第7章 测控——【电主轴的设计与选型】
电主轴的基础方案设计书研究(2)

[1]张曙《数控机床发展的新趋势》.数控机床市场. 2004年08期.
[2]刘丽云,王元娥.普通机床数控化改造中要考虑的主要问题[J].装备制造技术,2007,(4).
[3]赵忠敏.机床数控化改造的研究[J]煤矿机电.2005,(5).
[4]杨贵杰,秦冬冬,高速电主轴的关键技术及发展趋势。哈尔滨工业大学硕士学位论文2008
[12]周延佑.世界数控系统的发展与机床数控化改造[J].中国机电日报,2003.3.16.
[13]雷学东.数控原理与系统[M].南京:南京大学出版社,2002.6.
[14]卢胜利,王睿鹏,祝玲.现代数控系统[M].北京:机械工业出版社,2006.
[15]王计文.浅谈普通机床的数控改造[J].机床与液压.1999(3):82-83.
[20]罗永顺.普通机床数控化改造设计中关键问题的研究[J].机床与液压,2005,(6):193—195.
[21]张亚力.简述数控技术的发展趋势[J].国土资源高等职业教育研究,2006,(2).
[22]董笑鹏,张立娟,王兵然.浅谈我国数控技术的发展与前景[J].机电产品开发与创新,2009,(1).
电主轴(如图)
二、课题的研究方法:
1.课题的研究方法与技术路线
(1)总体设计方案
电主轴所融合的技术:1.高速轴承技术2.高速电机技术3.润滑4.冷却装置5.内置脉冲编码器
6.自动换刀装置7.高频变频装置。
(2)轴承整系统化设计
电主轴的关键技术是轴承的使用和设计,然后对轴承的润滑和冷却系统做出技术整合和设计。
由于高速加工不但可以大幅度提高加工效率,而且还可以显著提高工件的加工质量,所以其应用领域非常广泛,特别是在航空航天、汽车和模具等制造业中。于是,具有高速加工能力的数控机床已成为市场新宠。目前,国内外各著名机床制造商在高速数控机床中广泛采用电主轴结构,特别是在复合加工机床、多轴联动、多面体加工机床和并联机床中。电主轴是高速数控加工机床的“心脏部件”,其性能指标直接决定机床的水平,它是机床实现高速加工的前提和基本条件。
数控技术第7章 数控机床的伺服系统7-何雪明

(2)闭环伺服系统 有位置检测装置,且装在机床工作台上,直接检测 工作台的实际位移。 利用CNC装置的指令值与位置检测装置的检测值 的差值进行位置控制。 精度高,其运动精度取决于检测装置的精度,与传 动链的误差无关。 适用于大型或比较精密的数控设备。 (3)半闭环伺服系统 有位置检测装置,且装在电机或丝杠的端头,检测 角位移,间接获得工作台的位移。 精度比闭环控制低,滚珠丝杠的精度影响位置检测 的精度。适用于中小型数控机床。
4. 按反馈比较控制方式分类
(1)数字-脉冲比较伺服系统 将数控装置发出的数字(或脉冲)指令信号与检测装 置测量的以数字(或脉冲)形式表示的反馈信号直接 进行比较,产生位置差值,形成闭环和半闭环控制。 (2)相位比较伺服系统 采用相位工作方式,指令信号与反馈信号均以相位形 式表示并进行比较。 (3)幅值比较伺服系统 6以位置检测信号的幅值大小来反映机床位移量的大 小,并与指令信号进行比较。 (4)全数字控制伺服系统 由位置、速度和电流组成的三环反馈控制全部数字化。
2. 数控机床对主轴伺服系统的要求 (1)足够的输出功率。 主轴转速高,输出转矩小;主轴转速低,输出转 矩大。要求主轴驱动装置具有恒功率性质。 (2)调速范围宽。 数控机床的变速依照指令自动执行,要求能够在 较宽的转速范围内进行无级调速,较少中间传递 环节,简化主轴箱。 (3)定位准停功能。 为使得数控车床具有螺纹切削等功能,要求主轴 能与进给驱动实行同步控制。 在加工中为自动换刀,要求主轴具有高精度的准 停功能。
4. 反应式步进电机主要特征
(1)步距角和静态步距误差 步进电机步距角α与定子绕组的相数m、转子的齿数z、 通电方式k有关,即有:α=360°/(mzk)。 其中:m相m拍时,k=1;m相2m拍时,k=2,依 此类推。例如,三相三拍,z=40时,α= 360°/(3×40×1)=3°。 静态步距误差:在空载情况下,理论的步距角与实际 的步距角之差,以分表示,一般在10′之内。 步距误差主要由步进电机步距制造误差,定子和转子 间气隙不均匀以及各相电磁转矩不均匀等因素造成。
精品课件-现代数控机床(第二版)-现代数控机床7章

• ⑴ 直线电动机驱动进给单元的构成
• 如图7-11高速直线电动机进给单元由直线电动机、工作 台、滚动导轨、精密测量反馈系统和防护系统等部分构成 。
• 1—工作台 2—防护罩 3、12—导轨 4—床身 5、8— 辅助导轨
• 6、14—冷却板 7—次级 9—测量系统 10—光栅尺 11—拖链 13—初级
• 由图7-12a演变而来的直线电动机,其初级和次级的长度 是相等的。由于初级和次级之间要做相对运动,为保证初 级与次级之间的耦合保持不变,实际应用中初级和次级的 长度是不相等的。
• 与旋转电动机一样,改图变直7线-1电2 动机初级绕组的通电次序 ,可改变电动机运动的方向,因而可使直线电动机作往复 直线运动。在实际应用中,我们也可将次级固定不动,而 让初级运动。
• 为此,在电主轴结构设计时,必须严格遵守结构对称的原 则。如图7-10所示的电主轴结构,电动机转子与主轴之间 通过过盈套筒产生的过盈配合来传递扭矩,尽
• 量避免采用键、螺纹和其它零件连接
• ;在拆卸主轴时,是用高压泵将高压油从转子内套左端小 孔a压入环形内孔e,套筒1的内径在高压油的压力作用下 要胀大,这样就可以方便地将转子拆下。
• 为了避免上述主轴传动方式带来的缺点,高速加工主轴常 采用电主轴的结构形式。
•1.电主轴结构的基本构成
• 所谓电主轴结构就是将电机的转子直接作为机床的主轴, 主轴单元的壳体就是电机座,配合其它安全保障措施,从 而实现了电机与机床主轴的一体化。如图7-3所示,电主 轴结构通常由电主轴单元、轴承及其润滑单元、主轴冷却 单元以及动平衡单元组成。
• 磨削、钻孔加工和光整加工。 • 液体动、静压轴承目前主要用于重载大功率场合。这种轴
承是采用液体的动力 • 和静力相结合的方法,使主轴在油膜中支撑旋转。优点是
第七章 主传动系统设计

(2)第二变速组(b组)
ub1=42/42=1/1 ub2=22/62=1/2.82=1/φ3 级比:1:1/φ3= φ3:1 级比指数:x1=3 此二传动副使Ⅲ轴得到6种连续等比数列,第 一次扩大了变速范围
称为:第一扩大组
x1=3 表示相邻传动比相距 3 格
(3)第三变速组 (c) 组
uc1=60/30=2/1=φ2/1
2、拟定转速图的步骤 例:中型机床 Z=12 φ=1.41
n min=31.5 n电=1450 rpm
⑴ 确定变速组数
取P=2 或 3 则 Z=P1 x P2 x P3 ⑵ 确定变速组排列方案
因此,主运动电动机的功率:
N= N切+N空+N附 = N切/ηs + N空
⑵进给运动功率的确定 进给运动所消耗的功率比较小,因此,
如果进给运动与主运动或空行程运动共用 电机,则进给运动所耗功率可忽略不计 进给运动采用单独电机驱动,其功率可按 下式计算: NS=Q·Vs/60000ηs Q(N):进给牵引力
第七章 机床主要技术参数的确定
第一节 概述
金属切削机床的基本功能是: 提供切削加工所必须的运动和动力。 其基本工作原理是:通过刀具与工件之间的 相对运动,由刀具切除工件加工表面多余的 金属材料,形成工件表面的几何形状、尺寸, 并达到其精度和表面质量要求。
第二节 主要技术参数的确定
机床的主要技术参数包括机床的主参数和 基本参数,基本参数可包括尺寸参数、运 动参数和动力参数。
我们称之为: 变速组 或 传动组 按先后顺序定义为: a b c 即: a 变速组
b 变速组 c 变速组
此主传动系统可实现 12 级转速 为了更全面、更清楚地表示传动路线
电主轴技术讲座第六讲电主轴的选用

60/ 73 HSK - A63 18 000 67. 5/ 90 HSK - A63 18 000
60/ 77 HSK - A63 20 000 160/ 191 ISO - B40 14 000 160/ 191 HSK - A63 18 000
FP150 22 000 19 000 14 000 FL170 25 000 22 000 16 000 170 FM170 20 000 18 000 12 000 FP170 12 000 10 000 8 000
A 0. 3/ 92 000 0. 33/ 80 000 1. 6/ 80 000
最高转 速时输 出功率
/ kW
最高转 速时输 出转矩 / N·m
轴向静
态刚度/ ( N/μm)
MFW - HSK 170 591. 5 9 000 20 21. 2 13 500 20
1709/ 24 E63 MFW - HSK
230 693 5 000 32 61. 1 14 500 34 2305/ 24 A - E63 MFW - HSK
10/ 25 000 12/ 22 000 13. 5/ 25 000
— —
冷却 量/ (L/ mm)
— — 0. 5 0. 5/ 1 1 1 1. 5
1. 5/ 2
2. 5/ 3 3/ 3. 5
3. 5/ 4
3/ 3. 5
4/ 5 4/ 5 5/ 6 6/ 7
6/ 7
ISO
锥度类型 HS K
GA MFI
(4) 注意正确选择轴承类型与润滑方式 。在满足 需求条件下 ,应尽量选用陶瓷球混合轴承与永久性油 润滑的组合 ,这样可省去润滑部件并简化维护 。
7 轴的设计及计算
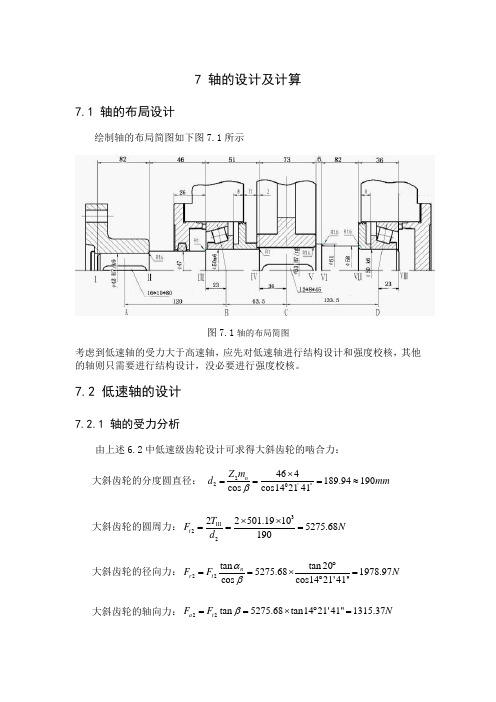
7 轴的设计及计算7.1 轴的布局设计绘制轴的布局简图如下图7.1所示图7.1轴的布局简图考虑到低速轴的受力大于高速轴,应先对低速轴进行结构设计和强度校核,其他的轴则只需要进行结构设计,没必要进行强度校核。
7.2 低速轴的设计7.2.1 轴的受力分析由上述6.2中低速级齿轮设计可求得大斜齿轮的啮合力: 大斜齿轮的分度圆直径: 220'''464189.94190cos cos142141n Z m d mm β⨯===≈ 大斜齿轮的圆周力:32222501.19105275.68190t T F N d III ⨯⨯===大斜齿轮的径向力:22tan tan 205275.681978.97cos cos1421'41''n r t F F N αβ︒==⨯=︒ 大斜齿轮的轴向力:22tan 5275.68tan1421'41''1315.37a t F F N β==⨯︒=7.2.2轴的材料的选择由于低速轴转速不高,但受力较大,故选取轴的材料为45优质碳素结构钢,调质处理。
7.2.3轴的最小直径根据教材【1】中15-2式可初步估算轴的最小直径,min d A =式中:0A —最小直径系数,根据教材【1】中表15-3按45钢查得0112=A P III —低速轴的功率(KW ),由表5.1可知:P III = 1.83kw n III —低速轴的转速(r/min ),由表5.1可知:n III =34.87r/min因此: min 11241.93d A mm === 输出轴的最小直径应该安装联轴器处,为了使轴直径-I II d 与联轴器的孔径相适应,故需同时选取联轴器的型号。
根据教材【1】中14-1式查得,ca A T K T III =式中:ca T —联轴器的计算转矩(N mm ⋅)A K —工作情况系数,根据教材【1】中表14-1按转矩变化小查得,1.5=A KT III —低速轴的转矩(N mm ⋅),由表5.1可知:3501.1910T N mm III =⨯⋅ 因此: 31.5501.1910751785ca A II T K T N mm ==⨯⨯=⋅ 按照计算转矩ca T 应小于联轴器公称转矩的条件,查标准GB/T 5014-2003或根据教材【2】中表14-4查得,选用LX2型弹性柱销联轴器,其具体结构及基本参数如图7.2以及表7.1所示,图7.2 LX2型弹性柱销联轴器结构形式图表7.1LX2型弹性柱销联轴器基本参数及主要尺寸由上表可知,选取半联轴器孔径42d mm =,故取42I II d mm -=,半联轴器的长度112L mm =,与轴配合的毂孔长度184L mm =。
电主轴设计模板

电主轴部件设计数据如下主轴转子(材料:20CrMnTi )和转子内套(材料:45#钢) 主轴转子结构 前轴颈直径(mm )最高转速(r/min ) 额定功率 (kW ) 额定转矩 (Nm )阶梯过盈套结构的特点阶梯过盈套是由两段相邻的过盈联结表面组成的、套内呈阶梯状的联结装置,如图1所示。
阶梯过盈套结构的特点主要有[2]:图1 阶梯过盈套的主要结构形式(1)为了便于拆卸,阶梯过盈套的内表面有一个阶梯。
当压力油注入油槽进行拆卸时,这个阶梯会对套产生一个轴向推力,如果两配合过盈面此时已形成了压力油膜,该轴向推力会自动地把阶梯过盈套从轴上推下来,过盈套两过盈面的阶梯差很小,通常在1mm 以下。
(2)在确定阶梯过盈套两结合面的过盈量的时候,应注意加工误差对最终过盈量的影响,特别是圆度误差和同轴度误差的影响。
通常过盈套两段的过盈量不一致。
但过盈套大小端过盈量的差值不能太大,其差值应补偿加工圆度和同轴度误差对过盈量的影响。
否则,将大大增加拆卸的难度。
(3)为方便拆卸,大小端配合面的宽度b1、b2应该一致。
阶梯过盈套过盈量的确定高速机床上所用的阶梯过盈套是一种可拆的过盈联结,工作时,配合面不允许产生塑性变形。
因此,过盈量应该控制在材料不产生塑性变形所允许的最大过盈量范围之内;另一方面它又必须大于该过盈联结传递负荷所需的最小过盈量。
设D为过盈套(包容件)的外径,d0为主轴内孔的直径,d为配合处(结合面)主轴的外径;l为配合面的有效长度(l=l1+l2),如图2所示。
图2阶梯过盈套传递力和转矩当过盈联结传递转矩为M(单位为Nm)时,结合面上所需最小结合压力P min,可按下式计算:=108..79KPa式中μ=0.08——配合面的摩擦系数由轴颈直径为145mm查轴承取d=160mm l=100mm D=200mmd0=80mm根据弹性力学原理,过盈联结传递负荷所需的最小有效过盈量δemin可按下式计算[3]:=0.52μm式中Ea、Ei——过盈套材料和主轴材料的弹性模量,20CrMnTi:密度:7.8×103kg/m3,弹性模量:207GPa泊松比:0.25屈服强度835MPa 45钢弹模210Gpa,泊松比0.3,密度7800千克/立方米屈服强度取355MpaCa、Ci——和包容件(过盈套)与被包容件(主轴)的直径比有关的系数=4.81=1.37式中va、vi——过盈套材料和主轴材料的泊松比必须指出,按式(3)所求的并不是最终所需的最小过盈量,还应考虑以下因素的影响:(1)配合表面的粗糙度。
电机与电气控制技术(第五版)课件第7章
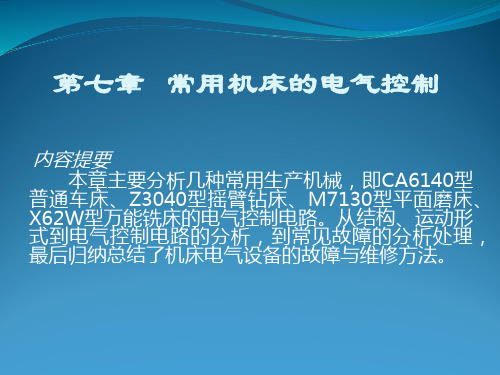
第五节 X62W型万能铣床电气控制电路 2
二、铣床的电力拖动形式和控制要求 铣床的主运动由一台笼型异步电动机拖动,直接起动,主轴电动机需 要正反转,但方向的改变并不频繁。 铣刀的切削是一种不连续切削,容易使机械传动系统发生振动,为了 避免这种现象,在主轴上装有飞轮,但在高速切削后,停车需要很长时 间,要求主轴在停机时有电气制动。 工作台可以做六个方向的进给运动,还可在六个方向上快速移动。其 进给运动和快速移动均由同一台笼型异步电动机拖动,直接起动,能够 正反转。 为防止刀具和机床的损坏,三台电动机之间要求有联锁控制,即在主 轴电动机起动之后另两台电动机才能起动运行。 冷却泵电动机只要求单向旋转。 具有完善的保护措施。
液压泵电动机M3由交流接触器KM4、 KM5控制正反转, 由热继电器FR2作过载保护。
冷却泵电动机M4因功率小,由开关QS2控制,不设过 载保护。
第三节Z3040型摇臂钻床电气控制电路 5
2.控制电路 由变压器TC提供127V交流电源给控制电路。控制 电路分:
1)主轴电动机M1的控制:按下按钮SB2,KM1线圈有 电,动合触点闭合, M1旋转并自锁。按下按钮SB1, M1失电停转。
第七章 常用机床的电气控制
内容提要
本章主要分析几种常用生产机械,即CA6140型 普通车床、Z3040型摇臂钻床、M7130型平面磨床、 X62W型万能铣床的电气控制电路。从结构、运动形 式到电气控制电路的分析,到常见故障的分析处理, 最后归纳总结了机床电气设备的故障与维修方法。
第二节 CA6140型普通車床电气控制电路 1
第三节 Z3040型摇臂钻床电气控制电路 1
一、摇臂钻床的主要结构 钻床是一种孔加工机床, 可用于在大、中型零件上进行 钻孔、扩孔、铰孔、锪孔、攻 丝及修刮端面等加工。摇臂钻 床是一种立式钻床,是机械加 工中的常用机床设备。Z3040 型摇臂钻床主要由底座、内立 柱、外立柱、摇臂、主轴箱、 工作台等组成。
- 1、下载文档前请自行甄别文档内容的完整性,平台不提供额外的编辑、内容补充、找答案等附加服务。
- 2、"仅部分预览"的文档,不可在线预览部分如存在完整性等问题,可反馈申请退款(可完整预览的文档不适用该条件!)。
- 3、如文档侵犯您的权益,请联系客服反馈,我们会尽快为您处理(人工客服工作时间:9:00-18:30)。
旗开得胜
读万卷书 行万里路
1
第7章 电主轴的测试仪器
现代机械设备发展的一个明显的趋势是向大型化、高速化、连续化和自动
化方向发展。现代的高速电主轴组成和结构越来越复杂,功能越来越强大,性
能和指标越来越高,同时,对设备的测试和维修要求越高,对检测高速电主轴
的仪器要求越来越精确。目前,对高速电主轴主要进行以下几个方面的检测。
7.1高速电主轴的回转精度测试[1]~[3]
[1]许可. 基于虚拟仪器LabVIEW的高速电主轴性能测试研究[D].哈尔滨工业大学,2013.
[2]陈长浩. 主轴运动精度的测试与研究[D].北京工业大学,2010.
[3]杨钢. 高速电主轴回转精度及静刚度测试研究[D].重庆大学,2008.
高速电主轴的回转精度,通常是指高速电主轴在加工的过程中,理想状态下
的回转中心线与现实情况下的回转中心线不重合。理想状态下的回转中心线,是
一条保持不变的直线。而现实中,由于振动,热温等原因,电主轴的回转中心有
所偏移。偏离程度可以描述出电主轴在回转过程中的回转误差。
主轴回转精度作为机床或仪器轴系工作性能与质量的重要指标,是影响精密
加工和测量精度的主要因素,测量和辨识主轴回转误差,是评定机床和仪器精度
的主要工作。
电主轴偏离的运动过程中,有三种形式:径向运动、轴向运动和倾角运动。
具体如下:
(1)径向运动是指转子在回转过程中的径向相对其理想轴线平行并沿着径
向平移运动,也叫做径向跳动。这种运动会导致教工过程中径向加工质量和精度
的降低。实际工况中尤其对铣削、磨削工序的影响较大,而对车削影响较小,仅
旗开得胜
读万卷书 行万里路
1
影响对圆的加工这种情况;
(2)轴向运动是指转子在回转过程中的轴向相对其理想轴的平移运动,也
叫做轴向窜动。和径向运动相反,这种运动不会影响径向加工表面,在实际工况
中对铣削、磨削工序的影响较小,而对车削过程的端面加工精度和质量影响较大。
(3)倾角运动是指转子在回转过程中的轴相对理想回转轴线形成某一变化
的角度。这种运动对轴向和径向的加工都有影响,其影响沿着轴向与径向都是不
一样的,倾角误差运动产生的最大径向误差是位于轴的某一端面,即角度摇摆半
径的最大位置。
然而,在实际测量转子的回转精度过程中,可以测量出在产生最大误差的工
作界面上的回转精度,即为整个轴线回转精度最大值。对于倾角误差运动的测试,
可以测试两个不同的截面的径向位移,在进行处理就可以得到角度摆动误差。因
此,对电主轴三种类型的回转精度测试只需要测试电主轴某截面的径向回转误差
测试和端面的轴向回转误差测试即可。
随着科学技术不断的快速发展,机床主轴回转精度测试也在不断升级。高速
电主轴的回转精度的测量常用方法有三种,分别为:打表测量法、单向测量法、
双向测量法。
(1)打表测量法
打表测量法,是最早的、简单的、容易操作的方法,既可以测试电主轴某
截面的径向回转误差,也可以测试端面的轴向回转误差,在现在许多工厂依然
在使用,但精度有待提高。通常可以使用仪器表(千分尺)直接测试电主轴回
转精度,也可以使用测量试件来评定主轴回转误差,测试示意图如图7.1所
示,某企业的几何精度检测如表7.1。工厂使用的仪器表如图7.2所示。
旗开得胜
读万卷书 行万里路
1
(a) 径向回转误差测试 (b)端面的轴向回转精度测试
图7.1 打表测量法
图7.2 测试仪器
表7.1 几何精度检测标准
序号 简图 检验 项目 允差mm 检验
工具
检验方法
参照JB 2670的有关
条文
旗开得胜
读万卷书 行万里路
1
G1 型式A 型式B 型式C 主轴定心面的径向
跳动
0.005
指示
器
5.6.1.2.2
型式A:固定指示
器,使其测头分别垂
直触及主轴锥体定心
面的大端和小端。转
动主轴检验。
误差分别计算。
误差以指示器两次读
数的最大差值计。
型式B、C:固定指示
器,使其测头垂直触
及主轴圆柱孔或圆锥
孔定心面。转动主轴
检验。
误差以指示器读
数的最大差值计。
G2
主轴的端
面跳动
(仅用于型式B的砂轮主轴) 指示
器
5.6.3.1.1
固定指示器,使
其测头垂直触及主轴
端面靠近外圆边缘
处。转动主轴检验。
误差以指示器读
数的最大差值计。
前端
轴承孔径
≤35 >35
0.005 0.008
G3 a. 0.010 指示
5.6.1.2.3
旗开得胜
读万卷书 行万里路
1
主轴接长
杆轴线的
径向跳
动:
a.靠近主
轴端部;
b.距主轴
端部L处
(仅用于
型式C
的砂轮
轴)
b. 器
在主轴锥孔内插入一
检验棒,固定指示
器,使其测头触及检
验棒表面:
a.靠近主轴端部;
b.距主轴端部L处。
转动主轴检验。
拔出检验棒,旋转90°
重新插入,再依次检
验三次。
a、b误差分别计
算。误差以四次测量
结果的平均值计
在垂直平面内和水
平面内均需检验
长度L
100 200
0.015 0.020
(2)单向测量法
单向测量法,是将一个位移传感器安装在回转面的一个方向上,如图7.3所
示,常见的位移传感器如图7.4所示。利用传感器对该方向上的连续采集数据,
根据转动频率绘制以角变化量为自变量的位移-角度曲线,加上基圆,按照旋转
角度展开程一个圆图像。单向测量法,只适用于具有敏感方向的主轴转精度的测
量。