某商用车摆锤碰撞安全性CAE分析
中央通道在车辆碰撞中的影响及CAE分析优化
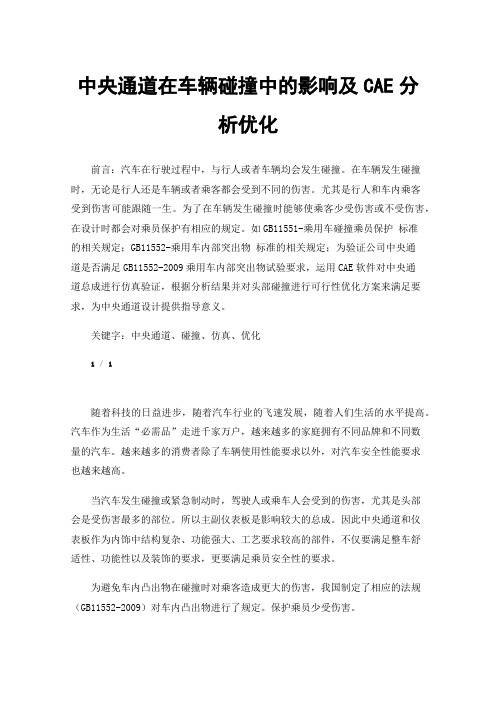
中央通道在车辆碰撞中的影响及CAE分析优化前言:汽车在行驶过程中,与行人或者车辆均会发生碰撞。
在车辆发生碰撞时,无论是行人还是车辆或者乘客都会受到不同的伤害。
尤其是行人和车内乘客受到伤害可能跟随一生。
为了在车辆发生碰撞时能够使乘客少受伤害或不受伤害,在设计时都会对乘员保护有相应的规定。
如GB11551-乘用车碰撞乘员保护标准的相关规定;GB11552-乘用车内部突出物标准的相关规定;为验证公司中央通道是否满足GB11552-2009乘用车内部突出物试验要求,运用CAE软件对中央通道总成进行仿真验证,根据分析结果并对头部碰撞进行可行性优化方案来满足要求,为中央通道设计提供指导意义。
关键字:中央通道、碰撞、仿真、优化1/1随着科技的日益进步,随着汽车行业的飞速发展,随着人们生活的水平提高。
汽车作为生活“必需品”走进千家万户,越来越多的家庭拥有不同品牌和不同数量的汽车。
越来越多的消费者除了车辆使用性能要求以外,对汽车安全性能要求也越来越高。
当汽车发生碰撞或紧急制动时,驾驶人或乘车人会受到的伤害,尤其是头部会是受伤害最多的部位。
所以主副仪表板是影响较大的总成。
因此中央通道和仪表板作为内饰中结构复杂、功能强大、工艺要求较高的部件,不仅要满足整车舒适性、功能性以及装饰的要求,更要满足乘员安全性的要求。
为避免车内凸出物在碰撞时对乘客造成更大的伤害,我国制定了相应的法规(GB11552-2009)对车内凸出物进行了规定。
保护乘员少受伤害。
在GB11552-2009乘用车内部凸出物引用标准有GB11551 乘用车正面碰撞乘员保护、GB15083 汽车座椅、座椅固定装置及头枕强度及试验要求、GB14166 机动车成年乘员约束系统。
以上标准的引用和制定都对仪表板和中央通道有限制作用。
一、GB11552-2009 乘用车内部凸出物中头部碰撞要求有座椅H点、试验装置、碰撞区域、碰撞速度、试验结果要求;①H点要求:后排可调式座椅或长条座椅应处于最后位置,不可调式座椅直接放置在H点上。
安全汽车碰撞实验报告总结(3篇)
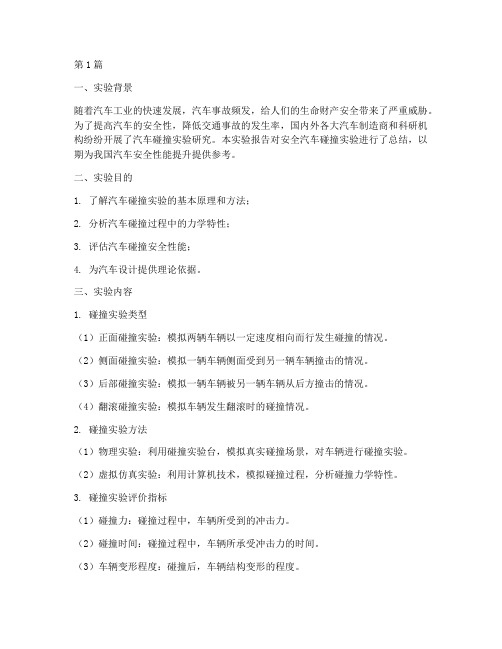
第1篇一、实验背景随着汽车工业的快速发展,汽车事故频发,给人们的生命财产安全带来了严重威胁。
为了提高汽车的安全性,降低交通事故的发生率,国内外各大汽车制造商和科研机构纷纷开展了汽车碰撞实验研究。
本实验报告对安全汽车碰撞实验进行了总结,以期为我国汽车安全性能提升提供参考。
二、实验目的1. 了解汽车碰撞实验的基本原理和方法;2. 分析汽车碰撞过程中的力学特性;3. 评估汽车碰撞安全性能;4. 为汽车设计提供理论依据。
三、实验内容1. 碰撞实验类型(1)正面碰撞实验:模拟两辆车辆以一定速度相向而行发生碰撞的情况。
(2)侧面碰撞实验:模拟一辆车辆侧面受到另一辆车辆撞击的情况。
(3)后部碰撞实验:模拟一辆车辆被另一辆车辆从后方撞击的情况。
(4)翻滚碰撞实验:模拟车辆发生翻滚时的碰撞情况。
2. 碰撞实验方法(1)物理实验:利用碰撞实验台,模拟真实碰撞场景,对车辆进行碰撞实验。
(2)虚拟仿真实验:利用计算机技术,模拟碰撞过程,分析碰撞力学特性。
3. 碰撞实验评价指标(1)碰撞力:碰撞过程中,车辆所受到的冲击力。
(2)碰撞时间:碰撞过程中,车辆所承受冲击力的时间。
(3)车辆变形程度:碰撞后,车辆结构变形的程度。
(4)乘员受伤程度:碰撞后,乘员所受到的伤害程度。
四、实验结果与分析1. 碰撞力分析碰撞力是评价汽车安全性能的重要指标之一。
实验结果表明,正面碰撞和侧面碰撞的碰撞力较大,且碰撞时间较短。
在碰撞过程中,车辆所受的冲击力与车速的平方成正比。
因此,降低车速可以有效降低碰撞力。
2. 碰撞时间分析碰撞时间是影响乘员受伤程度的重要因素。
实验结果表明,碰撞时间越短,乘员受伤程度越严重。
因此,在设计汽车时,应尽量缩短碰撞时间,提高乘员安全性。
3. 车辆变形程度分析车辆变形程度是评价汽车碰撞安全性能的重要指标。
实验结果表明,正面碰撞和侧面碰撞的车辆变形程度较大,而翻滚碰撞的车辆变形程度相对较小。
因此,在设计汽车时,应加强车辆结构强度,提高车辆抗碰撞能力。
重卡正面碰撞强度试验的有限元分析

重卡正面碰撞强度试验的有限元分析皮晓明【摘要】依据ECE29法规,对重卡驾驶室正面碰撞强度试验进行了有限元仿真.当摆锤正面撞击后,测量结果表明驾驶室方向盘外延到座椅的X向距离大于法规中人胸部厚度,证明了驾驶室具有足够的生存空间.【期刊名称】《汽车零部件》【年(卷),期】2010(000)009【总页数】2页(P69-70)【关键词】ECE29;正面碰撞试验;有限元仿真【作者】皮晓明【作者单位】宜春学院理工学院,江西宜春,336000【正文语种】中文0 引言汽车行驶中的安全性已经日益被人们所重视,其主动安全性在于如何避免发生行车事故,而被动安全性则在于发生事故后,如何减少乘员受到的伤害程度。
加装安全气囊可以减轻甚至避免驾驶人员头、胸部受到伤害,而提高驾驶室的强度和刚度,则在于发生撞车或翻车事故时减少驾驶室受压变形、压扁程度,给驾乘人员留出足够的生存空间。
因此正面碰撞强度是判断商用车驾驶室安全性能的一个重要指标[1-2]。
1 ECE29法规介绍欧洲经济委员会汽车标准法规第29条《关于对商用车驾驶室乘员保护方面的车辆认证统一规定》(ECE29)中对正面碰撞试验要求如下[3]:(1)摆锤从驾驶室前面以向驾驶室后面的方向撞击驾驶室。
撞击方向水平平行于车辆的纵向中心面,对于最大质量超过7 000 kg(本车质量8 800 kg)的车辆来说,碰撞的能量为45 000 N·m,根据摆锤质量1 500 kg,推算得到摆锤撞击驾驶舱速度为7.75 m/s。
(2)摆锤形状为长方形,平坦撞击表面宽2 500 mm,高800 mm。
边缘有半径不小于1.5 mm的圆角。
摆捶的撞击面与车辆最前部分接触,其重心高度低于驾驶室座椅R点50 mm处。
其重心位于车辆纵向中心平面内。
(3)法规规定,驾驶舱被摆锤撞击后,能保证乘员 (50%男性假人)有足够的生存空间。
2 有限元建模本分析使用Hypermesh进行网格划分,Ls-dyna计算,Hyperview后处理。
某商用车摆锤冲击安全性CAE分析与改进设计
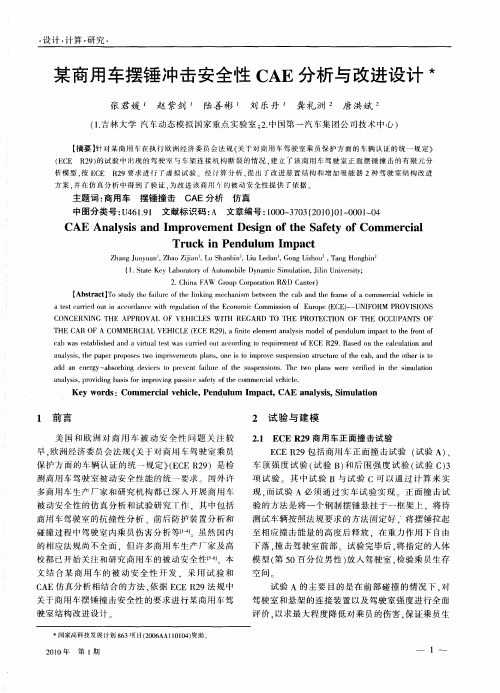
主题 词 : 商用 车
摆 锤撞 击
C E分析 A
仿 真
中图分类 号 : 4 1 l 文献标 识码 : 文章编 号 :0 0 3 0 (0 0 0 — 0 1 0 U6. 9 A 10 — 7 3 2 1 ) 10 0 — 4
CAE a y i n m p o e e tDe i n o h a ey o m me ca An l ssa d I r v m n sg ft e S f t fCo r il
c b w s e t bih d a d a vr a e t sc rid o t c o dn e u r me to C 9 B s d o h ac l t n a d a a s l e n i u l s wa a re u c r i g t rq i a s t t a o e n fE E R2 . a e n t e c lu ai n o a a y i, h a e r p s s t o i r v n e t p a s o e i t mp o e s s e s n s u t r ft e c b a d t e o h ri t n lss te p p rp o o e w mp o e l n s l n , n s o i rv u p n i t cu e o h a , n h t e o o r s a d al e e g - b o b n e ie o p e e t fi r ft e s s e so s h w ln r ei e n te smu ai n d l n r y a s r i g d vc s t r v n a l e o h u p n in .T e t o p a s we e v r d i h i l t u i f o a ay i, r vd n a i ri r vn a sv aey o ec mme ca e il . n lss p o i i gb ssf mp o i g p s i es ft ft o o h r ilv hc e
商用车驾驶室摆锤撞击安全性分析与改进

商用车驾驶室摆锤撞击安全性分析与改进随着我国交通事业的发展和人民生活质量的提高,人们对物流和出行也提出了更高和更新的要求,安全成了人们最为关注的问题。
预计到2010年,作为世界上最具发展潜力的中国重型卡车市场的销量将达到150万辆,届时将成为仅次于美国的第二大重卡市场。
重型商用汽车由于自身的结构尺寸大、车身质量大,一旦发生事故,就会造成严重的人身伤害、车辆损坏和公路设施的损坏。
重型商用汽车重大交通事故近年来各地时有发生,给生命和财产带来严重损害。
根据国家生产安全监督管理局统计的通报,近年来,伴随着高速公路里程的增加和客货运输业的发展,车速大大提高,随之而来的车祸频频发生,重型商用车事故呈直线上升,因此开展商用车安全技术研究,改进商用车安全性刻不容缓,研究提供重型商用汽车的安全性能具有非常重大的意义。
本文首先依据某商用车驾驶室的CAD模型,参考驾驶室正面摆锤撞击实车试验的变形情况进行结构简化,建立了驾驶室正面摆锤撞击仿真有限元模型,并给出了乘员生存空间的评价方法。
其次,依据实车试验条件进行驾驶室正面摆锤撞击试验的虚拟试验,通过仿真数据与实车试验数据的对比验证模型有效性,从整体上理解商用车驾驶室正面碰撞变形的本质,总结变形特点和出现的问题。
最后,针对出现的悬置断裂问题进行悬置结构的改进设计,提出了改进方案,使用已进行虚拟试验的驾驶室有限元模型多次进行仿真试验,总结和观察改进结果,并最终获得了悬置结构的改进模型,使驾驶室乘员的生存空间获得了保证。
本文给出了研究商用车驾驶室正面摆锤撞击安全性的研究方法;完成了正面摆锤撞击虚拟试验模型的建立工作,并给出了乘员生存空间的评价方法,为下一步开展研究工作奠定了模型基础;提出了悬置结构的合理改进方案,进而改善了商用车驾驶室正面摆锤撞击安全性,为商用车安全性研究工作的开展和深入探讨提供了参考和帮助。
轻型商用车整车碰撞安全开发
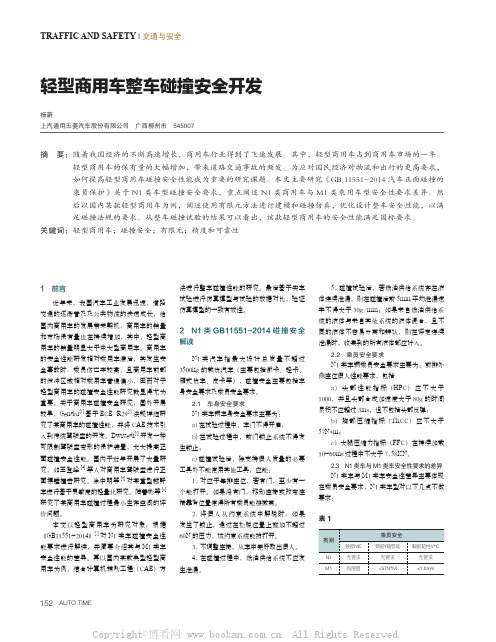
图 1 碰撞仿真分析流程图
整车几何模型
原始设计改进
ANSA 网格画分
hypermesh 有限元建模
网格改进
hypermesh 模型装配 边界条件设置
LsDyna 求解
装配与边界条件改进
HyPerview HyPerGraph
结果评价
3.1.1 碰撞理论简介 碰撞仿真采用显式积分法 [10],其仿真求 解时间决定于最小时间步。 3.1.2 整车模型搭建 首先,零件网格划分,包括输入 CAD 导 入、CAD 模型几何清理及网格的划分及质量 检查。其次,零部件之间连接关系的建立, 包括焊点连接、胶粘连接、铰链连接、螺栓 连接等。最后,边界条件设置、模型控制卡 片等。搭建完的整车模型如图 2 所示。
TRAFFIC AND SAFETY | 交通与安全
轻型商用车整车碰撞安全开发
杨蔚 上汽通用五菱汽车股份有限公司 广西柳州市 545007
摘 要:随着我国经济的不断高速增长,商用车行业得到了飞速发展。其中,轻型商用车占到商用车市场的一半。 轻型商用车的保有量的大幅增加,带来道路交通事故的频发。为应对国民经济对物流和出行的更高要求, 如何提高轻型商用车碰撞安全性能成为重要的研究课题。本文主要研究《GB 11551-2014 汽车正面碰撞的 乘员保护》关于 N1 类车型碰撞安全要求,重点阐述 N1 类商用车与 M1 类乘用车型安全性要求差异。然 后以国内某款轻型商用车为例,阐述使用有限元方法进行建模和碰撞仿真,优化设计整车安全性能,以满 足碰撞法规的要求。从整车碰撞试验的结果可以看出,该款轻型商用车的安全性能满足国标要求。
图 2 整车模型示意图
3.2 整车模型概况 整车模型由 14 个主要总成系统构成,如 图 3 所示,单元数 155 万,节点数 162 万。 3.3 碰撞工况介绍 根据 GB11551-2014《汽车正面碰撞的乘 员保护》,最大设计总质量不大于 2.5 吨的
汽车侧面碰撞的CAE仿真分析
FORUM | 论坛时代汽车 汽车侧面碰撞的CAE仿真分析杨延鹏 李洪力 陈静波 李国亮海马汽车有限公司 河南省郑州市 450016摘 要: 汽车被动安全开发,需要进行大量的整车碰撞和SRS验证,周期较长,过程复杂。
随着GB、C-NCAP等评价要求的提高,往往需要投入高昂的开发费用,而进行汽车碰撞安全的CAE仿真计算,并进行结构优化模拟,逐步成为研究汽车耐撞性的必然选择。
本文对汽车侧碰进行建模,根据仿真结果对基础车型进行评价,并通过结构优化提升车体结构耐撞性,为后续开发提供参考。
关键词:汽车;侧面碰撞;CAE仿真分析汽车结构耐撞性主要考虑整车碰撞过程中,基于GB法规、C-NCAP评价规则要求的正面碰撞、侧面碰撞等乘员生存空间保护,体现在两方面因素:生存空间碰撞侵入量、加速度或侵入速度[1]。
因此汽车设计中,必须保证车身结构吸能变形性能的稳定,进行实车碰撞试验来检验汽车被动安全性能,投入费用较高,整车需求量也较大。
CAE仿真分析有着方便性、成本低、可重复、周期快等特点,可以就汽车设计进行快速验证和结构优化建议,从而有效的提升设计效率,保障汽车结构的安全性。
1 侧面碰撞仿真模型建立根据企业建模标准并结合GB 20071-2006 《侧面碰撞的成员保护》的要求,建立汽车侧碰模型,如图1所示:1.1 模型建模根据实车数模分别对白车身、底盘、动力、CCB、转向、排气、冷却、开闭件、座椅等系统进行网格划分、材料属性定义、连接设置、建立各总成的碰撞模型。
在LS-DYNA软件中,考虑多应变率的影响,材料类型主要采用MAT24,根据BOM选择不同牌号并赋予属性。
实际碰撞中发动机、变速箱、轮毂等刚度较大,较其他部件变形较小,采用MAT20材料定义为刚体,缩减计算量。
根据连接类型,点焊采用MAT100 HEXA,二保焊采用RB2连接,玻璃胶、结构胶、减震胶分别进行设置,并建立运动件的各类铰接关系[2]。
1.2 整车搭建各分总成模型建立后,根据号段规则对节点、部件等分别编号,最后采用PATCH方式,建立总成间的连接。
基于CAE技术的车辆碰撞仿真分析
基于CAE技术的车辆碰撞仿真分析近年来,车辆碰撞事故频发,给人们的生命财产安全带来了巨大威胁。
因此,车辆碰撞仿真分析成为了一项重要的研究领域,以寻求在车辆碰撞事故中降低伤亡和损失。
而CAE(计算机辅助工程)技术则为进行车辆碰撞仿真分析提供了有效的手段。
CAE技术是指将计算机科学与工程学相结合,通过模拟和仿真分析的方法来解决工程问题。
它可以用来分析车辆在碰撞过程中的刚体运动、结构变形、应力分布等情况,从而揭示事故造成的损伤程度和车辆受力情况。
在进行车辆碰撞仿真分析时,首先需要建立一个准确的模型。
这个模型一般包括汽车的结构、材料和悬挂系统等方面的信息。
通过使用CAE软件,可以将这些信息输入到模型中,并对车辆进行详细的建模。
这样一来,就可以准确地模拟车辆在碰撞事故中的各个细节,如撞击瞬间的刚体运动、车身受力情况等。
仿真分析的结果往往可以提供丰富的数据,这对于分析事故原因、制定安全措施等方面具有重要意义。
通过对碰撞事故的仿真分析,可以评估车辆的破坏程度、安全性能以及各个结构部件的受力情况等。
这些数据能够为车辆制造商提供一个重要的参考,以优化设计并改进车辆结构,提高其安全性能。
除了用于事故分析之外,基于CAE技术的车辆碰撞仿真还可以用于测试新的安全设备和材料。
例如,研究人员可以通过仿真分析比较不同材料的硬度和韧性,以确定哪种材料最适合用于车辆结构。
这对于提高车辆的整体安全性能是非常重要的,以减少碰撞事故造成的损伤。
此外,CAE技术还可以用于优化车辆主动安全系统的设计。
通过分析车辆在碰撞事故中的运动特征和受力情况,可以得出一些关键信息,如碰撞速度、角度等。
这些信息可以用于进一步改进车辆的主动安全系统,如制动辅助、防抱死系统等,从而减少事故发生的可能性。
总的来说,基于CAE技术的车辆碰撞仿真分析是一个非常有意义且具有广泛应用前景的研究领域。
通过仿真分析,我们可以更好地理解车辆碰撞事故的产生和发展过程,为车辆的设计和生产提供重要的参考。
大客车侧面碰撞有限元仿真分析
2.3 乘员生存空间分析 图4为该车碰撞前后乘员生存空间对比图。可以看出,碰撞区域内的乘员生存空间受到严 重侵入,将对乘员生命安全造成很大威胁。
由于目前国内外还没有针对客车的侧面碰撞安全性法规,仅参考ECE R66侧翻法规中关于乘员生存空 间的相关规定进行评价。如图5所示。法规要求生存空间的最下边沿距座椅下地板上平面500mm.且测量点 的最大变形量应小于150mm;最上边沿距座椅下地板上平面l250mm,测量点的最大变形量应小于400mm。 为研究该车侧面碰撞后生存空间的侵人情况,分别提取碰撞区域生存空间范围内变形较大的4个测量点进 行评价。测量点位置如图6所示。表2为各测量点沿车体y方向的最大变形量。可以看出,所选取的4个测点 的最大变形量均超出ECE R66法规的要求,生存空间受到严重侵入,将对乘员造成危害。
元计算产品适用范围广泛,目前有国内外专业客户300余家,涉及美、加、日、韩、澳、德、 新等国,遍布石油化工、土木建筑、电磁电子、国防军工、装备制造、航空航天……等多个领域。
有限元语言及编译器(Finite Element Language And it’s Compiler,以下简称FELAC) 是中国科学院数学与系统科学研究院梁国平研究院于1983年开始研发的通用有限元软件平 台,是具有国际独创性的有限元计算软件,是PFEPG系列软件三十年成果(1983年—2013 年)的总结与提升,有限元语言语法比PFEPG更加简练,更加灵活,功能更加强大。目前 已发展到2.0版本。其核心采用元件化思想来实现有限元计算的基本工序,采用有限元语 言来书写程序的代码,为各领域,各类型的有限元问题求解提供了一个极其有力的工具。 FELAC可以在数天甚至数小时内完成通常需要一个月甚至数月才能完成的编程劳动。
大客车侧面碰撞有限元仿真分析
碰撞标准及CAE分析
2).试验条件:
0°障壁正面碰撞,障壁宽3m,高>1.5m, 质量≮ 7x10000 kg 2.2 车辆速度 50km/h,车辆不得靠自身驱动 2.3 空车,燃油箱注水90% 2.4 可调转向盘和驾驶座椅处在中间位置 2.5测量按ISO 6487 HPC=(t2-t1)[1/t2-t1 ∫t2t1adt]2
右侧门框的变形量列表(mm) L1 0.1 L2-0.6 L3-0.5 L4-0.2 L5-0.2 L6-1.6 L7-1.2 L8-0.3 法规规定,碰撞以后,必须能够打开足够数量的车门, 使乘员能正常进出,为此,测量出右侧门框的变形量 基本上不发生变化,在碰撞以后,能够打开的。
CAE分析建立转向盘的移动,车门和门框的
正面碰撞CAE分析ms纵梁碰撞变形情况:纵梁的变形情况可以判断 出整个车的碰撞性能的好坏,皱褶压缩的变形量最大,
最有利于吸收碰撞能量。
门框测量变形(mm) L1 -1.5 L2 -13.7 L3 -18.8 L4 -13.2 L5 -1.3 门框的最大压缩量为18.8mm,根据已经有的实验数 据,门框的最大变形量在40mm时,仍然能够打开
4.车门防撞杆
5.车身前端纵梁刚度 6.发动机副车架刚度与车身前纵梁刚度匹配 7.车门框和车门刚度 8.溃缩式转向柱-减小胸部伤害
四、新车安全评价体系(NCAP)
非官方的权威行业组织对进入市场的新车 安全评价 2. 评价按星级,分1、2、3、4、5个等级 ***** 33— 40 **** 25— 32 *** 17 — 24 ** 9 — 16 * 0—8
1.1
试验中,车门不得开启,试验后,有足够 数量车门能打开,使乘员逃逸 1.7 试验后,若有内部构件脱落,不得产生锋 利或锯齿边
- 1、下载文档前请自行甄别文档内容的完整性,平台不提供额外的编辑、内容补充、找答案等附加服务。
- 2、"仅部分预览"的文档,不可在线预览部分如存在完整性等问题,可反馈申请退款(可完整预览的文档不适用该条件!)。
- 3、如文档侵犯您的权益,请联系客服反馈,我们会尽快为您处理(人工客服工作时间:9:00-18:30)。
准 。国外许 多商用 车 生产 厂家 和研 究 机构 都 已深入 用 车驾 驶室 C E仿真 分析 , A 以此验 证该 商用 车 驾驶
开展 商用 车被动安全 性的仿真分析和试验研 究工 室 的安 全性 .
作 。其 中包 括 商用 车 驾驶 室 的抗撞 性 分析 、前 后 防 护 装 置 分 析 和 碰 撞 过 程 中驾 驶 室 内乘 员 伤 害 分 析
4 9
汽车实用技术
21 0 2年第 5期
其加 强板 、地 板 、侧 围等吸 收 。
22 乘员 生存 空 间分析 .
力 才 能打开 。
法规 要 求碰撞 后 , 驾驶 室要 拥有足 够 生存 空 问 , 保证 第5 百 分位 男性 人 体模 型各 部 分与 车身 内饰 及 O 转 向盘 、转 向管 柱有足 够 的空 隙 。从 图4 克制 ,碰撞 后转 向盘 与假 人腹 部有4 mm空隙 , 向管 柱及 附近 8 转 内饰 与 人体模 型膝 部 有4mm间距 , 8 能保证 在碰 撞 结 束 后人 体模 型 的生存 空 间。
d f r to dt ee e g b o p in a ay i ,s mmai e ei fu nc f ema a t r ec lii n, e o mai na r ya s r to n l ss u n h n r z dt l e eo t i fc o si t o lso h n h n nh h o t e c mme ca v h ce r n e d lm mp c d mmy lvng pa e r il e il fo t p n uu i a t u i i s c wa u n i tv l v l a e h e s q a t a ie y e au td.T t c mme ca e i l a eywa a i ae esmu ain a a y i. o r i l h ces f t sv ld td i t i lto n lss. v nh Ke wo d: m me ca e il , p n l y r Co r i l h ce v e du um nayss CAE nay i a l i, a lss
负荷 相 当 的载荷 , 最 大不 超过 1 t 但 0;驾驶 室 后 围强 中节 点数 123 8个 ,结构 部件 数 目为 11个 。依 104 9
度 施 加载 荷 载荷 与 车辆 最 大承 载质 量 成 正 比 ,要求 照 法规 定义 摆 锤和 驾 驶 室之 问的位 置关 系 、试 验边 每 吨 载重 施加 2 KN 静 载荷 。试验 完毕 后 .将第 5 界 条件 和接 触 。 0 百分 位 男性 的人 体模 型 放 人驾 驶室 .检验 乘 员 生存
一
图 6 门框压缩量
综上 所述 ,该 商用 车在 E E R 9 摆 锤碰 撞 过 C 2前
一
初始 生 存空 间 碰 揠 后 生 存 空 间
程 中满足 法规各 项要 求 。
3 、结束语
根据 对 E ER 9 规 中摆锤撞 击 试验 和相 关文 C 2 法
献 的研 究 ,确 定 了研 究 思路 的开 展 以及评 价指 标 。
i n u u Cr s Zh o S i i n Pe d l m a h a hy
( h ax a y t Auo bl C . t ,xa 1 2 0 S a n i v y tmo i o,L d i 7 0 0 ) He Du e n A s a tT kn cm ri e i e a s sac jc,w s bi e e e d l adcb nt bt c: aiga o me avhc ba r erho et e t lh d h n u m i r cl lc ae b ea s t p u n af e i
设 计 研 究
汽 车 实 j 技术 { j
A j (M BI P tT ) O LE A PLI EC NO OG ED T H L V
2 年 第 5 0l 2 期
20 l2 NO.5
某商用车摆锤碰撞 安全性 C E分析 A
赵 世 宜 ( 陕西重 型汽 车有 限公 司 ,陕西 摘 西安 7 00 ) 120
所示, 悬置 板 覆 盖件 组成 ,结构之 间主要 通过 2层 、3层 点 焊 摆锤撞击试验中以上部分吸能 比例见图3
及 缝焊 焊 等方 式进 行 连 接 。 因此 ,对 驾驶 室 主体 采 支架 吸 收 的 能量 占比最 高 ,悬 置支 架起 到 了传 力 、 用 四边 形 壳单 元 ,结 合 少部 分三 角 形 单元 对模 型 进 吸 能 的作用 ,其 次 能 量 吸收 主要 通 过前 围、纵梁 及
因素 ,对 该商用 车 的前摆 锤碰撞 假 人生存 空 间进行 了定量评 价 ,在 仿真 分析 中验证 了该商 用车 的
安全 性 。
关键 词 :商用 车 ;摆锤 分析 ;CA E分 析 CAE n l sso heS f t fCo m e ca u k A a y i ft a ey o m r il Tr c
…
。
1 、前摆锤碰撞有限元模型
我 国法规 《 用车 驾驶 室乘 员保 护》[基 本借 鉴 11 CER 9商用 车正面 撞 击试验 商 2 1 . E 2 E E R 9旨在 对货车 驾驶 室 强度 及其 与车 架 间 C 2 的连接 强度 做 出规 定 ,使 得车 辆在 翻 车 、撞击 等 恶
性 事 故 中能够 为车 内乘员 提供 足够 的生 存 空间 ,保
作者简介 : 世宜 , 赵 工程师 , 现就职于陕西重型汽车有 限公
司汽车工程研究 院 ,研究 领域 :汽车 C E分析 。 A
21年第 5 02 期
赵 世宜:某商用车摆锤碰撞 安全性 C E分析 A
4 8
障乘员安全I。现行的 E E R 9为 19 C 2 9 9年通过 的 行 离 散化 。为保证 计 算 精度 ,尽量 采用 四边 形 单元 ,
规 体 系有 欧洲经 济委 员会 法规 E E R 9 C 2 、瑞 典 国家 规 是货 车企业 无法 回避 的 问题 。本 文依据 E ER 9 C 2 法 规 Ⅵ S 2 0 :9 0 32 、美 国工程 师协 会标 准 S E标 法规 中关于 商用 车摆 锤撞 击 安全 性 的要 求进 行 某商 A
ee ntmo e n n d l m mpa tm o e , a c r i o te c re po dig p o iinso lme d la d pe u u i c d l c o dng t h o r s n n r v so ft ECE he R29 .
J
.
本 文分 析 某重 型商 用车 在施 行 E ER 9的 摆锤 C 2
撞 击 能量 分 别 由驾 驶 室变 形 、驾驶 室 向Байду номын сангаас 移 动
冲击 试 验( 1试验 A 中是 否可 以满足法 规 规 定乘 和 悬 置弯 曲变 形 消耗 掉 。驾驶 室 主要 部件 可 分 为前 图 )
前 员 生存 空 间及碰 撞 后 车架 与 驾驶 室 仍然 保持 有 效连 部 ( 面 罩 、前 围外板 、前 围 内板 、圈梁 及 仪表 板支 、 后 、 接要 求 I。依据 E ER 9在 H p r s 6 J C 2 y emeh软件 中建 立 架 相 关零 件) 后 部( 围 内外板 及其 与 地板连 接 件) 顶 、下 部( 板 、纵梁 、纵梁 加 地 了 该商 用车 正 面摆 锤撞 击 虚拟 试 验 分析 模 型 .虚拟 上 部( 盖 及其 加 强板) 、 车 试 验 的有 限元 模型 如 图 2所 示 ,计 算求 解采 用 强板及 地 板 附件) 左 部和 右部 ( 门及 相 关件 、侧 围 、驾驶 室 前后 悬 置等 部分 。 R do s 件进 行 。 型商 用车 驾驶 室 由大 面 积 的薄 内外板 及 其相 关连 接件 ) a is 软 重
要 :以某款 商用 车 驾驶 室为研 究对 象 ,参 照 E ER 9的相应 规定 ,建立 了摆锤 和 驾驶 室 的有 C 2
限元 模 型及摆 锤撞 击 的仿真 模型 ,对某商 用 车进行 前摆 锤碰 撞模拟 分 析 。通 过对过 程 能量 的验 证
证明了模型本身的正确性。对主要部件的变形及吸收能量的分析,总结出了影响碰撞结果的主要
10 +2 0 5 0 一5 Kg 刚性 摆锤 以一定 能量 撞 击驾 驶 室 ;顶 四边形 最 大单 元 内角 小于 1 5度 ,最 小单元 内角大 3
压 强度试 验 要求 驾驶 室结 构 能承 受 与车 辆前 轴 最大 于 4 度 。该 有 限元模 型共 包 含 1770个 单元 .其 5 23 9
引 言
欧洲 法规 E ER 90 , C 2 .2 此法 规对 新定 型产 品 自 2 1 01
年 7月 1日实施 。与此 同时在 国 内外 市场 竞争 日趋
美 国 和 欧洲 对 商 用 车 被 动 安 全 性 问题 关 注 较 激烈 的情 况 下 , 国内许 多商 用车 生 产厂 家积 极 开拓 早 , 目前 , 国际上 关 于商 用车 驾驶 室 强度试 验 的法 国内外 市场 ,满足 国 内外 日趋 严格 的商 用车 安全 法
需 与车 架 保持 连接 ,车 门不 得 自行 开 启 ,但 试 验 后 不 要钱 车 门能够 开 启p。 J
E E R 90 法 规 中正 面 摆锤 撞 击 试 验模 拟 两 C 2 —2
车 追尾 碰撞 情 况 ,矩 形 刚性 摆锤 的 尺 寸相 当于 前 面
图 2 货车驾驶室有 限元模型
T r u h t e p o es o n r y i v r e h o e t e s o e mo e .T e man c mp n n s o e h o g h r c s f e eg s e i d t e c r c s f t d 1 h i o o e t f t i f n h h