复合材料的界面
复合材料的界面缺陷与性能分析

复合材料的界面缺陷与性能分析在现代材料科学领域,复合材料因其优异的性能而备受关注。
然而,复合材料的性能并非仅仅取决于其组成成分,界面特性在很大程度上也决定了其整体性能的优劣。
复合材料的界面就如同是连接各个部分的桥梁,一旦这座“桥梁”存在缺陷,就会对整个复合材料的性能产生显著的影响。
首先,我们需要明确什么是复合材料的界面。
简单来说,复合材料的界面是指两种或两种以上不同材料之间的过渡区域。
这个区域虽然很薄,但却具有独特的化学和物理性质。
在这个界面区域内,材料之间的相互作用、化学键合、物理结合等因素共同决定了界面的性能。
那么,复合材料的界面缺陷都有哪些类型呢?常见的界面缺陷包括界面脱粘、孔洞、裂纹、残余应力等。
界面脱粘是指两种材料在界面处失去了有效的结合,这就好像是原本紧紧相连的手松开了。
孔洞则是在界面处形成的空穴,它们会削弱材料的连续性和承载能力。
裂纹的出现往往是由于应力集中或者材料本身的缺陷导致的,一旦裂纹在界面处扩展,就会严重影响复合材料的强度和韧性。
残余应力则是在复合材料制备过程中产生的内应力,当这种应力超过一定限度时,也会导致界面的破坏。
这些界面缺陷是如何产生的呢?一方面,复合材料在制备过程中的工艺参数不当可能会导致界面缺陷。
例如,在复合材料的成型过程中,如果温度、压力、时间等参数控制不好,就可能会出现界面结合不良的情况。
另一方面,原材料的表面处理不当也会引发界面缺陷。
如果原材料表面存在杂质、油污或者氧化层等,就会影响界面的结合强度。
此外,复合材料在使用过程中受到外界环境的影响,如温度变化、湿度变化、化学腐蚀等,也可能会导致界面缺陷的产生和扩展。
界面缺陷对复合材料的性能有着多方面的影响。
从力学性能来看,界面缺陷会显著降低复合材料的强度、刚度和韧性。
例如,界面脱粘会导致载荷无法有效地从一种材料传递到另一种材料,从而使复合材料在承受外力时容易发生过早失效。
孔洞和裂纹的存在会成为应力集中的源头,加速材料的破坏。
复合材料界面

复合材料界面复合材料是由两种或两种以上的材料组合而成的材料,具有优良的综合性能,被广泛应用于航空航天、汽车、建筑等领域。
复合材料的界面是指不同材料之间的分界面,其性能直接影响着整体材料的性能。
本文将从复合材料界面的性能、调控及应用等方面进行介绍。
首先,复合材料界面的性能对整体材料的性能有着重要的影响。
复合材料的性能往往受到界面结合强度、界面相容性、界面稳定性等因素的影响。
界面结合强度决定了不同材料之间的结合程度,直接影响着材料的强度和韧性。
界面相容性则关系到不同材料之间的相互作用,直接影响材料的耐磨性和耐腐蚀性。
界面稳定性则决定了复合材料在复杂环境下的稳定性和可靠性。
因此,优化复合材料界面的性能对提高整体材料的性能至关重要。
其次,复合材料界面的性能可以通过多种方法进行调控。
一方面,可以通过表面处理、界面改性等手段来提高复合材料界面的结合强度和相容性。
另一方面,可以通过界面设计、界面调控等手段来提高复合材料界面的稳定性和可靠性。
同时,还可以通过控制界面微观结构、界面能量等手段来实现对复合材料界面性能的精准调控。
综合运用这些方法,可以有效提高复合材料界面的性能,从而提高整体材料的性能。
最后,复合材料界面的性能对其应用具有重要意义。
在航空航天领域,优化复合材料界面的性能可以提高材料的抗疲劳性能和耐高温性能,从而提高飞机的安全性和可靠性。
在汽车领域,优化复合材料界面的性能可以提高材料的轻量化和节能性能,从而提高汽车的燃油经济性和环保性。
在建筑领域,优化复合材料界面的性能可以提高材料的耐久性和抗风压性能,从而提高建筑的安全性和稳定性。
因此,优化复合材料界面的性能对其应用具有重要的意义。
综上所述,复合材料界面的性能对整体材料的性能具有重要影响,可以通过多种方法进行调控,对其应用具有重要意义。
因此,加强对复合材料界面性能的研究和应用具有重要的意义,将有助于推动复合材料在各领域的应用和发展。
复合材料的界面相互作用与性能评估

复合材料的界面相互作用与性能评估在现代材料科学领域中,复合材料凭借其独特的性能优势,在众多领域都有着广泛的应用。
复合材料由两种或两种以上具有不同物理和化学性质的材料组成,其性能不仅取决于各组分材料的性能,更关键的是取决于它们之间的界面相互作用。
深入理解复合材料的界面相互作用对于准确评估其性能以及优化材料设计具有极其重要的意义。
复合材料的界面是指两种或多种不同材料之间的过渡区域。
这个区域的宽度通常在几个纳米到几十个微米之间,但其对复合材料整体性能的影响却不可小觑。
界面相互作用可以分为物理相互作用和化学相互作用两大类。
物理相互作用包括机械嵌合、范德华力和氢键等。
机械嵌合就像是拼图的拼接,当一种材料的微观结构能够嵌入另一种材料时,就形成了这种物理结合。
范德华力虽然相对较弱,但在界面处大量分子间的范德华力总和也能对结合强度产生一定的贡献。
氢键则是一种稍强的物理相互作用,例如在一些含有羟基、氨基等官能团的材料界面处就可能存在氢键。
化学相互作用则更为复杂和强烈。
常见的有化学键合,比如共价键、离子键等。
当两种材料在界面处能够发生化学反应,形成新的化学键时,它们之间的结合强度会显著提高。
这种化学结合不仅能增强材料的力学性能,还可能影响其热学、电学等其他性能。
界面相互作用对复合材料的性能有着多方面的影响。
首先是力学性能。
良好的界面结合能够有效地传递载荷,避免应力集中,从而提高复合材料的强度和韧性。
如果界面结合不良,在受到外力作用时,容易在界面处产生裂纹和脱粘,导致材料过早失效。
其次是热性能。
界面的存在会影响热传导的路径和效率。
如果界面结合紧密,热传导会更顺畅,有利于复合材料在高温环境下的使用;反之,则可能导致局部过热,影响材料的稳定性和使用寿命。
再者是电学性能。
在一些功能性复合材料中,如导电复合材料,界面的电学性质会直接影响材料的导电性。
如果界面存在电阻过大的问题,会降低整体的导电性能。
此外,界面相互作用还会影响复合材料的耐腐蚀性、耐磨性等其他性能。
复合材料的界面

复合材料的界面复合材料是由两种或两种以上不同的材料组成的材料,通过各自的特性相互作用形成的一种新型材料。
界面是不同材料之间的接触面,是复合材料性能的决定因素之一。
下面将从界面的作用、界面的特性和界面的调控三个方面对复合材料的界面进行详细介绍。
界面在复合材料中起着连接、传递和分散应力的作用。
首先,界面连接了不同材料一起,使其形成整体性能优于单个材料的复合材料。
其次,界面能够传递应力,使复合材料整体受力均匀、分散应力集中,提高材料的强度和韧性。
最后,界面还能够分散应力,减少裂纹扩展和断裂的可能性,延长复合材料的使用寿命。
界面的特性主要包括接触角度、界面能、亲水性或疏水性等。
首先,接触角度反映了界面的亲水性或疏水性,即其与液体接触时的表面张力。
亲水性的界面会使液体在复合材料中能够更好地湿润、浸润,提高复合材料的粘合度和界面传递性。
其次,界面能是指界面上分子之间相互作用的能量。
界面能越小,表示复合材料中不同材料之间的相容性越好,界面强度越高。
最后,亲水性界面和疏水性界面对复合材料的性能也会产生不同的影响。
如亲水性界面可增加复合材料的应力强度、韧性和热稳定性,而疏水性界面可减少复合材料的吸湿性和电导性。
界面的调控主要通过界面改性和表面处理两个途径实现。
首先,通过界面改性可以改变界面的性质,提高其性能,例如通过添加界面活性剂进行处理,使界面能更好地吸附和传递应力;通过聚合物接枝物改性,增加界面粘合力等。
其次,通过表面处理可以对界面进行改善,例如通过物理或化学方法处理材料表面,使其表面特性更加适合复合材料的应用。
常用的表面处理方法有溶剂清洗、电子束辐照、化学氧化等。
综上所述,界面是影响复合材料性能的重要因素,通过界面的调控可以改善复合材料的性能。
理解和研究界面的特性和调控方法对于开发出更加优异的复合材料具有重要意义。
复合材料的界面性能与优化分析
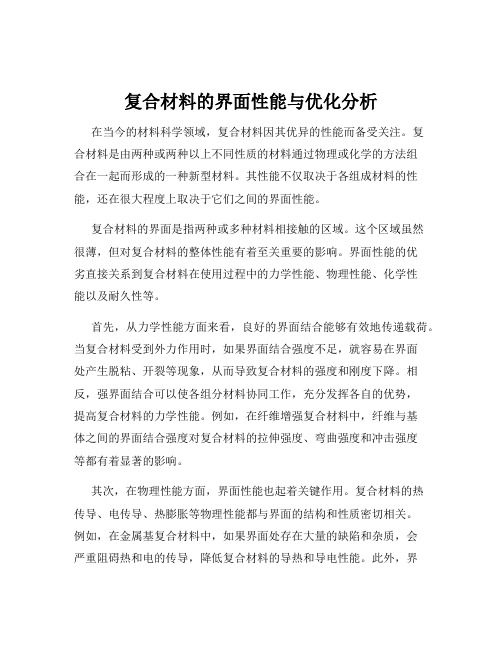
复合材料的界面性能与优化分析在当今的材料科学领域,复合材料因其优异的性能而备受关注。
复合材料是由两种或两种以上不同性质的材料通过物理或化学的方法组合在一起而形成的一种新型材料。
其性能不仅取决于各组成材料的性能,还在很大程度上取决于它们之间的界面性能。
复合材料的界面是指两种或多种材料相接触的区域。
这个区域虽然很薄,但对复合材料的整体性能有着至关重要的影响。
界面性能的优劣直接关系到复合材料在使用过程中的力学性能、物理性能、化学性能以及耐久性等。
首先,从力学性能方面来看,良好的界面结合能够有效地传递载荷。
当复合材料受到外力作用时,如果界面结合强度不足,就容易在界面处产生脱粘、开裂等现象,从而导致复合材料的强度和刚度下降。
相反,强界面结合可以使各组分材料协同工作,充分发挥各自的优势,提高复合材料的力学性能。
例如,在纤维增强复合材料中,纤维与基体之间的界面结合强度对复合材料的拉伸强度、弯曲强度和冲击强度等都有着显著的影响。
其次,在物理性能方面,界面性能也起着关键作用。
复合材料的热传导、电传导、热膨胀等物理性能都与界面的结构和性质密切相关。
例如,在金属基复合材料中,如果界面处存在大量的缺陷和杂质,会严重阻碍热和电的传导,降低复合材料的导热和导电性能。
此外,界面的存在还会影响复合材料的热膨胀系数,如果界面结合不良,在温度变化时容易产生热应力,导致复合材料的变形和破坏。
化学性能方面,界面是复合材料与外界环境相互作用的前沿阵地。
界面的化学稳定性决定了复合材料的耐腐蚀性、抗氧化性等化学性能。
如果界面处容易发生化学反应,如氧化、腐蚀等,就会削弱复合材料的性能,缩短其使用寿命。
例如,在聚合物基复合材料中,界面的亲水性或疏水性会影响其对水分的吸收和扩散,进而影响复合材料的耐湿性和耐老化性能。
那么,如何优化复合材料的界面性能呢?这需要从多个方面入手。
一方面,可以通过对原材料的表面处理来改善界面性能。
例如,对于纤维增强复合材料,可以对纤维表面进行氧化、涂层等处理,增加纤维与基体之间的化学键合和物理结合,提高界面结合强度。
复合材料的界面

改变强化材料表面的性质
• 对SiC晶须表面采用化学方法处理后XPS(X-ray Photoelectron Spectroscopy)分析的结 果。由C(1s)和Si(2p)的波谱可以看出,有的地方存在SiO2,有的地方不存在SiO2。 利用这样的表面状态的差来增强界面的结合力。
6.6.2 向基体添加特定的元素
• 在用烧结法制造复合材料的过程中,为了有助于 烧结,往往向基体添加一些元素。有时为了使纤 维与基体发生适度的反应以控制界面,也可以添 加一些元素。在SiCPCS纤维强化玻璃陶瓷(LAS) 中,如果采用通常的LAS成分的基体,在晶化处 理时会在界面产生裂纹。而添加百分之几的Nb时, 热处理过程中会发生反应,在界面形成数微米的 NbC相,获得最佳界面,从而达到高韧化的目的。
5.5 界面行为
5.5.1 界面的脱粘与剥离(Debonding)
研究界面的脱粘与剥离的意义
研究思路 ➢ 考虑基体中仅有一根纤维,受到拉伸载荷为Pf的情
况 ➢ 分析复合材料中强化材料与基体间应力传递的方
式 解析法: ➢ 应用最大剪切应力理论 ➢ 应用断裂力学理论
脱粘、剥离与滑动的关系为一旦发生脱粘与剥离,剥离部分就产生滑 动。解析法可以应用最大剪切应力理论,也可以应用断裂力学理论。
临界值
• 断裂的机制 张开型裂纹 φ=0
剪切型裂纹 φ=90 φ=tan-1(KⅡ/KⅠ)
界面对复合材料性能的影响
• 界面特性
复合材料性能
界面黏结强度下降复合材料弹性模量下降
• 但界面特性与复合材料性能的定量关系少
• 界面参数 (强度,韧性)
• 脆性组元的界面区域,尺寸与厚度相当的缺 陷 断裂力学模型
5.2.1 界面应力与非弹性过程
复合材料的界面理论

复合材料的界面理论1、界面形成及其形成1.1界面的定义复合材料的界面是指基体与增强相之间化学成分有显著变化的、构成彼此结合的、能起载荷传递作用的微小区域。
复合材料的界面是一个多层结构的过渡区域,约几个纳米到几个微米。
此区域的结构与性质都不同于两相中的任何一相。
这一界面区由五个亚层组成,每一亚层的性能都与基体和增强相的性质、复合材料成型方法有关。
界面区域如图1-1所示。
1.2界面的形成复合材料体系对界面要求各不相同,它们的成形加工方法与工艺差别很大,各有特点,使复合材料界面形成过程十分复杂,理论上可分为两个阶段: 第一阶段:增强体与基体在一组份为液态(或粘流态)时的接触与浸润过程。
在复合材料的制备过程中,要求组份间能牢固的结合,并有足够的强度。
要实现这一点,必须要使材料在界面上形成能量最低结合,通常都存在一个液态对固体的相互浸润。
所谓浸润,即把不同的液滴放到不同的液态表面上,有时液滴会立即铺展开来,遮盖固体的表面,这一现象称为“浸润”。
第二阶段:液态(或粘流态)组份的固化过程,即凝固或化学反应。
固化阶段受第一阶段的影响,同时它也直接决定着所形成的界面层的结构。
以固热性树脂的固化过程为例,固化剂所在位置是固化反应的中心,固化反应从中心以辐射状向四周扩展,最后形成中心密度大、边缘密度小的非均匀固化结构,密度大的部分称为胶束或胶粒,密度小的称胶絮。
2、界面对复合材料性能的影响及影响界面结合强度的因素 2.1界面对复合材料性能的影响复合材料内界面结合强度是影响复合效果的最主要因素。
界面的结合强度主要取决于界面的结构、物理与化学性能。
具有良好结合强度的界面,可以产生如下强化效应:(1)阻止裂纹的扩散,提高材料的韧性;(2)通过应力传递,使强化相承受较大的外载荷,提高复合材料的承载能力;(3)分散和吸收各种机械冲击和热冲击的能量,提高抗外加冲击的能力;(4)使强化相与基体产生既相互独立又相互协调的作用,弥补各自的缺点,获得新的材料使用性能。
第4章复合材料界面

表面张力(surface tension)
将含有一个活动边框的金属
2 l
线框架放在肥皂液中,然后取出
悬挂,活动边在下面。
由于金属框上的肥皂膜的表 面张力作用,可滑(surface tension)
如果在活动边框上挂一重物,使重 物质量W2与边框质量W1所产生的重力F 与总的表面张力大小相等方向相反,则 金属丝不再滑动。
5)混合结合。这种结合较普遍,是最重要的一种结合方式。是以 上几种结合方式中几个的组合。
4.2 复合材料的界面效应
• 界面是复合材料的特征,可将界面的机能归 纳为以下几种效应:
• (1)传递效应:界面可将复合材料体系中 基体承受的外力传递给增强相,起到基体和 增强相之间的桥梁作用。
• (2)阻断效应:基体和增强相之间结合力 适当的界面有阻止裂纹扩展、减缓应力集中 的作用。
由此可见,在研究和设计界面时, 不应只追求界面粘结而应考虑到最优 化和最佳综合性能。
4.3复合材料组分的相容性
• 物理相容性:
1. 是指基体应具有足够的韧性和强度,能够将 外部载荷均匀地传递到增强剂上,而不会有 明显的不连续现象。
2. 由于裂纹或位错移动,在基体上产生的局部 应力不应在增强剂上形成高的局部应力。
C12 (C2H5)2O
H2O NaCl LiCl Na2SiO3(水玻璃) FeO A12O3 Ag Cu
Pt
-30 25 20 803 614 1000 1427 2080 1100 1083 1773.5
25.56 26.43 72.88 113.8 137.8 250 582 700 878.5 1300 1800
4.4 复合材料的界面理论
• 由于界面尺寸很小且不均匀、化学成分及结 构复杂、力学环境复杂、对于界面的结合强 度、界面的厚度、界面的应力状态尚无直接 的、准确的定量分析方法;
- 1、下载文档前请自行甄别文档内容的完整性,平台不提供额外的编辑、内容补充、找答案等附加服务。
- 2、"仅部分预览"的文档,不可在线预览部分如存在完整性等问题,可反馈申请退款(可完整预览的文档不适用该条件!)。
- 3、如文档侵犯您的权益,请联系客服反馈,我们会尽快为您处理(人工客服工作时间:9:00-18:30)。
用于不含游离水,只含化学键合水或物理结合水的干燥 填料体系。
Eg:碳酸钙、水合氧化铝等。
13
2 单烷氧基焦磷酸酯基型 适合范围: 用于含湿量较高的填料体系,如陶土、滑石粉等。 三(二辛基焦磷酰氧基)钛酸异丙酯(TTOPP—385)就是典型 的单烷氧基焦磷酸酯基型偶联剂。
9
填充、增强材料的表面处理
为了改进增强纤维与基体之间的界面结构,改善两者间的结合性能, 需要对增强纤维进行适当的表面处理。
表面处理的方法是在增强纤维表面涂覆上一种称为表面处理剂的物质, 包括浸润剂、偶联剂等其它助剂,以制造与基体间好的粘结界面。
10
1 粉状颗粒的表面处理技术
无机粉体填料与有机高聚物的不相容性,重视研究改善粉 体填料的表面性质。
3
聚合物基复合材料界面的形成及作用机理 1. 界面的形成 两个阶段:基体与增强材料的接触与浸润过程;基体与增强 材料通过相互作用使界面固定阶段 界面层的结构包括:界面的结合力、界面区域的厚度和界面 的微观结构 通常对纤维进行表面处理以增强界面结合力
4
2. 界面作用机理
(1)界面张力、表面自由能、比表面能
lv
sv sl时,cos 0, 90o,不润湿
lv sv sl 0时,0<cos 1, 0o 90o,润湿
sv sl lv时,cos 1, 0o,完全润湿,粘附功最大
8
B. 化学键理论 偶联剂作用机理 强调增加界面的化学作用是改进复合材料性能的关键 硅烷偶联剂具有两种性质不同的官能团,一端为亲玻璃纤维的官能团 (X),一端为亲树脂的官能团(R),将玻璃纤维与树脂粘结起来,在界面 上形成共价键结合
概述
复合材料的界面: 指基体与增强物之间化学成分有显著变化的、构成彼 此结合的、能起载荷传递作用的微小区域。
界面通常可能包含以下几个部分: 基体和增强物的部分原始接触面; 基体与增强物生成的反应产物; 基体和增强物的互扩散层; 增强物上的表面涂层; 基体和增强物上的氧化物及它们的反应产物之间的接触面等。
2
复合材料中的界面构成
复合材料中的界面并不是一个单纯的几何面,而是一个多层结构的过渡 区域,界面区是从与增强剂内部性质不同的某一点开始,直到与树脂基 体内整体性质相一致的点间的区域。 复合材料的界面层,除了在性能和结构上不同于相邻两组分 相外,还具有如下特点: (1) 具有一定的厚度; (2) 性能在厚度方向上有一定的梯度变化; (3) 随环境条件变化而改变 。
1
复合材料的界面机能
界面的机能归纳为以下几种效应: 1) 传递效应 将外力传递给增强物,起到桥梁作用。 2) 阻断效应 阻止裂纹扩展、中断材料破坏、减缓应力集中 3) 不连续效应 在界面上产生物理性能的不连续性的现象 4) 散射和吸收效应 光波、声波等在界面产生散射和吸收 5) 诱导效应 增强物的表面结构使聚合物基体与之接触的物质的结构由 于诱导作用而发生改变,由此产生一些现象,如强的弹性、低的膨胀性、 耐冲击性和耐热性等。
沃兰的R基团及Cr-OH将与基体树脂反应,实验证明,粘附强度随纤维 表面上铬含量的提高而提高。
物质表面层中的分子与本体中的分子二者所处的力场是
不同的。以与饱和蒸汽相接触的液体表面分子与内部分子受
力情况为例:
l-g界面(液体表面)
5
(2)润湿与接触角 润湿
原来的固-气界面被新的固-液界面置换的过程。 固体表面的润湿程度可以由液体分子对其表面的作用力 大小来表征。
接触角(θ)
当一液滴在固体表面上不完全展开时,在气、液、固 三相会合点,液-固界面的水平线与气-液界面切线之间通 过液体内部的夹角θ,称为接触角。
1、硅烷偶联剂 ; 2、钛酸酯类构通式:
(RO)m Ti - (OX-R’-Y)n
11
(RO)m Ti - (OX-R’-Y)n
(RO)为钛酸酯和无机填料进行化学结合的官能团;
-Ti(OX)部分为钛酸酯的有机骨架,与聚合物的羧基之间 进行相互交换,起酯基和烷基转移反应;
17
2玻璃纤维的表面处理
有机铬合物类表面处理剂:有机酸与氯化铬的络合物(A);以甲基 丙烯酸氯化铬配合物(沃兰)应用最为广泛(B)
18
沃兰对玻璃纤维表面的处理机理 1. 沃兰水解
2. 玻璃纤维表面吸水
19
3. 沃兰与吸水的玻璃纤维表面反应 1) 沃兰之间及沃兰与玻璃纤维表面间形成氢键
20
2) 干燥,沃兰之间及沃兰与玻璃纤维表面间缩合-醚化反应
—X部分是和分子核心软相结合的基团,对钛酸酯的性质 有着重要影响;
R’是长链分子基团,起缠绕作用,能与热塑性树脂缠绕结 合在一起,改善冲击性能;
Y为胺基、丙烯酸、烃基及末端氢原子等;
m、n为官能团数。n>2时为多官能团的钛酸酯,可与多 官能团的热塑性及热固性树脂起作用。
12
根据分子结构及偶联机理,钛酸酯偶联剂可分为四种基 本类型。 1 单烷氧基脂肪酸型
14
3 螯合型 适用范围: 用于高湿填料和含水聚合物体系。 Eg:湿法二氧化硅、陶土、滑石粉、硅酸铝、水处理玻璃纤 维、炭黑等。 这类偶联剂分两种基本类型:螯合100型和螯合200型。 反应示意如下 :
15
螯合200型与填料表面的反应式:
16
4 配位体型 适用于许多填充体系。 配位体型钛酸酯偶联剂可以避免一些副反应: Eg:1、在聚酯中的酯交换反应; 2、在环氧树脂中与羟基反应; 3、在聚氨酯中与聚醇或异氰酸酯反应等。 其偶联机理与单烷氧基钛酸酯偶联剂类似。
6
界面发挥作用的微观机理
A. 界面浸润理论 浸润角的概论 完全浸润将使基体与填充剂间的粘结强度将大于基体的内聚强度
(a) 不完全浸润
(b) 不浸润
良好的浸润性,只是两个组元间可达到良好粘结的必要条件,并非充分条件
7
当三力平衡时,处于平衡态,则有,
sv sl lv cos
即 sl sv lv cos 0 ——杨氏方程 讨论: cos sv sl