几种钢管探伤方法可靠性分析
钢管对接焊缝探伤方法
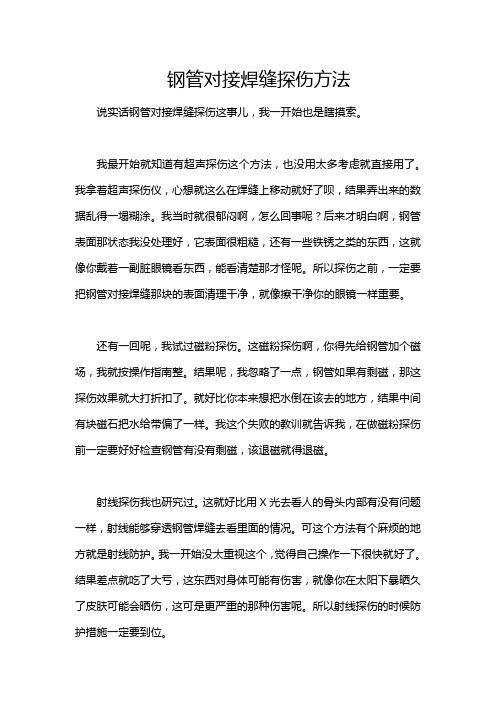
钢管对接焊缝探伤方法说实话钢管对接焊缝探伤这事儿,我一开始也是瞎摸索。
我最开始就知道有超声探伤这个方法,也没用太多考虑就直接用了。
我拿着超声探伤仪,心想就这么在焊缝上移动就好了呗,结果弄出来的数据乱得一塌糊涂。
我当时就很郁闷啊,怎么回事呢?后来才明白啊,钢管表面那状态我没处理好,它表面很粗糙,还有一些铁锈之类的东西,这就像你戴着一副脏眼镜看东西,能看清楚那才怪呢。
所以探伤之前,一定要把钢管对接焊缝那块的表面清理干净,就像擦干净你的眼镜一样重要。
还有一回呢,我试过磁粉探伤。
这磁粉探伤啊,你得先给钢管加个磁场,我就按操作指南整。
结果呢,我忽略了一点,钢管如果有剩磁,那这探伤效果就大打折扣了。
就好比你本来想把水倒在该去的地方,结果中间有块磁石把水给带偏了一样。
我这个失败的教训就告诉我,在做磁粉探伤前一定要好好检查钢管有没有剩磁,该退磁就得退磁。
射线探伤我也研究过。
这就好比用X光去看人的骨头内部有没有问题一样,射线能够穿透钢管焊缝去看里面的情况。
可这个方法有个麻烦的地方就是射线防护。
我一开始没太重视这个,觉得自己操作一下很快就好了。
结果差点就吃了大亏,这东西对身体可能有伤害,就像你在太阳下暴晒久了皮肤可能会晒伤,这可是更严重的那种伤害呢。
所以射线探伤的时候防护措施一定要到位。
后来我也知道另外一个方法叫着色探伤。
这个就简单一点,就像画画一样给焊缝涂上一层含有颜料的渗透剂,等一会儿渗透进焊缝缺陷里后,再把表面多余的擦去,然后涂上显像剂,有缺陷的地方颜料就会呈现出来,就像你把脏东西藏在布里头,现在用东西把脏东西吸出来显露在外面一样。
不过这个方法呢,检测的深度有限,只能发现比较表面的缺陷。
总之呢,不同的探伤方法各有利弊。
像那种不是很明显的内部缺陷,超声探伤和射线探伤可能更合适。
如果是比较简单看看表面可能有啥问题,着色探伤就可以了。
而且操作这些方法之前一定要先好好检查钢管的状态,把好基础这一关,探伤结果才更准呢。
钢管涡流探伤检验方法

钢管涡流探伤检验方法
钢管涡流探伤检验,那可真是个超厉害的技术!想象一下,它就像一位超级侦探,能在不破坏钢管的情况下,找出里面的小毛病。
那它到底咋操作呢?首先,把钢管放在检测设备上,就像把宝贝放在一个特殊的舞台上。
然后,开启涡流探伤仪,这玩意儿就像一个魔法棒,能发出神奇的信号。
这些信号在钢管里穿梭,就像小蚂蚁在寻找食物。
如果钢管里有缺陷,信号就会发生变化,就像小蚂蚁遇到了大石头。
这时候,检测人员就能根据信号的变化,判断出钢管有没有问题。
哇塞,是不是超神奇?
在这个过程中,安全性那是杠杠的!不用担心会对人造成伤害,就像在公园里散步一样安全。
稳定性也没得说,就像一座坚固的城堡,不会轻易被打倒。
那它都能用在啥地方呢?建筑工地上的钢管、石油管道、汽车零件,好多地方都能看到它的身影。
它的优势可多了,速度快得像闪电,一下子就能检测好多钢管。
而且还很准确,就像有一双火眼金睛,不放过任何一个小缺陷。
咱来看看实际案例吧!有一次,在一个大工地上,用涡流探伤检验方法检测了一批钢管。
哇,一下子就找出了几个有问题的钢管,避免了潜在的危险。
要是没有这个方法,说不定哪天就会出大事呢!
所以啊,钢管涡流探伤检验方法真的是太棒了!它就像一个守护天使,保护着我们的安全。
大家一定要重视这个方法,让它为我们的生活带来更多的保障。
钢材探伤分类及适用范围

钢材探伤分类及适用范围
钢材探伤是检测钢材内部缺陷或损伤的重要手段,主要可以分为以下几种:
1.磁粉探伤:应用磁性材料在识别缺陷和裂痕的表面上进行检测。
特别适用于低于硬度72的钢材。
它主要用于外表、近外表的裂纹和其它缺陷探伤,只检测管端400mm以内纵、横向伤。
2.超声波探伤:利用超声波进行检测,当超声波遇到缺陷时会有反射,这个反射可以被检测器捕捉到,通过检测波的延迟和振幅来确定缺陷的位置和性质。
适用于多种类型的钢材,包括铝、镁、铜、铸铁等,也可以检查纵向缺陷并用于测径、测厚。
超声波探伤仪可用于钢板数量较少时的人工检测,而钢板超声波自动探伤设备则适用于钢板企业的大规模检测。
3.涡流探伤:利用涡流进行检测,涡流可以检测到表面缺陷或者内部纹理。
主要用于外表、近外表探伤,以及穿透式涡流探伤主要检测横向缺陷和分层。
此外,涡流还可用于测厚、硬度、强度、测径、测距。
4.电磁探伤:探测材料结构的方法,利用感应电流和磁场相互作用的过程探测材料中的表。
此外,还有射线探伤、着色探伤、萤光探伤等其他方法,具体使用哪种探伤方法取决于钢材的类型、预期用途以及所需检测的缺陷类型。
例如,对于航天航海、压力容器和储罐、能源、桥梁等行业,由于需要保证钢板质量,因此钢材探伤尤为重要。
总的来说,钢材探伤方法多种多样,每种方法都有其特定的适用范围和优势。
在选择探伤方法时,需要根据具体情况进行综合考虑,以达到最佳的检测效果。
钢管探伤检验报告

钢管探伤检验报告1. 引言本文档是钢管探伤检验报告,旨在对钢管进行非破坏性检测,并分析评估其质量状况和可用性。
钢管作为一种常用的工业材料,其质量对工程安全和可靠性起着至关重要的作用。
通过探伤检验,我们可以评估钢管内部的缺陷情况,减少安全隐患,并为决策提供依据。
2. 检验方法钢管的探伤检验采用了磁粉检测和超声波检测两种主要方法。
磁粉检测主要用于检测钢管表面和近表面的缺陷,而超声波检测则能够深入材料内部,检测钢管的内部缺陷。
2.1 磁粉检测磁粉检测是一种基于磁粉粒子在磁场作用下显示缺陷的方法。
在磁粉检测过程中,我们首先对钢管表面进行粗糙度处理和清洁,然后涂覆磁粉液。
通过在磁场中对钢管进行磁化,磁粉液会在缺陷处形成磁粉聚集的明显特征,从而可视化缺陷位置和形态。
2.2 超声波检测超声波检测是一种利用超声波在材料中传播和反射的原理来检测缺陷的方法。
在超声波检测中,我们使用超声波探头将超声波引入钢管,通过接收并分析超声波的反射、散射和透射信号,可以精确地确定缺陷的位置、形态和尺寸。
3. 检测结果根据磁粉检测和超声波检测的结果,我们对钢管的质量状况进行了评估,并生成了以下报告:3.1 磁粉检测结果经过磁粉检测,我们检测到钢管表面和近表面的多处缺陷。
缺陷主要表现为裂纹、气孔和夹杂物。
根据缺陷大小和对钢管结构安全性的影响,我们将缺陷分为三个等级:轻微、中等和严重。
3.2 超声波检测结果超声波检测显示,在钢管内部存在一些隐蔽的缺陷。
这些缺陷主要是裂纹和气孔。
我们使用超声波技术确定了缺陷的尺寸和位置,并进行了定量评估。
4. 评估和建议针对钢管的缺陷情况,我们进行了评估和建议:4.1 轻微缺陷对于轻微缺陷,钢管的使用不会受到明显影响。
建议定期监测和维护,以确保缺陷不会进一步发展。
4.2 中等缺陷中等缺陷可能会对钢管的强度和可靠性产生一定的影响。
建议采取适当的修复措施,如焊接或补强材料,以提高钢管的使用寿命。
4.3 严重缺陷严重缺陷会对钢管的安全性和可靠性产生重大影响。
浅谈钢铁企业中管道探伤检测的应用

浅谈钢铁企业中管道探伤检测的应用钢铁企业中,管道的质量和安全性是非常重要的。
而管道的探伤检测是保障管道质量和安全性的重要手段之一。
本文将从不同的角度来探讨钢铁企业中管道探伤检测的应用。
一、管道探伤检测的意义管道作为钢铁企业中运输原料和产成品的重要设施,一旦发生泄漏或损坏就可能造成严重后果。
对管道的质量和安全性进行探测是十分必要的。
管道的探伤检测意义在于可以及时发现管道表面或内部的缺陷、磨损、腐蚀等问题,以便采取相应的维护和修复措施,确保管道的正常运行和安全使用。
目前,钢铁企业中常用的管道探伤检测方法主要有以下几种:1. 磁粉探伤法:磁粉探伤法是一种常用的管道表面缺陷检测方法。
通过涂抹磁粉或喷洒磁粉混合液在管道表面,再利用磁场作用下的磁粉自动吸附在管道表面缺陷处,形成磁粉痕迹,然后通过观察、摄影等手段来判断管道表面是否存在缺陷。
2. 超声波检测法:超声波检测法是一种应用广泛的管道内部缺陷检测方法。
通过超声波探测仪器向管道内部发射超声波,在超声波遇到管道内部缺陷时会发生反射或折射,通过收集和分析反射或折射的超声波信号来判断管道内部是否存在缺陷。
4. 电磁涡流检测法:电磁涡流检测法是一种常用的管道表面和近表面缺陷检测方法。
通过在管道表面或近表面放置电磁涡流探头,产生交变电磁场使得管道处于涡流感应状态,当管道表面或近表面存在缺陷时会影响涡流感应,通过探测仪器来判断管道表面或近表面是否存在缺陷。
以上方法各有优缺点,根据具体情况进行选择和应用。
在钢铁企业中,管道探伤检测的应用是非常广泛的。
对于输送原料和产成品的管道,需要定期进行探伤检测,确保管道的安全运行。
对于管道的安装、维护和修复过程中,也需要进行探伤检测,以确保管道的质量和安全性。
对于管道的新建项目或扩建项目,也需要进行探伤检测,以确保管道在投入使用之前就具有良好的质量和安全性。
管道探伤检测在钢铁企业中的应用是全方位的,贯穿管道的整个生命周期,对保障管道的质量和安全性起着至关重要的作用。
钢结构焊缝探伤的方法

钢结构焊缝探伤的方法钢结构的焊缝是连接钢材的重要部分,焊缝的质量直接影响到整个钢结构的强度和稳定性。
因此,对焊缝进行探伤是非常重要的一项工作。
本文将介绍几种常见的钢结构焊缝探伤方法。
1. 目视检查法目视检查法是最简单、最常用的焊缝探伤方法之一。
通过肉眼观察焊缝表面的形貌和颜色,可以初步判断焊缝的质量。
正常的焊缝表面应该平整、均匀,没有明显的裂纹、气孔和夹渣等缺陷。
目视检查法适用于焊缝表面缺陷较为明显的情况,但无法发现内部缺陷。
2. 渗透检测法渗透检测法是一种常用的焊缝表面缺陷检测方法。
它利用液体渗透剂的浸透性,将渗透剂涂覆在焊缝表面,待一定时间后擦拭干净,观察是否有渗透液残留的现象。
如果有残留,说明焊缝表面存在裂纹、气孔或夹渣等缺陷。
渗透检测法适用于焊缝表面缺陷较为细微的情况,但无法发现焊缝内部的缺陷。
3. 超声波检测法超声波检测法是一种常用的焊缝内部缺陷检测方法。
它利用超声波在材料中传播的特性,通过探头将超声波传入焊缝内部,接收反射回来的超声波信号,根据信号的强弱和时间来判断焊缝是否存在缺陷。
超声波检测法可以发现焊缝内部的裂纹、夹渣、气孔等缺陷,具有较高的灵敏度和准确性。
4. X射线检测法X射线检测法是一种常用的焊缝内部缺陷检测方法。
它利用X射线的穿透能力,通过将X射线照射在焊缝上,接收经过焊缝后的射线,根据射线的衰减程度来判断焊缝内部是否存在缺陷。
X射线检测法可以发现焊缝内部的裂纹、夹渣、气孔等缺陷,具有较高的探测深度和分辨率。
5. 磁粉检测法磁粉检测法是一种常用的焊缝表面和近表面缺陷检测方法。
它利用磁场的引导作用,将磁粉涂覆在焊缝表面,通过施加磁场使磁粉在焊缝表面和近表面形成磁线,观察磁粉的聚集情况来判断焊缝是否存在裂纹、夹渣、气孔等缺陷。
磁粉检测法适用于焊缝表面和近表面缺陷的检测,具有较高的敏感度和可靠性。
钢结构焊缝探伤的方法包括目视检查法、渗透检测法、超声波检测法、X射线检测法和磁粉检测法。
无缝钢管涡流探伤和漏磁探伤比较
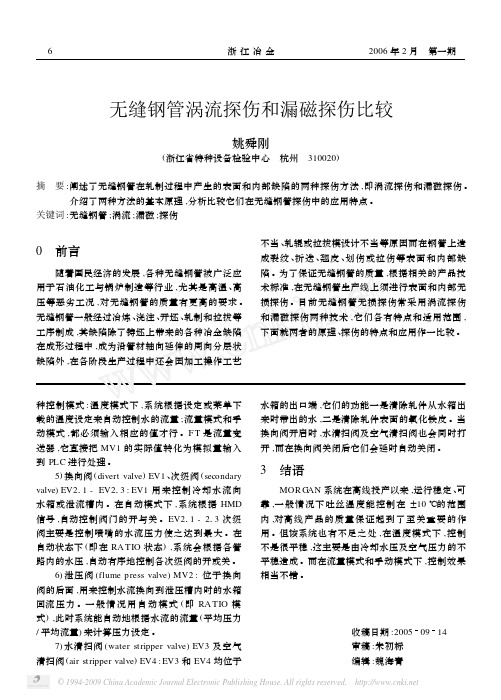
种控制模式:温度模式下,系统根据设定或菜单下载的温度设定来自动控制水的流量;流量模式和手动模式,都必须输入相应的值才行。
F T是流量变送器,它直接把MV1的实际值转化为模拟量输入到PLC进行处理。
5)换向阀(divert valve)EV1、次级阀(secondary valve)EV211-EV213:EV1用来控制冷却水流向水箱或泄流槽内。
在自动模式下,系统根据HMD 信号,自动控制阀门的开与关。
EV211-213次级阀主要是控制喷嘴的水流压力使之达到最大。
在自动状态下(即在RA TIO状态),系统会根据各管路内的水压,自动有序地控制各次级阀的开或关。
6)泄压阀(flume press valve)MV2:位于换向阀的后面,用来控制水流换向到泄压槽内时的水箱回流压力。
一般情况用自动模式(即RA TIO模式),此时系统能自动地根据水流的流量(平均压力/平均流量)来计算压力设定。
7)水清扫阀(water stripper valve)EV3及空气清扫阀(air stripper valve)EV4:EV3和EV4均位于水箱的出口端,它们的功能一是清除轧件从水箱出来时带出的水,二是清除轧件表面的氧化铁皮。
当换向阀开启时,水清扫阀及空气清扫阀也会同时打开,而在换向阀关闭后它们会延时自动关闭。
3 结语MOR G AN系统在高线投产以来,运行稳定、可靠,一般情况下吐丝温度能控制在±10℃的范围内,对高线产品的质量保证起到了至关重要的作用。
但该系统也有不足之处,在温度模式下,控制不是很平稳,这主要是由冷却水压及空气压力的不平稳造成。
而在流量模式和手动模式下,控制效果相当不错。
收稿日期:20050914审稿:朱初标编辑:魏海青 浙江冶金2006年2月 第一期无缝钢管涡流探伤和漏磁探伤比较姚舜刚(浙江省特种设备检验中心 杭州 310020)摘 要:阐述了无缝钢管在轧制过程中产生的表面和内部缺陷的两种探伤方法,即涡流探伤和漏磁探伤。
钢管探伤检测方法_解释说明以及概述
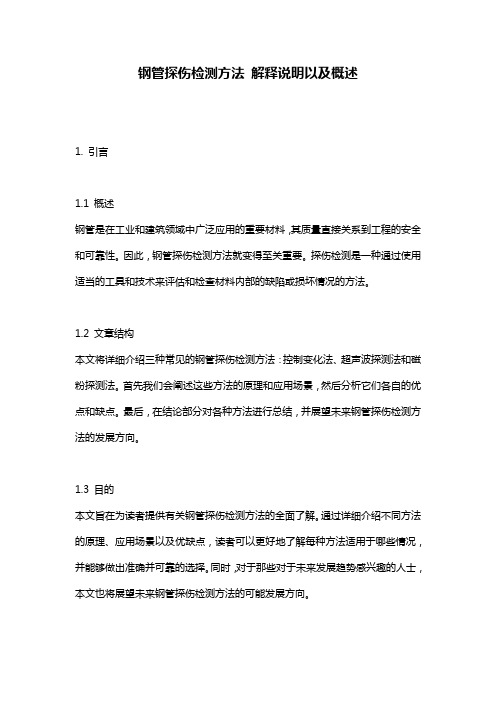
钢管探伤检测方法解释说明以及概述1. 引言1.1 概述钢管是在工业和建筑领域中广泛应用的重要材料,其质量直接关系到工程的安全和可靠性。
因此,钢管探伤检测方法就变得至关重要。
探伤检测是一种通过使用适当的工具和技术来评估和检查材料内部的缺陷或损坏情况的方法。
1.2 文章结构本文将详细介绍三种常见的钢管探伤检测方法:控制变化法、超声波探测法和磁粉探测法。
首先我们会阐述这些方法的原理和应用场景,然后分析它们各自的优点和缺点。
最后,在结论部分对各种方法进行总结,并展望未来钢管探伤检测方法的发展方向。
1.3 目的本文旨在为读者提供有关钢管探伤检测方法的全面了解。
通过详细介绍不同方法的原理、应用场景以及优缺点,读者可以更好地了解每种方法适用于哪些情况,并能够做出准确并可靠的选择。
同时,对于那些对于未来发展趋势感兴趣的人士,本文也将展望未来钢管探伤检测方法的可能发展方向。
2. 钢管探伤检测方法2.1 控制变化法控制变化法是一种常用的钢管探伤检测方法。
该方法通过对钢管进行特定外力作用,使其产生形状和尺寸变化,然后观察和测量这些变化来判断钢管内部是否存在缺陷。
控制变化法可以将钢管分为两种情况:静应力和动应力。
在静应力情况下,我们对钢管施加恒定外力,并测量其变形,以此来判断钢管内部是否存在缺陷。
例如,通过使用拉伸试验机对钢管进行拉伸实验,当发现钢管发生异常变形时,就能够判断出可能存在缺陷。
在动应力情况下,我们对钢管施加周期性外力,并观察其响应信号。
通过分析振动、位移或声波传播等方面的数据,在频域或时域上检测到异常信号可能表明了内部缺陷的存在。
2.2 超声波探测法超声波探测法是一种非破坏性检测技术,它利用超声波在材料中传播的特性来检测钢管内部的缺陷。
该方法通过发送超声波脉冲,利用声波在材料中传输时遇到不同介质或缺陷产生的反射、散射、衍射等现象,来识别和定位钢管内的缺陷。
超声波探测法可以检测出钢管内部的各种类型缺陷,如裂纹、夹杂、腐蚀等。
- 1、下载文档前请自行甄别文档内容的完整性,平台不提供额外的编辑、内容补充、找答案等附加服务。
- 2、"仅部分预览"的文档,不可在线预览部分如存在完整性等问题,可反馈申请退款(可完整预览的文档不适用该条件!)。
- 3、如文档侵犯您的权益,请联系客服反馈,我们会尽快为您处理(人工客服工作时间:9:00-18:30)。
摘要论述了钢管探伤中使用的漏磁、涡流、超声和电磁超声几种无损检测方法的可靠性。
通过对上述几种方法可靠性的比较可以看出,电磁超声方法具有其他无损检测方法不可比拟的优点和广阔的应用前景。
前言钢管是应用最广泛的钢材品种。
它的质量直接影响到经济效益及人员的生命安全。
世界各国都对钢管的质量检测给以极大的重视,采用了各种无损检测(NDT)方法对钢管进行严格的检测。
例如,德国的Mannesmann公司和日本的住友金属公司在检测大直径钢管时采用超声(UT)和漏磁(MFL)方法;检测小直径钢管时,采用超声和涡流(ET)方法,已形成了较为成熟的检测方案。
我国的钢管检测大量采用了超声及涡流方法,也愈来愈多地采用漏磁方法。
然而,由于钢管生产中产生的自然缺陷形貌的不确定性,常常发生肉眼明显可见的自然缺陷用N DT方法却检测不出来的现象。
因而,如何提高N DT的检测可靠性,就成为日益紧迫的课题。
本文结合钢管检测中曾出现过的一些自然缺陷漏检现象,从原理上及检测设备性能上进行深入分析,为制定最佳的检测方案提供了参考建议。
2MFL(Magnetic Flux Leakage)法的可靠性M FL法因其对管材表面状态要求不高,检出深度也较大,在国外的钢管检测中大量使用,国内也越来越多地采用,特别是石油用钢管的检测中已很普遍地使用了美国T ubescope公司制造的MFL探伤设备。
在MFL的使用中,由于管理上和技术上的原因,曾出现过一些漏检问题。
其中一个是与管轴线成45°角的缺陷常常漏检,为此做如下分析。
如图1所示,当缺陷延伸方向与磁化方向成角时,缺陷处形成的漏磁场B0要比B0(即=0°时的B)小,而B0对漏磁探头的贡献Bl与Bt会更小。
当=45°时,Bl与B t会比B0小50%[1]。
这就很容易导致“漏检”。
如将M F L设备中的纵向探头与横向探头同时使用,可能会减小漏检率,否则就很难保证这类倾斜伤的可靠检测。
在MFL法中影响可靠性的另一重要因素是自然缺陷与管表面的夹角。
理论计算[2]与实验研究[3]证明:如图2所示,当人工刻槽沿壁厚方向的取向与管外表面夹角为30°时,漏磁感应强度B下降50%,当角趋近于0°时,B趋近于0,即无法用M F L法检测出与表面平行的缺陷,如分层类缺陷。
此外,如钢管在轧制过程中变形较大,有时会将自然缺陷轧合。
这时,缺陷产生的漏磁就很小,导致很难用MFL法探出,这在图3中可清楚看出[5]。
图3中上部左、右两个记录曲线的剧烈起伏,就是自然缺陷有的部位被轧合所致。
在生产检测中,曾出现过用MFL法检测不出钢管中透壁大孔洞的现象。
抛开管理及人员因素,在技术上也应深入分析并加以防范。
如图4所示,缺陷形成的漏磁场可分解为垂直分量BZ和水平分量B X。
当缺陷宽度2b及深度h增大时,水平漏磁分量B X会线性增大,而且其B Z信号包络也呈现宽而缓的现状[2]。
因而按Fourier理论,其低频成分较大。
故用低通滤波就会较用高通滤波更容易探出这种大孔洞类的缺陷。
当然如有检测水平分量漏磁的探头,这种缺陷就更有把握探出。
对于用MFL法能探出距表面多深的缺陷,一直没有明确的结论。
这与仪器及探头性能及缺陷尺寸形状等都有关系。
但从管壁中磁感应强度的计算分析,在用直流磁化时,管壁厚为15 mm时的B值比管壁厚为小于5 mm时的B值小50%[4],故M FL法的检测深度不会大于15 mm。
如采用交流磁化,它会远远小于15 mm。
3ET(Eddy Current Testing)法的可靠性由于检测速度高,穿过式线圈ET法多年来广泛用于检验钢管质量,特别是其致密性。
在使用中证明,它难以探出铁磁性钢管中的裂纹状缺陷,所以在高标准的ET中,采用探针式线圈ET法。
此外,对于ET法究竟能探出距表面多深的缺陷这样一个简单的问题,似乎至今也末形成一个明确的共识。
有时甚至认为,在5 kHz检测频率下,还能检测出壁厚>5 mm的钢管内壁上的浅缺陷。
应该认识到,除非这时的内壁上的缺陷向外壁延伸得很深,以致构成了外壁缺陷,否则不可能将其探出。
因为从电磁波趋肤理论可知,在5 kHz的检测频率下,涡流密度的渗透深度只有0.25 mm左右(对铁磁性钢材)。
将它扩展10倍,即在渗透深度2.5 mm下,涡流密度已降至表面上涡流密度的10-10,因此根本不能探出这样深度上的缺陷。
对于钢管中常常产生的“外折”类缺陷,不少的涡流仪器与探头也往往发现不了。
经常出现外折肉眼明显可见,却无法将之用ET仪报警的尴尬现象。
自从出现了扇区式相位报警的涡流设备后,这种局面得到了根本改变。
但选择合适的仪器与探头并正确调整它,仍是不容忽视的重要问题。
4UT(Ultrasonic Testing)法的可靠性U T法在钢管探伤与测厚中应用最广。
然而,作为一种检测方法,其可靠性会受到各种因素的影响。
如对之分析研究不够,甚至会出现严重的漏检、误检现象。
下面仅对UT 中可能存在的几种降低UT的可靠性的因素做一些讨论。
(1)自然缺陷取向对U T可靠性的影响在钢管轧制过程中,出现频度较高的是轴向(纵向)缺陷。
然而,与钢管轴线呈一定角度延伸的缺陷也不少见。
垂直于管轴线的周向(横向)缺陷也时有发生(图5)。
NDT的任务就是将这些取向不同的缺陷都探出来。
(2)在钢管的UT中,如在探头配置的设计时考虑不周,只采用一种(或两种)探头配置去探如图5(a)所示的4种典型取向的缺陷,就有可能漏检。
从图5(b)的实验曲线可知,当缺陷与管轴线偏斜10°时,用脉冲回波法的UT,信噪比下降20 dB左右,对于偏斜45°的缺陷就根本探不出来。
因此,为了保证探出图5(a)所示的4种典型取向的缺陷,应配置如图5所示的4种取向的探头。
同样,为了可靠探出与钢管表面倾斜的折叠类缺陷,必须设置2组沿管周向相反方向入射的探头。
(2)声耦合方式对U T可靠性的影响水浸UT中,声波在管壁中传播衰减是很严重的。
因为水的声特征阻抗远小于钢,故声波从水向钢及从钢向水的往复透射率就很小。
其次,声波在管壁中的每次反射都伴随着波型转换。
而横波向水透射时又要完全被水吸收,故更显著地增大了水浸UT的超声衰减。
这就导致声波沿管壁传播距离很小,甚至连1/4周长也达不到。
在不考虑声传播过程中的波型转换,即在横波折射角为45°时,有机玻璃楔块制成的斜的接触法探头,对钢管(内孔为空气)的声压往复透射率的计算值T LS≈25%。
而在钢管外侧浸在水中,内侧仍为空气时T LS≈15%。
后者比前者低4 dB。
如果钢管内孔也充入水(例如水从大孔洞浸入内孔)时,则缺陷回波信号要比接触法或水膜法代替水浸法进行声耦合。
5电磁超声EMAT(Electromagnetic AcousticTransducer)探伤技术为解决声耦合给UT带来的各种困难,20世纪60年代末期出现了不需声耦合而直接在金属中激发与接收声波的电磁超声换能器(EMAT),经30年来的研究、开发,现今已进入工程化、商品化阶段。
美、德、俄、日等国已有商品仪器设备出售。
笔者从70年代初也开始了MEA T 的研究与开发,目前,研发的EMAT设备已在国内多家钢管、钢板的生产与使用单位成功地应用。
EMA T是靠3种方式产生L orent z力、磁致伸缩力及磁性力来激发与接收超声波的,直接在金属中激发与接收超声,不需要声耦合,所以可在粗糙表面的工件中及高温、高速运动的工件中进行超声检测。
它可以很容易选定所需的超声波模式,特别是能很简单地激发与接收SH波,这在压电超声换能器很难做到。
它在钢管(棒)中激发的超声,可绕工件传播几周甚至十几周,这就为用透过波来检测缺陷尺寸奠定了良好基础。
如前所述,在UT中如果缺陷与声束不完全垂直时,如其偏斜超过10°,反射波就大幅度下降[6]。
偏斜45°的缺陷就会漏检。
但是,如图6所示,透过波幅度的下降只受缺陷投影深度D影响,而基本不受缺陷倾斜角度的影响[5]。
从图6还可看出,当使用低频率时,在缺陷投影图深度对波长之比(D/)<0.5时,深度D 与规一化的透过波幅度(A T/A 0)呈近似的线性关系。
这就是说,在低频(大的波长)下进行UT时,缺陷尺寸的定量较准确。
EMAT可以很容易实现在低频下检测,并能对缺陷进行较准确的定量检测。
6MEL、ET、UT及EMAT法的可靠性比较用大量自然缺陷分别对MFL、ET、UT及E-M A T方法进行了比较实验[5]。
用各种既定深度的人工标准缺陷对每种方法的缺陷深度的测量进行标定。
然后对这些自然缺陷进行扫查探测。
将探测得的缺陷深度标在图中曲线的纵坐标上。
而其横坐标则表示将所检测的自然缺陷解剖(共解剖了500多个剖面)进行金相分析,实测出自然缺陷在该剖面上的真实深度。
从图7中的缺陷测量深度与真实深度的对应关系来看,测量结果的离散度以EMAT(图中系统E)为最小,图中系统F为窄脉冲超声探头以测厚方式垂直入射声波测得的结果。
当折叠类缺陷深度较大时,其测量结果的离散度最小,但当缺陷深度小于2 mm时,离散度相当大。
而MFL和ET法的离散度更大,在很多部位上测量深度为0,即探测不出来。
这可能是由于在该部位上缺陷被轧合了(即开口小)。
而EMAT就不存在这种漏检现象,在我们的EMAT设备使用中也证实了这一优点,不论人工缺陷还是自然缺陷,EMAT设备都有很高的检出率。
7结论(1)EM A T方法不仅能检测出各种标准所规定的人工缺陷,而且可以检测出多种自然缺陷,其可靠性是其他NDT法无可比拟的。
(2)在M FL法检测中,应将探纵、横向缺陷的探头及高、低通滤波器全部使用,以防缺陷漏检。
如可能,应开发检测水平分量漏磁场的探头,以确保其可靠性。
(3)在ET法中,应采用相位报警方式,以防折叠类缺陷漏检。
在对ET法的可靠性要求高时,应采用点探头式线圈的ET仪器与设备,以可靠检测裂纹类缺陷。
(4)在U T法的钢管探伤中,不宜采用全水浸式探头,而应采用水膜式探头,防止危险性缺陷漏检。