连铸机结晶器铜板简介及影响寿命因素
连铸结晶器铜板磨损原因分析

连铸结晶器铜板磨损原因分析2009-10-18 01:35连铸结晶器铜板磨损原因分析结晶器是整个连铸工艺的核心设备,直接影响到连铸的生产率、产品质量和生产成本。
在生产过程中,结晶器要不断地经受高温、高压和强磨擦的冲击,工作环境极其恶劣。
了解结晶器的磨损原因对于结晶器的设计和使用具有重要意义,这里对结晶器的磨损机理进行简要介绍。
1、结晶器的铜板裂纹结晶器的弯月面区域常有铜板裂纹出现,主要原因是铜板表面温度提高引起的极高的热流量,在此高温下,相对于钢质支持设施而言铜板趋向于膨胀。
尤其是对薄板坯连铸结晶器而言更是如此,由于拉坯速度快,铜板表面温度快速升高,铜板所承受的温度超过了其恢复再结晶温度,从而使其强度和硬度大大降低,使漏斗形过渡区经历了一个明显的3维膨胀运动。
这个热应变和机械应变组合加上硬度的下降(可达50%),导致了铜板表面裂纹的出现,而且裂纹倾向于以晶间方式进一步传播。
浇铸过程中过高的热量水平和由此而产生的结晶器铜板表面和亚表面区域的宏观塑性应变/形变,是导致结晶器弯月面处产生裂纹的主要原因。
这种损坏机理又受到极高温度区域的强化。
例如,从结晶器漏斗型区到结晶器平行区的过渡区域。
这时,结晶器热面和冷面之间的局部温度梯度可达到数百摄氏度。
结晶器铜板工作侧表面(热面)或多或少都要承受扩散的影响,钢水中的Zn、S、Cd和保护渣中的F都要扩散到铜板的表面和亚表面。
这些扩散元素会导致结晶器铜板的热脆性,导致裂纹的形成和扩散。
裂纹损坏的关键因素就是结晶器所经受的最高温度和结晶器服役时间。
当高速连铸时,结晶器材质经受超高温的另一个影响效应就是结晶器铜板发生塑性应变,导致弯月面下铜板变形,以及由于钢水内的Zn扩散到铜板中形成黄铜,即发生所谓的“黄铜化”现象。
后一个问题对于电炉钢厂或短流程轧钢厂问题尤为突出,因为电炉钢厂或短流程轧钢厂通常是利用废钢炼钢的。
黄铜的形成使得结晶器铜板产生热脆性,加之很高的工作温度而引起的应力,使结晶器铜板产生裂纹。
结晶器铜板使用寿命影响因素分析和改进措施
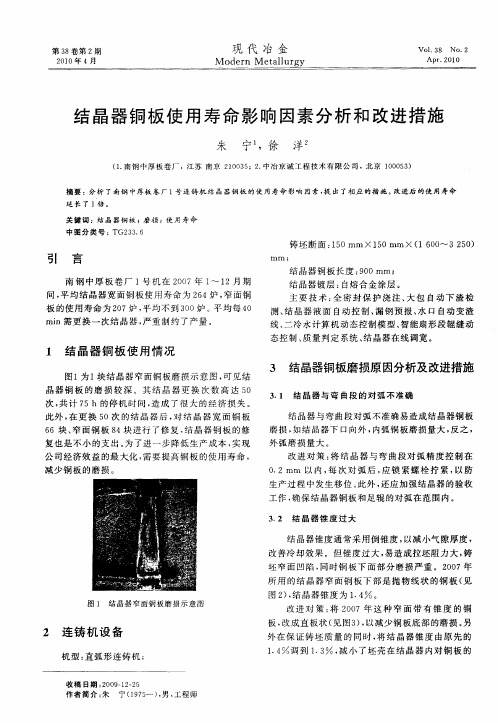
结 晶器锥 度通 常采用倒 锥度 , 以减小气 隙厚度 ,
改善冷 却效果 。但锥度 过大 , 易造成拉 坯阻力 大 , 铸
坯 窄面 凹陷 , 同时铜 板下 面部分磨 损严 重 。2 0 0 7年 所用 的结 晶器窄 面铜 板 下部 是抛 物 线状 的铜 板 ( 见 图 2 , 晶器锥 度为 1 4 。 )结 .
铸 坯 断 面 :5 1 0mmx 】 0mi x ( 60 32 0 5 l 1 0  ̄ 5 ) l
引 言
南 钢 中厚 板 卷 厂 1号 机 在 2 0 0 7年 1 1 ~ 2月 期 间 , 均结 晶器宽 面铜板使 用 寿命 为 2 4 , 面铜 平 6 炉 窄
nl I : Il
() 2 全程 进行 保 护 浇 注 , 好 大包 盖 、 好 保 护 盖 套
套管, 中间包 内确 保有 足够 的覆 盖剂 , 证 中包 的温 保 度 波动 范 围在 1 。 。 O C内 () 3 控制 循环使 用 的钢包 个数 , 减少 温降 。
3 5 铜 板 镀 层 不 正确 无 误 , 取 了 以下 二 项 措 采 施 : 1 每 逢 停 机 用 锥 度 仪 在线 测 量 结 晶器 的 倒 锥 ()
减小 波动 。 用 长时间 未用 的钢 包时 , 高精 炼炉 的 使 提 吊包 温度 , 保 温差变 化不 大 。 确
度 , 保 参 数合 适 ;2 窄 边 固定 不 紧或 铜 板 下 部 磨 确 () 损会 造成 铸 坯尺 寸变 化 , 因此 要 求 协力 单 位 在 维 修 时必须 把窄 面 的螺栓 固定 死 。
铜 板镀 层 质 量不 良 , 层 硬度 在 高 温下 将显 著 表
下 降 , 板耐用 度也 随之 降低 。 铜 连铸 结 晶器铜板 表 面
济钢三炼钢连铸结晶器寿命影响因素分

济钢三炼钢连铸结晶器寿命影响因素分刁承民李殿明王庆济钢第三炼钢厂摘要:结晶器是连铸机的心脏,阻碍结晶器寿命的因素有驱动报警、角部纵裂、铜板镀层脱落等缘故,依照显现的不同情形制定预防措施,大大提高了结晶器的使用寿命。
1.前言炼钢现有连铸机3台,2005到2006年由于生产任务重,节奏紧张,结晶器寿命大幅度降低,暴露出专门大的问题,还引发了几次漏钢的恶性事故。
结晶器频繁的更换,给生产带来极大的被动。
本文针对结晶器使用寿命低的问题进行了深入的分析,并制定了一系列的措施,结晶器寿命大幅度提高。
2.阻碍结晶器寿命的要紧缘故及预防措施表1为2005年9月到2006年9月一年之间1#铸机结晶器更换缘故统计表。
能够明显的看出造成结晶器寿命低要紧有驱动报警、热电偶、角裂等缘故。
表1结晶器更换缘故统计另外2,3#铸机在2006年3月到5月期间,因为结晶器弯月面小纵裂,镀层脱落更换结晶器20台,并造成3次漏钢事故,极大的阻碍了生产。
2.1驱动报警2.1.1 引起驱动报警的因素换包过程中油缸驱动报警L1机操纵显示见图1。
引起驱动报警的要紧缘故是:①换包时刻长,侧面收缩大,钢水下渗造成挤压;②宽面夹紧弹簧(见图2)使用时刻长,预紧力不够,弹簧失效。
驱动报警后,结晶器窄变倒锥度直和结晶器下口宽度要发生相应的变化,偏离实际设定值,结晶器调宽系统要对此进行自动调整。
调整后的值假如与实际设定值的偏差较大时,连续浇铸可能会带来漏钢事故的发生,对此要进行相应的降拉速甚至被迫停浇,给正常生产带来专门大的不便。
图1 驱动报警L1机操纵显示图2宽面夹紧弹簧及相应的预紧力2.1.2 驱动报警问题的解决针对结晶器驱动报警问题的发生,进行了以下改进措施:2.1.2.1改进操作,制定预案操作的改进要紧有以下十条:(1)快换中包时,钢包到站温度适当提高,钢水等铸机时刻不得过长,且钢包为包况良好的周转包。
(2)确保中间包、塞棒及水口烘烤情形良好,换包前再检查调整塞棒,检查正常后,将新中间包开至预定位置。
连铸圆坯结晶器

连铸机结晶器总成1、结晶器总成组合式结晶器由结晶器本体、支撑框架以及足锟等部件组成。
结晶器本体由4块铜板及支撑板组合而成,用螺栓连接为一体;支撑框架带有定位、固定装置和冷却水通道;足锟包括支架、锟子、轴承、水管和喷嘴等。
组合式结晶器可以配置液位检测装置、外置式电磁搅拌装置。
2、结晶器结构特点A、结晶器本体两块弧面铜板和两块侧面铜板组合成结晶器内腔,铜板上加工有若干冷却水槽(即水缝),用螺钉将铜板与支承板(也称为背板)连接。
支承板上设有冷却水通道,冷却水从振动台上的供水孔进入支撑框架再进入支承板,再通过支撑框架流回到振动台上的回水孔。
设计时,需要根据冷却水压强核算螺钉连接的受力及强度,并调整连接螺钉数量,直至满足要求。
一般情况下,两排螺钉之间布置5~6条水缝。
结晶器内腔角部的倒角一般采用早弧面和侧面铜板的结合部位垫有带45°斜面的铜质垫板形成;也有直接在侧面铜板上加工出倒斜角斜面的。
铜板厚度一般为45~50mm,主要取决于水缝深度和再加工要求。
可采用的材质有Cu—Ag和Cu—Cr—Zr。
如果连铸机拉速不高,相应铜板热面温度不超过250℃,可以采用Cu—Ag。
随着连铸技术发展和操作水平提高,连铸机拉速也相应提高,结晶器铜板有必要采用Cu—Cr—Zr合金,可以满足热面温度为350℃甚至更高的工况。
目前,国内方坯结晶器铜板次用Cu—Ag和Cu—Cr—Zr的都有,采用Cu—Cr—Zr的日趋增多。
为了提高结晶器使用寿命,铜板都会经过表面处理,即镀层。
典型的镀层材料有Cr、Ni、Ni—Fe、Ni—Co、Co—Ni。
Cr的硬度高,督促呢个化学稳定性好,但Cr与Cu的线膨胀系数差距较大,镀层结合力差,镀层易剥落。
Ni与Cu的结合力好,但其镀层硬度相对较低,高温耐磨性差。
现已很少采用单独镀Cr或Ni得铜板。
Ni—Fe、Ni—Co、Co—Ni都有硬度高、耐磨性好的特点,其中Ni—Fe的化学稳定性较差,其镀层韧性随着硬度增加会降低;Ni—Co的抗热交变性稍差;Co—Ni的材料成本较高。
炼钢二厂板坯连铸机结晶器铜板制造工艺优化
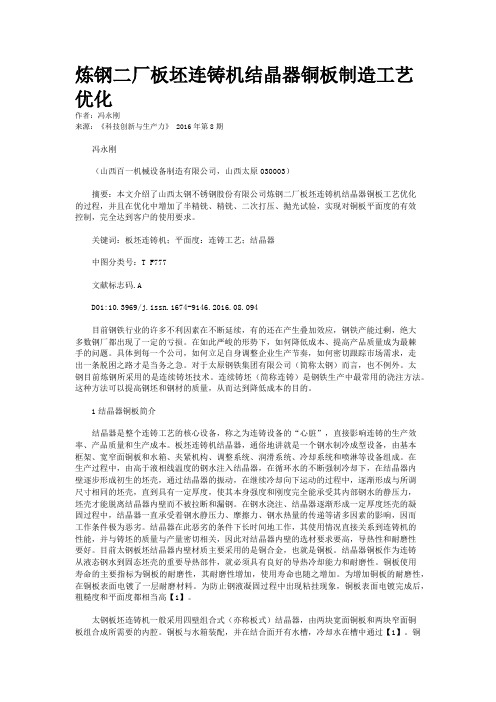
炼钢二厂板坯连铸机结晶器铜板制造工艺优化作者:冯永刚来源:《科技创新与生产力》 2016年第8期冯永刚(山西百一机械设备制造有限公司,山西太原030003)摘要:本文介绍了山西太钢不锈钢股份有限公司炼钢二厂板坯连铸机结晶器铜板工艺优化的过程,并且在优化中增加了半精铣、精铣、二次打压、抛光试验,实现对铜板平面度的有效控制,完全达到客户的使用要求。
关键词:板坯连铸机;平面度:连铸工艺;结晶器中图分类号:T F777文献标志码.AD01:10.3969/j.issn.1674-9146.2016.08.094目前钢铁行业的许多不利因素在不断延续,有的还在产生叠加效应,钢铁产能过剩,绝大多数钢厂都出现了一定的亏损。
在如此严峻的形势下,如何降低成本、提高产品质量成为最棘手的问题。
具体到每一个公司,如何立足自身调整企业生产节奏,如何密切跟踪市场需求,走出一条脱困之路才是当务之急。
对于太原钢铁集团有限公司(简称太钢)而言,也不例外。
太钢目前炼钢所采用的是连续铸坯技术。
连续铸坯(简称连铸)是钢铁生产中最常用的浇注方法。
这种方法可以提高钢坯和钢材的质量,从而达到降低成本的目的。
1结晶器铜板简介结晶器是整个连铸工艺的核心设备,称之为连铸设备的“心脏”,直接影响连铸的生产效率、产品质量和生产成本。
板坯连铸机结晶器,通俗地讲就是一个钢水制冷成型设备,由基本框架、宽窄面铜板和水箱、夹紧机构、调整系统、润滑系统、冷却系统和喷淋等设备组成。
在生产过程中,由高于液相线温度的钢水注入结晶器,在循环水的不断强制冷却下,在结晶器内壁逐步形成初生的坯壳,通过结晶器的振动,在继续冷却向下运动的过程中,逐渐形成与所调尺寸相同的坯壳,直到具有一定厚度,使其本身强度和刚度完全能承受其内部钢水的静压力,坯壳才能脱离结晶器内壁而不被拉断和漏钢。
在钢水浇注、结晶器逐渐形成一定厚度坯壳的凝固过程中,结晶器一直承受着钢水静压力、摩擦力、钢水热量的传递等诸多因素的影响,因而工作条件极为恶劣。
连铸结晶器提升在线使用寿命
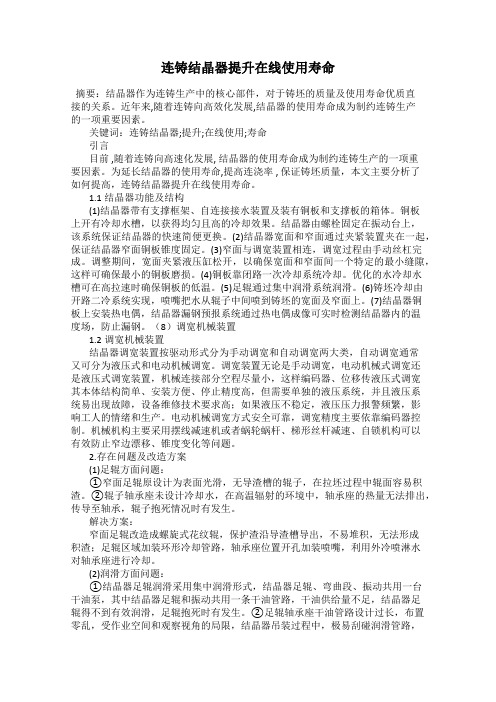
润滑站增加一台油泵,把结晶器、弯曲段、振动润滑系统分离,由一台干油泵给结晶器独立供油,保证油量充足;缩短油管长度(由1250mm改成900mm),规范布置,避开容易剐蹭的位置利用管夹固定,极大降低了吊装结晶器过程中的剐蹭机率。
(3)结晶器跑锥问题:
结晶器的锥度是结晶器的一个重要参数,不同钢种、不同断面对应不同的锥度,合适稳定的锥度,锥度过大,增大拉坯阻力,增大铜板的磨损,降低铜板使用寿命,锥度过小,拉坯过程中可能造成铸坯鼓肚,进而产生裂纹。窄面锥度设定通过调整结晶器上下蜗轮蜗杆减速机,锁定位置,保证锥度。生产过程中受热坯压力的影响,再加上锥度调整装置老化,前期跑锥现象频发,经常造成生产拉下和铸坯质量事故。
2.存在问题及改造方案
(1)足辊方面问题:
①窄面足辊原设计为表面光滑,无导渣槽的辊子,在拉坯过程中辊面容易积渣。②辊子轴承座未设计冷却水,在高温辐射的环境中,轴承座的热量无法排出,传导至轴承,辊子抱死情况时有发生。
解决方案:
窄面足辊改造成螺旋式花纹辊,保护渣沿导渣槽导出,不易堆积,无法形成积渣;足辊区域加装环形冷却管路,轴承座位置开孔加装喷嘴,利用外冷喷淋水对轴承座进行冷却。
1.2调宽机械装置
结晶器调宽装置按驱动形式分为手动调宽和自动调宽两大类,自动调宽通常又可分为液压式和电动机械调宽。调宽装置无论是手动调宽,电动机械式调宽还是液压式调宽装置,机械连接部分空程尽量小,这样编码器、位移传液压式调宽其本体结构简单、安装方便、停止精度高,但需要单独的液压系统,并且液压系统易出现故障,设备维修技术要求高;如果液压不稳定,液压压力报警频繁,影响工人的情绪和生产。电动机械调宽方式安全可靠,调宽精度主要依靠编码器控制。机械机构主要采用摆线减速机或者蜗轮蜗杆、梯形丝杆减速、自锁机构可以有效防止窄边漂移、锥度变化等问题。
结晶器铜管长寿命镀层镍钴铁合金

结晶器铜管长寿命镀层镍钴铁合金结晶器铜管是连铸机上的核心部件,承担着钢水凝固成型的作用,结晶器铜管质量的好坏不仅对铸坯产量、质量有很大的影响,而且对铜管本身的使用寿命影响更大。
在连铸生产过程中,结晶器铜管内表面的镀层与高温的钢水相接触,受到钢水的化学腐蚀,热侵蚀以及与坯壳之间的摩擦等综合的影响,结晶器铜管容易发生热变形,以及表面镀层的划伤,影响了连铸机的正常运行,降低了连铸效率,恶化了铸坯的质量。
由于铸坯的钢种与连铸机的工艺参数不同,结晶器铜管的使用寿命也不同。
提高结晶器铜管的使用寿命,是提高连铸机工作效率的唯一途径。
国内许多结晶器铜管生产厂家一直在围绕如何提高结晶器铜管使用寿命上进行长时间的探索。
在铜管内腔锥度的设计方面:结晶器铜管锥度从单锥度发展到多锥度、抛物线曲面等等。
在铜管原料的选择方面:从纯铜、磷铜发展到银铜及铬锆铜。
从而在热导性能、抗变形能力及使用寿命方面均有提高。
但在结晶器铜管内腔的镀层方面却始终没有多大的改进.目前,国内外许多结晶器铜管生产厂家,在结晶器铜管内表面处理上,仍然是采用镀硬铬这一传统工艺。
镀铬层虽然硬度较高,耐磨性能良好,但镀层较薄。
镀铬层本身存在微裂纹,另外,铬与铜的热膨胀系数相差很大,在高温状态下使用会出现横向裂纹。
在连铸生产过程中,由于钢水中的Zn、S、Cd及F经镀铬层的裂纹缝隙扩散到铜管的表面上,结晶器铜管基体出现了热脆性现象,使结晶器铜管基体表面形成大量的微裂纹,导致镀铬层的裂纹进一步扩大。
另外,结晶器铜管镀铬层是阳极镀层,在钢水长时间的化学腐蚀、热侵蚀的影响下,镀铬层会出现粉化及脱落现象,其耐磨性能大幅度下降,在铸坯过程中镀铬层很快被磨损掉,所以铬镀层的耐磨性能是很有限的,使用寿命比较短。
以断面为150mm×150mm的方坯为例:过钢量只有3500—4500吨左右,吨钢成本比较高。
结晶器铜管复合镀层----为了提高铬镀层的耐磨性能,延长结晶器铜管的使用寿命,将0.4—0.5mm厚的镍钴合金镀层,加入结晶器铜管内表面与镀铬层之间,作为过渡层。
常规板坯连铸机结晶器技术

常规板坯连铸机结晶器技术结晶器是连铸机中的铸坯成型设备, 是连铸机的核心设备之一。
其作用是将连续不断地注入其内腔的钢液通过水冷铜壁强制冷却,导出钢液的热量,使之逐渐凝固成为具有所要求的断面形状和一定坯壳厚度的铸坯,并使这种芯部仍为液相的铸坯连续不断地从结晶器下口拉出,为其在以后的二冷区域内完全凝固创造条件。
在钢水注入结晶器逐渐形成一定厚度坯壳的凝固过程中,结晶器一直承受着钢水静压力、摩檫力、钢水热量的传递等诸多因素引起的的影响,使结晶器同时处于机械应力和热应力的综合作用之下,工作条件极为恶劣,在此恶劣条件下结晶器长时间地工作,其使用状况直接关系到连铸机的性能,并与铸坯的质量与产量密切相关。
因此,除了规范生产操作、选择合适的保护渣和避免机械损伤外,合理的设计是保证铸坯质量、减小溢漏率、提高其使用寿命的基础和关键。
板坯连铸机一般采用四壁组合式(亦称板式)结晶器,也有一个结晶器浇多流铸坯的插装式结构。
结晶器主要参数的确定1 结晶器长度H结晶器长度主要根据结晶器出口的坯壳最小厚度确定。
若坯壳过薄,铸坯就会出现鼓肚变形,对于板坯连铸机,要求坯壳厚度大于10~15mm。
结晶器长度也可按下式进行核算:H=(δ/K)2Vc+S1+S2 (mm)式中δ——结晶器出口处坯壳的最小厚度,mmK——凝固系数,一般取K=18~22 mm/min0.5Vc——拉速,mm/minS1——结晶器铜板顶面至液面的距离,多取S1=100 mmS2——安全余量,S=50~100 mm对常规板坯连铸机可参考下述经验:当浇铸速度≤2.0m/min时,结晶器长度可采用900~950mm。
当浇铸速度2.0~3.0m/min时,结晶器长度可采用950~1100mm。
当浇铸速度≥3.0m/min时,结晶器长度可采用1100~1200mm。
2 结晶器铜板厚度h铜板厚度的确定是依据热量传热原理和高温下的使用性能,具体说,与铜板材质、镀层、机械性能、拉速、冷却水量的大小和分布等有关。
- 1、下载文档前请自行甄别文档内容的完整性,平台不提供额外的编辑、内容补充、找答案等附加服务。
- 2、"仅部分预览"的文档,不可在线预览部分如存在完整性等问题,可反馈申请退款(可完整预览的文档不适用该条件!)。
- 3、如文档侵犯您的权益,请联系客服反馈,我们会尽快为您处理(人工客服工作时间:9:00-18:30)。
连铸机结晶器铜板简介及影响寿命因素
作者:王腾飞戴昭颖张博
来源:《科学与财富》2015年第23期
摘要:本文简要介绍了京唐公司连铸机结晶器铜板的作用及镀层材质情况,并结合实际生产总结影响结晶器铜板寿命的因素及改进措施。
关键词:连铸机结晶器铜板;镀层材质;寿命
前言:
结晶器是连铸机的关键部件,铜板是结晶器的核心部件,钢水通过结晶器铜板向外导出热量而使钢水凝固结晶成一定厚度的坯壳,铜板在此过程中承受着高低温度产生的热应力、高温热膨胀带来的塑性变形、冷却收缩时带来的巨大拉应力、钢坯与铜板相对运动产生的摩擦力,这就要求结晶器铜板必须具有较高的热传导性,较高的抗拉强度,较高的再结晶温度,软化温度,热强性以抵抗变性,热疲劳能力,同时要有抵抗磨损的能力,提高过钢量,因此结晶器铜板在连铸过称中起到不可或缺的作用,提高结晶器铜板寿命更是降低炼钢成本的重要工作之一。
1 结晶器作用及其要求
结晶器是连铸机的核心,其作用是将连续不断地注入其内腔的钢液通过水冷铜板强制冷却,导出钢液的热量,使之逐渐凝固成为具有所需要求的断面形状和一定均匀厚度的坯壳,并使这种芯部为液相的铸坯连续不断地从结晶器下口拉出,为其在二冷区域内完全凝固创造条件。
钢水在结晶器中的凝固对铸坯表面质量和铸机的正常生产有着重大影响,在高温钢水注入结晶器,逐渐形成一定厚度坯壳的凝固过程中,结晶器铜板一直处于钢水与冷却水的静压力、高温氧化、冷热疲劳产生的热裂纹、温度梯度大产生变形、冷却水和保护渣成份的化学腐蚀、高温蒸汽的侵蚀,引锭、拉坯、振动产生的摩擦、磨损和调锥宽导致的擦痕等诸多损伤。
(1)良好的导热性,能使钢液快速凝固。
每1Kg钢水浇注成坯并冷却到室温,放出的热量约为1340KJ/Kg,若板坯尺寸为250×1700mm,拉速为1m/min,结晶器每分钟带走的热量多达20万KJ。
而结晶器长度又较短,一般不超过1m,在这样短的距离内要能带走大量的热量,要求它必须具有良好的导热性能。
若导热性能差,会使结晶器的铸坯壳变薄,为防止拉漏,只好降低拉速,因此结晶器具有良好的导热性是实现高拉速的重要前提。
(2)较高的高温强度。
铜板不仅在常温下要有较高的强度,在200~300℃(连铸过程中铜板温度)这样的温度下,仍要保持在实现热量传导的同时保持良好的机械性能,不出现再结晶软化,不出现明显的塑性变形,扇形变形要小。
且铜板内壁与高温金属接触,外壁通冷却
水,而其壁厚较薄,在厚度方向温度梯度较大,热应力高,铜板必须具有较大的刚度,以适应高热应力。
(3)较好的高温耐磨性。
结晶内部液态金属凝结为固态坯壳,具有一定的硬度,在震动装置的作用下,以一定速度移出,与铜板的表面产生摩擦、磨损、划伤,为保持铸坯形状、质量、耐用,必须具有高温条件下的良好的耐磨性。
(4)良好的工艺性能。
易加工制造保证质量,装拆和调整方便。
(5)较好的性能价格比。
2 结晶器铜板镀层材质
目前京唐公司采用的NiCo合金镀层,此种镀层性能优越,抗拉强度310-450Mpa,延伸度为10-20%,宽面硬度为HV400,窄面硬度为HV220,热导率为80W/(m.k)。
NiCo合金镀层特点为:由于Co原子从体积上更接近Ni原子,因而镀层内部应力较小,与母材结合效果相对改善。
(1)镀层中Co离子在高温使用中析出,产生一种有CoO的玻璃质氧化薄膜(也有称之为陶瓷层),随着铜板的受热和温度的上升,表层陶瓷层逐渐加厚,这种陶瓷层增加钢水的滑动性,具有更好的耐磨性与抗氧化性。
陶瓷层也避免了生产中发生的钢水飞沫的粘结现象。
(2)高温强度好,即使铜板表面温度高达500℃以上,硬度下降幅度较小,正常拉钢时也基本能保持常温性能,也能形成稳定的高硬度与耐磨表面层。
(3)动摩擦系数比其它金属低,因此可以降低结晶器在振动时的铜板与铸坯之间的振动阻抗,利于拉钢。
3 结晶器的寿命的影响因素
结晶器的寿命,京唐公司采用结晶器浇注铸坯的吨数来确定。
在一般操作条件下,一个结晶器可浇注板坯9万吨,即600炉左右。
影响结晶器寿命的因素很多,正确选择结晶器内壁的材质是延长结晶器寿命的关键。
由于结晶器内壁直接与高温钢水接触,要求其内壁材质导热系数要高,膨胀系数要低,在高温钢水接触,要求其内壁材质导热系数要高,膨胀系数要低,在高温下有足够的高温强度和耐磨性,还要塑性好易加工。
目前CoNi铜板能满足这一要求,是做结晶器内壁比较理想的材料。
另外,结晶器的冷却水要求使用无宏观悬浮物的净水,水压不宜过大,结晶器倒锥度选得愈大,下部磨损也愈严重。
结晶器的断面越大,长度越大,寿命也就愈低。
结晶器下面导辊的对中精度,以及二次水冷强度和结晶器振动方式都对结晶器寿命有影响。
结晶器内腔尺寸的变形、表面的粗糙程度,角部的裂缝大于0.3mm,底部厚度磨损超过1.5~2mm等,这些因素足以引起产品的缺陷时,就要将结晶器拆下,对铜板进行加工修复,同时必须清除水垢。
结晶器窄边的寿命通常比宽边低,一般窄边在浇注到9万吨之后要重新加工修复。
弧形结晶器内外弧沿弧线的不平行度误差超过0.4mm时,也应将其拆下修理。
连铸机拉速提高后出现了结晶器内外弧铜板裂纹以及镀层脱落等问题出现,如图1,经查看铜板表面镀层剥落位置,距上口65~80mm之间,距铜板左侧位置340~420mm之间。
剥落共计4处,大小为10mm×5mm矩形状,主要由于钢液面位置为65mm过高,导致传热效率较低所致。
这种情况容易导致镀层产生疲劳性裂纹,进而导致剥落,尤其易发生在宽面和窄面配合区域。
图1 京唐公司连铸3#机结晶器铜板镀层脱落
4 结论
随着京唐公司产能的不断提高,提高连铸机拉速的要求日益迫切,尤其是连铸3#、4#机1580*248mm以下的小断面,0.8m低拉速不仅仅影响为下游热连轧的供料,而且造成了拉钢周期长、转炉钢水富余量增加的不匹配问题。
通过技术攻关将3#、4#连铸机的小断面工作拉速提高至1.8m以上,高拉速下连铸机结晶器对铜板及其镀层的要求更高,根据京唐公司结晶器铜板目前使用情况,总结出结晶器延长寿命的主要经验是:
(1)结晶器冷却水:水质硬度应小于3度,进出水温差控制在4~8度。
(2)提高足辊和二冷1段导辊的对弧精度。
(3)根据铜板的新老程度、结合中间包钢水温度,控制适当的拉速。
(4)在铜板设计时,冷却水槽位置距铜板上口有一定距离,因此浇铸过程中,液面过高易导致铜板上口不能够充分有效冷却;保护渣的堆积、渣线过高等原因,导致铜板表面镀层产生烧结、裂纹,最终剥落,严重影响铜板寿命及产能的提高。
建议钢液面保持在80~100mm 以下,特别是在高拉速的工作条件下,特别要注意这些事项。
(5)建立结晶器铜板的档案,定期检修或更换。
■
参考文献
(1)张富强.中薄板坯高拉速连铸结晶器平均热流研究 [J]. 钢铁,2002,37(12):19
(2)蒋丽敏.热解析技术在结晶器铜板上的应用.冶金科技,中国钢铁新闻网
(3)李广海.板坯连铸结晶器内钢水流场和传热凝固数值模拟[J].钢铁研究学报,2007,19(12):21.
作者简介:
王腾飞(1987.11-16):男,汉族,河北唐山人,大学本科学历,首钢京唐钢铁联合有限责任公司公司,助理工程师,主要从事炼钢技术工作。