新型切削刀具的发展及应用
刀具材料论文

金属切削刀具的发展历史与现状前言刀具是机械制造中用于切削加工的工具,又称切削工具。
广义的切削工具既包括刀具,还包括磨具。
刀具技术的进步,体现在刀具材料、刀具结构、刀具几何形状和刀具系统四个方面,刀具材料新产品更是琳琅满目。
当代正在应用的刀具材料有高速钢、硬质合金、陶瓷、立方氮化硼和金刚石。
其中,高速钢和硬质合金是用得最多的两种刀具材料,分别约占刀具总量的30%~40%和50%~60%。
本文将介绍刀具的发展历程,发展现状,并对未来刀具的发展法相作出分析。
刀具的发展历史刀具的发展在人类进步的历史上占有重要的地位。
中国早在公元前28~前20世纪,就已出现黄铜锥和紫铜的锥、钻、刀等铜质刀具。
战国后期(公元前三世纪),由于掌握了渗碳技术,制成了铜质刀具。
当时的钻头和锯,与现代的扁钻和锯已有些相似之处。
然而,刀具的快速发展是在18世纪后期,伴随蒸汽机等机器的发展而来的。
1783年,法国的勒内首先制出铣刀。
1792年,英国的莫兹利制出丝锥和板牙。
有关麻花钻的发明最早的文献记载是在1822年,但直到1864年才作为商品生产。
那时的刀具是用整体高碳工具钢制造的,许用的切削速度约为5米/分。
1868年,英国的穆舍特制成含钨的合金工具钢。
1898年,美国的泰勒和.怀特发明高速钢。
1923年,德国的施勒特尔发明硬质合金。
在采用合金工具钢时,刀具的切削速度提高到约8米/分,采用高速钢时,又提高两倍以上,到采用硬质合金时,又比用高速钢提高两倍以上,切削加工出的工件表面质量和尺寸精度也大大提高。
由于高速钢和硬质合金的价格比较昂贵,刀具出现焊接和机械夹固式结构。
1949~1950年间,美国开始在车刀上采用可转位刀片,不久即应用在铣刀和其他刀具上。
1938年,德国德古萨公司取得关于陶瓷刀具的专利。
1972年,美国通用电气公司生产了聚晶人造金刚石和聚晶立方氮化硼刀片。
这些非金属刀具材料可使刀具以更高的速度切削。
1969年,瑞典山特维克钢厂取得用化学气相沉积法,生产碳化钛涂层硬质合金刀片的专利。
国内外刀具材料发展现状

国内外刀具材料发展现状随着现代制造业的不断发展,刀具作为重要的加工工具,在加工领域扮演着重要的角色。
刀具材料的选择直接影响到刀具的使用寿命、加工质量和效率。
因此,刀具材料的发展一直备受关注。
本文将从国内外的角度出发,探讨刀具材料的发展现状。
国内刀具材料的发展目前正处于快速发展阶段。
传统的刀具材料如碳钢、高速钢等仍然占据一定的市场份额,但其在高端领域的应用受到了一定的限制。
近年来,随着精密加工和高效加工需求的增加,新型刀具材料的需求也随之增长。
硬质合金作为一种重要的刀具材料,在国内得到了广泛应用。
硬质合金具有高硬度、耐磨性好的特点,适用于高速切削和重负荷切削。
国内硬质合金刀具材料的生产技术和品质不断提高,已经能够满足大部分加工需求。
除了硬质合金,陶瓷刀具材料也在国内得到了一定的应用。
陶瓷刀具材料具有高硬度、高耐磨性和高热稳定性的特点,适用于高温切削和高速切削。
国内陶瓷刀具材料的研发和生产技术已经取得了一定的突破,但与国外相比,仍然存在一定的差距。
在国外,刀具材料的发展相对较早,并且取得了较大的进展。
高速钢、硬质合金和陶瓷等刀具材料在国外得到了广泛应用。
同时,国外也在不断研发新的刀具材料,如超硬刀具材料、纳米材料等。
这些新材料具有更高的硬度、更好的耐磨性和更高的切削速度,能够满足更为复杂的加工需求。
国外的刀具材料研发也注重环保和可持续发展。
例如,一些国外公司开始研发可回收利用的刀具材料,以减少资源的浪费和环境的污染。
这种趋势在国内刀具材料的研发中也逐渐得到重视。
总的来说,国内外刀具材料的发展现状存在一定的差距。
国内刀具材料在硬质合金和陶瓷等领域取得了一定的进展,但与国外相比仍有较大差距。
国外刀具材料在研发和应用方面相对领先,不断推出新的刀具材料以满足不同的加工需求。
在未来,国内应加大对刀具材料的研发投入,提高刀具材料的品质和性能,以满足国内制造业的需求。
国内外刀具材料的发展现状存在一定的差距,国内刀具材料的发展相对滞后。
先进制造技术在车工中的研究进展和应用简介
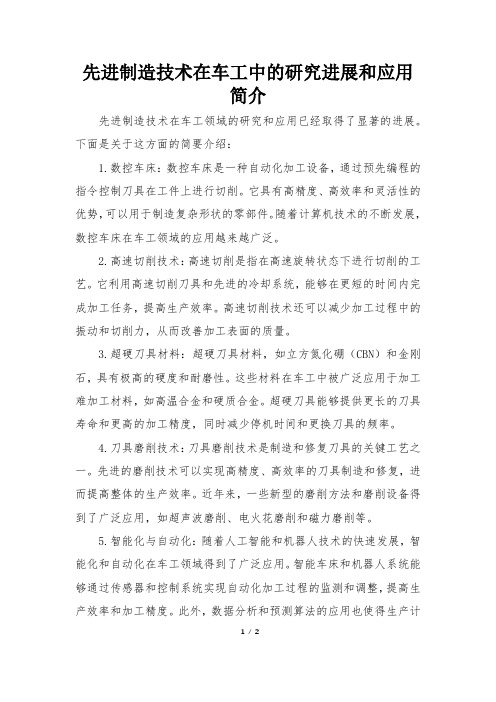
先进制造技术在车工中的研究进展和应用简介先进制造技术在车工领域的研究和应用已经取得了显著的进展。
下面是关于这方面的简要介绍:1.数控车床:数控车床是一种自动化加工设备,通过预先编程的指令控制刀具在工件上进行切削。
它具有高精度、高效率和灵活性的优势,可以用于制造复杂形状的零部件。
随着计算机技术的不断发展,数控车床在车工领域的应用越来越广泛。
2.高速切削技术:高速切削是指在高速旋转状态下进行切削的工艺。
它利用高速切削刀具和先进的冷却系统,能够在更短的时间内完成加工任务,提高生产效率。
高速切削技术还可以减少加工过程中的振动和切削力,从而改善加工表面的质量。
3.超硬刀具材料:超硬刀具材料,如立方氮化硼(CBN)和金刚石,具有极高的硬度和耐磨性。
这些材料在车工中被广泛应用于加工难加工材料,如高温合金和硬质合金。
超硬刀具能够提供更长的刀具寿命和更高的加工精度,同时减少停机时间和更换刀具的频率。
4.刀具磨削技术:刀具磨削技术是制造和修复刀具的关键工艺之一。
先进的磨削技术可以实现高精度、高效率的刀具制造和修复,进而提高整体的生产效率。
近年来,一些新型的磨削方法和磨削设备得到了广泛应用,如超声波磨削、电火花磨削和磁力磨削等。
5.智能化与自动化:随着人工智能和机器人技术的快速发展,智能化和自动化在车工领域得到了广泛应用。
智能车床和机器人系统能够通过传感器和控制系统实现自动化加工过程的监测和调整,提高生产效率和加工精度。
此外,数据分析和预测算法的应用也使得生产计1/ 2划和资源调度更加智能化。
综上所述,先进制造技术在车工领域的研究和应用涉及数控车床、高速切削技术、超硬刀具材料、刀具磨削技术以及智能化与自动化等方面。
这些技术的应用不仅提高了加工效率和精度,还为制造业带来了更大的发展潜力。
2/ 2。
6种数控刀具的种类、性能、特点、应用专业知识

6种数控刀具的种类、性能、特点、应用专业知识先进的加工设备与高性能的数控刀具相配合,才能充分发挥其应有的效能,取得良好的经济效益。
随着刀具材料迅速发展,各种新型刀具材料,其物理、力学性能和切削加工性能都有了很大的提高,应用范围也不断扩大。
一.刀具材料应具备基本性能刀具材料的选择对刀具寿命、加工效率、加工质量和加工成本等的影响很大。
刀具切削时要承受高压、高温、摩擦、冲击和振动等作用。
因此,刀具材料应具备如下一些基本性能:(1)硬度和耐磨性。
刀具材料的硬度必须高于工件材料的硬度,一般要求在60HRC以上。
刀具材料的硬度越高,耐磨性就越好。
(2)强度和韧性。
刀具材料应具备较高的强度和韧性,以便承受切削力、冲击和振动,防止刀具脆性断裂和崩刃。
(3)耐热性。
刀具材料的耐热性要好,能承受高的切削温度,具备良好的抗氧化能力。
(4)工艺性能和经济性。
刀具材料应具备好的锻造性能、热处理性能、焊接性能;磨削加工性能等,而且要追求高的性能价格比。
二.刀具材料的种类、性能、特点、应用1.金刚石刀具材料的种类、性能和特点及刀具应用金刚石是碳的同素异构体,它是自然界已经发现的最硬的一种材料。
金刚石刀具具有高硬度、高耐磨性和高导热性能,在有色金属和非金属材料加工中得到广泛的应用。
尤其在铝和硅铝合金高速切削加工中,金刚石刀具是难以替代的主要切削刀具品种。
可实现高效率、高稳定性、长寿命加工的金刚石刀具是现代数控加工中不可缺少的重要工具。
⑴金刚石刀具的种类①天然金刚石刀具:天然金刚石作为切削刀具已有上百年的历史了,天然单晶金刚石刀具经过精细研磨,刃口能磨得极其锋利,刃口半径可达0.002μm,能实现超薄切削,可以加工出极高的工件精度和极低的表面粗糙度,是公认的、理想的和不能代替的超精密加工刀具。
②PCD金刚石刀具:天然金刚石价格昂贵,金刚石广泛应用于切削加工的还是聚晶金刚石(PCD),自20世纪70年代初,采用高温高压合成技术制备的聚晶金刚石(Polycrystauine diamond,简称PCD刀片研制成功以后,在很多场合下天然金刚石刀具已经被人造聚晶金刚石所代替。
CBN适用情况

目前中国的汽车制造技术正向着高速、智能、复合、环保方面发展,这对切削刀具的要求更高,新型硬质合金刀具已经被广泛使用,而CBN(立方晶氮化硼)、PCD(聚晶金刚石)刀具和陶瓷刀具等代表当今技术发展水平的超硬刀具在汽车制造业中应用也越来越多。
为达到高效加工的目的,在汽车制造业中还大量使用组合式刀具和复合刀具。
同时现代汽车制造业还要求刀具供应商不仅能提供切削加工整体解决方案,并能提供及时有效的现场技术支持,形成与汽车制造企业的一种合作伙伴关系,以达到双赢目的。
山特维克可乐满、肯纳、伊斯卡、万耐特、山高、日立、住友电工、黛杰、三菱、株钻、森拉天时等着名刀具制造商在这方面都有很多成功案例。
Valenite可变直径气缸孔镗刀随着柔性技术在汽车工业加工中的成熟应用,以及产品的不断变型,用户对非标专用刀具的柔性也提出了更高的要求。
针对缸体中气缸孔的加工,Valenite设计了直径能够在一定范围内可变的气缸孔复合镗刀。
以共线加工三种不同直径缸孔的缸体为例,缸孔的直径分别为Φ82.54mm、Φ87.04mm、Φ91.1mm,最大与最小孔径相差8.56mm,机床型式为专用机床。
Valenite设计了一套变直径的复合镗刀、测量系统以及控制系统。
其中,镗杆共有三个小刀夹,两个用于半精镗(推镗),一个用于精镗(拉镗)。
镗杆内部的拉杆以及小刀夹采用特殊结构。
工作原理(见图1):初始在767处理器内设置三个不同的加工直径,根据不同的产品系列,选择不同的加工直径,如由Φ82.54mm切换到Φ87.04mm,处理器发出信号给镗杆后端的伺服电机,电机通过中间的转换装置把回转运动转换为液压缸的直线运动,从而驱动拉杆,将小刀夹的尺寸调整到Φ87.04mm后,小刀夹自锁。
然后,对加工过的缸孔进行测量,测量数据转换为信号传输到处理器中进行比较,如数据有偏差,将偏差补偿量转换为补偿信号传输到伺服电机,由电机对拉杆进行微调,使小刀夹产生弹性变形,从而实现尺寸自动补偿。
TiAIN涂层刀具的发展与应用
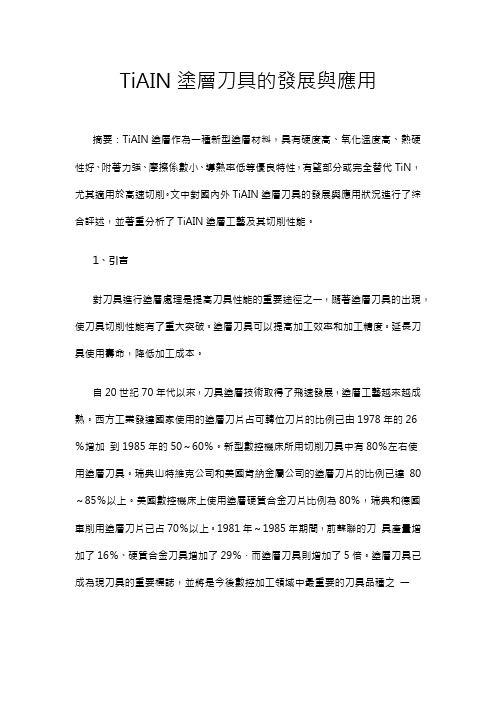
TiAIN塗層刀具的發展與應用摘要:TiAIN塗層作為一種新型塗層材料,具有硬度高、氧化溫度高、熱硬性好、附著力強、摩擦係數小、導熱率低等優良特性,有望部分或完全替代TiN,尤其適用於高速切削。
文中對國內外TiAIN塗層刀具的發展與應用狀況進行了綜合評述,並著重分析了TiAIN塗層工藝及其切削性能。
1、引言對刀具進行塗層處理是提高刀具性能的重要途徑之一,隨著塗層刀具的出現,使刀具切削性能有了重大突破。
塗層刀具可以提高加工效率和加工精度。
延長刀具使用壽命,降低加工成本。
自20世紀70年代以來,刀具塗層技術取得了飛速發展,塗層工藝越來越成熟。
西方工業發達國家使用的塗層刀片占可轉位刀片的比例已由1978年的26%增加到1985年的50~60%。
新型數控機床所用切削刀具中有80%左右使用塗層刀具。
瑞典山特維克公司和美國肯納金屬公司的塗層刀片的比例已達80~85%以上。
美國數控機床上使用塗層硬質合金刀片比例為80%,瑞典和德國車削用塗層刀片已占70%以上。
1981年~1985年期間,前蘇聯的刀具產量增加了16%、硬質合金刀具增加了29%.而塗層刀具則增加了5倍。
塗層刀具已成為現刀具的重要標誌,並將是今後數控加工領域中最重要的刀具品種之一TiAIN塗層作為一種新型塗層材料,具有硬度高、氧化溫度高、熱硬性好、附著力強、摩擦係數小、導熱率低等優良特性,尤其適用於高速切削高合金鋼、不銹鋼、鈦合金、鎳合金等材料。
在要求高耐磨性的場合下,鑒於TiN塗層在高溫性能方面所表現出的不足,TiAIN有望部分或完全替代TiN,因此,TiAIN塗層刀具具有極其廣闊的應用前景。
自1985年Knotek等首次發表了關於TiAIN塗層的研究成果後,人們便對其優異的抗高溫氧化能力和良好的使用性能表示了極大的關注,已經用多種PVD方法成功製備了TiAlN膜。
由於TiAlN塗層的製備方法不盡相同,已見報道的TiAlN塗層的性能也有差異。
表1是幾種常用塗層的主要性能比較(資料來源於Balzers塗層有限公司。
可在新用途中代替EDM的硬切削工艺

近 日 ,e o实 现 了新 突破 该 公 司开 发 了一种 Sc 能对硬质材 料进行单 点攻 丝 的新工 艺 , 此前这需要 而 用 E M 工艺完 成. 该工 艺可在 几乎所 有外径 位置 和 D 直径 2 5英 寸的内径 中生成螺纹 通过 在淬硬钢制成 . .
的轴 承 套 圈 衬 板 ( 度 为 6 c 硬 5 R )上 采 用 硬 攻 丝 方 法 ,
有复杂外形和几何形状 的部件进行铣削加工大 开方便 钢) ,e o刀具 公司 已觅得通过 采用其经过涂 覆的硬 Sc 之门 , 而这 以前是要通过 电火花加工 ( D E M)完成的。 质合金螺纹铣 刀 , 生成 具有 多种 牙型的优质螺纹 的新
使 D 需 ~15小 时 才 虽然对复杂 的外形 来说 , 电火花是精确 度最高 的一种 方 法 。 例 如 , 用 E M 技 术 时 , 要 1 .
新开发的 P D涂层 采用 T( i V i ) S N等先进材料 , 改
硬 质材 料 的车 间 发现 , 们 现在 能 选择 生 产并 予 以 善 了 P B 他 C N嵌件的性能。而这是在通过使刀 刃在较长 实施 . . 时 间内保持锋利 而实现的。涂层通过 降低摩擦系数而
从 如今 , 切削领域真正令人兴奋 的事情是 硬攻丝 改善耐磨 性 , 而减少切 削刃产生 的热量。 它们可提 硬
需要 3 ~4分 钟 。
而且 , 硬攻丝 不局限于直径较大 的部 件 、对于较 小尺 寸的部件 , e o首先采 用 J F 0 质合金立铣 Sc H 1 硬 8
刀 , 用 圆 弧 插 补 过 程 开 孔。 此 后 , 标 准硬 质 合 金 利 用
螺纹 铣刀生成 1 ~ 4条直径 在 0 1 0英寸 以上 的螺 2 0 .5
探析高速切削加工技术在数控机床中的应用
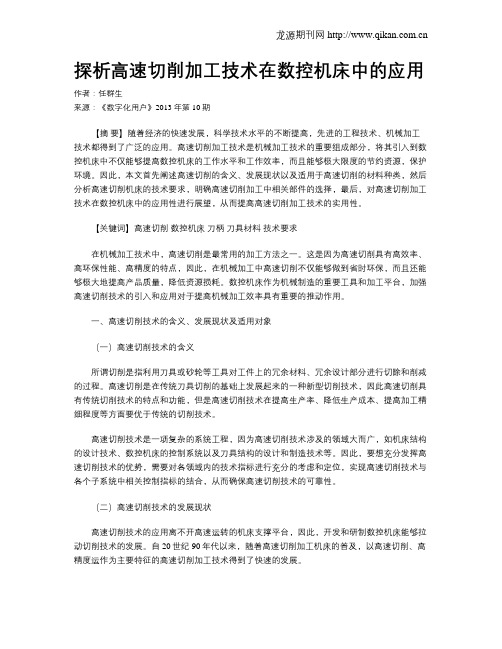
探析高速切削加工技术在数控机床中的应用作者:任群生来源:《数字化用户》2013年第10期【摘要】随着经济的快速发展,科学技术水平的不断提高,先进的工程技术、机械加工技术都得到了广泛的应用。
高速切削加工技术是机械加工技术的重要组成部分,将其引入到数控机床中不仅能够提高数控机床的工作水平和工作效率,而且能够极大限度的节约资源,保护环境。
因此,本文首先阐述高速切削的含义、发展现状以及适用于高速切削的材料种类,然后分析高速切削机床的技术要求,明确高速切削加工中相关部件的选择,最后,对高速切削加工技术在数控机床中的应用性进行展望,从而提高高速切削加工技术的实用性。
【关键词】高速切削数控机床刀柄刀具材料技术要求在机械加工技术中,高速切削是最常用的加工方法之一。
这是因为高速切削具有高效率、高环保性能、高精度的特点,因此,在机械加工中高速切削不仅能够做到省时环保,而且还能够极大地提高产品质量,降低资源损耗。
数控机床作为机械制造的重要工具和加工平台,加强高速切削技术的引入和应用对于提高机械加工效率具有重要的推动作用。
一、高速切削技术的含义、发展现状及适用对象(一)高速切削技术的含义所谓切削是指利用刀具或砂轮等工具对工件上的冗余材料、冗余设计部分进行切除和削减的过程。
高速切削是在传统刀具切削的基础上发展起来的一种新型切削技术,因此高速切削具有传统切削技术的特点和功能,但是高速切削技术在提高生产率、降低生产成本、提高加工精细程度等方面要优于传统的切削技术。
高速切削技术是一项复杂的系统工程,因为高速切削技术涉及的领域大而广,如机床结构的设计技术、数控机床的控制系统以及刀具结构的设计和制造技术等。
因此,要想充分发挥高速切削技术的优势,需要对各领域内的技术指标进行充分的考虑和定位,实现高速切削技术与各个子系统中相关控制指标的结合,从而确保高速切削技术的可靠性。
(二)高速切削技术的发展现状高速切削技术的应用离不开高速运转的机床支撑平台,因此,开发和研制数控机床能够拉动切削技术的发展。
- 1、下载文档前请自行甄别文档内容的完整性,平台不提供额外的编辑、内容补充、找答案等附加服务。
- 2、"仅部分预览"的文档,不可在线预览部分如存在完整性等问题,可反馈申请退款(可完整预览的文档不适用该条件!)。
- 3、如文档侵犯您的权益,请联系客服反馈,我们会尽快为您处理(人工客服工作时间:9:00-18:30)。
新型切削刀具的发展及应用
柯新民081268025
近年来,随着机械工业、汽车工业、航空航天:厂业、电子工业、能源工程和材料科学的进步,机床工业也逐步向着数控化、精密化、集成化、智能化的方向发展,因此对刀具材料的硬度、抗弯强度、冲击性能、粘结剂和组织等性能也提㈩了愈宋愈高的要求。
面对门益增多的难加工材料,多功能复合刀具、智能刀具、高速高效刀具逐渐成为现代制造技术的关键装备,因而成为时代的新宠,尤其在刀具材料与刀具结构方面有了新的发展。
一,新型刀具材料的发展回顾及展望
刀具材料的发展经历了工具钢、高速钢、硬质合金、陶瓷、超硬材料五个阶段。
1.新型高速钢材料(1)粉末冶金高速钢刀具近几年来,高速钢的最大变革就是发展了粉末冶金高速钢。
通过用高压氮气雾化熔融高速钢水得到细小的高速钢粉末,在真空状态下密闭烧结后,纾过高温高压压制成钢胚,然后锻轧成钢材,这样就避免了熔炼高速钢在铸锭时产生粗大炭化物偏析的问题,得到小于0.002mm的极细晶粒。
粉末冶金高速钢具有良好的力学性能。
例如,牌号为CPMTl5的粉末冶金高速钢,它的强度、韧性分别是相同化学成分的熔炼高速钢的2~2.5倍;高温热硬度比熔炼高速钢提高0.5~1HRC,耐磨性提高20%~30%。
因此,粉末冶金高速钢刀具适用于间断切削、强度高而切削刃又必须锋利、高压动载荷下切削的情况,适于制造大尺寸刀具、精密刀具、复杂刀具。
美国的Crucible公司、日本神户制钢所、日立金属公司、日本OSG公司、NACHI 公司等都能提供近20种粉末冶金高速钢,而我国钢厂所能提供的品种则较少,因此粉末冶金高速钢将为我国的金属加工工业带来新的发展机会。
(2)涂层高速钢刀具传统的涂层高速钢刀具是在高速钢刀具表面上采用物理气相技术(PVD)沉积2~5um厚的氮化钛(TIN)薄层,其硬度可达2000HV,并且具有很高的耐磨性。
近几年还研制山了ZrN、HfN、CrN、TiALN、金刚石碳涂层、复合涂层等新技术,使其不仅提高了刀具的耐用度,而且还能加工高硬度合金及高温合金等难加丁材料。
2.新型陶瓷材料(1)氧化铝系列纯氧化铝陶瓷(含乩20399%以上)由于强度低、抗热震性及断裂韧性较差,一般不广泛使用。
通过利用添加剂和品种等力法诱导等轴状AL203晶粒导向生长所获得的AL203陶瓷具有较好的韧性,使其成为近年来国内外研究的热点。
此外,颗粒增强AL203复合材料、晶须增强AL203复合材料、相变增韧AL203复合材料、ALzO~梯度功能材料等刀具比传统材料刀具在高温韧性、高温强度、热冲击性、寿命等方面有显著提高。
(2)氮化硅系列氮化硅足在氧化铝以后出现的一种刀具材料。
它具有比氧化铝更高的强度和断裂韧性,抗弯强度可达900~1000Mpa,可靠性高,不易产生裂纹,具有稳定的使用寿命。
热压自增韧氮化硅(Si3N4)、氧化锆相变氮化硅(如Al—Zr02(Y203)—Sl3N4烧结体)、纳米颗粒增韧氮化硅(如SiCp-Si3N4)、Slalon 等陶瓷材料都是近几年研究的热点。
其中sl3N4具有较高的断裂韧性和强度,是种适合切削冷硬铸铁和淬硬钢的刀具材料,特别适用于连续加工;A1-ZrO2(Y2O3)-Sl3N4氧化锆相变氮化硅陶瓷是以Zro2(Y2O3)—Si3N4为基体,加入2%的AI当Y2O3的含量的含量为2%~3%(摩尔分数)时,烧结而成的增韧陶瓷材料,其抗压强度、硬度及断裂韧性都较高:S1Cp—Sl3N4凡纳米颗粒增韧氮化硅陶瓷是以Sl3N4为基体,Y2O3、La2O3为烧结剂,采用高压方法制备
而成,比氮化硅单相陶瓷具有更好的力学性能;Slalon是氧化铝和氮化硅的固溶体,抗弯强度叫达1050—1450Hpa,硬度达94HRA,断裂韧性是几种陶瓷刀具中最高的,冲击强度、抗热冲击性能、抗氧化能力、抗蠕变能力、塑性变形能力、耐磨性都较si3N4刀具有明显提高,且化学性能稳定,耐热温度较高,适用于高速切削、强力切削、断续切削等。
此外,硼化物基体金属陶瓷(如TiB2-Fe、TiB2-FeMO-Fe—Ni、TiB2—Fe—Cr-NI)等陶瓷材料以及其它陶瓷—金属复合材料在刀具制造上都有一定的应用。
由于脆性大是陶瓷材料的致命弱点,因此如何进一步提高陶瓷刀具的断裂韧性和抗弯强度是目的研究的热点。
3.金刚石和CBN材料金刚石和CBN都是属于超硬刀具材料,从20世纪60年代起有了很大发展。
超硬材料化学成分及其形成硬度的规律与其它刀具材料不同:立方氮化硼(CBN)是非金属硼化物,晶体结构为面心立方;而金刚石则由碳元素转化而成,其晶体结构与CBN相似,它们的硬度远远高于传统刀具材料。
(1)新型全刚石刀具金刚石目前仍是自然界已发现的材料中最硬的材料,其显微硬度高达1000HV。
人造金刚石包括PCD单晶粉、PCD单晶粒、PCD聚晶复合片、人造CVD等,都是以石墨为原料,加入催化剂,经高温高压烧结而成。
金刚石刀具具有极高的硬度和耐磨性,其耐磨性是硬质合金的10~100倍,热膨胀系数为高速钢的1/10,导热系数为硬质合金的5~9倍,对有色金属及非金属材料高速镗削和精车能获得很高的表面加工质量。
近年来,新型金刚石刀具材料相继出现,如美国Kennametal公司采用CVD工艺,通过用等离子体焰矩法开发的KDl405纯金刚石刀且材料,就具有良好的韧性并可显著改善刀具的耐磨性,适用于加工高耐磨的非铁族材料,如中高含硅量的铝合金、各种材料金属基复合材料(MMC)、碳复合材料、增强型塑料、铜合金材料等。
(2)CBN刀具材抖CBN是继人造金刚石之后出现的一种新型刀具材料,近年来正逐渐齐牛产实践中推广采用。
它也是人工合成的一种超硬刀具材料,包括CBN单晶粉、PCBN聚晶片及聚晶复合片。
CBN材料具有高硬度(仅次于金刚石)、高热稳定性,对铁族元素呈惰性,故适合切削各种淬硬钢(包括碳素工具钢、合金工具钢、高速钢、轴承钢、模具钢等)、各种冷硬铸铁和耐磨铸铁、各种铁基、镍基、钴基和其它热喷涂(焊)零件。
此外,氮化碳材料亦是近几年出现的一种新型超硬度刀具材料,其硬度与CBN相近。
二、刀具结构的发展刀具结构是决定切削刀具使用性能的重要因素,只有通过先进的刀具结构才能发挥刀具材料和涂层的优势,因此国内外刀具制造商都十分重视刀具结构的研究和开发。
总的来说,新型刀具结构的发展方向,一是加大刀具的前角以降低切削力,使切削轩快并同时减轻刀具的载荷,提高切削效率;二足通过改变切削图形来降低切削力并加大进给速度:三是通过结构的设计减少铣削巾的震动。
此外,如高山公司的Quattromll平面铣刀也都是通过采用较大的前角以及可靠的装央定位方式以降低切削力和功率消耗;再如Walter公司的Xtra.tec钻头、山特维克公司的CoroDroll880浅孔钻通过多刃切削的互相搭配形成分屑效果,从而使切削轻快减低切削力,提高进给速度:Iscar公司的风火轮铣刀、日立公司的四刃圆角铣刀,包括我国上海工具厂近年来开发的波形刃叶根铣刀等都是通过结构设计上的改进来减小铣削加工中的震动。
总的来说,结构决定刀体和刀片的空间位置安排,既要保证刀具的刚性和容屑空间,义要使尺寸紧凑。
另外,设计与制订“切削图形”的灵活性与多样性、刀具几何角度的合理性与可调性、不同工序刀具的组合性与复合性将是未来刀具结构发展的新方向。