绿油培训教材
湿绿油丝印工艺培训教材
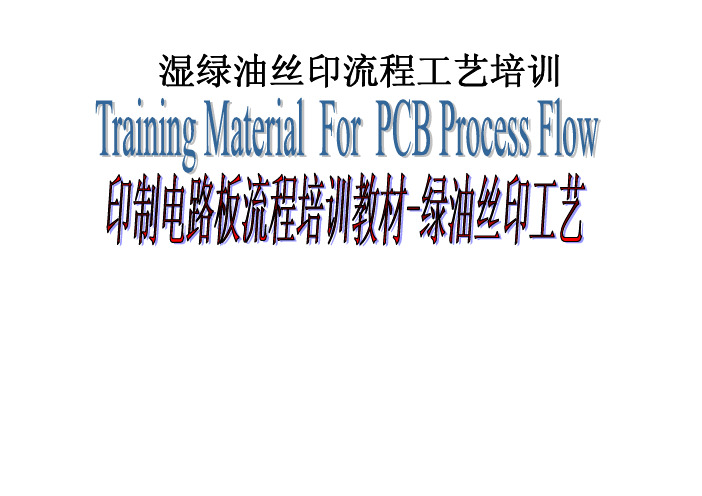
课堂守则•请将手机、BP机等通讯工具调到震动状态。
•请勿在上课期间,随意进出,以免影响其他同事。
•请勿交头接耳、大声喧哗。
•如有特殊事情,在征得培训导师的同意的情况下,方可离场。
以上守则,各位学员共同遵守绿油干净房工作环境绿油的作用防焊油墨的种类绿油流程图丝印前处理流程1.2.1磨板A.目的除去氧化及前工序胶渍及不明污染,增加铜表面粗糙度。
B.流程酸洗水洗火山灰磨板高压水洗DI水洗(水洗/超声波水洗) 风干烘干C.参数控制磨板机火山灰浓度范围控制在15~25%,磨痕宽度11~14mm,板面水膜维持时间大于15S。
对于停放在洁净房内超过4hr的板需重新磨板处理。
丝网介绍丝网简介a.网布材料(1) 依材质不同可分丝绢(silk),尼龙(nylon),聚酯(Polyester,或称特多龙),不锈钢,等.电路板常用者为后三者.(2) 编织法:最常用也最好用的是单丝平织法Plain Weave.(3) 网目数(mesh),网布厚度(thickness),线径(diameter),开口(opening)的关系网目数:每inch或cm中的开口数线径: 网布织丝的直径网布厚度:厚度规格有六,Slight(S),Medium(M), Thick(T),Half heavy duty(H),Heavyduty(HD),Super heavy duty(SHD)图显示印刷过程网布各元素扮演角色丝印刮刀a.刮刀硬度:70-75b.每班研磨一次c.刮刀角度:8-15刻度网与台面高度•网与台面高度约5-15mm丝印流程B.制程步骤丝网准备网版制造丝印第二面(钉床)油墨搅拌磨胶刮丝印第一面预热曝光板检查磨板预热丝印第二面丝印后停放•1)板子丝印油墨后的停放时间:• a.一般的板子丝印后到进行入炉预局的停放时间:最少10min,最长60min;• b.用36T网丝印板面的板子丝印后到进行入炉预局的停放时间:最少:30min,最长60min;• c.底铜≥2OZ的铜板丝印板面后到进行入炉预局的停放时间:最少:30min,最长60min;• d.丝印PSR-4000MH油墨的板子:•①丝印一次的板子:丝印后到进行入炉预局的停放时间:最少:60min,最长120min;•②丝印Linemask的板子:丝印Linemask后到进行入炉预局的停放时间:最少:10min ,最长60min;丝印板面按①进行。
绿油培训教材

绿油培训教材一、磨板1.开机前检查各缸液位看是否正常,检查喷嘴有无阻塞。
2.在磨板前,开机检查各马达运转是否正常。
3.做磨痕测试及水膜测试(磨痕12-15mm,水膜倾斜15º,15秒不破)。
4.磨板时时常检查喷嘴是否阻塞,各缸液位是否够。
5.在磨厚度不同板时,要重新做磨痕测试及水膜测试。
6.参数微蚀缸NPS 40~60g/lH2SO43~5g/l烘干段温度90±5℃速度不超过2.5m/min二、丝印1.品质要求:油墨均匀、孔内无绿油、无漏印、手指印、线路发红、钉床压伤、颗粒杂物、丝印不良、油墨入孔、油墨下发黑、不过油等现象。
2.目的:规范作业,保证品质。
3.适应范围:适应于本公司绿油丝印工序。
4.作业流程:查网→装网→装PIN→上刮胶→下油→调机→试印(合格)→批量印刷→插架5.丝印、塞孔参数控制范围:丝印气压:4-6kg/cm²塞孔:1-3 m/min 丝印:2-5 m/min网版:36T、39T、43T 丝印两次阻焊油:51T 油墨粘度:100-180PS刮胶硬度:65-75º丝印速度:2-5 m/min 网距:5-8mm6.塞孔板之特殊操作事项:塞BGA:采用钻孔铝片塞孔,塞孔铝片孔比板孔径大0.05mm。
1)刮胶硬度:65º2)塞孔油墨不允许添加开油水。
3)刮刀速度:1-3m/min 刮刀压力:最大(6kgkm²)4)第一面塞孔后板面不允许有明显油墨堆积,第二面见油珠或油珠平孔环即可。
5)塞孔必须用塞孔垫板作业。
6)其它走正常流程。
7)质量记录,每次生产前首件记录。
7-开油操作指示:A.调油步骤:1)根据MI领取并核对油墨型号名称和有效期。
2)取硬化剂加入主剂中,以各种油墨厂家规定的比例配制。
3)根据实际情况加入30毫升以下或不添加稀释剂搅拌15分钟以上,静止15分钟后注明时间,方可交付生产使用。
B.质量检查:1)开好的油墨用干净的油刀检查颜色是否一致、无颗粒,如有问题须知会组长或主管。
绿油培训教材

A、开启总电源和启动掣
B、开启显影一、二,循环水洗一、二、三、四 C、开启过滤泵、摇摆、强风吹干、热风吹干、照明、加热 掣等 D、开启“输送掣”,按要求调节速度于2.0-3.5m/min
E、待温度到达后,开始生产
F、生产中检查显影段的药水压力是否正常 G、关机时,依次将所有启动掣关闭,最后关闭总电源
4.2 操作条件 曝光能量: 300-1000mj/cm2
曝光指数:
真空度: 环境温度: 湿度: 尘粒:
30-160
650mmhg 18-22C 45%-65% 0.5m以下尘粒少于100K
曝光机温度: 15-20C
红菲林GII: 使用次数不超过600次
绿油培训教材
5、冲板(显影Development) 5.1 基本操作
绿油培训教材
5、冲板(显影)
冲板是指利用1%的碱性碳酸钠溶液与未曝光部分的绿
油发生化学反应,从而使绿油被冲洗掉的过程。经显影
后,通过UV机使绿油进一步硬化,以增加绿油的硬度。
绿油培训教材
6、印字( Component Mark)
采用丝印方法,依照客户要求在元件面(Component Side)
印上一些标记符号,以利于元件的安装及辨认。
铜面不受蚀刻液攻击而电镀的保护层。在蚀刻完成之后
需用褪锡药水将之除去,剩下所需之裸铜面,以便进行 后工序的制作。
绿油培训教材
2、磨板
本工序磨板过程是采用机械方法,利用大山灰对板
的高速冲击作用,以及高压水洗、超音波水洗,达
到粗化表面及清洁的目的,增加绿油的附着力。
绿油培训教材
3、涂布 涂布是指采用廉涂方式(Curtain coating)在板面上印
绿油培训教材
绿油培训讲义

绿油培训讲义一、丝印W/F目的1.使线路板形成阻焊层2.防止线路铜氧化二、涂布W/F方式1.丝网印刷2.帘式涂布3.静电喷涂三、W/F流程W/F前处理丝印预热曝光显影固化四、各工序特点1.前处理a.目的:除氧化,粗化铜b.要紧参数:磨痕宽度,磨刷速度c.常见问题①板面星点氧化:风刀堵塞或风管破旧漏风或鼓风机故障②板面光泽差:砂粉浓度低、增加砂粉③板面有砂粉:砂粉粒径过大,更换幼小砂粉2.丝印:a.目的:涂布绿油b.要紧参数:油墨粘度、刮胶硬度、网纱目数、拉网斜度c.常见问题:①只是油:油墨粘度高,刮胶硬度低或丝印压力小,网版垃圾②塞孔:丝印压力过大,索纸频率不足③聚油:油墨丝印过厚,绿油粘度高,丝印后静量时刻不足3.预热:a.目的:将涂布层中之溶剂挥发,便于曝光时绿油不粘GIIb.要紧参数:预锔温度、预锔时刻四、曝光a.目的:对绿油进行光固化b.重要参数:曝光尺c.常见问题:①背光渍:1.曝光能量高——降低、曝光能量2.板料问题——更换为U V料或黄料②菲林印:1.预热程度不足——增加预锔温度或时刻③曝光不良:1.真空度不足——提高真空度2.菲林光密度不足——换用新菲林,光密度≥3.5D五、冲板a.目的:将曝光之绿油留于板面,未曝光之绿油去除b.要紧参数:显影速度,显影温度,显影压力,药水浓度c.常见问题:①冲板不净:1. 预热过宽——降低预热温度,缩短时刻2.显影不足——速度降低,药水浓度压力较高至规定值3.绿油丝印过薄——增加绿油丝印厚度②显影速度:1.预热不足——增加预锔程度2.丝印过厚——降低绿油丝印厚度3.显影过分——增长率快显影速度,降低药水压力4.曝光能量低——升高曝光能量③辘痕:开高曝光能量,降低药水温度④绿油哑色:升高曝光能量,增加预热程度六、固化a.目的:对W/F进行热固化b.要紧参数:固化温度,固化时刻c.要紧问题:①底铜氧化:1.油薄———丝印加厚2.炉温过高———QA测量,修理调校3.烘锔时刻长———缩短烘锔时刻②甩油:烘锔时刻不足———增加烘锔时刻七、其它常见问1.线路氧化a.前处理问题:相应调整磨板参数及校调机器b.外来水分触板c.丝印前放置时刻过长:高速至4hr内2.固化后塞油VIA孔弹油a.后高温固化前预烘不足:增加预烘时刻b.超能力塞油VIA孔设计问题:改变设计或试用新型绿油c.设备问题不能保证低温:QA检测,PM跟进。
绿油工序培训教材(PPT 82页)

2.3 制作中的工艺控制 板面前处理 —— 火山灰 & 氧化铝粉磨板机
火山灰浓度:10-20vol%(参考)
测试方法:开机搅拌火山灰 & 氧化铝粉槽20分钟左右,用 烧杯取100ml,静置,待火山灰&氧化铝粉完全 静置下来,检查火山灰&氧化铝粉所在刻度: 10~20间为正常,16为佳。
18
磨痕宽度:12+/-2mm(参考),磨痕宽度的大小代表着板面磨损的程 度,而磨痕宽度的均匀性则代表着板面磨损是否均匀。
利用压缩空气将调稀绿油以雾化粒子的方式喷射在板面的绿油印 制方式.
11
1.3 本公司阻焊膜制作现状
本公司现广泛采用的是液态感光绿油,小部分为热固化油墨(非感光 型)制作绿油塞孔. 另外,本公司现存两种工艺方式在大批量生产,即 1)丝印绿油(Screen Print) 2)涂布绿油(Curtain Coating) 在第三部分将分丝印绿油及涂布绿油两种不炉
低温炉上的温度及时间设置匹配很重要,当温度过高, 设置时 间长,则绿油在冲板时不易从板面冲掉,从而影响焊锡性能;相 反当温度过低,设置时间短时,湿绿油尚未烘干,在曝光时会出 现底片压痕,显影时油墨易受显影液的浸蚀,引致脱落.
低温预锔炉的烘板效果不够,有一个简单的检验方法: 将出低温炉的板,待板面凉下来后,用大拇指按绿油面一 下,再碎布轻轻擦拭,如果拇指印仍在不消失,则证明预锔 不够,正常情况下应无拇指印。
测试方法:
(1)使用手动档开动磨板机(关磨辘)运输,放入一长度18〃或以上的 板。
(2)板行置火山灰磨辘后停止运输,开动磨辘运转约10S,停止磨辘。 (3)仅开动运输将板退出,观察板面磨痕宽度是否均匀,测量全部磨
痕的宽度,应全部在10-14mm范围内,否则应调整磨辘深度手轮。
绿油工序培训教材

1.2 阻焊膜之 分类
1.2.1 从油墨的感光类型来分,可分为感光型及非感光型.
非感光型油墨主要采取丝网印刷的方式,根据客户要求, 选取针对焊盘位加挡点,其他位则漏油的丝印网进行制作.其 工艺简单,性能可靠,但在印板过程中存有局限性.
而感光型油墨则可以采取多种涂覆方式.同时可以满足 绿油越来越高的分辨率要求,故其使用日益广泛.
水溶性显影之油墨因为其成本低,操作简单,亦可满足现制板的显影 制作,故在亚洲,九成以上的PCB厂采用水溶性显影之油墨。
1.2.3 从油墨的组成成分上来分,可分为纯环氧树脂类,环氧丙烯酸 共聚合物类,环氧丙烯酸混合物类和丙烯酸类. 对于油墨制造商来说,环氧树脂类的制作成本高于丙烯酸类,
但其的阻焊性能及物理化学性能均优于丙烯酸类.
真空度:60--75cmhg
曝光时,之所以有真空度要求,基于如下原理:如真空度达到要求 ,
曝光时的光线在两层mylar面射入时,发生折射的现象大大减少,可
Mylar
菲林 以保证曝光效果,有绿油窗遮光的部分不 会出现
1.2.4 从油墨的制作方式上可分为丝网印刷,幕帘涂布,静电喷涂, 辊涂,气式喷涂等方式,业界广为采用的为丝网印刷及幕帘涂 布.
丝网印刷(Screen Print)
在已有负性图案的网布上,用刮刀刮挤出适量的绿油油墨,透过 网布形成正形图案,印在基面或铜面上.
丝网印刷设备成本低,工艺简单,对制板类型的适用性高,可满足客 户各种高难度要求,但需要操作员工具有一定的技术要求,对于亚 洲,人力充足,成本低廉,故丝网印刷在亚洲较盛行.
第三部分 —— 绿油印技术 ---------- ---------- ---------- - 30
3.1 辅助工具介绍 ---------- ---------- ---------- ---------- ---- 32 3.2 丝印技术 ---------- ---------- ---------- ---------- ----- ----- 56
推荐-完整的原版绿带培训教材DMAIC各部分一 精品

120.84
117.32
Number of Distinct Categories = 8
round down( 2 Parts ) 1.414 23.1104
MS
4.0535
P / TV MS 4.0535 20.27%
Historical
20
有什麼發現? (運用工具找出什麼重要結果/結論之重點摘要?)
環境 Environment
物料 Materials
人員 Personal
排風不良(C) 落塵量過高(C)-X5
物料過期(C)
混料(C) 熱壓皮不良(C) 耗材不良(C) 清潔劑不良(C)
FPC不良(C) 客戶來料
不良(C)-X2
背光不良(C) 人員懶散 外觀不良(C)(C) LCD來料 不良(C)-X3
7.746
0.0000
錫少
0.384 74
0.12909 9
2.980 2
0.0014
Overall
0.748 07
0.06534 9
11.44 73
0.0000
OK
0.944 34
0.12909 9
7.314 8
0.0000
空銲
0.666 37
0.12909 9
5.161 6
0.0000
站立
1 0.12909 7.746 0.0000
10
2.4 製程能力
Average σ Zlt
Ppk Zst
製程能力估計
電性不良(C)
福利較差(C) 加班時數 過長(C)
流動率高(N)
薪資太低(C) 教育訓練不 完整(未C依)規定 作業(C)-X1
PCB绿油磨板培训教材
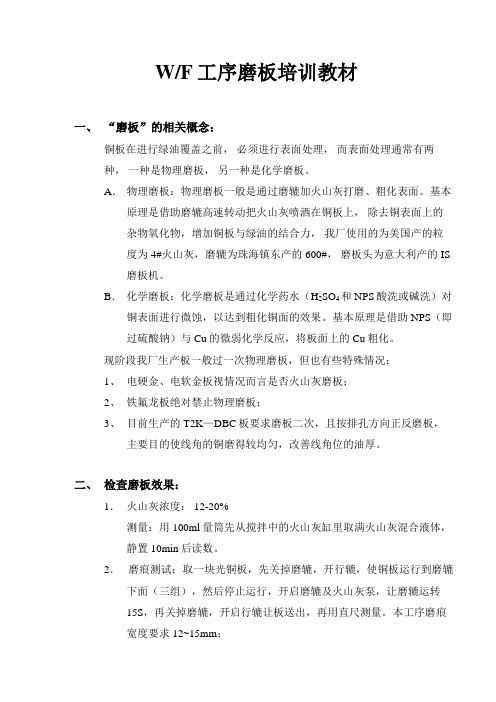
W/F工序磨板培训教材一、“磨板”的相关概念:铜板在进行绿油覆盖之前,必须进行表面处理,而表面处理通常有两种,一种是物理磨板,另一种是化学磨板。
A.物理磨板:物理磨板一般是通过磨辘加火山灰打磨、粗化表面。
基本原理是借助磨辘高速转动把火山灰喷洒在铜板上,除去铜表面上的杂物氧化物,增加铜板与绿油的结合力,我厂使用的为美国产的粒度为4#火山灰,磨辘为珠海镇东产的600#,磨板头为意大利产的IS磨板机。
B.化学磨板:化学磨板是通过化学药水(H2SO4和NPS酸洗或碱洗)对铜表面进行微蚀,以达到粗化铜面的效果。
基本原理是借助NPS(即过硫酸钠)与Cu的微弱化学反应,将板面上的Cu粗化。
现阶段我厂生产板一般过一次物理磨板,但也有些特殊情况:1、电硬金、电软金板视情况而言是否火山灰磨板;2、铁氟龙板绝对禁止物理磨板;3、目前生产的T2K—DBC板要求磨板二次,且按排孔方向正反磨板,主要目的使线角的铜磨得较均匀,改善线角位的油厚。
二、检查磨板效果:1.火山灰浓度: 12-20%测量:用100ml量筒先从搅拌中的火山灰缸里取满火山灰混合液体,静置10min后读数。
2.磨痕测试:取一块光铜板,先关掉磨辘,开行辘,使铜板运行到磨辘下面(三组),然后停止运行,开启磨辘及火山灰泵,让磨辘运转15S,再关掉磨辘,开启行辘让板送出,再用直尺测量。
本工序磨痕宽度要求12~15mm;3.水膜试验:将磨好之光铜板浸泡在水中45S,然后取出与水平成45度角,停放15S,观察水膜是否破裂,如破裂,则磨板效果不好,反之则OK。
三、磨板机的构造基本工艺流程:入板段→酸洗段→磨板段→水洗段→烘干段→收板段备注:1.磨板一次铜的厚度变量为0.01mil~0.02mil;2.磨板入板时左右轮放,且两板之间距离应保持在2-4cm;3.酸洗主要是去除板表面的油污及杂物;4.水洗一般分为清水洗、高压水洗、DI水洗等多个缸,其作用主要是冲掉表面残留的火山灰、药水、杂物等;5.烘干段的作用主要是将表面及孔内的水用强风及高温去掉,防止板氧化;6.电硬金板必须调整好磨辘压力后才能批量生产,此类板在磨板是一定不能露镍。
- 1、下载文档前请自行甄别文档内容的完整性,平台不提供额外的编辑、内容补充、找答案等附加服务。
- 2、"仅部分预览"的文档,不可在线预览部分如存在完整性等问题,可反馈申请退款(可完整预览的文档不适用该条件!)。
- 3、如文档侵犯您的权益,请联系客服反馈,我们会尽快为您处理(人工客服工作时间:9:00-18:30)。
W/F培训教材(初级)一、绿油常见名词释义:W/F:Wet Film S/M :Solder MaskD/I:Deionized water S/M Dam:S/M桥(俗称狗根)Fiducial Pad:锡钉对位PAD Sec:离子污染LMS、Line Mask (线面印刷) SIR:表面绝缘电阻Under Cut 绿油底部冲走翘起 VIP:Via in PadVBP:Via Between Pad S/M开窗S/M Open二、W/F所使用物料、Tooling简介:1、绿油种类及作用。
a. 环氧树脂IR(烘烤型)b.UV硬化型c.液态感光显像型 (本厂常用)d.干膜防焊剂.2、S/M主要用途:阻焊、绝缘、防氧化(护板)抗恶劣环境耐热、耐酸碱、防腐蚀、美观等。
3、S/M主要成份:合成树脂 UV及热硬化酚醛、甲酚二酸感光剂启动UV硬化查酮填充剂填充粉(硅石粉)色料(黄、蓝、紫、红、白、绿、黑)消泡平坦剂(消泡平坦)溶剂(脂类)流动性4、液态感光显像油墨原理:利用感光性树脂加硬化性树脂产生互穿式聚会成立体网状结构,以达到绿油的强度,在显影显像时则利用树脂中含有酸根键,可以弱碱( Na2Co3)溶液显像。
在终固化后链状聚合成立体网状结构。
5、红网、刮胶、菲林、Na2CO3、NaOH、丝印机。
1)网目数:43T & 36T “T”表示网目数,单位面积内网孔数(cm2)2)线径:网布织丝的直径网布,43T(65微米)开孔个数每 cm2 43个3)厚度:厚度规格阻焊35um、字符25um、碳油50um兰胶80um4)网张力:直接影响对位,因为印刷过程中对网布不断拉扯,因而新网张力非常重要一般测量5点四角和中间一个点,另网布采用染黄色聚酯网纱而得到更高显像。
5)刮胶:a. 材料常用有聚氨脂类(PU)b. 刮胶的硬度肖氏 60~80度目前 70~75度(肖氏)c. 刮胶长度对网版图案每侧长出 3—4英寸d. 刮胶平整及高度(须磨刮、高度要求)>2.8cm以上,小于或等于即时更换并且每班须换面印刷。
6)菲林:黑菲林材料:银盐片(遮光率好,易擦花)Dk≥4.0 Do≤0.15 红或黄菲林重氮片(遮光稍差不易擦花)Dk≥3.5 Do≤0.257)Na2Co3:用弱碱 1±0.2%浓度, 用来显像溶解冲洗未曝光部份的绿油8)NaoH :烧碱用来退S/M(包括终固化之绿油)9)丝印机:采用台湾产 AT-EW-800 型半自动丝印机 CL:800 HD型三、W/F流程:磨板丝印预焗曝光显影终固化A .磨板目的:去除氧化及前工序胶渍及不明污染物,增加铜表面粗糙度.参数:火山灰浓度 12~20% 7号火山灰磨痕宽度 10~15mm磨板后到丝印停放时间≥15min≤4 hr酸洗浓度 3~5%NPS 20~40 G/L流程:酸洗水洗火山灰磨高压水洗 DI水洗风干烘干磨板重点控制的缺陷:一、氧化 a、检查各缸水洗是否正常开启b、吸水辘是否吸水(吸水已吸饱和、太干燥、破损)c、冷强风风刀方向是否正确,风刀无堵塞,风管接口无松脱d 、烘干温度是否在要求值如A3# 65±5℃e、 H2SO4浓度是否正常 3~5%二、磨板不良:拖尾、亮板(未磨到)、磨辘痕、铜面污。
a. 做磨痕测试是否合格不合格要求SE调校、如压力调到最大值仍磨不到板即时更换磨辘(拖尾)b、检查磨辘两边压辘(黑色胶辘)机座是否磨损压不紧板造成跳辘未磨到板即更换压辘机座(亮板)c、磨辘痕主要为磨辘压力不均匀按a控制d、铜面污检查酸洗后段水洗是否有喷咀堵塞或水洗流量小造成酸污染水洗缸或火山灰缸,同时清理喷咀调整水洗压力,如已深度氧化污渍严重的板须重打粗磨一次(到PTH)三、擦花: a、保养机器后要用废板试机检查各段行辘运转正常,(每班生产前亦如此)b、放板距离至少2cm以上(一般要求50~60mm)(注:磨板面积不同的板隔的距离要更大例如先磨P修理板再放正常大板)c、放板不可放偏以磨板机卡子介为准d 、不可单手接收板B、丝印:目的、利用丝网图案在PCB板面印刷一层均匀绿油参数:丝印速度 2—5格胶刮角度 8—15度网与平台距离 0.6~1.5cm胶刮气压 4~6 bar油墨粘度 135±25 dps 硬:主 1:3流程:上网对位开油对位膜丝印检查C、预焗目的:用热循环炉使油墨内溶剂充分挥发使油墨部分硬化,曝光时不粘菲林。
参数:温度:70±3℃时: 43T 45~48min 36T 60~70min丝印:重点控制的缺陷一、先讲第一个问题,如何才能印好板。
准备工作:1、选取好刚磨好(平整锋利)的胶刮2、清洁好网、放板平台、丝印机平台、机身。
3、检查丝印机胶刮运行情况、速度均匀、上升、下降平稳包括网框两边上升下降的螺丝、胶刮上升下降的气压4、把丝印平台微调归零5、按油墨登记表中选好油墨6、上网用铜板装好3片管位钉,使网版挡油点基本与铜板上各孔对准,即时用皱纹胶固定3管位片,固定网框。
7、用皱纹胶圈按压网框调节丝印微调更进一步对位8、装上胶刮调节胶刮压应器在网版中的有效行程,固定感应器9、下油到网中,索纸用对网膜准确调位看板四周角都调正,不可调时松网、拉网调整。
10、首板检查无偏位、无塞孔、无油薄、无不过油、无聚油、无刮痕印无杂物。
11、批量生产,索纸后检板二、胶刮调整:刮胶硬度:70~75度(肖氏)胶刮高度>2.8cm每班换边气压 4~6 bar丝印方式左右双胶刮印刷与网框网版图案形成22.5度斜度胶刮与丝网印刷形成夹角在75~85度更适宜.(印刷原则:带斜度顺线路印刷)三、印刷方式:0.6mm以上。
四、丝印缺陷控制:1、油薄:油墨粘度偏低油墨太干粘网网清洁不足不透油(网显影不净)油墨加稀释剂搅伴不均匀胶刮不平整、锋利2、S/M塞孔:对位不良索纸不足丝印压力过大网掉挡油PAD或挡油点变小下油过多,油墨回流钉床底板探针清洁不足3、杂物:丝印房含尘量超标网底及平台清洁不足封网胶脱胶预焗炉含尘量高使用过期油墨4、不过油:胶刮不平整锋利油墨粘度过大丝印气压太小底铜过厚丝印速度过快5、丝印偏位:网变形张力不合格对位不准确6、预焗不良:焗死板,焗板不干1、a、焗板温度过高,时间过长b、焗炉内温度分布不均匀2、a、焗板温度过低,时间过短b、炉内抽风不良c、放板方向不正确d、油墨已贮存过期e、叠板焗炉D、曝光:目的:利用film底片通过强uv光照射使受光部分绿油形成聚合反应,使用它由单分子转换成高分子网状交连结构。
参数:菲林寿命:≥2 OZ ≤300次<2 OZ ≤450次真空度≥60cmHG灯管寿命:≥1200 hr 须更换(ORC机)曝光能量:PSR 4000 Z26 10~14格LP 2G G75L 75D 9~12格PSR 2200NC TT19 12~16格CIBA 1070 PSR 3241 8~12格缺陷控制:曝光偏位: 1、必须用10倍镜拍板,针对有BGA位板每个BGA都必须用10倍镜检查。
2、针对易偏位的一面朝光台玻璃面。
3、菲林变形时须重做菲林。
4、严控温湿度,温:20±3℃湿度:55±10%5、拍同种型号板4hr更换粘胶纸1次。
6、双手小心操作避免移动菲林。
曝光不良:1、必须做足真空达到60cmHG后擦气3次才曝光。
2、菲林光密度不合格。
3、清洁米垃菲林不足,每曝1架板(26PNL)对米垃清洁1次,菲林每使用5~10PNL须用酒精和菲林水清洁1次。
4、曝光后板未停放≥ 15min以上就显影。
对反菲林:1、C/S、S/S面菲林相似未做红胶纸对板边排孔标识2、未对菲林标靶3、漏板中单元对位菲林擦花:1、未双手拿菲林造成菲林打折2、曝光拍板员未定时修剪指甲,有戴手饰硬物擦花菲林操作时板在菲林上拖移未双手持板3、黑菲林擦化未检查合格就投入生产E、显影:流程:上板 NaCO3 1±0.2%药液冲洗2级~3级水洗 2~3级吸水辘风干烘干参数:温度 30±2℃药液浓度 1±0.2%压力 2.5~30 bar (一般)速度 (因机而异)缺陷控制:一、S/M冲不净:a、丝印后停放时间b、预焗炉时间长温度偏高,预焗炉抽风不良c、预焗后停放时间过长d、曝光能量太高e、菲林遮光率(光密度不合格)f、曝光真空达不到g、冲板速度、药水温度、浓度和药水压力冲板太慢under Cut过大,易引起到HAL后PAD边甩油h、油墨质量差,过期或稀释剂含水高二、S/M冲板过度:a、预焗温度时间不足b、预焗抽风不良c、曝光能量偏低d、冲板速度过慢药水浓度高,温度过高压力过大e、油墨质量差(过期)F、高温终固化参数:150℃X60 min(HAL板)150℃X100 min(沉金板,背板)150℃X30 min (丝印白字板)终固化缺陷控制:一、板黄:a、终焗时间过长,温度过高b、炉内抽风不良,温度分布不均匀二、爆油:a、未低于60℃进炉焗板b、对S/M前塞孔板或客户设计S/M开窗离PAD<4mil的板未分多段焗炉HAL后甩油:铜面氧化(磨板不良)油面太薄(独立线位铜厚)冲板under Cut过大曝光能量太低预焗不足终固化温度时间不足多次返喷浸泡 flux过久油墨本身质量差或过期四、S/M问答题:1、PCB为什么要塞 Via孔?a、防止波锋焊、回流焊时锡从导通孔贯穿流到元件面上引起短路。
b、避免助焊剂残留在导通孔内,吹不干,藏Sn.C、电子厂EMS后电路板在测试机上要求吸真空形成负压才可完成检测调试,客户自动插件用吸盘不漏气。
d. 保护孔内电镀层.2、S/M为什么会产生龟裂?a. 为预焗时板未焗干b. 曝光能量太低而造成,其中我厂用DSR 2200NC油墨及易形成(曝光能量要求高)另外偶尔因ORC机因曝光能量温度超过机内设定值而跳停导致板曝光不充分,显影后即形成.另稀释剂加到油墨中含水太高。
3、S/M表面哑色是怎么回事?a. 板预焗不良(如焗板抽风不良熔剂未完全挥发)b. 曝光能量偏低(它不是太低,主要是感光光亮油有此问题)4、曝油是如何产生?预焗时间不足,其中要求S/M前塞孔板低于60℃进炉,分段预焗,另一个原因,因板设计造成转弯处油太厚高温时造成油墨流平性而爆油上PAD(加大S/M开窗改善)塞孔油距PAD很近4mil~6mil,可以改成削PAD,允许上4mil S/M。
5、S/M气泡及油泡是如何产生?a . 丝印速度太快.b. 停放时间不足c.搅拌后的油墨停放不足要求≥15min以上.d.丝印胶刮硬度太软(60~65度肖氏)e.底铜过厚(≥2 OZ板)采用Line Mask印刷.6、S/M起皱是如何产生?a . 油墨丝印过厚b. 底铜过厚c.预焗不充分d.未低于60℃进炉,高温时进行分段式预烤改善.7、绿油测试项目?(可靠性测试)a . 油厚 0.4~2.0milb. 硬度铅笔硬度>2 H以上c.附着力满足3M胶带的附着力测试要求90~180度甩油测试d.Sec (Surface 10nic Contamination test)e.SIR(surface Insulation resistance test )f.耐溶剂,异丙醇1小时丙酮室温g.耐化学药品性10%H2SO4 室温 10%NaOHh.热冲击。