弯管力矩计算公式
弯管力矩计算公式之欧阳与创编

第二节管材弯曲一、材弯曲变形及最小弯曲半径二、管材截面形状畸变及其防止三、弯曲力矩的计算管材弯曲工艺是随着汽车、摩托车、自行车、石油化工等行业的兴起而发展起来的,管材弯曲常用的方法按弯曲方式可分为绕弯、推弯、压弯和滚弯;按弯曲加热与否可分为冷弯和热弯;按弯曲时有无填料(或芯棒)又可分为有芯弯管和无芯弯管。
图6—19、图6—20、图6—21和图6—22分别为绕弯、推弯、压弯及滚弯装置的模具示意欧阳与创编 2021.03.08图。
图6—19在弯管机上有芯弯管1—压块 2—芯棒 3—夹持块 4—弯曲模胎5—防皱块 6—管坯欧阳与创编 2021.03.08欧阳与创编2021.03.08图6—20 型模式冷推弯管装置 图6—21 V 形管件压弯模1—压柱 2—导向套 3—管坯 4—弯曲型模 1—凸模 2—管坯 3—摆动凹模欧阳与创编2021.03.08图6—22 三辊弯管原理1—轴 2、4、6—辊轮 3—主动轴 5—钢管一、材弯曲变形及最小弯曲半径管材弯曲时,变形区的外侧材料受切向拉伸而伸长,内侧材料受到切向压缩而缩短,由于切欧阳与创编 2021.03.08向应力θσ及应变θε沿着管材断面的分布是连续的,可设想为与板材弯曲相似,外侧的拉伸区过渡到内侧的压缩区,在其交界处存在着中性层,为简化分析和计算,通常认为中性层与管材断面的中心层重合,它在断面中的位置可用曲率半径ρ表示(图6—23)。
管材的弯曲变形程度,取决于相对弯曲半径D R 和相对厚度D t (R 为管材断面中心层曲率半径,D 为管材外径,t 为管材壁厚)的数值大小,D R 和D t 值越小,表示弯曲变形程度越大(即D R 和D t 过小),弯曲中性层的外侧管壁会产生过度变薄,甚至导致破裂;最内侧管壁将增厚,甚至失稳起皱。
同时,随着变形程度的增加,断面畸变(扁化)也愈加严重。
因此,为保证管材的成形质量,必须控制变形程度在许可的范围内。
管材弯曲的允许变形程度,称为弯曲成形极限。
管材弯曲力矩的计算方法

示 .
1.2 弯 曲变形 区 的应力 应变状态
图 1(b)所示 为管 材 弯曲变形 区的应 力 、应变 状态.当弯 曲变 形程 度较小 时 ,仅 在管 材切 向产 生较 大的
应力 ,而 管壁 厚 度方 向和 圆周方 向产生 的应 力 。都 很小 .随 弯 曲变形 程 度增大 ,塑性 变形 区 由断面
1 管材弯 曲变形 区的应力应变 状态分析
1.1 应变 中性 层 和应力 中性层
如 图 1(a)所 示 ,管 材 在 外 力 矩 作 用 下 纯 弯 曲 时 , 弯 曲变 形 区的 外 侧材 料 受 到 切 向拉 伸而伸 长 ,内侧材料 受
l
4 .
.
点
点
到 切 向压缩而 缩 短 由于切 向
初 始阶段,管材内部的切向应力印小于屈服极限 ,管 \/ : 一_广~\/
材(a 筹)) .随着外力矩 M 增大,管坯内外表面的材料开始发 、 岛一, 本1广‘ 田、 一
生 弹 塑性 变形.当 M 增 大到 使管 坯 内部各 处 的切应 力
‘
均
在冷态下 进行 弯曲加工 ,必 然产生 加工硬 化.塑性 硬化状 态下 切 向应 力的分布如 图 4(b)所示∞
面 2),则当中性层曲率半径P,弯曲角度为n时,距中性层 处的切 奄;
向 燮 刀
、
,
.
、
.
.
一 In _ J告 一ln【l+考J≈考
(1) 图2平剖面假设
因
距 离 成 正 比 ,在 管 坯 内、外 表 面 达 到 最 大值 ,如 图 3
所 示.
牢
图4所示为管材弯曲变形区的应力分布.弯曲的 \ . / ——.
一种圆管弯曲力矩计算公式及其验证

一种圆管弯曲力矩计算公式及其验证吴磊;黄凯东【期刊名称】《机床与液压》【年(卷),期】2016(044)006【摘要】The combination of the traditional pipe-bending technology and the CNC technology of machine tool make the pipe bending process automation. However,there is no fixed size and material specifications. Moreover, the non-linear relationship between the bending moment and the sizes brings troubles in choosing an electric ma-chine of the CNC pipe-bending device. Therefore,this paper presents a formula to calculate the pipe-bending mo-ment,for improving the calculating efficiency and reducing the testing cost. The numerical simulation and experi-mental test were carried out to verify the accuracy of the formula,respectively. The result shows that the presented formula is effective in solving the engineering problems.%数控弯管工艺是传统弯管工艺结合机床数控技术而产生的一种新工艺,可实现加工过程的自动化,但由于工件结构、加工尺寸和材料往往没有固定规格,而弯曲所需力矩与这些尺寸呈现非线性关系,这就给数控弯管设备针对工件选择电机带来不便,对此通过理论推导,得出弯管力矩的计算公式,由此确定弯管力矩,既能提高计算效率,又能减少试验成本。
弯管力矩计算公式

第二节管材弯曲一、材弯曲变形及最小弯曲半径二、管材截面形状畸变及其防止三、弯曲力矩的计算管材弯曲工艺是随着汽车、摩托车、自行车、石油化工等行业的兴起而发展起来的,管材弯曲常用的方法按弯曲方式可分为绕弯、推弯、压弯和滚弯;按弯曲加热与否可分为冷弯和热弯;按弯曲时有无填料(或芯棒)又可分为有芯弯管和无芯弯管。
图6—19、图6—20、图6—21和图6—22分别为绕弯、推弯、压弯及滚弯装置的模具示意图。
图6—19在弯管机上有芯弯管1—压块2—芯棒3—夹持块4—弯曲模胎5—防皱块6—管坯图6—20型模式冷推弯管装置图6—21V形管件压弯模1—压柱2—导向套3—管坯4—弯曲型模1—凸模2—管坯3—摆动凹模图6—22三辊弯管原理1—轴2、4、6—辊轮3—主动轴5—钢管一、材弯曲变形及最小弯曲半径管材弯曲时,变形区的外侧材料受切向拉伸而伸长,内侧材料受到切向压缩而缩短,由于切向应力θσ及应变θε沿着管材断面的分布是连续的,可设想为与板材弯曲相似,外侧的拉伸区过渡到内侧的压缩区,在其交界处存在着中性层,为简化分析和计算,通常认为中性层与管材断面的中心层重合,它在断面中的位置可用曲率半径ρ表示(图6—23)。
管材的弯曲变形程度,取决于相对弯曲半径D R 和相对厚度D t (R 为管材断面中心层曲率半径,D 为管材外径,t 为管材壁厚)的数值大小,D R 和D t 值越小,表示弯曲变形程度越大(即D R 和D t 过小),弯曲中性层的外侧管壁会产生过度变薄,甚至导致破裂;最内侧管壁将增厚,甚至失稳起皱。
同时,随着变形程度的增加,断面畸变(扁化)也愈加严重。
因此,为保证管材的成形质量,必须控制变形程度在许可的范围内。
管材弯曲的允许变形程度,称为弯曲成形极限。
管材的弯曲成形极限不仅取决于材料的力学性能及弯曲方法,而且还应考虑管件的使用要求。
对于一般用途的弯曲件,只要求管材弯曲变形区外侧断面上离中性层最远的位置所产生的最大伸长应变m ax ε不致超过材料塑性所允许的极限值作为定义成形极限的条件。
弯管力矩计算公式
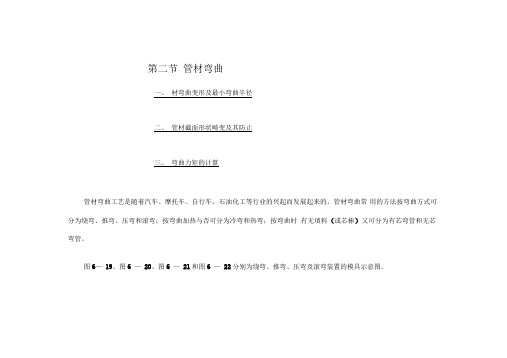
第二节管材弯曲一、材弯曲变形及最小弯曲半径二、管材截面形状畸变及其防止三、弯曲力矩的计算管材弯曲工艺是随着汽车、摩托车、自行车、石油化工等行业的兴起而发展起来的,管材弯曲常用的方法按弯曲方式可分为绕弯、推弯、压弯和滚弯;按弯曲加热与否可分为冷弯和热弯;按弯曲时有无填料(或芯棒)又可分为有芯弯管和无芯弯管。
图6—19、图6 —20、图6 —21和图6 —22分别为绕弯、推弯、压弯及滚弯装置的模具示意图。
图6 —19 在弯管机上有芯弯管1 —压块2—芯棒3—夹持块4—弯曲模胎5—防皱块6—管坯1 2 3图6 —20 型模式冷推弯管装置图6 —21 V形管件压弯模1 —压柱2—导向套3—管坯4—弯曲型模 1 —凸模2 —管坯3 —摆动凹模5 —钢管图6 — 22 三辊弯管原理1 —轴 2、4、6 —辊轮 3 —主动轴 一、材弯曲变形及最小弯曲半径 律管材弯曲时,变形区的外侧材料受切向拉伸而伸长,内侧材料受到切向压缩而缩短,由于切向应 力 J 及应变G 沿着管材断面的分布是连续的,可设想为与板材弯曲相似,外侧的拉伸区过渡到内侧的压缩区,在其交界处存在着中性层,为简化分析和计算,通常认为中性层与管材断面的中心层重合,它在断面中的位置可用曲率半径'表示(图6 —23)o 管材的弯曲变形程度,取决于相对弯曲半径RD和相对厚度t D(R为管材断面中心层曲率半径,D为管材外径,t为管材壁厚)的数值大小,RD和tD值越小,表示弯曲变形程度越大(即RD和tD过小),弯曲中性层的外侧管壁会产生过度变薄,甚至导致破裂;最内侧管壁将增厚,甚至失稳起皱。
同时,随着变形程度的增加,断面畸变(扁化)也愈加严重。
因此,为保证管材的成形质量,必须控制变形程度在许可的范围内。
管材弯曲的允许变形程度,称为弯曲成形极限。
管材的弯曲成形极限不仅取决于材料的力学性能及弯曲方法,而且还应考虑管件的使用要求。
对于一般用途的弯曲件,只要求管材弯曲变形区外侧断面上离中性层最远的位置所产生的最大伸长应变Fax不致超过材料塑性所允许的极限值作为定义成形极限的条件。
三点弯曲力矩公式

三点弯曲力矩公式
三点弯曲试验通常用于测试材料的弯曲强度。
在三点弯曲试验中,将一个梁状物(例如金属棒或复合材料板)放在两个支撑点上,然后在中间施加一个集中力,使梁状物发生弯曲。
三点弯曲力矩公式可以表示为:
M = F * L / 2
其中,M 表示弯曲力矩,单位为牛·米(N·m);F 表示施加的集中力,单位为牛(N);L 表示两个支撑点之间的距离,单位为米(m)。
这个公式的推导基于杠杆原理,即力矩等于力乘以力臂。
在三点弯曲试验中,集中力 F 作用在梁状物的中间,力臂为 L/2,因此弯曲力矩为 M = F * L / 2。
需要注意的是,这个公式只适用于理想情况下的三点弯曲试验,即梁状物在弯曲过程中没有发生变形或扭曲。
在实际情况下,梁状物可能会发生一定的变形,因此需要考虑材料的弹性模量等因素来修正这个公式。
1。
弯管力矩计算公式

弯管力矩计算公式管道弯曲通常会给管道系统带来很大的压力和应力,因此计算弯管力矩是确保管道系统结构和材料的强度足够的重要一步。
在计算弯管力矩时,有两个主要因素需要考虑:1.流体的速度和质量流量:流体的速度和质量流量直接影响到弯管处的流体力学压力。
流体在管道中的流动会受到流体速度和管道直径大小的影响,流体速度越大,流体对管道壁面的冲击力就越大,所产生的弯管力矩也越大。
2.弯曲半径和弯管角度:弯曲半径和弯管角度也会对弯管力矩的大小产生影响。
弯曲半径越小,弯管的曲率半径越小,所产生的弯管力矩就越大。
同样地,弯管角度的大小也会直接影响到弯管力矩的值,弯管角度越大,所产生的弯管力矩也越大。
根据上述因素,弯管力矩计算公式可以表示为:M=Pd×R其中,M是弯管力矩,单位是牛顿·米(N·m);P是流体在管道中的流体压力,单位是帕斯卡(Pa);d是管道的内径大小,单位是米(m);R是弯管的曲率半径,单位是米(m)。
此外,还有一些其他的因素可以对弯管力矩进行修正,比如管道的壁厚、材料的弹性模量和屈服强度等,这些因素可以根据具体情况进行修正。
需要注意的是,弯管力矩计算公式只是一个近似计算公式,实际应用中还需要考虑更多的因素和修正,比如管道的支持和固定方式、管道的温度和膨胀等。
因此,在实际工程设计中,需要综合考虑所有可能的影响因素,并根据实际情况进行计算和修正,以确保管道系统的安全可靠运行。
总之,弯管力矩计算公式是用于计算管道弯曲处的力矩的一个近似公式,其主要考虑了流体速度、质量流量、弯曲半径和弯管角度等因素。
然而,实际应用中还需要考虑更多的因素和修正,以确保管道系统的结构和材料强度足够,并保证系统的安全可靠运行。
钢管折弯扭力计算公式

钢管折弯扭力计算公式钢管是一种常用的建筑材料,它在建筑结构中扮演着重要的角色。
在设计和施工过程中,我们经常需要计算钢管的扭力,以确保其在使用过程中不会发生变形或破裂。
本文将介绍钢管折弯扭力的计算公式及其应用。
首先,我们需要了解一些基本概念。
钢管的折弯扭力是指在外力作用下,钢管发生弯曲和扭转的能力。
在实际工程中,我们通常需要计算钢管在扭转过程中所受的最大扭矩,以确保其在设计要求范围内。
扭矩的计算需要考虑到钢管的几何形状、材料性质和外力作用等因素。
钢管的折弯扭力计算公式可以表示为:T = K S R。
其中,T表示扭矩,单位为牛顿米(Nm);K为系数,与钢管的材料性质和几何形状有关;S为截面积,单位为平方米(m^2);R为弯曲半径,单位为米(m)。
在实际工程中,我们需要根据具体的钢管材料和几何形状来确定系数K的数值。
一般来说,钢管的材料性质可以通过材料的弹性模量和屈服强度来确定。
而钢管的几何形状则包括截面形状和尺寸等因素。
通过确定系数K的数值,我们就可以根据上述公式来计算钢管的折弯扭力。
在实际工程中,我们还需要考虑到外力作用对钢管的影响。
外力作用可以包括静载荷、动载荷和地震荷载等。
在计算扭矩时,我们需要将外力作用对钢管的影响考虑在内,以确保钢管在使用过程中不会发生变形或破裂。
除了计算钢管的折弯扭力,我们还需要对钢管的弯曲和扭转性能进行实验验证。
通过实验,我们可以验证计算公式的准确性,并且可以确定钢管在实际使用中的安全性能。
在进行实验时,我们需要考虑到实验样品的选择、加载方式、测量方法等因素,以确保实验结果的准确性。
综上所述,钢管的折弯扭力计算公式是钢结构设计和施工中的重要内容。
通过计算钢管的折弯扭力,我们可以确定钢管在使用过程中的安全性能,并且可以为工程设计和施工提供参考依据。
在实际工程中,我们需要根据具体情况来确定钢管的折弯扭力,并且需要进行实验验证,以确保钢管的安全使用。
希望本文能够对读者有所帮助,谢谢阅读!。
- 1、下载文档前请自行甄别文档内容的完整性,平台不提供额外的编辑、内容补充、找答案等附加服务。
- 2、"仅部分预览"的文档,不可在线预览部分如存在完整性等问题,可反馈申请退款(可完整预览的文档不适用该条件!)。
- 3、如文档侵犯您的权益,请联系客服反馈,我们会尽快为您处理(人工客服工作时间:9:00-18:30)。
弯管力矩计算公式-CAL-FENGHAI.-(YICAI)-Company One1第二节管材弯曲一、材弯曲变形及最小弯曲半径二、管材截面形状畸变及其防止三、弯曲力矩的计算管材弯曲工艺是随着汽车、摩托车、自行车、石油化工等行业的兴起而发展起来的,管材弯曲常用的方法按弯曲方式可分为绕弯、推弯、压弯和滚弯;按弯曲加热与否可分为冷弯和热弯;按弯曲时有无填料(或芯棒)又可分为有芯弯管和无芯弯管。
图6—19、图6—20、图6—21和图6—22分别为绕弯、推弯、压弯及滚弯装置的模具示意图。
2图6—19 在弯管机上有芯弯管1—压块2—芯棒3—夹持块4—弯曲模胎35—防皱块6—管坯?图6—20 型模式冷推弯管装置图6—21 V形管件压弯模41—压柱 2—导向套 3—管坯4—弯曲型模 1—凸模?2—管坯?3—摆动凹模图6—22三辊弯管原理561—轴 2、4、6—辊轮 3—主动轴 5—钢管一、材弯曲变形及最小弯曲半径管材弯曲时,变形区的外侧材料受切向拉伸而伸长,内侧材料受到切向压缩而缩短,由于切向应力θσ及应变θε沿着管材断面的分布是连续的,可设想为与板材弯曲相似,外侧的拉伸区过渡到内侧的压缩区,在其交界处存在着中性层,为简化分析和计算,通常认为中性层与管材断面的中心层重合,它在断面中的位置可用曲率半径ρ表示(图6—23)。
管材的弯曲变形程度,取决于相对弯曲半径D R 和相对厚度D t (R 为管材断面中心层曲率半径,D 为管材外径,t 为管材壁厚)的数值大小,D R 和D t 值越小,表示弯曲变形程度越大(即D R 和D t 过小),弯曲中7性层的外侧管壁会产生过度变薄,甚至导致破裂;最内侧管壁将增厚,甚至失稳起皱。
同时,随着变形程度的增加,断面畸变(扁化)也愈加严重。
因此,为保证管材的成形质量,必须控制变形程度在许可的范围内。
管材弯曲的允许变形程度,称为弯曲成形极限。
管材的弯曲成形极限不仅取决于材料的力学性能及弯曲方法,而且还应考虑管件的使用要求。
对于一般用途的弯曲件,只要求管材弯曲变形区外侧断面上离中性层最远的位置所产生的最大伸长应变m ax 不致超过材料塑性所允许的极限值作为定义成形极限的条件。
即以管件弯曲变形区外侧的外表层保证不裂的情况下,能弯成零件的内侧的极限弯曲半径min r ,作为管件弯曲的成形极限。
min r 与材料力学性能、管件结构尺寸、弯曲加工方法等因素有关。
图6—23管材弯曲受力及其应力应变状况a受力状态 b应力应变状态不同弯曲加工方式的最小弯曲半径见表6—2。
8表6—2管材弯曲时的最小弯曲半径(单位:mm)注:D为管材外径钢材和铝管在最小弯曲半径见表6—3。
表6—3钢管和铝管的最小弯曲半径 (单位:mm)二、管材截面形状畸变及其防止9管材弯曲时,难免产生截面形状的畸变,在中性层外侧的材料受切向拉伸应力,使管壁减薄;中性层内侧的材料受切向压缩应力,使管壁增厚。
因位于弯曲变形区最外侧和最内侧的材料受切向应力最大,故其管壁厚度的变化也最大(图6—24)。
在有填充物或芯棒的弯曲中,截面基本上能保持圆形,但壁厚产生了变化,在无支撑的自由弯曲中,不论是内沿还是外侧圆管截面变成了椭圆(圆6—24a,b),且当弯曲变形程度变大(即弯曲半径减小)时,内沿由于失稳起皱;方管在有支撑的弯曲(图6—24c,d)中,截面变成梯形。
1011图6—24管材弯曲后的截面形状关于圆管截面的变化情况,在生产中常用椭圆率来衡量。
椭圆率%100minmax ⨯-=D D D (6—21)式中maxD ——弯曲后管材同一横截面的任意方向测得的最大外径尺寸,min D ——弯曲后管材同一横截面的任意方向测得的最小外径尺寸。
图6—25是椭圆率线图,这是把椭圆率对应于无量纲曲率R R 0(0R 为管外半径,R 为弯曲断面中心层曲率半径)的变化表示在对数坐标上,以比值R t 。
作为参变量的直线族来表示的。
由图可知,弯曲程度越大,截面椭圆率亦越大,因此,生产中常用椭圆率作为检验弯管质量的一项重要指标,根据管材弯曲件的使用性能不同,对其椭圆率的要求也不相同。
例如用于工业管道工程中的弯管件,高压管不超过5%;中、低压管为8%;铝管为9%;铜合金、铝合金管为8%。
图6—2512椭圆率截面形状的畸变可能引起断面面积的减小,增大流体流动的阻力,也会影响管件在结构中的功能效果。
因此,在管件的弯曲加工中,必须采取措施将畸变量控制在要求的范围内。
防止截面形状畸变的有效办法是:1)在弯曲变形区用芯棒支撑断面,以防止断面畸变。
对于不同的弯曲工艺,应采用不同类型的芯棒。
压弯和绕弯时,多采用刚性芯棒,芯棒的头部呈半球形或其他曲面形状。
弯曲时是否需要芯棒,用何种芯棒,可由图6—26、图6—27确定。
13图6—26 14芯棒的结构形式15图6—27 16选用芯棒线图2)在弯曲管坯内充填颗粒状的介质、流体介质、弹性介质或熔点低的合金等,也可以代替芯棒,防止断面形状畸变的作用。
这种方法应用较为容易,也比较广泛,多用于中小批量的生产。
3)在与管材接触的模具表面,按管材的截面形状,做成与之吻合的沟槽减小接触面上的压力,阻碍断面的歪扭,是一个相当有效的防止断面形状畸变的措施。
4)利用反变形法控制管材截面变化(图6—28),这种方法常用于在弯管机上的无芯弯管工艺,其特点是结构简单,所以应用广泛。
采用反变形法进行无芯弯管,即是管坯在预先给定以一定量的反向变形,则在弯曲后,由于不同方向变形的相互抵消,使管坯截面基本上保持圆形,以满足椭圆度的要求,从而保证弯管质量。
17图6—2818无芯弯管示意图图6—28无芯弯管示意图1—弯曲模胎2—夹持块3—辊轮4—导向轮5—管坯R(R为中心层曲率半径,D为管材外径)反变形槽断面形状如图6—29,反变形槽尺寸与相对弯曲半径D有关。
见表6—4。
表6—4反变形槽的尺寸19≥—图6—29反变形槽20211—弯曲模胎2—反变形辊轮 管材厚度的变化,主要取决于管材的相对弯曲半径D R 和相对厚度D t 。
在生产中,弯曲外侧的最小壁厚min t 和内侧的最大壁厚m ax t ,通常可用下式作估算:⎥⎦⎤⎢⎣⎡--=D R D t t t 211min⎥⎦⎤⎢⎣⎡-+=D R D t t t 211max式中 t —管材原始厚度 (mm);D —管材外径 (mm);R —中心层弯曲半径 (mm)。
管材厚度变薄,降低了管件的机械强度和使用性能,因此,生产上常用壁厚减薄率作为衡量壁厚变化大小的技术指标,以满足管件的使用性能。
管壁的减薄率%100min⨯-=ttt式中t—管材原始厚度 (mm);mint—管材弯曲后最小壁厚 (mm)。
管材的使用性能不同,对壁厚减薄率也有不同的要求。
如用于工业管道工程的管件,对高压管不超过10%;对中、低压管不超过15%,且不小于设计计算壁厚。
减小管材厚度变薄的措施有:1) 降低中性层外侧产生拉伸变形部位拉应力的数值。
例如采取电阻局部加热的方法,降低中性层内侧金属材料的变形抗力,使变形更多地集中在受压部分,达到降低受拉部分应力水平的目的。
2) 改变变形区的应力状态,增加压应力的成分。
例如改绕弯为推弯,可以大幅度地从根本上克服管壁过渡变薄的缺陷。
2223 三、弯曲力矩的计算管材弯曲力矩的计算是确定弯管机力能参数的基础。
根据塑性力学理论分析,推导出管材均匀弯曲时的弯矩理论表达式如下:管材弯曲力矩:ρπσ343822Btr tr M s +=式中 s σ—屈服应力;t —管壁厚度;r —管材弯曲半径;B —应变刚模数;ρ—弯曲中性层曲率半径。
24 实际管材弯曲时的弯矩、不仅取决于管材的性能、断面形状及尺寸、弯曲半径等参数,同时还与弯曲方法、使用的模具结构等有很大的关系。
因此,目前还不可能将诸多因素都用计算公式表示出来,在生产中只能做出估算。
管材弯曲力矩可用下式估算:3ρσμD W M b =式中 D —管材外径;b σ—材料抗弯强度;W —抗弯断面系数;μ—考虑因摩擦而使弯矩增大的系数。
系数μ不是摩擦系数,其值取决于管材的表面状态,弯曲方式,尤其是取决于是否采用芯棒、芯棒的类型及形状,甚至有关芯棒的位置等多种因素。
一般来说,采用刚性芯棒、不用润滑时,可取μ=5~8;若用刚性的铰链式芯棒时,可取μ=3。
第三节管材翻卷成形一、管材外翻卷成形二、管材内翻卷成形管材翻卷成形是从传统的冲压翻边、缩口工艺发展起来的特种成形工艺,它是通过模具对管件施加轴向压力使管材口部边沿产生局部弯曲的变形过程。
利用此项技术制造零件具有工艺简单、工序少、成本低、质量好等一系列优点,甚至可以生产出用其他冲压方法难以得到的零件。
此工艺已在汽车、航空航天等工业领25域得到广泛应用。
管材翻转成形有两种基本方式,即外翻卷和内翻卷(图6—30)。
图6—30管材翻卷成形示意图26a、b外翻 c、d内翻1—管坯2—导流环3—锥模4—圆角模外翻卷管坯在轴向压力作用下,从内向外翻转,成形后增大其周长。
内翻卷管坯从外向内鄱卷,成形后减小其周长。
利用翻卷工艺除了能有效地成形多种筒类双壁管或多层管零件外,还可以加工凸底杯形件、阶梯管、异形管以及半双管、环形双壁汽筒、空心双壁螺母、热交换器、汽车消声器、电子工业中的波导管等。
目前上述零件一般采用多工步冲压和焊接方法加工,难度大,费用高,外观质量差。
采用翻卷工艺可保证零件使用可靠性,轻量化,节省原材料。
2728图6—31翻卷工艺加工成形的制件a 双层管b 阶梯管c 异形管d 凸底杯目前,根据资料,很多金属材料都可以在模具上以各种不同的翻卷方式成形,如铝合金、铜及铜合金、低碳钢、奥氏体不锈钢等,从110⨯φ到声5250⨯φ规格的管坯都可以成功地翻卷成双层管。
一、管材外翻卷成形翻卷成形,较其他成形工艺而言,其变形过程更为复杂,它包括扩口、卷曲、翻卷几种变形过程及其相互转换。
实现这种成形工艺的模具有多种,其中简单、常用的是锥形模和圆角模。
1. 锥形翻管模锥形翻管模结构如图6—32所示。
这种模具结构简单,在一套模具上可成形不同规格的管材,这一点是在其他管材成形模具上很难做到的。
另外作为精密管材翻卷成形的预成形工序,锥形模成形也得到广泛应用。
29图6—32锥形翻管模3031a 翻管模结构b 锥形翻管工艺参数1—压头2—管坯3—锥模翻管时,管坯的一端置于锥模上,另一端由压力机滑块施加轴向压力,以实现管坯翻卷。
设计这种模具时,模具的半锥角α是最关键的参数,α的大小除了决定翻管成形的可行性外还影响着翻管的几何尺寸,即翻管系数K (K =1D D,D 和1D 分别为管坯外径与翻管外径)。
显然,存在一临界半锥角0α,当模具的半锥角α≥0α时,翻卷才能正常进行。
μ、H 戈尔布诺夫根据主应力法导出: 02000sin 11cos sin 2αααπαD t --=32 考虑材料强化和扩口刚性端的影响,可将上式修改为:()⎪⎭⎪⎬⎫⎪⎩⎪⎨⎧⎥⎦⎤⎢⎣⎡+=+-110323cos n s AL t n L D σα 式中 L ——扩口平直端长度; Dtt t L 4tan tan 17.022+•=ααD ——管坯平均直径;t ——管坯壁厚;n ——材料硬化指数;A ——材料强化系数,s σ——材料屈服强度。