湿法炼锌浸出渣的处理方法
湿法炼锌渣的无害化处理及资源综合回收

湿法炼锌渣的无害化处理及资源综合回收长沙有色冶金设计研究院有限公司- 张乐如 -CONTENTS 目录概述1湿法炼锌工艺及其渣的种类2国内外湿法炼锌渣的处理方法3我国湿法炼锌渣处理的现状4湿法炼锌渣无害化处理方法选择5第一部分概述•由于环境保护意识日益增强,国家的环保政策日益严格,渣处理已经成为制约湿法炼锌的瓶颈;•湿法炼锌有多种不同工艺,产出的渣有多种,其化学成分和化学性质各不相同。
因为湿法炼锌渣属于危险废物的范围,这类危险废物产出量大,不可能也不允许长期堆存,必须进行无害化处理;•无害化处理的方法主要有两大类,一类是火法处理,另一类是填埋。
现在对危险废物填埋也作出了非常严格的规定,不仅对填埋设施提出了很高的要求,对危险废物的化学成分提出了严格的控制限值。
浸出渣即使进行预处理也无法达到控制限值的要求,例如浸出渣中的锌及其化合物(以总锌计)的控制限值为75mg/L是不可能达到的,即使反复洗涤和压滤,也只能达到1g/L左右。
危险废物允许进入填埋区的控制限值序号项目稳定化控制限值(mg/L)1 有机汞0.0012 汞及其化合物(以总汞计)0.253 铅(以总铅计) 54 镉(以总镉计)0.505 总铬126 六价铬 2.507 铜及其化合物(以总铜计)758 锌及其化合物(以总铍计)759 铍及其化合物(以总铍计)0.2010 钡及其化合物(以总钡计)15011 镍及其化合物(以总镍计)1512 砷及其化合物(以总砷计) 2.513 无机氟化物(不包括氟化钙)10014 氰化物物(以CN计) 5 危险废物填埋场要求防渗漏、防腐蚀,还需设有预处理站,建设投资很大,预处理的运行成本很高,这就增加了湿法炼锌的投资和运行成本。
因此研究湿法炼锌渣的无害化处理及综合回收是非常重要的课题。
第二部分湿法炼锌工艺及其渣的种类湿法炼锌工艺方法 热酸浸出 黄钾铁矾法 常规浸出法 热酸浸出 针铁矿法 加压氧气 浸出工艺目前常规浸出一般采用两段连续浸出,只产生一种浸出渣,其成分如下:成分Zn Pb Cu Fe CaO+MgO Al2O3SiO2S Ag(g/t) In(g/t)% 18-22 3-5 0.2-0.6 20-26 2-3 3-5 8-10 4-6 100-150 100-150 常规浸出法这种常规浸出渣具有回收价值,一般用回转窑回收其中的锌、铅和铟,产出次氧化锌烟尘,在其单独浸出过程中产生一种氧化锌浸出渣,由于该浸出渣含铅高,又称为“铅渣”或“铅泥”。
处理湿法炼锌净化钴镍渣的研究

处理湿法炼锌净化钴镍渣的研究目的:研究加酸方式(两种),浆化液固比,浆化时间,浸出时间,浸出温度,浸出PH,硫酸用量,加酸速度,浸出固液比,硫酸浓度对锌钴浸出率的影响仪器与药品:浓硫酸(98%。
化学纯),电动匀速搅拌器,酸度计等工艺流程:钴镍渣→破碎→浆化→浸出→过滤→滤渣,滤液破碎:钴镍渣粉碎后过20目分子筛(筛孔尺寸0.083mm),取筛下物进入下一步的浆化。
浆化:在烧杯中加入一定体积的蒸馏水,称取定量的粉碎后的钴镍渣样品,在机械搅拌的条件下将样品加入烧杯中浆化。
加酸浸出:分步加酸浸出,在搅拌的同时将一定浓度的硫酸分步加入到浆液中,并不断测定浆液的 PH值,控制浸出过程的PH和浸出终点的PH.一次性加液浸出,将相同总量的硫酸一次性加入到钴镍渣浆液中,对浸出过程的PH不加以控制。
过滤:反应结束后过滤浆液,分析滤液中锌离子的浓度,滤渣在90℃下干燥后称重,并分析钴镍元素的含量,计算浸出率。
实验步骤:1.两种加酸方式对锌钴浸出率的影响常温下,保持浆化固液比,机械浆化时间,浸出温度等其他条件相同。
(如常温下,浆化固液比为3,浆化时间为30分钟,浸出时间为6小时,硫酸浓度为400g/L,用量为80%,浸出液固比5)分步加酸浸出实验,采取常温下向钴镍渣浆液中分步加入400g/L的硫酸进行浸出实验,并不断测定浆液的PH,当PH小于数值3.5时,停止加酸;待十分钟左右,如果浆体的PH值升高,大于4.0,继续加酸:直到浸出液长时间稳定在4.0左右,即为浸出终点。
一次性加酸浸出实验,是将等浓度等体积的400g/L 的硫酸一次性加入到钴镍渣浆液中,对浸出过程的 PH不加以控制。
比较两次实验的锌钴浸出率。
2 .浆化固液比对锌钴浸出率的影响常温下,保持浆化时间(0.5小时),浸出时间(6小时),浓硫酸用量(80%),硫酸浓度(400g/L),控制过程PH≧3.5,终点PH≥4.0,浸出固液比(5)等条件相同,考察浆化液固比对锌钴浸出率的影响。
分析湿法炼锌净化钴渣新处理工艺

分析湿法炼锌净化钴渣新处理工艺摘要:湿法炼锌为常用锌生产模式,但是此种方式具有渣含锌量高及渣钴品位低等问题。
传统三段逆锑锌粉除钴工艺缺点明显,如高成本、性能稳定性差、深度净化无法实现及易生成有害气体等,导致其应用价值受到影响,同时也使得此种工艺应用受限。
现阶段,我国部分湿法炼锌企业采用新型试剂除钴工艺进行钴渣净化,能够取得理想的除钴效果。
当前,新型试剂出库过程中所生成的钴渣为有机渣,含锌量较高且钴含量较少,但是此种生产方式可生成有机渣,会加大回收难度,若不及时处理可造成钴渣长时间堆积,容易污染环境并损失有价金属或者加重经济损失,因此采用新的钴渣处理和净化工艺很有必要,同时也可提高经济效益与环境效益。
关键词:湿法炼锌;钴渣净化;处理新工艺;环境效益;经济效益作为我国重要的战略性矿产资源,锌在有色金属工业中占据着非常重要的地位,在合金铸造、黄铜制造以及镀锌等工艺中均有着非常广泛的应用。
但是我国锌资源存在储采比低、需求量大及锌资源供不应求等的特点。
湿法炼锌属于炼锌常用工艺,其应用价值已经大量研究及生产实践证实,具有中性浸出、净化以及电解工艺等日趋成熟,行业技术发展已经向综合回收有价金属过程中转移[1]。
1湿法炼锌净化钴渣现存问题分析锌在我国的生产量和消费量均较高,而湿法炼锌属于中国锌冶炼企业最为常用的冶炼方法。
如硫化锌精矿焙烧可获得锌焙砂,浸出后中性上清液不但含有锌,同时还含有少量的镍、钴、铜等杂质,无论对锌电解亦或对锌产出品质均会产生不良影响,故而在实施电解前必须净化上清液,净化过程中会造成锌大量残留,现阶段常用的净化工艺所产生的净化渣主要包括铜镉渣和钴渣等,故而对净化渣资源进行提炼和综合利用具有非常重要的价值。
钴为湿法炼锌过程中生成的主要有害杂质,若溶液中钴含量>1mg/L时,钴电积过程中阴极可生成锌、钴,导致锌反溶析出,不但会造成锌电解电流效率下降,还会造成锌片出现烧板等现象,净化过程中钴主要来源包括钴渣酸洗溶液、贫镉液中的钴以及锌精矿中的钴。
湿法炼锌

1 概述1.1 国内外发展锌冶炼方法分湿法和火法两大类,火法炼锌有横罐炼锌、竖罐炼锌和密闭鼓风炉炼锌。
横罐炼锌由于环境污染严重,劳动条件恶劣,已基本淘汰。
竖罐炼锌也存在环境污染、能耗较高、不利于综合回收的缺点,也逐步被其他方法所取代。
密闭鼓风炉炼锌又称帝国熔炼法(简称LSP),是由英国帝国熔炼公司开发出来的一种铅锌冶炼方法,20世界60年代开始应用于工业化生产,目前在全世界有20座炉,锌产量占世界锌总产量的12%左右。
由于该方法对原料适应性强,可以冶炼铅锌混合精矿,能耗较小,建设肉孜相对较少,并且很好地解决了火法冶炼的环境污染问题,具有较强的生命力和发展前景。
湿法炼锌是当今炼锌的主要方法,其产量占世界锌产量的80%以上,湿法炼锌可分为常规法、黄钾铁矾法、针铁矿法、赤铁矿法,采用较多的是前三种方法。
前面提到的湿法炼锌工艺,都需要采用氧化脱硫,一般是沸腾焙烧,焙烧产出的氧化锌焙砂送湿法炼锌系统生产电锌。
另外还有全湿法炼锌工艺,即硫化锌精矿直接加压氧浸工艺。
加压氧气浸出技术是加拿大谢利特·哥顿公司在20世纪50年代开发的,开始用于金属硫化精矿的处理,回收镍、钴,共建有6座工厂,其中4座回收镍,2座回收钴。
70年代加压氧浸被用于硫化锌精矿处理。
炼锌技术的发展方向主要是减少污染,降低消耗,节约成本和提高有价金属回收率等,由此推动炼锌技术的不断进步,创造出多种多样的炼锌技术和工艺流程,可供我们合理选择。
我国是世界上锌生产和消费大国,从1996年至今其产量稳居世界第一。
2014年我国锌产量582.7万t,占当年全球锌总产量1315万t的43.2%。
这是基于我国的镀锌钢板产量差不多占世界半壁江山、年产成百亿支锌锰电池大规模出口、制造业对黄铜等各类锌基合金需求旺盛、建筑业的高速发展使氧化锌涂料消费量急增等需求因素带动了锌产业的快速发展。
另外我国锌资源较为丰富,其储量及储量基础仅次于澳大利亚,居世界第二位。
锌湿法冶炼渣处理工艺研究

锌湿法冶炼渣处理工艺研究摘要:有色金属冶炼的环境保护和资源高效利用已成为制约行业可持续发展的关键因素,湿法炼锌生产的浸出渣开路问题是企业面临的难题之一。
本文针对我国湿法炼锌采用的主流工艺,基于生产过程的产生的各种浸出渣、净化渣、烟尘、污泥等含锌物料的来源、组成和污染物进行分析,较系统地总结了目前各类锌冶炼渣的综合利用及无害化处理技术。
关键词:湿法炼锌;锌冶炼渣;处理工艺1冶炼渣的来源与组成1.1常规浸出冶炼渣常规浸出过程为中性浸出和酸性浸出两段。
中性浸出液的净化采用置换或化学沉淀,一般加入锌粉去除铜镉,然后将溶液升温加锌粉和活化剂锑盐或砷盐去除钴镍,最后加锌粉去除复溶镉,分别得到铜镉渣和镍钴渣,也可采用黄药除钴生成黄酸钴渣。
添加铜渣或石灰乳去除氟、氯,分别得到氯化亚铜和氟化钙沉淀。
通过控制酸性浸出液的pH值,Fe2+被氧化成Fe3+后水解去除,酸性浸出渣含锌约20%,Fe约25%,铅约5%,烟尘中含有少量的氧化锌尘和SO2。
常规浸出冶炼渣为有害渣,含有价金属多,回收利用技术相对成熟。
1.2热酸浸出冶炼渣热酸浸出与常规浸出不同的是中性浸出渣采用二段高温高酸浸出,使渣中难溶于稀硫酸的铁酸锌溶解进入酸性浸出液。
富集于热酸浸出渣中的铅、银等称为铅银渣,其中锌主要以ZnS和ZnFe2O4形式存在,铁主要以Fe2O3和FeO形式存在,铅主要以PbS和PbSO4形式存在,银主要以Ag2S和AgCl形式存在。
热酸浸出液除铁后返回中性浸出流程,除铁工艺主要有:黄钾铁矾法、针铁矿法、赤铁矿法,使浸出液中的Fe以黄钾铁矾、针铁矿、赤铁矿的形式与溶液分离。
1.3高压氧浸浸出渣氧压浸出是在高压釜内直接高温氧压浸出硫化锌精矿,可避免副产硫酸,浸出液的处理过程与常规流程一致。
此工艺反应速度快,提高了原料中镓、锗、铟等稀散金属的回收率和铜、镉的浸出率和回收率,利于铅、银等贵金属的富集。
氧压浸出废渣含20%~25%的水份和12%~15%的元素硫,根据精矿原料的不同及后续渣处理工艺的差异,氧压浸出渣分为高银渣和低银渣,高银渣又分成高铁渣和低铁渣。
湿法炼锌除杂技术研究现状
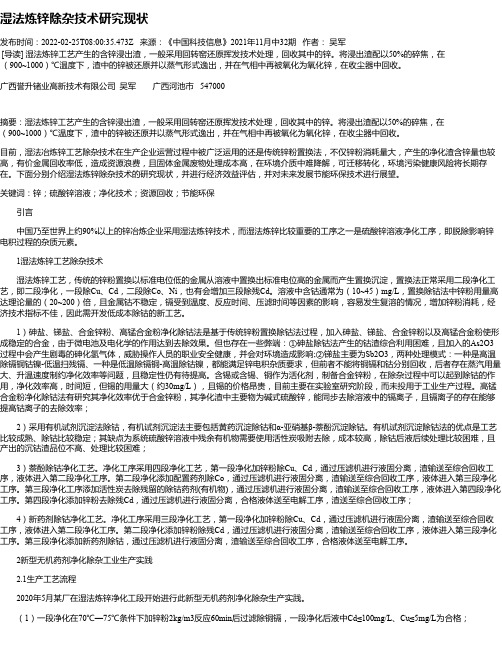
湿法炼锌除杂技术研究现状发布时间:2022-02-25T08:00:35.473Z 来源:《中国科技信息》2021年11月中32期作者:吴军[导读] 湿法炼锌工艺产生的含锌浸出渣,一般采用回转窑还原挥发技术处理,回收其中的锌。
将浸出渣配以50%的碎焦,在(900~1000)℃温度下,渣中的锌被还原并以蒸气形式逸出,并在气相中再被氧化为氧化锌,在收尘器中回收。
广西誉升锗业高新技术有限公司吴军广西河池市 547000摘要:湿法炼锌工艺产生的含锌浸出渣,一般采用回转窑还原挥发技术处理,回收其中的锌。
将浸出渣配以50%的碎焦,在(900~1000)℃温度下,渣中的锌被还原并以蒸气形式逸出,并在气相中再被氧化为氧化锌,在收尘器中回收。
目前,湿法冶炼锌工艺除杂技术在生产企业运营过程中被广泛运用的还是传统锌粉置换法,不仅锌粉消耗量大,产生的净化渣含锌量也较高,有价金属回收率低,造成资源浪费,且固体金属废物处理成本高,在环境介质中难降解,可迁移转化,环境污染健康风险将长期存在。
下面分别介绍湿法炼锌除杂技术的研究现状,并进行经济效益评估,并对未来发展节能环保技术进行展望。
关键词:锌;硫酸锌溶液;净化技术;资源回收;节能环保引言中国乃至世界上约90%以上的锌冶炼企业采用湿法炼锌技术,而湿法炼锌比较重要的工序之一是硫酸锌溶液净化工序,即脱除影响锌电积过程的杂质元素。
1湿法炼锌工艺除杂技术湿法炼锌工艺,传统的锌粉置换以标准电位低的金属从溶液中置换出标准电位高的金属而产生置换沉淀,置换法正常采用二段净化工艺,即二段净化,一段除Cu、Cd,二段除Co、Ni,也有会增加三段除残Cd。
溶液中含钴通常为(10~45)mg/L,置换除钴法中锌粉用量高达理论量的(20~200)倍,且金属钴不稳定,镉受到温度、反应时间、压滤时间等因素的影响,容易发生复溶的情况,增加锌粉消耗,经济技术指标不佳,因此需开发低成本除钴的新工艺。
1)砷盐、锑盐、合金锌粉、高锰合金粉净化除钴法是基于传统锌粉置换除钴法过程,加入砷盐、锑盐、合金锌粉以及高锰合金粉使形成稳定的合金,由于微电池及电化学的作用达到去除效果。
降低锌湿法冶炼过程浸出渣含锌的处理工艺

降低锌湿法冶炼过程浸出渣含锌的处理工艺摘要:在锌冶炼处理过程中,常用浸出工艺包括了常规浸出、高温高酸浸出、直接浸出,第一种处理工艺相较剩余两种,拥有投资成本少,处理工艺周期短的工艺优势,但是在使用过程中存在浸出渣中过高的含锌量,锌的回收率不高这一问题。
根据以往锌冶炼的浸出工艺经验,达到19%~22%的浸出渣含锌量,较热酸浸出渣5%~8%的含锌量明显要高。
所以对于锌冶炼企业来讲,想要提升锌冶炼过程中的锌回收率,减少浸出渣的渣量,控制锌冶炼成本投入,就要降低锌的浸出渣含锌。
本文对降低锌湿法冶炼过程中浸出渣含锌量的处理工艺进行试验探讨并加以总结。
关键词:锌湿法;冶炼;处理工艺引言生产锌时会产生各种类型的渣,而且绝大多数都属于危险的固体废弃物。
虽然大部分都可以返回到主流程当中,将含有的有价金属提取出来,但是仍然会存在一些冶炼渣,没有办法有效利用,存在环境污染风险,这成为了行业发展当中急需解决的技术和共性问题。
1锌冶炼工艺现状1.1浸出过程流量大在浸出处理工艺中达到600m3/h的流量,为了能够确保冲矿流量充足,预防沸腾炉焙砂发生“沉底”,中性浸出循环流量基本达到了400m3/h,另外加入200m3/h废酸,基本达到了450m3/h的酸性进出流量,分别包括100m3/h、100m3/h、250m3/h的分级底流、废酸与中性底流。
在浸出过程中过大流量不仅压缩了浸出时间,过低的温度和初始酸度,还随之降低了铜、锌内有价金属的浸出率,过大流量加大了浓缩澄清压力,极易导致浓缩槽的上清液过于浑浊,增高含固量,导致对后续的净化生产造成严重影响。
酸上清浑浊还会导致系统内部的浸出渣恶性循环,对生产渣平衡性有所突破,严重情况下甚至会无法维持浸出过程。
1.2浸出过程温度低该厂就降低锌湿法冶炼过程浸出渣含锌的合理与科学性做了大量的试验论证工作,运用了热焙砂冲矿、蒸汽加热这两种升温方法。
因为较大的浸出流量所致未能达到充足的升温时间,过低的浸出温度,在中性浸出时上清温度在65℃以内,酸性进出槽的温度在80℃以内。
锌浸出渣的处理
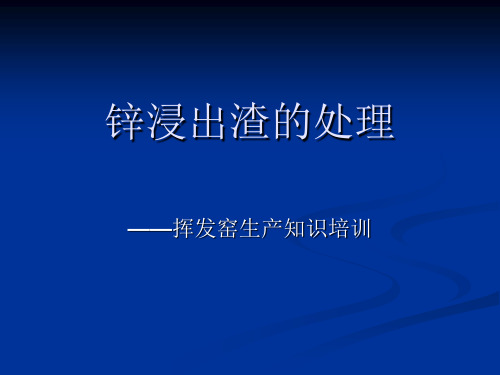
4、窑身转动 窑身的转速对于炉料在窑内停留时间,反 应速度及反应的完成程度有很大影响。转 速太大,炉料在窑内停留时间短,虽然翻 动良好,但反应不完全,渣含锌升高。转 速太慢,炉料在窑内停留时间长,焦粉 (无烟煤)燃烧完全,但处理量低。一般 来说,炉料在窑内的停留时间为2~3h, 窑身转速在60~120s/r。
注意!
硫化铅可与其他金属硫化物形成底熔点冰 铜,PbO与SiO2形成底熔点硅酸铅。所以, 当炉料中含PbS过高时,产生的金属铅、冰 铜、底熔点硅酸盐,由于其渗透力很强, 会渗入窑衬而侵蚀炉衬,当其聚集时使炉 料形成炉结,阻碍锌、铅的挥发,恶化操 作等。因此,应当在配料时配加更多的焦 粉(碎煤),以吸收溶体产物。另外采用 强制鼓风、延长高温区,提高废气出口温 度,也有利于铅、锌的挥发,减少熔渣。
硫酸铅:
铅在浸出渣中大部分以硫酸铅形态存在, 也有少量的硫化铅、氧化铅及硅酸铅。硫 酸铅在窑内被还原成硫化铅,氧化铅被还 原成金属铅,硫酸铅、硫化铅和氧化铅也 可能进行交互反应形成金属铅: PbSO4+PbS=2Pb+SO2 PbS+2PbO=3Pb+SO2 过程中不论PbS、PbO还是Pb都能挥发,且 以PbS、PbO挥发为主。
铁酸锌:由于锌精矿中含有较多的铁,在焙烧是形成铁 酸锌。在常规浸出条件下,铁酸锌几乎不溶解而残留在 渣中,约占渣含锌量的50~60%,它在窑内发生的反应: 3(ZnO· Fe2O3)+C=2 Fe3O4+3ZnO+CO ZnO· Fe2O3+ CO= ZnO+2 FeO+CO2 ZnO+ CO=Zn+CO2 当窑内温度在1050℃以上时,上述反应进行很快, 且有部分氧化铁被还原为金属铁,促使氧化锌的还原。 ZnO+Fe=Zn(气)+FeO ZnO· Fe2O3+Fe=Zn(气)+4FeO