表面热处理零件有效硬化层、渗层等的有关说明
热处理技术条件在零件图上的表示方法

热处理技术条件在零件涂上的表示方法1总则1.1 由效硬化层深度代号为:表面淬火回火——DS;渗碳或碳氮共渗淬火回火——DC;渗氮——DN。
1.2 技术要求中硬度和有效硬化层深度的指标值可用以下三种方法表示:a)一般采用:标出上、下限,如60~65HRC,DC=0.8~1.2;b)也可采用:偏差表示法,如600+5HRC,DC=0.8+0.40;c)特殊情况可只标下限值或上限值,如不小于50HRC,不大于229HRS。
1.3 复杂零件或其它原因技术要求难以标注,文字也难以表达时,则需另绘标注热处理技术要求的图。
2 正火、退火、淬火回火零件2.1 正火、退火、淬火回火零件标注硬度要求一般用布氏硬度(GB/T231)、洛氏硬度(GB/T230)表示,也可以用其它硬度表示。
2.2 局部热处理零件需将有硬化要求的部位在图形上用点划线框处。
轴对称零件或在不致引起误会情况下,也可用一条粗点划线画在热处理部位外侧表示。
3表面淬火零件3.1 表面淬火的表面硬度可用维氏硬度(GB/T4340)、表面洛氏硬度(GB/T1818)、洛氏硬度(GB/T230)表示。
但标准包括两部分:硬度值和相应的试验力。
如620~780HV30。
试验力选取与最小有效硬化层深度有关。
3.2 有效硬化层深度的标注包括三部分:深度代号、界限硬度值和要求的深度。
界限硬度只可根据最低表面硬度值按表选取,特殊情况,也可采用其它商定界限硬度值。
同样需在DS后标明。
如:620~780 HV30 DS500=0.8~1.6 (范围表示法)。
4 渗碳和碳氮共渗零件渗碳和碳氮共渗后淬火回火的零件的表面硬度,通常用维氏硬度或洛氏硬度表示。
对应的最小的有效硬化层深度和试验力与表面淬火零件相同。
其有效硬化层深度DC的表示法与DS基本相同,只是它的界限硬度值是恒定的,通常取550HV1,而且标注时一般可省略,特殊情况下可不采用此值,此时DC后必须注明商定的界限硬度值和试验力。
钢的渗碳硬化层有效深度的测量和检验
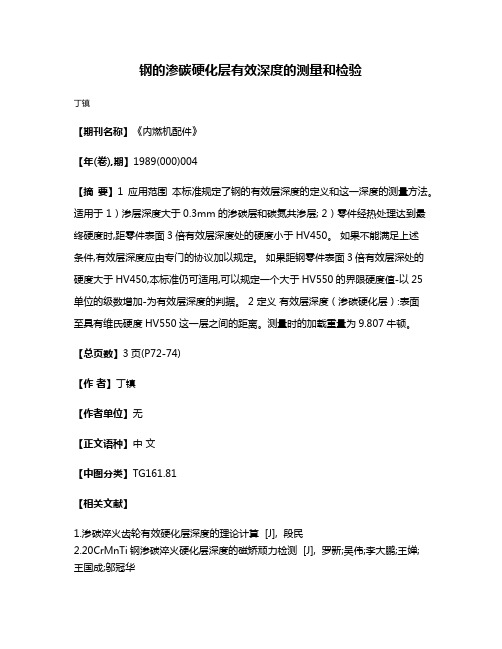
钢的渗碳硬化层有效深度的测量和检验
丁镇
【期刊名称】《内燃机配件》
【年(卷),期】1989(000)004
【摘要】1 应用范围本标准规定了钢的有效层深度的定义和这一深度的测量方法。
适用于 1)渗层深度大于0.3mm的渗碳层和碳氮共渗层; 2)零件经热处理达到最终硬度时,距零件表面3倍有效层深度处的硬度小于HV450。
如果不能满足上述
条件,有效层深度应由专门的协议加以规定。
如果距钢零件表面3倍有效层深处的硬度大于HV450,本标准仍可适用,可以规定一个大于HV550的界限硬度值-以25
单位的级数增加-为有效层深度的判据。
2 定义有效层深度(渗碳硬化层):表面
至具有维氏硬度HV550这一层之间的距离。
测量时的加载重量为9.807牛顿。
【总页数】3页(P72-74)
【作者】丁镇
【作者单位】无
【正文语种】中文
【中图分类】TG161.81
【相关文献】
1.渗碳淬火齿轮有效硬化层深度的理论计算 [J], 段民
2.20CrMnTi钢渗碳淬火硬化层深度的磁矫顽力检测 [J], 罗新;吴伟;李大鹏;王婵;
王国成;邬冠华
3.金相法测量渗碳(碳氮共渗)齿轮的有效硬化层深度 [J], 陈秋明;张永年
4.渗碳齿轮有效硬化层深度的确定和齿轮疲劳强度试验方法 [J], 李光瑾;叶俭;祝兵寿;陈德华;哈胜男;祖庆川;王伟;薛耀先
5.渗碳层深度和有效硬化层深度的控制 [J], 赵振东
因版权原因,仅展示原文概要,查看原文内容请购买。
渗碳类热处理术语

22) 渗碳层 渗碳工件碳含量高于原材料的表层。
23) 碳含量分布 在沿渗碳工件与表面垂直的方向上碳在渗层中的分布。
24) 渗碳层深度 由渗碳工件表面向内至碳含量为规定值处[一般为即(C) 0 .4%]的垂直距离。
9) 电解渗碳 在作为阴极的工件和与之同置于盐浴中的石墨阳极之间接通电源进行的渗碳。
10) 真空渗碳 在低于1x10^5Pa (通常是10~10^-1Pa)的条件下子渗碳气氛中进行的渗碳。
11) 高温渗碳 在950℃以上进行的渗碳。
12) 局部渗碳 仅对工件某一部分或某些区域进行的渗碳。
13) 穿透渗碳 薄工件从表面至中心全部渗透的渗碳。
27) 碳可用率 在气氛碳势从1%降至0.9% 时,1m3 (标准状态下)气体可传递到工件表面的碳量(以g/m3表示)。
28) 碳传递系数 单位时间(s)内气氛传递到工件表面单位面积的碳量(碳通量)与气氛碳势和工件表面碳含量(碳钢)之间的差值之比。
29) 空白渗碳 为预测工件渗碳后心部组织特征及可达到的力学性能,用试样在中性介质中进行与原定渗碳淬火周期完全相同的热处理。
14) 碳化物弥散强化渗碳 使渗碳表层获得细小分散碳化物以提高工件服役能力的渗碳。
15) 薄层渗碳 工件渗碳淬火后,表面总硬化层深度或有效硬化层深度小于或等于0.3mm 的渗碳。
16) 深层渗碳 工件在渗碳淬火后有效硬化层深度达3mm 以上的渗碳。
17) 复碳 工件因某种原因脱碳后,为恢复初始碳含量而进行的渗碳。
1) 渗碳 为提高工件表层的含碳量并在其中形成一定的碳含量梯度,将工件在渗碳介质中加热、保温,使碳原子渗入的化学热处理工艺。
零件热处理技术要求的提出及标注

零件热处理技术要求的正确提出及正确标注零件设计在确定了材料后,还要正确提出热处理技术要求,并在图样上正确地标注出来。
热处理技术要求,是指热处理质量的检验指标,除硬度和其它力学性能指标外,还有对组织、变形量以及局部热处理要求,对表面硬化零件有硬化层深度和渗层组织及脆性要求等等。
热处理技术要求的正确提出和正确标注,是一个合格热处理工作者的基本素质,也是在设计会审环节发表专业意见的基本依据。
1热处理技术要求的确定1.1硬度和其它力学性能的要求由于硬度试验简便快捷,又不破坏零件,而且硬度与强度等其它力学性能有一定对应关系,可以间接反映其他力学性能,因此,硬度成为热处理质量检验最重要的指标,不少零件还是唯一的技术要求。
对于重要受力件,除有硬度要求外,还有强度极限、屈服强度或断裂韧度等要求。
在较高温度下工作的重要受力件,还有持久强度和蠕变极限等要求。
在有腐蚀介质条件下工作的重要受力件,还有应力腐蚀、临界应力强度因子等要求。
在确定硬度以及力学性能指标时,要注意强度与韧性的合理配合,避免忽视韧性或过分追求韧性指标的偏向;注意组合件强度或硬度的合理匹配,提高零部件使用寿命。
例如,轴承滚珠一般要比套圈硬度高2-3HRC,汽车后桥主动齿轮的表面硬度一般要比被动齿轮高2-5HRC;处理好表面硬化零件(如渗碳淬火、渗氮、表面淬火等)的硬化层深度与表面、心部硬度的关系,使心部与表面达到最优匹配,适合零件的工作条件;由于材料强度、结构强度和系统强度三者不完全一致,所以设计中要处理好这三者的关系,对于某些重要零件,应根据模拟试验确定所需要的力学性能指标。
1.2表面硬化层深度选择需要表面硬化的零件,硬化层深度多少合适?这个指标的选择要考虑零件的工作条件、对性能的要求、失效形式和表面硬化工艺的特点。
首先要知道不同表面硬化工艺都有什么样工艺的效果?设备造价、变形开裂倾向、实用范围等有设么不同?下面分述以供参考:1.2.1 【渗碳淬火】表层状态是:层深0.2-2.0mm,表层硬化、压应力高,硬化层组织为马氏体+碳化物+残奥,层深均匀;性能特点是:硬度650~850HV(56~64HRC),耐磨性高,接触、弯曲疲劳强度高,抗咬合性好;变形开裂倾向性是:变形较大,不易开裂;设备造价:中等;适用范例:低碳钢、低碳合金钢等齿轮、轴、活塞销。
渗氮层、淬硬层、有效硬化层的硬度和厚度测试简介

0.05
0.02
0.35
0.15
0.1
0.05
0.4
0.2
0.15
0.05
0.5
0.25
0.2
0.1
0.6
0.3
0.25
0.1
0.65
0.3
0.3
0.1
0.75
0.3
3、总渗氮层深度
b、基体硬度的取点与测定,一般在3倍左右渗氮层深度的距离处测得的硬度值(至少取3点,平均值)做为基体硬度值。
c、对于渗氮层硬度变化很平缓的钢种,(如碳钢、低碳合金钢制件),其渗氮层深度可以从试样表面沿垂直方向测至比基体维氏硬度高30HV处。
d、当渗氮层深度有的特别浅,有的则较深时,检测力可以在0.2KG范围内选择(并注明,如HV0.2)
a、渗氮层脆性级别按维氏硬度压痕边缘碎裂程度分为5级
级别
渗氮层脆性级别说明
1
压痕边角完整无缺
2
压痕一边或一角碎裂
3
压痕二边或二角碎裂
4
压痕三边或三角碎裂
5
压痕四边或四角碎裂
b、渗氮层脆性检验一般采用维氏硬度计,试验力10公斤,试验力的加载必须缓慢(在5-9S内完成),试验力加载完成后必须停留5-10S,然后卸载试验力,特殊情况也可采用5KG或者30KG试验力。
一般零件推荐的化合物层厚度及公差表(单位/mm)
化合物层厚度
上偏差
化合物层厚度
上偏差
0.005
0.003
0.012
0.006
0.008
0.004
机械制造的热处理与表面硬化技术

机械制造的热处理与表面硬化技术机械制造中的热处理和表面硬化技术,是为了改善材料的力学性能和延长机械零部件的使用寿命。
热处理是通过加热和冷却的过程,对材料的微观结构和性能进行调整,而表面硬化技术则是在材料表面形成一层硬度较高的覆盖层。
本文将介绍热处理和表面硬化技术的基本原理和常用方法。
一、热处理技术热处理是通过对材料进行加热、保温和冷却的过程,改变材料的组织结构和性能。
常见的热处理方法包括退火、淬火、正火、回火等。
1. 退火退火是将材料加热到一定温度,然后缓慢冷却至室温的过程。
退火可以消除材料中的应力和缺陷,改善其塑性和韧性。
常见的退火方法包括全退火、球化退火、淬火退火等。
2. 淬火淬火是将材料加热到临界温度,然后迅速冷却至室温的过程。
淬火可以使材料形成硬而脆的组织,提高其硬度和耐磨性。
常见的淬火方法包括水淬、油淬、气体淬等。
3. 正火正火是将材料加热到临界温度,然后缓慢冷却的过程。
正火可以使材料形成较为均匀的组织,提高其韧性和强度。
常见的正火方法包括冷却速率正火、保温正火等。
4. 回火回火是将淬火后的材料加热到一定温度,然后缓慢冷却的过程。
回火可以消除淬火产生的应力和脆性,在保持硬度的同时提高材料的韧性。
常见的回火方法包括低温回火、中温回火、高温回火等。
二、表面硬化技术表面硬化技术是在材料表面形成一层硬度较高的覆盖层,以提高材料的抗磨性和耐腐蚀性。
常见的表面硬化技术包括渗碳、氮化、硬质合金喷涂、激光处理等。
1. 渗碳渗碳是将含碳气体加热和处理零件一起置于特定的温度下,使碳渗入材料表面形成高碳化层的过程。
渗碳可以提高材料的表面硬度和耐磨性,常用于零件的表面强化。
2. 氮化氮化是将零件置于氨气中加热处理,使氮与材料表面发生反应形成氮化物层的过程。
氮化可以显著提高材料的硬度和耐磨性,常用于高速切削工具和模具等零件的制造。
3. 硬质合金喷涂硬质合金喷涂是将硬质合金颗粒通过喷枪喷涂到材料表面,然后在高温下熔化并涂覆在材料表面形成覆盖层的过程。
D系列零件热处理渗碳产品缺陷分析与补救措施

D系列零件热处理渗碳产品缺陷分析与补救措施作者:张力芹刘光亮苗永顺来源:《科技风》2017年第05期摘要:结合热处理渗碳原理,对生产过程中出现的产品缺陷进行分析,进而对渗碳工艺进行完善和对产品缺陷进行补救。
关键词:碳化物;残余奥氏体组织;非马氏体组织;碳势热处理工段自正式生产以来,出现过渗碳产品热处理后的几种金相缺陷,本文通过对残余奥氏体、碳化物、非马氏体组织这三种金相指标等级超差缺陷产生的原因进行分析,结合实际生产现状,针对原因采取有效的补救措施,使渗碳产品热处理工艺和金相指标达到较理想的可控状态。
一、产品缺陷原因分析与补救措施(一)残余奥氏体超标分析与控制从齿轮服役条件上讲,适量的残余奥氏体,能提高渗层的韧度,接触疲劳强度,以及改善啮合条件,扩大接触面积,但残余奥氏体过量,常随着马氏体组织粗大,导致表层硬度下降,降低零件的耐磨性和耐疲劳强度,通常认为残余奥氏体量在30%体积分数以下是允许的。
按D16/D20系列渗碳齿轮金相检验标准规定残余奥氏体等级要求1~5级为合格状态,5级说明残余奥氏体含量在热处理工段生产过程中,出现过批量的输入轴、及季节性的L1.6/T1.4主减速齿轮残余奥氏超标,对引起残余奥氏体过量的原因分析:1)钢中合金元素多,如Cr、Mn、Ti、V、Mo、W、Ni等元素溶入奥氏中,增加了奥氏体的稳定性,促使淬火后残余奥氏体量增多。
2)渗层碳的质量分数过高即零件表层碳浓度高。
渗碳气氛碳势过高和渗碳温度偏高,使溶入奥氏体中的碳量增加,造成淬火后残余奥氏体量增多。
3)淬火温度偏高。
加热温度愈高,溶入奥氏体中的碳和合金元素也愈多,奥氏体的稳定性提高,残余奥氏体增多。
4)淬火油温度偏高,马氏体转变愈不充分,残余奥氏体量愈多。
经调查分析,对于输入轴和主减速齿轮残余奥氏体超差的情况,分别属于上述原因分析的第2条和第1、3条,为何有这样呢?主要因为:为保证输入轴返修后热变形量,在返修试验过程中,采取降低淬火温度的办法进行返修,但返修后金相结果出乎意料,残余奥氏体合格而碳化物等级超标,从而佐证了的上述原因第2条的分析。
高温环境下金属材料表面硬化处理

高温环境下金属材料表面硬化处理一、高温环境下金属材料表面硬化处理的重要性与挑战在众多工业领域,如航空航天、能源动力、石油化工等,金属材料常常需要在高温环境下运行。
高温会对金属材料的性能产生显著影响,例如导致材料强度下降、硬度降低、抗氧化性变差等。
而金属材料的表面硬化处理则成为应对这些问题的关键技术手段之一。
高温环境下金属材料表面硬化处理的重要性首先体现在提高材料的耐磨性上。
在高温工况中,金属部件之间的摩擦磨损依然不可避免,通过表面硬化可以显著增强材料表面的抗磨损能力,延长部件的使用寿命。
例如,在燃气轮机的叶片表面,经过硬化处理后,能够有效抵抗高温高速气流携带的微小颗粒的冲刷磨损,保证叶片在长时间运行过程中的气动外形和工作效率。
其次,表面硬化处理有助于提升金属材料的抗高温软化能力。
一般金属材料在高温下原子热运动加剧,晶格结构容易发生变化,从而使硬度和强度降低。
而经过特殊的表面硬化处理,在材料表面形成具有高温稳定性的硬化层,能够在一定程度上阻止或减缓这种软化现象,维持金属部件在高温下的力学性能,确保其在高温承载条件下的可靠性。
再者,良好的表面硬化处理还可以改善金属材料的抗高温氧化性能。
在高温有氧环境中,金属容易发生氧化反应,形成氧化膜。
若氧化膜不致密、不稳定,会进一步加速金属的氧化损耗。
表面硬化处理过程中,有时可以同时在材料表面引入一些抗氧化元素或形成致密的抗氧化相,从而增强材料表面的抗氧化屏障,减少氧化对材料性能的劣化作用。
然而,高温环境下金属材料的表面硬化处理也面临诸多挑战。
一方面,高温本身会对硬化处理工艺产生影响。
例如,一些传统的表面硬化工艺在高温环境下可能难以实施,或者其处理效果会大打折扣。
像常规的渗碳处理,在过高温度时,碳元素的扩散速率难以精准控制,容易导致渗层组织不均匀,影响硬化效果。
另一方面,要使硬化层在高温长期作用下保持稳定性能并非易事。
高温下硬化层与基体之间可能发生元素扩散、相变等复杂过程,从而破坏硬化层的结构完整性和性能稳定性。
- 1、下载文档前请自行甄别文档内容的完整性,平台不提供额外的编辑、内容补充、找答案等附加服务。
- 2、"仅部分预览"的文档,不可在线预览部分如存在完整性等问题,可反馈申请退款(可完整预览的文档不适用该条件!)。
- 3、如文档侵犯您的权益,请联系客服反馈,我们会尽快为您处理(人工客服工作时间:9:00-18:30)。
表面热处理零件有效硬化层、渗层等的有关说明
一、常用热处理零件硬化层深度、渗层深度有关术语、定义、代号和适用范围及检测方法
附注:①特殊情况下,经有关方协议,也可采用 4.903N~49.03N(0.5kgf~5kgf)内的某一试验力和其他值的极限硬度值,在特殊情况下要注明,如Dc49.03/515=0.6表示采用试验力49.03N(5kgf),极限硬度值为515HV时的有效硬化层深度等于0.6mm;
②特殊情况下,经有关方协议,也可采用4.903N~49.03N(0.5kgf~5kgf)内的某一试验力和其他值的极限硬度值,在特殊情况
下要注明,如Ds4.903/0.9=0.6表示采用试验力4.903N(0.5kgf),极限硬度值等于零件表面所要求的最低硬度的0.9倍时的有效硬化层深度等于0.6mm;
③测量方法有显微组织测量法和显微硬度测量法,选择的测量方法和它的精度取决于硬化层的性质和估计的深度。
由于测量方
法也影响到测量结果,因此选择哪种方法测量及何种试样形式,必须在图纸和工艺上预先规定;
④当工艺/图纸没有规定测量方法时,优先采用显微硬度法。
用显微硬度测量法检测时,一般试验力用1.96N(0.2kgf)的界线显
微硬度为基体硬度加30HV,除非工艺/图纸另有规定;
⑤试验力为0.9807N(0.1kgf)(HV0.1),极限硬度值HG一般规定为基体硬度加30HV。
特殊情况下,经有关方协议,也可采用
其他试验力的显微硬度和极限硬度值;
⑥试验力为0.9807(0.1kgf)(HV0.1),特殊情况下,经有关方协议,也可采用其他试验力的显微硬度和极限硬度值;
⑦测量方法有硬度法和金相法两种,采用哪种测量方法应预先规定。
硬度法规定采用试验力为2.94N(0.3kgf)的维氏硬度,从试
样表面测至比基体硬度高50HV处的垂直距离为渗氮层深度,对于渗氮层硬度变化很平缓的钢件(如碳钢、低碳低合金钢制件)可从试样表面沿垂直方向测至比基体维氏硬度值高30HV处。
特殊情况下,可由有关方协议,也可采用其他试验力和其他维氏极限硬度值,但应在工艺/图纸文件中注明。
二、对实际应用中的几点说明
1、本文是为了统一理解,使其规范化和标准化而编制的,要求各部门有关人员认真执行;
2、从前面表中所列术语可知,凡是有效硬化层深度都有一个极限硬度(或称界线硬度)的要求,对不同零件、不同的热处理方法、
不同的材料、不同的热处理要求的零件其定义的有效硬化层深度的极限硬度可能是不同的,因此,在设计图纸和编制工艺时应同时确定合理的极限硬度,只有可采用标准中规定了的极限硬度,工艺/产品图纸才可不作规定。
3、从2004年5月1日起,设计、工艺人员新设计编制的产品图、工艺文件应统一采用本文的相关术语,对于有同义的术语,只选择
带※的术语。
4、对于2004年5月1日以前设计、编制的产品图纸和工艺文件有相关热处理深度的术语,统一按照本文相应的术语来理解或解释,
对有明显不符本文的术语的个别零件,由技术开发部填写更改单经批准后进行更改。
上述时间以前的产品图纸有的有渗层深度要求又有有效硬化层深度要求的零件,在验收产品时,只检测有效硬化层深度,允许不检渗层深度,其图纸工艺再版时再作更改。
编制:审核:审定:
技术开发部
2004年4月12日。