非导电材料的放电加工
电火花新加工技术及其发展趋势
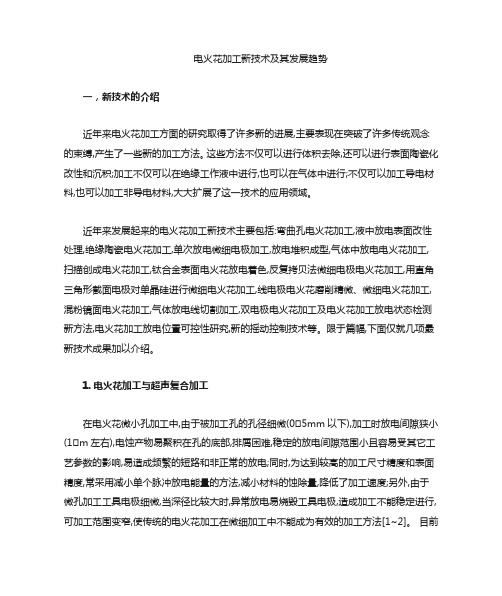
电火花加工新技术及其发展趋势一,新技术的介绍近年来电火花加工方面的研究取得了许多新的进展,主要表现在突破了许多传统观念的束缚,产生了一些新的加工方法。
这些方法不仅可以进行体积去除,还可以进行表面陶瓷化改性和沉积;加工不仅可以在绝缘工作液中进行,也可以在气体中进行;不仅可以加工导电材料,也可以加工非导电材料,大大扩展了这一技术的应用领域。
近年来发展起来的电火花加工新技术主要包括:弯曲孔电火花加工,液中放电表面改性处理,绝缘陶瓷电火花加工,单次放电微细电极加工,放电堆积成型,气体中放电电火花加工,扫描创成电火花加工,钛合金表面电火花放电着色,反复拷贝法微细电极电火花加工,用直角三角形截面电极对单晶硅进行微细电火花加工,线电极电火花磨削精微、微细电火花加工,混粉镜面电火花加工,气体放电线切割加工,双电极电火花加工及电火花加工放电状态检测新方法,电火花加工放电位置可控性研究,新的摇动控制技术等。
限于篇幅,下面仅就几项最新技术成果加以介绍。
1.电火花加工与超声复合加工在电火花微小孔加工中,由于被加工孔的孔径细微(0 5mm以下),加工时放电间隙狭小(1 m左右),电蚀产物易聚积在孔的底部,排屑困难,稳定的放电间隙范围小且容易受其它工艺参数的影响,易造成频繁的短路和非正常的放电;同时,为达到较高的加工尺寸精度和表面精度,常采用减小单个脉冲放电能量的方法,减小材料的蚀除量,降低了加工速度;另外,由于微孔加工工具电极细微,当深径比较大时,异常放电易烧毁工具电极,造成加工不能稳定进行,可加工范围变窄,使传统的电火花加工在微细加工中不能成为有效的加工方法[1~2]。
目前常采用的提高电火花加工能力的方法,如人工排气法,强迫冲液或抽液法、加速工作液循环等方法,常因加工条件或加工要求的限制而无法实现。
因此,为改善电火花加工性能,在微细加工中,采用超声电火花复合加工是非常有效的手段。
在电极上附加超声振动,就可以使电极端面频繁进入合适的放电间隙,提高火花击穿的概率;同时由于超声的空化作用和泵吸作用,可以增大被加工材料的去除量,加速工作液循环,改善间隙放电条件,从而提高被加工孔的深径比、加工稳定性、生产率和脉冲电源的利用率,并且在振幅得到良好控制的情况下,可以获得更高的加工精度。
各种加工方法的加工精度
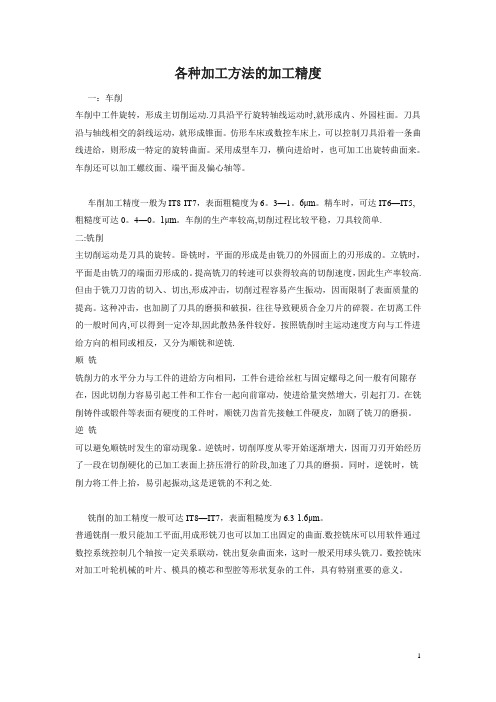
各种加工方法的加工精度一:车削车削中工件旋转,形成主切削运动.刀具沿平行旋转轴线运动时,就形成内、外园柱面。
刀具沿与轴线相交的斜线运动,就形成锥面。
仿形车床或数控车床上,可以控制刀具沿着一条曲线进给,则形成一特定的旋转曲面。
采用成型车刀,横向进给时,也可加工出旋转曲面来。
车削还可以加工螺纹面、端平面及偏心轴等。
车削加工精度一般为IT8-IT7,表面粗糙度为6。
3—1。
6μm。
精车时,可达IT6—IT5,粗糙度可达0。
4—0。
1μm。
车削的生产率较高,切削过程比较平稳,刀具较简单.二:铣削主切削运动是刀具的旋转。
卧铣时,平面的形成是由铣刀的外园面上的刃形成的。
立铣时,平面是由铣刀的端面刃形成的。
提高铣刀的转速可以获得较高的切削速度,因此生产率较高.但由于铣刀刀齿的切入、切出,形成冲击,切削过程容易产生振动,因而限制了表面质量的提高。
这种冲击,也加剧了刀具的磨损和破损,往往导致硬质合金刀片的碎裂。
在切离工件的一般时间内,可以得到一定冷却,因此散热条件较好。
按照铣削时主运动速度方向与工件进给方向的相同或相反,又分为顺铣和逆铣.顺铣铣削力的水平分力与工件的进给方向相同,工件台进给丝杠与固定螺母之间一般有间隙存在,因此切削力容易引起工件和工作台一起向前窜动,使进给量突然增大,引起打刀。
在铣削铸件或锻件等表面有硬度的工件时,顺铣刀齿首先接触工件硬皮,加剧了铣刀的磨损。
逆铣可以避免顺铣时发生的窜动现象。
逆铣时,切削厚度从零开始逐渐增大,因而刀刃开始经历了一段在切削硬化的已加工表面上挤压滑行的阶段,加速了刀具的磨损。
同时,逆铣时,铣削力将工件上抬,易引起振动,这是逆铣的不利之处.铣削的加工精度一般可达IT8—IT7,表面粗糙度为6.3-1.6μm。
普通铣削一般只能加工平面,用成形铣刀也可以加工出固定的曲面.数控铣床可以用软件通过数控系统控制几个轴按一定关系联动,铣出复杂曲面来,这时一般采用球头铣刀。
数控铣床对加工叶轮机械的叶片、模具的模芯和型腔等形状复杂的工件,具有特别重要的意义。
模具加工中的电极是什么东西

模具加工中的电极是什么东西一种是:电火花加工的放电端,用来加工型腔、刻字等,多制作成所需形状,材料为石墨、铜或铝(少见)。
另一种是:线切割加工的放电端,材料为钼丝,它的原理是通过电控部分对其施加高频高电压,当电极(钼丝)与接地端(工件)接触时,即形成高频打火产生高温,将与钼丝接触的工件面(极小的一条缝)迅速溶掉,即所谓的线切割。
所谓多电极加工,是指要加工的部位要求的精度比较高,对放电部位要进行2次或者两次以上放电,前期为平动较大的粗放电加工,后期为平动小的精放电加工电极就是电火花放电加工的放电点,金属的,预先做好形状,通过加工给工件上电腐蚀出规定的形状。
一个火花机要加工一个工件需要不止一个电极,不同的活要用不同的电极因为粗加工时用一个电极打效率,但是损耗比较大,粗打后换另外一个电极精打,但是电极的装卡需要很高的精度,再有就是电极找正什么的,总之是个很需要经验的活,因为再次装卡导致的误差很可能会影响模具的精度误差。
不过现在用快速夹具应该可以解决吧,伊罗哇夹具很好不过就是太贵几万块吧。
我不是搞模具的,我是搞火花机的,知道的没专门搞模具的多,一些问题只是根据我自己的理解回答的UG的我也没听过,至于画电极我觉得画电极加工路径似乎人没有计算机准确吧,你这里说的画电极是不是根据模具的样子来制作电极吧,说画是先把要做的电极图纸画出来啊,这个对模具加工是第一步啊,很重要的模具加工中的打电极是什么?技术点在哪里?电火花加工与线切割又有什么区别呢?电火花加工和电火花线切割加工都是通过间隙放电腐蚀工价加工。
不同的是线切割是使用钼丝切割出所需的轮廓形状。
简单的说,电火花加工能加工盲孔,而线切割加工只能加工通孔数控电火花线切割快走丝慢走丝区别?快走丝在专业术语中叫做:高速往复走丝电火花线切割机慢走丝在专业术语中叫做:低速单向走丝电火花线切割机二者的特点:往复走丝电火花线切割机床的走丝速度为6~12 m/s,产品的最大特点是具有1.5度锥度切割功能,加工厚度可超过1000mm以上,,应用于各类中低档模具制造和特殊零件加工,成为我国数控机床中应用最广泛的机种之一。
放电加工在微纳加工中的应用研究

放电加工在微纳加工中的应用研究近年来,随着微纳加工技术的快速发展,放电加工作为一种重要的微纳加工方法在微纳加工领域中发挥着重要的作用。
放电加工技术以放电为基础,利用电火花放电破坏材料表面的微小颗粒,从而实现微细加工。
在微纳加工中,放电加工具有高精度、高效率、无切削力等优势,因此在微纳加工的各个领域都得到了广泛应用。
首先,放电加工在微纳传感器制造中的应用研究方面展现了其独特的优势。
微纳传感器作为一种用于检测和测量微小物理量的传感器,其制造过程需要高精度的加工技术。
放电加工技术能够实现微米级和亚微米级的精度,使得微纳传感器的制造更加精细。
此外,放电加工技术还可以实现微纳传感器芯片的二次构造和微结构的附加加工,进一步提高传感器制造的复杂度和功能性。
其次,放电加工在微纳光学器件制造中的应用研究也十分重要。
微纳光学器件作为一种应用在光学系统中的微小尺寸光学元件,对于制造和加工精度要求很高。
放电加工技术可以实现微米级甚至亚微米级的精度加工,非常适合用于制造微纳光学器件。
通过放电加工技术,可以制造出具有特殊光学性能的微光栅、微透镜等微纳光学器件,满足不同光学系统对光学器件的精密要求。
此外,放电加工在微纳流控芯片制造中也具有广泛的应用前景。
微纳流控芯片作为一种用于微流体领域的微小尺寸芯片,其中的微流道和微通道要求具有高精度的加工和制造。
放电加工技术可以实现微米级的精度,可以用于加工微纳流控芯片中的微流道和微通道。
通过放电加工技术,可以制造出具有复杂结构和多层连接的微纳流控芯片,实现生物、医药、化学等领域的微流体控制。
除了以上提到的应用领域外,放电加工在微纳加工中还具有其他各种应用研究的潜力。
例如,在微纳电子器件制造中,放电加工技术可以用于制造微米尺寸的电极和导线;在微纳梳理制造中,放电加工技术可以实现微米级的精密加工;在微纳机械加工中,放电加工技术可以制造微米级的齿轮、螺纹等零部件。
放电加工技术的广泛应用使得微纳加工领域的研究更加丰富多样,也为微纳科技的发展提供了有力的支持。
特种加工简介

4
3 5
6
3 7 8
Tankertanker Design
一、概述
第一节 特种加工的产生和发展
1 特种加工的名称
Tankertanker Design
1.1 特种加工的产生和发展
2 特种加工的发展
从第一次产业革命以来,一直到第二次世界 大战以前,并没有产生特种加工的迫切要求,直 到1943年。
前苏联科学家拉扎连柯夫妇研究开关触点 遭受火花放电腐蚀损坏的现象和原因,发现电火 花的瞬时高温可使局部的金属熔化、气化而被腐 蚀掉,开创和发明了电火花加工。
(2)低速走丝线切割机床(WEDM-LS )
走丝速度慢,一般小于0.2m/s,电极丝做单向移动, 一般采用铜丝做电极丝,加工液为去离子水。 运丝稳定性好,加工精度高,表面质量好,但成本 高。这是国外生产和使用的主要机种。
Tankertanker Design
线切割数控编程要点 • 目前生产的线切割加工机床都有计算机自动 编程功能,即可以将线切割加工的轨迹图形 自动生成机床能够识别的程序。 • 高速走丝线切割机床一般采用3B(个别扩充为 4B或5B)格式,而低速走丝线切割机床通常采 用国际上通用的ISO(国际标准化组织)或EIA(美 国电子工业协会)格式。为了便于国际交流和 标准化,特种加工学会和特种加工行业协会 建议我国生产的线切割控制系统逐步采用ISO 代码。
Tankertanker Design
特种加工
Tankertanker Design
Tankertanker Design
Tankertanker Design
Tankertanker Design
3 1 2 3
电火花加工
电火花线切割加工
电火花加工技术

电火花加工技术的应用及其发展1.电火花加工技术的简介从前苏联科学院拉扎连柯夫妇在1943年研制出世界上第一台实用化电火花加工装置以来,电火花加工技术得到了飞速的发展,电火花加工技术是历史最悠久的特种加工方法之一,在模具制造业,航空和航天,电子等众多领域得到了广泛的应用。
电火花加工又称放电加工,也有称电脉冲加工,它是一种直接利用热能和电能进行加工的工艺。
电火花加工与金属切削加工的原理完全不同,在加工过程中,工件和工具不接触,而是靠工具与工件之间的脉冲性火花放电,产生局部,瞬间的高温把金属材料逐步的蚀除掉。
由于放电的过程产生火花所以也称电火花加工。
图1. 电火花加工的原理图如图1的原理图所示,工件与工具分别连接到脉冲电源的两个不同的极性的电极上。
当两电极加上脉冲电源后,工件和电极保持适当的距离,就会把工件和工具之间的介质击穿,形成放电通道。
放电通道产生瞬间高温,使工件表面的材料融化甚至气化,同时也使工作介质气化。
在放电间隙处迅速热膨胀并产生爆炸。
工件表面一部分材料被蚀除掉抛出,形成微小的电蚀坑。
脉冲放电结束后,经过一段时间间隔,使工作液恢复绝缘,脉冲电源反复作用于工件和工具电极上,上述过程不断重复进行,工件逐渐被加工成想要的形状。
2.电火花加工技术的应用范围由于电火花加工有其独特的优越性,再加上数控水平和工艺技术的不断提高,其利用领域日益扩大,已经覆盖到机械、宇航、航空、电子、核能、仪器、轻工等部门,用以解决各种难加工材料、复杂形状零件等有特殊要求的零件的制造,成为常规切削、磨削加工的重要补充和发展:模具制造是电火花成型加工应用最多的领域,而且非常的典型。
2.1以下简单介绍电火花成则加工在模具制造方面的的应用1.高硬度零件加工对于某些要求硬度较高的模具,或者是硬度要求特别高的滑块、顶块等零件,在热处理后其表固硬度高达50HRc以上,采用机加的方式将很难加工这么高硬度的件.采用屯火花加工可以不受材料硬度的影响。
作业-电火花加工、电火花线切割原理 2
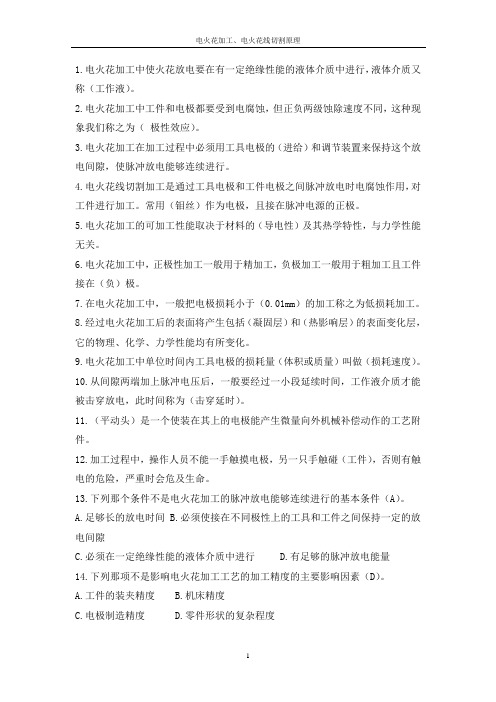
1.电火花加工中使火花放电要在有一定绝缘性能的液体介质中进行,液体介质又称(工作液)。
2.电火花加工中工件和电极都要受到电腐蚀,但正负两级蚀除速度不同,这种现象我们称之为(极性效应)。
3.电火花加工在加工过程中必须用工具电极的(进给)和调节装置来保持这个放电间隙,使脉冲放电能够连续进行。
4.电火花线切割加工是通过工具电极和工件电极之间脉冲放电时电腐蚀作用,对工件进行加工。
常用(钼丝)作为电极,且接在脉冲电源的正极。
5.电火花加工的可加工性能取决于材料的(导电性)及其热学特性,与力学性能无关。
6.电火花加工中,正极性加工一般用于精加工,负极加工一般用于粗加工且工件接在(负)极。
7.在电火花加工中,一般把电极损耗小于(0.01mm)的加工称之为低损耗加工。
8.经过电火花加工后的表面将产生包括(凝固层)和(热影响层)的表面变化层,它的物理、化学、力学性能均有所变化。
9.电火花加工中单位时间内工具电极的损耗量(体积或质量)叫做(损耗速度)。
10.从间隙两端加上脉冲电压后,一般要经过一小段延续时间,工作液介质才能被击穿放电,此时间称为(击穿延时)。
11.(平动头)是一个使装在其上的电极能产生微量向外机械补偿动作的工艺附件。
12.加工过程中,操作人员不能一手触摸电极,另一只手触碰(工件),否则有触电的危险,严重时会危及生命。
13.下列那个条件不是电火花加工的脉冲放电能够连续进行的基本条件(A)。
A.足够长的放电时间B.必须使接在不同极性上的工具和工件之间保持一定的放电间隙C.必须在一定绝缘性能的液体介质中进行D.有足够的脉冲放电能量14.下列那项不是影响电火花加工工艺的加工精度的主要影响因素(D)。
A.工件的装夹精度B.机床精度C.电极制造精度D.零件形状的复杂程度15.有关单工具电极直接成型法的叙述中,不正确的是(A)。
A.需要重复装夹B.不需要平动头C.加工精度不高D.表面质量很好16.脉冲参数主要包括(A)、脉冲间隙、峰值电压、峰值电流等电参数。
非导电工程陶瓷电火花磨削技术

LUY nh n Y Ll L ioe g J R ni I o g og U i I ap n I ej i X e
( olg f ca i l n lc o i E g er g C iaU ies yo t l m, o g ig2 7 6 ) C l e h nc dEet nc n i ei , hn nv r t f e oe D n yn 5 0 e o Me aa r n n i Pr u 1
非导 电工程 陶瓷 电火花 磨 削技术 木
刘永红 于丽丽 李小朋 纪仁杰
( 国石 油大学机 电工程 学院 东营 中 27 6) 50 1
摘 要 :开 发 出双 电极 同步 伺服 跟 踪 电火 花 磨 削 新 技 术 ,该 技 术 突 破 了传 统 的机 械 磨 削和 电解 电火 花机 械 复 合 磨 削方 法 ,利 用
等优点。
关键词:非导电工程陶瓷
中图 分 类号 :T 6 G6 1
电火花磨削
材料去除率
表面粗糙度
Te h o o y f r El c r c l s h r e Gr n i g 0 n c n uc i e c n l g o e t i a c a g i d n f Di No - o d tv
导电磨轮 与紧贴非导电工程陶瓷工件表面作 自动伺服进给运动 的薄片辅助 电极间的放电实现 电火花磨削。对非导电的 A 2 3 1 0 工程陶瓷进行加工试验,给出加工参数如脉冲宽度 、脉冲 间隔、峰值 电压、峰值电流 、磨轮转速 以及铜 片电极厚度等对材料 去除率和表面粗糙度的影响规律关系。试验 结果表 明,该种新型加工技术具有效率 高、表面质量好 、成本低和对环境无污染
- 1、下载文档前请自行甄别文档内容的完整性,平台不提供额外的编辑、内容补充、找答案等附加服务。
- 2、"仅部分预览"的文档,不可在线预览部分如存在完整性等问题,可反馈申请退款(可完整预览的文档不适用该条件!)。
- 3、如文档侵犯您的权益,请联系客服反馈,我们会尽快为您处理(人工客服工作时间:9:00-18:30)。
半导体、光学玻璃和工程陶瓷等难导电硬脆材料因具有耐磨性强、硬度高、绝缘性好等优良的性能,而在电子、光学、仪器仪表、航空航天、国防及民用工业等诸多领域有着越来越广泛的应用
•
放电加工的优点
放电加工和其他的加工方法相比,具备很多的优点1)加工过程是非接触加工、加工过程中没有宏观切削力可以用来进行微小孔加工等;
2)电解电火花复合加工设备简单、成本低,可以获得较好的表面质量,在微细加工中有很好的应用前景。
电火花辅助加工:
•高压电火花加工
•辅助电极电火花加工
•辅助电极可控烧蚀方式使被加工的非导
电陶瓷材料快速软化后机械磨削去除
高压电火花加工:
将难导电硬脆材料直接作为介质,利用尖电极与平板电极之间的高压产生强烈的辉光放电来蚀除难导电硬脆材料。
此方法只适用于对薄壁难导电硬脆材料进行打孔,虽然加工速度较快、成本较低,但由于加工表面过于粗糙,只能用于粗加工。
辅助电极电火花加工:
直接在难导电硬脆材料表面紧压金属板、金属网等导电
材料,或通过蒸镀、涂覆等方法在难导电硬脆材料表面形
成金属、碳素等导电层,并以煤油为工作液,利用火花放
电瞬间产生的高温作用使煤油热分解出来的碳、工具电极
溅射出来的金属及其化合物在难导电硬脆材料表面形成新
的导电层,从而在难导电硬脆材料与工具电极之间一直能
形成放电的回路,使得电火花加工能连续进行下去。
辅助电极可控烧蚀方式使被加工的非导电陶瓷材料快速软化后机械磨削
该方法采用导电的金属粘合剂砂轮作为磨轮,在磨轮和非
导电陶瓷之间连续送入导电片状辅助电极,在脉冲电压作用
下使磨轮与导电片状辅助电极之间产生火花放电,同时向加
工区域连续或间歇通入能与导电片状辅助电极材料产生烧蚀
放热效应的助燃气体(如氧气),使导电片状辅助电极材料
在电火花放电作用下达到燃点温度以上而处于熔融甚至气化
状态,然后与通入的助燃气体发生烧蚀反应,生成烧蚀产物,
并释放出大量的热量作用于非导电陶瓷材料表面,使非导电
陶瓷材料表面加热至软化甚至熔融状态,然后在磨轮的机械
磨削作用下磨削去除。
电解电火花复合加工(ECDM)是近年来在特
种加工领域出现的一种新技术,常用于耐热玻璃、陶瓷、
工业金刚石、石英等非导电材料的加工。
电解电火花放电
加工的工作原理如图所示:。
施加在工具电极(负极)和辅助电极(正极)之间的电
压较低时(如12V),则正负极之间仅有电化学反应发生,
并在工具电极(负极)表面生成氢气气泡,在氢气气泡生
成速率达到能相互合并形成氢气气膜后,氢气气膜阻绝电
极与电解液之间的导通,当电极与电解液之间的电压超过
一定临界值时,就会击穿氢气气膜而产生如放电加工的放
电现象,紧靠工具电极的工件材料则受到电化学放电产生
的高温以及高温时化学蚀刻的影响而发生材料的移除,达
到加工的目的。
目前较为认同的观点是,材料的去除是火花放电的热蚀
除和化学蚀除的复合作用。
从影响材料去除率的因素来讲,
加工电压和电流影响最大,其次是电解液。
电解质与生产率之间的关系
从对氧化铝陶瓷进行电解电火花加工实验中可以看出,在
给出的三种电解质中,NaOH水溶液最适合电火花加工非导
电的氧化铝陶瓷,并且随着NaOH浓度及加工电压的增加,
生产率也在增加。
电化学电火花加工方法的改进•郭教授提出为了加
速形成绝缘气体,
可以在工具电极上
作超声振动的方法。
可以看出工具电极作超声振动对加工效1、电极夹头2、工具电极3、超声波振动头4、绝缘层5、工件6、电解液7、辅助电极8、气体膜
超声振动对加工效率的影响
•超声振动的空化作用,更易于电解作用产生的气体在电极绝缘表面产生气体膜,形成绝缘条件从而缩短加工中的电解阶段时间,增大火花放电时间。
•有利于排出加工产物,改善极间环境,提高加工效率。
加工电流的影响加工条件:脉冲宽度为80μs ;脉冲间隔为50μs ;工件为氧化铝陶瓷;工作液为20%NaOH 溶液;工具电极为φ2mm 钢丝电极;超声振动频率为40KHZ ,超声振动幅值为μm.如图加工效率随电流
的增大而提高。
一、电流的增大能够
增加火花能量。
二、增大电流提高了
电化学产生气体的速
度
结论
•电化学电火花加工能够进行绝缘体材料的电火花加工,使不导电材料表面形成电火花放电的条件•为了能构提高加工效率可以采用在工具电极一端添加超声振动的方法提高效率。
•其导电溶液最好使用20%的NaOH电解质溶液
发展衍生:电化学放电线切割
其材料去除原理与ECDM 基本相同。
与电火花成型加工和电火花线切割加工间的关系类似,将ECDM 中的棒状电极用电极丝代替,并辅以走丝运动后,能够实现非导电硬脆材料的线切割加工。
谢谢。