连杆机构的优化设计
6连杆机构优化设计
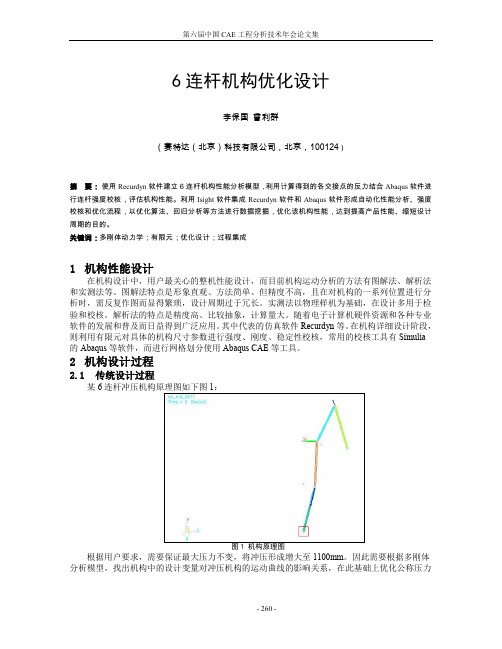
2000t,行程 1100mm 的多连杆机构。为满足用户使用要求和最小化生产厂家变更引起费用,此机 构必须满足下列条件: 驱动臂 R=250~280mm;支撑点变化范围 X=1100~1300,Y=150~350mm; 曲柄中心到下死点距离 2800~3150;公称压力 2400T,公称压力行程 30mm; 滑块拉伸行程为 400mm,拉伸行程内速度小于 21m/s,最大小于 23m/s,为保证冲压质量, 在拉伸行程内拉伸曲线要接近直线,如图 3 示; 连杆压力角小于 45 度; 摆杆与摇杆之间传动角大于 55 度; 连杆最大应力小于 60MPa。 对应的冲头的位移、速度、加速度曲线如图示:
1 机构性能设计
在机构设计中,用户最关心的整机性能设计,而目前机构运动分析的方法有图解法、解析法 和实测法等。图解法特点是形象直观、方法简单、但精度不高,且在对机构的一系列位置进行分 析时,需反复作图而显得繁琐,设计周期过于冗长。实测法以物理样机为基础,在设计多用于检 验和校核。解析法的特点是精度高、比较抽象,计算量大。随着电子计算机硬件资源和各种专业 软件的发展和普及而日益得到广泛应用。 其中代表的仿真软件 Recurdyn 等。 在机构详细设计阶段, 则利用有限元对具体的机构尺寸参数进行强度、刚度、稳定性校核,常用的校核工具有 Simulia 的 Abaqus 等软件,而进行网格划分使用 Abaqus CAE 等工具。
- 262 -
第六届中国 CAE 工程分析技术年会论文集
图 6:Isight 集成 Recurdyn、Abaqus 试验设计流程
粒子群算法(particle swarm optimization,PSO)由 Kennedy 和 Eberhart 在 1995 年提出,该算法 模拟鸟集群飞行觅食的行为,鸟之间通过集体的协作使群体达到最优目的,是一种基于 Swarm Intelligence 的优化方法。同遗传算法类似,也是一种基于群体叠代的,但并没有遗传算法用的交 叉以及变异,而是粒子在解空间追随最优的粒子进行搜索。PSO 的优势在于简单容易实现同时又 有深刻的智能背景,既适合科学研究,又特别适合工程应用,并且没有许多参数需要调整。目前, 已有的群智能理论和应用研究证明群智能方法是一种能够有效解决大多数优化问题的新方法,更 重要是,群智能潜在的并行性和分布式特点为处理大量的以数据库形式存在的数据提供了技术保 证。无论是从理论研究还是应用研究的角度分析,群智能理论及应用研究都是具有重要学术意义和 现实价值的。 粒子群算法(particle swarm optimization,PSO)搜索方向按照下式更新。
契贝谢夫四连杆机构的优化设计与应用

பைடு நூலகம்
机 械 设 计 与 制 造
Ma h n r De i n & c iey sg Ma u a t r n fcu e 6 3
2 1 年 9月 01
文 章 编号 :0 1 39 (0 10 — 0 3 0 10 — 9 7 2 1 )9 0 6 - 2
契 贝谢 夫 四连 杆机 构 的优 化 设计 与应 用 术
l低功耗、 低成本、 易控制的腿式行走机器人提供设计依据, 方法实用可行。 2
; l
关键词 : 契贝谢夫四杆机构 ; 优化设计 ; 腿式机器人 ;d m Aa s { 【 bt c】C eyhvfu _ l k ehsbe pii d it , sd o nl i l e o , i A s at hbse or 6 i a a en ot z  ̄ rl b e n aa ta m t d r ng m e F sy a yc h
( ol e f n fcui c n e n n ier g Suh et nvri f ce c n l g ua tr gS i c dE gn ei ,o tw s U ies y in e d C e o Ma n e a n to S a
T c n l y Mi y n 2 0 0 C ia e h oo , a a g6 1 1 ,hn ) g n
, . t ~ 、 N + 十 十 十 嘶 t 十 十 t N N N N 、 . ' N — 、 、 毫一 l 、斤 N 套 " ” 、 §斤 N N ^" " ¨ "
;
【 要】 摘 优化了契贝 谢夫平面四 杆机构。 首先, 利用解析法, 建立了契贝 谢夫平面四 杆机构的 { 数
li , e h i ,nr nis dbc eu tna e tm eS o { o c" ot ,c s c t f c na 。ei ni ybn eride , t 1e h n 1f 1 ) n a m 。 fu t jt f c。h e ede n ̄cd s 。n v
契贝谢夫四连杆机构的优化设计与应用
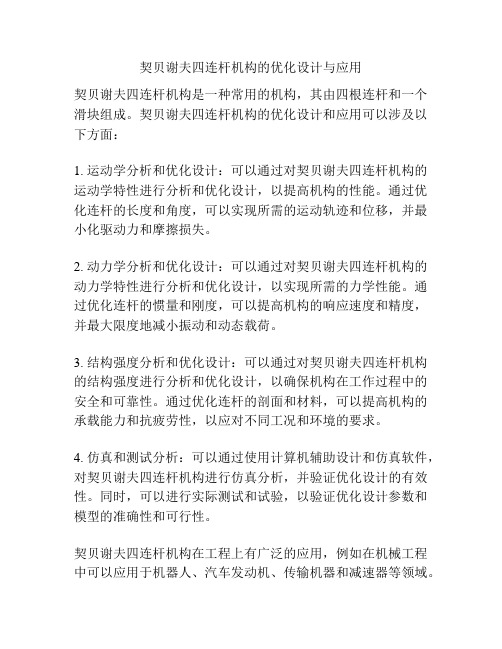
契贝谢夫四连杆机构的优化设计与应用
契贝谢夫四连杆机构是一种常用的机构,其由四根连杆和一个滑块组成。
契贝谢夫四连杆机构的优化设计和应用可以涉及以下方面:
1. 运动学分析和优化设计:可以通过对契贝谢夫四连杆机构的运动学特性进行分析和优化设计,以提高机构的性能。
通过优化连杆的长度和角度,可以实现所需的运动轨迹和位移,并最小化驱动力和摩擦损失。
2. 动力学分析和优化设计:可以通过对契贝谢夫四连杆机构的动力学特性进行分析和优化设计,以实现所需的力学性能。
通过优化连杆的惯量和刚度,可以提高机构的响应速度和精度,并最大限度地减小振动和动态载荷。
3. 结构强度分析和优化设计:可以通过对契贝谢夫四连杆机构的结构强度进行分析和优化设计,以确保机构在工作过程中的安全和可靠性。
通过优化连杆的剖面和材料,可以提高机构的承载能力和抗疲劳性,以应对不同工况和环境的要求。
4. 仿真和测试分析:可以通过使用计算机辅助设计和仿真软件,对契贝谢夫四连杆机构进行仿真分析,并验证优化设计的有效性。
同时,可以进行实际测试和试验,以验证优化设计参数和模型的准确性和可行性。
契贝谢夫四连杆机构在工程上有广泛的应用,例如在机械工程中可以应用于机器人、汽车发动机、传输机器和减速器等领域。
在机械设计和制造过程中,优化设计和应用契贝谢夫四连杆机构可以提高机械系统的性能、效率和可靠性。
此外,契贝谢夫四连杆机构也可以应用于模拟和教学实验,用于解决实际问题和培养学生的设计和创新能力。
平面连杆机构优化设计及运动仿真

{ = 一 ( 卢 一 ∞
: +一
芏
:
一 咖 5
‘ 一 ‘ 。 。 妒 ( 13 )
.
将 已 知 数 据 代 入 优 化 设 计 的数 学 模 型 表 示为 :
r —— —— — — —— —— —— 一
2 ‘ √ + 等 一 2 ‘ c 0 s 妒
m i n f ( x ) = 、 / ∑ 【 一 m ) + ( 一 ) ]
:
其中 = 0 +r p f ; 0 为曲柄 1 的起
( 2 .1 )
始角,c p f 为已 知量。
1 . 3确定约 束条件 1 . 3 . 1曲柄摇杆机构存在条件约束 为
岛( x ) = 3 0 P — y ≤ 0 ( 22 )
.
g 1 ( ) :/ 1 + , 2 一 一『 4 0 g : ( ) =f l + f ] 一f 2 一f 4 0
g 3 ( ) =f l +7 4 一f 3 — 1 2 0
g 4 ( ) =一 ‘≤0
应 用技 术
平面连杆机构优化设计及运动仿真
邹 学敏 蒋 晓 峰
湖南省特 种设 备检 验检 测研 究院永州分院 湖南 永州 4 2 5 0 0 0
摘要: 以四杆机构为例 ,根据其设计要求和特点 , 建 立 了四杆机构 的优化设计数 学模型 ,在满足诸多影响 因素 的条件下 ,用计算机软件进行优化设 计 以获得 一个在各 方面均 较令人 满意的机构 设计方案;并对优化设计 的曲柄摇杆机构进行运 动仿真分 析。结果表 明: 采用优化设 计方法可以缩短设 计周期 、 提高设计质 量和设 计精度 ; 运动仿真起 到很好的反馈作用和验证作用。同时该方 法也为 多杆机构和其他机构 的优 化和仿真设计提供 了 借 鉴。 关键 词 :平 面连杆机构 M A T L A B 优化设计 运 动仿真
基于matlab的平面连杆机构优化设计

基于matlab的平面连杆机构优化设计
基于Matlab的平面连杆机构优化设计是指利用Matlab软件平台,对平面连杆机构进行优化设计的过程。
平面连杆机构是一种常见的机械传动机构,广泛应用于各种机械系统中,如机械手、凸轮机构等。
优化设计是指通过数学建模、计算和分析,寻求满足一定性能要求的最优设计方案。
在基于Matlab的平面连杆机构优化设计中,通常需要建立机构的数学模型,包括几何模型和运动学模型。
几何模型描述机构的几何形状和尺寸,而运动学模型则描述机构的位置、速度和加速度等运动参数。
然后,利用Matlab 进行数值计算和分析,以确定最优的设计参数。
具体来说,基于Matlab的平面连杆机构优化设计可以分为以下几个步骤:1.建立数学模型:根据实际问题,建立平面连杆机构的几何模型和运动学模
型,将实际问题转化为数学问题。
2.定义优化目标:根据设计要求,定义优化目标函数,如最小化某个性能参
数、最大程度满足某个约束条件等。
3.确定设计变量:选择影响优化目标的主要参数作为设计变量,如连杆长度、
角度等。
4.约束条件:根据实际应用需求和机构运动特性,定义约束条件,如角度范
围、位移范围等。
5.求解优化问题:利用Matlab的优化工具箱进行数值计算,求解优化问题,
得到最优设计方案。
6.结果分析和验证:对优化结果进行分析和验证,确保最优设计方案的有效
性和可行性。
总之,基于Matlab的平面连杆机构优化设计是一种通过数学建模和数值计算来寻求最优设计方案的方法。
它可以帮助设计师快速找到满足性能要求的设计方案,提高设计效率和产品质量。
装载机反转六连杆机构的优化设计

中 图 分 类 号 : 1 .1 U4 55
引言
装 载机 主 要 用来 铲 、 、 、 散 装物 料 , 一 种 用途 十 装 卸 运 是
装 载 机 的 工 作 机 构
运 用 机 械 动 力 学 仿 真 软 件 ( AMS 建 立 了 某 装 载 机 反 转 六 连 杆 机 构 的 动 力 学 模 型 , 其 进 行 了 仿 真 研 究 , AD ) 对 发 现 在 装 载 机 铲 装 作 业 过 程 中 , 斗 的 最 大 转 动 角 度 达  ̄ 2 .。 经 过 A MS 化 设 计 后 , 斗 的 最 大 转 动 角 度 降 f f 。 从 铲 f 39 , J DA 优 铲  ̄ ] , 9
转 自缸
提 升过 程 中 , 斗有 一 定程 度 的转 动 。 了在 装载 作 业 中减 铲 为
少 物料 的撤 落 , 以下2 办 法 。 有 种 () 动 臂 提 升 过 程 中 , 驶 员 不 停 地 调 整 转 斗 油 缸 的 1在 驾 位置 . 持 铲 斗 的角度 不 变 : 保 () 过 优 化 设 计 的 方 法 使 反 转 六 连 杆 机 构 在 动 臂 举 2 通 升 过 程 中保 持 铲斗 的角 度 不 变 。 第 1 方 法容 易使 驾 驶 员产 生 疲 劳 , 此不 宜采 用 : 2 种 因 第 种 方 法 是 现 在 通 用 的 办 法 。 传 统 的 机 械 设 计 常 采 用 试 算 的
装载 机 的工 作 机构 主要 包 括 转 斗 油 缸 、 臂 、 臂 、 摇 动 铲
分 广 泛 的 工 程 机 械 ,轮 胎 式 装 载 机 由于 其 速 度 快 、 灵 活 机 斗 、 杆 和 动 臂 油 缸 6 部 件 , 为 六 连 杆 机 构 。 因 为 转 斗 连 个 称 又 动 、 率 高 而 被 广 泛 使 用 E2 某 型 装 载 机 在 装 载 物 料 过 程 油 缸 的 运 动 方 向 和 铲 斗 的 转 动 方 向 相 反 .所 以称 为 反 转 六 效 l] -。 中经 常 出现 物料 撤 落 的情况 , 重 影 响 了其 作 业效 率 。 严 经分 析后 认 为 ,物料 撤 落 的主 要原 因是 装载 机在 动 臂 连 杆 机 构 。 某 装 载 机 工 作 装 置 的 结 构 如 图 1 示 [。 所 3 ]
铰链四杆机构实现连杆轨迹的优化设计

%铰链四杆机构实现连杆轨迹的优化设计% (调用目标函数lgjg_gjyh_mb 和非线性约束函数lgjg_gjyh_ys)%设计变量:x(1)-机架;x(2)-曲柄;x(3)-连杆;x(4)-摇杆;x(5)-连杆附杆;% x(6)-机架倾斜角beta;x(7)-连杆与附杆夹角 gamma;x(8)-曲柄相初始角thetaO; %设计变量初值 x0=[50;7;55;25;25;-12;15;50]; %设计变量边界 lb=[10;8;10;10;10;-20;5;5]; ub=[60;30;60;40;30;30;15;60]; % % % %hd=pi/180;delta_ n=acos((xo pt(3)A2+xo pt(4) ^2-(x0 pt(1)-xo pt(2))A2)/(2*x op t(3)*xo pt(4))); fprintf (' 机构最小传动角 delta_min = %3.4f ° \n',delta_n/hd);%调用多维约束优化函数(lgjg_gjyh_ys)计算最优点x*的性能约束函数值 [g,ceq]=lgjg_gjyh_ys(xo pt); disp ' fprintf (' 最小传动角约束函数值 g1* = %3.4f \n',g(1))fprintf (' 曲柄长度 <=机架长度 g2* = %3.4f \n',g(2)) fprintf (' 曲柄长度 <=连杆长度 g3* = %3.4f \n',g(3))fprintf (' 曲柄长度 <=摇杆长度 g4* = %3.4f \n',g(4))fprintf (' 曲柄+机架 <=摇杆+连杆 g5* = %3.4f \n' ,g(5)) fprintf (' 曲柄+连杆 <=摇杆+机架 g6* = %3.4f \n ',g(6)) fprintf (' 曲柄+摇杆 <=连杆+机架 g7* = %3.4f \n' ,g(7)) fprintf (' 机架长度<=60 g8* = %3.4f \n',g(8)) fprintf (' 曲柄长度>=8 g9* = %3.4f \n',g(9))fprintf (' 曲柄长度<=30 g10* = %3.4f \n',g(10)) fprintf (' 连杆长度<=60 g11* = %3.4f \n',g(11)) fprintf (' 摇杆长度<=40 g12* = %3.4f \n',g(12)) fprintf ('附杆长度>=10g13* = %3.4f \n',g(13))fprintf (' 机架长度 d = %3.4f mm \n',xo pt(1)) fprintf (' 曲柄长度 a = %3.4f mm \n',xo pt(2)) fprintf (' 连杆长度 b = %3.4f mm \n',xo pt(3)) fprintf (' 摇杆长度 c = %3.4f mm \n',xo pt(4)) fprintf (' 连杆附杆长度 h = %3.4f mm \n',xo pt(5)) fprintf (' 机架倾斜角 beta = %3.4f ° \n :X op t(6))fprintf (' 连杆与附杆夹角 gamma = %3.4f ° \n ',xo pt(7fprintf (' 曲柄初始位置角theta0 = %3.4f ° \n ',xo pt(8)) fprintf ('M 点轨迹坐标偏差f* = %3.4f\n ',fo pt)I线性不等式约束(g(2)〜g(20))中设计变量的系数矩阵 a 省略,定义为空矩阵“[]”线性不等式约束(g(2)〜g(20)中的常数项列阵b 省略,定义为空矩阵“[]” 没有等式约束,参数 Aeq 和beq 定义为空矩阵“[]” 调用非线性优化函数[xop t,fo pt]=fmi ncon( @lgjg_gjyh_mb,x0,[],[],[],[],lb,ub,@lgjg_gjyh_ys); dis p铰链四杆机构实现连杆轨迹的优化设计最优解最优点的约束函数值附杆长度<=30 g14* = %3.4f \n',g(14)) fprintf ('fprintf (' 机架倾斜角>=-20 °g15* = %3.4f \n',g(15)) fprintf ('机架倾斜角<=30 °g16* = %3.4f \n',g(16)) fprintf ('连杆附杆夹角>=0 °g17* = %3.4f \n',g(17)) fprintf ('连杆附杆夹角<=15 °g18* = %3.4f \n',g(18)) fprintf (' 曲柄初始角>=0 °g19* = %3.4f \n',g(19)) fprintf ('曲柄初始角<=15 °g20* = %3.4f \n',g(20)) 计算结果:Op timizati on term in ated: magn itude of direct ional derivative in search direct ion less tha n 2*op ti on s.Tol Fun and maximum con stra int violati on is less tha n op ti on s.TolC on.Active in equalities (to with in op ti on s.TolC on = 1e-006): lower2 ********in eqli n ineqnon li n9铰链四杆机构实现连杆轨迹的优化设计最优解upperan 机架长度 d = 51.7446 mm曲柄长度 a = 8.0000 mm连杆长度 b = 53.6230 mm摇杆长度 c = 25.4846 mm连杆附杆长度h = 22.6784 mm机架倾斜角beta = 11.4185 °连杆与附杆夹角gamma = 14.9999 °曲柄初始位置角theta0 = 50.0664 °M点轨迹坐标偏差f* = 1.9718机构最小传动角delta_min = 53.8751最优点的约束函数值最小传动角约束函数值g1* = -482.3881曲柄长度<=机架长度g2* = -43.7446曲柄长度<=连杆长度g3* = -45.6230曲柄长度<=摇杆长度g4* = -17.4846曲柄+机架<=摇杆+连杆g5* = -19.3631曲柄+连杆<=摇杆+机架g6* = -15.6062曲柄+摇杆<=连杆+机架g7* = -71.8830机架长度<=60 g8* = -8.2554曲柄长度>=8 g9* = 0.0000曲柄长度<=30 g10* = -22.0000连杆长度<=60 g11* = -6.3770摇杆长度<=40 g12* = -14.5154附杆长度>=10 g13* = -12.6784附杆长度<=30 g14* = -7.3216机架倾斜角>=-20 °g15* = -31.4185机架倾斜角<=30 °g16* = -18.5815连杆附杆夹角>=0 °g17* = -14.9999%铰链四杆机构实现连杆轨迹的优化设计 --目标函数文件---lgjg_gjyh_mb.mfun ctio n f=lgjg_gjyh_mb(x) %曲柄输入角增量Dtheta=[0,22,44,66,88,129,221,314]; %连杆上M 点给定的坐标 Sx=[26,23,20,17,13,10,20,30]; Sy=[16,17,17,16,15,11,6,12]; %目标函数 hd=pi/180;theta=x(8)+Dtheta;%曲柄输入角=初始角+角增量ep silo n=ata n(x(2).*si n((theta-x(6))*hd)/(x(1)-x(2).*cos((theta-x(6))*hd)));etaz=x(1)A2+x (2) ^2+x (3)^2-x (4) ^2-2*x(1)*x(2).*cos((theta-x(6))*hd); etam=2*x(3)*sqrt(x(1)A2+x (2)^2-2*x(1)*x(2).*cos((theta-x(6))*hd));eta=etaz./etam;p hi=x(6)+x(7)+eta-e psil on;Mx=x(2).*cos(theta*hd)+x (5) .*cos( phi*hd);My=x(2).*s in (theta*hd)+x (5).*si n(p hi*hd); f=sqrt(sum((Mx-Sx).A2+(My-Sy).A2)/8);%铰链四杆机构实现连杆轨迹的优化设计 fun ctio n [g,ceq]=lgjg_gjyh_ys(x)连杆附杆夹角<=15 曲柄初始角>=0 ° 曲柄初始角<=15 °g18* = -0.0001 g19* = -50.0664 g20* = -9.9336%凑整解的计算xz=[52,8,54,25,23,11.5,15,50]; fz=lgjg_gjyh_mb(xz);gz=lgjg_gjyh_ys(xz); delta_z=acos((xz(3)A2+xz(4)A2-(xz(1)-xz(2))A2)/(2*xz (3) *xz (4))); dis pI anfprintf (' fprintf (' if gz<=0dis p 'else铰链四杆机构实现连杆轨迹的优化设计凑整解M 点轨迹坐标偏差机构最小传动角f* = %3.4f delta_z= %3.4f ° 未a***、\n',fz)\n ',delta_z/hd)&&&&&&&&凑整解在可行域内 &&&&&&&&'dis p 'end&&&&&&&& 凑整解在可行域外&&&&&&&&'********铰链四杆机构实现连杆轨迹的优化设计凑整解M 点轨迹坐标偏差f* = 1.9989机构最小传动角 delta_z = 53.5270 &&&&&&&& 凑整解在可行域内********&&&&&&&&%连杆上M 点实际x 坐标 %连杆上M 点实际y 坐标 % M 点坐标偏差均方根值--约束函数文件---lgjg_gjyh_ys.m%机构最小传动角(40度)约束g(1)=x (3)A2+x(4)A2-(x(1)-x(2))A2-2*x (3) *x(4)*cos(40* pi/180); %曲柄存在条件约束 g(2)=-x(1)+x(2); g(3)=-x(3)+x(2); g(4)=-x(4)+x(2);g(5)=x(1)+x(2)-x(3)-x(4); % 曲柄 + 机架<= 摇杆 +连杆 g(6)=-x(1)+x(2)+x(3)-x(4); % 曲柄 + 连杆 <= 摇杆 +机架 g(7)=-x(1)+x(2)-x(3)+x(4); %曲柄+ 摇杆 <=连杆 +机架%边界约束g(8)=x(1)-60;% 机 架 <=60g(9)=8-x(2);g(10)=x(2)-30;%8 <=曲柄<=30g(11)=x(3)-60;%连; 杆 <=60g(12)=x(4)-40;%摇; 杆 <=40g(13)=10-x(5);g(14)=x(5)-30; g(15)=-x(6)-20;g(16)=x(6)-30; g(17)=-x(7);g(18)=x(7)-15; g(19)=-x(8);g(20)=x(8)-60; ceq珂];% 10 <=连杆附杆 <=30 % -20度 <=机架倾斜角% 0度 <=连杆附杆夹角 % 0度 <=曲柄初始角曲柄长度 曲柄长度 曲柄长度 <=机架长度 <=连杆长度 <摇杆长度<=30 度 <=15 度 <=60 度。
滚切剪曲柄连杆机构优化设计
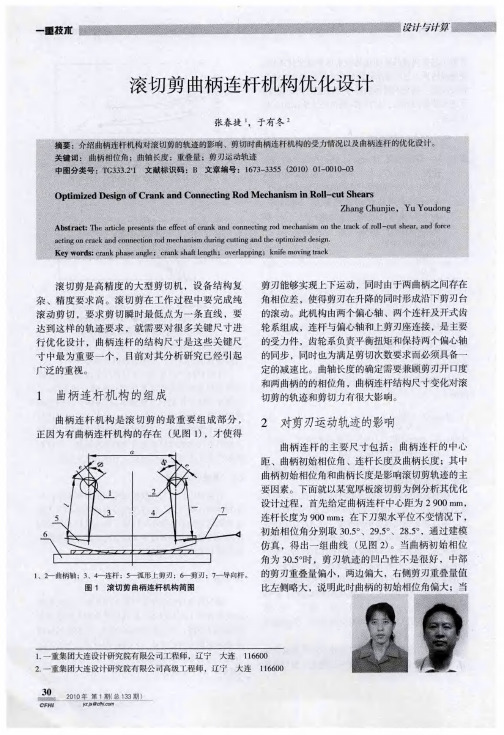
-
15 5 0 5 .62 E+ 0
| ’
L
水 力 平
1 f竖 力 直 I
I I
பைடு நூலகம்f
善47+5 _3E0 . O 5
-
7 1 7 E+ 0 .8 5 0 5 1O 0 . E+ 07 0 O . 2O 3 ( 4. . . ( 8 0 . 0. 1 2. . 1 O . . ) O 5 0 6 0 7. ) . 90 1 O l . l 0 O
一
量 技商
0
言 三 一 6
翻{
皋
蜜
一 9
—
2o 5o
一 0 ) 2( o
~l o 5o
—l D 00
—0 50
( )
50 0
l o ‘ Ⅺl
l OO 5
2)o ( o
2 o0 5
F 剪刃水平位置f m I ) I 】
图 3 曲柄 长度 对 剪 刃重 叠量 的 影 响
26 5 +0) .2 E ( 6
’ ●
,
/
『
J
力杆件。因此在设计滚切剪曲柄连杆机构时必须对 结构尺寸进行优化。在优化滚切剪的设计中,首先
要确 定 曲柄 连杆 的长度 和初始 向位角 ,比较简 便 的 方法是 参考 与设计 目标相 近规格 的滚切 剪 的结构 尺
’
弓 一 .5 + ( 92 E 0 6 )
不是很理想 ,中部的剪刃重叠量偏大,两边偏小 , 说明曲柄的初始相位角偏小 ;可当曲柄初始相位角 为 2.o ,滚 切 剪 的剪 刃 重 叠 量 的对 称 性 很 好 , 95时
剪 刃重叠 量 的误差 为 1 9 m,满 足 2m 的设 计 . 2m 6 m 要求 。由此 可见 ,曲柄 的初始 相位 角对剪 刃重 叠量
- 1、下载文档前请自行甄别文档内容的完整性,平台不提供额外的编辑、内容补充、找答案等附加服务。
- 2、"仅部分预览"的文档,不可在线预览部分如存在完整性等问题,可反馈申请退款(可完整预览的文档不适用该条件!)。
- 3、如文档侵犯您的权益,请联系客服反馈,我们会尽快为您处理(人工客服工作时间:9:00-18:30)。
令 : ) : I = 。 m , : , ) , ,
若满足
< J
通过对连 杆机构建 立数学模 型 ,在编程 过程 中用 约束优 化问题上 的内点惩罚 函数法和 P w l法 ,对 连杆机构进 行优 oe l 化设 计 。
参考文献 : 【 刘 惟 信 . 械最 优化 设 计 ( 二版 ) 】北京 : 华 大学 出 版社 , 1 】 机 第 [. M 清
’
) 2 =2
一 )
特殊 地在编 程计 算过程 中 , 令加权 因子 W 1 得 目标 函 =, 数式/( , 1 详见后 附程序 中的 目标函数子程序。 )
收稿 日期 :0 9 1— 2 20 — 2 1 作者简介 : 黎毓鹏( 9 1 )男 , 17 一 , 广西南宁人 , 工程师 , 从事教学及 科研 工作。
,
且转动角(1 l的夹角 ) f和 , 的最大最小值为
≤ 1 5。 , ≥ 4 3 y咖 5。
一 … ~
一
要 以给定 的运动和实 际运 动规律 问的偏差最 小为追求 目
标 。对于该问题 , 建立数学模型如下所述。
∞y ■ — — — ~
g 3 ,( ) 5 。 ( )g 4 , ) (
z fz +2c( 手 2zo +一 s )
——一
≤O
在编程计算 中以上五式分别构成约束 条件式 g 1 ,( ) ( )g 2 ,
4 对 求解 结果 的总 结分 析
图 1 连杆机构
此次 编程过程 中 ,分别用到 了约束优 化问题的问接解法
和直接解法 。现对 内点惩罚 函数法 和复合 形法 的计算步骤和
二
3 约束 条 件 的建立
曲柄连杆机构 的杆长限制条件
f+f ] 。 ’ 一厶≤ 0 f+f 一 一厶 0 f+厶一f一1 ≤ 0 一f ,l 3 ≤ , l ’ 3
律运动 :
^
= + 一 一 ) 。 — ( 0 J
曲柄连杆机构 的角度限制条件
2 Z2 ,
中图分类号 : H 1 T I2
文献标识码 : A
文章编 号: 6 2 5 5 ( 0 0 0 — 0 6 0 17 — 4X 2 1 3 03 — 2 J
如图 1 所示连杆机构, 预先给定机架 2 曲柄 2由极限角 。 , ,
转到 = + 时 , ‰ 要求摇杆 f由极限角 开始按如下规 ]
3 6
《 装备制造技术 ̄ oo 2 l 年第 3 期
方 向 进 行 一 维 搜 索
i l X + q 一 l
:
方 向全 用第 轮 的搜 索方 向 ,初始点则 取 和
“
中函数
i 2 … ' n ’ :1 ,一, 1 ' n
,
值较小 的点 。 () 5 收敛条件为
19 9 4.
.
I 2+ ) △) . l 一 (一 一 )o△ (一) ( :<5 。
则 由 出发沿 ㈣ 向进行一维搜 索 求 出该方 向最小点 方
,
’
,
并 以 ‘ 作为 k+ 轮 的初 始点 , 1 然后 进行第 k l 的搜索 , +轮
E up n Ma u a t n e h o o y No 3 2 0 q i me t n f cr gT c n lg . , 01 i
连杆机构 的优化设计
黎毓 鹏 , 陆静 平 , 炳琼 , 铁异 , 咏春 黄 张 宋
( 广西大学 机械工程学院 , 广西 南宁 5 00 3 04)
则转下步。
() 。 3步
I
若不等式成 立 , 则认为求得 最优点 一 (∞)若不 成立 r , () 5 计算 , =c^并令 l= ( , ) 一 , 田 =后+1后转向 4 第 1 42 P w l 求最优点 的计算步 骤和 结果分析 . o el 法 () 1 给定初始点 ‰和计算精度 8 逐次沿 n , 个线 性无 关的
摘 要: 以一个四连杆 机构作为 实例 , 立足编程 的需要 , 对在 约束优化 问题 上的 内点 惩罚函数 方法和 P w l方法进行 了多方 面的探 oe l
讨 , 而 达 到 了 连杆 机 构优 化设 计 的 目标 。 从
关键词: o l法 ; P we l 目标 函数 ; 约束条件 ; 设计 变量
( ) 算 k轮 中相邻二点 目标 函数值 的下 降量 , 找 出下 2计 并
降量最大者及相应方 向
△= a J :m _ x i
一C) s s i ,
l s { m。 l0 或 :I )I 一≤
5 . 语 结束
l. ≤ s :
() 3 沿共 轭方向 : ’X 计算反射点 : 一 n - O
2 目标 函数 的 建立
将 杆 件 1 杆 件 3的 转 角 均 分 为 1 分 , 有 和 0等 则
() 4 检验精度
斋 1,,; = ,1,, =2 1 砉 ,…1 ,… 0 2 0
故而确定优化设 计的 目标 函数 为
l 0
' 一
— — 一
I( ) ) , ) l l - I
1 设 计 变量 的选取
若取 厶定值单位 1 连杆 机构 的运 动状态和尺寸可由杆 长 ,
l, 和角度 , 完全确定 。由此优化设计变量可以定 为 。, l
程序框图总结如下 :
41 内点惩罚 函数法 的计算步骤和结果分析 . () 1 选初始 点 , 此点应 满足 甑∽ <0( Ⅱ=12 … , , , , m)
但不应在边界上 ; () 2 选适 当的惩罚 因子初始 值 , 降低 系数 c 计算 精度 , 8 和 s, l !并令 k=0 ; () 3 构造惩罚 函数 , 调用方法 , 求每次迭代 的 m n ( ) it , b 和 ( k最优点 ; 一 )
X 【 ,,, I [ , , , : zl T ] 。。 = 。!,