普通车床加工简单实例
利用普通车床实现半圆弧加工
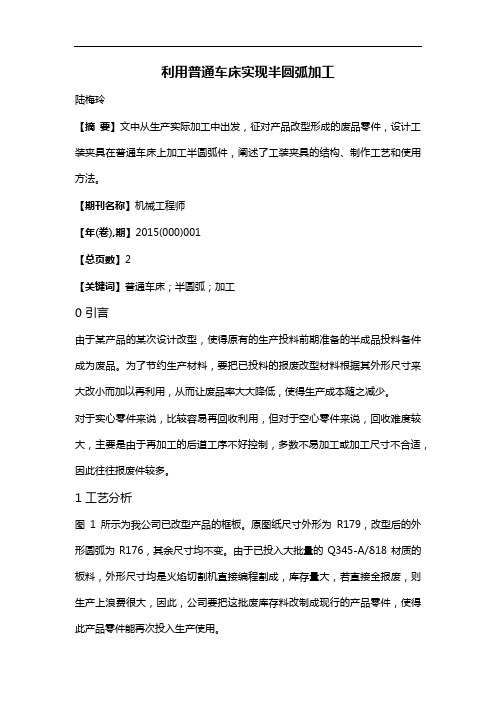
利用普通车床实现半圆弧加工陆梅玲【摘要】文中从生产实际加工中出发,征对产品改型形成的废品零件,设计工装夹具在普通车床上加工半圆弧件,阐述了工装夹具的结构、制作工艺和使用方法。
【期刊名称】机械工程师【年(卷),期】2015(000)001【总页数】2【关键词】普通车床;半圆弧;加工0 引言由于某产品的某次设计改型,使得原有的生产投料前期准备的半成品投料备件成为废品。
为了节约生产材料,要把已投料的报废改型材料根据其外形尺寸来大改小而加以再利用,从而让废品率大大降低,使得生产成本随之减少。
对于实心零件来说,比较容易再回收利用,但对于空心零件来说,回收难度较大,主要是由于再加工的后道工序不好控制,多数不易加工或加工尺寸不合适,因此往往报废件较多。
1 工艺分析图1所示为我公司已改型产品的框板。
原图纸尺寸外形为R179,改型后的外形圆弧为R176,其余尺寸均不变。
由于已投入大批量的Q345-A/δ18材质的板料,外形尺寸均是火焰切割机直接编程割成,库存量大,若直接全报废,则生产上浪费很大,因此,公司要把这批废库存料改制成现行的产品零件,使得此产品零件能再次投入生产使用。
对比前后图纸来看,从工艺技术上分析,存在以下问题:1)现根据改型后的R176来看,其外圆弧加工余量只有3 mm,且还不是半圆,由于板材不是实心,空心部分比较大,且外形比较难控制,因此技术改造比较大;2)如选用铣床设备来实现加工,加工过程还能省时省力些,但本部门因生产设备能力所限,并无此设备,因此这种方案实施不通;而对于本部门来说,只有用于粗加工的普通车床可以考虑,而普通机床由于只适用粗加工,其机床精度所限,3 mm的单边余量太小,而且所要加工的零件只是近半个的空心圆弧且还是空心,如果直接上车床加工,无法直接完成夹紧及加工。
2 夹具设计与应用根据本公司实际加工能力出发,特设计了工装夹具来辅助生产加工,也就是设想把2块近半圆的圆弧加入工装夹具拼成整圆来加工,这样车床上装夹方便,利于实现此工件产品的加工,其设计思路具体如图2所示,实施步骤如下:2.1 制作工装夹具过程1)选取同零件厚度相同的板料,取用现场边角料即可,由于不需要太高的精度,因此上火焰切割机编程割成图2中序号2所示的长条圆弧实心板的工装夹具。
数控车床编程实例详解(30个例子)(1).

车床编程实例一半径编程图3.1.1 半径编程%3110 (主程序程序名)N1 G92 X16 Z1 (设立坐标系,定义对刀点的位置)N2 G37 G00 Z0 M03 (移到子程序起点处、主轴正转)N3 M98 P0003 L6 (调用子程序,并循环6 次)N4 G00 X16 Z1 (返回对刀点)N5 G36 (取消半径编程)N6 M05 (主轴停)N7 M30 (主程序结束并复位)%0003 (子程序名)N1 G01 U-12 F100 (进刀到切削起点处,注意留下后面切削的余量)N2 G03 U7.385 W-4.923 R8(加工R8 园弧段)N3U3.215 W-39.877 R60 (加工R60 园弧段)N4 G02 U1.4 W-28.636 R40(加工切R40 园弧段)N5 G00 U4 (离开已加工表面)N6 W73.436 (回到循环起点Z 轴处)N7 G01 U-4.8 F100 (调整每次循环的切削量)N8 M99 (子程序结束,并回到主程序)直线插补指令编程图3.3.5 G01 编程实例%3305N1 G92 X100 Z10 (设立坐标系,定义对刀点的位置)N2 G00 X16 Z2 M03 (移到倒角延长线,Z 轴2mm 处)N3 G01 U10 W-5 F300 (倒3×45°角)N4 Z-48 (加工Φ26 外圆)N5 U34 W-10 (切第一段锥)N6 U20 Z-73 (切第二段锥)N7 X90 (退刀)N8 G00 X100 Z10 (回对刀点)N9 M05 (主轴停)N10 M30 (主程序结束并复位)车床编程实例三圆弧插补指令编程%3308N1 G92 X40 Z5 (设立坐标系,定义对刀点的位置)N2 M03 S400 (主轴以400r/min 旋转)N3 G00 X0 (到达工件中心)N4 G01 Z0 F60 (工进接触工件毛坯)N5 G03 U24 W-24 R15 (加工R15 圆弧段)N6 G02 X26 Z-31 R5 (加工R5 圆弧段)N7 G01 Z-40 (加工Φ26 外圆)N8 X40 Z5 (回对刀点)N9 M30 (主轴停、主程序结束并复位图3.3.8 G02/G03 编程实例倒角指令编程图3.3.10.1 倒角编程实例%3310N10 G92 X70 Z10 (设立坐标系,定义对刀点的位置)N20 G00 U-70 W-10 (从编程规划起点,移到工件前端面中心处)N30 G01 U26 C3 F100 (倒3×45°直角)N40 W-22 R3 (倒R3 圆角)N50 U39 W-14 C3 (倒边长为3 等腰直角)N60 W-34 (加工Φ65 外圆)N70 G00 U5 W80 (回到编程规划起点)N80 M30 (主轴停、主程序结束并复位)车床编程实例五倒角指令编程%3310N10 G92 X70 Z10 (设立坐标系,定义对刀点的位置)N20 G00 X0 Z4 (到工件中心)N30 G01 W-4 F100 (工进接触工件)N40 X26 C3 (倒3×45°的直角)N50 Z-21 (加工Φ26 外圆)N60 G02 U30 W-15 R15 RL=3(加工R15 圆弧,并倒边长为4 的直角)N70 G01 Z-70 (加工Φ56 外圆)N80 G00 U10 (退刀,离开工件)N90 X70 Z10 (返回程序起点位置)M30 (主轴停、主程序结束并复位)图3.3.10.2 倒角编程实例车床编程实例六圆柱螺纹编程螺纹导程为1.5mm,δ=1.5mm,δ'=1mm ,每次吃刀量(直径值)分别为0.8mm、0.6 mm 、0.4mm、0.16mm图3.3.12 螺纹编程实例%3312N1 G92 X50 Z120 (设立坐标系,定义对刀点的位置)N2 M03 S300 (主轴以300r/min 旋转)N3 G00 X29.2 Z101.5 (到螺纹起点,升速段1.5mm,吃刀深0.8mm)N4 G32 Z19 F1.5 (切削螺纹到螺纹切削终点,降速段1mm)N5 G00 X40 (X 轴方向快退)N6 Z101.5 (Z 轴方向快退到螺纹起点处)N7 X28.6 (X 轴方向快进到螺纹起点处,吃刀深0.6mm)N8 G32 Z19 F1.5 (切削螺纹到螺纹切削终点)N9 G00 X40 (X 轴方向快退)N10 Z101.5 (Z 轴方向快退到螺纹起点处)N11 X28.2 (X 轴方向快进到螺纹起点处,吃刀深0.4mm)N12 G32 Z19 F1.5 (切削螺纹到螺纹切削终点)N13 G00 X40 (X 轴方向快退)N14 Z101.5 (Z 轴方向快退到螺纹起点处)N15 U-11.96 (X 轴方向快进到螺纹起点处,吃刀深0.16mm)N16 G32 W-82.5 F1.5 (切削螺纹到螺纹切削终点)N17 G00 X40 (X 轴方向快退)N18 X50 Z120 (回对刀点)N19 M05 (主轴停)N20 M30 (主程序结束并复位)恒线速度功能编程%3314车床编程实例七图3.3.14 恒线速度编程实例N1 G92 X40 Z5 (设立坐标系,定义对刀点的位置)N2 M03 S400 (主轴以400r/min 旋转)N3 G96 S80 (恒线速度有效,线速度为80m/min)N4 G00 X0 (刀到中心,转速升高,直到主轴到最大限速)N5 G01 Z0 F60 (工进接触工件)N6 G03 U24 W-24 R15 (加工R15 圆弧段)N7 G02 X26 Z-31 R5 (加工R5 圆弧段)N8 G01 Z-40 (加工Φ26 外圆)N9 X40 Z5 (回对刀点)N10 G97 S300 (取消恒线速度功能,设定主轴按300r/min 旋转)N11 M30 (主轴停、主程序结束并复位)车床编程实例八%3317M03 S400 (主轴以400r/min 旋转)G91 G80 X-10 Z-33 I-5.5 F100(加工第一次循环,吃刀深3mm)X-13 Z-33 I-5.5(加工第二次循环,吃刀深3mm)X-16 Z-33 I-5.5(加工第三次循环,吃刀深3mm)M30 (主轴停、主程序结束并复位)图3.3.17 G80 切削循环编程实例车床编程实例九G81 指令编程(点画线代表毛坯)图3.3.20 G81 切削循环编程实例%3320N1 G54 G90 G00 X60 Z45 M03 (选定坐标系,主轴正转,到循环起点)N2 G81 X25 Z31.5 K-3.5 F100 (加工第一次循环,吃刀深2mm)N3 X25 Z29.5 K-3.5 (每次吃刀均为2mm,)N4 X25 Z27.5 K-3.5 (每次切削起点位,距工件外圆面5mm,故K 值为-3.5)N5 X25 Z25.5 K-3.5 (加工第四次循环,吃刀深2mm)N6 M05 (主轴停)N7 M30 (主程序结束并复位车床编程实例十G82 指令编程(毛坯外形已加工完成)%3323N1 G55 G00 X35 Z104(选定坐标系G55,到循环起点)N2 M03 S300 (主轴以300r/min 正转)N3 G82 X29.2 Z18.5 C2 P180 F3(第一次循环切螺纹,切深0.8mm)N4 X28.6 Z18.5 C2 P180 F3(第二次循环切螺纹,切深0.4mm)N5 X28.2 Z18.5 C2 P180 F3(第三次循环切螺纹,切深0.4mm)N6 X28.04 Z18.5 C2 P180 F3(第四次循环切螺纹,切深0.16mm)N7 M30 (主轴停、主程序结束并复位)图3.3.23 G82 切削循环编程实例车床编程实例十一外径粗加工复合循环编制图3.3.27 所示零件的加工程序:要求循环起始点在A(46,3),切削深度为1.5mm(半径量)。
普通车床操作实训操作教程
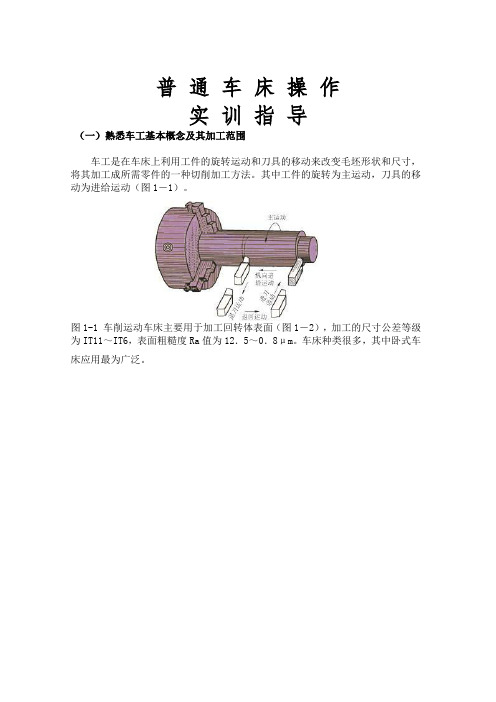
普通车床操作实训指导(一)熟悉车工基本概念及其加工范围车工是在车床上利用工件的旋转运动和刀具的移动来改变毛坯形状和尺寸,将其加工成所需零件的一种切削加工方法。
其中工件的旋转为主运动,刀具的移动为进给运动(图1-1)。
图1-1 车削运动车床主要用于加工回转体表面(图1-2),加工的尺寸公差等级为IT11~IT6,表面粗糙度Ra值为12.5~0.8μm。
车床种类很多,其中卧式车床应用最为广泛。
图1-2 普通车床所能加工的典型表面a)车外园 b)车端面 C)车锥面 d)切槽、切断 e)切内槽 f)钻中心孔g)钻孔 h)镗孔 i)铰孔 j)车成形面 k)车外螺纹 l)滚花(二)学习卧式车床型号及结构组成Ⅰ、机床的型号C 6 1 32主参数代号(最大车削直径的1/10,即320mm)机床型别代号(普通车床型)机床组别代号(普通车床组)机床类别代号(车床类)C 6 16主参数的1/10,即车床主轴轴线到导轨面的尺寸为160mm,(其车削工件最大直径为320mm)。
组别(普通车床)类别(车床类)Ⅱ、卧式车床的结构1.卧式车床的型号卧式车床用C61×××来表示,其中C为机床分类号,表示车床类机床;61为组系代号,表示卧式。
其它表示车床的有关参数和改进号。
2.卧式车床各部分的名称和用途C6132普通车床的外形如图1-3所示。
图1-3 C6132普通车床1-床头箱;2-进给箱;3-变速箱;4-前床脚;5-溜板箱;6-刀架;7 -尾架;8-丝杠;9-光杠;10-床身;11-后床脚;12-中刀架;13-方刀架;14-转盘;15-小刀架;16-大刀架图1-4 刀架图1-5 尾座1顶尖 2套筒锁紧手柄 3顶尖套筒 4丝杆 5螺母 6尾座锁紧手柄 7手轮 8尾座体 9底座(三)卧式车床的传动系统电动机输出的动力,经变速箱通过带传动传给主轴,更换变速箱和主轴箱外的手柄位置,得到不同的齿轮组啮合,从而得到不同的主轴转速。
普通车床加工工艺步骤
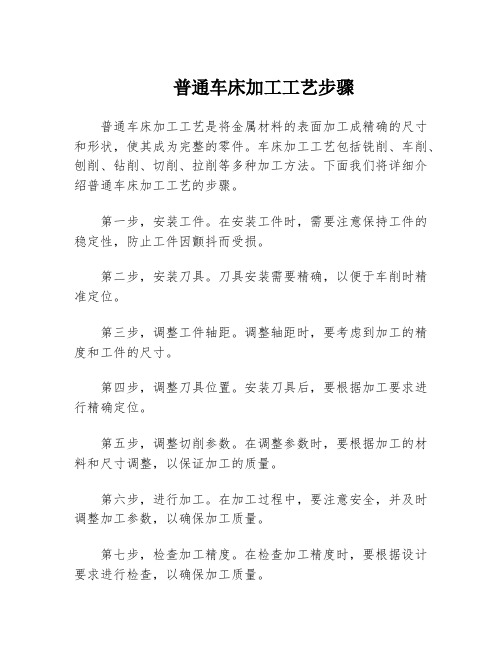
普通车床加工工艺步骤
普通车床加工工艺是将金属材料的表面加工成精确的尺寸和形状,使其成为完整的零件。
车床加工工艺包括铣削、车削、刨削、钻削、切削、拉削等多种加工方法。
下面我们将详细介绍普通车床加工工艺的步骤。
第一步,安装工件。
在安装工件时,需要注意保持工件的稳定性,防止工件因颤抖而受损。
第二步,安装刀具。
刀具安装需要精确,以便于车削时精准定位。
第三步,调整工件轴距。
调整轴距时,要考虑到加工的精度和工件的尺寸。
第四步,调整刀具位置。
安装刀具后,要根据加工要求进行精确定位。
第五步,调整切削参数。
在调整参数时,要根据加工的材料和尺寸调整,以保证加工的质量。
第六步,进行加工。
在加工过程中,要注意安全,并及时调整加工参数,以确保加工质量。
第七步,检查加工精度。
在检查加工精度时,要根据设计要求进行检查,以确保加工质量。
以上就是普通车床加工工艺的步骤。
车床加工工艺是一种精密加工工艺,需要有一定的技术要求,且操作过程也比较复杂,因此在实施过程中应注意安全,同时根据加工要求调整车床参数,以确保加工质量。
普通车床加工简单实例1

磨床 钳工台
°
工艺路线
• • • •
•
•
• • • •
工序0 : 铸造 工序5:涂防锈漆 工序10:时效 工序20: 车(1)粗车、半精车端 面C 、Φ200外圆、粗车、半精车 Φ60圆孔、精车端面C (2)调头粗车、半精车端面A、 Φ96外圆、端面B、精车端面A(车 床) 工序30: 钳工 划内键槽线及 6×Φ20孔中心线 工序40 :插 插槽(插床) 工序50 :钻 钻6 × Φ20孔(钻床) 工序60:钳工 去毛刺(钳工台) 工序70:检验
车床
40
车
1
车床 车床
50
车
1 2
60
铣
1 2
1、2 3、4
铣床
70
钳工 检验
钳工台
80
思考题5解答:工艺编制
• • • • • • • • • • •
P157
• • • • •
需要加工表面:所有 A:粗——半精——精(1.6) B:粗——精(6.3) C:粗——半精——精(1.6) Φ200外圆:粗——精(3.2) Φ60孔:粗——精(1.6) 其余:粗 加工顺序: (1)粗车、半精车端面C 、Φ200外圆、 粗镗、半精镗Φ60圆孔、精车端面C; (2)调头粗车端面A、Φ96外圆、端面B、半精车端面A、端 面B、精车端面A(车床) (3)划内键槽线及6×Φ20孔中心线 (4)插槽(插床) (5)钻6 × Φ20孔(钻床) (6)去毛刺(钳工台) (7)检验
2
3 4 5 6
30 40 50 60
钳 插 钻 钳
思考题6解答:制订机械加工工艺,具体条
件:45钢,圆料ф70,小批量生产。
其余
• • • • • • • • • • •
数控车工普车操作图纸大全

外圆车削(一)要求:车削一定要在熟悉车床之后进行并首先会刃磨外圆车刀。
D L Ra1Ø45—00.10142±0.50 6.32Ø40—00.10140±0.303.2序号质检内容配分评分标准1 外圆公差30 超0.02扣5分2 外圆RX6.3 20 降一级扣10分3 长度公差10 超差不得分4 倒角二处5×2 不合格不得分5 平端面二处5×2 不合格不得分6 接刀痕 5 接刀痕大扣分7 工件完整 5 不完整扣分8 安全文明操作10 违章扣分第三次课件请保留阶台车削(二)序号质检内容配分评分标准1 外圆公差三处10x3 超0.01扣2分2 外圆Ra3.2 三处6x3 降一级扣3分3 长度公差三处4x3 超差不得分4 倒角二处3x2 不合格不得分5 平端面二处4x2 不合格不得分6 清角去锐边四处2x4 不合格不得分7 工件完整 5 不完整扣分8 安全操作10 违章扣分材料毛坯时间45 Ø50x145材料毛坯时间45 Ø50x150多阶台车削(三)序号质检内容配分评分标准1 外圆公差六处5x6 超0.01扣2分,超0.02不得分2 外圆Ra3.2 六处3x6 降一级扣2分3 长度公差六处3x6 超差不得分4 倒角二处2x2 不合格不得分5 清角去锐边十处10 不合格不得分6 平端面二处2x2 不合格不得分7 工件外观 6 不完整扣分8 安全文明操作10 违章扣分此件用上次课件改制材料毛坯时间45一夹一顶车削(四)序号质检内容配分评分标准1 外圆公差四处8x4 超0.01扣2分,超0.02不得分2 外圆Ra3.2 四处4x4 降一级扣2分3 长度公差四处3x4 超差不得分4 倒角二处3x2 不合格不得分5 清角二处2x3 不合格不得分6 平端面二处3x2 不合格不得分7 中心孔 5 不合格不得分8 工件外观7 不完整扣分9 安全文明操作10 违章扣分要求:会正确使用A.B型中心钻。
车床加工案例
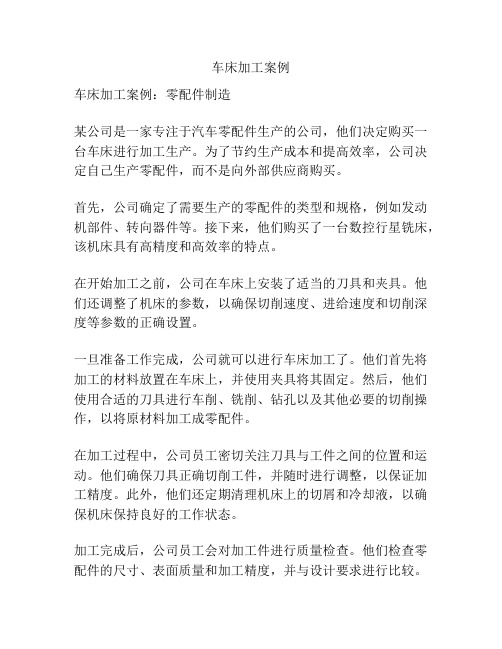
车床加工案例车床加工案例:零配件制造某公司是一家专注于汽车零配件生产的公司,他们决定购买一台车床进行加工生产。
为了节约生产成本和提高效率,公司决定自己生产零配件,而不是向外部供应商购买。
首先,公司确定了需要生产的零配件的类型和规格,例如发动机部件、转向器件等。
接下来,他们购买了一台数控行星铣床,该机床具有高精度和高效率的特点。
在开始加工之前,公司在车床上安装了适当的刀具和夹具。
他们还调整了机床的参数,以确保切削速度、进给速度和切削深度等参数的正确设置。
一旦准备工作完成,公司就可以进行车床加工了。
他们首先将加工的材料放置在车床上,并使用夹具将其固定。
然后,他们使用合适的刀具进行车削、铣削、钻孔以及其他必要的切削操作,以将原材料加工成零配件。
在加工过程中,公司员工密切关注刀具与工件之间的位置和运动。
他们确保刀具正确切削工件,并随时进行调整,以保证加工精度。
此外,他们还定期清理机床上的切屑和冷却液,以确保机床保持良好的工作状态。
加工完成后,公司员工会对加工件进行质量检查。
他们检查零配件的尺寸、表面质量和加工精度,并与设计要求进行比较。
如果发现任何不合格的零件,他们会重新进行加工,直到满足要求为止。
最后,公司将加工好的零配件清洗,并进行表面处理,如喷漆、电镀等。
然后,他们将零配件进行包装,并准备发货给客户。
通过自己的车床加工,公司能够更好地控制生产过程和质量。
由于自己生产零配件,公司可以减少成本,并确保供应的及时性。
此外,他们还可以根据市场需求调整生产计划,并快速响应客户的要求。
总之,车床加工在零配件制造中起着重要作用。
通过正确使用车床和合适的加工方法,公司可以提高生产效率,满足客户需求,并获得竞争优势。
普通车床加工简单实例课件

实践操作步骤及注意事项
3. 选择刀具
根据加工需求,选择合适的刀具,并进行安装和调整。
4. 调整机床参数
根据加工要求,调整车床的主轴转速、进给速度等参数。
5. 开始加工
启动车床,进行加工操作,注意观察加工过程,及时调整参数或更 换刀具。
准备好所需的所有工具,如刀具、量具、 夹具等,并确保它们都完好无损。
将待加工的工件放置在机床的工作台上, 并确保工件固定稳定。
装夹工件
01
选择夹具
根据工件的形状和大小,选择 合适的夹具,并将夹具固定在
机床的工作台上。
02
装夹工件
将工件放置在夹具中,并使用 压板、螺栓等工具将工件固定
在夹具中。
03
检查固定情况
削。
操作步骤
1. 选择合适的车刀,确定切 削用量和切削速度。
2. 将毛坯夹持在卡盘上,调 整卡盘转速和进给速度。
3. 用车刀从毛坯端面开始, 按照图纸要求的尺寸进行切 削。
4. 在切削过程中,注意调整 车刀角度和进给量,保证圆 锥体的锥度和精度。
螺纹的加工
加工方法:使用螺纹车刀在工件表面切削出螺纹。 操作步骤 1. 选择合适的螺纹车刀,确定切削用量和切削速度。
在加工完成后,应先关闭机床电 源,再将刀具和工件从机床上取
下。
工件检查
对加工完成的工件进行检查,如发 现有缺陷或不符合要求的地方,应 及时进行返工或处理。
机床维护
对机床进行维护保养,如清理切屑 、更换油液等,以保证机床的良好 运转状态。
03
普通车床加工简单实例
圆柱体的加工
- 1、下载文档前请自行甄别文档内容的完整性,平台不提供额外的编辑、内容补充、找答案等附加服务。
- 2、"仅部分预览"的文档,不可在线预览部分如存在完整性等问题,可反馈申请退款(可完整预览的文档不适用该条件!)。
- 3、如文档侵犯您的权益,请联系客服反馈,我们会尽快为您处理(人工客服工作时间:9:00-18:30)。
其余
2 3 4 5 10 15 20 25 钳工 铣削 钻削 钳工 检验 1 1
铣键槽 钻4×Φ6孔 去毛刺
思考题6:编制图示挂轮架轴的机械加工工艺过程。 0.02 零件材料:45钢,小批生产。技术要求: 25 0.04 和方头处淬火40~45HRC,未注倒角1×45°。 (热处理:正火、调质)
30 40 60
热 磨 检
思考题8:如图所示方头小轴,中批量生产, 材料为20Cr,要求12h7 mm段渗碳(深 0.8mm~1.1mm),淬火硬度为HRC50 ~ HRC55 ,试拟定其机械加工工艺路线。
方头小轴制造工艺路线 下料:20Cr钢棒22mm×470mm若干段 1 粗 加 工 3 5 7 9 半 精 加 工 17 精 加 工 25 19 21 23 磨 11 13 15 车 车 铣 、 12mm圆柱段。 车 车
思考题3解答:工序、安装、工位 、工步、工步划分示意表
序 号 10 工序 下料 1 20 车 2 30 40 50 60 车 车 车 铣 1 2 1 2 1 2 1 2 1 1 2 1、2 3、4 安 装 工 位 工步 内 容
:
切断 车端面 钻中心孔 车另一端面 钻另一中心孔 车φ30mm 外圆 车φ20mm 外圆 车φ18mm 外圆 倒角1×45° 车螺纹M20 铣两平面 铣另两平面
在锯床上切断下料; 车一端面钻中心孔,调 头,车另一端面钻中心 孔;在另一台车床上将 整批工件一端外圆都车 至φ30mm及φ20mm ;调头再用车刀车削整 批工件的φ18外圆;又 换一台车床,倒角,车 螺纹;最后在铣床上铣 两平面,转90°后,铣 另外两平面。
思考题4 图示零件,材料为HT200 。小批量生产 时,制定其机械加工工艺。
• 思考题1 写出小批生产如图所示螺栓 零件的机械加工工艺过程(包括工序、 安装、工步)工件的毛坯为圆棒料、 材料为Q235。
:
• • • • • • • • • • • • • •
序号 工序 1 车削
安装 工位 1(三爪夹盘)
2
车削
1 (三爪夹盘)
工步 1 2 3 4 5 6 7 1 2
内容 (1)车端面A (2)车外圆E (3)车螺纹外径D (4)车端面B (5)倒角F (6)车螺纹 (7)切断 (1)车端面C (2)倒棱G 铣六方
0.02 0.04
定位基准
外圆 一夹一顶 一夹一顶
一夹一顶 顶尖
外圆及两端面
检验
思考题7 编制图示轴套的机械加工工艺过程。 零件材料:45钢,小批生产。技术要求:淬 火HRC40~45,未注倒角1×45°。
:
思考题7解答:轴套机械加工工艺过程
序号 工序 10 20 锯 车 工 序 内 容 定位基准 棒料Φ50mm×150mm 车端面、外圆、内孔、倒角、外圆 切断等(内外圆留余量 0.3mm) 淬火40~45HRC 磨内孔至要求 外圆 磨外圆、端面、倒角至要求 内孔 检验
工艺路线
• 工序1(1)粗车、半精车端 面C 、Φ200外圆、粗车、 半精车Φ60圆孔、精车端面 C • (2)调头粗车、半精车端 面A、Φ96外圆、端面B、精 车端面A(车床) • 工序2:划内键槽线及 6×Φ20孔中心线 • 工序3 :插槽(插床) • 工序4 :钻6 × Φ20孔(钻 床) • 工序5:去毛刺(钳工台) • 工序6:检验
挂轮架轴机械加工工艺过程
序号 10 20 30 40 50 60 70 80 90 100 110 120
工序 下料 热处理 车削 热处理 车削 钳工 铣削 钳工 热处理 车削 磨削 检验
工 序 内 容 下料(棒料) 正火 粗车端面、中心孔、外圆 调质 精车外圆、切槽、倒角 划线 铣方头、两平面 去毛刺 淬火 车螺纹M16、M18 粗精磨 25
20
车
30 40 50 60 70
钳 插 钻 钳 检验
思考题5解答:制订机械加工工艺,具体条
件:45钢,圆料ф70,小批生产。
其余
序号 工序 0 车削
安装 1
内容 粗车、半精车右端面、 Φ40外圆、台阶面、钻、 扩Φ14孔; 调头粗车、半精车左端面、 Φ60外圆、粗、半精镗 Φ30孔; 调头精车Φ40外圆; 调头以Φ40为基准面,精 镗Φ30孔,端面。 划键槽线及6×Φ6孔中心 线
(读图P157)
°
•
>30孔铸造
°
需要加工表面:所有 A:粗——半精——精(1.6) B:粗——半精(6.3) C:粗——半精——精(1.6) Φ200外圆:粗——半精(3.2) Φ60孔:粗——半精(1.6) 其余:粗 加工顺序: (1)粗车、半精车端面C 、Φ200外圆、 粗镗、半精镗Φ60圆孔、精车端面C; (2)调头粗车端面A、Φ96外圆、端面B、半精车端面A、端面 B、精车端面A(车床) (3)划内键槽线及6×Φ20孔中心线 (4)插槽(插床) (5)钻6 × Φ20孔(钻床) (6)去毛刺(钳工台) (7)检验
3 4 5
铣削 去毛刺 检验
1(分度头) 1-6
思考题2解答:一根长100mm的轴,材料为 12CrNi3A渗碳钢,外圆直径Φ100mm, 表面粗糙度Ra0.4um外圆表面要求渗碳 淬火硬度HRC55~60,试选择该外圆的 加工方法并写出机械加工工艺路线。
(中批量生产)
基准
• 车端面-钻中心孔-车另一端面-钻另一 中心孔-粗车外圆-淬火-研磨中心孔、 端面-磨外圆-检验
夹左端柱段,车右端面及右端外圆,留磨余量每面0.2mm(7mm
不车),按长度切断,每段切留余量(2~3)mm。
夹右端柱段,车左端面,留余量2mm;车左端外圆至20mm。
检验 渗碳
夹左端 20mm段,车右端面,留余量1mm,打中心孔;车7mm 夹12部分,车左端面至尺寸,打中心孔。
铣削17mm×17mm方头。 检验 淬火 HRC50~55 。
磨端面、中心孔 粗糙度Ra0.4m 磨各面、磨12h7 mm外圆,达到图纸要求。 去毛刺 检验
编写盘套件工艺过, 外圆直径Φ100mm,表面粗 糙度Ra0.4um外圆表面要求渗碳淬火硬度HRC55~ 60。 • 3、
其余
°
热处理:方头处淬火40~45HRC,正火、调质
°
序号 0 5 10
工序
安装
工位
工步
内 铸造
容
设备
涂防锈漆 时效 1 2 3 1 4 5 6 7 1 2 2 3 4 5 6 粗车端面C 半精车端面C 粗车Φ200外圆 精车Φ200外圆 粗车Φ60圆孔 精车Φ60圆孔 精车端面C 粗车端面A 半精车端面A 车Φ96外圆 粗车端面B 精车端面B 精车端面A 划内键槽线及6×Φ20孔中心线 插槽 钻6 × Φ20孔 去毛刺 钳工台 插床 钻床 钳工台 车床