三维封装的现在和未来
微电子封装技术及发展探析

微电子封装技术及发展探析摘要近年来,随着科学技术的不断进步与发展,集成电路的广泛使用使得我国工业的飞跃发展成为现实和可能,受此影响,集成电路产业也成为可我国国民经济长期可持续发展的关键。
在集成电路产业之中,微电子封装技术的高低将直接决定整个集成电路的电性能、机械性能、光性能和热性能的优劣,在这样的情况下,对微电子封装技术及其发展进行分析和探讨就变得十分有必要了。
基于此,本文从微电子封装技术的发展历程、现状出发,就现阶段我国微电子封装技术的特点及其未来的发展趋势进行了探析。
关键词微电子;封装技术;发展探析在电子信息技术不断发展的当下,微型化、多功能化、高性能化逐步成为电子产品未来发展的基本要求,而为了更好地实现上述目的、确保电子产品能够正常使用,就离不开微电子封装技术对其提供相应的支持。
目前,我国常用的微电子封装技术主要有倒装芯片技术、芯片规模封装等,不同的封装技术有不同的应用范围,只有在明确不同封装技术的特点的基础上,才能保证对大限度地发挥不同封装技术的优势和作用。
下面,本文将就微电子封装技术及其发展进行详细阐述。
1 微电子封装技术常见分类及特点1.1 BGA封装技术BGA封装技术诞生于20世纪90年代,其中文全称为焊球阵列封装技术,由于已经有了较长的发展历程,因而在目前的应用实践中有着较高的技术成熟度,通过球柱形焊点阵列进行I/O端与基板的封装是其主要的封装原理。
相较于其他常见微电子封装技术,BGA封装技术的主要优势在于阵列密度高、组装成品率高。
在塑料焊球阵列、陶瓷焊球阵列、金属焊球阵列等多种BGA封装技术中,装芯片焊球阵列封装将是未来BGA技术的主要发展方向[1]。
1.2 3D封装技术3D封装技术是伴随着移动互联网的发展而逐渐兴起的,目前主要应用于手持设备的高密度立体式组装之中,是同时满足多个芯片组立体式封装需求的有效途径。
在现阶段市面上常见的各种封装技术中,3D封装技术具备的主要技术优势在于功能性丰富、封装密度高、电性能热性能突出。
系统级封装技术及其应用

▪ SiP技术与传统封装的设计灵活性对比
1. SiP技术提供了更高的设计灵活性,可以在封装内部灵活配 置各种功能模块,并且可以根据需求进行定制化设计。 2. 传统封装的设计相对固定,难以根据市场需求进行快速调整 和更新。 3. SiP技术的设计灵活性有助于电子产品更好地适应市场变化 和用户需求。
SiP技术与传统封装对比
▪ SiP技术与传统封装的成本对比
1. SiP技术可以降低系统级封装的成本,因为其能够在单个封装内集成多个功能模 块,减少了组件数量和组装步骤。 2. 传统封装需要分别制造和装配各个独立的功能模块,导致成本较高。 3. 随着SiP技术的发展和应用规模的扩大,预计其成本优势将更加明显。
SiP技术与传统封装对比
▪ SiP技术的基本原理
1. SiP技术的核心思想是在一个小巧的封装内整合多种功能部 件,如处理器、存储器和传感器等。 2. 通过精细的布线和堆叠设计,实现各组件之间的高效通信和 协同工作。 3. SiP封装可以采用不同的制造工艺和技术,如倒装芯片、晶 圆级封装和硅穿孔等。
系统级封装技术原理
▪ 封装材料的选择
系统级封装技术概述
▪ 系统级封装的优势和挑战
1. SiP技术的主要优势包括更高的电路密度、更好的热管理、 更快的数据传输速度以及更低的生产成本。 2. SiP技术也面临一些挑战,如设计复杂度增加、散热问题加 剧、可靠性验证困难等。 3. 解决这些挑战的关键在于采用先进的设计工具、改进封装材 料和工艺,以及加强测试和验证方法的研究。
#. 封装技术发展历程
,
1. 随着纳米技术和微电子技术的发展,各种先进的封装技术不断涌现。 2. 这些技术包括扇出型封装(Fan-out)、嵌入式封装(Embedded)、异构集成( Heterogeneous Integration)等。 3. 先进封装技术旨在提高封装效率、降低成本并优化系统性能。, 【封装技术的未来趋势】:
2023年电子封装技术专业特色简介

2023年电子封装技术专业特色简介电子封装技术是现代电子工程领域的重要分支之一,它涵盖了电子器件封装设计与制造、可靠性测试、材料与工艺研究等一系列内容,是电子工程中不可或缺的重要环节。
近年来,随着制造业的进一步转型升级和市场需求的变化,电子封装技术也面临着新的挑战和机遇。
在传统的电子封装技术领域,其主要关注点是封装设计和可靠性评估,虽然已经涵盖了 semiconductor 和 packaging 的关键领域,但其研究的限制在于缺乏深刻理解的材料和物理学机制。
随着新型材料、新型构型的出现和封装工艺的不断创新,电子封装技术已经发展出了一些新的特色和趋势,以下是其中的几个方面:一、三维封装随着微电子技术的不断升级,芯片的功能越来越强大,但体积却越来越小,这就需要三维封装技术的应用。
三维封装技术是将多个芯片和电路元件垂直叠加封装在一起,以实现更高性能和更小尺寸的电子产品。
它可以在不增加产品尺寸的前提下,提高产品的功耗和速度等性能指标。
三维封装技术相较于传统封装技术,需要更复杂的细节处理,并且需要考虑解决热分布不均、压力不均等新的问题,在封装工艺、材料选用、设计等方面都需要更高的技术水平和更火的设计思想。
二、可靠性设计可靠性是一个电子封装技术永恒的话题,是产品质量、性能、寿命等方面的重要指标。
在电子封装技术中,优化设计并加强可靠性评估是不可避免的趋势。
基于工业 4.0 的思想,电子封装技术的可靠性设计已经开始由受试者系统单纯的验风险转移为预测性的质量保证体系,并且需集成物理测试、仿真、分析为一体的方法,来提高开发周期与成功率。
这些方法包括可靠性分析(如强化测试、衰减测试等)、可靠性预测(如使用MATLAB或其它仿真软件实现电子产品在正常使用的生命周期内,研究产品可靠性与失效机制)和机器学习技术来帮助预测封装失效风险。
三、多功能封装电子封装技术逐渐向多功能封装方向发展,这也是近年来的一个重要的趋势。
多功能封装是在保证器件基本功能的前提下增加多样化的特性,如在传输和处理信号的同时实现电源管理,这样除了提高性能和可靠性外还能够减小产品体积,降低成本。
BGA多芯片组件及三维立体封装(3D)技术
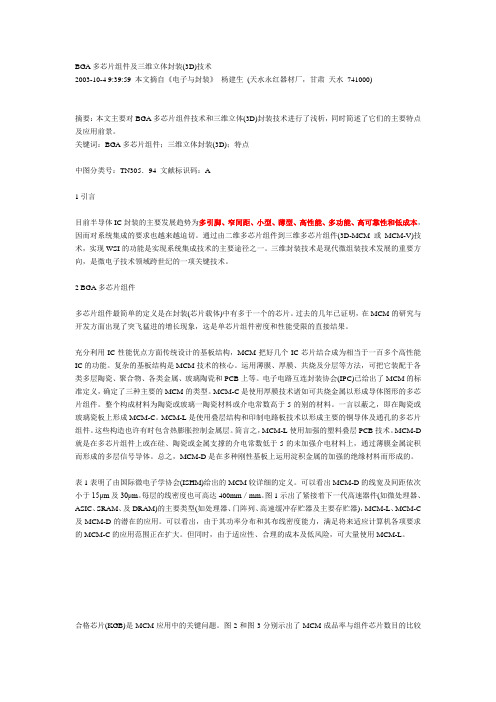
BGA多芯片组件及三维立体封装(3D)技术2003-10-4 9:39:59 本文摘自《电子与封装》杨建生(天水永红器材厂,甘肃天水741000)摘要:本文主要对BGA多芯片组件技术和三维立体(3D)封装技术进行了浅析,同时简述了它们的主要特点及应用前景。
关键词:BGA多芯片组件;三维立体封装(3D);特点中图分类号:TN305.94 文献标识码:A1引言目前半导体IC封装的主要发展趋势为多引脚、窄间距、小型、薄型、高性能、多功能、高可靠性和低成本,因而对系统集成的要求也越来越迫切。
通过由二维多芯片组件到三维多芯片组件(3D-MCM或MCM-V)技术,实现WSI的功能是实现系统集成技术的主要途径之一。
三维封装技术是现代微组装技术发展的重要方向,是微电子技术领域跨世纪的一项关键技术。
2 BGA多芯片组件多芯片组件最简单的定义是在封装(芯片载体)中有多于一个的芯片。
过去的几年已证明,在MCM的研究与开发方面出现了突飞猛进的增长现象,这是单芯片组件密度和性能受限的直接结果。
充分利用IC性能优点方面传统设计的基板结构,MCM把好几个IC芯片结合成为相当于一百多个高性能IC的功能。
复杂的基板结构是MCM技术的核心。
运用薄膜、厚膜、共烧及分层等方法,可把它装配于各类多层陶瓷、聚合物、各类金属、玻璃陶瓷和PCB上等。
电子电路互连封装协会(IPC)已给出了MCM的标准定义,确定了三种主要的MCM的类型。
MCM-C是使用厚膜技术诸如可共烧金属以形成导体图形的多芯片组件。
整个构成材料为陶瓷或玻璃一陶瓷材料或介电常数高于5的别的材料。
一言以蔽之,即在陶瓷或玻璃瓷板上形成MCM-C。
MCM-L是使用叠层结构和印制电路板技术以形成主要的铜导体及通孔的多芯片组件。
这些构造也许有时包含热膨胀控制金属层。
简言之,MCM-L使用加强的塑料叠层PCB技术。
MCM-D 就是在多芯片组件上或在硅、陶瓷或金属支撑的介电常数低于5的未加强介电材料上,通过薄膜金属淀积而形成的多层信号导体。
三维系统级封装技术中的TSV侧壁绝缘工艺研究的开题报告
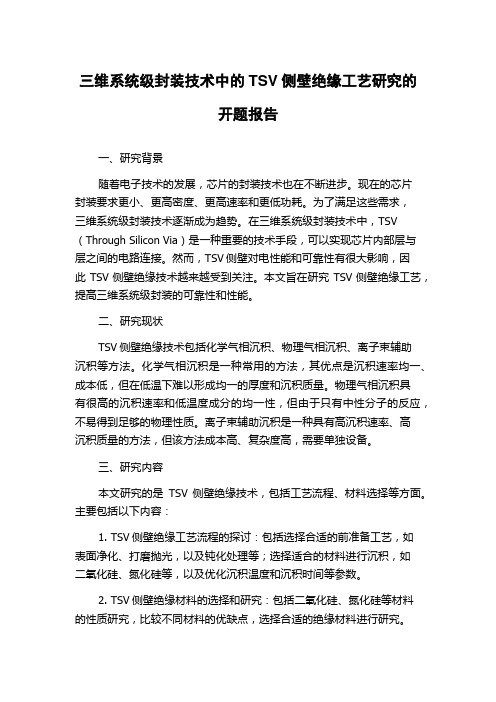
三维系统级封装技术中的TSV侧壁绝缘工艺研究的开题报告一、研究背景随着电子技术的发展,芯片的封装技术也在不断进步。
现在的芯片封装要求更小、更高密度、更高速率和更低功耗。
为了满足这些需求,三维系统级封装技术逐渐成为趋势。
在三维系统级封装技术中,TSV (Through Silicon Via)是一种重要的技术手段,可以实现芯片内部层与层之间的电路连接。
然而,TSV侧壁对电性能和可靠性有很大影响,因此TSV侧壁绝缘技术越来越受到关注。
本文旨在研究TSV侧壁绝缘工艺,提高三维系统级封装的可靠性和性能。
二、研究现状TSV侧壁绝缘技术包括化学气相沉积、物理气相沉积、离子束辅助沉积等方法。
化学气相沉积是一种常用的方法,其优点是沉积速率均一、成本低,但在低温下难以形成均一的厚度和沉积质量。
物理气相沉积具有很高的沉积速率和低温度成分的均一性,但由于只有中性分子的反应,不易得到足够的物理性质。
离子束辅助沉积是一种具有高沉积速率、高沉积质量的方法,但该方法成本高、复杂度高,需要单独设备。
三、研究内容本文研究的是TSV侧壁绝缘技术,包括工艺流程、材料选择等方面。
主要包括以下内容:1. TSV侧壁绝缘工艺流程的探讨:包括选择合适的前准备工艺,如表面净化、打磨抛光,以及钝化处理等;选择适合的材料进行沉积,如二氧化硅、氮化硅等,以及优化沉积温度和沉积时间等参数。
2. TSV侧壁绝缘材料的选择和研究:包括二氧化硅、氮化硅等材料的性质研究,比较不同材料的优缺点,选择合适的绝缘材料进行研究。
3. 测试TSV侧壁绝缘层的性质:包括测试TSV侧壁绝缘层的厚度、密度、粗糙度、耐压性、导电性等性质,并与国内外同类研究进行比较。
四、研究意义TSV侧壁绝缘技术是三维系统级封装技术中很重要的组成部分,其性能与可靠性直接影响到整个芯片的性能和可靠性。
研究TSV侧壁绝缘技术,可以提高三维系统级封装的可靠性和性能,推动三维系统级封装技术的发展。
此外,本文的研究结果还将为电子制造业提供有力的技术支持。
2024年微电子封装市场发展现状
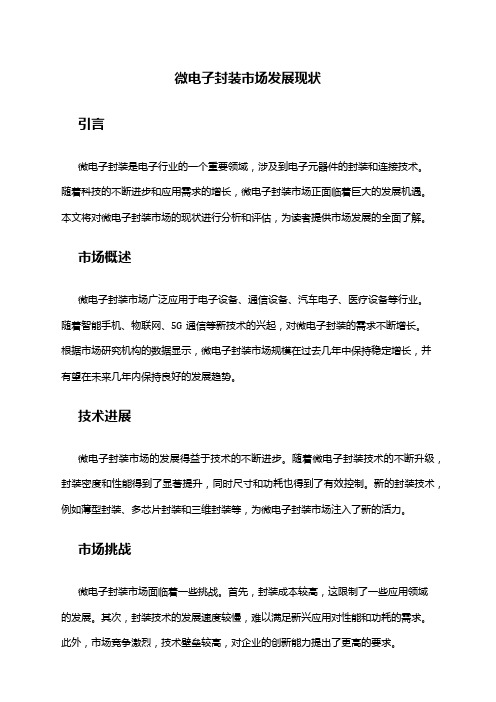
微电子封装市场发展现状引言微电子封装是电子行业的一个重要领域,涉及到电子元器件的封装和连接技术。
随着科技的不断进步和应用需求的增长,微电子封装市场正面临着巨大的发展机遇。
本文将对微电子封装市场的现状进行分析和评估,为读者提供市场发展的全面了解。
市场概述微电子封装市场广泛应用于电子设备、通信设备、汽车电子、医疗设备等行业。
随着智能手机、物联网、5G通信等新技术的兴起,对微电子封装的需求不断增长。
根据市场研究机构的数据显示,微电子封装市场规模在过去几年中保持稳定增长,并有望在未来几年内保持良好的发展趋势。
技术进展微电子封装市场的发展得益于技术的不断进步。
随着微电子封装技术的不断升级,封装密度和性能得到了显著提升,同时尺寸和功耗也得到了有效控制。
新的封装技术,例如薄型封装、多芯片封装和三维封装等,为微电子封装市场注入了新的活力。
市场挑战微电子封装市场面临着一些挑战。
首先,封装成本较高,这限制了一些应用领域的发展。
其次,封装技术的发展速度较慢,难以满足新兴应用对性能和功耗的需求。
此外,市场竞争激烈,技术壁垒较高,对企业的创新能力提出了更高的要求。
发展趋势微电子封装市场在未来几年中有望保持持续增长。
首先,5G通信的商用化将推动微电子封装市场的快速发展。
其次,人工智能、物联网等新兴技术的普及将提高对微电子封装的需求。
此外,节能环保、小型化等市场需求也将促进微电子封装技术的创新和升级。
市场竞争格局微电子封装市场竞争激烈,主要厂商包括英特尔、三星电子、台积电、中芯国际等。
这些企业在封装技术研发、生产能力和市场份额方面具有较强优势。
此外,新兴企业也在不断涌现,通过技术创新和市场定位寻求突破。
结论微电子封装市场是一个充满机遇与挑战并存的市场。
随着新技术的不断涌现和应用领域的不断扩展,微电子封装市场有望进一步发展壮大。
为保持竞争力,企业需加强技术创新、提高生产效率,并关注市场趋势的变化,及时调整发展战略。
电子封装技术发展现状及趋势

电子封装技术发展现状及趋势龙乐【摘要】The current IC wafer ling width characteristics is micronanoelectronic scale. The microminiaturization process of electronic products and electronic systems will depend on the advanced packaging technology .It has increasingly become a focus of the semiconductor industry. Novel packaging technology with larger market value around home and abroad in recent years are introduced. Basic structures and fabrication processes of some typical packaging are bescribed in detail. Furthermore, it is pointed out current status and development trend of packaging technology.In the recent years, endless varieties of packagings are proposed. It implements a new and higher level of packaging integration with higher assemble density, more strong features, better performance, smalles size, lower power consumption, faster speed, smaller delay, cost reduction,etc. Researches and process of packaging cannot be ignored. It has a great market potential and development in the days to come. Advanced packaging technology are forcing semiconductor industry access the More-than-Moore era .%现今集成电路晶圆的特征线宽进入微纳电子时代,而电子产品和电子系统的微小型化依赖先进电子封装技术的进步,封装技术已成为半导体行业关注的焦点之一。
电子封装技术毕业论文文献综述

电子封装技术毕业论文文献综述在电子技术领域的快速发展中,电子封装技术作为其中的重要一环,不断演进和创新。
本文将对电子封装技术的发展、目前面临的挑战以及未来方向进行综述,以提供更多的研究参考和理论支持。
一、引言电子封装技术是电子器件制造中至关重要的一环。
它涉及到将电子元器件集成到封装中,并通过封装实现电子元器件互联、保护和散热等功能。
随着电子技术的不断进步和应用领域的扩大,电子封装技术也迎来了新的挑战和机遇。
二、电子封装技术的发展历程1. 早期传统封装技术传统封装技术主要包括通过针脚和焊盘实现电子元器件的封装,并以塑料封装为主。
这种封装方式简单、成本低,但无法满足高密度、高速和小型化等要求。
2. 高级封装技术的崛起随着微电子技术的兴起,高级封装技术应运而生,如表面贴装技术(SMT)、裸芯封装技术(COB)、芯片级封装技术(CSP)等。
这些封装技术实现了更小尺寸、更高集成度和更高速度的电子器件。
三、电子封装技术的挑战1. 热管理问题随着电子产品功耗的增加,散热成为电子封装技术面临的重要挑战。
传统封装技术往往无法满足高功耗电子器件的散热需求,因此需要开发新的散热材料和散热设计方法。
2. 高密度封装随着电子器件集成度的提高,如何在有限的空间内实现更多的器件封装,成为电子封装技术面临的挑战。
这需要开发更小尺寸的封装材料、更好的互联技术以及更高精度的制造工艺。
四、电子封装技术的未来发展方向1. 三维封装技术三维封装技术通过将电子器件在垂直方向上进行堆叠,有效提高了集成度和性能。
这是未来电子封装技术发展的重要方向。
2. 柔性封装技术柔性封装技术可以将电子器件在柔性基底上进行封装,实现了更高的可靠性和适应性。
随着可穿戴设备和可弯曲显示器等市场的兴起,柔性封装技术将成为重要的发展方向。
3. 绿色环保封装技术随着环保意识的提高,绿色环保封装技术也备受关注。
未来的电子封装技术需要使用更环保的材料和制造工艺,尽可能降低对环境的影响。
- 1、下载文档前请自行甄别文档内容的完整性,平台不提供额外的编辑、内容补充、找答案等附加服务。
- 2、"仅部分预览"的文档,不可在线预览部分如存在完整性等问题,可反馈申请退款(可完整预览的文档不适用该条件!)。
- 3、如文档侵犯您的权益,请联系客服反馈,我们会尽快为您处理(人工客服工作时间:9:00-18:30)。
三维封装的现在和未来微电子学一班随着便携式电子系统复杂性的增加, 对VLSI集成电路用的低功率、轻型及小型封装的生产技术提出了越来越高的要求。
同样, 许多航空和军事应用也正在朝该方向发展。
为满足这些要求, 现在产生了许多新的3- D 封装技术, 或是将裸芯片, 或是将MCM 沿z 轴叠层在一起, 这样, 在小型化方面就取得了极大的改进同时, 由于z 平面技术总互连长度更短, 会产生寄生电容, 因而系统功耗可降低约30%。
三维(3D)封装技术的分类三维封装的结构类型有3种: 一是埋置型3D封装,即在多层基板底层埋置IC 芯片,顶层组装IC芯片,其间高密度互连; 二是有源基板型3D封装,即在Si或GaAs 衬底上制造多层布线和多种集成电路,顶层组装模拟IC芯片和其它元器件; 三是叠层型3D封装,即把多个裸芯片或封装好芯片或多芯片模块( MCM)沿Z轴叠装、互连,组装成3D封装结构。
由于叠层型3D封装适用范围广,并且工艺相对简单,成本相对较低,已引起国外多家公司的注意,如Actel , IBM, Harris, Mo to rola 等著名公司都在积极开展叠层型3D封装的研究工作。
下面将重点介绍叠层型3D封装。
1.埋置型3D 结构这是一种实施最早( 八十年代) , 也是最为灵活方便的3D, 同时又可作为后布线的芯片互连技术, 能大大减少焊点, 提高电子产品可靠性的电子封装技术。
埋置型3D 结构又可分为基板开槽埋置型和多层布线介质埋置型, 如图1所示。
在混合集成电路( H IC) 多层布线中埋置R、C 元件已经普遍, 而埋置IC芯片和R、C 后的布线顶层仍可贴装各类IC 芯片, 就可构成更高组装密度的3D-MCM 结构。
由于布线密度及功率密度都很高, 所以这种3D-MCM 所使用的基板多为高导热的Si 基板、AIN 基板或金属基板。
上图是AIN 基板多层布线介质埋置IC 的3D-MCM 结构, 制作方法与常规多层布线技术相同。
2.有源基板型3D 结构自从IC 出现以来, 人们就试图将一个复杂的电子整机甚至电子系统都集成在一大片Si 圆片内, 成为圆片规模IC( WSI) 。
今天的VLSI、ASIC( 专用集成电路) 已部分地实现了WSI, 如CPU、DSP、摄录一体机等, 就是一个个小系统。
有些芯片的尺寸达到近30mm 见方, 能集成数千万个器件。
这种有源Si基板再多层布线, 上面再安装多芯片, 就可形成有源基板型的3D-MCM, 从而以立体封装形式达到了WSI 所能实现的功能。
无论是一个大尺寸的复杂IC 作为Si 基板还是WSI 作为Si 基板来进一步实现3D, 其关键是要解决有源Si基板的成品率问题, 因为是成品率决定成本、价格。
而解决成品率和成本、价格的有效办法之一是降低Si 基板有源部分的复杂性和集成度, 并对重要或关键部分增加心要的冗余设计。
这类有源基板型的3D-MCM 结构如下图所示。
有源基板型3D-MCM 的主要优点,一是工艺与一般半导体IC工艺相同,从而可实现大规模工业化生产, 并随着半导体艺技术的发展而不断提高; 二是Si 基板与其上面安装的IC 芯片能达到应力完全匹配, 从而使电子产品有更高的可靠性。
3. 叠层型3D 结构叠层型3D, 是将LSI 、VLSI 芯片、MCM 或WSI 无间隙的层层叠装而成,是研制开发的非常活跃的3D 结构。
上图是在基板的两侧用直接芯片贴装( DCA) 方法形成的3D 结构, 芯片连接分别采用了丝焊( WB) 、载带自动焊( TAB) 和倒装焊( FC) 。
最常见的裸芯片叠层3D封装是先将生长凸点的好芯片倒扣焊接在薄膜载体上,这种薄膜载体的材质为陶瓷或环氧玻璃,上面有导体布线,内部互连焊点,两侧有外部互连焊点,再把多个薄膜载体叠装互连。
其结构见下图。
三维(3D)封装技术的优点与局限性尺寸和重量3- D 设计替代单芯片封装缩小了器件尺寸、减轻了重量。
尺寸缩小及重量减轻的那部分取决于垂直互连的密度。
和传统的封装相比, 使用3- D技术可缩短小尺寸、减轻重量达40~ 50 倍。
表1从体积和重量上比较了TI 公司3- D 裸芯片封装和分立、2- D 封装( 通常所说的MCM) 。
由表1 可见, 相对MCM 技术、3- D 封装技术可缩小体积5~ 6 倍, 减轻重量2~ 13 倍; 而相对分立式封装技术, 3- D 封装技术可缩小体积10~ 20 倍, 减轻重量3~ 19 倍。
这些都是因为解决了传统技术所带来的多余重量和尺寸问题。
就Aladdin 并行处理器来说, 它比Cray X- MP 处理器的尺寸和体积分别要缩小660 和2700 倍。
硅片效率封装技术的一个主要问题是PCB 芯片焊区, 如图1 所示, MCM 由于使用了裸芯片, 焊盘减小了20~ 90% , 而3- D 封装则更有效地使用了硅片的有效区域, 这被称之为硅片效率,硅片效率是指叠层中总的基板面积与焊区面积之比, 因此和其他2- D 封装技术相比, 3- D 技术的硅片效率超过延迟延迟指的是信号在系统功能电路之间传输所需要的时间。
在高速系统中, 总延迟时间主要受飞行时间限制, 飞行时间是指信号沿互连传输的时间, 飞行时间t 与互连长度成正比, 因此缩短延迟就需要用3- D 封装缩短互连长度。
缩短互连长度, 降低了互连伴随的寄生电容和电感, 因而缩短了信号传输延迟。
例如, 使用MCM 技术的信号延迟缩短了约300% 。
而使用3- D 技术由于电子元件相互间非常接近, 延迟则更短, 如图 2 所示。
噪声噪声通常被定义为夹杂在有用信号间不必要的干扰, 影响着信号的信息。
在高性能系统中, 噪声处理主要是一个设计问题, 噪声通过降低边缘比率、延长延迟及降低噪声幅度限制着系统性能, 会导致错误的逻辑转换。
噪声幅度和频率主要受封装和互连限制。
在数字系统中存在4 个主要噪声源:1) 反射噪声; 2) 串扰噪声; 3) 同步转换噪声;4) 电磁干扰( EMI) 。
所有这些噪声源的幅度取决于信号通过互连的上升时间, 上升时间越快, 噪声越大。
3- D 技术在降低噪声中起着缩短互连长度的作用, 因而也降低了互连伴随的寄生性。
另一方面, 如果使用3- D 技术没考虑噪声因素, 那么噪声在系统中会成为一个问题。
比方说, 如果互连沿导线的阻抗不均匀或其阻抗不能匹配源阻抗和目标阻抗, 那么就潜在一个反射噪声,进一步说, 如果互连间距不够大, 也会潜在串扰噪声。
由于缩短互连、降低互连伴随的寄生性, 同步噪声也被减小,因而, 对于同等数目的互连,产生的同步噪声更小。
功耗电子系统中散失的能量E 与互连寄生电容C的关系为E = CV2 , 因而功耗p= fCV2 , 其中, V 为通过C 的摆动电压, f 为每秒的转变数目。
由于寄生电容和互连长度成比例, 所以, 由于寄生性的降低, 总功耗也降了下来。
例如, 10% 的系统功耗散失在PWB 上的互连中, 如果采用MCM 技术制造产品, 功耗将降低5 倍, 因而产品比PWB 产品要少消耗8%的功耗, 而如果采用3- D 技术制造产品,由于缩短了互连长度, 降低了互连伴随的寄生性,功耗则会更低。
速度3- D 技术节约的功率可以使3- D 器件以每秒更快的转换速率( 频率) 运转而不增加功耗, 此外, 寄生性( 电容和电感) 的降低, 3- D 器件尺寸和噪声的减小便于每秒的转换率更高, 这使总的系统性能得以提高。
例如, 采用3- D MCM 集成技术的Aladdin 并行处理器比Cray X- MP 处理器每个单位体积可获得35000 百万条指令数秒( MIPS) 和10800 浮点运算次数/ 秒( FLOPS) 的改善。
互连适用性和可接入性假定典型芯片厚度为6mm, 如图3 所示, 在3- D 封装图形中, 距叠层中心元件等互连长度的元件有116 个, 而采用2- D 封装技术, 距中心元件等距离的元件只有8 个, 因而, 叠层互连长度的缩短降低了芯片间的传输延迟。
此外, 垂直互连可最大限度地使用有效互连, 而传统的封装技术则受诸如通孔或预先设计好的互连的限制。
由于可接入性和垂直互连的密度( 平均导线间距的信号层数)成比例, 所以3- D 封装技术的可接入性依赖于垂直互连的类型。
外围互连受叠层元件外围长度的限制, 与之相比, 内部互连要更适用、更便利。
带宽在许多计算机和通信系统中, 互连的带宽( 特别是存储器的带宽) 对性能有所限制, 因而, 低潜伏( 延迟) 、宽母线是非常理想的。
例如, 闻名于世的Intel Pentium Pro 公司将CPU 和2 级存储器用多孔PGA 封装在一起以获得大的存储器带宽。
令人激动的是3- D 封装技术可能被用来将CPU 和存储器芯片集成起来, 避免了高成本的多孔PGA。
3D封装目前所遇到问题对于3D-TSV阵列堆叠,关键要素有通孔形成/填充、晶圆减薄、质量评价与检测技术、凸点形成和芯片与芯片/衬底的键合等。
这些问题的解决将依赖于大量新型设备与工艺的开发。
图 1在设计方案提出之后,设备和材料就成为制造3D-TSV IC的关键因素减薄技术与设备减薄技术面临的首要挑战就是超薄化工艺所要求的<50μm的减薄能力。
在这个厚度上,硅片很难容忍减薄工程中的磨削对硅片的损伤及内在应力,其刚性也难以使硅片保持原有的平整状态。
目前业界的主流解决方案是采用东京精密公司所率先倡导的一体机思路,将硅片的磨削、抛光、保护膜去除、划片膜粘贴等工序集合在一台设备内,硅片从磨片一直到粘贴划片膜为止始终被吸在真空吸盘上,始终保持平整状态,从而解决了搬送的难题。
刻蚀技术与设备TSV制程都面临一个共同的难题:通孔的刻蚀。
目前通常有两种方法:激光钻孔以及深反应离子刻蚀(DRIE)。
激光加工系统供应商Xsil公司为TSV带来了最新解决方案,Xsil称激光钻孔工艺将首先应用到低密度闪存及CMOS传感器中,随着工艺及生产能力的提高,将会应用到DRAM中。
在TSV刻蚀设备领域,Lam Research推出了第一台300mm TSV刻蚀设备2300Syndion,并已发货至客户。
而Aviza针对TSV先进封装也推出了Omegai2L刻蚀系统,日月光(ASE)已宣布将采用此系统研发先进制程技术。
晶圆键合技术与设备EVG公司(奥地利)自2002年起,便致力于针对3D集成开发300mm晶圆键合设备,其首款300mm多反应腔3D键合系统已在2008年完成。
CEA-Leti (法国)及SET(法国)成功开发出新一代高精度(0.5μm)高键合力(4000N)的300mm晶圆器件键合设备FC300错误!未找到引用源。
质量评价与检测技术相关设备可以预见,TSV的特殊性还会给3D IC制造的检测和量测带来前所未有的困难,控制TSV通孔工艺需要几何尺寸的量测,以及对刻蚀间距和工艺带来的各种缺陷进行检测。