高端液压支架结构件制造工艺的先进性分析
引进国外先进技术 生产高端液压支架
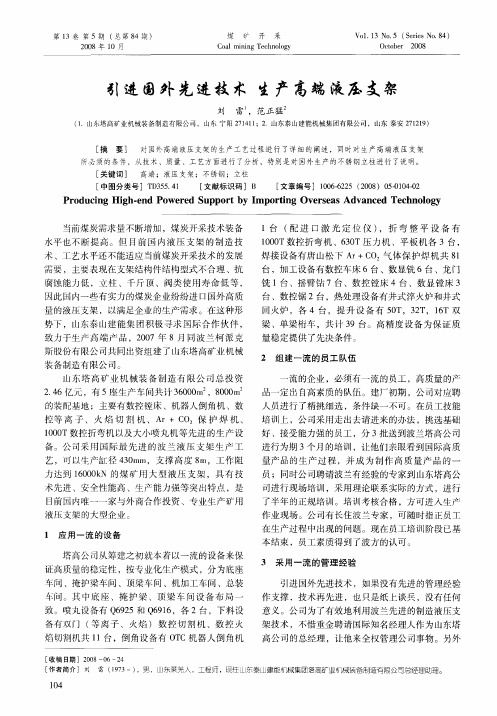
量产 品的 生 产 过 程 ,并 成 为 制 作 高 质 量 产 品 的一 员 ;同时公 司聘 请 波兰有 经验 的专 家 到山东塔 高公 司进行 现场培 训 ,采 用理论 联 系实际 的方式 ,进行
了半年 的正规 培训 。培训 考核合格 ,方 可进入 生产
作业现 场 。公 司有 长住波 兰专家 ,可 随时指 正员工
第1 3卷 第 5期 ( 第 8 总 4期 ) 2) ( 8年 l ( 】 O月
煤 矿 开 采
Co lmi i c o0 y a nng Te hn lg
Vo . 3 No 5 ( e is N . 4) 1 1 . Sr o 8 e
0co e 2 08 tb r 0
高端 ;液 压 支 架 ;不锈 钢 ; 立柱
所必须 的条件,从技术 、质量 、工艺方面进行 了分析 ,特别是对国外生产 的不锈钢立柱 进行 了说 明。
[ 键词 ] 关
[ 中图分类号]T 3 54 D 5. 1
[ 文献标识码 ]B
[ 文章编号]10 _2 5( o 8 5o o _2 0662 20 )0 _14o
2 组建 一流 的员工 队伍
一
装备 制造有 限公 司。
山 东塔 高 矿 业 机 械 装 备 制 造 有 限公 司 总投 资 24 . 6亿元 ,有 5座 生产车 间共计 3 o 0 0 O 6 m ,8 0 m 的装 配基地 ;主要 有数控 镗床 、机器人 倒 角机 、数 控 等 离 子 、火 焰 切 割 机 、A r+C ,保 护 焊 机 、 0 1( T数控折 弯机 以及大小 喷 丸机 等先 进 的生 产设 (0 ) 】 备 。公 司采 用 国际 最 先 进 的波 兰 液 压 支架 生 产 工
高端液压支架结构件制造工艺的先进性分析

矫 平 、 弯 工 序 是 成 型 零 件 的 终 结 工 2 l 标 准 执 行 。 型 时 , 缝 根 部 间 隙 为 压 01 成 焊
步 , 接 制 约 着 部 件 的 成 型 质 量 。 平时 必 0 mm, 果 存 在 较 大 间隙 , 须 将 工 件 直 矫 ~2 如 必 须将 工件 毛 刺 、 边 清 理 干 净 , 于 变 形的 矫 平 或 刀 找 , 不 能 采 用 强 力 挤 压 变 形 的 飞 对 决
发 展 , 对 液 压 支 架 的 制 造 工 艺 又 有 了 更 这
高 的 要 求 。 们 公 司 是 与 波 兰 可 派 克 斯 公 我
后 再 进行 切 割 ; 于 需 压 弯 的 开 口部 位 , 对 可 作 平 台 以 外 增 设 弹 性 浮 动 支 撑 架 。
只割 好 口两 侧 缝 隙 , 止 压 弯 时 产 生 “口 防 裂” 象。 现
1. 2 成 型 2.
司合 作 的 一 家 合 资 企业 , 业 设 计 、 造液 专 制
压支架, 目前 已制 造 出 Z QY9 0 / 4 0 0 0 2 /5 D、
成 型 是 液 压 支 架 结 构 件制 造 的 关 键 工 序之一 。 型前 , 零 件必须检验合格 , 成 各 按 液 压 支架 结 构 件制 造 技 术 条 件MT/ 8 — T5 7
工 业 技 术
SI C C NE&TCNLG E EHOO Y
高端液压支架 结构 件制造工 艺的先进性 分析
赵忠刚 曹文 明 虞长 江 ( 山东塔 高矿 业机械 装备 制造 有限公 司 山东 宁阳 2 1 1 ) 7 1 4
摘 要 : 文 分 别从 高端 液 压 支 架 结 构件 制 造 相 关工 序 抛 丸 , 本 下料 , 磨 , 丸 . 平 , 弯 、 型 、 接 、 孔 等进 行 了细 致 的阐 修 抛 矫 压 成 焊 镗 述, 分析 了我公 司高端液 压支架 结构件制造 工艺 的先进 性 , 通过近年 来良好 的使 用效 果进一 步进 行 了确 定。 并 关键 词 : 丸 成型 焊接 多层 多道 低 强匹配 抛 中 图 分 类 号 : H1 T 6 文 献 标 识 码 : A 文 章 编 号 : 6 2 3 9 ( 0 0 ( ) 0 l -0 1 - 7 I 2 I ) 2a 一 1 2 7 2 7
国产高端液压支架制造工艺方案之探究
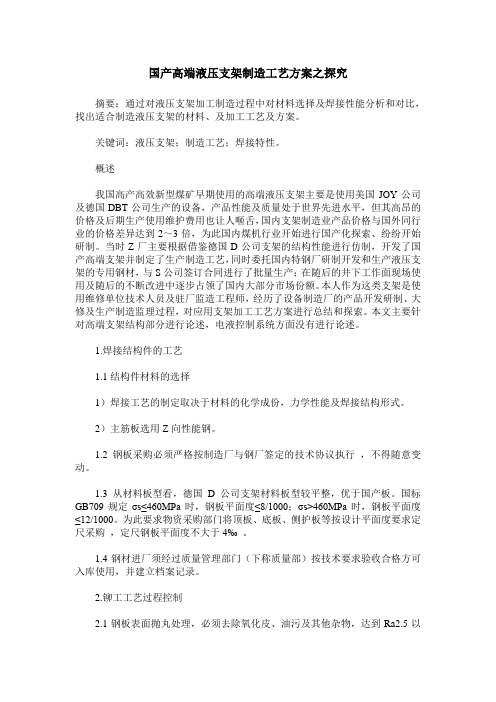
国产高端液压支架制造工艺方案之探究摘要:通过对液压支架加工制造过程中对材料选择及焊接性能分析和对比,找出适合制造液压支架的材料、及加工工艺及方案。
关键词:液压支架;制造工艺;焊接特性。
概述我国高产高效新型煤矿早期使用的高端液压支架主要是使用美国JOY公司及德国DBT公司生产的设备,产品性能及质量处于世界先进水平,但其高昂的价格及后期生产使用维护费用也让人咂舌,国内支架制造业产品价格与国外同行业的价格差异达到2~3倍,为此国内煤机行业开始进行国产化探索、纷纷开始研制。
当时Z厂主要根据借鉴德国D公司支架的结构性能进行仿制,开发了国产高端支架并制定了生产制造工艺,同时委托国内特钢厂研制开发和生产液压支架的专用钢材,与S公司签订合同进行了批量生产;在随后的井下工作面现场使用及随后的不断改进中逐步占领了国内大部分市场份额。
本人作为这类支架是使用维修单位技术人员及驻厂监造工程师,经历了设备制造厂的产品开发研制、大修及生产制造监理过程,对应用支架加工工艺方案进行总结和探索。
本文主要针对高端支架结构部分进行论述,电液控制系统方面没有进行论述。
1.焊接结构件的工艺1.1结构件材料的选择1)焊接工艺的制定取决于材料的化学成份,力学性能及焊接结构形式。
2)主筋板选用Z向性能钢。
1.2钢板采购必须严格按制造厂与钢厂签定的技术协议执行,不得随意变动。
1.3从材料板型看,德国D公司支架材料板型较平整,优于国产板。
国标GB709规定σs≤460MPa时,钢板平面度≤8/1000;σs>460MPa时,钢板平面度≤12/1000。
为此要求物资采购部门将顶板、底板、侧护板等按设计平面度要求定尺采购,定尺钢板平面度不大于4‰ 。
1.4钢材进厂须经过质量管理部门(下称质量部)按技术要求验收合格方可入库使用,并建立档案记录。
2.铆工工艺过程控制2.1钢板表面抛丸处理,必须去除氧化皮、油污及其他杂物,达到Ra2.5以上级别。
1)厚板下料时选用9M或6M数控切割机和光电跟踪切割机,薄板下料时选用剪板机,平板机或压力机矫正,弯曲成形件选用合适吨位的油压机在胎具上进行冷弯或热煨,制作样板检验,主筋板、耳板的底边留刀检量进行机加工,依此作为后续加工的基准。
特厚煤层液压支架结构件的制造工艺探讨

关键 词 : 特 厚煤 层 ;放 顶煤 ;液压 支架 结构 件 ;制造 工 艺
中图分 类号 : T D 3 5 5 . 4 4 文献标识码 : B 文章编号 : 1 0 0 1 — 0 8 7 4 ( 2 0 1 3 ) 0 2— 0 0 8 5— 0 3
Man u f a c t u r e Te c h ni c s o f Hy dr au l i c Su p p o r t Par t s i n Su p e r — Th i c k Se am
液 压 支架 , 对特 厚煤 层 放 顶煤 液 压 支 架 曾采 取 以下
的制 造工艺 。
性, 使得 我 国大 多数 煤 矿 特厚 煤 层 开 采 基本 上 都 抛
弃 了 以前 采 用 的分层 开 采 方 式 , 而 将 放 顶煤 开 采 作 为 特厚煤 层 开采技 术 的首选 , 为此, 用 于特 厚煤层 工 作 面 的放 顶煤 液压 支架 的制 造工 艺 已引起 有关制 造
接性 能差 , 焊后 应力 大 。
2 特 厚煤 层放 顶煤 液压支 架 结构件 制造 工艺
我厂 从 2 0 0 8年 以 来 先 后 曾 制 造 过 Z F 1 5 0 0 0 /
2 7 . 5 / 4 2型 、 Z F 1 3 0 0 0 / 2 5 / 3 8型 和 Z F 1 0 0 0 0 / 2 3 / 3 5型
0 引言 在“ 十二 五 ” 期 间 大 同 煤 矿 集 团将 建 成 十 一 座 千 万 吨级矿 井 , 这 几座 矿井 可采 的煤层 储量 大 、 煤 层 厚 度也 均达 2 0 m 以上 。近 年来Байду номын сангаас, 由于综 采 放顶煤 开 采 技术 在安 全 、 高 效 生 产 等方 面 显 现 出明 显 的优 越
简析液压支架结构件制造技术
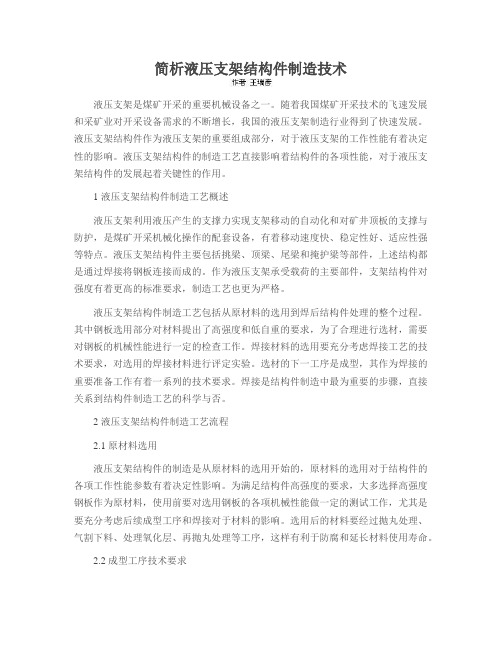
简析液压支架结构件制造技术液压支架是煤矿开采的重要机械设备之一。
随着我国煤矿开采技术的飞速发展和采矿业对开采设备需求的不断增长,我国的液压支架制造行业得到了快速发展。
液压支架结构件作为液压支架的重要组成部分,对于液压支架的工作性能有着决定性的影响。
液压支架结构件的制造工艺直接影响着结构件的各项性能,对于液压支架结构件的发展起着关键性的作用。
1 液压支架结构件制造工艺概述液压支架利用液压产生的支撑力实现支架移动的自动化和对矿井顶板的支撑与防护,是煤矿开采机械化操作的配套设备,有着移动速度快、稳定性好、适应性强等特点。
液压支架结构件主要包括挑梁、顶梁、尾梁和掩护梁等部件,上述结构都是通过焊接将钢板连接而成的。
作为液压支架承受载荷的主要部件,支架结构件对强度有着更高的标准要求,制造工艺也更为严格。
液压支架结构件制造工艺包括从原材料的选用到焊后结构件处理的整个过程。
其中钢板选用部分对材料提出了高强度和低自重的要求,为了合理进行选材,需要对钢板的机械性能进行一定的检查工作。
焊接材料的选用要充分考虑焊接工艺的技术要求,对选用的焊接材料进行评定实验。
选材的下一工序是成型,其作为焊接的重要准备工作有着一系列的技术要求。
焊接是结构件制造中最为重要的步骤,直接关系到结构件制造工艺的科学与否。
2 液压支架结构件制造工艺流程2.1 原材料选用液压支架结构件的制造是从原材料的选用开始的,原材料的选用对于结构件的各项工作性能参数有着决定性影响。
为满足结构件高强度的要求,大多选择高强度钢板作为原材料,使用前要对选用钢板的各项机械性能做一定的测试工作,尤其是要充分考虑后续成型工序和焊接对于材料的影响。
选用后的材料要经过抛丸处理、气割下料、处理氧化层、再抛丸处理等工序,这样有利于防腐和延长材料使用寿命。
2.2 成型工序技术要求成型是液压支架结构件制造工艺的重要工序。
成型方式一般有两种:一是依照工件底板上的划线进行拼装,适用于单件或批量小的工件;二是使用专用的成型拼装模具,适用于大批量的零件。
高端液压支架关键技术研究与产业化-科学进步奖答辩PPT课件

8s/架 50000
1
≌
≌ >
32
五、推动技术进步的作用和推广效果
• 本项目实现液压支架技术的跨越式发展, 产业化发展,完全替代进口,并越居世界 领先,彻底改变了我国高端液压支架依靠 进口的局面,带动了相关产业链的发展, 推动了重大装备技术的进步。
• 近三年来,在50多个矿区,推广应用高端 液压支架33600多台,一大批年产600~ 1000万吨工作面,达到世界领先水平。
2020/2/20
27
二 、关键技术 — 高端液压支架技术标准研究
本项目研究制订了四个国家标准七项行业标准
2020/2/20
28
三 、主要创新点
首创液压支架围岩耦合三维动态优化设 1 计方法体系和软件系统,6~7m系列高
端液压支架设计研制。
发明高端液压支架用高强度焊接结构钢 2 及低温焊接新工艺,首次提出了支架结
35
2020/2/20
5
一 、立项背景和目的
• 高端液压支架技术难题及产业化难度
4.大缸径抗冲击立柱和电液控制等元部件的 关键可靠性问题难以解决,密封等关键元 部件技术“瓶颈”制约。
5.现有实验条件无法满足高端支架试验要求
6.支架的整体可靠性差,无故障运行时间短, 寿命只15000次工作循环与欧标30000次 差一半。
2020/2/20
19
二 、关键技术 — 高端液压支架电液控制系统开发
创新开发了国内首套具有 自主知识产权的高端液压 支架电液控制系统,形成 这一高新技术产业。已推 广应用30多套。
2020/2/20 电液控制系统成套设备
20
二 、关键技术 — 高端液压支架电液控制系统开发
开发研制了综采工作面集成供液系统
液压支架整体结构稳定性制造工艺方面的控制
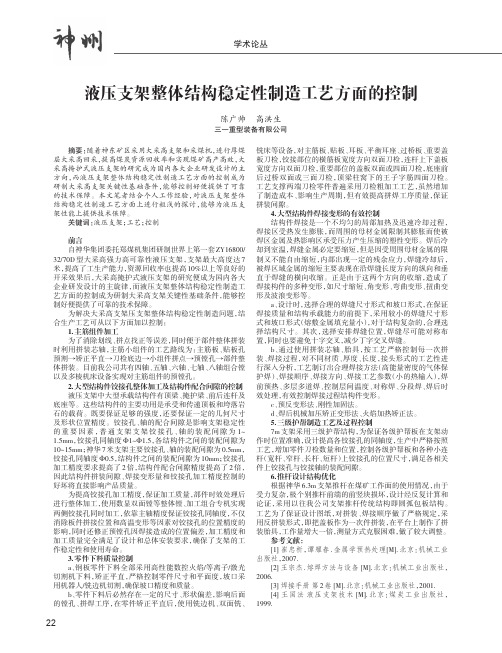
学术论丛液压支架整体结构稳定性制造工艺方面的控制陈广帅高洪生三一重型装备有限公司摘要:随着神东矿区采用大采高支架和采煤机,进行厚煤层大采高回采,提高煤炭资源回收率和实现煤矿高产高效,大采高掩护式液压支架的研究成为国内各大企业研发设计的主方向,而液压支架整体结构稳定性制造工艺方面的控制成为研制大采高支架关键性基础条件,能够控制好便提供了可靠的技术保障。
本文笔者结合个人工作经验,对液压支架整体结构稳定性制造工艺方面上进行粗浅的探讨,能够为液压支架性能上提供技术保障。
关键词:液压支架;工艺;控制前言自神华集团委托郑煤机集团研制世界上第一套ZY16800/32/70D 型大采高强力高可靠性液压支架,支架最大高度达7米,提高了工生产能力,资源回收率也提高10%以上等良好的开采效果后,大采高掩护式液压支架的研究便成为国内各大企业研发设计的主旋律,而液压支架整体结构稳定性制造工艺方面的控制成为研制大采高支架关键性基础条件,能够控制好便提供了可靠的技术保障。
为解决大采高支架压支架整体结构稳定性制造问题,结合生产工艺可从以下方面加以控制:1.主筋组件加工为了消除划线、拼点找正等误差,同时便于部件整体拼装时利用拼装芯轴,主筋小组件的工艺路线为:主筋板、贴板孔预割→矫正平直→刀检底边→小组件拼点→预镗孔→部件整体拼装。
目前我公司共有四轴、五轴、六轴、七轴、八轴组合镗以及多棱机床设备实现对主筋组件的预镗孔。
2.大型结构件铰接孔整体加工及结构件配合间隙的控制液压支架中大型承载结构件有顶梁、掩护梁、前后连杆及底座等。
这些结构件的主要功用是承受和传递顶板和垮落岩石的载荷。
既要保证足够的强度,还要保证一定的几何尺寸及形状位置精度。
铰接孔、轴的配合间隙是影响支架稳定性的重要因素,普通支架支架铰接孔、轴的装配间隙为1~1.5mm ,铰接孔同轴度Φ1~Φ1.5,各结构件之间的装配间隙为10~15mm ;神华7米支架主要铰接孔、轴的装配间隙为0.5mm ,铰接孔同轴度Φ0.5,结构件之间的装配间隙为10mm ;铰接孔加工精度要求提高了2倍,结构件配合间隙精度提高了2倍,因此结构件拼装间隙、焊接变形量和铰接孔加工精度控制的好坏将直接影响产品质量。
液压支架关键零部件材料性能分析及工艺研究
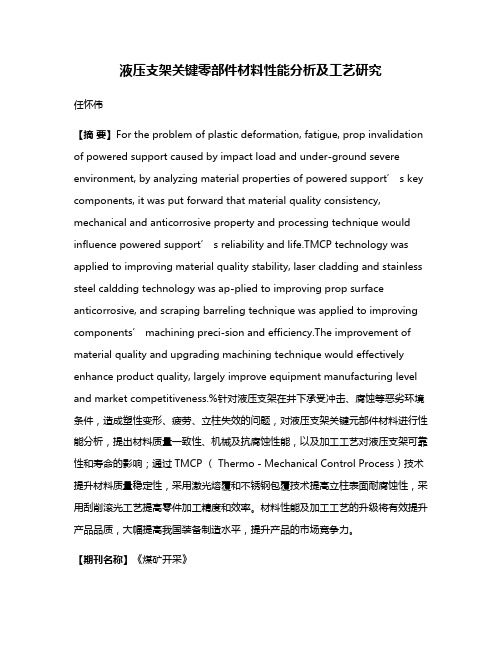
液压支架关键零部件材料性能分析及工艺研究任怀伟【摘要】For the problem of plastic deformation, fatigue, prop invalidation of powered support caused by impact load and under-ground severe environment, by analyzing material properties of powered support’ s key components, it was put forward that material quality consistency, mechanical and anticorrosive property and processing technique would influence powered support’ s reliability and life.TMCP technology was applied to improving material quality stability, laser cladding and stainless steel caldding technology was ap-plied to improving prop surface anticorrosive, and scraping barreling technique was applied to improving components’ machining preci-sion and efficiency.The improvement of material quality and upgrading machining technique would effectively enhance product quality, largely improve equipment manufacturing level and market competitiveness.%针对液压支架在井下承受冲击、腐蚀等恶劣环境条件,造成塑性变形、疲劳、立柱失效的问题,对液压支架关键元部件材料进行性能分析,提出材料质量一致性、机械及抗腐蚀性能,以及加工工艺对液压支架可靠性和寿命的影响;通过TMCP ( Thermo-Mechanical Control Process)技术提升材料质量稳定性,采用激光熔覆和不锈钢包覆技术提高立柱表面耐腐蚀性,采用刮削滚光工艺提高零件加工精度和效率。
- 1、下载文档前请自行甄别文档内容的完整性,平台不提供额外的编辑、内容补充、找答案等附加服务。
- 2、"仅部分预览"的文档,不可在线预览部分如存在完整性等问题,可反馈申请退款(可完整预览的文档不适用该条件!)。
- 3、如文档侵犯您的权益,请联系客服反馈,我们会尽快为您处理(人工客服工作时间:9:00-18:30)。
高端液压支架结构件制造工艺的先进性分析摘要:本文分别从高端液压支架结构件制造相关工序抛丸、下料、修磨、抛丸、矫平、压弯、成型、焊接、镗孔等进行了细致的阐述,分析了我公司高端液压支架结构件制造工艺的先进性,并通过近年来良好的使用效果进一步进行了确定。
关键词:抛丸成型焊接多层多道低强匹配液压支架是煤矿开采重大装备,液压支架技术发展水平是国家煤机装备发展水平的重要标志。
近年来,随着我国开采技术的飞速提升和大矿井的高效需求及强力支护的需要,国内液压支架行业迅猛发展,自主产品已完全取代进口产品,且我国的液压支架正向着高端支架方向发展。
支架所用的材料由16Mn、Q460、Q550向Q690、Q890发展,这对液压支架的制造工艺又有了更高的要求。
我们公司是与波兰可派克斯公司合作的一家合资企业,专业设计、制造液压支架,目前已制造出ZQY9000/24/50D、ZF15000/23/43、ZY17000/32/70D型高端液压支架,制造技术驰骋在国内领先水平行列。
下面,我就将多年来在实践中学习、总结的高端液压支架结构件中外结合的制造工艺的先进性进行系统分析。
1 结构件制造主要工艺1.1 抛丸-下料-修磨-抛丸首先对合格的钢板进行抛丸处理,然后按程序气割下料、修磨氧化渣,最后再进行抛丸处理(预钻孔件和倒角件须在钻孔和倒角后进行该工序的抛丸处理)。
通过两次抛丸处理,钢板的表面增加了0.2mm 厚度的强化密实层,增加了防腐能力,提高了使用寿命;同时,除锈后下料切割能提高工件的切割质量。
下料时,对于长主筋板、U型件等须预留防变形连体拉筋,待工件冷却后再进行切割;对于需压弯的开口部位,可只割好开口两侧缝隙,防止压弯时产生“口裂”现象。
1.2 矫平-压弯-成型1.2.1 矫平-压弯矫平、压弯工序是成型零件的终结工步,直接制约着部件的成型质量。
矫平时必须将工件毛刺、飞边清理干净,对于变形的主筋板,我公司在大型平板机上进行矫平,对于其他小尺寸筋板,通常在压力机上进行矫平。
压弯之前,钢板至少保持10℃,否则需要预热到最少25℃,对于易裂件要加热到800℃~900℃,并保证热透方可压弯。
折弯时方向尽量和钢板纹络方向垂直,折弯部分的内边需要进行打磨,可以利用铣床加工。
工件的直线度及平面度均不得大于1/1000,对于较长的主筋板,由于切割后变形量超差,可以利用机加工方式进行刀找,否则在成型时将会产生较大的成型间隙,影响焊接质量。
对于拼焊后的变形的主筋板,可以在压力机上矫平,并在压力机工作平台以外增设弹性浮动支撑架。
1.2.2 成型成型是液压支架结构件制造的关键工序之一。
成型前,各零件必须检验合格,按液压支架结构件制造技术条件MT/T587-2011标准执行。
成型时,焊缝根部间隙为0~2mm,如果存在较大间隙,必须将工件矫平或刀找,决不能采用强力挤压变形的方式来减小间隙,强力装配会进一步加大焊接后工件的内应力。
对于铸造的件,需在成型前修磨其焊道两侧30mm内毛坯表面的氧化皮及杂质,直到“见亮”。
成型有两种方式:一种是在工件底板上划线后按线拼装;另一种是采用专用成型工装模具进行。
前者主要针对单体和小批量部件,后者则针对较大批量部件。
不论哪种方式,对于有装配尺寸的裆距都应适当加大2mm~3mm,以抵消焊接后的工件收缩量,这就要求划线或制造成型工装模具时将该尺寸让出来。
成型模具往往采用单侧定位、另侧楔铁挤紧的方式,这样便于在成完型后快速取出部件。
由于结构件框架焊接收缩量的存在,盖面板类宽度一般比内裆筋板宽度小1.5mm~2mm,便于结构件盖面工序的顺利进行。
成型定位焊缝:焊角高度为6mm~8mm,长度为40mm~60mm,间隔300mm左右,当焊缝长度不足300mm时,单侧定位焊不得少于两处。
点焊参数:电压U=19V~23V,电流I=180A~230A,气体流量V=12~15(升/分)。
点焊时,需从工件中间向两侧进行,点焊前的预热依照焊接预热的方式。
点焊材质:通常用50公斤级焊丝,当板材是60公斤级以上时,可以用60公斤级焊丝。
点焊前必须将焊道两侧25mm范围内清理干净。
成型时需在各内裆加固撑筋,以防止或减小焊接变形。
撑筋的强度要绝对足够,撑筋必须与主筋板垂直加固,通常点焊在离焊缝100mm左右的位置,能有效防止主筋板焊后发生的弹性收缩,又能利于主筋板焊道的施焊工作。
为更好的防止焊接变形,对于连杆和小型顶梁部件,可以采用“背对背”点焊方式;而对于底座或大型顶梁类部件,则采用加固“背筋”的方式以防止焊接变形。
1.3 焊接1.3.1 焊接材料焊接材料一般选择原则:Q460、Q550、27SiMn、ZG25MnTiB 之间的相互焊接所用焊丝牌号:SLD-60(H08Mn2Si60E);Q550高强板相互焊接应选用焊丝牌号:GHS-70;Q690高强板相互焊接应选用焊丝牌号:GHS-80;Q345(16Mn)钢材相互焊接与其它材料的焊接所用焊丝牌号:ER50-6(H08Mn2SiA)。
不同材质的材料相互焊接时,依照低强匹配的原则。
为减少焊接变形和内应力,尽量减少热值的输入;为提高焊道的塑性和韧性,防止热影响区材质脆化,尽量减少母材向焊道的溶解量,为此,我们采用细焊丝、小电流焊接方式;焊丝规格为φ1.2,应符合GB/T8110-1995规定。
由于高端液压支架主要在井下承受较大的压力,对焊道的韧性和塑性要求较高,为减少焊道材质的碳当量,防止焊道裂纹,对于打底焊的焊道,焊接Q550以上高强板时,为控制焊道的碳当量,保持焊道的塑性和韧性,通常选择低一级强度的焊丝。
焊接填充焊道和盖面焊道时,一般采用等强匹配。
对于Q690以上的板材,在适当加大焊道尺寸的前提下,可以采用低强匹配的焊接方式。
1.3.2 保护气体为更好地保护焊道的质量,我公司采用二氧化碳和氩气混合的富氩气体保护方法,其中氩气占80%,氧气占20%。
该类混合气体保护焊能有效减少焊接飞溅、使焊道高温状态下有效隔绝空气不被氧化,且能使焊道成型美观。
1.3.3 焊接温度焊接温度包括点焊温度、预热温度、层间温度。
材质不同其焊接温度不同,其点焊温度依照预热温度执行,Q460材质的焊前预热温度为80℃~120℃,Q550材质的为100℃~150℃,Q690材质的为150℃~200℃。
预热后要等大约1min,待温度均匀、稳定后用红外线测温仪测温。
预热温度的测量范围必须是焊道两侧75mm宽度处,条件允许的话,应当从火焰烘烤板面的背面进行测温。
层间温度规定:Q460板材达到75℃~120℃,Q550板材达到80℃~150℃,Q690板材达到120℃~200℃。
焊接温度对焊道的质量至关重要,过低将会使焊道出现淬硬缺陷,过高则易形成粗大的魏氏体组织,降低焊道的塑性和韧性。
1.3.4 具体焊接工艺参数(表1)1.3.5 焊前清理、加热焊接前必须将焊道两侧25mm范围以内清理干净所有杂质、油污及水份,对于发生裂纹的定位焊缝必须清除后重新点焊,防止发生诱导性延展裂纹。
清理干净后开始用中性火焰加热,必须采用大面积烘烤预热的方式,随温度升高再逐渐做好局部加热,单侧加热范围不低于150mm,并采用摆动方式。
为防止局部变形致使应力加大现象,坚决杜绝使用集中加热和点加热方式。
1.3.6 焊接方式由于高端液压支架多采用Q550、Q690高强板,其碳当量WCE 值较大,焊接时有明显的淬硬倾向,热影响区容易形成硬脆的马氏体组织,使焊道的塑性和韧性下降,潜伏较大的冷裂倾向。
因此,焊接时应以较小的热输入量,参照“多层多道焊接示意图”进行焊接,图中焊道道数为该尺寸焊道的最少道数。
对于存在较大工艺间隙的部位,必须先将此间隙充填焊接完成,为顺利进行整体多层多道焊接做好基础。
待预热温度达到要求后先进行焊道打底焊接,并以先焊纵焊缝、再焊横焊缝的方式,即先焊变形量较大的,后焊变形量较小的焊缝。
整体打底后,再以此方式进行后续多层多道焊接。
多层多道焊接有较多优点:前道焊缝对后道焊缝有预热的作用,后道焊缝对前道焊缝有退火的作用;多层多道焊接的热输入值较小,防止形成粗大的魏氏体组织,能起到对焊缝组织晶粒细化的作用,可以提高焊缝的韧性和塑性(如图1)。
多层多道焊接时,对于搭接的焊道,为防止接头处出现较大的应力集中现象,焊接接头必须错位25mm以上。
在工件的拐角处不能停止焊接,一直焊接到离角落大约50毫米的地方方可暂停。
为减小工件变形量,一般是由两名焊接人员采用对称焊接方式。
为保持焊件温度,通常采用烤、焊不停的方式,即专人对工件用烤枪烘烤,同时专人进行焊接,能使工件一直处于回火温度状态,有助于细化焊缝晶粒和去除焊接应力,并能提高工作效率和节约烘烤气体。
1.3.7 层间清理焊接过程中必须做好层间清理,我公司采用风铲对焊道进行层间清理,使用此方法一方面清除焊道层间杂质;另一方面风铲的强力高频冲击又对焊道进行了舒展及应力释放,减少了焊接应力。
在使用风铲时,必须在焊后及时进行,否则就达不到对焊道进行舒展及应力释放的效果。
1.3.8 焊接应力的消除经过长期的探索、总结,我公司对液压支架主要结构件焊接应力的消除采用多层多道焊接过程的自行回火与振动时效相结合的方式。
焊道焊接完成后,在冬季要及时用耐高温石棉被进行盖捂。
对焊接完成的工件,必须及时进行振动时效处理,此方式较以往热处理退火去除应力的方法能节约成本和提高效率。
时振动时效的振动时间按结构件重量确定。
结构件≤1T:振10min;1T<结构件≤3T:振12min;3<结构件≤6T:振15min;6<结构件≤12T:振20min。
1.4 镗孔我公司液压支架主要结构件的各铰接孔在对头镗床上加工,比以往采用普通镗床加工提高了各孔系加工的同轴度和效率,并省略了划线工序。
加工时,只需将工件吊装在工作台上,依铰接孔处配合件有效旋转空间尺寸为基准,并参考工件加工余量,通过调整底部的调高垫铁和Z轴及X轴方向的定位器,即可快速确定工件空间位置,紧固后镗孔。
镗工完成后清理铁屑、毛刺和冷却液,并在加工处及时涂油。
2 结语我公司通过长期的摸索和总结,在波兰液压支架制造工艺的基础上进一步研究和实验,目前已将液压支架制造工艺的先进性提升到国内一流水平。
通过改良,目前液压支架结构件制造工艺较以往明显提高了制造质量和效率,得到了用户的高度评价,具有良好的经济效益和社会效益。