航空器无损检测 目视检测
常用无损检测方法简介

以进行磁粉检测。பைடு நூலகம்磁法几乎不受空间位置的限 制,效率高,重复性好,易实现自动化控制,其局 限性在于只适合于湿法磁粉检测,不能多向磁化, 只能检测表面缺陷,对于近表面缺陷的检测灵敏度 很低。
磁粉检测的灵敏度与磁化方向有较大关系,如 当磁力线方向与缺陷的走向平行时,相当于该缺陷 具有极大的宽深比而不易被检出,所以使用磁粉检 测时,需要对工件至少在两个垂直的方向进行磁化 检测,以免造成漏检。
关键词:无损检测;应用范围;局限性
无损检测因其不影响产品本身而被广泛应用于 各类产品的检测。常用的无损检测方法有:目视检 测(VT)、渗透检测(PT)、磁粉检测(MT)、 射线检测(RT)及超声检测(UT),其中VT、 PT、MT用于检测产品的表面缺陷,而RT和UT用 于检测产品的内部缺陷。
1. 目视检测(VT) 目视检测主要用于检测工件外形或表面状态 是否符合要求,如外形尺寸、配合面状态等。 EN13018中将目视检测分为直接目视和间接目视两 种,直接目视指被检测区域到眼睛之间没有发生 光线的间断,不借助任何工具的检测以及借助放大 镜、内窥镜、光导纤维等光线传导介质的检测方法 均属于直接目视。而间接目视则指在检测过程中被 检测区与眼睛之间光线不连续的检测方法,如使用 拍照或摄像方式记录被检测区状态后,再通过眼睛 观看照片或视频来判定被检测区的方法属于不连续 检测。 目视检测最大的优点是成本低,可用于各种各 样产品的检测。因此广泛用于产品的初步质量判定
渗透检测
表面开口缺陷
灵敏度高,不受空间限 不能用于表面疏松材质的检验,效率低,污染
图2
冷加工
335 2016年 增刊1
2016 第二届轨道交通先进金属加工及检测技术交流会
降低检测灵敏度。 施加渗透剂的过程中需保持工件表面湿润,使
无损检测技术在航空发动机上的应用
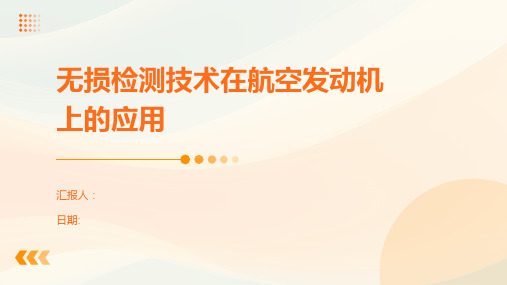
无损检测技术具有非破坏性、全面性、实时性等优点,能够有效地检测出材料内部的缺陷、损伤等不连续性,为 产品质量控制、运行安全性评估提供重要的依据。
无损检测技术的发展历程
初创阶段
20世纪初,无损检测技术开始起步,主要采用简单的敲击、目视 等方法进行检测。
初步发展阶段
20世纪中叶,随着科技的发展,无损检测技术开始得到初步发展 ,超声、射线等无损检测技术开始应用于实际生产中。
长寿命和可靠性
航空发动机需要保证长寿命和可靠性,这就要求 在其整个生命周期内进行有效的无损检测。
航空发动机的无损检测要求
准确性和可靠性
无损检测结果必须准确可靠,不能误报或漏报 缺陷。
实时性和在线性
无损检测过程必须能够在发动机运行时进行实 时或在线检测。
检测方法的多样性
针对航空发动机的不同部位和不同材料,需要采用多种无损检测方法。
03
无损检测技术在航空发动机上 的应用实例
超声检测在航空发动机上的应用
总结词
通过高频声波在材料内部传播,检测异常和缺陷。
详细描述
超声检测技术利用高频声波在材料内部传播的特性,通过接收和分析反射回来的 声波信号,判断材料内部是否存在异常或缺陷。在航空发动机领域,超声检测主 要用于检测发动机叶片、涡轮盘等关键部件的裂纹、气孔等缺陷。
高精度检测
无损检测技术将进一步提高检测精度,能够更加准确地发现发动机 内部的微小缺陷和损伤,提高航空器的安全性。
多技术融合
将多种无损检测技术进行融合,形成综合检测系统,能够更加全面地 检测航空发动机的性能和状态。
THANKS
谢谢您的观看
总结词
利用电磁感应原理,检测导电材料中的 缺陷。
VS
航空器损伤检查方法

对于非金属构件,例如塑料、玻璃纤维复合材料 等构件的损伤,涡流检测法是不适用的。 对于钢构件一般不采用涡流检测法探伤。 涡流检测法不能检测出平行于探测面的裂纹。此 外,它存在容易使人误解的边界效应,当板材太 薄(厚度小于1.5mm)时,板的边缘或紧固件 孔边的边界效应较大,会给检测带来一定的困难。
局部密封试验
对气密舱仅进行了小范围的修理,则可进行局部密封试 验,检查修理部位的密封性。为了确定气密舱的漏气源, 通常有三种试验方法: (一)抽真空法 在可疑的试验缝处涂肥皂水,罩上透明的罩,抽真空并 进行观察,冒肥皂泡处即为漏气部位。 (二)压力法 向气密舱内灌充空气,在舱外试验处涂肥皂水并进行观 察。冒肥皂泡处即为漏气部位。这种方法一般是与采用 压力降法做整机气密舱地面密封试验同时进行。
(4)一般情况下,钉头倾斜或铆钉松动将成群 地出现,并且钉头多半向同一方向倾斜。如果铆 钉头出现倾斜,但不成群地出现,并且不是向同 一方向倾斜,这种铆钉头倾斜可能是由于铆接质 量不高引起的。 (5)通常情况下,应该用大一号(直径加大 1/32in)的铆钉替换这些铆钉。同样,如果铆钉 孔不圆,扩孔后也用大一号的铆钉来更换。
借助于强光手电筒目视检查表面裂纹,方法如图 所示,检验人员应将手电筒朝向自己,并将手电 筒保持与表面呈5~450角。绝不要使手电筒的反 射光束直接射到眼睛,应使眼睛保持在反射光束 之上。
孔探仪是具有多种用途的光学检测工具,可用于 各种各样视力极限所不能看到部位的检查。它是 目视检查的重要工具,在航空维修中已得到广泛 应用。 例如,通过发动机检查孔采用孔探仪检查燃烧室 的裂纹、烧蚀,叶片的烧伤、变形、打伤以及采 用孔探仪检查起落架作动筒壁的裂纹和腐蚀等损 伤。
(5)存在碎屑或污染物处,可能会产生腐蚀来自第2节 结构密封与试验
民航无损检测标准简介

民航无损检测标准简介民航NDT标准是为了满足国内外民航规章和管理要求制订的。
这些要求主要包含在CCAR/FAR121、135、145和43部。
为了落实这些规章,又颁发了很多规范和咨询通告,主要有:●ATA-2200的105规范《NDT方法的人员培训和资格鉴定指南》(适用于五种方法和热成像)。
●ATA-2200的107规范《目视检测人员培训和资格鉴定指南》。
●FAA咨询通告AC43-13-1B《飞机检查和修理可接受的方法、技术和规范》,其中第5章为“无损检测”,第2节为目视检查要求,第3节为5种NDT方法要求。
●AC65-31 A《无损检测人员的培训,资格及认证》(4/25/03)。
至2007年底,民航总局共颁布了无损检测方面的民用航空行业标准有:1.MH/T3001-2004 《航空器无损检测人员资格鉴定与认证》由于无损检测工作的正确性和有效性取决于检测人员的技术水平和能力。
因此,有必要制订统一的人员资格鉴定和认证标准,用来评定检测人员是否能胜任其职责,并颁发证书予以证明。
于2004年10月1日实施的MH/T3001-2004 《航空器无损检测人员资格鉴定与认证》,修改采用美国国家宇航标准NAS 410(2003年2月颁发)《无损检测人员资格鉴定与认证》(英文版),以代替MH/T3001-1995《航空器无损检测人员技术资格鉴定规则》。
该标准规定了在民用航空器制造、运行、维修和翻修行业中从事无损检测(NDT)工作的人员资格鉴定与认证的最低要求。
2004 年12月,美国FAA对民航标准MH/T3001-2004《航空器无损检测人员资格鉴定与认证》予以认可。
该标准适用于使用液体渗透检验 ( PT )、磁粉检验 ( MT )、涡流检验 ( ET )、超声检验 ( UT )和射线照相检验 ( RT )的NDT通用方法处理或评价验收材料、产品、零件、组件和分组件的人员;也适用于直接负责NDT技术的人员、NDT技术外部审核人员以及NDT技术培训人员。
无损检测方法目视检测

无损检测方法目视检测目视检测1.1 目视检测概述◼目视检测是以肉眼或与各种光学仪器相结合来对被检工作表面进行直接观察或测量的一种无损检测方法。
目视检测概述◼目视检测是一种表面检测方法,不但能检测工件的几何尺寸、结构完整性、形状缺欠等,而且还能检测工件表面上的缺欠和其他细节。
受表面照度的影响容易出现漏检。
1.2目视检测基础知识1.2.1光学基础◼光源物体对眼睛引起光的感觉◼光的传播光的直线传播、小孔成像◼光通量按照产生的明亮程度估计辐射通量叫光通量,国际单位流明(lm)◼发光强度I=ψ/ωI---发光强度(坎德拉cd)ψ---光通量(流明lm)ω---立体角1.2.1光学基础◼照度物体单位面积上所获得的光通量称为物体表面的光照度,简称照度E=ψ/sE---照度(lx)ψ---光通量(lm)s---面积(m2)◼光的反射和折射◼光的吸收和散射1.2.2视力视力主要指中心视力,中心视力指视网膜黄斑中心凹视觉敏锐度,即对物体的精细分辨力。
决定视力的主要因素是:1、物体的大小2、物体与眼睛的距离◼人眼构造◼眼睛的适应◼人眼分辨率◼人看清楚物体的条件◼光强与颜色的观察及分辨力◼目视人眼的视力检查近视力、远视力、色盲的检查1.3 目视检测设备与仪器◼光源可见光源分自然光源和人工光源◼光源的选择目视检测中,光源是一个很重要的检测器材,合理正确的选用光源是保证目视检测的一个重要因素,主要考虑以下几个方面:光谱能量分布:一般采用类似日光的光源或黄绿色使用寿命:选择寿命长一些的使用条件:使用照度均匀、聚光作用好、防爆、在安全电压以下◼反光镜、放大镜、望远镜目视中最常用的反光镜是平面反光镜放大镜可以看清工件各部分细节◼工业内窥镜◼照度计每年交检一次◼照相机1.3 目视检测设备与仪器◼测量工具包括线性测量设备(直尺、卷尺)、千分尺、游标卡尺、塞尺、间隙测量规、各类焊接检验尺、半径量规、深度量规、螺纹规等千分尺常用于测量外径或内径最小读数可为0.001mm焊接检验尺主要由主尺、高度尺、咬边深度尺和多用尺四部分组成。
【检验】目视检验VT是工业上无损检测的方法之一是利用眼睛的视
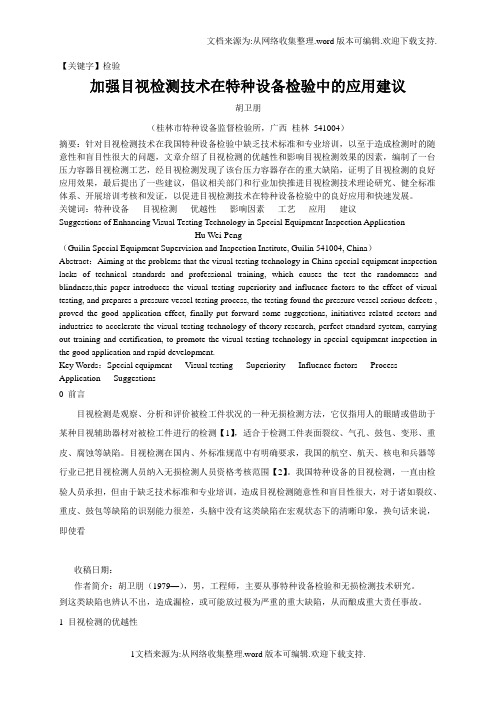
【关键字】检验加强目视检测技术在特种设备检验中的应用建议胡卫朋(桂林市特种设备监督检验所,广西桂林541004)摘要:针对目视检测技术在我国特种设备检验中缺乏技术标准和专业培训,以至于造成检测时的随意性和盲目性很大的问题,文章介绍了目视检测的优越性和影响目视检测效果的因素,编制了一台压力容器目视检测工艺,经目视检测发现了该台压力容器存在的重大缺陷,证明了目视检测的良好应用效果,最后提出了一些建议,倡议相关部门和行业加快推进目视检测技术理论研究、健全标准体系、开展培训考核和发证,以促进目视检测技术在特种设备检验中的良好应用和快速发展。
关键词:特种设备目视检测优越性影响因素工艺应用建议Suggestions of Enhancing Visual Testing Technology in Special Equipment Inspection ApplicationHu Wei-Peng(Guilin Special Equipment Supervision and Inspection Institute, Guilin 541004, China)Abstract:Aiming at the problems that the visual testing technology in China special equipment inspection lacks of technical standards and professional training, which causes the test the randomness and blindness,this paper introduces the visual testing superiority and influence factors to the effect of visual testing, and prepares a pressure vessel testing process, the testing found the pressure vessel serious defects , proved the good application effect, finally put forward some suggestions, initiatives related sectors and industries to accelerate the visual testing technology of theory research, perfect standard system, carrying out training and certification, to promote the visual testing technology in special equipment inspection in the good application and rapid development.Key Words:Special equipment Visual testing Superiority Influence factors Process Application Suggestions0 前言目视检测是观察、分析和评价被检工件状况的一种无损检测方法,它仅指用人的眼睛或借助于某种目视辅助器材对被检工件进行的检测【1】,适合于检测工件表面裂纹、气孔、鼓包、变形、重皮、腐蚀等缺陷。
无损检测方法
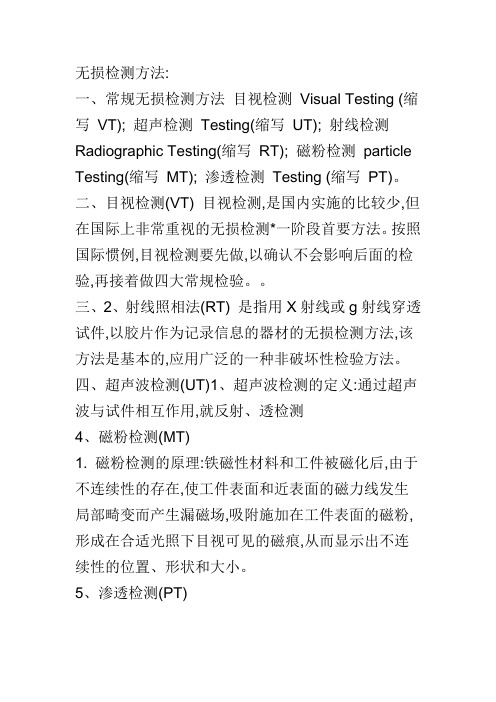
无损检测方法:一、常规无损检测方法目视检测Visual Testing (缩写VT); 超声检测Testing(缩写UT); 射线检测Radiographic Testing(缩写RT); 磁粉检测particle Testing(缩写MT); 渗透检测Testing (缩写PT)。
二、目视检测(VT) 目视检测,是国内实施的比较少,但在国际上非常重视的无损检测*一阶段首要方法。
按照国际惯例,目视检测要先做,以确认不会影响后面的检验,再接着做四大常规检验。
三、2、射线照相法(RT) 是指用X射线或g射线穿透试件,以胶片作为记录信息的器材的无损检测方法,该方法是基本的,应用广泛的一种非破坏性检验方法。
四、超声波检测(UT)1、超声波检测的定义:通过超声波与试件相互作用,就反射、透检测4、磁粉检测(MT)1. 磁粉检测的原理:铁磁性材料和工件被磁化后,由于不连续性的存在,使工件表面和近表面的磁力线发生局部畸变而产生漏磁场,吸附施加在工件表面的磁粉,形成在合适光照下目视可见的磁痕,从而显示出不连续性的位置、形状和大小。
5、渗透检测(PT)1.液体渗透检测的基本原理:零件表面被施涂含有荧光染料或着色染料的渗透剂后,在毛细管作用下,经过一段时间,渗透液可以渗透进表面开口缺陷中;经去除零件表面多余的渗透液后,再在零件表面施涂显像剂.无损检测检测产品:压力管道:工业压力管道、油气长输管道、工业金属热力管道、工业金属燃气管道压力容器(含气瓶):电力工业锅炉压力容器、固定式压力容器、移动式压力容器钢结构工程:建筑工程用钢结构、路桥钢结构、水利工程钢结构、电力工程钢结构锅炉:蒸汽锅炉、热水锅炉、有机热载体锅炉起重机械:桥式起重机、门式起重机、塔式起重机、流动式起重机、铁路起重机、门座起重机、桅杆起重机、悬臂式起重机、缆索起重机、轻小型起重机客运索道、大型游乐设施船舶及船用产品:动力装置、舱室设备、甲板机械海上设施水面以上钢结构铸件、钢锻件、紧固件螺栓、螺钉、螺柱和螺母广告牌检测:墙体广告、落地式广告牌、楼顶广告牌GB/T 26951-2011 焊缝无损检测磁粉检测GB/T 28705-2012 无损检测脉冲涡流检测方法GB/T 26646-2011 无损检测小型部件声发射检测方法GB/T 26595-2011 无损检测仪器周向X射线管技术条件GB/T 28704-2012 无损检测磁致伸缩超声导波检测方法GB/T 26952-2011 焊缝无损检测焊缝磁粉检测验收等级GB/T 26953-2011 焊缝无损检测焊缝渗透检测验收等级。
无损检测方法金属产品及零部件的目视检测

无损检测方法金属产品及零部件的目视检测目视检测作为一种非常简单和直观的无损检测方法,广泛应用于金属产品和零部件的质量控制领域。
它可以帮助检测人员快速检测出可能存在的缺陷和问题,从而确保产品的质量和安全。
本文将探讨目视检测方法及其在金属产品和零部件领域的应用。
一、目视检测的原理和方法目视检测是基于人眼对物体外观的观察和辨识能力进行的一种无损检测方法。
其原理是通过直接观察金属产品和零部件的外观特征,来判断是否存在缺陷或问题。
目视检测方法主要包括以下几个步骤:1. 准备工作:确保检测环境清洁、明亮,以保证检测人员能够清楚地观察产品和部件的外观。
2. 观察:检测人员通过肉眼观察金属产品和零部件的外观特征,包括表面的颜色、纹理、形状等。
3. 辨识:根据观察到的外观特征,检测人员判断是否存在缺陷或问题。
常见的缺陷包括表面裂纹、变形、凹陷等。
4. 记录和报告:将观察到的缺陷和问题记录下来,并及时向相关人员汇报。
二、目视检测在金属产品和零部件领域的应用目视检测方法在金属产品和零部件的生产和质量控制过程中起着重要的作用。
它可以对产品进行快速的初步检测,帮助排除有明显缺陷的产品,从而节省时间和成本。
1. 表面缺陷检测:目视检测方法可以准确地观察到金属产品和零部件的表面缺陷,如裂纹、划伤等。
通过及时发现和修复这些表面缺陷,可以提高产品的质量和寿命。
2. 尺寸和形状检测:通过目视检测方法,可以直接观察到金属产品和零部件的尺寸和形状是否符合要求。
如产品的直径、长度、宽度等参数是否在允许范围内。
这对于保证产品的装配性能和使用效果至关重要。
3. 表面质量检测:目视检测方法可以帮助检测人员观察到金属产品和零部件的表面是否存在气泡、氧化、粗糙等质量问题。
通过及时发现和处理这些质量问题,可以提高产品的整体品质。
4. 焊接质量检测:目视检测方法在金属产品和零部件的焊接质量检测中也得到了广泛应用。
检测人员可以通过观察焊接接头的外观特征,来评估焊接质量是否合格。
- 1、下载文档前请自行甄别文档内容的完整性,平台不提供额外的编辑、内容补充、找答案等附加服务。
- 2、"仅部分预览"的文档,不可在线预览部分如存在完整性等问题,可反馈申请退款(可完整预览的文档不适用该条件!)。
- 3、如文档侵犯您的权益,请联系客服反馈,我们会尽快为您处理(人工客服工作时间:9:00-18:30)。
题目:航空器无损检测目视检测1 范围本规范规定了民用航空器无损检测中目视检测的分类、技术要求、检测方法和记录以及孔探的要求。
本规范适用于民用航空器及其所用材料和零部件表面不连续性及其他缺陷的目视检测。
2 依据2.2 民用航空行业标准MH/T3019-2009《民用航空器无损检测:目视检测》3 术语和定义MH/T 3001中确立的术语适用于本标准4 分类4.1按照使用工具的不同目视检测可分为:a) 直接目视检测(direct visual testing):检测人员眼睛到被检测物体的光学路径无中断,检测时眼睛与检测面的距离不大于60 cm (25 in),且与检测面的角度不低于30°的目视检测。
它又分为:1) 不使用任何工具,直接通过眼睛进行的目视检测;2) 使用反光镜、放大镜等简单工具进行的目视检测;b) 间接目视检测(remote visual testing):借助刚性内窥镜和柔性内窥镜等专用器具,或使用摄影、视频和遥控技术,实现检测人员眼睛到被检测物体的光学路径中断的目视检测。
4.2根据检查要求可分为:a)—般目视检查(Inspection—General Visual):为查找明显的损伤、故障或缺陷而对内部、外部区域、安装件或组件进行的目视检查。
除有题目:航空器无损检测目视检测特别说明外,这种等级的检查均应在可触及的范围内进行;b)详细检查(Inspection—Detailed/DET):为了检测损伤、故障或不正常的迹象,对一个特定的结构区域、系统、安装件或组件进行仔细的检查。
检查时需有良好的光线照明,必要时需有直接照射的补充光线照明;检查时可借助反光镜、放大镜等辅助工具,必要时还应对检查区域进行表面清洁和特殊的接近程序;c)特殊详细检查(Inspection—Special Detailed/SDI )为了检测损伤、故障或不正常的迹象而对一个特定的项目、安装件和组件进行详细的检查。
这种检查可能需要专门的无损检测(NDT) 技术和设备,必要时还应进行复杂的清洁、特殊的接近或者拆卸、分解。
5 技术要求5.1人员资格按本标准实施间接目视检测的人员应按MH/T 3001的规定进行资格鉴定和认证,同时应按合同与采购单的规定进行培训。
各级人员只应从事与本人技术资格等级相应的技术工作。
5.2视力检查目视检测申请人应保证至少单眼视力(矫正视力或裸眼视力)达到GB 1153中远视力表等级1.0。
其他视力检查要求见MH/T30015.3施工指南施工指南应由航空器及部附件制造厂家推荐或本专业3级人员批准或审核。
目视检测人员应按相应的施工指南进行检测。
施工指南应至少包括:a) 标题、编号和日期;b) 适用的技术或参考文件c) 受检零件的名称、件号、序号;d) 检测的部位、区域和可能的损伤(包括示意图、草图或照片)题目:航空器无损检测目视检测e) 检测前的准备要求;f) 检测中使用的目视检测辅助工具及要求;g) 检测后的记录要求和损伤的标记方式;h) 安全提示。
5.4环境条件5.4.1目视检测应在均勻柔和的光线条件下进行,不应在强烈的直射光线下进行。
5.4.2目视检测的光照度应不小于160 lx,局部目视检测时光照度应不小于500 lx,必要时应使用辅助照明。
5.4.3间接目视检测的环境和工作条件应满足检测设备的使用要求5.5工具与设备5.5.1直接目视检测工具5.5.1.1 手电筒5.5.1.1.1所用手电筒的光朿扩散角和亮度应满足工作要求。
5.5.1.1.2手电筒可使用白炽灯、氪灯、卤素灯、氙灯等类型的灯泡。
5.5.1.1.3在危险的工作环境中(例如燃油箱内)使用的手电筒应符合安全防护要求。
5.5.1.2反光镜和放大镜5.5.1.2.1当眼睛无法直接观察到被检查结构和零部件的表面时,可使用反光镜。
反光镜镜面应平整光洁,无影像畸变,并可在90°范围内调节,以便改善视角。
5.5.1.2.2目视检测使用的放大镜应符合GB/T 20968的要求。
5.5.2间接目视检测设备内窥镜可以是刚性或柔性的,内窥镜的分辨率、长度、直径、焦距、视向和视角等均应符合施工指南要求。
有测量要求时,宜选择具备测量功能的内窥镜,也可与相邻已知尺寸参照物进行对比。
使用的辅助设备(如照相机,视频摄录装置和遥控爬行器等)题目:航空器无损检测目视检测应满足工作要求6检测方法6.1基本要求目视检测主要用于检测航空器结构、发动机及其零部件以下缺陷和异常:——因过热导致的变色和烧蚀;——表面的翘曲、隆起和凹坑;——金属结构表面裂纹、腐蚀和变形;——管路的破裂、磨损、开裂和凹坑;——线路的磨损;——复合材料分层和保护漆层损伤;——外来异物;——其他异常。
目视检测应根据检测部位的特点,进行系统的检查,防止任何部分被遗漏。
目视检测观察到异常情况后,可通过嗅、听、品味及触摸等方法进行综合判断,必要时应采用其他无损检测方法验证。
6.2手电的使用手电筒的人射光束应朝向观察方向,并与检测表面呈5°〜45°的倾角。
检测时眼睛观察方向应高于手电筒的反射光束,如图1所示。
确定表面裂纹的长度时,手电筒的人射光束应与裂纹长度方向成直角照射。
题目:航空器无损检测目视检测图1手电筒的使用6.3腐蚀的检测6.3.1初检初步检查所有检测区域是否有腐蚀造成的损伤与变形。
检测前应去除检测表面污染物,但不应去除检测零部件和区域的保护漆层。
6.3.2检测使用工具和设备去除漆层,详细检查6.3.1发现的可能有损伤与变形区域表面是否存在腐蚀,必要时可使用其他无损检测方法确认金属材料腐蚀状况。
6.3.3去除腐蚀的确认去除腐蚀之后,应通过目视或其他无损检测方法确认腐蚀处理的效果。
6.4表面裂纹和其他异常的检测6.4.1初检初步检查所有被检测区域是否有外来物、结构裂纹和变形、紧固件丢失、零件牢固性等。
检测前应去除被检测表面的污染物,但不应去除被检测零部件和区域的保护漆层。
检测过程中,可根据需要去除保护漆层。
6.4.2检测按照一般目视检查或详细检查要求进行检测.题目:航空器无损检测目视检测6.4.3损伤确认检测发现裂纹和其他异常后,必要时应使用其他无损检测方法确认。
6.4.4处理结果确认对损伤和异常进行处理后,应通过目视检测和其他无损检测方法确认处理的效果。
7.孔探7.1孔探人员资质要求7.1.1相关专业专科(含专科)以上毕业,试用期满后从事飞机维修工作5年以上,并具有3年(含)航线或者定检实际维护经历。
7.1.2有英语读写能力,能正确理解发动机孔探工作相关英文资料,同时具备一定的电脑操作能力。
(以上两条适用于2012年以后申请的人员)7.1.3持有维修人员执照。
7.1.4按照培训大纲参加孔探人员课程培训。
7.1.5获得相关发动机内窥镜操作培训证书。
7.1.6视力(或矫正视力)超过1.2。
7.1.7身体健康,性格平和,胜任岗位工作需要。
7.2孔探控制要求7.2.1孔探检查须全程视频记录并保存,对发现的缺陷须拍照存档。
完成检查后12小时内,内窥镜检查人员须通过SAP系统填写《发动机孔探检查报告单》;7.2.2同一台发动机需由不同的内窥人员在连续两次内窥检查中交替安排执行检查。
7.2.3发动机孔探检查工作实行复检制度,复检由另一名具备合格资质的内窥人员以查看内窥结果(照片和录像的方式)进行,完成复检后在工卡或《发动机孔探检查报告单》上须盖章确认。
题目:航空器无损检测目视检测7.2.4对于发生了空中停车或影响到发动机性能、飞行操纵的事件(包括发动机喘振、排气温度超温、振动指示异常、包容性/非包容性内部损伤等)的发动机,在确认需进行发动机孔探工作的情况下(尤其是发动机本体发生损伤),孔探检查工作必须由至少两名内窥检查人员来实施并对缺陷、故障予以最终确认。
7.2.5实施内窥镜工作前内窥镜检查人员需调阅前次相同部位的《发动机孔探检查报告单》,在内窥镜工作中应对损伤数据进行比对,如出现差异,则需由另一名内窥镜检查人员进行复查确认。
对监控使用发动机(已发现内部缺陷)的内窥镜检查,必须每次对前后两次内窥镜照片进行对比,并将每次测量数据详细记录在《发动机孔探检查报告单》中,同时描述每一个缺陷的发展情况。
7.2.6对于检查发现有缺陷,并且需要向OEM咨询后续使用、监控方案的不正常情况,孔探人员应该在完成孔探工作之后的2小时内上传孔探报告,并将情况通过邮件通报维管部MCC和工程技术部动力装置部。
对于按CDR/TV等放行的发动机,孔探检查一旦发现缺陷扩展并超出放行标准的,必须立即报告维管部MCC和工程技术部动力装置部,在重新获得OEM的批准并完成相应审批程序后才能放行。
7.3孔探检查报告单的填写要求7.3.1内窥镜检查人员必须认真填写下列内容;发动机序号、飞机号/位置、发动机型号、孔探原因和内容、定检工卡号/技术指令号、孔探发现的故障/缺陷记录、孔探结论和标准、检查者签名(或盖章)、检查日期、使用时间/循环(TSN,CSN)。
7.3.2孔探原因必须写明孔探是定期孔探还是非例行孔探。
定期孔探需写明定检级别,非例行孔探必须写明非例行孔探原因。
7.3.3孔探检查发现的故障/缺陷记录栏目必须写明故障/缺陷的部位,缺陷的形式(弯曲,烧伤,裂纹,卷曲等);缺陷的数据尺寸必须用详细的附图标明;重复检查的项目要说明故障/缺陷的发展情况。
题目:航空器无损检测目视检测7.3.4结论和标准栏必须写明故障/缺陷是否在标准范围内,并指明所依据AMM/EO/TO/工卡标准,并写明具体的任务号、段落号。
7.3.5发动机使用小时和循环来源于飞机技术记录本。
8.记录应以文本、照片和录像等形式对检测发现的缺陷与异常进行记录。
检测记录应具有可追溯性。
书面记录至少应包括:a)检测零部件名称、件号和序号;b)检测报告编号;c)检测部位;d)使用的检测设备;e)使用的施工指南、标准或工作单;f)缺陷的描述和评价(附必要的照片和视频图像);g)检测人员印章、电子编码或签字,检测日期。