工论文大螺距梯形内螺纹的加工摘要:在数控车床上加工螺纹并不是非常困难的事情,对于每一个专业技工来说都可以把此项加工做的很好,但是大螺距梯形内螺纹的加工就很困难,原因主要是工艺上的难以把握。
在原来的方法基础上做部分的改进,使得大螺距梯形内螺纹的加工从理论上降低难度。
关键词:大螺距;梯形;螺纹;加工;数控机床科技的进步体现在工程制造业上就是将电子信息技术与制造技术充分的融合,比如数控车床的出现,从一定程度上使机械的加工工艺向前迈进了一大步,但是还是有一些技术需要用新方法新科技去弥补,而大螺距梯形内螺纹的加工就是其中一种需要去深化改进的。
1 大螺距梯形内螺纹的车削方法梯形螺纹,牙型为等腰梯形,牙型角为30°且对称,牙根强度高,对于30°梯形螺纹比普通60°或55°螺纹的中径要厚且有强度,还有它要比其他的螺纹更耐磨,但直径不能太小,因此广泛应用在需要较大传动力的场合。
1.1 梯形内螺纹孔径和刀头宽度的计算对于梯形螺纹孔径的计算,通常采用Da≈d-p,其孔径公差可通过梯形螺纹有关公差表进行查找;对于梯形内螺纹车刀刀头宽的计算,刀头宽比外梯形螺纹牙顶宽稍大一些。
1.2 数控机床车刀和刀杆的选择及装夹在数控机床车削时,刀杆尺寸应根据工件内fL尺寸选择,孔径较小采用整体式内螺纹车刀,一般采用刀杆是能承受切削力的刀杆,其几何角度、刀具材料与梯形外螺纹车刀相同。
梯形内螺纹车一般磨有前角(车铸铁梯形内螺纹车刀除外),通过计算来修正刀尖角;同时,车制对配的螺母时,应保证车出的螺母与螺杆牙形角一致,采用专用样板,以基准面靠紧工件的外圆表面来找对车刀的正确位置;在车削过程中,背吃刀量不宜掌握,可先车准螺孔尺寸,然后在平面上车出一个轴向深l~2mm、孔径等于螺纹基本尺寸(大径)的台阶。
作为对刀基准,粗车时,应保证车刀刀尖和对刀基准有0.10~0.15mm的间隙;精车时使刀尖逐渐与对刀基准接触。
论车削梯形螺纹方法
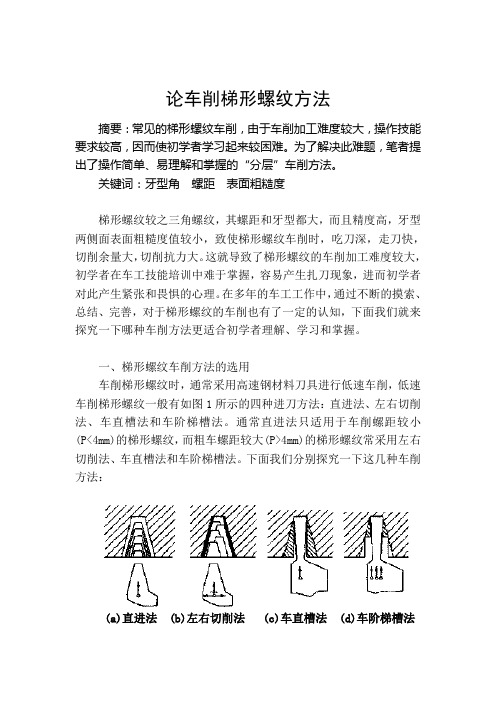
论车削梯形螺纹方法摘要:常见的梯形螺纹车削,由于车削加工难度较大,操作技能要求较高,因而使初学者学习起来较困难。
为了解决此难题,笔者提出了操作简单、易理解和掌握的“分层”车削方法。
关键词:牙型角螺距表面粗糙度梯形螺纹较之三角螺纹,其螺距和牙型都大,而且精度高,牙型两侧面表面粗糙度值较小,致使梯形螺纹车削时,吃刀深,走刀快,切削余量大,切削抗力大。
这就导致了梯形螺纹的车削加工难度较大,初学者在车工技能培训中难于掌握,容易产生扎刀现象,进而初学者对此产生紧张和畏惧的心理。
在多年的车工工作中,通过不断的摸索、总结、完善,对于梯形螺纹的车削也有了一定的认知,下面我们就来探究一下哪种车削方法更适合初学者理解、学习和掌握。
一、梯形螺纹车削方法的选用车削梯形螺纹时,通常采用高速钢材料刀具进行低速车削,低速车削梯形螺纹一般有如图1所示的四种进刀方法:直进法、左右切削法、车直槽法和车阶梯槽法。
通常直进法只适用于车削螺距较小(P<4mm)的梯形螺纹,而粗车螺距较大(P>4mm)的梯形螺纹常采用左右切削法、车直槽法和车阶梯槽法。
下面我们分别探究一下这几种车削方法:(a)直进法 (b)左右切削法 (c)车直槽法 (d)车阶梯槽法图1 梯形螺纹车削的四种进刀方法1.直进法:直进法也叫切槽法,如图1(a)所示。
车削螺纹时,只利用中拖板进行横向(垂直于导轨方向)进刀,在几次行程中完成螺纹车削。
这种方法虽可以获得比较正确的齿形,操作也很简单,但由于刀具三个切削刃同时参加切削,振动比较大,牙侧容易拉出毛刺,不易得到较好的表面品质,并容易产生扎刀现象,因此,它只适用于螺距较小的梯形螺纹车削。
2.左右切削法:左右切削法车削梯形螺纹时,除了用中拖板刻度控制车刀的横向进刀外,同时还利用小拖板的刻度控制车刀的左右微量进给,直到牙形全部车好,如图1(b)所示。
用左右切削法车螺纹时,由于是车刀两个主切削刃中的一个在进行单面切削,避免了三刃同时切削,所以不容易产生扎刀现象。
从车削梯形螺纹实训指导方法看实训教学改进
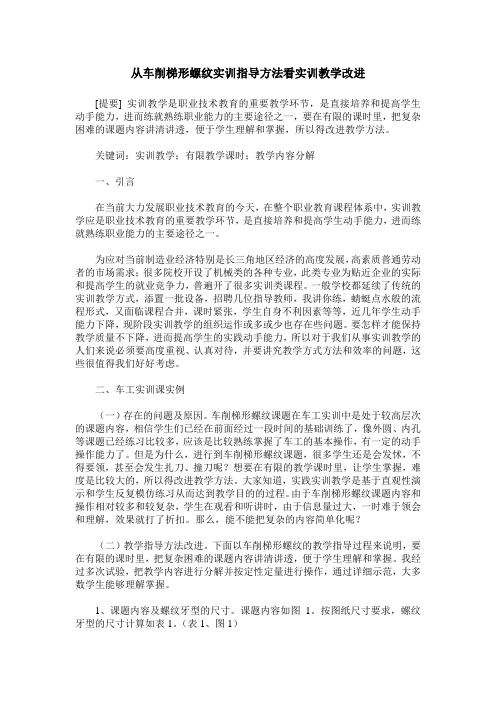
从车削梯形螺纹实训指导方法看实训教学改进[提要] 实训教学是职业技术教育的重要教学环节,是直接培养和提高学生动手能力,进而练就熟练职业能力的主要途径之一,要在有限的课时里,把复杂困难的课题内容讲清讲透,便于学生理解和掌握,所以得改进教学方法。
关键词:实训教学;有限教学课时;教学内容分解一、引言在当前大力发展职业技术教育的今天,在整个职业教育课程体系中,实训教学应是职业技术教育的重要教学环节,是直接培养和提高学生动手能力,进而练就熟练职业能力的主要途径之一。
为应对当前制造业经济特别是长三角地区经济的高度发展,高素质普通劳动者的市场需求;很多院校开设了机械类的各种专业,此类专业为贴近企业的实际和提高学生的就业竞争力,普遍开了很多实训类课程。
一般学校都延续了传统的实训教学方式,添置一批设备,招聘几位指导教师,我讲你练,蜻蜓点水般的流程形式,又面临课程合并,课时紧张,学生自身不利因素等等,近几年学生动手能力下降,现阶段实训教学的组织运作或多或少也存在些问题。
要怎样才能保持教学质量不下降,进而提高学生的实践动手能力,所以对于我们从事实训教学的人们来说必须要高度重视、认真对待,并要讲究教学方式方法和效率的问题,这些很值得我们好好考虑。
二、车工实训课实例(一)存在的问题及原因。
车削梯形螺纹课题在车工实训中是处于较高层次的课题内容,相信学生们已经在前面经过一段时间的基础训练了,像外圆、内孔等课题已经练习比较多,应该是比较熟练掌握了车工的基本操作,有一定的动手操作能力了。
但是为什么,进行到车削梯形螺纹课题,很多学生还是会发怵,不得要领,甚至会发生扎刀、撞刀呢?想要在有限的教学课时里,让学生掌握,难度是比较大的,所以得改进教学方法。
大家知道,实践实训教学是基于直观性演示和学生反复模仿练习从而达到教学目的的过程。
由于车削梯形螺纹课题内容和操作相对较多和较复杂,学生在观看和听讲时,由于信息量过大,一时难于领会和理解,效果就打了折扣。
- 1、下载文档前请自行甄别文档内容的完整性,平台不提供额外的编辑、内容补充、找答案等附加服务。
- 2、"仅部分预览"的文档,不可在线预览部分如存在完整性等问题,可反馈申请退款(可完整预览的文档不适用该条件!)。
- 3、如文档侵犯您的权益,请联系客服反馈,我们会尽快为您处理(人工客服工作时间:9:00-18:30)。
浅谈车工实训教学中梯形螺纹的车削【摘要】梯形螺纹的车削不管是在生产实践中,还是在技能训练模块中,是非常重要的。
本文就梯形螺纹车削过程中车刀的刃磨要求、工件的装夹、车刀的装夹和机床的调整以及车削时如何利用梯形螺纹的计算公式从数学方面来保证粗加工余量的快速去除和精加工余量的有效预留,如何使用三针测量法。
从而达到高效、稳定地车削梯形螺纹。
【关键词】梯形螺纹;分成切削法;螺纹升角;向左赶刀
梯形螺纹的工件不仅广泛的被用在各种机床上,其螺距和牙型都大,而且精度高,牙型两侧面表面粗糙度值较小,致使梯形螺纹车削时,吃刀深,走刀快,切削余量大,切削抗力大。
这就导致了梯形螺纹的车削加工难度较大,学生在车工技能培训中难于掌握,容易产生扎刀现象,进而使学生对此产生紧张和畏惧的心理,很多操作者都是因为无法快速的去除粗加工余量和将精加工余量留得过多或过少,导致加工速度太慢或将工件报废。
在多年的车工实习教学中,通过不断的摸索、总结、完善,对于梯形螺纹的车削也有了一定的认知,在此谈谈分层车削法车削梯形螺纹时的心得体会。
一、车梯形螺纹的工艺准备
1、梯形螺纹的各部分尺寸计算:(以tr42×6-7h螺纹为例)如下图①:
梯形螺纹的轴向剖面形状是一个等腰梯形,如何使车刀沿这个等腰梯形的腰向下延伸,形成一个15°的角呢?在这里就要运用三
角函数算一个进刀比。
如车刀直进1mm,车刀向左进多少才能形成一个15°的角,利用三角函数tg15°=0.268,进刀比为1: 0.268,但是这个进刀比有小数,不是整数,在实际的操作中不方便,为了在实际的操作中方便简单,我们最好找一个整数比,计算一下可知11: 3和1: 0.268接近,可以用它来做进刀比。
2、车刀的选择、刃磨:车刀选用14×14高速钢材料,粗车刀刃磨时,为了便于左右切削并留有精车余量,两侧切削刃之间的夹角应小于牙型角30°,小30′左右。
刀头宽度小于牙槽底宽w
(w=1.93),刀头宽度取1. 2mm左右。
为了使车刀两条侧切削刃锋利且受力、受热均衡,将前刀面磨成左高右低、前翘的形状,使纵向前角10°-15°、右后角取(3°-5°)+ ψ、左后角取(3°-5°)-ψ、ψ为螺纹升角;精车刀刀头宽度取1. 5mm左右,纵向前角0°-5°,后角均可略取大些。
为保证牙型角正确,两侧切削刃之间的夹角略大于牙型角,刀头宽度仍可略小于牙槽底宽,略比粗车时宽一些,取1.5mm,以利于螺纹底面和两侧面的加工,并保证两侧面的表面粗糙度达到要求。
3、车床的选择和调整:选择精度高、磨损少的车床,正确调整机床各处间隙,对床鞍、中小滑板的配合部分进行检查和调整、注意控制机床主轴的轴向窜动、径向圆跳动以及丝杠轴向窜动。
4、工件的装夹:为了提高效率,大余量地车削梯形螺纹,在满足工件技术要求前提下,一般粗、精车都用一夹一顶装夹,个别对中径跳动要求高,不适合一夹一顶加工的工件,也应粗车选择一夹
一顶装夹,精车时用两顶尖装夹来保证工件的技术要求。
装夹工件的时候卡盘一定要夹紧,防止产生切削力大于工件夹紧力的情况。
5、车刀的装夹:车刀主切削刃必须与工件轴线等高,同时应和工件轴线平行。
刀头的角平分线要垂直与工件的轴线。
用样板找正装夹,以免产生螺纹半角误差。
二、梯形螺纹的车削方法
学生练习车p=6的梯形螺纹,采用的是分层车削法。
现以车tr42×6-7h螺纹来介绍我是如何指导学生用分层车削法车削梯形螺纹的。
1、螺纹大径(略小0.15左右)和两端倒角(2×15°)车好,然后将梯形螺纹粗车刀对到工件外圆上,将中滑板调至零位,同时小滑板朝前进方向消除间隙后对零。
此举目的是方便学生记住刻度,不易出错。
2、粗车螺纹:螺纹车刀刚切入工件,总切削面积不大,可以选择较大些的切削深度,车床转速可选择70r/min,如tr42×6的螺纹,螺纹牙型高度h3=0.5p+ac ,ac为间隙量取0.5mm,牙高
h3=0.5p+ac=0.5×6+0.5=3.5mm;我把它分成四层进行,第一到三层先进行直进法车四刀,进刀量分别是10格6 格4格2格,然后我选择全部向左借刀,每刀小滑板转6格,这样可避免小滑板空程影响而出现扎刀现象,这是关键。
具体进刀和借刀方法见表1。
第四层只两刀,经过四层26刀车削螺纹共车深3.5mm,可算粗
车完成。
3、精车螺纹:换上螺纹精车刀,将它在螺纹大径上对刀,并将中滑板刻度盘对零。
由于精车刀刀头宽度仍小于牙槽底宽,故精车刀可落到槽底,目测使精车刀处于槽中间,看此时刻度盘值,然后以每次进刀0.1~0.2mm,将总进刀深度车至3.5~3.7mm(因应车深度为牙高3.5mm,大径小径偏差0~0.419mm,二者之和3.5+(0~0.419/2)=(3.5-3.7)mm),而粗车时已车切削深度3.5mm,故实际只需进刀0.1~0.2mm。
当牙底车平后,又向右侧赶刀,每次0.1~0.05mm,至将右侧面全部车起、车平,然后以低速进0.02mm或走空刀(中、小滑板均不进刀),将右侧车至光洁度达到要求,再将螺纹刀直接进至左边侧面,每车一刀就用游标卡尺量一量牙顶宽,当牙顶宽接近2.2mm时,再用三针测量其m值。
当m值合格时,螺纹中径即合格。
4、螺纹测量:三针测量法是测量外螺纹中经的一种比较精密的方法。
适用于测量一些精度要求较高、螺纹升角小于4?的螺纹工件。
测量时把三根直径相等的量针放在螺纹相对应的螺旋槽中,用千分尺量出两边量针顶点之间的距离m,如下图②。
例:车tr42×6-7h梯形螺纹,用三针测量螺纹中径,求量针直径和千分尺读数值m?
量针直径dd=0.518 p≈3.1mm
千分尺读数值 m=d2+4.864 dd-1.866 p
=39+4.864×3.1-1.866×6
=39+15.08-11.20
=42.88mm
测量时应考虑公差,则m=42.88-0.118~ 42.88-0.453为合格。
m值应在42.427~42.762的范围内。
三针测量法采用的量针一般是专门制造的,在实际应用中,有时也用优质钢丝或新钻头的柄部来代替,但与计算出的量针直径尺寸往往不相符合,这就需要认真选择。
要求所代用的钢丝或钻柄直径尺寸,最大不能在放入螺旋槽时被顶在螺纹牙尖上,最小不能放入螺旋槽时和牙底相碰。
5、至此梯形螺纹加工完毕。
在整个加工过程中,粗加工用26刀,约需时间15分钟左右,精加工8~12刀左右。
同样约需15分钟(包含测量的时间),而且由于每次车削参加切削的刃不太长,所受的切削力不太大,故切削过程平稳,不会出现扎刀的现象,更不会打刀。
从而保证车梯形螺纹的快速和稳定。
总之,在实践教学中,“分层切削法”这种易懂、易掌握的车削梯形螺纹方法,得到了充分地肯定和好评。
教师能够较形象、较直观地把车削方法讲解和传授给学生,学生普遍也能够较快、较容易地理解和掌握这种车削方法,大大降低了梯形螺纹车削这一课题的教学难度和强度。
但在生产实践中梯形螺纹的车削是相当复杂的,车削过程中不可仅仅应用一种方法去车削,而应融会贯通,因此学生只有掌握和熟练了各种车削方法,才能在车削过程中灵活运用,高效率、高精度、高品质地完成梯形螺纹车削。
参考文献:
[1]车工工艺与技能训练,南开大学出版社,2012.06.
[2]机械切削工技能,机械工业出版社,2004.7.
作者简介:
李正清(1957.2-),男,莆田涵江人,大学本科,高级讲师。