提高水性环氧防腐底漆耐盐雾性的办法
水性环氧防腐涂料的研究与制备
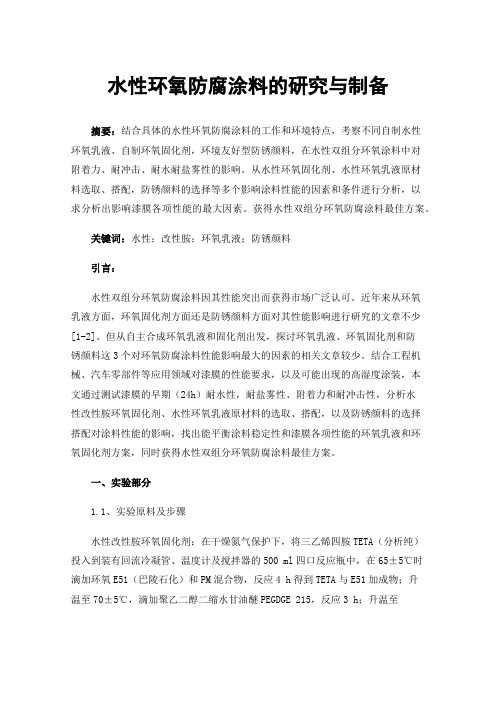
水性环氧防腐涂料的研究与制备摘要:结合具体的水性环氧防腐涂料的工作和环境特点,考察不同自制水性环氧乳液、自制环氧固化剂,环境友好型防锈颜料,在水性双组分环氧涂料中对附着力、耐冲击、耐水耐盐雾性的影响。
从水性环氧固化剂、水性环氧乳液原材料选取、搭配,防锈颜料的选择等多个影响涂料性能的因素和条件进行分析,以求分析出影响漆膜各项性能的最大因素。
获得水性双组分环氧防腐涂料最佳方案。
关键词:水性;改性胺;环氧乳液;防锈颜料引言:水性双组分环氧防腐涂料因其性能突出而获得市场广泛认可。
近年来从环氧乳液方面,环氧固化剂方面还是防锈颜料方面对其性能影响进行研究的文章不少[1-2]。
但从自主合成环氧乳液和固化剂出发,探讨环氧乳液、环氧固化剂和防锈颜料这3个对环氧防腐涂料性能影响最大的因素的相关文章较少。
结合工程机械、汽车零部件等应用领域对漆膜的性能要求,以及可能出现的高湿度涂装,本文通过测试漆膜的早期(24h)耐水性,耐盐雾性、附着力和耐冲击性,分析水性改性胺环氧固化剂、水性环氧乳液原材料的选取、搭配,以及防锈颜料的选择搭配对涂料性能的影响,找出能平衡涂料稳定性和漆膜各项性能的环氧乳液和环氧固化剂方案,同时获得水性双组分环氧防腐涂料最佳方案。
一、实验部分1.1、实验原料及步骤水性改性胺环氧固化剂:在干燥氮气保护下,将三乙烯四胺TETA(分析纯)投入到装有回流冷凝管、温度计及搅拌器的500 ml四口反应瓶中,在65±5℃时滴加环氧E51(巴陵石化)和PM混合物,反应4 h得到TETA与E51加成物;升温至70±5℃,滴加聚乙二醇二缩水甘油醚PEGDGE 215,反应3 h;升温至75±5℃,滴加单环氧化合物BEG(江苏森菲达)封端,反应至活泼氢当量为(120±10),最后加入去离子水稀释到60%固含。
环氧乳液:将E20溶于PM中,加入用PEG-8000、PEG4000(陶氏)自制的反应型乳化剂,在65-75℃,高速分散(2000-3000/min)下缓慢加入去离子水直至相转换,稀释至所需的固含和粘度。
水性环氧防腐漆配方及应用研究

水性环氧防腐漆配方及应用研究随着环保意识的增强,对高性能防腐涂料的需求也十分迫切。
本文介绍了水性环氧防腐涂料的制备方法,讨论了水性环氧体系的优点。
标签:水性环氧;底漆;防腐性引言随着国家对环境保护的重视及人们环保意识的日益增强,水性涂料成为涂料发展的重要方向和研究热点。
水性环氧防腐涂料是以水为分散介质,环氧树脂作为主要成膜物质的一种的涂料,因其绿色环保、生产施工方便、无安全隐患、成本较低等优势而成为研究热点。
1.实验部分1.1实验原料和制备方法主要原料:水,润湿剂,分散剂,增稠剂,消泡剂,助溶剂,闪锈剂,环氧乳液及固化剂(美国翰森,亨斯曼,美国空气化学,自制),功能填料(三聚磷酸铝粉,磷酸锌粉),滑石粉,硫酸钡,云母粉等。
A组份制备方法:在搅拌釜中依次加入水,润湿剂,分散剂,闪锈剂,助溶剂,消泡剂等,控制搅拌速度为400转/min,搅拌20min-30min,然后将滑石粉,磷酸锌粉,硫酸钡,三聚磷酸铝粉,云母粉等加入上述混合液中,开启高速分散模式,转速900转/min。
搅拌1h,加入反应釜中分散均匀,最后加入环氧树脂乳液,增稠剂制得水性环氧防腐涂料A组份,并将A组份研磨至细度≤40um。
B组分制备方法:在搅拌釜中加入消泡剂,润湿流平剂,水性环氧固化剂搅拌均匀即可。
1.2水性环氧防腐涂料基本配方水性环氧防腐涂料基础配方见表1所示。
1.3试验仪器和水性环氧防腐涂料性能检测漆膜硬度仪(TQC-SP0500),高速分散搅拌器(FJS-300),盐雾试验仪(YWX/Q-250),NDJ旋转粘度计等。
水性环氧防腐涂料依据《水性环氧树脂防腐涂料》HG/T4759-2014标准要求制作检测样板。
2.结果与讨论2.1水性环氧树脂乳液与固化剂体系对成膜性能的影响2.1.1胺氢当量对漆膜基本性能的影响本试验采用自主开发的水性环氧树脂固化剂体系,研究胺氢当量对漆膜基本性能的影响。
其结果如表2所示。
2.1.2防腐清漆对比试验影响本文通过自主开发的水性环氧乳液清漆体系与市售产品清漆体系进行对比试验,其性能结果如表3所示。
防腐涂层耐盐雾性试验方法及相关标准

防腐涂层耐盐雾性试验方法及相关标准1.定义、目的及应用防腐涂层的耐盐雾性是指防腐涂层对盐雾侵蚀的抵抗能力。
由于沿海及近海地区的空气中富含呈弥散微小水滴状的盐雾,含盐雾空气除了相对湿度较高外,其比重也较空气大,容易沉降在各种物体上,而盐雾中的氯化物具有很强的腐蚀性,对金属材料及保护涂层具有强烈的腐蚀作用。
作为耐腐蚀试验之一的耐盐雾试验标准方法,包括中性盐雾试验、醋酸-盐雾试验、铜加速的醋酸-盐雾试验(CASS试验)以及湿(盐雾)/干燥/湿气—循环腐蚀环境试验。
特别中性盐雾试验被认为是评定与海洋气氛有密切关系的材料的有关性质的最有效的方法。
因为它可以模拟由湿度或温度,或者由两者共同引起的某些加速作用的基本条件。
可以讲耐盐雾性试验是各类防腐蚀涂料的加速性能试验中最经典、应用最广泛的检测项目,虽然对耐盐雾性试验与实际性能的相关性还是有很大的争论,但是实际应用还是非常普遍。
同时耐盐雾性试验方法也是金属材料耐腐蚀性能试验的主要方法之一。
所以广泛应用于评价和比较底材、前处理、涂层体系或它们的组合体的耐腐蚀情况,另外在许多工业生产、采矿、地下工程、国防工程以及鉴定程序中也成为非常有用的手段。
醋酸-盐雾试验和铜加速的醋酸-盐雾试验(CASS试验)的两种方法被认为更适于钢或锌基压铸件上的装饰性镀铬、镉以及化学处理的铝上的磷化或阳极化等。
而湿(盐雾)/干燥/湿气—循环腐蚀环境试验则主要用来模拟在室外侵蚀环境中发生的腐蚀过程,如海洋环境。
由于与天然老化之间有很好的相关性,所以一些标准的循环己成功用于汽车工业、建筑涂料和通用型防腐蚀涂料的评价中。
2.相关标准各国都有该试验方法的标准,内容基本相同,表1列出耐盐雾性试验方法的标准和试验参数的比较。
表1耐盐雾性试验方法,标准和相关参数标准应用提出单位试验参数GB/T 1771-1991 中国国标(35±2)℃ISO 7253 国际标准(35±2)℃ISO 11997-1:2005 国际标准(35±2)℃ASTM B117-1997 美国ASTM (35±2)℃ASTM B287-1997 美国ASTM (35±2)℃ASTM B368-1997 美国ASTM (35±2)℃3.试验设备和参数(1)盐雾试验箱基本组成和工作原理目前国内外普遍采用的试验没备是盐雾试验箱。
耐盐雾的表面处理
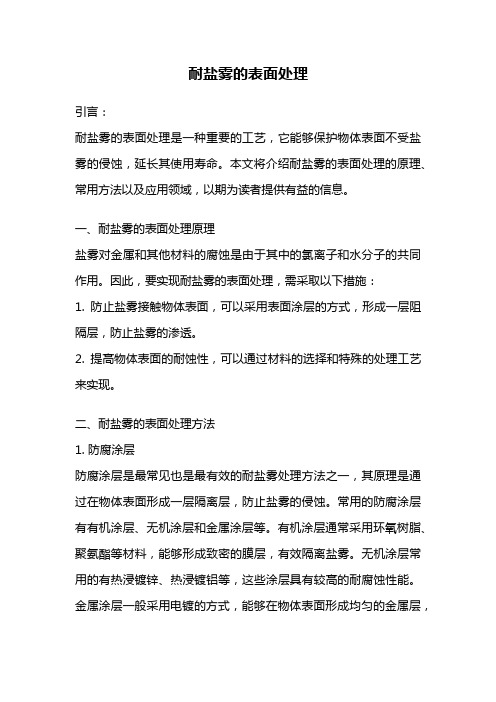
耐盐雾的表面处理引言:耐盐雾的表面处理是一种重要的工艺,它能够保护物体表面不受盐雾的侵蚀,延长其使用寿命。
本文将介绍耐盐雾的表面处理的原理、常用方法以及应用领域,以期为读者提供有益的信息。
一、耐盐雾的表面处理原理盐雾对金属和其他材料的腐蚀是由于其中的氯离子和水分子的共同作用。
因此,要实现耐盐雾的表面处理,需采取以下措施:1. 防止盐雾接触物体表面,可以采用表面涂层的方式,形成一层阻隔层,防止盐雾的渗透。
2. 提高物体表面的耐蚀性,可以通过材料的选择和特殊的处理工艺来实现。
二、耐盐雾的表面处理方法1. 防腐涂层防腐涂层是最常见也是最有效的耐盐雾处理方法之一,其原理是通过在物体表面形成一层隔离层,防止盐雾的侵蚀。
常用的防腐涂层有有机涂层、无机涂层和金属涂层等。
有机涂层通常采用环氧树脂、聚氨酯等材料,能够形成致密的膜层,有效隔离盐雾。
无机涂层常用的有热浸镀锌、热浸镀铝等,这些涂层具有较高的耐腐蚀性能。
金属涂层一般采用电镀的方式,能够在物体表面形成均匀的金属层,提高其耐盐雾能力。
2. 防护膜防护膜是一种常用的耐盐雾处理方法,其原理是在物体表面形成一层具有耐蚀性的薄膜,能够有效隔离盐雾。
常用的防护膜有聚合物膜、陶瓷膜和金属膜等。
聚合物膜通常采用溶液法或浸渍法涂覆在物体表面,形成一层致密的薄膜。
陶瓷膜一般采用化学气相沉积或物理气相沉积的方法制备,具有优异的耐蚀性能。
金属膜常用的有氧化铝膜和氧化锌膜,这些膜能够在物体表面形成一层致密的氧化层,提高其耐盐雾能力。
三、耐盐雾的表面处理应用领域耐盐雾的表面处理广泛应用于海洋工程、汽车制造、航空航天等领域。
在海洋工程中,由于海水中盐分较高,物体容易受到盐雾的侵蚀,因此对海洋工程设备和结构进行耐盐雾的表面处理是必要的。
在汽车制造中,汽车长期在恶劣的环境下运行,如海岸地区或冬季的盐雪地区,车身容易受到盐雾的侵蚀,因此对汽车表面进行耐盐雾的处理能够延长其使用寿命。
在航空航天领域,飞机在飞行过程中会暴露在高湿度和盐雾环境下,如果不进行耐盐雾的处理,会严重影响飞机的安全性能。
涂料盐雾

我来跟大家交流一下以共同上进为目的,一般来讲如今做防腐漆(水性和油性)都要求做耐盐雾,亚硝酸钠和钼酸酸钠虽然有较好的瞬间的抗闪锈性,但不利于耐盐雾性和环保性甚至致癌,故涂料这一块现在基本上已经不用,对于要开发新的产品在原则上应不予选用。
我做水性工程师近十年了,我把我的经验跟大家交流一下,以推进中国水性漆的快速发展!以下是我的一点心得:第一抗闪锈:油性漆不存在抗闪锈性,据说油性涂料要想提高耐盐雾性最好的方法是提高碳钢的钝化膜质量和涂膜的附着力.那么水性漆的抗闪锈和耐盐雾是不是也可以从这方面入手呢,抗闪锈剂的加入是不是可以显著的提高碳钢的钝化膜质量呢,我根据以上原理选用了能挥发且能迅速钝化碳钢的抗闪锈剂。
这种抗闪锈剂不含亚硝酸盐等无机盐类而全部是挥发性的有机物,成分最终全部挥发掉,这样在解决抗闪锈的同时不但不会影响涂膜的耐盐雾性反而能极大的提高耐盐雾性能!对抗闪锈的效果是相当的好。
最后谈一下谈一下抗闪锈的影响因素:抗闪锈剂的种类,添加浓度和溶液的PH对效果影响较大!建议大家选用钝化型的抗闪锈剂。
(如果大家感兴趣的话我把这类供应商推荐给大家希望对大家有用,联系资料附后.)第二耐盐雾性:不管是油性还是水性涂料,其防锈性和耐盐雾性应遵循以下原则:1. 选好相应的树脂和防绣颜料(环保无毒的这是发展的趋势),这是基础,树脂要对基材有非常好的干/湿附着力和防锈性,酸值要低且玻璃化温度至少要高于盐雾实验的温度35度(放在第6点说);颜料当然也要选具有优异的防锈性、涂膜抗起泡性和膜下钢板耐蚀性。
值得推荐的环保防锈颜料有:美国哈罗克司的SZP-391,磷酸锌铁MHH-LXT(优异),羟基亚磷酸锌(Nalin 2),有机缓蚀剂改性的无机颜及三聚磷酸铝等。
跟铬酸盐相比就防锈性能而言:磷酸锌铁MHH-LXT要好许多,而SZP-391和Nalin 2跟其相当或稍好。
前者是进口的贵一些但效果好许多的。
主要体现在具有优异的防锈性、涂膜抗起泡性和涂膜下钢板耐蚀性。
涂料做盐雾试验的方法步骤

涂料做盐雾试验的方法步骤
进行涂料的盐雾试验是为了测试涂料在盐雾环境中的耐腐蚀性能。
一般来说,盐雾试验的方法步骤如下:
1. 样品准备,首先,需要准备好需要进行盐雾试验的涂料样品。
样品应该是代表性的,通常是涂在金属板上。
2. 设备准备,接下来,需要准备好盐雾试验设备,通常是盐雾
试验箱。
确保设备处于正常工作状态,盐水浓度和温度符合试验要求。
3. 样品安装,将涂料样品安装在盐雾试验箱内,确保样品表面
完全暴露在盐雾环境中。
4. 设定试验条件,根据涂料的要求,设定盐雾试验的时间和温度。
一般来说,试验时间为数百小时至数千小时不等。
5. 进行试验,开始盐雾试验,让设备产生盐雾环境,并保持设
定的试验条件。
6. 观察和记录,在试验过程中,定期观察样品的表面情况,记录涂层的腐蚀情况,包括出现的锈斑、脱落等情况。
7. 试验结束和分析,当试验时间结束后,取出样品,进行表面清洁和检查。
根据试验结果进行分析,评估涂料的耐腐蚀性能。
以上就是进行涂料盐雾试验的一般方法步骤。
在实际操作中,还需要根据具体涂料的要求和标准进行相应的调整和处理。
希望这些信息能够对你有所帮助。
石墨烯改性环氧富锌底漆的制备及耐盐雾性能研究

即可制得石墨烯改性环氧防腐涂料甲组分。
D90≤10 μm的石墨烯材料耐盐雾性能达3 000 h。
乙组分的制备过程为将两种固化剂按照质量比
另外石墨烯的制备方式也至关重要,目前市面上
例混合均匀后,转移至样品罐中即可。
的石墨烯制备方式主要由氧化还原方法和物理法制
1.3 石墨烯改性环氧富锌涂层的制备
备。通过氧化还原方法制备的石墨烯的晶格结构损坏
Flake Sizes
w(石墨烯)/%
石墨烯片径(D90)/μm ≤10
耐盐雾性能/h 3 000
≤20
2 300
0.75
≤40
1 500
≤90
500
墨烯晶格完整率较高,导电性较好,在涂层中能充分 发挥石墨烯的作用[9],本文采用的石墨烯均为物理法 制备。 2.2 石墨烯添加量对耐盐雾性能的影响
石墨烯添加量对富锌底漆耐盐雾性能具有较大 影响,随着配方中石墨烯添加量逐渐增加,涂层的导 电性不断增加,通过石墨烯间的搭接,锌粉之间形成 良好的电子传输通道,有效提高锌粉的利用率,更好 发挥锌粉的阴极保护作用。当石墨烯添加量继续增加 时,涂层导电性能不断增加,基材和腐蚀介质之间形成 良好的原电池效应,从而导致出现基材的快速腐蚀[10], 因此对石墨烯添加量的控制是影响耐盐雾性能的关 键。本文通过添加不同比例的石墨烯量,在其他实验 条件相同的情况下,筛选最佳的石墨烯添加量。图2是 不同石墨烯添加量的环氧富锌底漆在耐盐雾3 000 h 时的照片。当石墨烯添加量为0(质量分数,后同)时,
Sizes (500 h)
表2 不同石墨烯片径的石墨烯改性环氧富锌底漆耐盐雾 测试结果
Table 2 Salt Spray Resistance Test Results of Graphene Modified Epoxy Zinc-rich Primer with Different Graphene
关于耐盐雾技术要求

耐盐雾技术要求主要是针对材料、构件或产品在含有盐分的环境中能够抵抗腐蚀和性能退化的能力。
这些要求通常适用于海洋、沿海地区或其他高盐分环境中的应用,比如船舶、飞机、汽车以及电子设备等。
以下是实现耐盐雾技术要求的一些关键方面:
1. 材料选择:选择适合高盐分环境的材料是基础。
不锈钢、铝合金、某些塑料和橡胶等材料具有较好的耐腐蚀性能。
2. 表面处理:通过涂装、电镀、阳极氧化或化学转化膜等表面处理方法可以显著提高材料的耐盐雾性能。
3. 设计优化:设计时应尽量减少尖锐边缘和缝隙,以降低腐蚀的风险。
同时,设计应便于排水和清洁,避免盐分长时间滞留。
4. 防护涂层:应用防腐涂料可以形成保护层,隔离金属和腐蚀环境的直接接触。
涂层应均匀、无缺陷,并具有良好的附着力和耐久性。
5. 盐雾测试:为了评估产品的耐盐雾性能,通常会进行标准的盐雾试验。
这些测试模拟了盐分对材料的长期侵蚀作用,如中性盐雾试验(NSS)、醋酸盐雾试验(ASS)和铜加速醋酸盐雾试验(CASS)等。
6. 质量控制:在生产过程中,应实施严格的质量控制措施,确保所有的耐盐雾处理步骤都达到了规定的标准和要求。
7. 维护和检查:即使产品已经经过耐盐雾处理,定期的维护和检查仍然是必要的,以确保其在整个使用寿命期间保持良好的性能。
满足耐盐雾技术要求的产品能够在恶劣环境中保持功能性和结构完整性,延长使用寿命,并减少维护成本。
因此,在设计、制造和测试阶段都应充分考虑这些要求。
- 1、下载文档前请自行甄别文档内容的完整性,平台不提供额外的编辑、内容补充、找答案等附加服务。
- 2、"仅部分预览"的文档,不可在线预览部分如存在完整性等问题,可反馈申请退款(可完整预览的文档不适用该条件!)。
- 3、如文档侵犯您的权益,请联系客服反馈,我们会尽快为您处理(人工客服工作时间:9:00-18:30)。
提高水性环氧防腐底漆耐盐雾性的办法
1、使用助剂,提高碳钢钝化膜的质量。
如钝化型抗闪锈剂,可增
强干态和湿态的附着力;如水分子阻换剂,将粘接界面变成疏水型;如硅烷偶联剂,可提高界面附着力。
2、提高涂膜干态和湿态下的附着力,需要选择一个合适的树脂固
化体系。
亲水基含量太高的体系往往湿态粘接强度差,水分子渗透到界面的可能性大增。
2-1 固化后的涂膜疏水性越强,水分就越难以渗透。
2-2 固化后的涂膜跟底材的湿态附着力越好,水分就难以渗透到界面。
一方面取决于体系产生的羟基越多,跟底材的附着力越好,如多氨基的固化体系,另一方面取决于体系的憎水性和湿态下剥离强度要高。
2-3经过钝化的金属界面附着力更优。
3、涂膜的Tg>35°C,这样盐雾试验中,涂膜不会软化,变形小就不
易起泡。
需要选择一个合适的树脂固化体系。
3-1油性环氧的很容易Tg>35°C,因为均相体系中环氧树脂分子和固化剂分子充分缠绕接触,水性环氧则不同,以下因素会制约其交联度。
3-1-1 乳胶粒子的大小,粒子越粗,粒子中间部位很难接触到树脂或固化剂的分子,交联密度下降,体现为涂膜硬度不够。
反之,则固化度提高,Tg提高。
3-1-2 树脂和固化剂的相容性,影响接触机率。
3-1-3二者的配比取决于残留量,树脂残留多,则固化剂要减量。
3-1-3-1,固化剂为水溶性的,则树脂残留多,所以固化剂要适
当减量;
3-1-3-2树脂固化剂均为乳胶粒子,则树脂固化剂均会残留,粒
子大的组分残留多,可考虑等当量;
3-1-3-3自乳化环氧树脂乳化油性固化剂的体系,硬度上来相对
较慢,树脂固化剂均会残留,但树脂残留多,固化剂残留少,
所以固化剂要适当减少;
3-1-3-4水乳型固化剂乳化油性环氧的体系,硬度上来相对较慢,
树脂固化剂均会残留,但树脂残留多,固化剂残留少,所以固
化剂要适当减少;
3-1-3-5乳液型自乳化固化剂配合自乳化环氧体系,二者可相互
乳化,相容性较好,二者接触充分,尽管二者均有残留,但相
对残留少,可考虑等当量配比。
该体系相对具有更高的耐盐雾
参数。
3-1-4 固化剂分子中氨基和刚性基团的数量。
氨基多,交联度
高,刚性基团多,Tg和涂膜硬度相对就较高。
3-2 固化的温度和时间,影响交联度,从而能影响Tg。
3-3 固化体系的活化能,影响交联度和固化速度,从而能影响Tg。
4、合适的颜基比,使树脂能充分浸润颜料体系。
一般PVC在30-35%
是比较合适的选择范围,
5、形成碱性涂膜,可阻止电化学反应,防止析出氢气导致鼓泡,
一个合适的树脂固化体系。
5-1腐蚀发生的电化学反应:
在一般情况下,只要水中有0.4摩尔/升的盐的浓度,钠和氯离子就可以穿过涂膜扩散,因此在有盐雾的情况下,下列阴
极反应就可能发生:
阴极:有氧存在时:O2 + 2H2O + 4e =4OH-
无氧存在时:2H+ + 2e=H2 (因为水存在电解平衡:OH- + H+ = H2O)
对应的阳极也发生以下反应:
阳极:Fe-2e=Fe2+
阴极和阳极反应的结果,生成氢氧化亚铁,随后氧化成带结合水的三氧化二铁。
离子透过涂膜比水和氧盐慢得多,涂膜所含羟基离节后使其带负电,因此会选择性的吸收阳离子透过涂膜(如钠离子)。
经研究证实,阳离子透过涂膜结果使得涂膜起泡脱落。
5-2无氧存在时会产生氢气,这就是上面说到的涂膜发生鼓泡的另外一个原因。
从以上两个阴极反应可以看出只要涂膜的PH值呈碱性且很高的话,反应就不会向右进行从而阻止了氧分子的溶解;在无氧存在时由于PH较高,这样H+浓度就非常的低,释氢反应就不会发生。
故就抑制了阴极反应,没有了阴极反应阳极反应自然也就大大减低了。
阴阳
两极反应的停止就阻止了电子的传递,故涂膜的电阻就不会降低同时保持良好的防腐性。
6、颜填料的选择。
尤其是防锈颜料的选择.防锈颜料分为物理防锈
和化学防锈两种,前者有云母氧化铁和超细云母粉,这些片状
物料能增强漆膜的致密性,对腐蚀介质起屏蔽作用,降低渗透
率;后者如铅系、铬酸盐、磷酸盐颜料,原采用磷酸锌和三聚
磷酸铝,后在配方中使用一种新型的复合磷酸铝为主防锈颜料,以磷酸锌和三聚磷酸铝为辅,磷酸盐离解产生的磷酸根可使金
属表面钝化,引起阳极极化,而锌粒子和铝离子则在阴极反应
引起阴极极化。
可大大提高涂膜的防锈能力。
7、交联密度(参照第3点),需要一个合适的树脂固化体系。
7-1乳胶粒子的大小,影响树脂和固化剂的混合均匀度,从而影
响交联度。
选择粒径小的环氧或者固化剂乳液,具有更高的交
联密度。
7-2多官能度的树脂和固化剂体系,提高交联密度。
7-3相容性好,成膜性好,影响混合均匀度和相互接触机率,从
而影响交联度。
7-4合适的固化温度和时间。
7-5树脂和固化剂体系的活化能。
活性高的环氧体系在相同温度
下具有更高的交联度和更快的固化速度。
7-6树脂/ 固化剂的当量比,影响交联度。
8、涂膜的的厚度
当然耐盐雾性能也跟涂膜的厚度也有相当大的关系,涂膜厚水氧分子要穿透涂层需要的时间就长。
耐盐雾性与涂膜厚度成正比。
9、树脂中单官能团或增塑型乳化剂的含量
9-1外乳化类型通过添加乳化剂后相转变的方式乳化环氧,乳化剂有单环氧基的或者增塑型的,往往需要添加10-20%才能充分乳化环氧树脂,影响固化物的致密性和耐热性、硬度、耐腐蚀性等参数,自乳化性环氧乳液为双官能团环氧树脂接入亲水基,交联密度高,耐腐蚀性相对较高。
9-2.EP380\EP750自乳化环氧体系,配合胺类固化剂及碱性颜料固化后形成了碱性较高的涂膜,可阻止电化学反应,抑制腐蚀金属和防止阳离子堆积和析出氢气导致起泡。
10、环氧固化剂体系中亲水基和疏水基的相对和绝对数量
10-1亲水基含量高,如亲水型分子结构的固化剂,固化后的涂膜水分透入的机率大增,耐盐雾性受影响。
10-2反之,疏水基含量高,如油性固化剂,固化后形成的涂膜具有天然憎水性,湿态附着力提高,水分透入的机率减少,耐盐雾性较高。
10-3亲水基和疏水基含量均高,相比单纯的亲水基含量高,固化后的涂膜具有一定的疏水性,耐盐雾性相对提高。
10-4环氧固化剂体系相对较少的亲水基具有更高的憎水性、湿态附着力和耐盐雾性。
参考资料:
1、水性环氧涂料防腐涂料耐盐雾性能研究曾凡辉陈红梅谢续江(株洲时代绝缘有限责任公司湖南 412001)
2、水性环氧涂料耐盐雾性影响因素的研究沈春华杜飞飞姚唯亮金贤君(上海涂料有限公司技术中心上海 200062)
3、水性环氧体系对金属防腐底漆耐盐雾性的影响卢学军(长沙新德航化工有限公司湖南长沙 410000)
4、涂料盐雾百度文库
5、提高涂料耐盐雾性的办法百度文库。