飞锤支架夹具结构设计
飞锤支架工艺设计及专用夹具设计说明书

机械制造工艺学课程设计说明书课题名称飞锤支架零件工艺规程设计及机床专用夹具的设计学院机电学院专业机械工程及自动化学号姓名指导老师2013年 6 月27日一、课程设计的目的机械制造工艺学课程设计是在学完了《机械制造工艺学》课程,进行生产实习之后的一个重要教学实践环节。
它要求学生综合应用本课程及有关先修课程(工程材料与热处理、机械设计、互换性与测量技术、金属切削机床、金属切削原理与刀具等)的理论以及在生产实习中学到的实践知识进行工艺规程设计,是毕业设计前的一次综合训练。
通过本次机械制造工艺学课程设计,应达到以下目的:1.学生能熟练运用“机械制造工艺学”课程中的基本理论以及生产实践中学到的实践知识,正确制定一个中等复杂零件的工艺规程。
2.学生能根据被加工零件的工艺规程,运用夹具设计的基本原理和方法,设计一套专用夹具。
3.培养学生熟悉并快速高效运用有关手册、标准、图表等技术资料的能力。
4.进一步培养了学生识图、制图、运算和编写技术文件的基本技能。
二、课程设计的内容与要求(1)根据给定的零件绘制零件图“飞锤支架”零件图(一张)(2)对零件进行工艺分析工艺规程(一份)(3)设计某一道工序所需机床夹具装配图(1-2张)“飞锤支架”钻两侧孔专用夹具图(一张)(4)设计夹具中主要非标准零件图“飞锤支架”定位销零件图(一份)(5)编写课程设计说明书“飞锤支架”零件工艺规程设计及机床专用夹具的设计三、零件分析(一)零件的功用,结构和特点给定零件是飞锤支架,它的作用是作为飞锤工作中的支架,在飞锤的运动工作中起支承定位作用。
它是飞锤调速器上的一个零件,用来连接支撑调速飞锤,以使飞锤平稳转动,达到改变转动惯量来调节转速的目的。
飞锤支架是对称结构,通过其中心孔φ7套于转轴上,而一对飞锤对称装于两对φ6孔中,随支架一起转动。
当转速改变时,飞锤与转轴夹角也改变,从而改变转动惯量来调节转速。
所以,飞锤支架的加工质量将影响调速器的调速精度。
飞锤支架的夹具设计说明

编号_2003011125航空航天大学毕业设计课题名称飞锤支架的夹具设计学院机电学院专业机械工程及自动化年级2003级班级 20030111学号 2003011127姓名甲秋指导教师志东柏何宁2007年5 月毕业设计任务书题目:设计飞锤支架夹具容:(1)零件的工艺分析(2)飞锤支架夹具设计(3)绘制夹具装配图(4)夹具设计说明书(5)加工程序部分原始资料:该零件图样一生产纲领为5000件/年;大批量生产班级:20030111学生:甲秋指导教师:志东柏何宁2007年5月目录前言------------------------------------------------------------------------------------------------------------(3)1.零件的工艺分析---------------------------------------------------------------------------------------(4)1.1 零件的功用、结构和特点----------------------------------------------------------------------------(4)1.2 主要加工表面及要求----------------------------------------------------------------------------------(4)2.飞锤支架夹具设计------------------------------------------------------------------------------------(6)2.1工序的工艺分析----------------------------------------------------------------------------------------(6)2.2定位方案及定位元件选择和设计-------------------------------------------------------------------(8)3.绘制夹具装配图见附表一--------------------------------------------------------------------------(13)4.夹具设计说明书----------------------------------------------------------------------------------------(15) 4.1夹具设计的基本要求---------------------------------------------------------------------------------(15)4.2夹具设计的程序--------------------------------------------------------------------------------------(17)5.加工程序-------------------------------------------------------------------------------------------------(22)6.结论-----------------------------------------------------------------------------------------------------(24)7.参考文献-----------------------------------------------------------------------------------------------(24)(1)飞锤支架零件图------------------------------------------------------------------------------1(2) 装配图--------------------------------------------------------------------------------------附表一前言毕业设计是每个大学生在毕业前必须完成的一个教学环节,是对我们所学专业的一个综合测试,也是对我们毕业生做的一次具体的、重要的考验。
飞锤支架加工工艺设计与分析

飞锤支架加工工艺设计与分析 电 工程 学院 湖北 ・ 武汉
中 图分 类 号 : T H1 6 2 文献 标 识 码 : A
4 3 0 0 7 4 )
文章编号 : 1 6 7 2 — 7 8 9 4 ( 2 0 1 3 ) 2 2 — 0 0 8 8 — 0 2 分缺乏过渡 。 2 . 3结 构 工 艺 分析 ( 1 ) 由于零件结构复杂 、 不规则 , 若用型材毛坯 而金属切
( 1 ) 7 L 径为 D 7的孔 , 其形 位公 差遵守包 容要求 , 表面粗 糙度 R a 6 . 3 Xm,孔 的端 面 与 宽 l I 8的槽 相通 ,孔 口倒 角
l * 45。
( 2 ) 飞锤 支架 O 1 1 的回转 面 , 表面粗糙度 为 R a 6 . 3 m。 ( 3 ) 飞锤 支架  ̄ 1 5的回转面 , 表面粗糙度 为 R a l 2 . 5 m。 ( 4 ) o 1 9的回转 面和右 端面 , 表面粗糙度为 R a 1 . 6 m, 并 倒角。 ( 5 ) 飞锤支架表面 2— 0 6 . 5锪平  ̄ 1 2的沉孔 , 铣上 表面及 其轮廓 , 表面粗糙度不作要求 。 ( 6 ) 4—0 6的孔 , 表 面 粗糙 度 为 R a 6 . 3 m, 倒角 1 " 4 5 。 ( 7 ) 宽 1 8的槽 , 表面粗糙度为 R a 6 . 3 m。
de s i g n
3零 件材 料及 J j  ̄ - r 要求
3 . 1零 件 材 料 及 其 热处 理 要 求 零件材料为 Q T 6 2 — 2 , 抗拉强度 6 2 MP a , 延长率 2 %。 球 墨 铸铁碳硅含量较 高, 具有 良好 的流动性和 自补缩能力 。球 化 处 理过程中球化剂的加入 , 一方 面使 铁液 的温度 降低 , 另一 方 面镁 、 稀土等元素在浇包及浇注系统 中形成夹渣 。 因此 , 经 过球化处理后铁液 的流动性下降。同时 , 如果这些夹 渣进入 型腔, 将会造成夹杂 、 针孔 、 铸件表面粗糙等铸造缺陷 。 3 . 2主 要 加 工 表 面 及 要 求
支架夹具设计说明

题 目 支架钻孔加工专用夹具设计院(系)别 机电及自动化学院专 业 机械制造及其自动化级 别 2009级学 号 0911116036姓 名 沈华坤指导老师 黄国钦 华侨大学机电及自动化学院2012年10月专业课程综合设计目录第一章夹具设计任务 (1)1.1 零件(产品)结构分析及零件图 (1)1.2 支架钻孔工序的重点技术要求分析 (2)第二章拨叉夹具设计方案的确定 (3)2.1 基准面的选择(夹具体方案的确定) (3)2.2 定位方式及定位元件的选择 (3)2.3 夹紧方案及夹紧元件选择 (3)2.4夹具结构 (4)第三章主要零件设计及计算说明 (6)3.1夹紧力计算 (6)3.2其他零件设计计算 (8)第四章夹具定位误差计算 (14)第五章夹具的装配要求及使用说明 (15)参考文献附录第一章夹具设计任务1.1零件(产品)结构分析及零件图1、零件的二维图如图1.1所示图1.1 支架CAD图2、零件的三维图如图1.2所示图1.2 支架三维图1.2 支架钻孔工序六的重点技术要求分析1、支架钻孔工序图六如图1.3所示图1.3 工序图2、工装及切削要素数据表如表1.1所示表1.1工装及切削要素数据表如表 工步号 工 步 内 容工 艺 装 备 主轴转速 切削速度 进给量 切削深度 进给次数 工步工时 r/min m/min mm/r mm 机动 辅助 01 钻与φ18垂直的孔φ10至φ9.8X525卧式铣床 545 17.1 0.4 4.9 1 0.18 02 粗铰与φ18垂直的孔φ10 锥柄麻花钻8.9φ 680 21 0.3 0.1 1 0.153、工序的重点技术要求分析由工件的零件图和三维立体图可以看出,钻与18φ垂直的孔10φ至8.9φ的重点是保证两通孔的垂直度要求。
故夹具体应围绕保证其垂直度的精度来设计,同时也要保证其表面粗糙度及位置精度。
第二章支架夹具设计方案的确定2.1 基准面的选择(夹具体方案的确定)因采用卧式钻床,故待加平面处于水平位置。
飞锤支架工艺规程设计
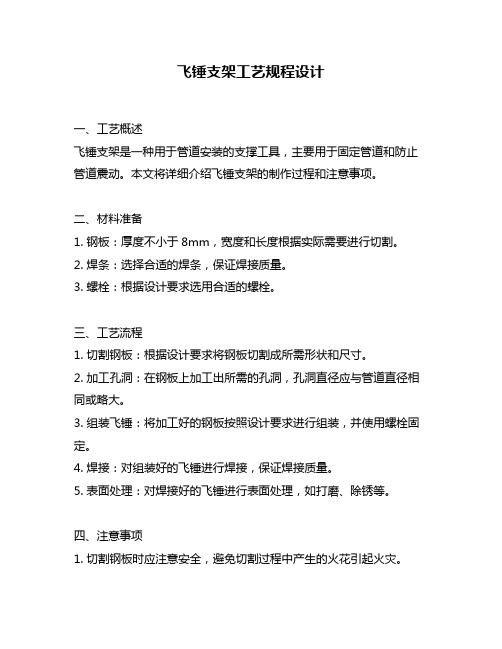
飞锤支架工艺规程设计一、工艺概述飞锤支架是一种用于管道安装的支撑工具,主要用于固定管道和防止管道震动。
本文将详细介绍飞锤支架的制作过程和注意事项。
二、材料准备1. 钢板:厚度不小于8mm,宽度和长度根据实际需要进行切割。
2. 焊条:选择合适的焊条,保证焊接质量。
3. 螺栓:根据设计要求选用合适的螺栓。
三、工艺流程1. 切割钢板:根据设计要求将钢板切割成所需形状和尺寸。
2. 加工孔洞:在钢板上加工出所需的孔洞,孔洞直径应与管道直径相同或略大。
3. 组装飞锤:将加工好的钢板按照设计要求进行组装,并使用螺栓固定。
4. 焊接:对组装好的飞锤进行焊接,保证焊接质量。
5. 表面处理:对焊接好的飞锤进行表面处理,如打磨、除锈等。
四、注意事项1. 切割钢板时应注意安全,避免切割过程中产生的火花引起火灾。
2. 加工孔洞时应注意孔洞的位置和大小,确保与管道匹配。
3. 组装飞锤时应按照设计要求进行,不得随意改动。
4. 焊接时应注意焊接质量,避免出现焊缝裂纹等问题。
5. 表面处理时应彻底除去表面的锈蚀物,并进行打磨。
五、质量控制1. 钢板厚度和尺寸应符合设计要求。
2. 孔洞直径和位置应与管道匹配。
3. 飞锤组装后应稳定可靠,不得出现松动等情况。
4. 焊接质量应符合相关标准要求。
5. 表面处理后表面光滑无毛刺。
六、检验方法1. 对钢板、孔洞和飞锤进行尺寸检测,确保符合设计要求。
2. 对飞锤进行抗拉强度测试,测试结果应符合相关标准要求。
七、安全注意事项1. 切割钢板时必须戴好防护眼镜和手套等个人防护装备,避免产生危险。
2. 在焊接时必须戴好防护面罩和手套等个人防护装备,避免受到辐射和热量的伤害。
八、环保要求1. 废弃的钢板、焊条等材料应妥善处理,避免对环境造成污染。
2. 焊接过程中应注意控制焊接烟尘的排放,减少对环境的影响。
九、工艺改进1. 可以引入自动化设备,提高生产效率和产品质量。
2. 可以采用新型材料进行制作,提高产品性能和使用寿命。
飞锤支架工艺设计及专用夹具设计说明书概要
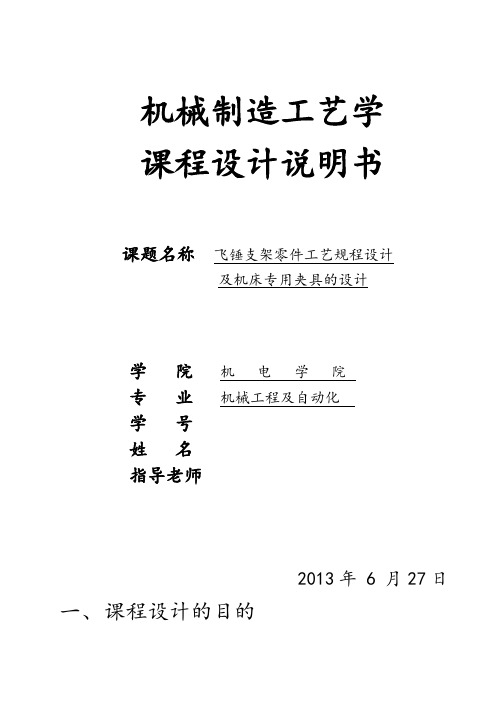
机械制造工艺学课程设计说明书课题名称飞锤支架零件工艺规程设计及机床专用夹具的设计学院机电学院专业机械工程及自动化学号姓名指导老师2013年 6 月27日一、课程设计的目的机械制造工艺学课程设计是在学完了《机械制造工艺学》课程,进行生产实习之后的一个重要教学实践环节。
它要求学生综合应用本课程及有关先修课程(工程材料与热处理、机械设计、互换性与测量技术、金属切削机床、金属切削原理与刀具等)的理论以及在生产实习中学到的实践知识进行工艺规程设计,是毕业设计前的一次综合训练。
通过本次机械制造工艺学课程设计,应达到以下目的:1.学生能熟练运用“机械制造工艺学”课程中的基本理论以及生产实践中学到的实践知识,正确制定一个中等复杂零件的工艺规程。
2.学生能根据被加工零件的工艺规程,运用夹具设计的基本原理和方法,设计一套专用夹具。
3.培养学生熟悉并快速高效运用有关手册、标准、图表等技术资料的能力。
4.进一步培养了学生识图、制图、运算和编写技术文件的基本技能。
二、课程设计的内容与要求(1)根据给定的零件绘制零件图“飞锤支架”零件图(一张)(2)对零件进行工艺分析工艺规程(一份)(3)设计某一道工序所需机床夹具装配图(1-2张)“飞锤支架”钻两侧孔专用夹具图(一张)(4)设计夹具中主要非标准零件图“飞锤支架”定位销零件图(一份)(5)编写课程设计说明书“飞锤支架”零件工艺规程设计及机床专用夹具的设计三、零件分析(一)零件的功用,结构和特点给定零件是飞锤支架,它的作用是作为飞锤工作中的支架,在飞锤的运动工作中起支承定位作用。
它是飞锤调速器上的一个零件,用来连接支撑调速飞锤,以使飞锤平稳转动,达到改变转动惯量来调节转速的目的。
飞锤支架是对称结构,通过其中心孔φ7套于转轴上,而一对飞锤对称装于两对φ6孔中,随支架一起转动。
当转速改变时,飞锤与转轴夹角也改变,从而改变转动惯量来调节转速。
所以,飞锤支架的加工质量将影响调速器的调速精度。
飞锤支架工艺及夹具设计[铣宽14槽]
![飞锤支架工艺及夹具设计[铣宽14槽]](https://img.taocdn.com/s3/m/d9b8f81ef12d2af90242e652.png)
常州机电职业技术学院毕业设计(论文)说明书作者:学号:系部:专业:题目:飞锤支架加工工艺及夹具设计指导者:评阅者:年月毕业设计(论文)中文摘要本设计是基于飞锤支架零件的加工工艺规程及一些工序的专用夹具设计,加工外圆及孔的车夹具设计。
飞锤支架零件的主要加工表面是平面及孔系。
一般来说,保证平面的加工精度要比保证孔系的加工精度容易。
因此,本设计遵循先面后孔的原则。
并将孔与平面的加工明确划分成粗加工和精加工阶段以保证孔系加工精度。
基准选择以-中间拔叉的输入轴和输出轴的支承孔作为粗基准,以顶面与两个工艺孔作为精基准。
主要加工工序安排是先以支承孔系定位加工出顶平面,再以顶平面与支承孔系定位加工出工艺孔。
在后续工序中除个别工序外均用顶平面和工艺孔定位加工其他孔系与平面。
支承孔系的加工采用的是坐标法镗孔。
整个加工过程均选用机床。
关键词飞锤支架,零件,加工工艺,专用夹具,设计毕业设计(论文)外文摘要Title: The flying hammer bracket parts fork processing technology and fixture designAbstract:This design is the special fixture for machining technology for the flying hammer bracket parts and process design based on car fixture design, machining and hole. The main processing surface flying hammer bracket parts is the plane and a seriesof hole. In general, ensure the machining accuracy of plane than to ensure the accuracyof the processing easily. Therefore, the design follows the surface after the first hole principle. And the hole and the plane processing clearly divided into roughing and finishing stages to ensure machining precision. Datum selection to the bearing hole in the middle fork of the input shaft and output shaft as a rough benchmark,the top surface and the two holes as a precision technology base. The main processof machining technology is first to support hole positioning processing the top plane, and then the top plane and the series of supporting hole location hole processing technology. In addition to the follow-up processes are individual processes with thetop plane positioning technology and other processing Kong and plane. Processing support holes using the coordinate boring. The whole process selection of machine tool.Keywords:flying hammer bracket, parts, processing, special fixture, design目录1.零件分析 (1)1.1零件作用 (1)1.2零件工艺分析 (1)2.选择毛坯种类并确定制造方法 (2)3.工艺规程的设计 (2)3.1基准的选择 (2)3.2制定工艺路线 (2)3.3工艺路线确定 (3)3.4机械加工余量、工序尺寸及毛坯尺寸的确定 (4)4 铣14槽夹具设计 (11)4.1研究原始质料 (11)4.2定位基准的选择 (11)4.3切削力及夹紧分析计算 (11)4.4误差分析与计算 (12)4.5零、部件的设计与选用 (13)4.5.1定位销选用 (13)4.5.2 定向键与对刀装置设计 (13)4.6夹具设计及操作的简要说明 (14)总结 (15)致谢 (16)参考文献 (17)1.零件分析1.1 零件作用设计题目所给零件是飞锤支架。
飞锤支架工艺设计及专用夹具设计说明书资料
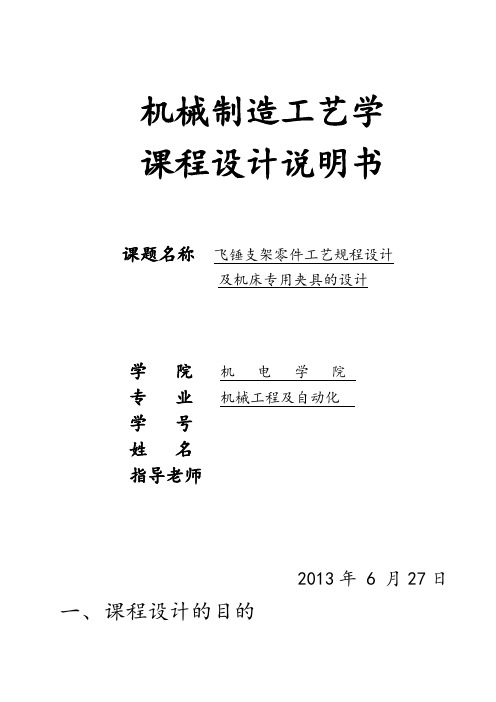
机械制造工艺学课程设计说明书课题名称飞锤支架零件工艺规程设计及机床专用夹具的设计学院机电学院专业机械工程及自动化学号姓名指导老师2013年 6 月27日一、课程设计的目的机械制造工艺学课程设计是在学完了《机械制造工艺学》课程,进行生产实习之后的一个重要教学实践环节。
它要求学生综合应用本课程及有关先修课程(工程材料与热处理、机械设计、互换性与测量技术、金属切削机床、金属切削原理与刀具等)的理论以及在生产实习中学到的实践知识进行工艺规程设计,是毕业设计前的一次综合训练。
通过本次机械制造工艺学课程设计,应达到以下目的:1.学生能熟练运用“机械制造工艺学”课程中的基本理论以及生产实践中学到的实践知识,正确制定一个中等复杂零件的工艺规程。
2.学生能根据被加工零件的工艺规程,运用夹具设计的基本原理和方法,设计一套专用夹具。
3.培养学生熟悉并快速高效运用有关手册、标准、图表等技术资料的能力。
4.进一步培养了学生识图、制图、运算和编写技术文件的基本技能。
二、课程设计的内容与要求(1)根据给定的零件绘制零件图“飞锤支架”零件图(一张)(2)对零件进行工艺分析工艺规程(一份)(3)设计某一道工序所需机床夹具装配图(1-2张)“飞锤支架”钻两侧孔专用夹具图(一张)(4)设计夹具中主要非标准零件图“飞锤支架”定位销零件图(一份)(5)编写课程设计说明书“飞锤支架”零件工艺规程设计及机床专用夹具的设计三、零件分析(一)零件的功用,结构和特点给定零件是飞锤支架,它的作用是作为飞锤工作中的支架,在飞锤的运动工作中起支承定位作用。
它是飞锤调速器上的一个零件,用来连接支撑调速飞锤,以使飞锤平稳转动,达到改变转动惯量来调节转速的目的。
飞锤支架是对称结构,通过其中心孔φ7套于转轴上,而一对飞锤对称装于两对φ6孔中,随支架一起转动。
当转速改变时,飞锤与转轴夹角也改变,从而改变转动惯量来调节转速。
所以,飞锤支架的加工质量将影响调速器的调速精度。
- 1、下载文档前请自行甄别文档内容的完整性,平台不提供额外的编辑、内容补充、找答案等附加服务。
- 2、"仅部分预览"的文档,不可在线预览部分如存在完整性等问题,可反馈申请退款(可完整预览的文档不适用该条件!)。
- 3、如文档侵犯您的权益,请联系客服反馈,我们会尽快为您处理(人工客服工作时间:9:00-18:30)。
目录前言------------------------------------------------------------------------------------------------------------(3)1.零件的工艺分析---------------------------------------------------------------------------------------(4)1.1 零件的功用、结构和特点----------------------------------------------------------------------------(4)1.2 主要加工表面及要求----------------------------------------------------------------------------------(4)2.飞锤支架夹具设计------------------------------------------------------------------------------------(6)2.1工序的工艺分析----------------------------------------------------------------------------------------(6)2.2定位方案及定位元件选择和设计-------------------------------------------------------------------(8)3.绘制夹具装配图见附表一--------------------------------------------------------------------------(13)4.夹具设计说明书----------------------------------------------------------------------------------------(15) 4.1夹具设计的基本要求---------------------------------------------------------------------------------(15)4.2夹具设计的程序--------------------------------------------------------------------------------------(17)5.加工程序-------------------------------------------------------------------------------------------------(22)6.结论-----------------------------------------------------------------------------------------------------(24)7.参考文献-----------------------------------------------------------------------------------------------(24)(1)飞锤支架零件图------------------------------------------------------------------------------1(2) 装配图--------------------------------------------------------------------------------------附表一1.2 主要加工表面及要求1. 孔径为φ7036.00+的孔,其形位公差遵守包容要求,表面粗糙度Ra1.6μm,孔的端面与宽185.02.0++的槽相通,孔口倒角1×45°。
2. 飞锤支架φ11的回转面,表面粗糙度为Ra6.3μm。
3. 飞锤支架φ15的回转面,表面粗糙度为Ra12.5μm。
4. φ190033.0-的回转面和右端面,表面粗糙度为Ra1.6μm,并倒角。
5. 飞锤支架表面2-φ6.5锪平φ12的沉孔,铣上表面及其轮廓,表面粗糙度不作要求。
6. 4-φ612.004.0+-的孔,表面粗糙度为Ra6.3μm,倒角1×45°。
7. 宽185.02.0+-的槽,表面粗糙度为Ra6.3μm。
机械加工加工方案表(1)工艺路线如表1所示,根据185.02.0++的加工要求选择φ18的三面刃铣刀和XA6132铣床。
2.飞锤支架夹具设计2.1工序的工艺分析零件为飞锤支架,材料为QT62—2。
生产类型为:大批量生产。
该零件工艺规程见工艺卡。
先要求设计第4道工序铣185.02.0++槽的铣床夹具。
零件的加工要求为:宽0.50.218++mm ,表面粗糙度为Ra6.3um.本工序的加工条件为XA6132铣床及φ12端面铣刀,工件右侧回转体,φ0.03607+孔、4-φ0.120.046+-孔、及2-φ6.5锪平φ12孔均已加工,达到图样要求。
正火处理,毛坯上铣185.02.0++槽的经济精度可达IT8,表面粗糙度Ra6.3um ,在铣夹具上加工时适当控制进给速度,可以保证槽的尺寸精度和表面粗糙要求。
因此在本工序加工时,主要应考虑要如何保证槽的宽度偏差。
图1-1工序图2.2定位方案及定位元件选择和设计 2.2.1定位方案的选择1.根据工序加工要求,工件在夹具中的定位方案如下:如图1-1所示:要夹住的工件主要尺寸。
回转面及其端面为主要定位基准,限制6个自由度X、方案一:以φ190-.0033回转面为止推基准,限制2个自由度,以零件左端面Y、X、Y、Z,以φ190.0033-外型轮廓宽30的长方体外型轮廓作为防转基准,限制3个自由度。
工件在夹金紧的时候又限制了一个自由度。
方案一草图回转面及其端面为主要定位基准,限制6个自由度X、方案二:以φ190-.0033回转面为止推基准,限制2个自由度,以φ45的圆外Y、X、Y、Z,以φ190.0033-型轮廓作为防转基准,限制3个自由度。
同样工件在夹金紧的时候又限制了一个自由度。
方案二草图回转面及其端面为主要定位基准,限制6个自由度X、方案三:以φ190-.0033回转面为止推基准,限制2个自由度,以2-φ6.5锪Y、X、Y、Z,以φ190-.0033平12的两个孔为防转基准,限制3个自由度。
同样工件在夹金紧的时候又限制了一个自由度。
此方案是用螺栓固定达到防转的目的,其作用了力方向如下图受F1和F2的作用力。
方案三草图选择基准时应保证工件安装可靠,夹具设计简单、操作方便。
方案一:按照基准重合原则确定的,用设计基准作为定位基准,以避免定位基准与设计基准不重合而引起的基准不重合误差。
有利于保证加工精度,夹紧力可以抵消部分切削力。
有利于提高夹紧刚度,缺点是夹紧力大容易引起定位元件变形。
夹具设计简单,装夹方便。
方案二:和方案一差不多,只有装夹的方向有点不同,不存在基准不重合误差,有利于保证加工精度,夹紧力可以抵消部分切削力。
方案三:按照基准统一原则确定的,有利于夹具的设计制造,夹紧力方向指向定位元件刚性较大的方向。
缺点是不容易保证槽的的精确度,铣刀进给的轴向力完全由工件承受,会引起定位元件变形。
本工序加工18的槽,从夹具制造的简单方便考虑,可以选择方案三。
但是方案三在装夹是麻烦,大量的时间浪费在装夹上 ,故不采用。
从加工的切削力和夹紧力方面考虑,加工时夹紧力不需要太大。
综合两方面的考虑故选择方案一。
2.定位元件设计:设计定位元件的结构如图1-2所示。
夹具与零件的外型轮廓相似。
图1-2这样能较容易、较稳定地保证加工精度。
用夹具装夹工件时,工件相对与刀具的位置由夹具保证,基本不受工人技术水平的影响,因而能较容易、教稳定地保证工件的加工精度。
能提高劳动生产率,减轻工人的劳动强度。
采用夹具后,工件不需划线找正,装夹方便迅速,显著地减少了辅助时间,提高了劳动生产率。
夹紧力的计算:因采用的是手动夹具故夹紧力无须计算。
3.绘制夹具零件图图1-34、夹紧装置设计夹紧机构的三要素是夹紧力方向的确定、夹紧力作用点的确定、夹紧力大小的确定。
夹紧里的方向如图3左视图所示夹具左端固定不动,装夹时工件受夹紧力F和与其相对的反作用力F1。
夹紧力作用点的选择应遵循的规则:(1)为了使定位稳定,夹紧力作用点应该落在主要的定位支承面上,活络在主要的定位支承面上的支承点所围成的面积内;(2)夹紧力应作用在工件刚性较好的部位上,不应该使工件产生夹紧变形或使工件产生翻砖力矩;(3)为了防止工件在加工过程中产生振动,夹紧力的作用点应尽量靠近被加工表面;(4)夹紧力作用点的数目,应尽量在工件的整个接触面上分布均匀,以减小夹紧变形。
夹具三维图该夹具是用平口钳固定,是手动夹具为丝杆传动。
在装夹过程中方便简单,节约了大量的装夹时间。
操作方便,使用安全、可靠,且改善工人的劳动条件,减轻劳动强度。
在夹紧过程中用不会使工件产生变形。
零件三维造型3.绘制夹具装配图见附表一夹具总图绘制完毕后,对夹具上的非标准件要绘制零件工作图,并规定相应在的技术要求。
零件工作图应严格遵照所规定的比例绘制。
视图、投影应完整,尺寸要标注齐全,所标注的公差及技术条件应符合总图要求,加工精度及表面光洁度应选择合理。
在夹具设计图纸全部完毕后,还有待于精心制造和实践和使用来验证设计的科学性。
经试用后,有时还可能要对原设计作必要的修改。
因此,要获得一项完善的优秀的夹具设计,设计人员通常应参与夹具的制造、装配,鉴定和使用的全过程。
夹具体是夹具的基本件,它既要把夹具的各种元件、机构、装置连接成一个整体,而且还要考虑工件装卸的方便。
因此,夹具体的形状和尺寸主要取决于夹具各组成件的分布位置、工件的外形轮廓尺寸以及加工的条件等。
在设计夹具体时应满足以下基本要求。
①、具有足够的强度和刚度。
②、结构简单、轻便,在保证强度和刚度前提下结构近可能简单紧凑,体积小、质量轻和便于工件装卸。
③、安装稳定牢靠。
④、结构的工艺性好,便于制造、装配和检验⑤、尺寸要稳定且具有一定精度。
⑥、清理方便。
夹具体毛坯制造方法的选择综合考虑结构合理性、工艺性、经济型、标准化以及各种夹具体的优缺点等,选择夹具体毛坯制造方法为铸造夹具体;夹具体的外形尺寸在绘制夹具总图时,根据工件、定位元件、夹紧装置及其辅助机构在总体上的配置,夹具体的外形尺寸便已大体确定。
然后进行造型设计,再根据强度和刚度要求选择断面的结构形状和壁厚尺寸。