感应耦合式电浆蚀刻原理
ICP刻蚀原理:气体、功率的选择--ICP操作流程

一、电感耦合等离子体(ICP)刻蚀原理 3二、刻蚀的基本要求9 (负载效应、图形的保真度、均匀性、表面形貌、刻蚀的清洁)三、等离子体刻蚀的基本过程11 (物理溅射刻蚀、纯化学刻蚀、离子增强刻蚀、侧壁抑制刻蚀)四、影响刻蚀效果的因素14 掩膜的影响、工艺参数的影响(ICP Power源功率、RF Power偏压功率、工作气压气体成分和流量、温度)五、附加气体的影响16六、多种条件刻蚀技术18 高速率刻蚀、高选择比刻蚀、特定剖面刻蚀一、电感耦合等离子体(ICP)刻蚀原理包括两套通过自动匹配网络控制的13.56MHz射频电源一套连接缠绕在腔室外的螺线圈,使线圈产生感应耦合的电场,在电场作用下,刻蚀气体辉光放电产生高密度等离子体。
功率的大小直接影响等离子体的电离率,从而影响等离子体的密度。
第二套射频电源连接在腔室内下方的电极上,此电极为直径205mm的圆形平台,机械手送来的石英盘和样品放在此台上进行刻蚀。
激光干涉仪端口ICP功率源水冷却的射频线圈静电屏蔽晶片夹/氦气冷却机制平板功率源实验中刻蚀三五族材料使用的是英国Oxford仪器(Oxford instruments plasma technology)公司的plasma180系统中的plasmalab system100型ICP。
可以刻蚀GaN、AlGaN、GaAs、InP、InGaAs、InGaP/AlGaInP 、InGaAs/InGaAsP等多种化合物材料。
苏州纳米所材料ICP功率:0-3000wRF功率:0-1000w压力范围:1-100mT加工范围:6寸工艺气体:Cl2,BCl3,HBr,CH4,He,O2,H2,N2氦气冷却由氦气良好的热传导性,能将芯片上的温度均匀化1torr=1.333mbarGaN刻蚀ProfileICP操作流程装片1.在Pump界面点击左边Pump图标下Stop,切换至Vent,120s后打开Loadlock2.涂抹真空油脂:根据片子尺寸大小,在托盘上涂抹均匀一层油脂3.放片:放片的时候要用镊子轻轻夹住样片,将样片一边贴在油脂上,慢慢地放下另一边,用镊子按住样片一端,在油脂上稍稍一动样片,以便赶走样片与油脂之间的气泡,使得样片与油脂紧密粘在一起。
电浆的基础讲解
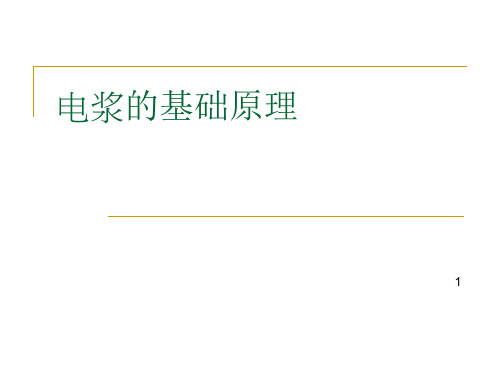
原子核
基態
分解碰撞(Dissociation Collision)
电子和分子碰撞时,如果因撞击而传递到分子的能量会 比分子的键结能量要高戥,那就能打破化学键并且产生 自由基(Free Radicals)
e- + AB → A + B + e AB 是分子,而A和B两者都是由分解碰撞所產生的自由
在抽至高真空的反应室内的两个平行板电极之 间加上电压来產生电浆
电浆的产生
由於这两个平行板 电极就好像电容器 中的电极,所以也称 為电容耦合型 (Capacitively Coupled)电浆源
RF电浆的产生
两电极中通RF高电压,产生交流电场 如RF能量够高,自由电子会被加速 直到自由电子得到足够的能量来和反应室中的
游离率也与压力,电极间的距离,製程气体的种 类以及电浆反应器的设计有关
控制施加的功率→控制电子能量→控制游离率
电浆的产生
直流电浆源[Direct Current (DC) Plasma], 用 于离子佈植机(Ion Implanter)
射頻电浆源[Radio Frequency (RF) Plasma], 用于感应式耦合电浆(ICP)
离子化碰撞(Ionization Collision)
当电子与一个原子或一个分子相碰撞,它会将 部分的能量传递至受到原子核或分子核所束缚 的轨道电子上
如果轨道电子获得的能量而足以脱离核子的束 缚,它就会变成自由电子
e- + A → A+ + 2 e (e-代表电子,A代表中性原子或分子,而A+代表
原子或分子碰撞以产生另一个离子和另一个自 由电子 离子化碰撞是一连串的反应,因此整个反应室 就迅速地充满了等量的电子和离子,也就是充 满了电浆
电容屏ITO、银浆蚀刻设备工作原理

电容屏ITO、银浆蚀刻设备⼯作原理电容屏ITO、银浆蚀刻设备⼯作原理触摸屏的⼴泛应⽤,ITO导电薄膜受到⼈们的重视。
⽽紫外激光的波长短、能量集中、分辨率⾼,因此在去除焊料外壳、在电⼦线路板上钻微孔、在薄膜或薄⽚材料中制作微通道、进⾏精密切割和对移动破碎站接等微加⼯领域具有⼴泛的应⽤,现在红外光纤也在这技术上得到很好的应该。
ITO薄膜激光刻蚀设备正是利⽤紫外激光器的⾼能量特性来对ITO薄膜进⾏冷加⼯处理,在薄膜表⾯制作微细的通道,完成图形的制备。
与传统的湿法光刻技术不同,它不需要事先在薄膜上⽤光刻胶形成掩模,既简化了⼯艺流程也不会造成环境污染。
本系统刻蚀的线宽在⼏⼗微⽶,属于激光微细加⼯技术的范畴。
在加⼯过程中由于激光能量的⾼斯分布特性,在物件划槽截⾯形状为椭圆或类三⾓形,影响了ITO导电薄膜的性能,进⽽制约了液晶显⽰⾏业的发展。
本加⼯设备中⾃⾏研制了⼀套激光微细加⼯的匀光系统,使激光能量分布均匀,呈现类似的平顶分布,很好地解决了上述问题。
与市场上已经成熟的光束整形器件相⽐,匀光系统有相对的优势。
供应:激光蚀刻银浆、光刻银浆、细线印刷银浆、导电碳浆、UV⾼透绝缘油.品牌有:韩国inktec、⽇本太阳油墨、美国ECM~欢迎来电~139******** QQ:598362644E-mail:*************匀光系统介绍这⾥所⽤的激光器提供波长为355 nm的紫外光源,该光源保证单模(TEM00)输出并且截⾯能量呈⾼斯分布;激光束⾸先经过扩束镜准直,使得光束的束腰直径增⼤,发散⾓减⼩。
扩束后的激光束垂直照射到匀光系统的⼈射⾯,经匀光系统分光后,激光束由进⼊前截⾯为圆形的⼀束激光束变为截⾯为半圆形的两束激光,并且这两束激光束平⾏射出;被分光后的两束激光经聚焦镜聚焦后各⾃的光斑相互接近,此时两个光斑的能量发⽣重叠形成⼼得光斑,随着两个光斑之间距离的接近,沿垂直半圆光斑直径的中⼼,叠加后的能量分布近似为平顶,如图1所⽰。
蚀刻工艺原理

蚀刻工艺原理蚀刻工艺是一种常见的微纳加工技术,广泛应用于半导体制造、光学器件制造、生物芯片制备等领域。
蚀刻工艺的原理主要是利用化学溶液或等离子体等介质对材料表面进行物理或化学的腐蚀,从而形成所需的微细结构。
蚀刻工艺的原理可以分为湿法蚀刻和干法蚀刻两种类型。
湿法蚀刻是指利用化学溶液对材料表面进行溶解或氧化的蚀刻工艺。
在湿法蚀刻中,通常会选择一种特定的蚀刻溶液,通过控制溶液的成分、温度、浓度等参数,使得溶液与材料表面发生特定的化学反应,从而实现对材料的蚀刻加工。
湿法蚀刻工艺具有成本低、加工速度快等优点,但也存在溶液处理、废液处理等环境污染问题。
干法蚀刻是指利用等离子体或气相化学反应对材料表面进行蚀刻的工艺。
在干法蚀刻中,通常会使用高能离子束或化学气相沉积等技术,将气相中的原子或分子聚集到材料表面,通过化学反应或物理碰撞的方式对材料表面进行加工。
干法蚀刻工艺具有加工精度高、表面质量好等优点,但也存在设备成本高、加工速度慢等缺点。
蚀刻工艺的原理在实际应用中通常需要考虑多种因素,包括材料的选择、蚀刻溶液的配方、加工参数的优化等。
在半导体制造领域,蚀刻工艺常用于芯片的电路图案定义、衬底的表面处理等工序,对蚀刻加工的精度、均匀性、成本等方面都有较高的要求。
在生物芯片制备领域,蚀刻工艺常用于微流控芯片、生物传感器等微纳结构的加工,对蚀刻加工的生物相容性、加工速度等方面也有特殊要求。
总的来说,蚀刻工艺的原理是通过化学溶液或等离子体对材料表面进行物理或化学的腐蚀,从而实现对材料的微细加工。
不同类型的蚀刻工艺在实际应用中各有优缺点,需要根据具体的加工要求和材料特性进行选择和优化。
随着微纳加工技术的不断发展,蚀刻工艺在微纳加工领域的应用前景将更加广阔。
蚀刻工艺原理
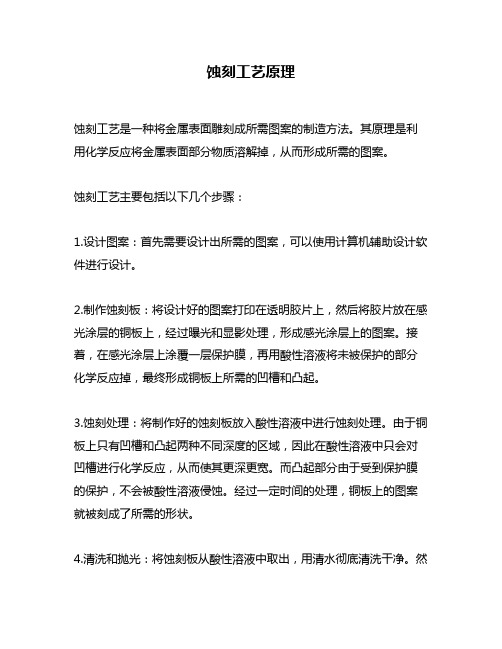
蚀刻工艺原理
蚀刻工艺是一种将金属表面雕刻成所需图案的制造方法。
其原理是利用化学反应将金属表面部分物质溶解掉,从而形成所需的图案。
蚀刻工艺主要包括以下几个步骤:
1.设计图案:首先需要设计出所需的图案,可以使用计算机辅助设计软件进行设计。
2.制作蚀刻板:将设计好的图案打印在透明胶片上,然后将胶片放在感光涂层的铜板上,经过曝光和显影处理,形成感光涂层上的图案。
接着,在感光涂层上涂覆一层保护膜,再用酸性溶液将未被保护的部分化学反应掉,最终形成铜板上所需的凹槽和凸起。
3.蚀刻处理:将制作好的蚀刻板放入酸性溶液中进行蚀刻处理。
由于铜板上只有凹槽和凸起两种不同深度的区域,因此在酸性溶液中只会对凹槽进行化学反应,从而使其更深更宽。
而凸起部分由于受到保护膜的保护,不会被酸性溶液侵蚀。
经过一定时间的处理,铜板上的图案就被刻成了所需的形状。
4.清洗和抛光:将蚀刻板从酸性溶液中取出,用清水彻底清洗干净。
然
后进行抛光处理,使铜板表面更加光滑。
以上就是蚀刻工艺的基本原理和步骤。
蚀刻工艺具有制作精度高、生
产效率高、成本低等优点,在电子、印刷、珠宝等领域得到广泛应用。
电感耦合等离子体原理

1、物理溅射蚀刻(只有能量离子)溅射刻蚀利用能量离子对材料表面进行轰击,使原子从材料表面飞溅出去,从而实现去除材料的目的。
溅射率(每个入射离子所溅射出来的材料原子数)随着离子能量的增加而快速增加。
在离子能量一定的情况下,不同材料的溅射速率相差不大,故而这个过程选择性很差。
溅射是纯物理过程,速率一般比较低。
离子轰击的方向性很强,具有很高的各向异性,可以形成亚微米级的图形,是四种蚀刻中唯一一个可以去除非挥发性产物的过程。
离子能量高低会形成三种效果:①能力太低,轰击在蚀刻材料表面被反射回去了或吸附在材料表面②轰击材料表面导致材料表面原子溅射出去③能量太高,离子轰击到材料内部去了2、纯化学蚀刻(蚀刻粒子)等离子与蚀刻材料形成气相产物,产物必须具有挥发性,这个过程可以具有很高的选择比。
3、离子增强蚀刻(蚀刻粒子+能量离子)离子增强刻蚀是物理溅射刻蚀和化学刻蚀相结合的工艺过程。
离子轰击作用的辅助大大增强了衬底表面的化学反应活性,提高了反应生成物的挥发性,刻蚀效果有明显改善4、侧壁抑制蚀刻(蚀刻粒子+能量离子+先驱物粒子)侧壁抑制刻蚀需要在刻蚀中使用能形成阻挡层的粒子,即等离子体同时提供刻蚀粒子、能量离子和形成阻挡层的先驱物粒子。
先驱物粒子可以吸附在衬底表面形成阻挡层(聚合物薄膜),衬底正面离子轰击比较强,破坏了阻挡层的形成或形成后被去除暴露出衬底表面,而离子轰击薄弱的地方如侧壁,阻挡层附着在侧壁,保护衬底不被蚀刻。
常用的阻挡层先驱物粒子包括CF2、CF3、CCl2等,可以形成碳氟或碳氯聚合物薄膜。
此种工艺可以获得垂直侧壁的高度各向异性备注:等离子体可以包含三种:蚀刻粒子、能量离子、形成阻挡层的先驱物粒子5、工艺对ICP的影响①掩膜:如光刻胶,显影后需要有一个烘烤的过程,称为坚膜,作用有四:去除光刻胶里剩余的溶剂+增强光刻胶与衬底的附着力+提高光刻胶的抗高温、抗蚀刻能力+获得不同角度的胶坡度。
坚膜温度不能太高,否则光刻胶中溶剂太少,导致去胶困难,同时增加了光刻胶内部内应力,导致附着力差。
蚀刻技术
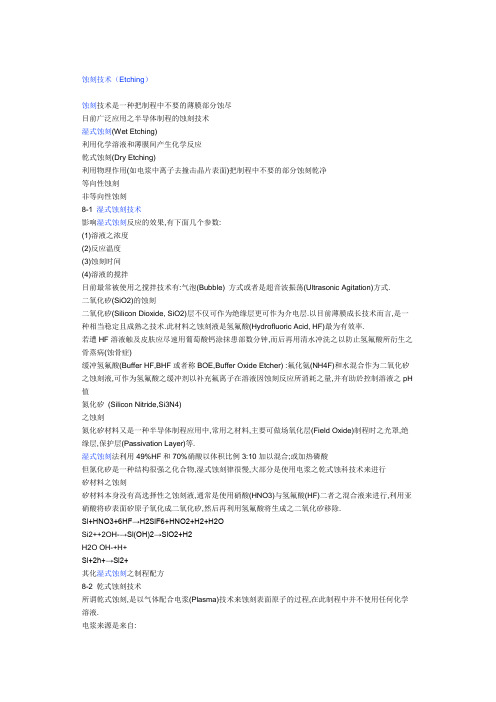
蚀刻技术(Etching)蚀刻技术是一种把制程中不要的薄膜部分蚀尽目前广泛应用之半导体制程的蚀刻技术湿式蚀刻(Wet Etching)利用化学溶液和薄膜间产生化学反应乾式蚀刻(Dry Etching)利用物理作用(如电浆中离子去撞击晶片表面)把制程中不要的部分蚀刻乾净等向性蚀刻非等向性蚀刻8-1 湿式蚀刻技术影响湿式蚀刻反应的效果,有下面几个参数:(1)溶液之浓度(2)反应温度(3)蚀刻时间(4)溶液的搅拌目前最常被使用之搅拌技术有:气泡(Bubble) 方式或者是超音波振荡(Ultrasonic Agitation)方式.二氧化矽(SiO2)的蚀刻二氧化矽(Silicon Dioxide, SiO2)层不仅可作为绝缘层更可作为介电层.以目前薄膜成长技术而言,是一种相当稳定且成熟之技术.此材料之蚀刻液是氢氟酸(Hydrofluoric Acid, HF)最为有效率.若遭HF溶液触及皮肤应尽速用葡萄酸钙涂抹患部数分钟,而后再用清水冲洗之以防止氢氟酸所衍生之骨蒸病(蚀骨症)缓冲氢氟酸(Buffer HF,BHF或者称BOE,Buffer Oxide Etcher) :氟化氨(NH4F)和水混合作为二氧化矽之蚀刻液,可作为氢氟酸之缓冲剂以补充氟离子在溶液因蚀刻反应所消耗之量,并有助於控制溶液之pH 值氮化矽(Silicon Nitride,Si3N4)之蚀刻氮化矽材料又是一种半导体制程应用中,常用之材料,主要可做场氧化层(Field Oxide)制程时之光罩,绝缘层,保护层(Passivation Layer)等.湿式蚀刻法利用49%HF和70%硝酸以体积比例3:10加以混合;或加热磷酸但氮化矽是一种结构很强之化合物,湿式蚀刻律很慢,大部分是使用电浆之乾式蚀科技术来进行矽材料之蚀刻矽材料本身没有高选择性之蚀刻液,通常是使用硝酸(HNO3)与氢氟酸(HF)二者之混合液来进行,利用亚硝酸将矽表面矽原子氧化成二氧化矽,然后再利用氢氟酸将生成之二氧化矽移除.Si+HNO3+6HF→H2SiF6+HNO2+H2+H2OSi2++2OH-→Si(OH)2→SiO2+H2H2O OH-+H+Si+2h+→Si2+其化湿式蚀刻之制程配方8-2 乾式蚀刻技术所谓乾式蚀刻,是以气体配合电浆(Plasma)技术来蚀刻表面原子的过程,在此制程中并不使用任何化学溶液.电浆来源是来自:(1)一个是带正电荷的离子(2)另外是带负电的电子团目前常用之电浆蚀刻技术有:1.活性离子蚀刻(Reactive Ion Etching, RIE).2.磁强化活性离子蚀刻(Magnetically Enhanced RIE, MERIE).3.活性离子蚀刻(Feactive Ion Beam Etching, RIBE).4.低电压及电密度之电子回旋共振(Electron Cyclotron Resonance, ECR).5.螺旋波(Helicoid Wave).6.螺旋共振器(Helicoid Resonator).7.感应耦合电浆(Inductively Coupled Plasma, ICP).电浆之基本性质电浆可视为离子化之气态,这些带正负电粒子藉著静电力之交互作用,而呈现出集体化行为(Collective Behavior)激发气体成离子化态之方式有二种方式:(1)直流电浆(DC Plasma)(2)射频交流电浆(AC Plasma) :(1)无电荷蓄积现象及(2)离子化之效果比DC方式来的强(3)反应腔真空度不必太高乾式蚀刻方法1. 电浆蚀刻技术:2. 反应性离子蚀刻技术(Reactive lon Etching, RIE)为半导体制程之主流(结合物理和化学去除薄膜之机构,具非等向性蚀刻优点和选择性蚀刻技术)有下列几种蚀刻机制:(1)非活性粒子的物理溅击作用.(2)活性粒子的物理溅击作用.(3)电浆之化学反应.(4)活性离子之化学反应.物理作用化学作用基本上,乾蚀刻依反应器对操作形态可分下面几种:1.电容耦合式电浆反应器:2.磁加强性反应式离子蚀刻法(Magnetically Enchanced RIE, MERIE):3.电子回旋共振蚀刻技术(Electron Cyclotron Resonance, ECR):4.螺旋波(Helicoin Wave)蚀刻技术:5.感应耦合电浆蚀刻技术(Inductively Coupled Plasma, ICP):电浆蚀刻之主要效应1. 氢气效应(Hydrogen Effect):CF4电浆是蚀刻Si ,SiO2最常用到之气体,二者之蚀刻率非常接近,若加入少量氢气, Si的蚀刻率随加入H2量增加而急剧下降,而SiO2之蚀刻率却缓慢下降.H2分解成自由基及离子,H自由基和F自由基结合成HF以降低F自由基浓度,而降低对Si蚀刻率Si + 4F SiF4SiO2 + 4F SiF4 + O22. 氧气效应(Oxygen Effect):CF4+O COF2+2F含氧的生成物消耗电浆内的碳原子,使F/C比例升高,因此CF4+O2的电浆对Si之蚀刻率比单纯以CF4快3. 选择性之蚀刻:控制电浆的气体贮组成,控制CF4内之H2和O2含量H(g)+F(g)→HF(g)4. 负载效应(Loading Effect):整体负载效应: 和所要蚀刻之基材面积有关,蚀刻率和晶片数成反比微负载效应(区域负载效应) :由於蚀刻活性种传输不平均所致5. 深宽比之外观效应(Aspect Ratio Dependent Etching, ARDE): 不同宽度的深沟所蚀刻的深度不尽相同,宽度较宽蚀刻后之深度较深6. 电浆蚀刻之天线效应(Antenna Effect):8-3 蚀刻技术未来走向乾式蚀刻技术之发展,在确保半导体制程线宽0.2μm以下扮演极为重要之角色,以目前所研发蚀刻技术之重点,不外乎在改善蚀刻机之非等向性,选择性与蚀刻率之问题.让电浆内离子密度和能量独立进行控制和调整以强化乾式蚀刻之非等向性,选择性与蚀刻率。
蚀刻

• 磁场强化活性离子蚀刻是在传统的活性离子蚀刻系统中加入永久性磁 铁或线圈,产生与芯片平行的磁场,又由于自给偏压所形成的电场与 芯片垂直,因此电子将以螺旋的方式移动,如此一来可减少电子与腔 壁间的撞击,并增加电子撞击气体分子的机率,而产生较高密度的电 浆。
• 感应耦合式电浆是在反应器上方有一介电层窗,其上方有螺旋缠绕的线圈, 并藉由此感应线圈在介电层窗下方产生电浆,电浆的产生位置距离芯片只有 几个平均自由径,故只有少量的电浆密度损失,因此可达成高密度电浆。 BMR的HIETCH将传统的两种系统整合起来了。
纯物理性蚀刻分析
• 利用偏压将离子加速,进行对wafer 的sputter,此过程乃完全利用物理 上能量的转移。 • 离子撞击拥有很好的方向性,可获 得接近垂直的蚀刻轮廓(非等向性 蚀刻anisotropic)。 • 光阻与待蚀刻材料两者将同时遭受 蚀刻,造成对屏蔽物质的蚀刻选择 比变差,同时蚀刻终点(End point) 必须精确掌控,因为以离子撞击方 式蚀刻对于底层物质的选择比很低 (selectively较差)。 • 此外,它的蚀刻效率较低。
• 纯化学反应性蚀刻拥有类似于湿式蚀刻的优点及 缺点,即高选择比及等向性蚀刻。无法应用至次 微米(Å)的组件制程上,包含了线宽控制与均匀性 等问题。
纵观蚀刻过程
• 氟碳比,(Fluorin to Carbon ratio model) gasCF4
– 氟的作用是与基材表面产生化学反应,产生挥发性的产物,因此当氟的成 份增加时,蚀刻速率增加。在硅表面上的反应会消耗氟,而碳并不会损失。 – 碳在电浆中的作用为提供聚合物的来源(可保护侧壁不被蚀刻) ,因此 碳会抑制蚀刻的进行,当碳的成份增加时,将使得蚀刻速率减缓。 – 在制程中加入O2,可消耗C,氟碳比上升,蚀刻速度上升。CF4 + O2 COF2 + 2F – 在制程中加入H2,形成HF(2CF4+H2 2HF+2C),对硅而言,蚀刻速度直线下降,但 对氧化硅,因其含有氧的成分,可局部消耗碳,蚀刻速度不变,这样可提 升SiO2和Si的蚀刻选择比。
- 1、下载文档前请自行甄别文档内容的完整性,平台不提供额外的编辑、内容补充、找答案等附加服务。
- 2、"仅部分预览"的文档,不可在线预览部分如存在完整性等问题,可反馈申请退款(可完整预览的文档不适用该条件!)。
- 3、如文档侵犯您的权益,请联系客服反馈,我们会尽快为您处理(人工客服工作时间:9:00-18:30)。
1.蚀刻的定义:
蚀刻是将材料使用化学反应或物理撞击作用而移除的技术
2. 什么是电浆:具有等量的正電荷和負電荷的離子氣體
電漿就是有著帶電與中性粒子之準中性的氣體,基本上电浆式由部分解离的气体及等量的带正,负电荷的粒子所组成,其中所含的气体具有高度活性,它式利用外加的电场驱动而形成,并且会产生辉光放电现象。
(蚀刻用的电浆中,气体的解离程度很低,属于低密度电浆)
3. 电浆的形成:
电浆是介由直流(DC)偏压或交流射频(RF)偏压下的电场形成,如下图所示
在电浆中的电子来源通常由二:一为分子或原子解离后所产生的电子,另为离子撞击电极所产生的二次电子,在直流(DC)电场下产生的电浆其电子主要以二次电子为主,而交流射频(RF)电场下产生的电浆其电子源其以分子或原子解离后所产生的电子为主。
4.为什么A3采用交流射频(RF)电场产生电浆粒子:
在电浆蚀刻中以直流方式产生辉光放电现象,会由一下确定1。
,需要消耗较高的功率,这样产生的粒子密度低。
不利于快速生产。
2.需要以粒子撞击电极产生二次电子,如此将造成电极材料的耗损;3.所需电极材料必须为导体,如此一来将不适用于晶圆制程中。
在射频放电(RF Discharge)状态下,由于高频操作,使得大部分的电子早半个周期内没有足够的时间移动到正电极,因此这些电子将会在电极间震荡,并与气体分子产生碰撞。
而射频放电所需的震荡频率下限将视电极间的间距,压力,射频电场振幅的大小及气体分子的解离能为而决定。
一般的射频系统所采用的操作频率大都为13.56HZ
相较与直流放电,射频放电具有一下优点:1.放电的情况可一直持续下去而无需二次电子的发射,当晶圆本身即为电极的一部分时,这点对半导体材料制程显得十分重要了。
;2.由于电子来回的震荡,因此粒子化的几率大为提高,蚀刻速率因此而提升;3.可在较低的电极电压下操作,以减少电浆对元器件所导致的损坏;4.对于介电质材料同样可以运作。
5.A3机台电浆蚀刻的基本物理及化学现象
在电浆蚀刻中,随着制程参数及电浆状态的改变,可以区分为两种极端的性质蚀刻方式,即纯物理性蚀刻与纯化学反应蚀刻。
纯物理蚀刻可视为物理溅镀(Sputter)方式它式利用辉光放电,将气体如Ar,解离程带正电的粒子,再利用偏压将电子加速,溅击在被蚀刻物的表面,而将被蚀刻物质原子击出。
此过程乃完全利用物理上的能量转移,故称之为物理性蚀刻。
其特色为粒子撞击拥有很好的方向性,可变为接近垂直的蚀刻轮廓。
但缺点式由于粒子式以撞击的方式蚀刻的目的,因此光阻与待蚀刻材料两者将同时遭受蚀刻,造成对遮罩物质的蚀刻选择比较差,同时蚀刻终点必须精确掌控,因为以粒子撞击方式蚀刻对底层物质的选择比较低,且被击出的物质往往是非挥发性物质,而这些物质容易再度沉积至被蚀刻物薄膜的表面或侧壁。
加上蚀刻效率偏低,因此,以纯物理性蚀刻方式在集成电路制造过程中很少被用到。
化学反应蚀刻,是利用电浆产生化学活性极强的原(分)子团,此原(分)子团扩散至待蚀刻物质的表面,并与待蚀刻物质反应产生挥发性反应生成物,并被真空设备抽
离反应腔室。
因此种反应完全利用化学来达成,故称之为化学反应,此种蚀刻方式相近于湿法蚀刻,只是反应物及产物的状态由液态改变为气态,并利用电浆来促进蚀刻的速率。