焦炭热强度
焦炭热强度测试检测方法
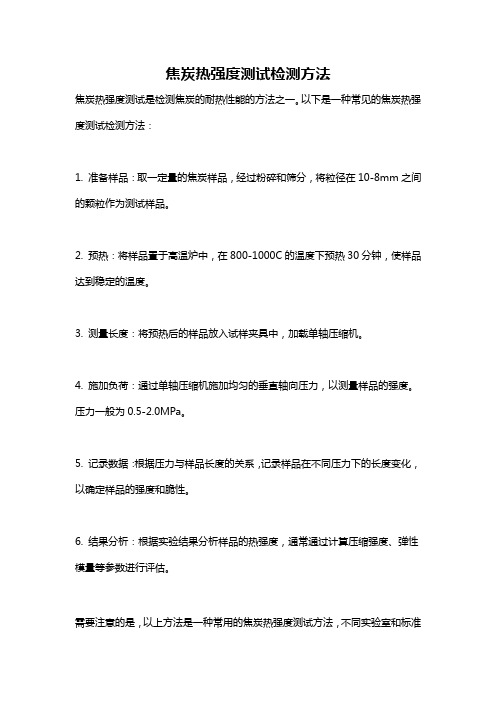
焦炭热强度测试检测方法
焦炭热强度测试是检测焦炭的耐热性能的方法之一。
以下是一种常见的焦炭热强度测试检测方法:
1. 准备样品:取一定量的焦炭样品,经过粉碎和筛分,将粒径在10-8mm之间的颗粒作为测试样品。
2. 预热:将样品置于高温炉中,在800-1000C的温度下预热30分钟,使样品达到稳定的温度。
3. 测量长度:将预热后的样品放入试样夹具中,加载单轴压缩机。
4. 施加负荷:通过单轴压缩机施加均匀的垂直轴向压力,以测量样品的强度。
压力一般为0.5-2.0MPa。
5. 记录数据:根据压力与样品长度的关系,记录样品在不同压力下的长度变化,以确定样品的强度和脆性。
6. 结果分析:根据实验结果分析样品的热强度,通常通过计算压缩强度、弹性模量等参数进行评估。
需要注意的是,以上方法是一种常用的焦炭热强度测试方法,不同实验室和标准
可能会有所不同,具体的测试步骤及参数应根据实际情况和相关标准进行确定。
焦炭热态强度与影响因素分析

焦炭热态强度与影响因素分析随着我国整体经济的增长,钢铁工业也在逐步稳固发展,而焦炭作为钢铁工业中的重要组成部分,它起着骨架、还原剂和热源的作用,随着高炉的大型化,焦炭热态性能对高炉的运转,效率等方面的作用也越来越重要。
近年来,炼焦行业中对焦炭热态性能也是越来越重视,而焦炭的质量相对来说就尤为重要。
本文对焦炭热态强度与影响因素进行全面的分析,希望可以为整个行业乃至社会提供借鉴和帮助。
标签:焦炭;热态性能;影响因素;分析与探讨在整个炼焦行业当中,将焦炭的冷态强度作为衡量焦炭质量非常重要的标准这是长久以来的习惯。
但是,近年来随着高炉的大型化我们发现,焦炭热态强度性能对于高炉的高效率的运行和其他的一些方面更为重要,对于其影响也更为明显,由此本文通过对焦炭热态性能强度与影响的角度来分析问题并提出措施,为行业生产提供理论上的支撑和依据。
1 焦炭热态性能焦炭作为高炉炼铁工艺不可或缺的一个重要燃料,近年来随着高炉的喷吹燃料技术发展和进步,行业中焦炭的质量显的越来越重要,但是我们发现焦比却不断下降,我们会发现焦炭的质量对高炉冶炼的影响越来越明显,也可以这样说焦炭的质量在高炉炼铁工艺中起到的作用越来越重要,同时焦炭也成为限制阻碍高炉生产发展的重要影响因素之一。
用于高炉冶炼的焦炭通常都需要去满足成分、粒度和强度等三个方面的质量要求,比如固定C含量高、灰分低、有害元素的含量低,粒度为40~60mm并且需要均匀,冷强度高等一些质量上的要求。
为了可以保证焦炭在炉内的温度和气氛条件下的抗破碎和磨损的能力,还必须要求焦炭具有一定的热强度和较弱的反应性。
而焦炭的热强度是可以看出其焦炭热态性能的一个机械强度的指标。
它表现焦炭在使用环境的温度和气氛下,同时经受热应力和机械力时,抵抗破碎和磨损的能力。
2 焦炭热态强度与影响因素我们了解到影响焦炭热态强度的影响因素有很多,通过我们的一些试验,再经过分析焦炭反应性以及反应后强度之间的关系,在这个角度去研究焦炭热态强度的影响因素,我们发现焦炭反应性和反应后强度它们之间存在着负相关性,并且焦炭的气孔结构、显微组分和碱金属对焦炭热态强度均会有不同程度的影响。
国标焦炭热强度的取样标准
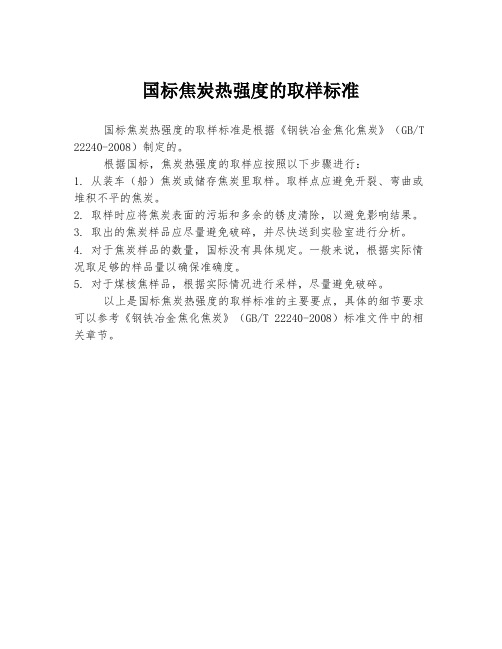
国标焦炭热强度的取样标准
国标焦炭热强度的取样标准是根据《钢铁冶金焦化焦炭》(GB/T 22240-2008)制定的。
根据国标,焦炭热强度的取样应按照以下步骤进行:
1. 从装车(船)焦炭或储存焦炭里取样。
取样点应避免开裂、弯曲或堆积不平的焦炭。
2. 取样时应将焦炭表面的污垢和多余的锈皮清除,以避免影响结果。
3. 取出的焦炭样品应尽量避免破碎,并尽快送到实验室进行分析。
4. 对于焦炭样品的数量,国标没有具体规定。
一般来说,根据实际情况取足够的样品量以确保准确度。
5. 对于煤核焦样品,根据实际情况进行采样,尽量避免破碎。
以上是国标焦炭热强度的取样标准的主要要点,具体的细节要求可以参考《钢铁冶金焦化焦炭》(GB/T 22240-2008)标准文件中的相关章节。
焦煤的热强度指标
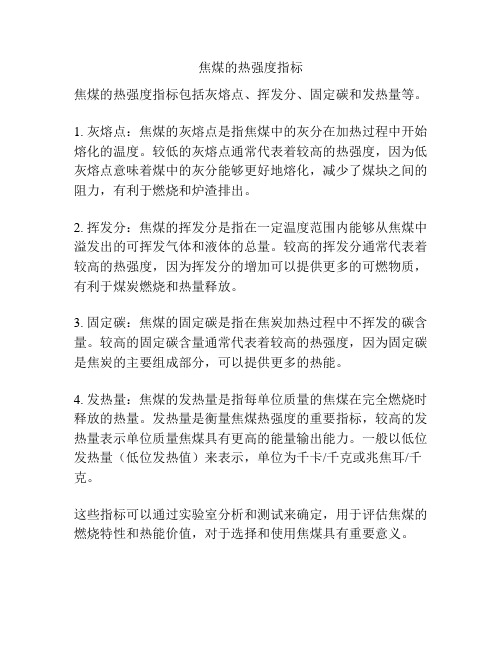
焦煤的热强度指标
焦煤的热强度指标包括灰熔点、挥发分、固定碳和发热量等。
1. 灰熔点:焦煤的灰熔点是指焦煤中的灰分在加热过程中开始熔化的温度。
较低的灰熔点通常代表着较高的热强度,因为低灰熔点意味着煤中的灰分能够更好地熔化,减少了煤块之间的阻力,有利于燃烧和炉渣排出。
2. 挥发分:焦煤的挥发分是指在一定温度范围内能够从焦煤中溢发出的可挥发气体和液体的总量。
较高的挥发分通常代表着较高的热强度,因为挥发分的增加可以提供更多的可燃物质,有利于煤炭燃烧和热量释放。
3. 固定碳:焦煤的固定碳是指在焦炭加热过程中不挥发的碳含量。
较高的固定碳含量通常代表着较高的热强度,因为固定碳是焦炭的主要组成部分,可以提供更多的热能。
4. 发热量:焦煤的发热量是指每单位质量的焦煤在完全燃烧时释放的热量。
发热量是衡量焦煤热强度的重要指标,较高的发热量表示单位质量焦煤具有更高的能量输出能力。
一般以低位发热量(低位发热值)来表示,单位为千卡/千克或兆焦耳/千克。
这些指标可以通过实验室分析和测试来确定,用于评估焦煤的燃烧特性和热能价值,对于选择和使用焦煤具有重要意义。
焦炭反应后强度和热强度

焦炭反应后强度和热强度全文共四篇示例,供读者参考第一篇示例:焦炭是一种高度含碳的固体燃料,通常用于冶金和煤化工生产中。
在燃烧过程中,焦炭会发生一系列化学反应,这些反应不仅会影响焦炭的强度,还会影响其热强度。
本文将探讨焦炭反应后的强度和热强度,并分析其对焦炭质量和应用的影响。
焦炭在高温下燃烧时,会发生一系列氧化反应,主要包括碳氧化反应和硫氧化反应。
碳氧化反应是指焦炭中的碳与氧气反应生成二氧化碳或一氧化碳,这些气体会随着燃烧过程释放出来。
硫氧化反应则是指焦炭中的硫与氧气反应,生成二氧化硫或三氧化硫,这些气体也会排放到大气中。
这些氧化反应会导致焦炭的质量和强度下降,因为碳和硫的氧化产物会使焦炭失去一定的燃料价值。
除了氧化反应外,焦炭还可能发生其他化学反应,如焦炭的煤化学反应和水解反应。
焦炭的煤化学反应是指焦炭中的有机物质与热解副产物反应,可能生成一些气体和液体产物。
水解反应则是指焦炭中的水分与焦炭中的氢气或氧气反应,可能生成一些氢气和二氧化碳等产物。
这些化学反应会影响焦炭的热强度,因为产生的气体和液体会影响焦炭的热值和燃烧性能。
焦炭的强度主要受其化学成分和结构特征的影响。
一般来说,焦炭的密度越高、孔隙率越低、结晶度越高,其强度也会越高。
焦炭在高温下燃烧时,会发生一些热化学反应,如焦炭的炭化、气化和熔化等反应。
这些热化学反应会改变焦炭的结构和形貌,进而影响其强度。
焦炭的炭化反应是指焦炭中的有机物质被高温裂解生成炭质颗粒,这些颗粒会填充焦炭中的孔隙,增加焦炭的密度和强度。
焦炭的热强度主要由其热值和燃烧性能决定。
热值是指单位质量焦炭完全燃烧释放的热量,通常以焦炭的高位发热值或低位发热值表示。
高位发热值是指焦炭完全燃烧时释放的热量,不考虑燃烧产物中的水蒸气凝结热。
低位发热值则是指焦炭完全燃烧时释放的热量,考虑了水蒸气凝结热。
燃烧性能主要取决于焦炭的燃烧速度、燃烧温度和热值。
在焦炭生产和应用过程中,焦炭的强度和热强度至关重要。
焦炭的强度
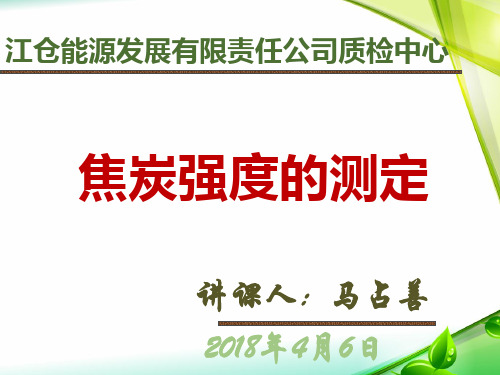
焦炭强度的测定
讲课人:马占善 2018年4月6日
焦炭强度的测定
01
测定焦炭强度的意义
02
焦炭的冷强度(机械强度)
03
焦炭的热强度(CRI和CSR)
Contents
目录Leabharlann Chapter 1焦炭强度的测定意义
1 Chapter
焦炭强度的测定意义
1、焦炭在高炉中的作用:主要是起骨架作用、还原剂、和供热源。 2、M40,主要模拟焦炭在高炉中的骨架硬度和运输过程中的抗碎强度,指标服务于焦炭在 高炉中的应用,主要是焦块从高炉料钟落下到料柱上面和落下后再承受下批原料落下时的 冲击,以及焦块在块状带阶段承受的压力具有一定的模拟性。 3、M10,耐磨强度,它主要与焦炭的气孔壁厚度和焦炭的强度有关,测试中磨损源于焦块 之间、焦块与鼓壁之间的磨损。它对于焦块处于高炉块状带阶段,焦块与焦块、焦块与矿 石、焦块与炉壁之间,在自上而下的移动过程具有良好的模拟性。 4、CRI,在块状带下部,铁矿石中的铁氧化合物与上升炉气中的CO发生间接反应生成CO2, 温度高于800℃时,焦炭产生明显的气化反应生成CO,这种消耗称为碳溶损失。软溶带和 滴落带碳溶反应剧烈,CRI主要测定碳溶反应。 5、CRS.主要测定焦炭在软溶带和滴落带承受的压力的能力,对高炉生产具有较高的指导 价值。
焦炭的热强度(CRI和CSR)
反焦 焦炭的反应性CRI:
应炭 称取一定质量的焦炭式样,置于反应器中没在 1100℃+-5℃时与CO2反应2H后,以焦炭损失
后 的百分数表示焦炭反应性CRI, CRI越小越好
强度﹛反应性 反应后强度CSR:
及
反应后的焦炭经I型转鼓试验后,以大于10mm 粒级的焦炭占反应后焦炭的质量分数表示 焦炭反应后强度CSR, CSR越大越好
国标焦炭热强度的取样标准
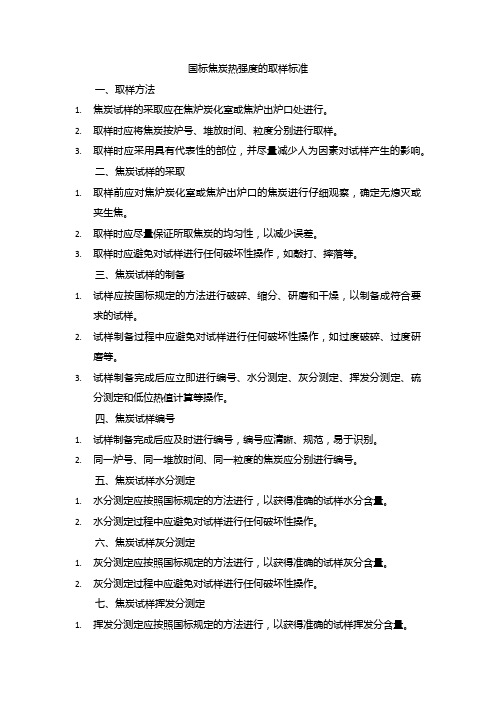
国标焦炭热强度的取样标准一、取样方法1.焦炭试样的采取应在焦炉炭化室或焦炉出炉口处进行。
2.取样时应将焦炭按炉号、堆放时间、粒度分别进行取样。
3.取样时应采用具有代表性的部位,并尽量减少人为因素对试样产生的影响。
二、焦炭试样的采取1.取样前应对焦炉炭化室或焦炉出炉口的焦炭进行仔细观察,确定无熄灭或夹生焦。
2.取样时应尽量保证所取焦炭的均匀性,以减少误差。
3.取样时应避免对试样进行任何破坏性操作,如敲打、摔落等。
三、焦炭试样的制备1.试样应按国标规定的方法进行破碎、缩分、研磨和干燥,以制备成符合要求的试样。
2.试样制备过程中应避免对试样进行任何破坏性操作,如过度破碎、过度研磨等。
3.试样制备完成后应立即进行编号、水分测定、灰分测定、挥发分测定、硫分测定和低位热值计算等操作。
四、焦炭试样编号1.试样制备完成后应及时进行编号,编号应清晰、规范,易于识别。
2.同一炉号、同一堆放时间、同一粒度的焦炭应分别进行编号。
五、焦炭试样水分测定1.水分测定应按照国标规定的方法进行,以获得准确的试样水分含量。
2.水分测定过程中应避免对试样进行任何破坏性操作。
六、焦炭试样灰分测定1.灰分测定应按照国标规定的方法进行,以获得准确的试样灰分含量。
2.灰分测定过程中应避免对试样进行任何破坏性操作。
七、焦炭试样挥发分测定1.挥发分测定应按照国标规定的方法进行,以获得准确的试样挥发分含量。
2.挥发分测定过程中应避免对试样进行任何破坏性操作。
八、焦炭试样硫分测定1.硫分测定应按照国标规定的方法进行,以获得准确的试样硫分含量。
2.硫分测定过程中应避免对试样进行任何破坏性操作。
九、焦炭试样低位热值计算1.低位热值计算应根据国标规定的方法进行,以获得准确的试样低位热值。
2.低位热值计算过程中应避免对试样进行任何破坏性操作。
十、焦炭试样热强度分级1.热强度分级应根据国标规定的方法进行,以获得准确的试样热强度等级。
2.热强度分级过程中应避免对试样进行任何破坏性操作。
焦炭热强度
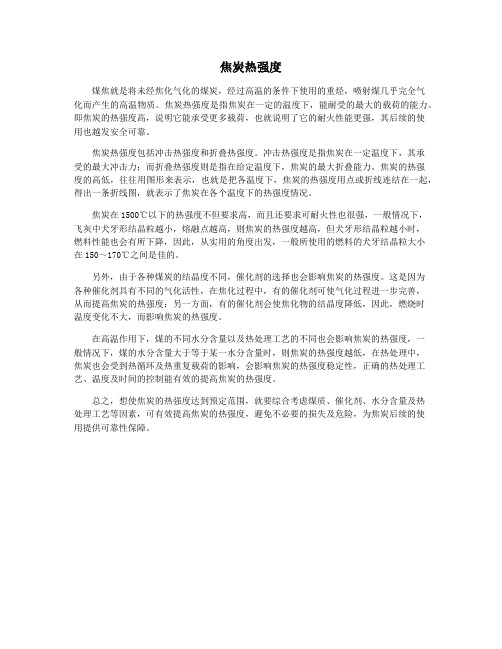
焦炭热强度煤焦就是将未经焦化气化的煤炭,经过高温的条件下使用的重烃,喷射煤几乎完全气化而产生的高温物质。
焦炭热强度是指焦炭在一定的温度下,能耐受的最大的载荷的能力。
即焦炭的热强度高,说明它能承受更多载荷,也就说明了它的耐火性能更强,其后续的使用也越发安全可靠。
焦炭热强度包括冲击热强度和折叠热强度。
冲击热强度是指焦炭在一定温度下,其承受的最大冲击力;而折叠热强度则是指在给定温度下,焦炭的最大折叠能力。
焦炭的热强度的高低,往往用图形来表示,也就是把各温度下,焦炭的热强度用点或折线连结在一起,得出一条折线图,就表示了焦炭在各个温度下的热强度情况。
焦炭在1500℃以下的热强度不但要求高,而且还要求可耐火性也很强,一般情况下,飞灰中犬牙形结晶粒越小,熔融点越高,则焦炭的热强度越高,但犬牙形结晶粒越小时,燃料性能也会有所下降,因此,从实用的角度出发,一般所使用的燃料的犬牙结晶粒大小在150~170℃之间是佳的。
另外,由于各种煤炭的结晶度不同,催化剂的选择也会影响焦炭的热强度。
这是因为各种催化剂具有不同的气化活性,在焦化过程中,有的催化剂可使气化过程进一步完善,从而提高焦炭的热强度;另一方面,有的催化剂会使焦化物的结晶度降低,因此,燃烧时温度变化不大,而影响焦炭的热强度。
在高温作用下,煤的不同水分含量以及热处理工艺的不同也会影响焦炭的热强度,一般情况下,煤的水分含量大于等于某一水分含量时,则焦炭的热强度越低,在热处理中,焦炭也会受到热循环及热重复载荷的影响,会影响焦炭的热强度稳定性,正确的热处理工艺、温度及时间的控制能有效的提高焦炭的热强度。
总之,想使焦炭的热强度达到预定范围,就要综合考虑煤质、催化剂、水分含量及热处理工艺等因素,可有效提高焦炭的热强度,避免不必要的损失及危险,为焦炭后续的使用提供可靠性保障。
- 1、下载文档前请自行甄别文档内容的完整性,平台不提供额外的编辑、内容补充、找答案等附加服务。
- 2、"仅部分预览"的文档,不可在线预览部分如存在完整性等问题,可反馈申请退款(可完整预览的文档不适用该条件!)。
- 3、如文档侵犯您的权益,请联系客服反馈,我们会尽快为您处理(人工客服工作时间:9:00-18:30)。
焦炭热强度
是反映焦炭热态性能的一项机械强度指标。
它表征焦炭在使用环境的温度和气氛下,同时经受热应力和机械力时,抵抗破碎和磨损的能力。
焦炭的热强度有多种测量方法,其中一种是热转鼓强度测定。
测量焦炭的热转鼓强度,一般是将焦炭放在有惰性气氛的高温转鼓中,以一定转速旋转一定转数后,测定大于或小于某一筛级的焦炭所占的百分率,以此表示焦炭热强度。
焦炭反应性焦炭反应性是焦炭与二氧化碳。
氧和水蒸气等进行化学反应的能力,焦炭反应后强度是指反应后的焦炭在机械力和热应力作用下抵抗碎裂和磨损的能力。
焦炭在高炉炼铁。
铸造化铁和固定床气化过程中,都要与二氧化碳。
氧和水蒸气发生化学反应。
由于焦与氧和水蒸气的反应有与二氧化碳间的反应相类似的规律,因此大多数国家都用焦炭与二氧化碳间的反应特性评定焦炭反应性。
中国标准GB/T4000-1996规定了焦炭反应性及反应后强度试验方法。
其做法是使焦炭在高温下与二氧化碳发生反应,然后测定反应后焦炭失重率及其机械强度。
焦炭反应性指标以损失的焦炭质量与反应前焦样总质量的百分数表示。
焦炭反应性按下式计算:
CRI=(m-m1)/m×100
式中:CRI-焦炭反应性,%
m-焦炭试样质量,g
m1-反应后残余焦炭质量,g。
焦炭反应后强度指标以转鼓后大于10mm粒级焦炭占反应后残余焦炭的质量百分数表示。
反应后强度按下式计算:
CSR=m2/m1×100
式中:CSR-反应后强度,%
m2-转鼓后大于10mm粒级焦炭质量,g
1
m1-反应后残余焦炭质量,g。
焦炭反应性CRI及反应后强度CSR的重复性,不得超过下列数值:
CRI:r≤2.4%
CSR:r≤3.2%
焦炭反应性及反应后强度的试验结果均取平行试验结果的算术平均值。
焦炭反应性与二氧化碳、氧和水蒸气等进行化学反应的能力,焦炭反应后强度是指反应后的焦炭再机械力和热应力作用下抵抗碎裂和磨损的能力。
焦炭在高炉炼铁、铸造化铁和固定床气化过程中,都要与二氧化碳、氧和水蒸气发生化学反应。
由于焦与氧和水蒸气的反应有与二氧化碳的反应类似的规律,因此大多数国家都用焦炭与二氧化碳间的反应特性评定焦炭反应性。
中国标准(GB/T4000-1996)规定了焦炭反应性及反应后强度试验方法。
其做法是使焦炭在高温下与二氧化碳发生反应没,然后测定反应后焦炭失重率及其机械强度。
焦炭反应性CRI及反应后强度CSR的重复性r不得超过下列数值:
CRIr≤2.4
CSR:≤3.2
焦炭反应性及反应后强度的试验结果均取平行试验结果的算术平均值一级冶金焦灰分A≦12.0;硫分S≦0.6%;抗碎强度M25≧92.0(M40≧80.0);耐磨强度M10 M25时,≦7.0 M40时,≦7.50;反应后强度CSR/%≧55;水分含量4.0±1.0
二级冶金焦灰分A≦13.5;硫分S≦0.8%;抗碎强度M25≧88.0
(M40≧76.0);耐磨强度M10≦8.50;反应后强度CSR/%≧50;水分含量
5.0±2.0三级冶金焦灰分A≦15.0;硫分S≦1.0%;抗碎强度M25≧83.0
(M40≧72.0);耐磨强度M10≦10.50;反应后强度CSR/%≧;水分含量≦12.0
准一级冶金焦灰分A﹤12.5%
2
固定碳是焦炭的主要成分.将焦炭再次隔绝空气加热到850℃以上,从中析出挥发物,剩余部分系固定碳和灰分.挥发物含量是焦炭成熟度的重要标志,挥发物含量过高表示焦炭不成熟(生焦),挥发物含量过低表示焦炭过烧(过火焦).生焦耐磨性差,使高炉透气性不好,并能引起挂料,增加吹损,破坏高炉操作制度.过火焦易碎,容易落入熔渣中,造成排渣困难,风口烧坏等现象.
焦炭转鼓强度
焦炭转鼓强度是表征常温下焦炭的抗碎能力和耐磨能力的重要指标,作转鼓强度试验时,将焦炭置于转动的鼓内,借助提升板反复地提起、落下。
在此过程中,焦炭与鼓壁以及焦炭与焦炭相互撞击和摩擦,导致焦炭沿裂纹断开、表面磨损、粒度变小。
焦炭强度即指焦炭经转鼓试验后,用大小两个粒级的焦炭量各占入鼓焦炭量的百分率分别表示的抗碎能力和耐磨能力。
转鼓强度是在经验基础上,通过规范性的转鼓试验方法获得的一种块焦强度指标。
焦炭抗碱性
焦炭抗碱性是指焦炭在高炉冶炼过程中抵抗碱金属及其盐类作用的能力。
焦炭本身的钾。
钠等碱金属含量很低,约0.1%~0.3%,但是在高炉冶炼过程中,由矿石带入的大量钾和钠。
在高炉内形成液滴或蒸气。
造成碱的循环。
并富集在焦炭中。
使炉内焦炭的钾。
钠含量远比入炉焦为高。
可高达3%以上。
这就足以对焦炭产生有害影响。
在高碱负荷的高炉中,这种影响更为严重,因此抗碱性是对高炉焦的一个特殊要求。
钾、钠对焦炭反应性、焦炭机械强度和焦炭结构均会产生有害的影响,以致危害高炉操作。
(1)对焦炭反应性的影响。
钾、钠对焦炭与CO2反应有催化作用。
一般情况下,钾、钠在焦炭中每增加0.%~0.5%,焦炭与CO2的反应速度约提高
10%~15%,钾、钠还可降低焦炭与CO2反应的开始温度。
含3%钾、钠的焦炭比含0.1%~0.3%钾、钠的焦炭的反应开始温度约降低50~100℃。
3
(2)对机械强度的影响,钾。
钠及其氧化物能渗入焦炭的碳结构。
形成石墨钾、石墨钠等层间化合物。
使碳结构变形,开裂而导致焦炭机械强度下降。
(3)对焦炭结构的影响,焦炭与CO2反应过程中,钾、钠的催化作用使表面反应增强,因此焦炭气孔壁的减薄程度加剧,钾、钠还使焦炭光学组织中的各向异性组分反应率有较大的增加,
(4)对反应后强度的影响,钾、钠虽然对焦炭与CO2的反应起催化作用。
但在同一反应程度下。
强度并不因钾。
钠的存在而下降更多。
这是因为催化作用虽然增强了焦炭的表层反应。
却减轻了焦炭的内部反应,但在相同的反应时间内。
碱金属能使反应程度加深。
导致块焦反应后强度明显下降。
(5)对高炉操作的不良影响,钾。
钠对焦炭质量的影响也会给高炉生产带来不良后果,焦炭与CO2反应的开始温度降低。
可导致高炉炼铁焦比升高’由于焦炭与CO2反应速度增加。
焦炭在高炉中的降解失重加剧,机械强度和块度急剧下降。
导致焦炭在高炉下部高温区过多粉化。
影响高炉顺行’钾。
钠蒸气在高炉上部与煤气中的CO2反应生成碳酸盐而析出,这些碱金属碳酸盐部分粘附在炉壁上,会侵蚀耐火材料,影响高炉寿命。
提高焦炭抗碱性的措施有以下几点,
(1)增加低挥发分煤在配合煤中的用量,降低焦炭反应性,提高开始反应温度,从根本上缓解焦炭强度在高炉内的过早恶化。
(2)提高炼焦装炉煤的散密度,使焦炭气孔壁厚度增加,从而提高抵抗CO2的侵蚀能力。
提高焦炭反应后强度。
(3)在炼焦配合煤可添加一些CO2反应的抑制剂或在焦炭表面喷洒这种抑制剂。
以降低钾。
钠对CO2反应的催化作用,曾以SiO2和B2O3作为抑制剂。
进
行提高焦炭抗碱性试验,试验表明。
添加0.5%的B2O3后。
焦炭反应性可降低30%~50%。
(4)减少碱金属在高炉内的循环,可以降低焦炭中的钾钠富集量,降低高炉炉身上部温度可减缓焦炭在进入软融带前发生过多的碳溶反应。
从而使焦炭能承受更剧烈的反应而不致使强度过早变差。
4
焦炭的质量评价
1、焦炭中的硫分:硫是生铁冶炼的有害杂质之一,它使生铁质量降低。
在炼钢生铁中硫含量大于0.07%即为废品。
由高炉炉料带入炉内的硫有11%来自矿石;
3.5%来自石灰石;82.5%来自焦炭,所以焦炭是炉料中硫的主要来源。
焦炭硫分的高低直接影响到高炉炼铁生产。
当焦炭硫分大于1.6%,硫份每增加
0.1%,焦炭使用量增加1.8%,石灰石加入量增加3.7%,矿石加入量增加0.3%高炉产量降低1.5—2.0%.冶金焦的含硫量规定不大于1%,大中型高炉使用的冶金焦含硫量小于0.4—0.7%。
2、焦炭中的磷分:炼铁用的冶金焦含磷量应在0.02—0.03%以下。
3、焦炭中的灰分:焦炭的灰分对高炉冶炼的影响是十分显著的。
焦炭灰分增加1%,焦炭用量增加2—2.5%因此,焦炭灰分的降低是十分必要的。
4、焦炭中的挥发分:根据焦炭的挥发分含量可判断焦炭成熟度。
如挥发分大于
1.5%,则表示生焦;挥发分小于0.5—0.7%,则表示过火,一般成熟的冶金焦挥发分为1%左右。
5、焦炭中的水分:水分波动会使焦炭计量不准,从而引起炉况波动。
此外,焦炭水分提高会使M04偏高,M10偏低,给转鼓指标带来误差。
6、焦炭的筛分组成:在高炉冶炼中焦炭的粒度也是很重要的。
我国过去对焦炭粒度要求为:对大焦炉(1300—2000平方米)焦炭粒度大于40毫米;中、
小高炉焦炭粒度大于25毫米。
但目前一些钢厂的试验表明,焦炭粒度在40—25毫米为好。
大于80毫米的焦炭要整粒,使其粒度范围变化不大。
这样焦炭块度均一,空隙大,阻力小,炉况运行良好。
5。