切削用量的选择
简述切削用量的选择原则

简述切削用量的选择原则
切削用量是指切削工艺中每一次切削的刀具转动次数和转动距离。
切削用量的选择是指在切削过程中,选择合适的切削用量,使切削工艺能够实现最终的加工目标,以保证产品的质量和产量。
切削用量的选择要考虑以下几个方面:
一、材料的特性。
不同材料有不同的力学性能,如强度、耐磨性、塑性等,这些性能会影响刀具的正确选择和使用,从而影响切削用量的选择。
二、切削工艺要求。
切削工艺要求包括切削速度、深度、面积、质量等,这些要求可以为切削用量的选择指明方向。
三、刀具性能。
刀具的极限切削速度、前角、切削力、耐磨性等将直接影响切削用量的选择。
四、机床技术参数。
切削机床的精度、平稳度、动态响应等性能都会影响刀具的使用,因此也会影响切削用量的选择。
根据以上几个方面,可以确定切削用量的尺寸大小、切削速度、转角等参数,以达到最终的加工目标。
在实际使用中,应该结合实际情况,有经验地运用这些原则,及时调整切削用量,才能保证加工质量和产量。
综上所述,切削用量的选择包括考虑材料的特性、切削工艺要求、刀具性能以及机床技术参数等因素,其最终目的是为了实现切削工艺中最终加工目标,确保产品的质量和产量。
此外,在实际使用中要根据实际情况,有经验地运用这些原则,及时调整切削用量,以保证加
工质量和产量。
合理选择切削用量
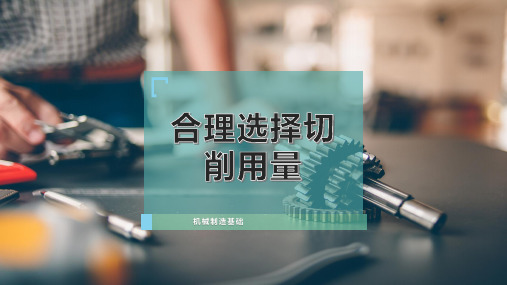
16
课堂实训——选择切削用量
机械制造基础
3)确定切削速度 vc 根据已知条件和已确定的 ap 和 f 值,由P139-140页表得切削速度 vc 130~160 m/min。由于该轴为
细长轴,应选取较小的切削速度,因此切削速度 vc 130 m/min。计算机床转速为
n 1 000vc 1 000 130 1 035 r/min πd 3.14 40
70~80
背吃刀量 ap/(mm)
2~6 进给量 f /(mm/r)
0.3~0.6
切削速度 vc /(m/min)
100~120 90~110 70~90 70~90 50~70 60~80 60~70
6~10
0.6~1
70~90 60~80 50~70 50~70 40~60 50~70 50~60
0.4~0.7 0.6~0.9
0.4~0.6
跳到 P144
5
二、进给量的选择
机械制造基础
续表
铸铁及 铜合金
16×25
20×30 25×25
40
0.4~0.5
60
0.6~0.8
0.5~0.8
0.4~0.6
100
0.8~1.2
0.7~1
0.6~0.8
0.5~0.7
400
1~1.4
1~1.2
0.8~1
0.6~0.8
寸为 46 mm×350 mm,加工尺寸为 39 mm×300 mm。在普通卧式车床CA6140上加工,使用焊接式硬
质合金YT15车刀,刀杆截面尺寸为16 mm×25 mm,刀具几何参数为
o 15,o 8,r 75, s 0,rε 1 mm,br1 0,
切削用量的选择

切削用量的选择切削速度、进给量和切削深度三者称为切削用量。
它们是影响工件加工质量和生产效率的重要因素。
车削时,工件加工表面最大直径处的线速度称为切削速度,以v(m/min)表示。
其计算公式:v=πdn/1000(m/min)式中:d——工件待加工表面的直径(mm)n——车床主轴每分钟的转速(r/min)工件每转一周,车刀所移动的距离,称为进给量,以f(mm/r)表示;车刀每一次切去的金属层的厚度,称为切削深度,以ap(mm)表示。
为了保证加工质量和提高生产率,零件加工应分阶段,中等精度的零件,一般按粗车一精车的方案进行。
粗车的目的是尽快地从毛坯上切去大部分的加工余量,使工件接近要求的形状和尺寸。
粗车以提高生产率为主,在生产中加大切削深度,对提高生产率最有利,其次适当加大进给量,而采用中等或中等偏低的切削速度。
使用高速钢车刀进行粗车的切削用量推荐如下:切削深度ap=0.8~1.5mm,进给量f=0.2~0.3mm/r,切削速度v取30~50m/min(切钢)。
粗车铸、锻件毛坯时,因工件表面有硬皮,为保护刀尖,应先车端面或倒角,第一次切深应大于硬皮厚度。
若工件夹持的长度较短或表面凸不平,切削用量则不宜过大。
粗车应留有0.5~1mm作为精车余量。
粗车后的精度为IT14-IT11,表面粗糙度Ra值一般为12.5~6.3μm。
精车的目的是保证零件尺寸精度和表面粗糙度的要求,生产率应在此前提下尽可能提高。
一般精车的精度为IT8~IT7,表面粗糙度值Ra=3.2~0.8μm,所以精车是以提高工件的加工质量为主。
切削用量应选用较小的切削深度ap=0.1~0.3mm和较小的进给量f=0.05~0.2mm/r,切削速度可取大些磨普通车刀视频。
我用数控车加工锻件,吃刀为4-6毫米,走刀0.3,转速才280.但车刀干不了四五个活就不行了请问下怎么刃磨的好?刀刃、排屑槽多宽?感觉问题应该就是在排屑槽里满意答案网友回答2014-05-03把0.3进给改0.15,不知直径多大70以下转速800,还有就是磨完刀让懂磨刀的人看看锻件毛坯是否可以利用数控车床进行粗加工,主要是轴类锻件,最大进刀量大约多少,材料45#,能用焊接刀吗?当然可以了,但是最好用现在比较先进的扒皮数控,该车床专门针对粗车设计,包括各类锻件;普通经济型数控也可以,但是一定根据产品特点下手,不可盲目进行锻件粗车;而且吃刀量以单边3-5mm为最佳;当然不是绝对,一定结合实际车削情况适当调整吃刀;,不然对机床不利;能用焊接到,但是要选用耐冲击的材料走刀F0.25转速S430用专用的刀杆个刀吧单边2.5mm可根据情况调整数控车钢件和车铸件有什么不一样,2011-05-02 17:40ni576962600|分类:职业教育|浏览477次进给,转速大概在多少知道的举个例子.......我以前是做铸件的,还有钢件精车的的一些技巧??比如粗车第一刀车多少,留多少余量精车等等?分享到:2011-05-08 14:14提问者采纳如果是45钢和50钢的话粗加工F给0.32 D至少2.5,如果不是很细的话转速要根据工件大小而定,余量精车至少要0.5,太少了车不亮精加工F给0.1左右,转速给高点如果是30MM的话我都给2500左右!这要看什么材料普通钢1mm,不锈钢20丝,直径大的转速也底,cnc机床已知车削长度2200mm,车削进给0.4mm/min,主轴转速180转,求2200mm要花多少时间车削完。
简述切削用量的选择原则
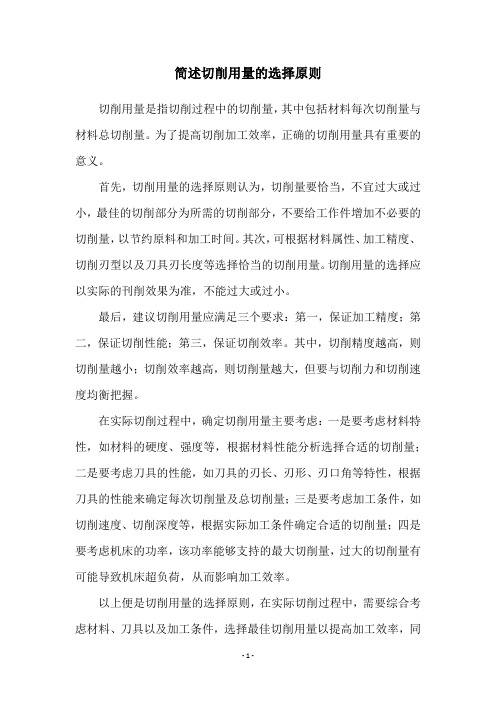
简述切削用量的选择原则
切削用量是指切削过程中的切削量,其中包括材料每次切削量与材料总切削量。
为了提高切削加工效率,正确的切削用量具有重要的意义。
首先,切削用量的选择原则认为,切削量要恰当,不宜过大或过小,最佳的切削部分为所需的切削部分,不要给工作件增加不必要的切削量,以节约原料和加工时间。
其次,可根据材料属性、加工精度、切削刃型以及刀具刃长度等选择恰当的切削用量。
切削用量的选择应以实际的刊削效果为准,不能过大或过小。
最后,建议切削用量应满足三个要求:第一,保证加工精度;第二,保证切削性能;第三,保证切削效率。
其中,切削精度越高,则切削量越小;切削效率越高,则切削量越大,但要与切削力和切削速度均衡把握。
在实际切削过程中,确定切削用量主要考虑:一是要考虑材料特性,如材料的硬度、强度等,根据材料性能分析选择合适的切削量;二是要考虑刀具的性能,如刀具的刃长、刃形、刃口角等特性,根据刀具的性能来确定每次切削量及总切削量;三是要考虑加工条件,如切削速度、切削深度等,根据实际加工条件确定合适的切削量;四是要考虑机床的功率,该功率能够支持的最大切削量,过大的切削量有可能导致机床超负荷,从而影响加工效率。
以上便是切削用量的选择原则,在实际切削过程中,需要综合考虑材料、刀具以及加工条件,选择最佳切削用量以提高加工效率,同
时节约切削原料,以降低切削成本。
第七章 切削用量的选择

在选择合理切削用量时,必须考虑加工性质。 由于粗加工和精加工要完成的加工任务和追求的目 标不同,因而切削用量选择的基本原则也完全不同。
7.7.1
粗加工时切削用量选择的基本原则
粗加工时高生产效率是追求的基本目标。这个目 标常用单件机动时最少或单位时间切除金属体积最多 来表示。下面以外圆纵车为例加以说明(图7-1)。
3.确定切削速度vc 当刀具使用寿命T、背吃刀量ap与进给量f确定 后,即可按式(7.4)计算切削速度vc
(7.4) 式中 k vc——切削速度修正系数,与刀具材料和几 何参数、工件材料等有关。 Cv 、 xv 、yv 、m及K vc值见表7.3.加工其他工件 材料时的系数及指数可查切削用量手册。
由式(6.6)可知,在选择切削用量时:应首先 选择最大的ap,其次要在机床动力和刚度允许的前提 下,选用较大的f,最后再根据式(6.6)选择合理的 vc值。
当刀具使用寿命为一定值用高速钢车刀切钢时,切削用量之间有式(7.3) 关系
(7.3)
式(7.3)表明,为保证刀具合理使用寿命,
不参与优化。因此,切削用量的优化主要是指切削切 削速度vc与进给量f的优化组合。 以单件成本最低为目标的优化目标函数的建 立过程如下: 当ap一定时,由式(7.1)
式中 由式(6.5)得
式中
将tm 、T值代入式(6.14),得 式中
式( 7.9 )即为所建立的单件成本最低的目标函 数。求该函数的极值,得
合理切削用量的选择可按下列方法进行:
1.确定背吃刀量ap
ap一般根据性质与加工余量来确定。
切削加工一般分为粗加工、半精加工和精加工
粗加工时,在保留半精与精加工余量的前提下,若机 床刚度允许,加工余量应尽可能一次切掉,在中等功 率机床上采用硬质合金刀具车外圆时,粗车取ap=2 ~ 6mm,半精车去ap=0.2 ~ 3mm,精车取ap=0.1 ~ 0.3mm。
切削 用量的合理选择
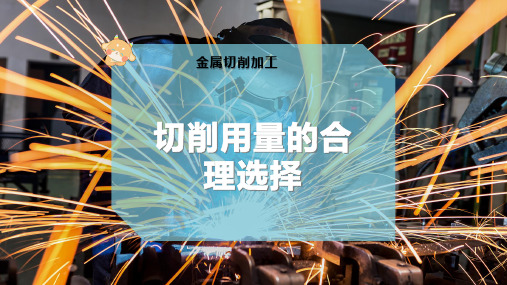
2)根据机床说明书,取机床实际进给量 =0.51mm/r。 3)检验机床进给机构允许的进给量。参考CA6140车床说 明书,查出机床进给机构允许的最大进给抗力为:FMfmax= 3528N。 计算切削时进给力为:
统、工件刚度以及精加工时表面粗糙度要求,确定进给量。
3)根据刀具寿命,确定切削速度。 4)所选定的切削用量应该是机床功率所允许的。
1.2切削用量的合理选择方法
1.背吃刀量的合理选择
背吃刀量一般是根据加工余量来确定。 粗加工(表面粗糙度Ra=50~12.5μm)时,尽可能一 次走刀即切除全部余量,在中等功率的机床上加工,取 ap=8~10mm;加工余量太大或余量不均匀、工艺系统刚性 不足或者断续切削时,可分几次走刀。 半精加工(Ra=6.3~3.2μm)时,取ap=0.5~2mm。 精加工(Ra=1.6~0.8μm)时,取ap=0.1~0.4mm。
1.5切削用量的优化概念
切削用量的优化是指在一定的预定目标及约束条件下, 选择最佳的切削用量。
在实际生产中,由于各种条件(加工零件、机床、刀 具、夹具等)都在变化,很难确定出一组最合理的切削用 量数值。
利用切削用量优化的方法,在确定加工条件下,综合 考虑各个因素,通过计算机辅助设计,能找出满足高效、 低成本、高利润和达到表面质量要求的一组最佳的切削用 量参数。实际切削用量的优化过程就是建立优化目标的数 学模型,用计算机求极值。主要目标函数有三个。
床功率是否允许。 在实际生产中,切削用量的合理选择,既可参照有关 手册的推荐数据,也可凭经验根据选择原则确定。
1.3车削用量的合理选择例题
切削用量的选择和计算公式
切削用量的选择和计算公式切削用量的选择和计算是机械加工中非常重要的一环,它直接影响到加工效率、加工质量和工具的使用寿命。
正确选择和计算切削用量可以使加工过程更加稳定和高效。
本文将介绍切削用量的选择和计算公式,并探讨其在机械加工中的应用。
切削用量的选择。
切削用量是指在切削加工过程中,刀具与工件之间的相对运动距离。
切削用量的选择需要考虑到工件材料、刀具材料、切削速度、进给速度等因素。
一般来说,切削用量越大,切削效率越高,但是过大的切削用量会导致刀具磨损加剧,甚至损坏刀具。
因此,在选择切削用量时需要在保证加工效率的前提下,尽量减小刀具的磨损。
切削用量的计算公式。
切削用量的计算公式通常包括切削速度、进给速度和刀具的切削刃数。
切削速度是指刀具在工件表面的相对运动速度,通常用Vc表示,单位为m/min。
进给速度是指刀具在工件表面的进给速度,通常用f表示,单位为mm/r。
刀具的切削刃数是指刀具上切削刃的数量,通常用z表示。
根据切削速度、进给速度和刀具的切削刃数,切削用量的计算公式可以表示为:切削用量 = 切削速度×进给速度×刀具切削刃数。
在实际应用中,切削用量的计算公式可以根据具体的加工情况进行调整,以满足加工的要求。
切削用量的应用。
切削用量的选择和计算在机械加工中具有重要的应用价值。
正确选择切削用量可以提高加工效率,降低成本,提高产品质量。
同时,合理的切削用量还可以延长刀具的使用寿命,减少刀具的更换次数,降低加工成本。
在实际加工中,切削用量的选择和计算需要结合具体的加工情况进行调整。
例如,在加工硬质材料时,可以适当增大切削用量,以提高加工效率;在加工精密零件时,可以适当减小切削用量,以保证加工精度。
此外,切削用量的选择还需要考虑到刀具的类型、刀具的磨损情况、工件的材料和形状等因素。
总之,切削用量的选择和计算是机械加工中非常重要的一环。
正确选择和计算切削用量可以提高加工效率、降低成本、提高产品质量。
切削用量选择的基本原则
切削用量选择的基本原则切削用量选择是机械加工中非常重要的一环,合理的切削用量选择可以提高加工效率,降低能耗,延长刀具寿命,确保加工质量。
下面将介绍切削用量选择的基本原则。
1. 根据加工材料的特性选择切削用量:不同的材料具有不同的硬度、塑性、热导率等特性,因此在选择切削用量时需要考虑这些因素。
一般来说,对于硬度较高的材料,应选择较小的切削用量,以避免刀具过早磨损;对于塑性较好的材料,可以适当增加切削用量,以提高加工效率。
2. 根据刀具的类型选择切削用量:不同类型的刀具具有不同的切削能力和切削稳定性,因此在选择切削用量时需要考虑刀具的特性。
一般来说,对于切削能力较强的刀具,可以选择较大的切削用量,以提高加工效率;对于切削稳定性较好的刀具,可以适当增加切削用量,以提高加工精度。
3. 根据加工表面粗糙度要求选择切削用量:不同的加工表面粗糙度要求需要选择不同的切削用量。
一般来说,对于要求较高的加工表面粗糙度,应选择较小的切削用量,以提高加工精度;对于要求较低的加工表面粗糙度,可以适当增加切削用量,以提高加工效率。
4. 根据加工精度要求选择切削用量:不同的加工精度要求需要选择不同的切削用量。
一般来说,对于要求较高的加工精度,应选择较小的切削用量,以提高加工精度;对于要求较低的加工精度,可以适当增加切削用量,以提高加工效率。
5. 根据切削热量选择切削用量:切削过程中会产生大量的热量,如果切削用量选择不当,会导致切削热量过大,影响加工质量。
因此,在选择切削用量时需要注意控制切削热量,避免过热引起刀具磨损和工件变形。
6. 根据加工环境选择切削用量:加工环境对切削用量也有一定的影响。
例如,如果加工环境温度较高,应适当减小切削用量,以避免切削热量过大;如果加工环境湿度较大,应选择较大的切削用量,以提高切削稳定性。
切削用量选择的基本原则是根据加工材料特性、刀具类型、加工表面粗糙度要求、加工精度要求、切削热量和加工环境等因素综合考虑,选择合适的切削用量,以达到提高加工效率、降低能耗、延长刀具寿命和确保加工质量的目的。
切削用量的合理选择
表7-5 硬质合金车刀及高速钢车刀粗车外圆和端面时的进给量
3)切削速度 切削速度vc是根据刀具耐用度T确定的。在背吃刀量ap和进给量f
确定后,根据规定的刀具耐用度T,计算刀具耐用度T所允许的切削n计,再选取机床主轴实际转速n,最后由机床主轴实 际转速n计算实际切削速度vc。
对切削加工实际生产来 说,较方便的是根据切 削用量手册查表确定切 削用量。切削用量手册 中的数据是在积累了大 量的生产经验及试验研 究工作的基础上,经过 科学的数据处理后制定 出来的。查表确定切削 用量后,还可根据具体 生产条件适当调整。
把各公式的计算结果绘 制成各种图表,直接从 其上选择切削用量。针 对具体机床制成的切削 用量图表,更适合于生 产现场使用。
3)切削速度 c 半精加工和精加工的切削速度
也是受刀具耐用度的限制,因此,
切削速度与粗加工时的计算方法相同。但由于半精加工和精加工切削条
件较好,刀具耐用度比粗加工时规定得大,所以半精加工和精加工时的
切削速度一般比粗加工时高。
1.3 提高切削用量的途径
提高切削用量的途径很多,可归纳为以下几个方面: (1)采用切削性能更好的新型刀具材料。 (2)改善工件材料的加工性。 (3)改进刀具结构和选用合理刀具几何参数。 (4)提高刀具的制造和刃磨质量。 (5)采用新型的、性能优良的切削液和高效率的冷却方法。
(7-1)
若加工余量A太大或加工工艺系统刚性比较差,则加工余量A
可经二次或更多次走刀去除。若分二次走刀,则它们的背吃刀量
的表达式分别为
ap1=(3/4~2/3)A ap2=(1/3~1/4)A
(7-2) (7-3)
2)进给量 当背吃刀量确定后,根据加工工艺系统允许的切削力,进一步确定
切削用量的选择原则
数控编程时,编程人员必须确定每道工序的切削用量,并以指令的形式写入程序中。
切削用量包括切削速度、背吃刀量及进给速度等。
对于不同的加工方法,需要选用不同的切削用量。
1、切削用量的选择原则粗加工时,一般以提高生产率为主,但也应考虑经济性和加工成本;半精加工和精加工时,应在保证加工质量的前提下,兼顾切削效率、经济性和加工成本。
具体数值应根据机床说明书、切削用量手册,并结合经验而定。
从刀具的耐用度出发,切削用量的选择顺序是:先确定背吃刀量,其次确定进给量,最后确定切削速度。
2、背吃刀量的确定(ap)背吃刀量由机床、工件和刀具的刚度来决定,在刚度允许的条件下,应尽可能使背吃刀量等于工件的加工余量,这样可以减少走刀次数,提高生产效率。
确定背吃刀量的原则:(1)在工件表面粗糙度值要求为Ra12.5μm~25μm时,如果数控加工的加工余量小于5mm~6mm,粗加工一次进给就可以达到要求。
但在余量较大,工艺系统刚性较差或机床动力不足时,可分多次进给完成。
(2)在工件表面粗糙度值要求为Ra3.2μm~12.5μm时,可分粗加工和半精加工两步进行。
粗加工时的背吃刀量选取同前。
粗加工后留0.5mm~1.0mm余量,在半精加工时切除。
(3)在工件表面粗糙度值要求为Ra0.8μm~3.2μm时,可分粗加工、半精加工、精加工三步进行。
半精加工时的背吃刀量取1.5mm~2mm。
精加工时背吃刀量取0.3mm~0.5mm。
3、进给量(f)的确定进给量主要根据零件的加工精度和表面粗糙度要求以及刀具、工件的材料选取。
最大进给速度受机床刚度和进给系统的性能限制。
工件或刀具每转一周时,刀具与工件在进给运动方向上的相对位移量。
进给速度v f是指切削刃上选定点相对工件进给运动的瞬时速度。
v f=fn式中v f——进给速度(mm/s);n——主轴转速(r/s);f——进给量(mm)确定进给速度的原则:1)当工件的质量要求能够得到保证时,为提高生产效率,可选择较高的进给速度。
- 1、下载文档前请自行甄别文档内容的完整性,平台不提供额外的编辑、内容补充、找答案等附加服务。
- 2、"仅部分预览"的文档,不可在线预览部分如存在完整性等问题,可反馈申请退款(可完整预览的文档不适用该条件!)。
- 3、如文档侵犯您的权益,请联系客服反馈,我们会尽快为您处理(人工客服工作时间:9:00-18:30)。
• 7.1切削用量选择的基本原则 切削用量选择的基本原则 • 7.1.1粗加工时的切削用量选择的基本原则 粗加工时的切削用量选择的基本原则
πd w L h Lh tm = = n w a p f 1000 v c a p f
A0=πdwLh/1000
→
A0 tm = vc a p f
• 高生产效率是追求的基本目标。 高生产效率是追求的基本目标。 • 提高 c、增大 和ap,都能提高生产率 。 提高v 增大f和 • 切削用量三要素对刀具寿命的影响程度不同,由大到小影响次序是:vc、 切削用量三要素对刀具寿命的影响程度不同,由大到小影响次序是: f、ap。为保持已确定的刀具寿命,若提高其中一要素,则必须相应地降 为保持已确定的刀具寿命,若提高其中一要素, 低另外两要素。 低另外两要素。可见切削用量三要素对生产率的影响程度是不同的 。
• 7.2合理切削用量的选择方法 7.2合理切削用量的选择方法 • 1.背吃刀量 p的确定 背吃刀量a 背吃刀量 • 一般根据加工性质与加工余量确定 p。切削加工一般分为 一般根据加工性质与加工余量确定a 粗加工、半精加工和精加工。 粗加工、半精加工和精加工。 • 粗加工 表面粗糙度Ra50~12.5mm)时,在机床功率和刀 粗加工(表面粗糙度 表面粗糙度 ~ 时 具强度允许情况下,一次走刀应尽可能切除全部余量。 具强度允许情况下,一次走刀应尽可能切除全部余量。 在中等功率机床上,背吃刀量可达2~ 在中等功率机床上,背吃刀量可达 ~6mm。 。 • 半精加工 表面粗糙度Ra6.3~3.2mm)时,背吃刀量取为 半精加工(表面粗糙度 表面粗糙度 ~ 时 0.3~2mm。 ~ 。 • 精加工 表面粗糙度Ra1.6~0.8mm)时。背吃刀量取为 精加工(表面粗糙度 表面粗糙度 ~ 时 0.1~0.3mm。 ~ 。
• 在生产中选择切削速度的一般原则是: 在生产中选择切削速度的一般原则是: • (1)粗车时,ap和f 较大,故选择较低的 c;反之精车时选择较 粗车时, 较大,故选择较低的v 粗车时 高的vc。 高的 • (2)工件材料强度、硬度高时,应选较低的vc。 工件材料强度、硬度高时,应选较低的 工件材料强度 • (3)切削合金钢比切削中碳钢切削速度降低 切削合金钢比切削中碳钢切削速度降低20%~30%;切削 切削合金钢比切削中碳钢切削速度降低 ~ ; 调质状态的钢比切削正火、 调质状态的钢比切削正火、退火状态钢要降低切削速度 20%~30%;切削有色金属比切削中碳钢的切削速度可提高 ~ ; 100%~300%。 ~ 。 • (4)刀具材料的切削性能愈好,切削速度也选得愈高,如硬质 刀具材料的切削性能愈好,切削速度也选得愈高, 刀具材料的切削性能愈好 合金钢的切削速度比高速钢刀具可高几倍, 合金钢的切削速度比高速钢刀具可高几倍,涂层刀具的切削 速度比未涂层刀具要高,陶瓷、金刚石和CBN刀具可采用更 速度比未涂层刀具要高,陶瓷、金刚石和 刀具可采用更 高的切削速度。 高的切削速度。
•ห้องสมุดไป่ตู้
精车的一个突出的问题是保证加工表面的粗糙度的要求。 精车的一个突出的问题是保证加工表面的粗糙度的要求。减上表面 粗糙度Ra值的主要措施有如下几点 值的主要措施有如下几点。 粗糙度 值的主要措施有如下几点。 和进给量f,可减小残留 (1)合理选用切削用量。选用较小的切削深度 和进给量 可减小残留 )合理选用切削用量。选用较小的切削深度ap和进给量 面积, 值减小。 面积,使Ra值减小。 值减小 或刀尖磨有小圆弧, (2)适当减小副偏角 )适当减小副偏角Kr′,或刀尖磨有小圆弧,以减小残留面积,使Ra值 或刀尖磨有小圆弧 以减小残留面积, 值 减小。 减小。 (3)适当加大前角γ0,将刀刃磨得更为锋利。 )适当加大前角 ,将刀刃磨得更为锋利。 值达到0.2~ (4)用油后加机油打磨车刀的前、后刀面,使其 值达到 ~0.1µm, )用油后加机油打磨车刀的前、后刀面,使其Ra值达到 可有效减小工件表面的Ra值 可有效减小工件表面的 值。 (5)合理使用切削液,也有助于减小加工表面粗糙度 值。低速精车 )合理使用切削液,也有助于减小加工表面粗糙度Ra值 使用乳化液或机油;若用低速精车铸铁应使用煤油, 使用乳化液或机油;若用低速精车铸铁应使用煤油,高速精车钢件和较 高切速精车铸铁件,一般不使用切削液。 高切速精车铸铁件,一般不使用切削液。
• • • • • • •
补充粗车多次走刀的情况: 补充粗车多次走刀的情况: 1.工艺系统刚度低,余量不均匀 工艺系统刚度低, 工艺系统刚度低 2.余量过大 余量过大 3.断续切削 断续切削 结论: 结论: 第一次走刀和头几次要尽可能大;若只有2次走刀 次走刀, 第一次走刀和头几次要尽可能大;若只有 次走刀,则第一次是总共 的三分之二到四分之三。 的三分之二到四分之三。 粗车铸、锻件毛坯时,因工件表面有硬皮,为保护刀尖, 粗车铸、锻件毛坯时,因工件表面有硬皮,为保护刀尖,应先车端 面或倒角,第一次切深应大于硬皮厚度以预防刀尖过早磨损。 面或倒角,第一次切深应大于硬皮厚度以预防刀尖过早磨损。若工件夹 持的长度较短或表面凸不平,切削用量则不宜过大。 持的长度较短或表面凸不平,切削用量则不宜过大。 粗车应留有0.5~ 作为精车余量。 粗车应留有 ~1mm作为精车余量。粗车后的精度为 作为精车余量 粗车后的精度为IT14-IT11,表 表 面粗糙度Ra值一般为 值一般为12.5~6.3µm。 面粗糙度 值一般为 ~ 。
第7章切削用量的选择 章切削用量的选择
选择合理的切削用量是切削加工中十分重要 的环节, 的环节,切削用量不仅是在机床调整前必须确定 的重要参数,而且其数值合理与否对加工质量、 的重要参数,而且其数值合理与否对加工质量、 加工效率、生产成本等有着非常重要的影响。 加工效率、生产成本等有着非常重要的影响。选 择合理切削用量时,必须考虑加工性质。 择合理切削用量时,必须考虑加工性质。合理的 切削用量是指在保证加工质量的前提下, 切削用量是指在保证加工质量的前提下,充分利 用刀具切削性能和机床性能, 用刀具切削性能和机床性能,获得高生产率和低 加工成本的切削用量。 加工成本的切削用量。
• •
2.确定进给量 确定进给量f 确定进给量 粗加工时,工件表面质量要求不高,但切削力往往很大, 粗加工时,工件表面质量要求不高,但切削力往往很大, 合理进给量的大小主要受机床进给机构强度 机床进给机构强度、 合理进给量的大小主要受机床进给机构强度、刀具的强度 与刚性、工件的装夹刚度等因素的限制。粗车时工件材料, 与刚性、工件的装夹刚度等因素的限制。粗车时工件材料, 刀杆尺寸,工件直径与选定的切削深度进行选择, 刀杆尺寸,工件直径与选定的切削深度进行选择,一般 f=0.3~0.6mm/r。 。 半精加工和精加工时, 半精加工和精加工时,合理进给量的大小则主要受工件加 工精度和表面粗糙度的限制。 工精度和表面粗糙度的限制。根据预先估计的切削速度与 刀尖圆弧半径进行选择,常取f=0.08~0.3mm/r。此外,还 刀尖圆弧半径进行选择,常取 。此外, 需要考虑到所选的进给量能满足加工精度,甚至卷屑、 需要考虑到所选的进给量能满足加工精度,甚至卷屑、断 屑的要求。 屑的要求。 生产实际中多采用查表法确定进给量。 生产实际中多采用查表法确定进给量。
•
•
• •
粗加工时,根据工件材料,车刀刀杆直径, 粗加工时,根据工件材料,车刀刀杆直径,以及被吃刀量 查表; 查表; 半精加工以及精加工时,根据粗糙度工件材料, 半精加工以及精加工时,根据粗糙度工件材料,估计的切 削速度以及刀尖圆弧半径来查。 削速度以及刀尖圆弧半径来查。
• 3.切削速度 c的选择 切削速度v 切削速度 值选定后, 在ap、f值选定后,一般根据合理的刀具寿命计算或用查表 值选定后 来选定切削速度。 来选定切削速度。 Cv • v c = (1 − m ) m x y K v c T a pv f v 60 • • 式中 Kvc:切削速度修正系数, Kvc的大小受工件材料、毛 切削速度修正系数, 的大小受工件材料、 坯表面状态、刀具几何参数等切削条件的影响。 坯表面状态、刀具几何参数等切削条件的影响。 • Cv 、xv 、yv、m及Kvc值可查阅《机械加工工艺手册》。 及 值可查阅《机械加工工艺手册》 • 根据工件尺寸计算工件转数 根据工件尺寸计算工件转数n: N=1000vc/πdw • 根据机床说明书取较低而相近的机床主轴转数 ,计算实际 根据机床说明书取较低而相近的机床主轴转数n, 切削速度。 切削速度。
• • • • • •
7.1.2精加工时的切削用量选择的基本原则 7.1.2精加工时的切削用量选择的基本原则 首先保证加工精度和表面质量, 首先保证加工精度和表面质量,同时兼顾必要的 使用寿命和生产效率。 使用寿命和生产效率。 先选取较小的ap和f,其中: 先选取较小的 ,其中: ap根据加工余量来定; 根据加工余量来定; f根据表面粗糙度来定; 根据表面粗糙度来定; 最后利用切削用量手册选取或者用公式计算确定v 最后利用切削用量手册选取或者用公式计算确定 c。
• 高速钢: 高速钢:
vc =
Cv f a
2 3 1 3 p
• (1) f保持不变,ap增加至 ap,如仍保持合理的刀具寿命, 保持不变, 增加至3 如仍保持合理的刀具寿命, 保持不变 必须降低30%,此时生产率提高了 倍。 则vc必须降低 ,此时生产率提高了1.1倍 • (2) ap保持不变,f增加至 f,如仍保持合理的刀具寿命, 保持不变, 增加至 ,如仍保持合理的刀具寿命, 增加至3 必须降低50%,此时生产率提高了 倍。 则vc必须降低 ,此时生产率提高了0.5倍 • 增大ap 比增大f更有利于提高生产率。 增大 比增大 更有利于提高生产率。 更有利于提高生产率 • 结果:为了保证合理的刀具寿命,在选择切削用量时:首 结果:为了保证合理的刀具寿命,在选择切削用量时: 先选择最大的a 其次在机床动力和刚度条件允许条件内, 先选择最大的 p ,其次在机床动力和刚度条件允许条件内, 选用较大的f 选用较大的 ,最后根据公式选择合适的速度