汽车高强板零件冲压工艺及模具结构设计-1
冲压模具结构及设计PPT课件( 32页)

设计时采用经验公式: C (1 .5~2 .0 )t (C 3 m)m
第八章 冲压模具结构及设计
(五)凸模长度计算 当采用固定卸料板和导料板时,其凸模长度按下式计算: Lh1h2h3h 当采用弹压卸料板时,其凸模长度按下式计算:
Lh1h2th
角选取与加工方法有关:放电加工 4'~20',
(落料模 10' ,复合模 5' );机械加工经
钳工精修 15'~30'
机加工β =2。~3。;电火花加工β <1。;线切割加 工 β =1。~1.5。。
第八章 冲压模具结构及设计
5、锥形凹模 用于冲裁薄料和凹模厚度较薄的情况。
•
9、照自己的意思去理解自己,不要小看自己,被别人的意见引入歧途。
•
10、没人能让我输,除非我不想赢!
•
11、花开不是为了花落,而是为了开的更加灿烂。
•
12、随随便便浪费的时间,再也不能赢回来。
•
13、不管从什么时候开始,重要的是开始以后不要停止;不管在什么时候结束,重要的是结束以后不要后悔。
•
14、当你决定坚持一件事情,全世界都会为你让路。
第一节 冲压模具及零件的分类
模具设计主要是确定模具的类型、结构和模具零件的 选用、设计与计算。
一、冲压模具的分类
(1)按工序性质划分 冲裁模、弯曲模、拉深模等。
(2) 按工序组合程度划分 单工序模、级进模、复合模。
第八章 冲压模具结构及设计
(3)按导向方式划分 无导向的开式模、有导向的导板模、导柱模等。
第八章 冲压模具结构及设计
本章目录
第一节 冲压模具及零件的分类 第二节 冲压模具主要零件设计 第三节 级进模结构设计要点 第四节 冲压模具设计要点 第五节 冲压设备的选择 第六节 复合模结构分析 第七节 级进模结构分析 第八节 冲压模具设计实例分析
高强度板冲压工艺及模具制造

高强度板冲压工艺及模具制造在汽车高强度板的冲压工艺设计过程中,科学地进行工艺补充造型以及变参数的拉延筋设计,削减了模具调试次数,缩短了模具制造周期和制造成本,保证了产品质量。
高强度板应用在车身结构中能够使车身减重达到25%左右,节约约15%的燃油。
因此,提高高强度板在车身结构件中的利用率,对于实现汽车质量轻量化、节省能源、爱护环境和平安性能等方面具有重要意义。
本文结合实际重点介绍了汽车掩盖件中高强度板材的冲压工艺设计与模具制造留意事项。
冲压工艺所示为我公司担当开发某模具项目的一个冲压件前防撞梁外板。
其材料为D340LA,料厚为1.2mm,形状尺寸:长为1290mm,宽为220mm,高为67mm。
前防撞梁外板依据产品的尺寸,我们可以看出,该产品外部外形并不简单,但却属于高强度钢板。
通常,对于高强度板材零件的冲压过程,会产生零件扭曲、回弹和翘曲等问题,必需加以解决。
因此,要在冲压工艺制定过程中留意以下事项:1. 拉延成形要充分高强度板材零件在冲压时,其外形要尽量全部拉延出来,不要靠后序的翻边、整形工序来实现,也就是说,要通过拉延成形,让板料产生充分的塑性变形,削减自身的回弹应力。
但如何才能让高强度板材产生充分的塑性变形,需要通过设计合理的工艺补充来实现,以往此类零件的拉延筋通常设计成圆形的,但对于此件,我们采纳了方筋.前防撞梁外板拉延数模前防撞梁外板拉延方筋尺寸2.进行CAE分析通过拉延成形工序做好数模后,必需要进行CAE分析,并依据分析的结果,判定零件回弹趋势大小,然后在数据上加以补偿,并用补偿后的数模作为加工依据。
零件的拉延工序回弹补偿。
3.冲孔模具型面加工数据的确定拉延工序后、翻边修整工序前的修边冲孔模具型面加工数据,肯定要以调试好的最终拉延件为准,而不能以经过CAE分析后作过回弹补偿的拉延数模数据为准。
这就需要对最终拉延件进行逆向建模,然后以逆向建模的数据作为加工修边冲孔模具的加工工艺数模依据。
丰田车身外部加强板汽车毕业设计冲压模具设计
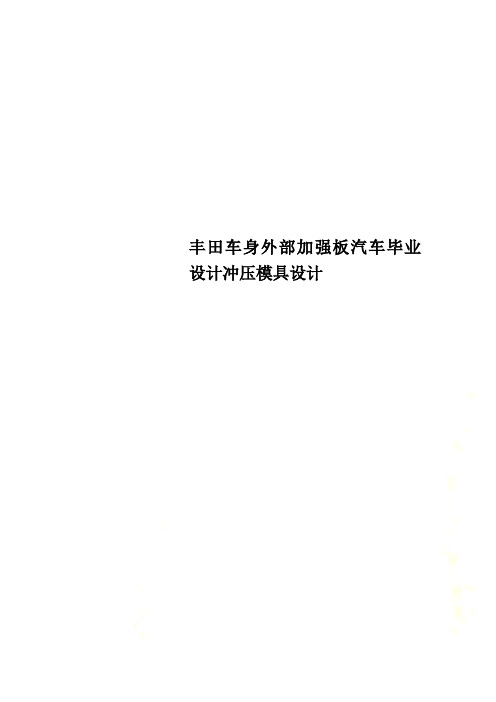
丰田车身外部加强板汽车毕业设计冲压模具设计目录第1章前言。
(3)第2章冲压件工艺性分析 (4)2.1 冲压件工艺分析。
(5)2.2 冲压件工艺方案的确定 (5)2.3 级进模的设计流程 (6)第3章主要工艺参数计算3.1 主要问题及技术要求 (8)3.2 确定工序的合并与工序顺序 (9)3.3 冲压零件的排样方法 (10)3.4 相关尺寸计算 (11)3.4.1 材料的利用率 (11)3.4.2冲压力与压力中心,初选压力机 (12)3.4.3整形力的计算 (13)3.4.4凸模的长度 (14)3.4.5冲裁模的间隙确定 (14)3.4.6计算凸凹模刃口尺寸及公差 (14)第4章模具总体设计4.1 凸模、凹模的结构设计 (15)4.2 落料凹模的主要技术要求 (16)4.2.1定位零件的设计 (16)4.2.2 卸料装置的设计 (17)4.2.3 行程限位的设计 (18)4.3 模架的设计 (19)4.4 导向零件的设计 (20)第5章结论 (20)第6章参考文献 (21)总装图 (22)第一章前言模具工业可称之为「工业产品之母」,因为除了传统工业产品需借助「模具」,才能快速精确、或自动的生产外,目前的高科技产品也不例外。
我国模具标准化工作起步较晚,模具标准件生产、销售、推广和应用工作也比较落后,因此,模具标准件品种规格少、供应不及时、配套性差等问题长期存在,从而使模具标准件使用覆盖率一直较低。
近年来虽然由于外资企业的介入,比例已有较大提高,但总的来说还很低。
据初步估计,目前这一比例大致为40%~45%之间。
而国际上一般在70%以上,其中中小模具在80%以上。
由于我国模具企业的性质和所在的地区不同,模具标准件使用覆盖率存在很大差异。
三资企业要比其他企业高,南方的企业要比北方的企业高。
这在广东表现得最明显。
广东集中了大量的三资企业,他们带动了其他企业观念的转变和市场的发展,因而广东模具企业的模具标准件使用覆盖率要远远高于其他地区。
冲压模具工艺结构设计书

冲压模具工艺结构设计书一、冲压工艺与模具设计 1.冲压件工艺分析①材料:该冲裁件的材料A3钢是普通碳素钢,具有较好的可冲压性能。
②零件结构:该冲裁件结构简单,并在转角有四处R2圆角,比较适合冲裁。
③尺寸精度:零件图上所有未注公差的尺寸,属自由尺寸,可按IT14级确定工件尺寸的公差。
孔边距12mm 的公差为-0.11,属11级精度。
查公差表可得各尺寸公差为:零件外形:65 mm 24 mm 30 mm R30 mm R2 mm零件内形:10 mm孔心距:37±0.31mm 结论:适合冲裁。
2.工艺方案及模具结构类型该零件包括落料、冲孔两个工序,可以采用以下三种工艺方案: ①先落料,再冲孔,采用单工序模生产。
②落料-冲孔复合冲压,采用复合模生产。
③冲孔-落料连续冲压,采用级进模生产。
方案①模具结构简单,但需要两道工序、两套模具才能完成零件的加工,生产效率较低,难以满足零件大批量生产的需求。
由于零件结构简单,为提高生产效率,主要应采用复合冲裁或级进冲裁方式。
由于孔边距尺寸12 mm 有公差要求,为了更好地保证此尺寸精度,最后确定 用复合冲裁方式进行生产。
工件尺寸可知,凸凹模壁厚大于最小壁厚,为便于操作,所以复合模结构采用倒装复合模及弹性卸料和定位钉定位方式。
3.排样设计查《冲压模具设计与制造》表2.5.2,确定搭边值: 两工件间的搭边:a=2.2mm 工件边缘搭边:a1=2.5mm 步距为:32.2mm 条料宽度B=D+2a1=65+2*2.5 =70确定后排样图如2所示一个步距内的材料利用率η为: η=A/BS ×100%=1550÷(70×32.2)×100%0 -0.74 0 -0.52 0-0.520 -0.52 0 -0.52 +0.36-0.11=68.8%查板材标准,宜选900mm×1000mm的钢板,每张钢板可剪裁为14张条料(70mm×1000mm),每张条料可冲378个工件,则η为:η=nA1/LB×100%=378×1550/900×1000×100%=65.1%即每张板材的材料利用率为65.1%4.冲压力与压力中心计算⑴冲压力落料力F总=1.3Ltτ=1.3×215.96×2×450=252.67(KN)其中τ按非退火A3钢板计算。
汽车冲压工艺及模具设计

汽车冲压工艺及模具设计1汽车用支架件工艺性分析该汽车支架的冲压件形状见图1,材料为08F钢;精度为IT12;料厚为1.2mm,结构对称,表面平整,表面要求无划痕、毛刺等,孔不允许有严重的变形,且大批量生产.对该冲压件工艺性分析,主要考虑以下几个方面:(1)冲压件的形状和尺寸;(2)冲压件的精度、粗糙度及材料;(3)冲压件的技术要求及生产批量;(4)弯曲工艺条件.通过该零件图观察分析可知,该工件精度等级为IT12,因此该工件对精度要求不高,普通冲裁即可实现,从零件形状上看,结构对称,工件在冲裁后弯曲过程中不会产生偏移现象.直角弯曲时的最小孔边距为Lmin=r+2t[2]=0.6+2×1.2=3mm,而实际工件孔边距为4mm,大于最小弯曲孔边距,因此,在制件的弯曲过程中,不会使底孔发生变形,可采用先冲孔后弯曲方案进行成型.另外材料选用08F钢,属于低碳钢,因此材料塑性好,便于成形.从以上分析中可看出,该支架件的冲压工艺性良好,可通过冲压成形的方法进行生产.符合普通弯曲件经济精度要求.2冲压工艺方案确定通过对该零件的结构工艺性分析可知,其基本成形工序为:落料、冲孔、弯曲.其可采用的冲压工艺方案如下:方案1:采用单工序模具冲裁.即落料模、冲孔模、弯曲模3副模具来完成.虽然模具结构简单,制造方便,但各工序间不容易保证尺寸精度,很难满足生产技术要求,模具制造费用较大,占用设备多,操作不便,生产效率低,难以满足大批量生产的要求.方案2:采用复合模冲裁.即落料、冲孔复合模,单工序弯曲模.由于该件结构不复杂而且对称,适用于形状较复杂、精度要求高的大中型件的大批量生产,制造难度不大,易保证尺寸的精度,操作方便,与单工序模相比,减少单工序模数量,提高生产效率.方案3:采用级进模冲裁.即落料、冲孔、弯曲级进模冲压.虽然冲压生产效率高,易实现机械化、自动化,操作安全简单,制件质量高,但级进模设计和制造过程费用成本高,对技术经验的依赖性较强[1-6].通过上述三个工艺方案在产品质量、生产效率、设备条件、模具的制造和经济效益等方面进行对比分析,可明显看出,方案3为最佳冲裁工艺.3主要零部件结构设计与计算3.1排样设计.排样的合理与否,会直接影响材料的利用率,还会影响到模具结构、生产率、制件质量、生产操作方便与安全等.因此,排样是冲裁工艺与模具设计中一项重要工作.查《冲压工艺与模具设计》[2]可知:工件之间搭边值a1=2mm,工件与侧边之间搭边值a=2.5mm.根据板料规格和厚度公差表,经过计算,板料1250×1500mm的利用率高,故选择用1.2×1250×1500的08F钢板料.经计算,纵排排样利用率高,排样方式如图2所示.图2纵排排样图利用率计算如下:查《冲压工艺与模具设计》[2]知,b=112.4mm,s=55mm,利用CAD绘图软件求得A=3922.92mm,一个步距的材料利用率:η=Ab×S×100%=3922.92112.4×55×100%=63.46%其中,A为一个步距内冲裁件的实际面积;b为条料宽度;S为步距.η总=NALB×100%其中,N为一张板料上所冲裁零件的总数量;A为一个冲裁件的实际面积;L为板料的长度;B为板料的宽度.n1=Bb=1250112.4=11.12,取n1=11,n2=LS=150055=27.27,取n2=27η总=11×27×3922.921250×1500×100%=62.14%3.2凸、凹模刃口与结构设计.由于该支架零件轮廓结构复杂,落料凸、凹模采用配合加工法.先加工好凸模作为基准件,然后配做凹模,使它们保持最小双面间隙Zmin.其公差不再受凸、凹模间隙大小限制,制造容易,并容易保证凸、凹模间的间隙.冲裁凸、凹模刃口尺寸与结构如图3(a)~(d)所示.(a)凸模配合加工刃口尺寸计算分为以下三类:第一类磨损后增大的尺寸,公式为Ad=(A-xΔ)+δd0.其对应第一类尺寸的凹模刃口尺寸为51.175+0.0170mm,20.84+0.0120mm,5.88+0.0100mm,2.9+0.0100mm.第二类磨损后减小的尺寸,公式为Bd=(B+x Δ)0-δd.其对应第二类尺寸的凹模刃口尺寸为48.590~0.012mm,3.10~0.010mm.第三类磨损后基本不变的尺寸,公式为Cd=C±18Δ.其对应第三类尺寸的凹模刃口尺寸为28±0.0225mm,16±0.026mm.落料凸模的刃口基本公称尺寸与凹模相同,分别是51.175mm,20.84mm,5.88mm,2.9mm,48.59mm,3.1mm,28mm,16mm,但要在技术要求中注明:凸模刃口尺寸按照落料凹模刃口实际尺寸配合,以保证最小双面合理间隙值为0.1mm.3.3冲孔部分凸凹模刃口尺寸的计算.以凸模为基准来计算冲孔部分的凸、凹模的刃口尺寸,冲孔凸模刃口的基本尺寸采用分别加工,按《冲压工艺与模具设计》中表3-26公式ap=(a+xΔ)0-δp.经过计算可得冲孔凸模冲裁分别为ap1=(6+1×0.12)0-0.007=6.120-0.007mm,ap2=(7.5+1×0.15)0-0.007=7.650-0.007mm,ap3=(7.8+1×0.15)0-0.007=7.950-0.007mm.4模具其他零部件设计选用4.1凸模固定板设计.凸模固定板上需要开设4个阶梯形圆孔,与冲孔凸模进行配制,由于冲孔凸模与上模座之间没有销钉、螺钉的连接,为了使冲孔凸模固定在上模座上,因此采用凸模固定板来实现.(1)凸模固定板的厚度一般取落料凹模厚度的0.6~0.8倍,其平面尺寸可与落料凹模、卸料板的外形尺寸相同,但是还应该考虑紧固螺钉、销钉的位置;(2)凸模固定板上的冲孔凸模的安装孔与凸模采用H7/m6过渡配合,压入后端面要磨平;(3)凸模固定板的上下表面应磨平,与凸模安装孔的轴线垂直粗糙度1.6~0.8μm;(4)凸模固定板的材料一般采取45#钢[3,7-9].4.2推件块设计.根据《冲压工艺及模具设计》图3-116可知,材料选用45#钢,热处理硬度为43~48H RC.推件块与冲孔凸模采用间隙配合H8/f8.4.3模具结构设计该模具采用复合冲裁模,其结构设计如下:(1)采用倒装式复合模.凸凹模装在下模,冲孔凸模和落料凹模安装在上模,便于落料,冲孔废料则通过凸凹模的内孔从压力机台面的孔漏下,且有利于安全操作.(2)上模座采用了刚性推件装置.当上模座向上回程时,压力机通过打杆、推杆和推件块将冲裁件从落料凹模中推出.(3)卸料时,下模采用了弹性卸料的装置,弹性卸料装置由卸料板、卸料板螺钉和橡胶组成.通过橡胶产生的压缩回弹力使条料从凸凹模周围脱出,进而实现卸料功能.5模具结构及工作过程图4为落料-冲孔复合模总装图。
汽车复杂制动零件冲压工艺与模具设计

目录摘要 (3)关键词 (3)引言 (4)第一章冲压工艺方案和冲压力的计算 (4)1.1 毛胚尺寸计算 (5)1.2 零件冲压工艺方案的确定 (6)1.3 排样方案 (7)1.3.1 确定排样方案 (7)1.3.2 确定搭边值 (7)1.3.3 计算材料利用率 (8)1.4 计算各工序冲压力 (9)1.4.1 冲裁力 (9)1.4.2 弯曲力 (10)1.4.3 卸料力和推料力 (11)1.5 计算压力中心 (12)1.6 压力机的选取 (12)1.6.1 设备类型的选择 (12)1.6.2 设备规格的选择 (13)2.1 冲孔落料凸、凹模尺寸计算 (15)2.1.1 尺寸计算原则 (15)2.1.2 模具间隙的选择 (16)2.1.3 尺寸计算 (16)2.2 凸模的结构设计和校核 (17)2.2.1 压应力的校核 (18)2.2.2 稳定性的校核 (18)2.3 凹模的结构设计和校核 (19)2.4 定位零件的设计 (21)2.5 导向零件的设计 (21)2.6 卸料与推件装置的设计 (22)2.7 模柄的选择 (23)2.8 螺钉的选择 (23)2.9 模架的选择 (23)第三章弯曲模具设计 (25)3.1 弯曲工艺分析 (25)3.2 结构尺寸设计 (26)3.2.1 凸模与凹模之间的间隙 (26)3.2.2 弯曲时凸模与凹模的宽度尺寸 (27)3.2.3 弯曲时模具的圆角半径和凹模深度 (28)结论 (29)致谢...................................................... 错误!未定义书签。
参考文献:.. (30)汽车复杂制动零件冲压工艺与模具设计摘要冲压加工是一种高效的零件加工方法,这种方法是在常温下,利用压力机,使用模具对材料施加压力,使材料产生分离或塑性变形,从而获得最终零件。
其应用于汽车、电器、电机和仪表等众多行业【1】。
先进的冲压工艺方案和模具设计能够提高生产效率,增加经济效益,而且能够使整个制造过程很好地和环境融入在一起。
高强板零件冲孔落料级进模设计
右件各 1 , 个 年生产纲领为 6万 一8万件 。模 具设计要求结构
强度满足 冲模使用寿命 ( 要求 3 0万次 )设计轻便 , , 操作简单 , 生产效率高 , 尽量降低生产成 本及模具制作成本。
() c 所示 。经计算 比较 , 2 b 的材料 利用率为 6 - 图 () 24%, 2 图
够有效提高原材料的利用率 , 充分利用原材料 , 减少废料 的产
1 零 件分析
图 1 件 为 轿 车 中发 动 机 罩 铰 链 加 强 板 冲 压 件 ,该 零 件 零 的材 质 为 B 1P , 厚 为 t 1 2 0 1料 : .mm, 件 单 车 用 量 为 2个 , 0 零 左
组合 件 , 防止在 制时 , 出现偏差 , 或损坏模具 ; 导正 销有效地 保证 板料在1 送料及压 制时不错位 , ) 1 『 = 保证 了制什 的精度 ; 并且 根据侧 刃定位的要求 , 增加 了定位器 、 定位饭等 。
( ) 横 具 为 下 落 料 结 构 , 入 了滑 料 板 , 零 件 滑 至 工 4 装 将 作 台上 , 了收集整理 , 小的料 豆等则采 用废料 盒结 构 , 便 而 生 产 完后 再进 行 清 理 , 便操 作从而 降低 整车 的制作 成本 , 并保证
制件的冲压质量及模具使用寿命。 为保证 冲压件 的质量及较 高的模具寿命 ,设计时采用周 边 均有搭边 的形式 , 这样 可使条 料顺利人 料 、 出料 , 证操作 保 的稳定性及 生产 效率 。从图 2中可看 出, 制件展开料为异型 , 采用直 排 , 然导致 利用 率很 低 , 为 5 . 必 仅 09%, 图 2 a 所 如 () 示, 因此应采用套裁 的形式 , 才能提高材料 利用率 , 如图 2 b 、 ( )
高强度板汽车零件的工艺设计和模具开发
高强度板汽车零件的工艺设计和模具开发摘要:随着汽车保有量的不断增大,环境污染和能源短缺等问题也越来越严重。
人类为了可持续发展,必须高度重视环保和节能问题,而通过汽车轻量化,可以实现节能减排,其中高强度钢板一种常见的轻量化方法。
为此,本文对高强度板汽车零件的工艺设计和模具开发设计进行了相关的探究。
关键词:高强度板;工艺设计;模具开发现代汽车的结构、性能及技术方面正朝着减重、节能减排及安全方向发展。
而汽车的质量与能耗之间成线性关系,相关资料显示,每降低1%的汽车质量,则随之可降低0.6%~1.0%的燃耗,能耗也和尾气排放的关系十分密切。
所以,为了节能和环保,汽车可以适当轻量化。
为了可以满足现代汽车制造的要求,板料供应商设计开发了强度高、成型性好的高张力钢板。
而板料性能却是影响汽车零件成型性能和以及模具使用寿命的主要因素,同时板料强度的大幅提升也对冲压工艺与模具开发提出了更高的要求。
基于此,下文进行相关研究分析。
1 高强板汽车零件的冲压工艺设计1.1 拉延(1)拉伸深度应尽可能均匀。
针对断面深度不同的零件,相较于普通钢板,高强钢板采用的拉延深度应更深,使最深断面处的材料可以满足流动要求。
(2)高强度钢板的延伸率较低,针对某些材料/产品,可以采用压型成型,比如车门的防撞梁等。
虽然可能会减小回弹,但是却使制件的扭曲风险提高了。
对于高强度钢板零件,需要尽可能一次成型,否则,由于应力强化致使二拉或整形较易产生破裂、回弹或扭曲,进而使形状不理想。
(3)为了防止压边圈起皱、充分成型,在拉伸高强钢板时,应适当增大压边力。
若压边力过小则可能会使压边圈起皱,甚至顶起整个压边圈,进而消除流料约束力。
(4)锌铁合金不能作为钢板的软模材料,建议采用铸铁或45#钢板。
(5)针对地板横梁、顶盖加强梁、中柱加强板及前仓纵梁等零件,应考虑采用落料后成型工艺。
(6)如果高强钢板的形状变化严重或侧壁强度的均匀度不高,则应采用拉伸成型工艺,并配合修边工艺。
汽车冲压模具的结构组成
汽车冲压模具的结构组成一、汽车冲压模具结构组成概述汽车冲压模具啊,那可真是汽车制造里超级重要的一部分呢!就像盖房子的砖头一样基础又关键。
它的结构组成有好多有趣的部分哦。
二、主要结构部分1. 工作零件这部分就像是模具的心脏。
比如说冲头和凹模,冲头就像一个勇往直前的小战士,负责对材料进行冲压动作,而凹模呢,就像一个温柔的小窝,等着冲头把材料压进来,它们俩配合得可好了,才能把汽车零件的形状冲压出来。
这俩的形状和尺寸都得特别精确,要是有一点点偏差,那冲压出来的汽车零件可就成“歪瓜裂枣”啦。
2. 定位零件这就好比是模具里的小导航。
它的任务就是确保材料在冲压的时候待在正确的位置。
要是没有定位零件,那材料在冲压的时候就会像喝醉了酒的小虫子一样到处乱晃悠,这样冲压出来的零件肯定是不符合要求的。
比如说定位销和定位板,它们就牢牢地把材料固定在该在的地方,让冲压工作顺利进行。
3. 卸料零件卸料零件呢,就像是模具里的小管家。
在冲压完成后,它就负责把冲压后的零件或者废料从模具上清理掉。
如果没有卸料零件,那冲压后的零件可能就卡在模具里出不来,废料也会堆积在模具里,这样模具就没办法进行下一次冲压了,就像一个人吃饱了东西不消化一样难受。
像卸料板就是很常见的卸料零件啦。
4. 导向零件这部分就像是模具的小轨道。
它保证了冲头和凹模在冲压过程中能够准确地对合。
就像火车在铁轨上行驶一样,如果没有导向零件,冲头和凹模可能就会“跑偏”,那冲压出来的零件就会出现厚度不均匀之类的问题。
导柱和导套就是导向零件的典型代表。
5. 模架模架就像是模具的骨架。
它把模具的各个部分都支撑起来,给其他零件提供一个稳定的工作环境。
就像我们人如果没有一个好的骨架,就站不稳一样,模具要是没有模架,其他零件也没办法好好工作啦。
模架一般是由上下模板、模柄等部分组成的。
三、结构之间的协同工作这些结构部分可不是各自为政的哦,它们就像一个超级团队一样协同工作。
当汽车冲压模具开始工作的时候,定位零件先把材料稳稳地固定好,就像给材料找了个专属座位。
轿车中高强度板冲压工艺分析及模具设计与调试new
轿车中高强度板冲压工艺分析及模具设计与调试Automobile’s Stamping Technological Analysis of the high intensity plank with Die design and debugging.孔玉民KONG Yu-min河北隆泰模具有限公司Hebei Long Tai pattern limited company摘要:根据我国汽车工业的发展,以及国外各类车型,进入我国市场,汽车的新技术、新工艺、新材料更新加快。
原有车身材料不适应新时代的需求,逐渐被新的材料取代(通称:高强度板)。
该零件是轿车车顶内侧加强板,产品要求成型后,型面变型小,不扭曲等现象。
针对本零件材料是高强度板,具有较高的强度和韧性,塑性变形小,回弹大等特性。
分别对零件的成形、拉延进行工艺分析,阐述成形拉延的平衡应力、应变状态,制定出合理工艺方案及模具结构,制造出合格零件。
Abstract: According to the our country automobile industrial of development, and foreign each kind of car type, enter our country market, automobile of new technique, new craft, new the material renewal speed.The original carriage material is unwell at the request of modern ear, was gradually replace by the new material( general name for:High intensity plank).That spare parts is a seamy side of the car to strengthen the plank, after product request to model, the type faces to distort little, no distortion, etc. characteristic.Aim at this spare parts material is a high intensity plank, having the higher intensity and tenacities, plastic distortion little, elasticity big etc. Take shape, pull to postpone to carry on the craft analysis to the spare parts respectively, balance that elaborates to take shape to pull to postpone should dint, the contingency appearance, draw up a reasonable craft project and the molding tool structure, make a qualified spare parts.关键词:高强度板成形拉延应力、应变模具设计回弹Keywords: high intensity plank; plastic distortion; stress; strain; forming; drawing; die designing.前言:零件形状特点:料厚:0.7㎜长917㎜宽311㎜高35㎜材料:B340/590 DP,零件净重0.7㎏。
- 1、下载文档前请自行甄别文档内容的完整性,平台不提供额外的编辑、内容补充、找答案等附加服务。
- 2、"仅部分预览"的文档,不可在线预览部分如存在完整性等问题,可反馈申请退款(可完整预览的文档不适用该条件!)。
- 3、如文档侵犯您的权益,请联系客服反馈,我们会尽快为您处理(人工客服工作时间:9:00-18:30)。
一、概述
迈腾
70%
本田雅阁 340MPa以上 48%
车型 FIAT 500 Opel corsa Mercedes Cclass Ford Mondeo Volvo V70 Audi A5
7
高强钢比例 65% 68% 70% 60% 69% 68%
2014-03
马自达6睿翼 590~1480MPa 49% 보고계획
微增大卸载回弹,但对于有底 凹模或带顶出器弯曲时,w 的
大小对卸载回弹影响不明显。
보고계획
16
1 w 25 2 1 w 20 2 1 w 15 2 1 w 10 2
凹模跨度对回弹的影响
2014-03
二、汽车用高强板零件工艺设计 ● 拉弯深度h 与拉深变形不同,由于没有 周向压缩,拉弯深度h 越大,侧 直边中弹性变形积累越多,卸载 后产生的回弹也相对增大了。 过大h 拉弯,不仅侧直边刚 度不足导致其本身弹性回复,而 且降低了法兰直边与凸模底部的 平行度。这种情况下,可考虑适 当加大压料力以增强侧直边成形 刚度。
(二)模具调试
보고계획
2 2014-03
一、概述 汽车自诞生以来,已经走过了风风雨雨的一百多年。汽车的性能和外 观发生了翻天覆地的变化。当今的车身部件大多采用钢板冷冲压成形,对 其尺寸偏差、表面质量和刚性的要求极为严格。车身作为汽车的重要组成 部分其质量占汽车总质量的30%-40%,占整车成本的20%以上。
由上表可以看出,高强钢板的σs和σb比低碳钢板高得多,而n值和r
值却比较低,因此高强钢板的成形性能比低碳钢板差,成形极限比低碳
钢板小。高强钢板虽与低碳钢板一样具有破裂和起皱问题,但由于σs和 σb高,n值和r值低,影响贴模性的几何面缺陷和定形性问题更为突出。
因此要保证高强钢板的冲压质量,不仅要避免破裂和起皱问题,更重要
보고계획
5 2014-03
一、概述
2012年国内汽车产销1900万辆,预测2013年国内汽车产销将达到1960万 辆。 07年国内汽车车身高强板应用为14%-17%左右,超高强板应用为0, NCAP碰撞安全系数多为3星。国外车身高强板应用为50%以上,超高强 板应用为6%-7% , NCAP碰撞安全系数为5星。
3°-6°
⑤、增大压料板压力
⑥、产品侧壁增加加强筋
보고계획
22 2014-03
二、汽车用高强板零件工艺设计 ⑦、二次弯曲
一次压弯
二次压弯
零件脱模后
压料板 压料板 压弯凸模
压弯凹模
第1次弯曲R部
压弯凸模 一次压弯 向纵壁移动 第1次弯曲R部 向纵壁移动 二次压弯
1次的弯曲 1次的弯曲
보고계획
23 2014-03
보고계획
20 2014-03
二、汽车用高强板零件工艺设计
⑤、材料对角度变化的影响 a)、材料强度的影响 U形件在弯曲加工过程中抗拉强度σb和屈服强度σs的影响。经 过对实际生产调试跟踪调查显示,随着抗拉强度和屈服强度的增加 ,角度的变化(回弹)就越大,这是由于随着抗拉强度和屈服强度 的增加,板厚表里应力的弯曲力矩也呈线性增加的缘故。
보고계획
3 2014-03
一、概述
安全性成为汽车最重要 的评价指标,很多国家 都拥有自己的车身碰撞 安全检测机构。
中国新车评价规程
日本JNCAP 欧洲NCAP碰撞标准
美国高速公路安全协会 国际上广泛采用高强度钢板 提高了车体的抗凹陷性、耐 久强度和大变形冲击强度安 全性。
性能比较 低碳钢板 高强钢板 屈服强度 ( σ s /MPa ) <250
二、汽车用高强板零件工艺设计
(一)、高强钢板和普通低碳钢板性能比较
屈服强度 ( σs /MPa ) 低碳钢板 高强钢板 <250 可达400以上 抗拉强度 指数 (n) 0.2-0.26 0.10-0.18 各项异性指 数(r) 1.0-1.8 0.9-1.2
减轻侧壁回弹。 ● 凹模圆角半径rd对回弹的影响 减小rd可增强侧壁刚度并减小
回弹,但在较大压料力情况下拉弯,有时可能导致法兰负回弹。
R=15mm R=20mm R=10mm
R=15mm R=10mm R=5mm
보고계획
15 2014-03
二、汽车用高强板零件工艺设计
●
凸、凹模间隙δ
16 14 12 10 8 6 4 2 0 -2 -4 -6 -8 1.0 1.2
보고계획
18 2014-03
压弯成形时的应力状态
零件脱模后的应力状态
二、汽车用高强板零件工艺设计 1)、模具形状和产品形状对回弹的影响: 如图所示:这是一个简单U 型件压弯示意图 Rp:凸模圆角半径。Rd:凹模圆角半径。C:凸模与凹模间隙。 ①、凸模圆角半径的影响 凸模圆角半径越小角度变化越小,当凸模圆角半径为零时,其角度 变化为零。凸模圆角半径越大其角度变化就越大。变形机理是弯曲半径 小时,其圆角处的塑性变形量大,所以促进了加工硬化。反之弯曲半径 大时,由于塑性变形量小,而使加工硬化变少。 ②、凹模圆角半的影响 在U形件弯曲过程中, 当凹模圆角半径变大时,弯 曲支点间距离大,在初期成 形过程中形成的弯曲范围扩 大,这个被弯曲的范围,随 着成形的进展,被弯曲回复 보고계획
一、概述
超高强钢板 高强度TRIP钢 800MPa 高强钢板 HSLA钢 C-Mn钢 普通钢板 270MPa 低碳钢 部分DP钢 BH钢 TRIP钢 CP钢
DP钢 马氏体钢 TWIP钢 车门防撞杆、保险杠和B柱
骨架件
低强度IF钢
外覆盖件
보고계획
8 2014-03
一、概述
보고계획
9 2014-03
보고계획 可达400以上
澳大利亚ANCAP
抗拉强度 ( σ b /MPa ) <400 可达900以上
4
硬化指数 (n ) 0.2-0.26 0.10-0.18
各项异性指数 (r ) 1.0-1.8 0.9-1.2
2014-03
一、概述 减轻汽车自重是节约能源和提高燃料经济性的最基本途径之一。 研究显示,若汽车整车重量降低10%,燃油效率可提高6%至8%;汽车 每减少100kg,百公里油耗可降低0.3至0.6升,二氧化碳排放量可减 少约5g/km。 汽车的轻量化不仅可以减小汽车的滚动阻力、加速阻力和爬坡阻 力降低燃油消耗,而且也有利于改善汽车的转向加速、制动等多方面 的性能,同时还可以降低噪声振动污染。 降低汽车重量的方法有很多种。 采用高强度钢板车身,在等强度设计 条件下可以减少板厚及重量。钢板厚 度分别减小0.05mm、0.1mm和0.15mm时, 车身分别减重6%、12%和18%。
果r0°越大,宽向变形大、厚向变
形小,切向变形不充分使卸载回弹 增大。
보고계획
13
厚向异性系数R00
2014-03
二、汽车用高强板零件工艺设计
●
压边力对回弹的影响
7
自由弯曲时,弯曲切向变形 不充分,卸载回弹较大。利用压 料力拉弯成形时,可增大切向拉 变形量,减小或消除板厚弹变形 区域,减小卸载回弹。DP600高 强板V形件拉弯的有限元模拟结 果显示,随压料力增大,卸载回 弹明显减小。
回弹角/°
6 5 4 3 2 1 0 0 t0 =1mm R/t0 =10 20 40 60
模拟值
80
100
压边力/KN
보고계획
14 2014-03
二、汽车用高强板零件工艺设计 ● 凹模底圆角半径rda对回弹的影响 凹模底角半径rda大,U形件底
部变形程度减弱,侧直边的回弹明显增大;减小rda可增强镦死效果,
2 / r / 1 r
ω=π/2+θ (r=1,2,3)
在冲压深度与板宽比h0/b0=4.5、
-2.8 -3.0 -3.2 -3.4 -3.6 0.0 0.5 1.0 1.5 2.0 2.5 3.0 b0=10mm t0=1mm R/t0=10
R/t0=10的条件下, 有限元模拟结
二、汽车用高强板零件工艺设计 产品名称:加强梁 材料DP600 料厚1.2
汽车高强板梁类零件冲压工艺及模具结构设计
一汽模具制造有限公司
보고계획
1
张云山 2014.03.23
2014-03
一、概述
二、汽车用高强钢板梁类零件工艺设计
(一)、高强钢板和普通低碳钢板性能比较 (二)、高强板梁类零件冲压尺寸精度问题的分类 (三)、高强板梁类零件影响冲压尺寸精度问题因素及 发生机理 (四)、工艺方案设计 三、模具结构设计和调试 (一)模具结构设计
보고계획
17 2014-03
20 30 40 50
二、汽车用高强板零件工艺设计
2、回弹(角度变化)产生的机理:
简单压弯梁类零件产生回弹的机理 :压弯类零件基本都是几何形状比较简 单的零件,他们在实际生产中所产生的 缺陷基本都是角度变化缺陷,角度变化 产生的原理,图示出的是在简单U字形弯 曲成形时,在R部的角度变化例子。从图 中可以看见,在弯曲成形中,在弯曲圆 角外部,材料由于伸长而产生拉伸的应 力,而在弯曲圆角内部,材料由于压缩 ,又产生了压缩的应力。但是在零件脱 模后,由于存在弹性变形和板厚内外应 力释放,即发生了力矩,从而产生角度 变化。
的是要想办法解决回弹问题保证零件的形状和尺寸精度。
보고계획
10 2014-03
二、汽车用高强板零件工艺设计 (二)、3
高强钢板在满足尺寸公差方面,与薄钢板的冲压成形和其他加工方法 (机械加工、锻造)有很大不同,这是由于在冲压加工时所产生应力分布 的弹塑性变形对制件尺寸影响很大。因此,工艺方案、成形方法、成形条 件,对冲压成形时的尺寸精度影响非常大。经常看到的典型的尺寸精度问 题有以下几种: 1、回弹(角度变化): 夹着弯曲棱线的二个面的 夹角角度和模具型面角度 不相同的现象。如图所示: 弯曲棱线