连铸技术简介
连铸原理与工艺
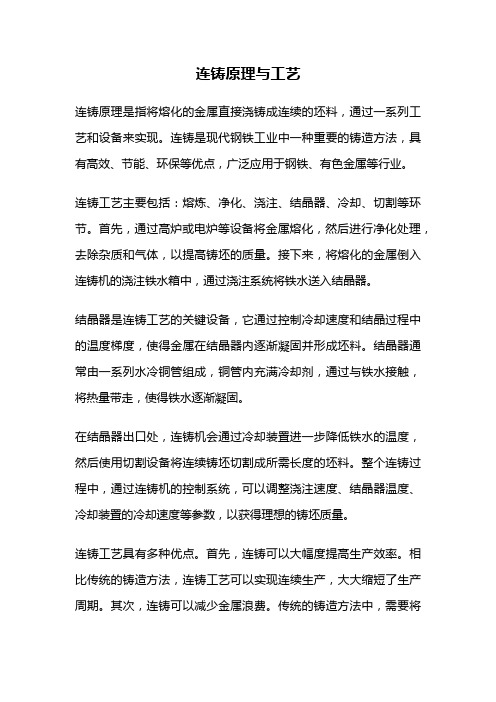
连铸原理与工艺连铸原理是指将熔化的金属直接浇铸成连续的坯料,通过一系列工艺和设备来实现。
连铸是现代钢铁工业中一种重要的铸造方法,具有高效、节能、环保等优点,广泛应用于钢铁、有色金属等行业。
连铸工艺主要包括:熔炼、净化、浇注、结晶器、冷却、切割等环节。
首先,通过高炉或电炉等设备将金属熔化,然后进行净化处理,去除杂质和气体,以提高铸坯的质量。
接下来,将熔化的金属倒入连铸机的浇注铁水箱中,通过浇注系统将铁水送入结晶器。
结晶器是连铸工艺的关键设备,它通过控制冷却速度和结晶过程中的温度梯度,使得金属在结晶器内逐渐凝固并形成坯料。
结晶器通常由一系列水冷铜管组成,铜管内充满冷却剂,通过与铁水接触,将热量带走,使得铁水逐渐凝固。
在结晶器出口处,连铸机会通过冷却装置进一步降低铁水的温度,然后使用切割设备将连续铸坯切割成所需长度的坯料。
整个连铸过程中,通过连铸机的控制系统,可以调整浇注速度、结晶器温度、冷却装置的冷却速度等参数,以获得理想的铸坯质量。
连铸工艺具有多种优点。
首先,连铸可以大幅度提高生产效率。
相比传统的铸造方法,连铸工艺可以实现连续生产,大大缩短了生产周期。
其次,连铸可以减少金属浪费。
传统的铸造方法中,需要将金属熔化后倒入铸型中,过程中会有一定的浪费。
而连铸工艺中,可以直接将熔融金属浇注成坯料,减少了金属的浪费。
此外,连铸还可以提高产品质量。
连铸的结晶过程中,金属凝固速度较快,晶粒细小,可以获得更均匀、致密的铸坯。
最后,连铸工艺对环境友好。
相比传统的铸造方法,连铸工艺中不需要使用砂型和砂芯,减少了对环境的污染。
然而,连铸工艺也存在一些挑战和问题。
首先,连铸过程中会产生较高的温度和压力,对设备和工艺的要求较高。
此外,连铸中还容易产生缺陷,如气孔、夹杂等,需要通过净化和控制工艺参数来解决。
另外,连铸工艺对结晶器的要求较高,结晶器的结构和材料需要经过精心设计和选择,以保证连续铸造的稳定性和质量。
连铸原理与工艺是一种高效、节能、环保的铸造方法,通过熔炼、净化、浇注、结晶器、冷却和切割等环节,将熔化的金属直接浇铸成连续的坯料。
连铸技术的基本原理
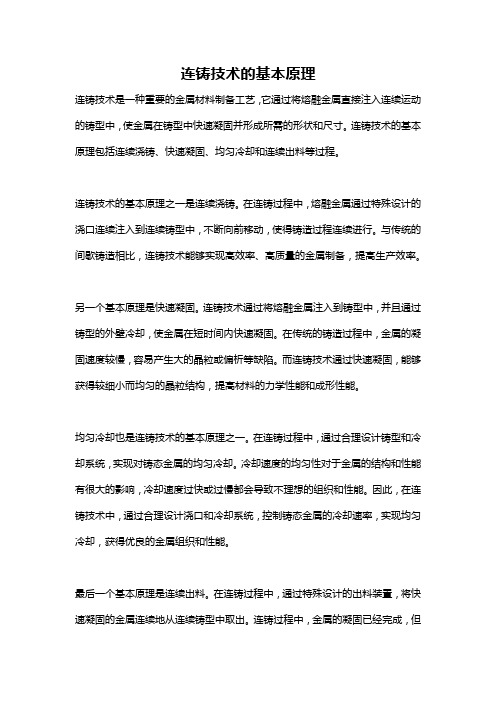
连铸技术的基本原理连铸技术是一种重要的金属材料制备工艺,它通过将熔融金属直接注入连续运动的铸型中,使金属在铸型中快速凝固并形成所需的形状和尺寸。
连铸技术的基本原理包括连续浇铸、快速凝固、均匀冷却和连续出料等过程。
连铸技术的基本原理之一是连续浇铸。
在连铸过程中,熔融金属通过特殊设计的浇口连续注入到连续铸型中,不断向前移动,使得铸造过程连续进行。
与传统的间歇铸造相比,连铸技术能够实现高效率、高质量的金属制备,提高生产效率。
另一个基本原理是快速凝固。
连铸技术通过将熔融金属注入到铸型中,并且通过铸型的外壁冷却,使金属在短时间内快速凝固。
在传统的铸造过程中,金属的凝固速度较慢,容易产生大的晶粒或偏析等缺陷。
而连铸技术通过快速凝固,能够获得较细小而均匀的晶粒结构,提高材料的力学性能和成形性能。
均匀冷却也是连铸技术的基本原理之一。
在连铸过程中,通过合理设计铸型和冷却系统,实现对铸态金属的均匀冷却。
冷却速度的均匀性对于金属的结构和性能有很大的影响,冷却速度过快或过慢都会导致不理想的组织和性能。
因此,在连铸技术中,通过合理设计浇口和冷却系统,控制铸态金属的冷却速率,实现均匀冷却,获得优良的金属组织和性能。
最后一个基本原理是连续出料。
在连铸过程中,通过特殊设计的出料装置,将快速凝固的金属连续地从连续铸型中取出。
连铸过程中,金属的凝固已经完成,但温度较高,通过连续出料并进行后续的热处理,可以获得所需的金属材料。
总的来说,连铸技术的基本原理包括连续浇铸、快速凝固、均匀冷却和连续出料。
这些原理相互作用,使得连铸技术成为一种高效、高质量的金属材料制备方法。
连铸技术的广泛应用,不仅能够提高金属材料的生产效率,提高材料的力学性能和成形性能,还能够减少金属材料的能源消耗和环境污染。
随着现代工业的发展,连铸技术在制造业中的地位和作用将越来越重要,对于推动金属材料制造业的发展具有重要的意义。
连铸的名词解释
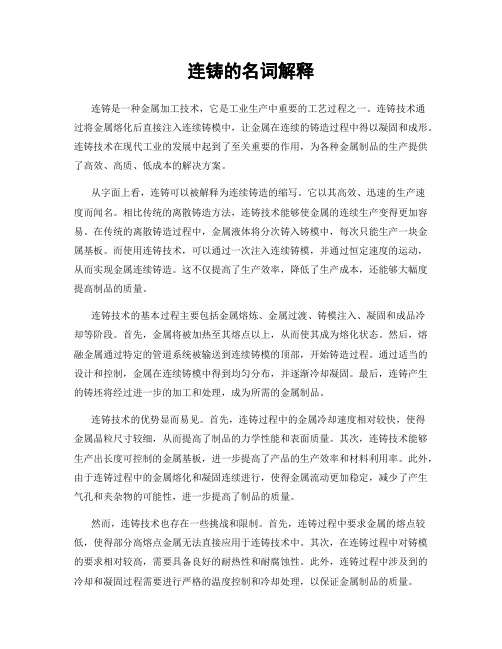
连铸的名词解释连铸是一种金属加工技术,它是工业生产中重要的工艺过程之一。
连铸技术通过将金属熔化后直接注入连续铸模中,让金属在连续的铸造过程中得以凝固和成形。
连铸技术在现代工业的发展中起到了至关重要的作用,为各种金属制品的生产提供了高效、高质、低成本的解决方案。
从字面上看,连铸可以被解释为连续铸造的缩写。
它以其高效、迅速的生产速度而闻名。
相比传统的离散铸造方法,连铸技术能够使金属的连续生产变得更加容易。
在传统的离散铸造过程中,金属液体将分次铸入铸模中,每次只能生产一块金属基板。
而使用连铸技术,可以通过一次注入连续铸模,并通过恒定速度的运动,从而实现金属连续铸造。
这不仅提高了生产效率,降低了生产成本,还能够大幅度提高制品的质量。
连铸技术的基本过程主要包括金属熔炼、金属过渡、铸模注入、凝固和成品冷却等阶段。
首先,金属将被加热至其熔点以上,从而使其成为熔化状态。
然后,熔融金属通过特定的管道系统被输送到连续铸模的顶部,开始铸造过程。
通过适当的设计和控制,金属在连续铸模中得到均匀分布,并逐渐冷却凝固。
最后,连铸产生的铸坯将经过进一步的加工和处理,成为所需的金属制品。
连铸技术的优势显而易见。
首先,连铸过程中的金属冷却速度相对较快,使得金属晶粒尺寸较细,从而提高了制品的力学性能和表面质量。
其次,连铸技术能够生产出长度可控制的金属基板,进一步提高了产品的生产效率和材料利用率。
此外,由于连铸过程中的金属熔化和凝固连续进行,使得金属流动更加稳定,减少了产生气孔和夹杂物的可能性,进一步提高了制品的质量。
然而,连铸技术也存在一些挑战和限制。
首先,连铸过程中要求金属的熔点较低,使得部分高熔点金属无法直接应用于连铸技术中。
其次,在连铸过程中对铸模的要求相对较高,需要具备良好的耐热性和耐腐蚀性。
此外,连铸过程中涉及到的冷却和凝固过程需要进行严格的温度控制和冷却处理,以保证金属制品的质量。
尽管如此,连铸技术在如今的工业生产中扮演了重要的角色。
连铸工艺所应用的技术

连铸工艺所应用的技术连铸技术是一种将液态金属直接凝固成连续铸坯的工艺,它在现代钢铁工业中占据着重要的地位。
连铸技术的发展可以追溯到上世纪中叶,目前已经成为钢铁工业中主要的铸造方法之一。
下面将介绍连铸工艺所应用的一些技术。
首先,连铸工艺需要用到一种特殊的铸造设备,即连铸机。
连铸机是由一系列组件构成的,包括铜模、结晶器、铸坯撑架、牵引设备等。
这些组件相互配合,形成了连续铸造的整套流程。
其中,铜模起到了导热和传导的作用,使得液态金属能够顺利凝固;结晶器则能够冷却铸坯,使其凝固成固态,并控制凝固过程中的温度分布和组织形貌;铸坯撑架用于支撑铸坯,以便于它从结晶器中顺利通过;牵引设备则可以将铸坯拉伸出来,形成所需的铸坯尺寸。
其次,连铸技术在应用过程中需要进行温度和速度的控制。
凝固过程中温度和速度的控制对于铸坯的质量和性能具有重要影响。
一般来说,温度的控制包括了结晶器和冷却水的温度控制、液态金属的供给温度控制等。
而速度的控制则涉及到牵引设备的牵引速度控制等。
通过合理地控制温度和速度,可以确保铸坯的凝固过程和组织形貌的形成,从而得到所需的铸坯性能。
此外,连铸工艺还需要考虑动态过程模拟和数值模拟技术的应用。
动态过程模拟可以利用计算机软件对铸造过程进行模拟,从而优化工艺参数和铸造条件,提高铸坯质量。
数值模拟则可以通过计算流体力学和热传导理论,预测液态金属流动和凝固形貌的变化,为铸造工艺的优化和调整提供依据。
此外,连铸技术在控制质量方面也有许多应用。
连铸机需要配备一套完整的检测系统,用于对铸坯的质量进行在线监测和控制。
这些检测系统包括了温度测量、氧含量测量、流速测量等多项指标的检测和控制,以确保铸坯的质量符合要求。
最后,连铸技术还需要考虑铸坯的切割和后续处理技术。
连铸铸坯通常呈长条状,需要进行切割成所需长度的坯料。
切割方式可以采用火焰切割、机械切割等多种方式,切割过程需要注意切口的质量和尺寸的控制。
切割完成后,铸坯还需要进行一系列后续处理工序,例如表面清理、热处理等,以提高铸坯的性能和质量。
金属冶炼过程中的连铸技术

中大型钢厂由于规模较大,连铸技术 主要用于生产大型钢材和特殊钢材, 如大型矩形坯、板坯、方坯等。
中大型钢厂的连铸技术应用中,通常 采用先进的连铸工艺流程,如电磁搅 拌、结晶器振动、动态二冷等,以提 高产品质量和降低能耗。
中大型钢厂的连铸机通常采用多流形 式,以提高生产效率和降低成本。
不锈钢冶炼的连铸技术应用
06
连铸技术的应用实例
小型钢厂的连铸技术应用
小型钢厂由于规模较小,连铸技 术主要用于生产小型钢坯和钢材 ,如小型圆钢、小型矩形坯等。
由于设备规模较小,连铸机通常 采用单流或双流形式,便于维护
和操作。
小型钢厂的连铸技术应用中,通 常采用传统的连铸工艺流程,如 钢水注入、结晶器冷却、二次冷
却等。
中大型钢厂的连铸技术应用
板坯连铸技术主要用于生产薄板和钢板,广泛应用于汽车、船舶、建筑、家电等 领域。
板坯连铸技术的优点包括高精度、高质量、高效率等,是现代金属板材制造的重 要技术之一。
圆坯连铸技术
圆坯连铸技术主要用于生产圆形的钢坯,主要应用于石油、 化工、电力等领域。
圆坯连铸技术的优点包括高效率、低成本、节能环保等,是 现代圆形结构件制造的重要技术之一。
智能化与自动化
智能化
随着人工智能和大数据技术的应用,连铸技术正朝着智能化方向发展。通过建立智能化监控系统,实 时监测生产过程,对异常情况自动预警和处理,提高生产安全性和稳定性。
自动化
自动化是提高连铸生产效率和产品质量的重要手段。通过自动化设备、机器人和自动化控制系统,实 现连铸生产过程的自动化操作,减少人工干预,提高生产效率。
05
连铸技术的发展趋势
高效化与节能化
高效化
随着技术的不断进步,连铸技术正朝着提高生产效率和降低能耗的方向发展。 通过优化工艺参数、改进设备结构和采用先进的控制技术,实现连铸生产的高 效化,提高铸坯质量和产量。
连铸工艺要点

连铸工艺要点连铸工艺是指连续铸造技术,是铁合金、钢铁等冶金行业中的一种主要生产工艺。
其工艺特点是连续铸造、高效能、高品质、节能环保等。
下面我们来了解一下连铸工艺的要点。
1. 连铸设备连铸设备是连铸工艺的核心,由铸机、结晶器、引伸器、切割机、输送机等组成。
铸机是整个设备的主体,结晶器是铸机的核心部分,引伸器是为了延长铸坯结晶器内的结晶长度,切割机是将连续铸坯切割成长度符合要求的坯料,输送机将坯料送到后续加工工序。
2. 连铸模具连铸模具是决定铸坯质量和工艺效果的重要因素,也是连铸设备的重要组成部分。
模具材料要求高强度、高温耐用、不易变形。
常用的模具材料有高硅铸铁、高铬铸铁、尿素醛树脂等。
模具结构形式有直立式、倾斜式、水平式等,不同结构形式适用于不同铸造条件。
3. 冷却水系统连铸过程中,冷却水系统起着非常重要的作用。
冷却水系统包括结晶器水口、结晶器壁面、引伸器、切割机等部位的冷却系统。
冷却水系统的稳定性和冷却效果直接影响铸坯的质量。
冷却水的温度、流量、压力等参数的调节需要精细控制。
4. 铸造工艺参数连铸工艺参数的优化对铸坯质量和生产效率有重要影响。
铸造参数包括结晶器冷却、引伸器速度、拉拔速度、切割位置等。
优化铸造参数可以控制铸坯中的缺陷、提高铸坯表面质量、降低成本并提高生产效率。
5. 质量控制质量控制是连铸工艺中的重要环节。
铸坯质量的稳定性和可控性直接影响产品的质量和生产效率。
质量控制包括铸坯表面质量检测、铸坯内部缺陷检测、坯料长度检测等。
不同的质量控制手段需要不同的检测设备和技术支持。
连铸工艺的要点包括连铸设备、连铸模具、冷却水系统、铸造工艺参数和质量控制。
在实际生产中,要根据不同的生产条件和产品要求,综合考虑这些要点,优化工艺流程,提高生产效率和产品质量。
连铸技术

CW W / D W
0.4
h
1 热阻1 热阻2 热阻3 热阻4 热阻5
QC 2 1 q A
3.2影响结晶器传热的因素
3.2.1 结晶器锥度
对大小方坯断面来说,设计具有三维锥度
的结晶器内腔可以增加传热量。而对板坯来说,
仅仅窄面为适应断面收缩带有锥度,而宽面一 般是彼此平行的。窄面锥度要根据浇铸速度和 钢种来调节,而且使通过窄面的热流密度基本 上应与宽面保持一致。
qm 0 273 a Cu2 273 ha a Cu2
4 4
热阻的大小决定于:①结晶器铜板的表面 状态;②润滑剂的性质;③坯壳与铜板间的气
隙大小。
(4)结晶器铜板内部传热。这个过程也是传
导传热过程,其热阻取决于铜的导热系数和铜
板厚度,由于铜板具有良好的导热性,因此这 一过程的热阻是很小的。
△T总=△T1+△T2+△T3+△T4+△T5
△T1出钢过程的温降; △T2出完钢钢水在运输和静臵期间的温降 (1.0~1.5℃/min); △T3钢包精炼过程的温降(6~10℃/min);
△T4精炼后钢水在静臵和运往连铸平台的温降
(5~1.2℃/min); △T5钢水从钢包注入中间包的温降。
2.3 钢水温度控制要点
连铸技术
朱苗勇 东北大学
2003年12月
内容提要
◆ 概 述 ◆ 连铸钢水的温度要求
◆ 连续铸钢的凝固与传热
◆ 中间包冶金 ◆ 连铸坯质量
1 概 述
1.1连铸过程
钢水直接铸成接近最终产品尺寸的钢坯。 这一想法经过一百多年的努力探索,终于使该 技术在本世纪70年代开始大规模用于实际,并 逐步形成了今天的连铸技术。 主要设备由钢包、中间包、结晶器、结晶 器振动装臵、二次冷却和铸坯导向装臵、拉坯 矫直装臵、切割装臵、出坯装臵等部分组成。
连铸技术介绍讲解

引锭杆存放区域
输送辊道区域
输送辊道区域
出坯区域
连铸机出坯区域: 移钢机将冷床辊道上的铸坯移至液压推钢冷床。
移钢机 用途:
移钢机将冷床区辊道上的方坯移至步进翻转冷床上,或将矩形坯移至推钢机 上。
性能: 推头可摆动升降,推钢 主要参数: 横移速度:20 m/min 移钢数量: 160x160mm-9m 5根 150x150mm-9m 5根 传动电机: 功率 22 Kw /台x 2台 推头升降行程: 380 mm
• 纵向走行速度: 2-20m/min
• 纵向走行驱动电机: 7.5Kw 2个/台
• 升降行程:
400 mm
• 升降速度:
1.5 m /min
• 横向调节行程:
100 mm
结晶器振动装置及铸坯 一次及二次冷却区域
结晶器振动装置
结晶器振动装置 • 振动形式:四连杆半板簧机构
• 振动曲线:正弦
主要参数 驱动装置: 电机减速机 振幅: 0~±6mm 振动频率范围:30~300 c/min
主要技术特点及承诺:
1,充分发挥在工厂设计方面的技术实 力,综合考虑连铸机在车间内的合理布 置。
2,综合考虑车间内连铸机的电缆沟、 管廊及旋流井等设施的工艺布置,使之 更为合理,顺畅。
3,统一提出连铸机的各专业工厂设计 资料,达到统一技术管理的目的。
炼钢、连铸工艺参数
•转炉数量: •转炉公称容量: •最大出钢量: •转炉冶炼周期: •连铸机数量: •连铸坯断面:
形式:整体框架 特点: 快速吊装定位
主要参数:
辊径
Ф170 mm材料: 35CrMo
辊子轴承 连铸扇形段专用轴承
轴承间隙 采用C4系列
辊子润滑 油气润滑
- 1、下载文档前请自行甄别文档内容的完整性,平台不提供额外的编辑、内容补充、找答案等附加服务。
- 2、"仅部分预览"的文档,不可在线预览部分如存在完整性等问题,可反馈申请退款(可完整预览的文档不适用该条件!)。
- 3、如文档侵犯您的权益,请联系客服反馈,我们会尽快为您处理(人工客服工作时间:9:00-18:30)。
48 67
48 67
200
265
230
280
1880热轧 (三热轧) 同左
288.5
288.5
96
2050热轧 2050热轧 厚板轧机, (一热轧) (一热轧) 2050热轧 辊道直送 同左 同左
1580热轧 1580热轧 初轧、无缝 (二热轧) (二热轧) 同左 同左 专门运输车
送坯方式
九 、宝钢板坯连铸机情况 前工序条件—设备配置 ▲冶炼设备
12 结晶器电磁技术 13 自动开浇技术
14 高频率小振幅液压振动,可调整振动参数
15 垂直弯曲型连续弯曲、连续矫直连铸机 16 小辊密排、全分节辊 17 辊缝自动测量 ○
○
○ ○ ○
18 气水冷却,宽向冷却自动控制
19 动态轻压下 20 计算机板坯质量判定 21 最佳长度切割计算和控制 22 四面火焰清理机 23 快速硫印和低倍检验 ○ ○
机电成套事业本部
连铸技术
2009年08月
一、冶金生产工艺
钢铁生产的 三大主工序 炼铁厂
铁矿石→铁水
原料场 烧结 高炉
炼钢厂
铁水→铸坯
冶炼
铁水→钢水
脱硫 冶炼 精练 转炉 电炉
轧钢厂
铸坯→钢材
加热炉 初轧 精轧 酸洗 冷轧
高炉
LF CAS KIP VD RH 连铸 钢水→铸坯
方坯 板坯 园坯
线材轧机
三、连铸机分类
按外形分为
1—立式连铸机;2—立弯式连铸机;3—直结晶器多点弯曲连铸机 4—直结晶器弧形连铸机;5—弧形连铸机; 6—多半径弧形(椭圆形)连铸机;7—水平式连铸机
三、连铸机分类
按铸坯断面分
(界定无统一规定,参考目前生产情况确定的尺寸范围)
小方坯连铸机: 断面70×70 ~ 200×200mm
铸机基本半径/mm 铸机长度/mm min-1 拉坯速度Vc/m·
1.3~2.2
同左
2.5
连铸机流间距/mm
6200
6100
九 、宝钢板坯连铸机情况
铸机编号 设置场所
铸机中心距/mm 铸机辊面标高 中间包容量/t 平均连浇炉数/炉 (设计值) 平均浇铸时间 (min/炉) 铸机作业率/% 设计年产量 (万吨/年) 板坯去向 40000 FL+900 60 3.88
► 部分下线铸坯经四面火焰清理机清理后,再进人工火焰清 理机组进行检查清理,称量,送热轧;
四、连铸工艺流程
钢水罐回转台
长水口氩封 盛钢桶下渣检测
宝 钢 股 份 号 连 铸 机 生 产 工 艺 流 程 图 4
气-水冷却 宽向冷却控制 动态轻压下 引锭杆收集装置 去毛刺台车
中间罐
浸入式水口氩封 结晶器液位控制 自动加保护渣 结晶器电磁技术 结晶器液压振动
4号板坯连 铸机
三热轧
宝钢股份4号连铸机精炼工艺路线
十 、部门情况
上海宝信软件股份有限公司
营销本部
机电成套事业本部
自动化事业本部
智能化事业本部 海外软件事业本部
解决方案事业本部
系统服务事业本部
十 、部门情况
机电成套事业本部
机电研究所 新型连铸事业部 机电一体化产品事业部 总包工程市场部
梅山工业民用工程设计研究院
型钢轧机 板带轧机 钢管轧机
COREX
一、冶金生产工艺
炼钢生产 工艺路线
≤80t
在线吹氩喂丝
方坯连铸机
LF
转炉
80~120t
LF、VD
方/异型/板坯铸机
>120t
LF、RH
方/板坯铸机
方/板/薄板坯铸机
电炉
LF、VD/VOD
二、连铸技术的发展
连续铸钢技术:将高温钢水连续直接浇铸成一定形状 的技术,简称连铸。 连铸机:实现将钢水直接浇铸成铸坯的一组设备。 连续技术的发展经历了从上世纪
4人
20人 7人 4人 3人
HRM
Pinch Roll 1 Cooling Table Shear Pinch Roll 2 loop controller Down Coiler
○
○ ○ ○ ○ ○ 利用宝钢现有设施
九 、宝钢板坯连铸机情况
铸机编号 设置场所
厚度/mm 铸坯 规格
1#
2# 一炼钢
3#
4#
5# 二炼钢
6#
7# 电炉厂
8#
210、230、 250
900~1930 8000~12000 1/2
250
220、250、 300
1300~2300 6800~10800 1/2
板坯连铸公辅设施包括:
► 检化验设施:钢水成分分析、连铸坯的硫印和酸浸低倍等宏观检验
► 供配电系统:连铸机及公辅设施的高压供电,提供各电压等级的电源。
► 电气传动控制系统:连铸机及辅助设施等的低压配电,设备的电气传动控
制(传动方式、运转方式、操作方式和数据设立方式),电气室的设置。
► 自动化仪表:连铸机及辅助设施的仪表检测控制。如温度、流量、压力、称
4 5 6
7 8
大容量带挡渣堰的中间罐 中间罐连续测温 浸入式水口快速更换装置
保护浇铸,中间罐开浇前吹Ar,赶走空气 结晶器保护渣自动加入
○
○ ○
○
○ ○ 缓上
9
结晶器在浇铸过程中调宽
○
○ ○
○
10 结晶器液面自动控制 11 结晶器热成像系统(含漏钢预报)
八、连铸机装备水平
序号 项 目 名 称 提高生 提高铸 高温板 产率 坯质量 坯热送 ○ ○ 备 注
指定机清坯 无缺陷坯 热送热装
手工清理
写号 F列辊道 称重
6号机生产 的硅钢
1450mm火焰 清理装置 过跨台车
在线称量 三热轧板坯库
五、板坯连铸工艺设备组成
板坯连铸设备组成包括:
► 起重设备 ► 平台上设备 ► 主机设备 ► 出坯精整设备 ► 中间罐维修设备
► 机械维修设备
六、板坯连铸公辅系统
一炼钢:3×300 t 转炉 二炼钢:3×250t 转炉(可以扩到300t) 电炉厂:2×150t电炉
▲精炼设备
一炼钢:RH、LF、CAS、KIP
二炼钢:RH、LF、IR-UT
电炉厂:LF、VD/VOD
九 、宝钢板坯连铸机情况 前工序条件—钢水精炼工艺路线
LF 1RH 2RH
转炉
IR-UT LF 1RH 2RH 1RH 2RH LF
► 40年代的试验开发
► 50年代开始步入工业生产 ► 60年代弧形铸机的出现 ► 70年代由能源危机推动的大发展 ► 80年代日趋成熟的技术
► 90年代后面临新变革的发展历程。
二、连铸技术的发展
至今,连铸的工艺和设备技术日趋完善,其代表性技术为: ► 钢包回转台实现多炉连浇;
► 快速更换中间罐技术;
重、自动开浇、二次冷却水量控制
► 自动控制系统:大包转台至热轧交接辊道的电气设备,铸坯上、下线的操
作过程。按软件功能划分为L1,基础自动化控制系统,L2过程控制计算机 系统和L3生产控制计算机系统。
► 通讯设施:自动指令系统,有线对讲装置,全厂性专用电话(调度电话、无
线电对讲)、工业电视、起重机通讯系统、火灾自动报警及联动系统
事业本部新产品研发 新型及常规连铸技术集成及EP工程综合服务 机电一体化产品设备设计、供货及运维服务
设计为龙头的钢铁工业全流程工厂设计及设备 EP总包
十 、部门情况
宝信新型连铸 事业部
Ladle
专家+设计人员+管理人员 45人
Tundish
Twin Roll Caster
专 家 总 监
工艺设计室 设备设计室 三电设计室 制造安装综合室 业务室
230
230
230
Φ153、Φ178 、□160*160
宽度/mm 长~1750 9000~11000 1/2
900~1450 8000~11000 1/2
同左 同左 1/2 4000~11000 1/6
铸机台数/流数
机型
垂直弯曲型,垂直弯曲型,垂直弯曲型,垂直弯曲型,垂直弯曲型,垂直弯曲型, 5点弯曲4点 5点弯曲13点 8点弯曲5点 多点弯曲多点 7点弯曲8点 7点弯曲8点 矫直 矫直 矫直 矫直 矫直 矫直 9555 39324.9 1.3~1.5, Max1.8 6100 9555 39392.1 1.0~1.62, Max1.8 6100 10000 34172 0.76~1.52, Max1.7 7200 9500 41354.87 9555 37388 0.8~1.5, Max1.8 6100 9555 37388 10/14/20.5m 17350
四、板坯连铸机工艺流程
四、板坯连铸机工艺流程
四、连铸工艺流程
四、连铸工艺流程
钢水
起重机
回转台
装引锭杆、密封引锭头 中间罐车就位下降对中 钢水罐转至中间罐上方
人工开滑动水口 钢流稳定后装长水口
TD钢水到设定值打开塞棒 自动开浇系统投入
四、连铸工艺流程
钢液过水口孔人工加保护渣 液位检测装置检测到钢液时自动 控制TD水口开口度 测量辊检测板坯长度, 切割机根据检测信号, 对头部、板坯和尾部以 及试样进行切割 引锭杆尾部出水平扇形段 后,被卷扬机提升。当引 锭头与板坯连接处出水平 扇形段后,引锭头与板坯 自动脱离
跟踪尾坯,二冷系统逐段自动关闭 尾坯到规定位置时,进行下一浇次上装引锭杆操作
精整工艺流程
精整工艺流程因产品而已,各厂有所不同,主要环节有:
► 横移台车将两流的铸坯送至精整辊道; ► 质判系统判定无缺陷坯,经目视、称重,直接送至热轧;
► 少量缺陷坯下线堆存空冷,人工清理,送热轧板坯库; ► 部分高温铸坯经四面火焰清理机清理后,称量,送热轧;