流程工业生产设备管理系统的设计与实现
PLC的工业控制系统的设计与实现
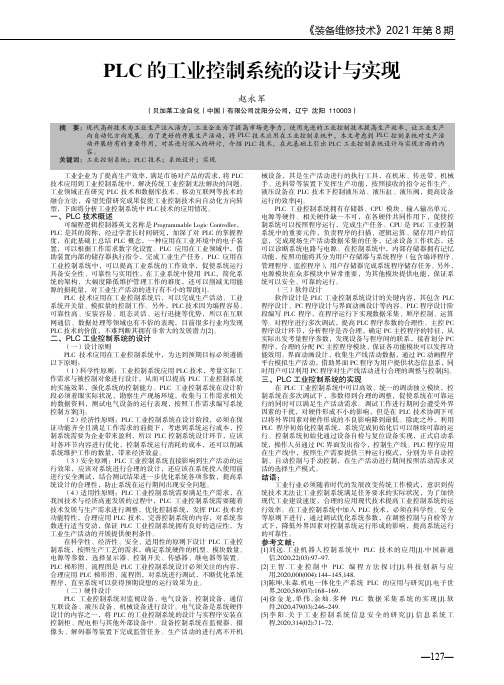
《装备维修技术》2021年第8期—127—PLC 的工业控制系统的设计与实现赵永军(贝加莱工业自化(中国)有限公司沈阳分公司,辽宁 沈阳 110003)工业企业为了提高生产效率,满足市场对产品的需求,将PLC 技术应用到工业控制系统中,解决传统工业控制无法解决的问题。
工业领域正在研究PLC 技术和数据库技术、移动互联网等技术的融合方法,希望凭借研究成果促使工业控制技术向自动化方向转型,下面将分析工业控制系统中PLC 技术的应用情况。
一、PLC 技术概述可编程逻辑控制器英文名称是Programmable Logic Controller,PLC 是其的简称,经过学者长时间研究,加深了对PLC 的掌握程度,在此基础上总结PLC 概念,一种应用在工业环境中的电子装置,可以根据工作需求数字化设置。
PLC 应用在工业领域中,借助装置内部的储存器执行指令,完成工业生产任务。
PLC 应用在工业控制系统中,可以提高工业系统的工作效率,促使系统运行具备安全性、可靠性与实用性,在工业系统中使用PLC,简化系统的架构,大幅度降低维护管理工作的难度,还可以削减无用能源的损耗量,对工业生产活动的进行有不小的帮助[1]。
PLC 技术应用在工业控制系统后,可以完成生产活动、工业系统开关量、模拟量的控制工作。
另外,PLC 技术因为编程容易、可靠性高、安装容易、组态灵活、运行迅捷等优势,所以在互联网通信、数据处理等领域也有不俗的表现,目前很多行业均发现PLC 技术的价值,不难判断其拥有非常大的发展潜力[2]。
二、PLC 工业控制系统的设计(一)设计原则 PLC 技术应用在工业控制系统中,为达到预期目标必须遵循以下原则: (1)科学性原则:工业控制系统应用PLC 技术,考量实际工作需求与被控制对象进行设计,从而可以提高PLC 工业控制系统的实施效果,强化系统的控制能力。
PLC 工业控制系统在设计阶段必须着眼实际状况,勘察生产现场环境,收集与工作需求相关的数据资料,测试电气设备的运行表现,按照工作需求编写系统控制方案[3]。
工业控制系统设计流程
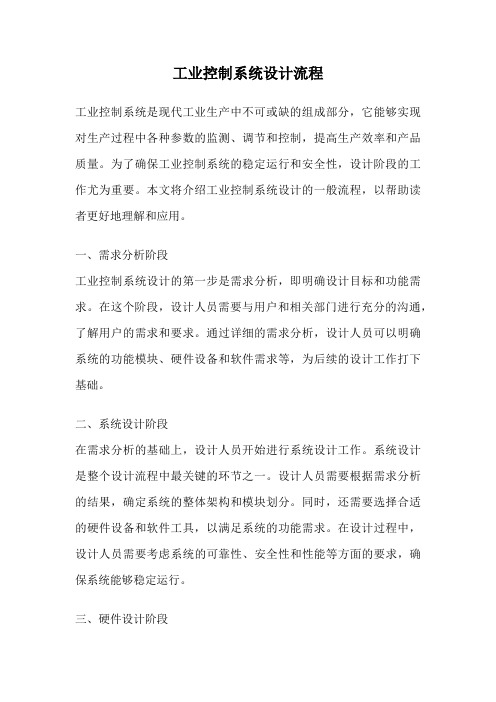
工业控制系统设计流程工业控制系统是现代工业生产中不可或缺的组成部分,它能够实现对生产过程中各种参数的监测、调节和控制,提高生产效率和产品质量。
为了确保工业控制系统的稳定运行和安全性,设计阶段的工作尤为重要。
本文将介绍工业控制系统设计的一般流程,以帮助读者更好地理解和应用。
一、需求分析阶段工业控制系统设计的第一步是需求分析,即明确设计目标和功能需求。
在这个阶段,设计人员需要与用户和相关部门进行充分的沟通,了解用户的需求和要求。
通过详细的需求分析,设计人员可以明确系统的功能模块、硬件设备和软件需求等,为后续的设计工作打下基础。
二、系统设计阶段在需求分析的基础上,设计人员开始进行系统设计工作。
系统设计是整个设计流程中最关键的环节之一。
设计人员需要根据需求分析的结果,确定系统的整体架构和模块划分。
同时,还需要选择合适的硬件设备和软件工具,以满足系统的功能需求。
在设计过程中,设计人员需要考虑系统的可靠性、安全性和性能等方面的要求,确保系统能够稳定运行。
三、硬件设计阶段硬件设计是工业控制系统设计中的重要环节。
在硬件设计阶段,设计人员需要根据系统的功能需求,选择合适的传感器、执行器、控制器等硬件设备,并进行电路设计和布线。
设计人员还需要考虑硬件设备的可靠性和稳定性,以及与其他设备的接口兼容性。
通过合理的硬件设计,可以确保系统的数据采集和控制功能能够正常运行。
四、软件设计阶段软件设计是工业控制系统设计中不可或缺的一部分。
在软件设计阶段,设计人员需要根据系统的功能需求,编写相应的控制算法和逻辑程序。
同时,还需要进行软件架构设计和界面设计,以提高系统的可操作性和用户体验。
软件设计过程中,设计人员需要注重代码的可读性和可维护性,确保软件的稳定性和可靠性。
五、系统集成和调试阶段系统集成和调试是工业控制系统设计流程中的最后一步。
在这个阶段,设计人员需要将硬件设备和软件模块进行集成,并进行系统级测试和调试。
通过测试和调试,可以发现和解决系统中存在的问题,确保系统的功能和性能能够满足设计要求。
工厂自动化排产调度系统设计与实现

工厂自动化排产调度系统设计与实现近年来,随着科技的不断发展和工业生产的进一步发展,工厂自动化已经成为了当下智能制造的重要标志之一。
工厂自动化排产调度系统是工厂自动化的重要组成部分,它能够根据生产计划和生产数据自动对生产过程进行调度和优化,从而提高生产效率和产能。
本文将介绍工厂自动化排产调度系统的设计与实现。
一、需求分析在设计工厂自动化排产调度系统之前,需要对系统进行需求分析,以确保系统在实现过程中能够满足工厂的生产需求。
我们的工厂需要一个能够实现以下功能的工厂自动化排产调度系统:1. 按照生产计划自动排产,同时能够对排产计划进行调整和优化,以确保生产线的最高效率。
2. 实时监测并记录生产线上的生产数据,对数据进行分析,找出瓶颈并进行优化,以降低生产成本和提高生产效率。
3. 能够自动调配生产线上的人员和设备,并根据生产情况进行动态调整,以达到最优排产效果。
4. 实现生产过程的全面管理,包括产品原材料进货、加工、质检和包装等全过程的跟踪和管理。
二、系统设计在需求分析的基础上,我们开始进行工厂自动化排产调度系统的设计。
这里,我们将系统分成了以下几个部分:生产计划管理模块、生产调度管理模块、生产数据监控管理模块和原材料进货管理模块。
1. 生产计划管理模块生产计划管理模块是工厂自动化排产调度系统的核心,它能够根据生产计划自动排产,并且能够根据生产过程中的实际情况实时调整和优化生产计划。
该模块的具体功能如下:a. 生产计划制定:该模块能够根据生产计划制定工艺流程和生产工序,并将其转换成具体的生产排产计划。
b. 生产排产:该模块能够根据生产计划实时进行排产,并将排产计划发送给生产线上的设备和人员。
c. 生产调整:该模块能够根据生产实时情况进行动态调整和优化生产计划,以达到最优排产效果。
2. 生产调度管理模块生产调度管理模块主要负责对生产设备和人员进行调度和管理,以确保生产线的稳定运行和高效率生产。
该模块的具体功能如下:a. 设备管理:该模块能够对生产设备进行调度和管理,并根据设备的实际情况进行调整和优化。
MES流程工业生产管理系统

MES流程工业生产管理系统MES(Manufacturing Execution System,流程工业生产管理系统)是指通过计算机技术和自动化技术对生产过程进行管理和控制的一种系统。
它通过将生产过程中的各个环节进行全面的监控和协调,实现了生产过程的信息化、集成化和智能化管理。
MES系统在现代工业生产中发挥着重要的作用,被广泛应用于各个工业领域。
MES系统在流程工业生产中扮演着中枢的角色,它与ERP(Enterprise Resource Planning,企业资源计划)系统和SCADA (Supervisory Control and Data Acquisition,监控与数据采集)系统等相结合,完成从生产计划到生产实施的全过程管理。
MES系统通过对工艺流程、设备、物料和人员的数据进行采集和分析,实现了对生产过程的实时控制和调度,并提供及时准确的信息反馈和决策支持,达到提高生产效率、降低生产成本、保证产品质量的目的。
MES系统由多个核心模块组成,例如工艺流程管理、生产计划与调度、物料管理、设备管理、质量管理、仓储管理等。
其中,工艺流程管理模块是MES系统的核心,它主要负责对生产过程进行监控和控制,包括工艺参数采集、过程控制、异常处理等。
生产计划与调度模块负责制定生产计划并进行合理的排产安排,确保生产任务的按时完成。
物料管理模块负责对物料库存进行管理和追踪,确保生产过程中所需物料的供应和消耗的控制。
设备管理模块对生产设备进行监控和维护管理,确保设备的正常运行。
质量管理模块负责对产品质量进行监控和检验,确保产品符合质量标准。
仓储管理模块负责对产品的入库和出库进行管理,确保产品的正常流通。
MES系统的实施和应用对企业的生产管理起到了积极推动作用。
它不仅提高了生产效率和质量,降低了生产成本,还缩短了生产周期,提高了企业的竞争力。
由于MES系统的实时性和准确性,企业能够及时发现和处理生产过程中的异常情况,避免了生产事故的发生。
工业自动化的自动化生产流程设计

目录
工业自动化概述自动化生产流程设计基础自动化生产流程的设计步骤自动化生产流程的关键技术自动化生产流程的应用案例
01
CHAPTER
工业自动化概述
工业自动化是指在工业生产过程中,通过自动控制、检测、优化、调度和管理等一系列手段,实现生产过程的自动化和智能化,提高生产效率、降低成本、提升产品质量。
总结词
卫生安全、高程注重卫生安全和标准化,通过自动化设备实现高效、连续的生产,提高产品质量和降低人工干预。
THANKS
感谢您的观看。
调试与优化
对生产线员工进行自动化操作和维护培训,提高员工的技能水平。
人员培训
按照设计的自动化生产流程进行生产,确保产品质量和产量达标。
生产实施
根据实际生产情况,对自动化生产流程进行持续优化,提高生产效益。
持续优化
04
CHAPTER
自动化生产流程的关键技术
传感器技术是自动化生产流程中的重要组成部分,用于检测和测量各种物理量,如温度、压力、流量和位置等。
确定自动化水平
根据企业战略和成本效益分析,确定自动化生产线的自动化水平。
需求变更管理
在需求分析阶段,应充分考虑未来可能的需求变更,以便灵活应对。
03
02
01
将各模块和设备集成到自动化生产系统中,实现信息交互和协同工作。
系统集成
对集成后的系统进行功能和性能测试,确保系统稳定可靠。
系统测试
根据测试结果,对系统进行调试和优化,提高生产效率。
传感器技术通过将物理量转换为电信号或数字信号,为自动化系统提供实时、准确的数据,以实现精确控制和优化生产过程。
传感器技术的发展趋势包括高精度、高可靠性和智能化,以满足不断升级的自动化生产需求。
工业控制系统的设计与实现

工业控制系统的设计与实现工业控制系统是一个基于自动化技术与计算机技术相互融合的高新技术系统,是现代工业化生产不可或缺的一部分。
在工业生产过程中,人们需要依靠工业控制系统,对生产过程进行重点监测和控制,以确保生产过程顺利、稳定、高效。
本文将从工业控制系统设计的角度,谈谈这种系统的实现过程,包括设计、编程、测试、应用等步骤。
一、需求分析在工业控制系统的设计中,首先需要进行需求分析。
这个阶段的主要任务是制定系统目标,明确控制对象,确定控制策略和控制算法等。
在制定系统目标时,需要综合考虑生产过程中的实际工艺流程、生产环境、设备性能等因素。
然后,根据生产过程的特点,确定需要控制的对象,例如温度、压力、流量、速度等。
此外,还需要根据实际生产环境、问题文化和运营方式等因素,制定合适的控制策略和算法,以提高产品质量、降低人力成本和提高生产效率。
二、系统设计在需求分析的基础上,可以开始系统的设计阶段。
这个阶段需要确定系统结构、软件架构、网络配置等关键技术,以便实现控制系统的自动化。
具体操作方法包括以下几个步骤:1、制定控制系统的硬件配置方案。
在这一步骤中,需要考虑采集信号的方式、采集信号的传输方式、控制执行机构的选型等。
2、设计控制系统的软件架构。
软件架构是工业控制系统的基石。
在这一步骤中,需要确定控制系统的软件体系、程序结构、控制算法等内容。
3、设计控制系统的网络配置。
在这一步骤中,需要确定网络的拓扑结构、通信协议、数据传输方式等内容。
三、程序编写在控制系统设计完成后,需要进行程序编写。
程序编写的任务是把控制系统设计的各个环节紧密地融合起来,实现工业控制系统的自动化。
具体程序编写的方法包括以下几个方面:1、确定程序结构。
在这一步骤中,需要确定程序的组织结构,包括数据结构、控制流程、逻辑调整等内容。
2、编写程序代码。
在这一步骤中,需要编写程序代码,包括控制算法代码、网络通讯代码、界面代码等。
3、编写程序调试代码。
流程工业生产设备管理系统的设计与实现

2 . I n s t i t u t e o f A u t o m a t i o n , C h i n e s e A c a d e my o f S c i e n c e s , B e i j i n g 1 0 0 1 9 0 , C h i n a )
Ab s t r a c t T h e s y s t e m t a k e s r e a l — — t i me d a t a b a s e a s a c o r e t o c o l l e c t r e l- a t i me o p e r a t i n g d a t a o f e q u i p me n t b a s e d o n a l l - p u r p o s e
( 1 . J i a n g x i N e i r n E l e c t i r c& A u t o ma t i o n C o . , L t d , N a n , C h i n a ;
De s i g n a n d I mp l e me n t a t i o n o f P r o d u c io t n Eq u i p me n t Ma n a g e me n t S y s t e m o f P r o c e s s I n d u s t r y HU Yu — q i n , HUANG Z h e n — l i ,L I U Do n g — p o
多个 工程 项 目, 实践证 明 系统 投 运后 减 少 了设 备停 机 时间, 提 高 了设 备 管理 水 平, 具 有较 强 的 实用价值 和 应 用 前 景
[ 关 键词 ] 设备 管理 系统 ; 实时数 据库 ; RF I D; 信 息化
生产流程控制系统设计与优化
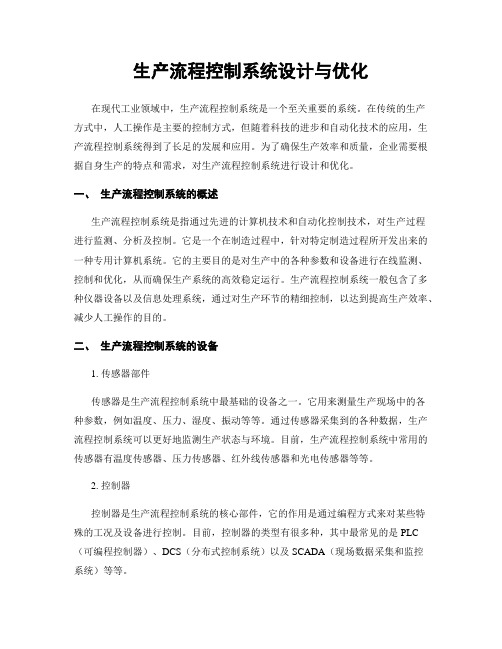
生产流程控制系统设计与优化在现代工业领域中,生产流程控制系统是一个至关重要的系统。
在传统的生产方式中,人工操作是主要的控制方式,但随着科技的进步和自动化技术的应用,生产流程控制系统得到了长足的发展和应用。
为了确保生产效率和质量,企业需要根据自身生产的特点和需求,对生产流程控制系统进行设计和优化。
一、生产流程控制系统的概述生产流程控制系统是指通过先进的计算机技术和自动化控制技术,对生产过程进行监测、分析及控制。
它是一个在制造过程中,针对特定制造过程所开发出来的一种专用计算机系统。
它的主要目的是对生产中的各种参数和设备进行在线监测、控制和优化,从而确保生产系统的高效稳定运行。
生产流程控制系统一般包含了多种仪器设备以及信息处理系统,通过对生产环节的精细控制,以达到提高生产效率、减少人工操作的目的。
二、生产流程控制系统的设备1. 传感器部件传感器是生产流程控制系统中最基础的设备之一。
它用来测量生产现场中的各种参数,例如温度、压力、湿度、振动等等。
通过传感器采集到的各种数据,生产流程控制系统可以更好地监测生产状态与环境。
目前,生产流程控制系统中常用的传感器有温度传感器、压力传感器、红外线传感器和光电传感器等等。
2. 控制器控制器是生产流程控制系统的核心部件,它的作用是通过编程方式来对某些特殊的工况及设备进行控制。
目前,控制器的类型有很多种,其中最常见的是PLC (可编程控制器)、DCS(分布式控制系统)以及SCADA(现场数据采集和监控系统)等等。
3. 无线传输设备无线传输设备也是一个十分重要的部件。
它的作用就是把从传感器这些各种设备中采集到的数据以无线信号的形式传输到指定的存储设备中进行处理。
目前,无线传输设备的种类非常多,例如RTU、DTU、传感器模块等等,通过这些设备,可以实现生产生产流程的实时监测和数据采集。
三、生产流程控制系统的优化方法1. 降低能耗电能和燃料是现代工业生产过程中必不可少的,但由于它们的消耗量的增加,直接影响到生产成本及企业的竞争力。
- 1、下载文档前请自行甄别文档内容的完整性,平台不提供额外的编辑、内容补充、找答案等附加服务。
- 2、"仅部分预览"的文档,不可在线预览部分如存在完整性等问题,可反馈申请退款(可完整预览的文档不适用该条件!)。
- 3、如文档侵犯您的权益,请联系客服反馈,我们会尽快为您处理(人工客服工作时间:9:00-18:30)。
0引言制造执行系统(Manufacturing Execution System ,MES)是位于上层的计划管理系统与底层的工业控制系统之间的面向车间层面的信息管理系统。
它将企业ERP/MRP 与企业的现场控制有机地集成起来[1],为管理人员提供计划的执行并跟踪所有资源(人、设备、物料)的当前状态,实现生产过程优化管理。
生产设备管理系统是MES 体系中围绕生产设备的管理系统,主要完成企业生产设备管理的各方面工作,实现设备管理的数字化和信息化。
本文在MES 技术环境下,针对流程工业设备管理存在的问题,基于实时数据库和RFID 技术机理,设计和开发了一套生产设备管理系统。
该系统包含设备档案管理、设备检修计划管理、设备点巡检管理、设备故障分析、设备能效分析等子系统,并结合实时数据库、RFID 技术、专家知识库、信息化技术实现了设备管理水平的有效提升,有效地解决了设备管理中存在的问题,推动了设备有效、稳定、经济的使用,从而降低了生产成本,提高了企业效益。
流程工业生产设备管理系统的设计与实现胡玉琴1,黄振利1,刘东坡2(1.江西瑞林电气自动化有限公司,江西南昌330031;2.中国科学院自动化研究所,北京市100190)〔摘要〕基于实时数据库和RFID 技术的通用生产设备管理系统,以实时数据库为核心,实现设备实时运行数据的采集;采用RFID 技术实现设备的点巡检管理;通过信息化方式实现设备档案信息和设备检修计划管理;基于实时数据和设备故障专家知识库实现设备实时效能分析和设备故障诊断功能。
该系统已成功应用于多个工程项目,实践证明系统投运后减少了设备停机时间,提高了设备管理水平,具有较强的实用价值和应用前景。
〔关键词〕设备管理系统;实时数据库;RFID ;信息化中图分类号:TP274文献标识码:B文章编号:1004-4345(2013)03-0057-04Design and Implementation of Production Equipment Management System of Process IndustryHU Yu-qin 1,HUANG Zhen-li 1,LIU Dong-po 2(1.Jiangxi Nerin Electric &Automation Co.,Ltd ,Nanchang,Jiangxi 330031,China;2.Institute of Automation,Chinese Academy of Sciences,Beijing 100190,China)Abstract The system takes real-time database as a core to collect real-time operating data of equipment based on all-purpose production equipment management system with real-time database and RFID technology;RFID technology is adopted to achieve point inspection management of equipment;information method is adopted to implement equipment file information management and equipment repair plan;based on real -time data and equipment fault expert knowledge base,real -time performance analysis of equipment and fault diagnosis function of equipment can be achieved.The system has been successfully applied in several projects,it proved from practice that the system can reduce time of equipment shutdown,improve the level of equipment management and has strong practical value and application prospect after being put into production.Keywords Equipment management system;Real-time data base;RFID;informatization收稿日期:2013-02-05作者简介:胡玉琴(1975—),女,主要从事过程自动化工程项目研究及市场推广工作。
有色冶金设计与研究第34卷2013年第3期6月1设备管理系统分析1.1流程工业设备特点流程工业在设备方面的特点包括:1)流程工业的设备是一条相对固定的生产线,设备投资比较大,因此生产线上的设备维护特别重要,一旦发生故障,则成本较高[2]。
2)流程工业大多采用规模化的生产方式,生产工艺技术相对成熟,广泛采用了过程控制系统,且控制生产工艺条件的自动化设备比较成熟[3]。
3)流程工业的自动化程度较高,设备控制级普遍采用DCS 、PLC 及各种智能仪表、数字传感器等。
1.2MES与设备管理系统美国先进制造研究机构AMR (Advanced Manufacturing Research )提出的企业集成模型描述了MES 在企业系统中的位置和作用,如图1所示。
由图1可知,MES 在工厂计划管理系统和车间底层生产控制系统间起到的是非常重要的承上启下作用。
而设备管理系统作为MES 中的重要组成部分,是为了提高企业的市场竞争力和管理水平,运用计算机和网络技术建立的信息化管理体系[4]。
本文设计的设备管理系统采集设备的运行情况、技术状态、维修更新情况等信息,为维护保养及维修计划的制定提供决策帮助;对设备数据资料进行规范化管理,并将设备状态、设备的综合利用率以及设备的使用、调配和维护等信息实时、准确地提供给各职能管理人员,同时生成各种设备统计分析报告,为企业经营计划、主生产计划和车间作业计划等子系统提供参数,以便对企业的长期和短期生产计划进行必要的调整和修正;合理地制定设备检修计划,以减少偶然事故所造成的经济损失;加强设备履历、日常维护管理和监控,以提高设备利用率。
1.3实时数据库实时数据库(RTDB -Real Time Data Base)是数据库系统发展的一个分支,是数据库技术结合实时处理技术产生的。
其作为MES 和DCS 的桥梁和纽带,是MES 实现与DCS 系统进行数据采集与数据下发的重要平台和枢纽。
一方面,MES 通过实时数据库将设备运行数据、DCS 过程采集数据、现场生产数据采集上来,并保存在MES 的业务数据库中,供各功能模块统计、分析;另一方面,MES 将生产管理信息、ERP 生产计划信息通过实时数据库下达到各DCS 系统,并由DCS 自动或由现场生产人员根据信息执行各类生产操作。
1.4RFID技术无线射频辨识系统(RFID)是一种无线射频辨识技术,由读取器(Reader)、电子卷标(Tag)、天线(Antenna)和后端应用系统等组成。
其动作原理是由读取器发射特定频率给感应器,用以驱动感应器电路将芯片内部数据传回。
RFID 技术凭借其无线传输特性与物品标识的唯一性和安全性,在标签上能覆盖产品、设备重要信息数据,能够实现产品的追溯、设备的到位检查等。
RFID 系统与数据库管理系统以及计算机网络等技术结合,提供了全自动、安全、便利与实时监控的系统功能。
2设备管理系统设计与实现2.1设备管理系统层次结构本系统设计的设备管理系统的层次结构如图2所示,主要架构包括5层结构。
图2流程工业设备管理系统层次结构图1企业信息化管理集成模型有色冶金设计与研究第34卷58··1)DCS 层。
在设备管理系统的层次结构中,DCS 作为集散控制系统和现场执行层,提供各设备的实时运行数据,包括设备运行时间、运行次数、运行故障反馈到相应的设备指标测量值等。
这些数据是进行实时设备运行分析的重要数据源。
2)实时数据层。
实时数据层在系统中作为连接DCS 与设备管理系统集成平台的桥梁和纽带,将DCS 的设备相关数据传递给设备管理系统集成平台,进行保存、处理、分发、分析和统计。
3)系统集成平台层。
设备管理系统采用了平台+模块的方式实现整体系统功能。
系统集成平台以数据库为背景,以实时数据库为底层通讯层,包括完善的系统平台管理、权限管理、日志管理、事件管理、通讯管理。
4)系统功能层。
根据流程工业设备管理业务需求,本系统设计了设备档案管理、设备检修计划管理、设备点巡检管理、设备能效分析、设备故障诊断等五个功能子模块。
系统主功能界面如图3所示。
5)ERP 层。
设备管理系统与ERP 可以进行有效的数据交互,从而实现企业全信息化管理。
2.2主要功能模块系统结构功能图如图4所示。
图3系统主功能界面图4流程行业设备管理系统功能框1)设备档案管理。
设备档案管理模块采用面向对象的设计方法对设备资料进行管理。
设备档案管理的功能包括设备分类属性(技术参数、设备技术规格书、设计文件、配件材料)的管理、设备基本信息的管理和单台设备属性(点巡检数据、检修数据、能效记录)的管理。
模块提供了一个网络化的、多级权限管理的设备档案电子信息平台。
2)设备检修计划管理。
检修计划与检修管理模块实现对全厂检修任务的统筹安排和全面管理功能,提供年检修计划管理、月检修计划管理和检修管理三个单元,不仅能辅助企业管理人员快速完成年检修计划和月检修计划的组织、编制、报送、审批、派发等工作,还能自动生成检修工单并跟踪记载各检修计划项目的执行结果及执行质量,全方位满足企业对设备检修计划的统筹安排和管理需求。
3)设备故障分析。
故障分析模块是点巡检模块、故障诊断模块与检修计划模块之间的桥梁,主要是对已产生的所有故障事件进行人工分析确认,最终形成驱动故障性月检修计划制定的故障分析记录表。
故障分析模块功能包括故障提示、故障事件浏览、故障处理状态管理、故障分析记录表管理和故障分析记录管理。
4)设备点巡检管理。
点巡检模块采用RFID 标签对现场设备进行标识,利用手持式点巡检仪进行数据采集。
功能包括设备点检表配置、工种配置、路线配置、点检配置下载、点检结果上传、结果浏览、换班漏检、设备状态分析等。
该模块提供了一个监督和管理的平台,确保设备点巡检制度有效地执行,为设备维修维护提供帮助,并为故障诊断和质量跟踪分析提供设备运行数据。