主轴加工工艺
电机主轴加工工艺
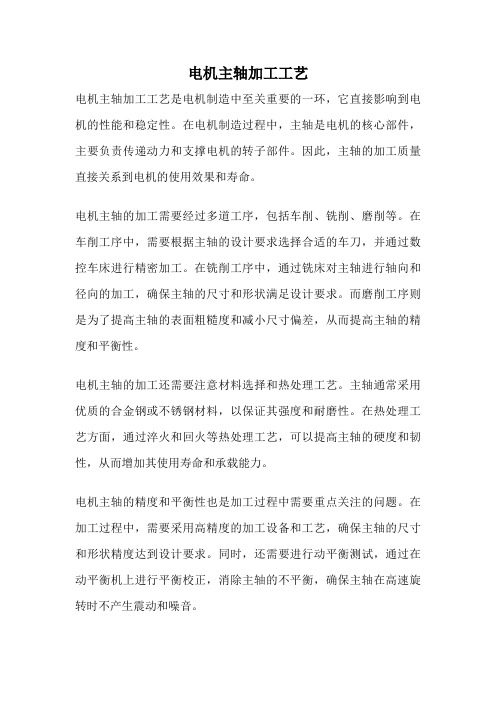
电机主轴加工工艺电机主轴加工工艺是电机制造中至关重要的一环,它直接影响到电机的性能和稳定性。
在电机制造过程中,主轴是电机的核心部件,主要负责传递动力和支撑电机的转子部件。
因此,主轴的加工质量直接关系到电机的使用效果和寿命。
电机主轴的加工需要经过多道工序,包括车削、铣削、磨削等。
在车削工序中,需要根据主轴的设计要求选择合适的车刀,并通过数控车床进行精密加工。
在铣削工序中,通过铣床对主轴进行轴向和径向的加工,确保主轴的尺寸和形状满足设计要求。
而磨削工序则是为了提高主轴的表面粗糙度和减小尺寸偏差,从而提高主轴的精度和平衡性。
电机主轴的加工还需要注意材料选择和热处理工艺。
主轴通常采用优质的合金钢或不锈钢材料,以保证其强度和耐磨性。
在热处理工艺方面,通过淬火和回火等热处理工艺,可以提高主轴的硬度和韧性,从而增加其使用寿命和承载能力。
电机主轴的精度和平衡性也是加工过程中需要重点关注的问题。
在加工过程中,需要采用高精度的加工设备和工艺,确保主轴的尺寸和形状精度达到设计要求。
同时,还需要进行动平衡测试,通过在动平衡机上进行平衡校正,消除主轴的不平衡,确保主轴在高速旋转时不产生震动和噪音。
电机主轴加工工艺还需要注重质量控制和检测。
在加工过程中,需要严格执行工艺流程和操作规程,确保每道工序的质量和精度。
同时,还需要进行尺寸检测、表面质量检查和功能测试,确保主轴的质量达到标准要求。
电机主轴加工工艺是电机制造中的关键环节,它直接影响到电机的性能和稳定性。
通过合理的工艺流程和严格的质量控制,可以确保电机主轴具有优良的加工质量和稳定性,从而提高电机的使用效果和寿命。
在未来的电机制造中,我们需要不断优化主轴加工工艺,推动电机制造技术的进步和发展。
车床主轴的加工工艺
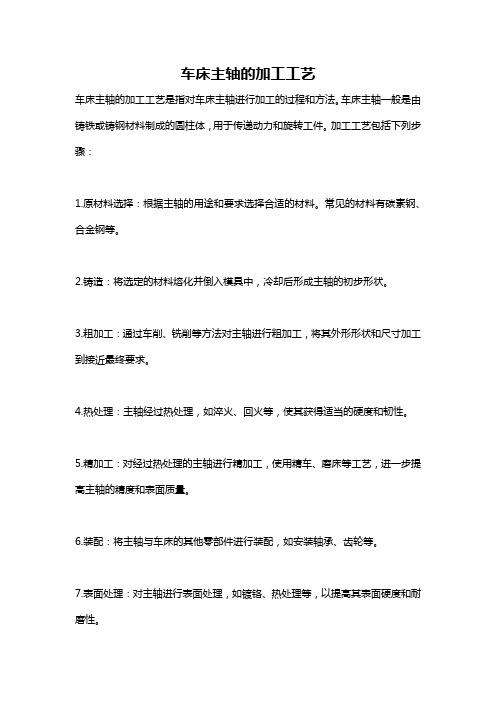
车床主轴的加工工艺
车床主轴的加工工艺是指对车床主轴进行加工的过程和方法。
车床主轴一般是由铸铁或铸钢材料制成的圆柱体,用于传递动力和旋转工件。
加工工艺包括下列步骤:
1.原材料选择:根据主轴的用途和要求选择合适的材料。
常见的材料有碳素钢、合金钢等。
2.铸造:将选定的材料熔化并倒入模具中,冷却后形成主轴的初步形状。
3.粗加工:通过车削、铣削等方法对主轴进行粗加工,将其外形形状和尺寸加工到接近最终要求。
4.热处理:主轴经过热处理,如淬火、回火等,使其获得适当的硬度和韧性。
5.精加工:对经过热处理的主轴进行精加工,使用精车、磨床等工艺,进一步提高主轴的精度和表面质量。
6.装配:将主轴与车床的其他零部件进行装配,如安装轴承、齿轮等。
7.表面处理:对主轴进行表面处理,如镀铬、热处理等,以提高其表面硬度和耐磨性。
8.检测:对加工完成的主轴进行检测,包括尺寸、形状、硬度等的检测,确保其达到设计要求。
以上是车床主轴加工的一般工艺流程,具体的加工工艺还会根据不同的要求和设计进行调整和改进。
ca6140型卧式车床主轴的加工工艺过程

车床主轴零件的加工工艺过程〔一〕CA6140型卧式车床主轴的加工主运动为回转运动的各种金属切削机床的主轴,是轴类零件中最有代表性的零件。
主轴上通常有内、外圆柱面和圆锥面,以及螺纹、键槽、花键、横向孔、沟槽、凸缘等不同形式的几何外表。
主轴的精度要求高,加工难度大,假设对主轴加工中一些重要问题〔如基准的选择、工艺道路的拟定等〕能做出正确的分析和解决,那么其他轴类零件的加工就能迎刃而解。
以CA6140型卧式车床主轴为例,分析轴类零件的加工。
如下列图为CA6140车床主轴简图,其材料为45钢。
图 CA6140型卧式车床主轴简图1.主轴的功用及技术要求分析〔1〕支承轴颈主轴的两支承轴颈A,B与相对应的内孔配合,是主轴组件的装配基准,其制造精度将直接影响到主轴组件的旋转精度。
当支承轴颈不同轴时,主轴产生径向圆跳动,影响以后车床使用时工件的加工质量,因此,对支承轴颈提出了很高要求。
尺寸精度按IT5级制造,两支承轴颈的圆度公差0.005㎜,径向圆跳动公差0.005㎜,外表粗糙度Ra值为0.4µm。
〔2〕装夹外表主轴前端锥孔是用于安装顶尖或心轴的莫氏锥孔,其中心线必须与支承轴颈中心线严格同轴,否那么会使工作件产生圆度、同轴度误差,主轴锥孔锥面的接触率要大于75%;锥孔对支撑轴颈A,B的圆跳动允差:近轴端为0.005㎜,距轴端300㎜处为0.01㎜,外表粗糙度Ra值为0.4µm。
主轴前端短圆锥面是安装卡盘的定心外表。
为了保证卡盘的定心精度,短圆锥面必须与支承轴颈同轴,端面必须与主轴回转中心垂直。
短圆锥面对支撑轴颈A,B圆跳动允差为0.008㎜,外表粗糙度Ra值为0.8µm。
〔3〕螺纹外表主轴的螺纹外表用于锁紧螺母的配合。
当螺纹外表中心线与支承轴颈中心线歪斜时,会引起主轴组件上锁紧螺母的端面跳动,导致滚动轴承内圈中心线倾斜,引起主轴径向跳动,因此,加工主轴上的螺纹外表时,必须控制其中心线与支承轴颈中心线的同轴度。
C6150车床主轴箱箱体加工工艺及工装夹具设计

C6150车床主轴箱箱体加工工艺及工装夹具设计1.C6150车床主轴箱箱体加工工艺主轴箱箱体一般由铸铁材料制成,其加工工艺主要包括以下几个步骤:(1)铸造准备:对铸铁材料进行熔炼、净化和浇铸前的处理,确保铸件质量。
(2)铸件浇铸:将熔化的铸铁材料倒入模具中,使其冷却、凝固成型。
(3)铸件脱模:待铸件冷却后,从模具中取出,进行清理和修整。
(4)精密加工:对铸件进行加工,包括切割、铣削、钻孔等工序,以使得箱体尺寸和形状精确到达要求。
(5)表面处理:对箱体表面进行打磨、抛光,以提高外观质量。
(6)检测和装配:对加工好的主轴箱箱体进行检测,确保质量达到要求,然后进行组装。
在主轴箱箱体的加工过程中,合理设计工装夹具可以提高加工效率和加工质量,减少劳动强度。
(1)定位夹具设计:主要用于确定箱体的位置和角度,以保证加工精度。
定位夹具可以根据箱体形状和尺寸设计,一般采用刚性夹具,如V型块。
(2)夹紧夹具设计:用于夹紧箱体,以防止其在加工过程中发生松动或位移。
夹紧夹具可以采用螺栓和垫圈进行固定,或者采用气动或液压夹紧装置。
(3)切削夹具设计:用于加工箱体的切削过程,包括刀具和刀架的选择和安装。
切削夹具要根据加工要求和箱体材料的切削特性来设计,以保证加工质量和效率。
(4)保护夹具设计:用于保护箱体的外表面和内孔。
保护夹具可以采用橡胶垫和保护套等材料进行设计,以确保箱体不被切削工具碰伤。
(5)检测夹具设计:用于检测箱体的尺寸和形状,以确保其符合加工要求。
检测夹具可以采用测量工具和传感器等设备进行设计,以确保检测的准确性和可靠性。
总之,C6150车床主轴箱箱体加工工艺和工装夹具设计是车床加工中的重要环节,可以通过合理的工艺和夹具设计来提高加工效率和加工质量。
C6150铣床主轴箱箱体加工工艺及工装夹具设计
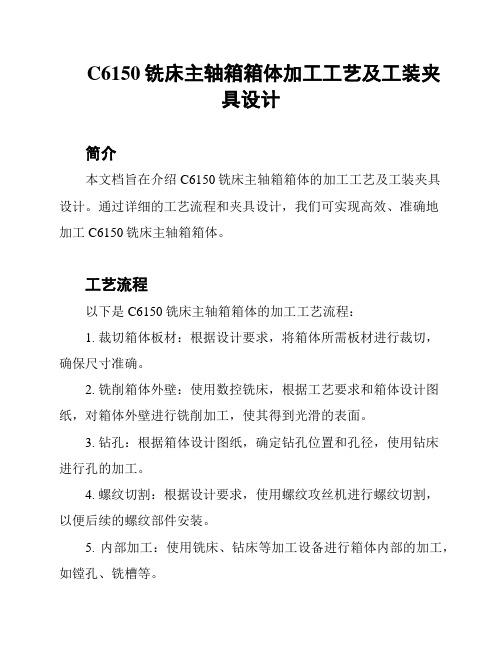
C6150铣床主轴箱箱体加工工艺及工装夹具设计简介本文档旨在介绍C6150铣床主轴箱箱体的加工工艺及工装夹具设计。
通过详细的工艺流程和夹具设计,我们可实现高效、准确地加工C6150铣床主轴箱箱体。
工艺流程以下是C6150铣床主轴箱箱体的加工工艺流程:1. 裁切箱体板材:根据设计要求,将箱体所需板材进行裁切,确保尺寸准确。
2. 铣削箱体外壁:使用数控铣床,根据工艺要求和箱体设计图纸,对箱体外壁进行铣削加工,使其得到光滑的表面。
3. 钻孔:根据箱体设计图纸,确定钻孔位置和孔径,使用钻床进行孔的加工。
4. 螺纹切割:根据设计要求,使用螺纹攻丝机进行螺纹切割,以便后续的螺纹部件安装。
5. 内部加工:使用铣床、钻床等加工设备进行箱体内部的加工,如镗孔、铣槽等。
6. 表面处理:对箱体外表面进行喷漆、砂光等表面处理,提高外观质量和耐腐蚀性能。
7. 总装:将各个部件进行组装,确保箱体完整并达到设计要求。
8. 检验:对加工完成的箱体进行检验,确保尺寸、外观等符合要求。
工装夹具设计为了确保加工过程的稳定性和准确性,需要设计适用的工装夹具。
以下是针对C6150铣床主轴箱箱体加工的工装夹具设计要点:1. 定位夹具:设计合适的定位夹具,确保箱体定位准确且稳定。
2. 固定夹具:设计合适的固定夹具,保持箱体在加工过程中的稳定性,防止移位或震动。
3. 安全夹具:考虑工人安全,设计适用的安全夹具,确保操作过程中人员不受伤。
4. 加工导向夹具:设计适用的加工导向夹具,可以确保箱体在加工过程中的位置准确,避免误差。
以上是C6150铣床主轴箱箱体加工工艺及工装夹具设计的简要介绍。
通过遵循这些工艺流程和合理设计工装夹具,我们能够高效、准确地加工C6150铣床主轴箱箱体。
CA6140车床主轴加工工艺

车床主轴加工工艺1.CA6140车床主轴技术要求及功用图1 CA6140车床的主轴简图图1为CA6140车床主轴零件简图。
由零件简图可知,该主轴呈阶梯状,其上有安装支承轴承、传动件的圆柱、圆锥面,安装滑动齿轮的花键,安装卡盘及顶尖的内外圆锥面,联接紧固螺母的螺旋面,通过棒料的深孔等。
下面分别介绍主轴各主要部分的作用及技术要求:⑴支承轴颈主轴二个支承轴颈A、B圆度公差为0.005mm,径向跳动公差为0.005mm;而支承轴颈1∶12锥面的接触率≥70%;表面粗糙度Ra为0.4mm;支承轴颈尺寸精度为IT5。
因为主轴支承轴颈是用来安装支承轴承,是主轴部件的装配基准面,所以它的制造精度直接影响到主轴部件的回转精度。
For personal use only in study and research; not for commercial use⑵端部锥孔主轴端部内锥孔(莫氏6号)对支承轴颈A、B的跳动在轴端面处公差为0.005mm,离轴端面300mm处公差为0.01 mm;锥面接触率≥70%;表面粗糙度Ra为0.4mm;硬度要求45~50HRC。
该锥孔是用来安装顶尖或工具锥柄的,其轴心线必须与两个支承轴颈的轴心线严格同轴,否则会使工件(或工具)产生同轴度误差。
⑶端部短锥和端面头部短锥C和端面D对主轴二个支承轴颈A、B的径向圆跳动公差为0.008mm;表面粗糙度Ra为0.8mm。
它是安装卡盘的定位面。
为保证卡盘的定心精度,该圆锥面必须与支承轴颈同轴,而端面必须与主轴的回转中心垂直。
⑷空套齿轮轴颈空套齿轮轴颈对支承轴颈A、B的径向圆跳动公差为0.015 mm。
由于该轴颈是与齿轮孔相配合的表面,对支承轴颈应有一定的同轴度要求,否则引起主轴传动啮合不良,当主轴转速很高时,还会影响齿轮传动平稳性并产生噪声。
For personal use only in study and research; not for commercial use⑸螺纹主轴上螺旋面的误差是造成压紧螺母端面跳动的原因之一,所以应控制螺纹的加工精度。
主轴的机械加工工艺

主轴的机械加工工艺嘿,朋友们!今天咱来聊聊主轴的机械加工工艺,这可真是个有趣又重要的事儿啊!你想想看,那主轴就好比是机器的心脏,它得足够强壮、精准,才能让整个机器顺畅地运转起来呀!那怎么才能把主轴加工得完美呢?首先得选好材料,这就跟盖房子打地基一样重要。
要是材料不行,后面再怎么努力也是白搭呀!得找那种结实耐用、性能优良的材料,这样加工出来的主轴才可靠。
然后就是各种加工手段啦!车削、铣削、磨削等等,就像是给主轴做造型的魔法。
车削能让它初步成型,铣削能给它加上各种精细的特征,磨削呢,则让它变得光滑无比,就像打磨一块美玉一样。
在加工的过程中,可得注意精度啊!这可不是闹着玩的,差之毫厘谬以千里呀!就好像你走路,稍微偏一点可能就走到沟里去啦!加工主轴也是一样,尺寸、形状都得把握得死死的,不能有一点马虎。
还有啊,刀具的选择也很关键呢!不同的刀具就像是不同的画笔,能画出不同的效果。
选对了刀具,加工起来那叫一个事半功倍。
你说,要是主轴加工不好,那机器还能好好工作吗?就好比一个人心脏有毛病,那还能活蹦乱跳吗?肯定不行呀!所以说,这主轴的机械加工工艺可真是太重要啦!在实际操作中,师傅们得像对待宝贝一样对待主轴,每一个步骤都要小心翼翼。
这可不是随随便便就能搞定的事情,需要经验、技术,还需要那份认真负责的态度。
你看那些厉害的机器,不都是因为有了完美的主轴才能发挥出强大的威力吗?就像一辆跑车,要是发动机不行,再好看又有啥用呢?总之呢,主轴的机械加工工艺是一门大学问,需要我们不断地去学习、去探索。
只有这样,我们才能制造出更好、更强的机器,为我们的生活和工作带来更多的便利和进步。
这可不是我在吹牛哦,这是实实在在的道理呀!大家可得重视起来呀!。
主轴的加工工艺路线
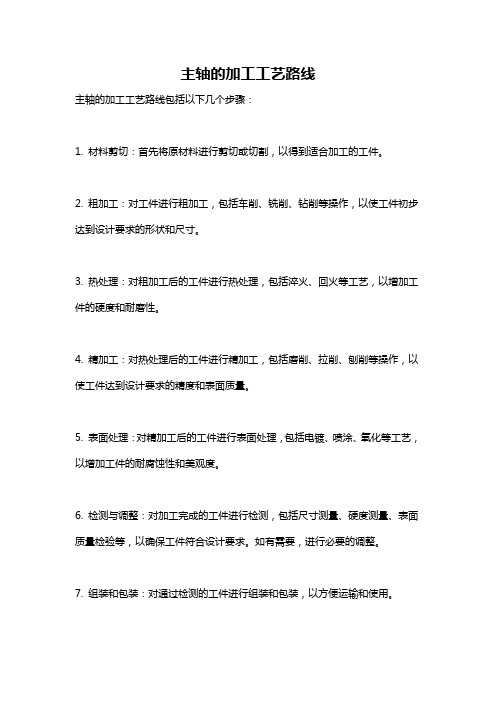
主轴的加工工艺路线
主轴的加工工艺路线包括以下几个步骤:
1. 材料剪切:首先将原材料进行剪切或切割,以得到适合加工的工件。
2. 粗加工:对工件进行粗加工,包括车削、铣削、钻削等操作,以使工件初步达到设计要求的形状和尺寸。
3. 热处理:对粗加工后的工件进行热处理,包括淬火、回火等工艺,以增加工件的硬度和耐磨性。
4. 精加工:对热处理后的工件进行精加工,包括磨削、拉削、刨削等操作,以使工件达到设计要求的精度和表面质量。
5. 表面处理:对精加工后的工件进行表面处理,包括电镀、喷涂、氧化等工艺,以增加工件的耐腐蚀性和美观度。
6. 检测与调整:对加工完成的工件进行检测,包括尺寸测量、硬度测量、表面质量检验等,以确保工件符合设计要求。
如有需要,进行必要的调整。
7. 组装和包装:对通过检测的工件进行组装和包装,以方便运输和使用。
8. 质量控制:对整个加工过程进行质量控制,包括使用符合要求的设备和工具、制定合理的工艺流程、操作规范等,以确保加工出的主轴达到设计和客户要求的质量标准。
- 1、下载文档前请自行甄别文档内容的完整性,平台不提供额外的编辑、内容补充、找答案等附加服务。
- 2、"仅部分预览"的文档,不可在线预览部分如存在完整性等问题,可反馈申请退款(可完整预览的文档不适用该条件!)。
- 3、如文档侵犯您的权益,请联系客服反馈,我们会尽快为您处理(人工客服工作时间:9:00-18:30)。
主轴加工工艺的研究与探讨
主轴的功用、精度:
1.功用:
在一般的金属切削机床中,主轴把旋转运动及扭矩通过主轴端部的夹具或刀具。
在工作中,主轴不但承受扭转力矩,而且承弯曲力矩。
所以要求机床主轴的扭转刚度和弯曲刚度都很高。
2.机床主轴精度:(机床精度的重要组成部分)
即输出旋转精度,也为主轴的工作表面精度。
下面仅真对主轴自身的关键精度而言:
1)主轴支承轴径、轴肩端面的精度:
●主轴支承轴径的制造精度(椭圆度、锥度、不同轴度、
不垂直度等)
●主轴轴肩端面对主轴回转轴心线的不垂直度
2)主轴工作表面的精度:
●内外锥面的尺寸精度、几何形状精度、光洁度和接触
精度;
●定心表面相对与支承轴径表面的同轴度;
●定位端面相对与支承轴径轴心线的垂直度。
注:机床主轴的工作表面指主轴的莫氏锥孔、轴端外锥或法蓝外圆等。
3.主轴材料、热处理及作用
材料:45#,65Mn,40Cr,38CrMoAl(氮化钢),20Cr或20Cr MnTi(渗碳钢)等
热处理:退火,正火,调质,高频淬火,渗碳,氮化,
热处理作用:提高主轴强度,刚性,表面硬度,及耐疲劳强度、尺寸稳定性等综合机械性能。
退火及正火:降低材料硬度,改善切削加工性能,消除锻造内
应力,细化晶粒,并使金属组织均匀。