粗铜的火法精炼工艺
粗铜的火法精炼(楚雄)
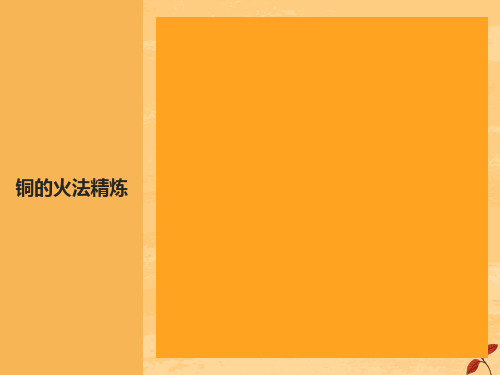
炉子密封性差,散热损失大,烟气泄漏多,车间环境差。
氧化、还原作业,对于氧化剂和还原剂的利用率低。
风管及辅助材料消耗大,操作效率低。
炉子操作安全性不如回转精炼炉和倾动精炼炉。
氧化、还原、扒渣和出铜等作业全部是手工操作。劳动量和劳动强度大,劳动条件差,难以实现机械化和自动化。
1、固定式射炉的缺点
固定式反射炉结构
三、固定式反射炉
固定式反射炉是传统的火法精炼设备,是一种表面加热的膛式炉,结构简单,操作容易,可以处理冷料,也可以热料,可以烧固体燃料、液体燃料或气体燃料。炉子容积可大、可小,波动范围较大。为了在精炼时使各部分熔体的温度保持均匀,从而使熔体各部分的杂质(特别是气体)含量及浇铸温度均匀,炉子作业空间不能太长以免发生温度降,为使熔池温度趋于一致,精炼炉有1.5~2m的燃烧前室,而且把炉顶做成下垂式,保证炉尾温度与炉子中央的温度相近。
无论采用固体、液体或气体燃料,燃烧过程的好坏是决定反射炉供热状况的首要条件。燃烧过程与烧嘴构造、烧嘴性能、燃烧条件以及操作等因素有关。诸如燃料与空气混合均匀、燃料入炉的扩散角适当、入炉后能尽快着火、及合理的火焰长度和温度等,都是保证燃料有效燃烧的重要条件。此外,由结构型式和尺寸决定的炉子本身的热工特性,也影响着炉内的传热。
火法冶炼铜及湿法冶炼铜工艺介绍

题,不利于贵金属等有价伴生元素的回收, 因此在工业上未得到广泛应用。
• 我国铜冶炼主要以火法冶炼为主,总产量占全 部铜产量约96%,我国也是采用铜冶炼工艺种 类最多的国家,国际上先进的铜冶炼技术在我 国大多已采用,且生产规模远大于其它国家, 同时仍存在大量采用落后生产工艺、污染严重 的中小型铜冶炼企业,根据《有色金属产业调 整和振兴规划》的要求,铜冶炼行业规划目标 是:按期淘汰落后产能,节能减排取得积极成 效,企业重组取得进展,创新能力明显增强, 资源保障能力进一步提高。
• 火法炼铜的原则流程如下,流程图见图
• 铜精矿(15~30%Cu)——造锍熔炼——冰 铜 (铜锍25~70%Cu)——吹炼——粗铜 (98~99%Cu)——火法精炼——阳极铜 (99%Cu)——电解精炼——电铜(99.9599.98%Cu)。
• 火法炼铜生产过程一般由以下几个工序组 成:备料、熔炼、吹炼、火法精炼、电解 精炼,最终产品为电解铜。配套工序:阳 极泥处理、余热回收、余热发电、烟气收 尘、烟气制酸、循环水系统等。
• 火法冶炼铜主要产物环节如下:
• 除火法工艺外,近20 年来湿法炼铜工艺也取 得了长足的进步,湿法工艺不仅可以处理一些 难选的氧化矿和表外矿、铜矿废石等,而且随 着细菌浸出和加压浸出的发展,亦可以处理硫 化铜矿石,并能获得较好的经济效益,从而大 大拓宽了铜资源综合利用范围。该法是在常温 常压或高压下,用溶剂浸出矿石或焙烧矿中的 铜,经过净液,使铜和杂质分离,而后用萃取 -电积法,将溶液中的铜提取出来。对氧化矿 和自然铜矿,大多数工厂用溶剂直接浸出;对 硫化矿,一般先经焙烧,而后浸出。
火法冶炼及湿法冶炼 铜工艺介绍
• 铜的冶炼工艺有火法冶炼和湿冶炼两种 方法。
铜冶炼水平与工艺水平

铜冶炼水平与工艺水平1)火法冶炼工艺当前,全球矿铜产量的75%-80%是以硫化形态存在的矿物经开采、浮选得到的铜精矿为原料,火法炼铜是生产铜的主要方法,特别是硫化铜精矿,基本全部采用火法冶炼工艺。
火法处理硫化铜精矿的主要优点是适应性强,冶炼速度快,能充分利用硫化矿中的硫,能耗低。
其生产过程一般由以下几个工序组成:备料、熔炼、吹炼、火法精炼、电解精炼,最终产品为电解铜。
原料制备工序:将铜精矿、燃料、熔剂等物料进行预处理,使之符合不同冶炼工艺的需要。
熔炼工序:通过不同的熔炼方法,对铜精矿造硫熔炼,炼成含铜、硫、铁及贵金属的冰铜,使之与杂质炉渣分离;补出的含二氧化硫烟气经收尘后用于制造硫酸或其他硫制品,烟尘返回熔炼炉处理。
吹炼工序:除去冰铜中的硫铁,形成含铜及贵金属的粗铜,炉渣和烟尘返回上一工序处理。
火法精炼工序:将粗铜中硫等杂质进一步去除,浇铸出符合电解需要的阳极板。
电解精炼工序:除去杂质,进一步提纯,生产出符合标准的阴极铜成品,并把金银等贵金属富集在阳极泥中。
传统熔炼方法如鼓风炉熔炼、反射炉熔炼和电炉熔炼,由于效率低、能耗高、环境污染严重而逐渐被新的富氧强化熔炼工艺所代替[[3]新的富氧强化熔炼可分为闪速熔炼和熔池熔炼两大类,前者包括奥托昆普型闪速熔炼和加拿大国际镍公司闪速熔炼等,后者包括诺兰达法、三菱法、艾萨法、奥斯麦特法和瓦纽可夫法以及我国自主开发的水口山法、白银炉熔炼、金峰炉熔炼等技术。
铜锍吹炼方法有传统的卧式转炉、连续吹炼炉、虹吸式转炉。
新型吹炼技术包括艾萨吹炼炉、三菱吹炼炉和闪速吹炼炉等。
粗铜的火法精炼在阳极炉内进行,对于转炉产出的液态粗铜采用回转式阳极炉或固定式反射炉精炼,经氧化、还原等作业进一步脱除粗铜中的铁、铅、锌、砷、锑、铋等杂质,并浇铸成含铜99.2%-99.7%的阳极板。
铜电解工艺有传统电解法、永久阴极电解法和周期反向电流电解法3种。
目前大多数电解铜厂都使用传统电解法,永久阴极电解法和周期反向电流电解法是20世纪70年代以来发展的新技术。
粗铜的火法精炼

书山有路勤为径,学海无涯苦作舟粗铜的火法精炼铜锍吹炼产出的粗铜含有较高的硫、氧和其他一些杂质,如铁、钴、锌、铅、锡、镍、砷、锑、铅等,此外还有含有硒、碲、锗、金、银等稀有元素和贵金属,其总含量可达0.5%~2%。
为除去粗铜中的杂质和回收贵金属等有价元素,应将粗铜进行火法精炼和电解精练。
火法精炼只能将对氧亲和力较大的杂质除到一定的程度,而贵金属仍留于火法精炼铜中。
粗铜火法精炼的目的是为电解精炼提供合乎要求的阳极铜,并浇铸成表面平整、厚均匀、致密的阳极板,以保证电解铜的质量和降低电解精炼的成本。
在火法精炼时,由于铜是主体,杂质浓度很低,故铜首先被氧化:4[Cu]+O2=2[Cu2O] 生成的氧化亚铜溶于铜熔体中,将铜液中的杂质Me 氧化:[Cu2O]+[Me]=2[Cu]+(MeO)欲使杂质残留于铜液中的极限浓度最低,应控制以下因素:(1)氧化亚铜始终保持饱和状态;(2)降低杂质氧化物的活度;(3)温度不宜太高。
粗铜火法精炼多采用固定式精炼炉、回转式精炼炉,也还有倾动式精炼炉。
表1 和表2 列出了国内外一些火法精炼过程的指标。
表1 国内火法精炼技术经济指标(一)厂别铜精炼回收率/%铜精炼真收率/%床能率/t·(m2·d)-1 燃料还原剂种类单耗/kg·t-1 种类单耗/kg·t-1 鑫冶(上海)99.9199.28.28 重油80~90 重油6 白银99.6958~12 重油70~90 重油8 云冶99.898.74 重油87 木炭粉13 重冶99.698.54.36 天然气167m3/t 柴油11 株冶99.797 重油90~110 重油10~20 广冶99.0296.83.1 重油180 重油6 贵冶99 重油50~60 液化石油气4~6 大冶98 重油42 重油5~6 表1 国内火法精炼技术经济指标(二)厂别烟气废热利用每炉还原时间/h 渣率/%渣含铜/%电耗/kW·h·t-1 水耗/t·t-1 铸模消耗/个·t-1(阳极)利用方式利用率/%鑫冶(上海)锅炉空气预热器生产蒸汽热风621.50.5~0.610~30301.8 铸铁120。
生产铜的工艺(3篇)

第1篇一、引言铜作为一种重要的金属资源,广泛应用于电气、电子、机械、建筑、装饰等领域。
我国是世界上最大的铜消费国,铜产业的发展对国民经济具有重要意义。
本文将详细介绍生产铜的工艺,包括铜的采矿、选矿、冶炼、精炼等环节。
二、采矿1. 铜矿床类型铜矿床主要分为:沉积铜矿床、火山岩铜矿床、矽卡岩铜矿床、斑岩铜矿床等。
2. 铜矿开采方法(1)露天开采:适用于埋藏较浅、规模较大的铜矿床。
主要采用爆破、挖掘、运输等工序。
(2)地下开采:适用于埋藏较深、规模较小的铜矿床。
主要采用凿岩、爆破、装载、运输等工序。
三、选矿1. 选矿目的选矿是将铜矿石中的铜矿物与其他矿物分离,提高铜的品位和回收率。
2. 选矿方法(1)物理选矿:包括重力选矿、磁选、浮选等。
(2)化学选矿:包括浸出、溶剂萃取、电解等。
3. 物理选矿(1)重力选矿:利用矿物密度差异进行分离。
如跳汰选矿、摇床选矿等。
(2)磁选:利用矿物磁性差异进行分离。
如湿式磁选、干式磁选等。
(3)浮选:利用矿物表面性质差异进行分离。
如油酸、水玻璃等浮选剂。
4. 化学选矿(1)浸出:利用溶剂与铜矿物反应,使铜溶解于溶液中。
如硫酸浸出、酸浸等。
(2)溶剂萃取:利用萃取剂与铜离子形成可溶性络合物,实现铜的分离。
如硫酸铜萃取、氯化铜萃取等。
(3)电解:利用电解质溶液中的铜离子在电极上还原成金属铜。
如阳极泥电解、阳极泥火法冶炼等。
四、冶炼1. 冶炼目的冶炼是将选矿后的铜精矿转化为金属铜,提高铜的纯度。
2. 冶炼方法(1)火法冶炼:包括熔炼、吹炼、精炼等工序。
(2)电解精炼:将铜精矿或阳极泥电解成高纯度铜。
3. 火法冶炼(1)熔炼:将铜精矿与焦炭、石灰石等熔剂混合,在高温下熔炼成粗铜。
(2)吹炼:利用吹炼炉将粗铜吹炼成阳极铜。
(3)精炼:将阳极铜电解成高纯度铜。
4. 电解精炼(1)阳极:采用阳极泥或电解精炼后的阳极铜作为阳极。
(2)阴极:采用纯铜板作为阴极。
(3)电解液:采用硫酸铜溶液作为电解液。
铜的加工冶炼工艺流程
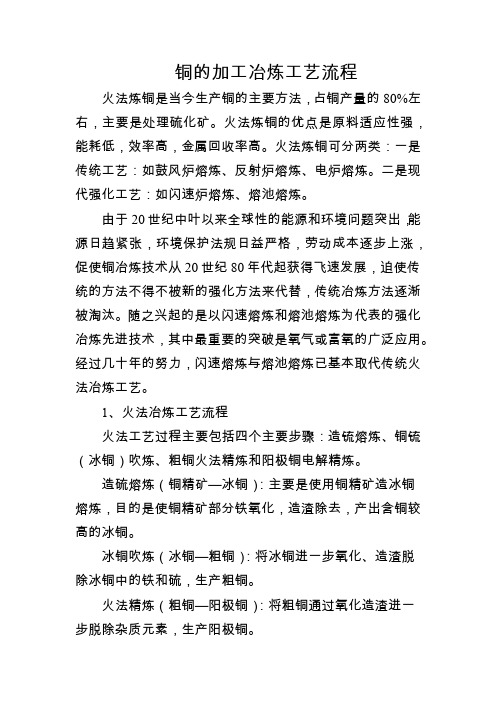
铜的加工冶炼工艺流程火法炼铜是当今生产铜的主要方法,占铜产量的80%左右,主要是处理硫化矿。
火法炼铜的优点是原料适应性强,能耗低,效率高,金属回收率高。
火法炼铜可分两类:一是传统工艺:如鼓风炉熔炼、反射炉熔炼、电炉熔炼。
二是现代强化工艺:如闪速炉熔炼、熔池熔炼。
由于20世纪中叶以来全球性的能源和环境问题突出,能源日趋紧张,环境保护法规日益严格,劳动成本逐步上涨,促使铜冶炼技术从20世纪80年代起获得飞速发展,迫使传统的方法不得不被新的强化方法来代替,传统冶炼方法逐渐被淘汰。
随之兴起的是以闪速熔炼和熔池熔炼为代表的强化冶炼先进技术,其中最重要的突破是氧气或富氧的广泛应用。
经过几十年的努力,闪速熔炼与熔池熔炼已基本取代传统火法冶炼工艺。
1、火法冶炼工艺流程火法工艺过程主要包括四个主要步骤:造锍熔炼、铜锍(冰铜)吹炼、粗铜火法精炼和阳极铜电解精炼。
造硫熔炼(铜精矿—冰铜):主要是使用铜精矿造冰铜熔炼,目的是使铜精矿部分铁氧化,造渣除去,产出含铜较高的冰铜。
冰铜吹炼(冰铜—粗铜):将冰铜进一步氧化、造渣脱除冰铜中的铁和硫,生产粗铜。
火法精炼(粗铜—阳极铜):将粗铜通过氧化造渣进一步脱除杂质元素,生产阳极铜。
电解精炼(阳极铜—阴极铜):通过引入直流电,阳极铜溶解,在阴极析出纯铜,杂质进入阳极泥或电解液,从而实现铜和杂质的分离,产出阴极铜。
火法炼铜一般流程图2、火法冶炼工艺分类(1)闪速熔炼闪速熔炼(flash smelting)包括国际镍公司因科(Inco)闪速炉、奥托昆普(Outokumpu)闪速炉和旋涡顶吹熔炼(ConTop)3种。
闪速熔炼是充分利用细磨物料巨大的活性表面,强化冶炼反应过程的熔炼方法。
将精矿经过深度干燥后,与熔剂经干燥一起用富氧空气喷入反应塔内,精矿粒子在空间悬浮1-3s时间,与高温氧化性气流迅速发生硫化矿物的氧化反应,并放出大量的热,完成熔炼反应即造锍的过程。
反应的产物落入闪速炉的沉淀池中进行沉降,使铜锍和渣得到进一步的分离。
火法炼铜工艺讲解

火法炼铜工艺讲解1 概述铜是人类应用的最古老的金属之一,它有很长的、很光辉的历史。
考古学证明,早在一万年前,西亚人已用铜制作装饰品之类的物件。
铜和锡可制成韧性合金青铜,考古发现在公元前约3000年,历史已进入了青铜时代。
而今铜的化学、物理学和美学性质使它成为广泛应用于家庭、工业和高技术的重要材料。
铜具有优良可锻性、耐腐蚀性、韧性,适于加工;铜的导电性仅次于银,而其价格又较便宜,故而被广泛应用于电力;铜的导热性能也颇佳;铜和其他金属如锌、铝、锡、镍形成的合金,具有新的特性,有许多特殊的用途。
铜是所有金属中最易再生的金属之一,再生铜约占世界铜供应总量的40%。
铜以多种形态在自然环境中存在,它存在于硫化物矿床中(黄铜矿、辉铜矿、斑铜矿、蓝铜矿)、碳酸盐矿床中(蓝铜矿、孔雀石)和硅酸盐矿床中(硅孔雀石、透视石),也以纯铜即所谓“天然铜”的形态存在。
铜以硫化矿或氧化矿形式露天开采或地下开采,采出矿石经破碎后,再在球磨机或棒磨机中磨细。
矿石含铜一般低于1%。
1.1 国内外铜冶金的发展现状目前国内外的铜冶炼技术的发展主要还是以火法冶炼为主,湿法为辅。
铜的火法生产量占总产量的80%左右。
目前,全世界约有110座大型火法炼铜厂。
其中,传统工艺(包括反射炉、鼓风炉、电炉)约占1/3;闪速熔炼(以奥托昆普炉为主)约占1/3;熔池熔炼(包括特尼恩特炉、诺兰达炉、三菱炉、艾萨炉、中国的白银炉、水口山炉等)约占1/3。
另外,世界范围内铜冶金工业同样面临铜矿资源短缺的问题,国土资源部信息中心统计资料表明:在世界范围内,铜是仅次于黄金的第2个固体矿产勘查热点,全球固体矿产勘查支出中约20%是找铜的,并且这一比例还有增加的趋势。
相应地,铜也是各大势力集团争夺的焦点之一。
从全球角度看铜的保证年限只有约29年。
铜的主要出口国是拉美发展中国家。
1.2商洛情况全市已发现各类矿产60种,已探明矿产储量46种,其中大型矿床15处,中型矿床24处。
铜火法精炼和湿法精炼

铜火法精炼和湿法精炼铜火法火法精炼是利用某些杂质对氧的亲和力大于铜,而其氧化物又不溶于铜液等性质,通过氧化造渣或挥发除去。
其过程是将液态铜加入精炼炉升温或固态铜料加入炉内熔化,然后向铜液中鼓风氧化,使杂质挥发、造渣;扒出炉渣后,用插入青木或向铜液中注入重油、石油气或氨等方法还原其中的氧化铜。
还原过程中用木炭或焦炭覆盖铜液表面,以防再氧化。
精炼后可铸成点解精炼所用的铜阳极或铜锭。
精炼炉渣含铜较高,可返回转炉处理。
精炼作业在反射炉或回转精炉内进行。
火法精炼的产品叫火精铜,一般含铜99.5%以上。
火精铜中常含有金、银等贵金属和少量杂质,通常要进行电解精炼。
若金、银和有害杂质含量很少,可直接铸成商品铜锭。
粗铜火法精炼主要由鼓风氧化和重油还原两个操作环节构成。
铜中有害杂质除去的程度主要取决于氧化过程,而铜中氧的排除程度则取决于还原程度。
1.氧化过程由于粗铜含铜98%以上,所以在氧化过程中,首先是铜的氧化:4Cu+O2=2Cu2O生成的Cu2O溶解于铜液,在操作温度1373~1523K条件下,Cu2O在铜中的杂质金属(Me)发生反应:Cu2O +Me=2Cu+MeO反映平衡常数:K=[MeO]*[Cu]/[Cu2O][Me]因为MeO在铜里溶解度小,很容易饱和;而铜的浓度更大,杂质氧化时几乎不发生变化,故都可视为常数,因此K*=[Me]/[Cu2O]所以,Cu2O的浓度越大,杂质金属Me的浓度就越小。
因此,为了迅速完成地出去铜中的杂质,必须使铜液中Cu2O的浓度达到饱和。
升高温度可以增加铜液中Cu2O的浓度,但温度太高会使燃料消耗增加,也会使下一步还原时间延长,所以氧化期间温度以1373~1423K为宜。
此时Cu2O的饱和浓度为6%-8%。
氧化除杂质时,为了减少铜的损失和提高过程效率,常加入各种溶剂如石英砂,石灰和苏打等,使各种杂质生成硅酸铅、砷酸钙等造渣除去。
脱硫是在氧化精炼最后进行,这是因为有其他对氧亲和势力的金属时,铜的硫化物不易被氧化,但只要氧化除杂质金属结束,立即就会发生剧烈的相互反应,放出SO2: CuS+2Cu2O=6Cu+SO2这时铜水出现沸腾现象,称为“铜雨”。
- 1、下载文档前请自行甄别文档内容的完整性,平台不提供额外的编辑、内容补充、找答案等附加服务。
- 2、"仅部分预览"的文档,不可在线预览部分如存在完整性等问题,可反馈申请退款(可完整预览的文档不适用该条件!)。
- 3、如文档侵犯您的权益,请联系客服反馈,我们会尽快为您处理(人工客服工作时间:9:00-18:30)。
粗铜的火法精炼工艺1概述1.1阳极炉精炼的目的粗铜火法精炼的任务是除去一部分杂质,目的是为电解精炼提供合乎要求的阳极铜,并浇铸成表面平整、厚度均匀、致密的阳极板,以保证电解铜的质量和降低电解精炼的成本。
1.2阳极炉精炼的过程描述转炉产出的粗铜装入粗铜包子,用液体吊车倒入阳极炉内,先通入压缩空气使之产生氧化反应,氧化结束后扒出炉渣,开始通入还原剂使之产生还原反应,还原结束后开始浇铸,精炼过程采用重油做燃料。
阳极板的双圆盘定量浇铸系统是由程序来自动控制的。
产生的烟气经过空气换热器冷却后经排空。
1.3阳极炉精炼的工艺流程2粗铜火法精炼原理粗铜的火法精炼包括氧化与还原两个主要过程。
粗铜的火法精炼通常是在1150~1250℃的温度下,先向铜熔体中鼓入空气,使铜熔体中的杂质与空气中的氧发生氧化反应,以金属氧化物MO形态进入渣中,然后用碳氢还原剂将熔解在铜的氧出去,最后浇铸成合格的阳极送去电解精炼。
2.1阳极炉精炼氧化原理及主要物理化学变化阳极炉氧化精炼是在1150~1200℃的高温下,将空压风鼓入熔铜中,由于铜液中大多数杂质对氧的亲合力都大于铜对氧的亲合力,且多数杂质氧化物在铜水中的溶解度很小,当空气中的氧通入铜熔体中便优先将杂质氧化除去。
脱硫是在氧化过程中进行的。
向铜熔体中鼓入空气时,除了O2直接氧化熔铜中的硫产生SO2之外,氧亦熔于铜中。
但熔体中铜占绝大多数,而杂质占极少数,按质量作用定律,优先反应的是铜的大量氧化:4Cu+O2=2Cu2O所生成的Cu2O 溶解于铜水中,其溶解度随温度升高而增大。
1100℃,溶解的Cu2O=5%,相应的O2=0.56%1150℃,溶解的Cu2O=8.3%,相应的O2=0.92%1200℃,溶解的Cu2O=12.4%,相应的O2=1.38%1250℃,溶解的Cu2O=13.1%,相应的O2=1.53% 500℃1083℃20406080100Cu 重量% CuO700℃900℃1065℃1200℃1230℃3.4712.41300℃当Cu2O 含量超过该温度下的溶解度时,则熔体分为两层,下层是饱和了Cu2O 的铜液相,上层是饱和了铜的Cu2O 液相。
溶解在铜熔体中的Cu2O ,均匀地分布于铜熔体中,能较好地与铜熔体中的杂质接触,那些对氧亲和力大于铜对氧亲和力的杂质(Me),便被Cu2O所氧化:[Cu2O] + (Me)=2[Cu] + [MeO]。
这样在氧化精炼中一部分发生Cu—Cu2O—Cu的变化而起到氧的传递剂作用。
铜熔体中杂质氧化主要是以这个方式进行的。
当然,也有少部分杂质,直接被炉气或空气中的氧所氧化,其反应为:2(Me)+ O2=2 [MeO]。
这种反应,在氧化精炼中不占主导地位。
为了使空气中的氧尽量与铜反应生成Cu2O,且使Cu2O与杂质良好接触,进而氧化杂质。
就必须把空气鼓入铜熔体中,使空气形成无数小气泡,使铜熔体翻腾,以增大气—液相接触面,加快Cu2O和杂质间的扩散,强化氧化精炼过程。
铜液中Cu2S和其它金属硫化物,它在精炼初期氧化的较缓慢,但在氧化后期时,温度达1175℃时,硫在铜液中溶解度可达9%,开始按[Cu2S]+2[Cu2O]=6[Cu]+SO2反应激烈地放出SO2,使铜水沸腾,有小铜液滴喷溅射出,形成所谓“铜雨”而将硫脱除,也标志着氧化将结束。
2.2阳极炉氧化过程杂质行为杂质的氧化顺序,从理论上说,可按杂质对氧的亲合力的大小来粗略地判断,其排列顺序为铝、硅、锰、锌、铁、镍、砷、锑、硫、铋、铜、银、金。
然而,在实际精炼过程中,杂质氧化的明显顺序是不存在的,而是许多杂质同时发生氧化,只是在某一个时刻氧化程度不同而已杂质的氧化顺序和除去程度,与下列因素有关:(1)杂质在铜中的浓度和对氧的亲合力;(2)杂质氧化后所生成的氧化物在铜中的溶解度;(3)杂质及其氧化物的挥发性、杂质氧化物的造渣性。
上述因素中,杂质的浓度、对氧的亲合力和杂质氧化物在铜中的溶解度是主要因素,杂质及其氧化物在铜中的溶解度愈大,则该杂质愈难除去,杂质对氧的亲合力愈小,则该杂质愈难氧化,因而也难以除去。
因此在阳极炉精炼过程中,杂质按其易难除去程度可分为三类:易除去的、难除去的和不能除去的。
(1)易除去杂质:包括铁、锌、铅、锡、硫等A、铁:铁是易于除去的杂质,它在铜的熔体中是有限溶解,不与铜生成化合物,在火法精炼中,能迅速而完全地除去,它在炉料的熔化和氧化阶段初期即被氧化成FeO并与石英熔剂作用生成硅酸盐炉渣,或进一步氧化成Fe2O3,与其它金属氧化物生成铁酸盐即MeO. Fe2O3炉渣。
如精炼作业在碱性炉衬的炉子中进行,过程又不加入石英熔剂,则全部的铁几乎都氧化成Fe2O3而呈铁酸盐炉渣。
B、锌:锌和铜在液态时互溶,固态时形成一系列固溶体。
精炼过程中,锌可直接蒸发,熔体中的ZnO在有还原剂覆盖铜熔体的情况下,也能被还原成金属锌而蒸发,并在炉气中被氧化成ZnO ,随炉气排出。
此外,还有一部分ZnO与SiO2作用生成硅酸锌即ZnO·SiO2,与Fe2O3生成铁酸锌即ZnO·Fe2O3炉渣。
当精炼含锌高的铜料时,为加速锌的蒸发,在熔化期和氧化期均应提高炉内温度,并在熔体表面覆盖一层木碳或不含硫的焦炭颗粒,使还原成金属锌蒸发,以免生成结块而妨碍蒸锌过程的正常进行。
C、铅:铅和铜在固态时互不溶解,在铜熔体中溶解度很小,但铅对电解的危害较大,须将其控制在所允许的范围内,铅的氧化是在铜熔化时就开始,一直延续到开始还原时为止,通常采用的除铅方法是向炉内加入石英熔剂,使PbO成硅酸盐的形态除去,因PbO浓度较大,固用压缩空气强制将细粉状熔剂吹入熔体内效果较好。
然而用硅酸盐造渣脱铅的方法操作时间长,铜的损失大,炉渣酸性化,对碱性炉衬腐蚀严重,尤其是要使铅的含量降低到0.005%以下更是如此。
此外用氧化硼作剂,使铅呈硼酸盐形态除去,亦有显著效果,但其成本较高。
D、锡:锡是比较难以除去的杂质,但从处理矿石或精矿得到的粗铜中,含锡很少,一般只有万分之几,不会给精炼作业带来较大困难。
锡在氧化成,其可用加入碱性熔剂如Na2CO3和CaO等方法除去。
E、硫:硫在粗铜中,主要以Cu2S和其它金属硫化物形式存在,它在精炼初期氧化的较缓慢,但在氧化后期时,便开始按[Cu2S]+2[Cu2O]=6[Cu]+SO2反应激烈地放出SO2,使铜水沸腾,有小铜液滴喷溅射出,形成所谓“铜雨”。
要使硫降至0.008%以下,在1200℃时铜水含氧在0.1%即可。
然而为了加速反应,实践中常将氧的浓度提高到0.9~1%,保持熔体中Cu2O为饱和状态。
同时采用低硫的重油供热,炉气中SO2浓度应低于0.1%,防止SO2溶解于铜熔体中,温度应控制在1200℃,并使炉内为中性或微氧化性气氛。
(2)难除去的杂质:包括镍、砷、锑A、镍:镍在氧化阶段氧化缓慢,而氧化生成的分布在炉渣和铜水中,镍之所以难除去,一方面由于镍对氧的亲合力接近于铜,另一方面在有砷、锑存在时,镍、砷、锑的氧化物形成易深于铜熔体中的三元氧化物,阻碍镍进入炉渣。
镍氧化生成的NiO.Cu2O和As2O5.Sb2O5生成镍和铜的砷酸盐和锑酸盐,即6 Cu2O.8 NiO. As2O5和6 Cu2O.8 NiO. Sb2O5,所谓“镍云母”它们部分溶于铜中,使除去镍、砷、锑困难,部分沉积炉底易形成炉结,为了除镍,除添加使生成的造渣外,还可加入分解和破坏镍云母,减少这些化合物在铜熔体中的溶解。
B、砷、锑砷、锑在精炼时,如形成 As2O3和Sb2O3,易于挥发而除去,如形成As2O5和Sb2O5,则不能挥发,与铜的氧化物生成砷酸盐和锑酸盐,溶解于铜熔体中,难以除去。
在精炼的氧化期,砷和锑生成具有挥发性的三氧化物,即As2O3和Sb2O3,一部分随炉气逸出,其余部分与铜生成可溶于铜熔体的亚砷酸铜和亚锑酸铜,如熔体中始终饱和以Cu2O时,砷、金北的三氧化物将继续氧化成不挥发的五氧化物,即As2O5和As2O5 ,并生成砷酸铜和锑酸铜溶解于铜熔体中。
当精炼含砷、锑相当高的粗铜时,根据砷、锑化合物的性质,可采取重复氧化和还原数次,将其从铜中除去,可向铜熔体中加入Na2CO3或CaO等碱性溶剂,使砷、锑生成不溶于铜的砷酸钠、砷酸钙、锑酸钠、锑酸钙,组成炉渣,上升到熔体表面而被除去。
(3)不能除去杂质:包括金、银、硒、碲、铋等A、金和银:金、银在火法精炼中不被氧化而留在精炼铜中,只有银部分地被挥发性杂质如锌、砷、锑等带走,因此银损失可达2.5%。
B、硒、碲:硒和碲在粗铜中的含量很少,通常只是十万分之几,硒、碲在氧化精炼时,有少量被氧化成SeO2、TeO2,随炉气排出,但大部分的硒、碲仍留在铜液中,在电解精炼时,从阳极泥回收。
C、铋:铋与铜在熔体中完全互溶,对氧的亲合力与铜差不多,沸点又高,因此,既不能氧化,又不能挥发除去,基本进入铜液中。
对于我们处理的二次铜精矿,其主要杂质成份为铁、镍、硫、金银贵金属及稀有金属,所以进入火法精炼炉中的粗铜液它可能存在的杂质也不外乎这几种。
2)阳极炉精炼还原原理及主要物理化学变化在氧化精炼过程中,为了有效地除杂脱硫,必须使Cu2O在熔体中达到饱和的程度,这样在氧化精炼结束时,铜熔体中仍残留着相对数量的Cu2O。
为了满足阳极铜的要求,必须把这部分Cu2O还原成金属铜。
我国铜火法精炼中常用的还原剂有:木炭或焦粉、粉煤以及插木法还原、重油、天然气、甲烷或液氨。
其中使用气体还原剂是最简便的但受区域影响无法普及,近年来国内各工厂大都采用重油作还原剂,虽然还原效果好,也比较经济,但油烟污染严重。
随着目前环保趋势要求,使用粉煤为原料的固体还原剂开始普及。
无论采用哪种还原剂,其还原过程均为还原性物质对氧化亚铜的还原。
下面以重油作还原剂为例分析其还原过程。
重油主要成份为各种碳氢化合物,高温下分解才成氢和碳,而碳燃烧成CO。
所以重油还原实际上是氢、碳、一氧化碳及碳氢化合物对氧化亚铜的还原:Cu2O+H2=2Cu+H2O Cu2O+C=2Cu+COCu2O+CO=2Cu+C2O 4Cu2O+CH4=8Cu+C2O+2H24Cu2O+CuHm=8Cu+0.5(m-2)H2+H2O+C2O+CO在用重油做还原剂时,铜熔体中出现的气体有CO、C2O、H2O、N2、H2、和SO2。
前四种气体基本上不溶解于铜熔体中,而后两种气体则溶解于铜熔体中。
采用重油还原时,铜样断面不如插木还原的铜样光亮,其原因是插木时分解放出大量水蒸汽、氢气和甲烷等,水蒸汽的存在稀释了氢气的浓度,降低了氢的分压。
而用重油还原时,分解出来的水蒸汽很少,故氢气浓度大、氢的分压较大。
而氢在铜水中的溶解度与其分压的平方根成正比。
所以用重油还原时吸收的氢比插木还原多,当铜凝固时,部分氢析出,铜样断面出现许多微观小孔,使其外观金属光泽不亮。