活性染料低温皂洗工艺
活性染料固色步骤工艺流程

活性染料固色步骤工艺流程下载温馨提示:该文档是我店铺精心编制而成,希望大家下载以后,能够帮助大家解决实际的问题。
文档下载后可定制随意修改,请根据实际需要进行相应的调整和使用,谢谢!Download tips: This document is carefully compiled by theeditor. l hope that after you downloadthem,they can help yousolve practical problems. The document can be customized andmodified afterdownloading,please adjust and use it according toactual needs, thank you!活性染料固色步骤工艺流程:① 染料吸附:织物预处理后,在一定温度、pH值及电解质存在下,使活性染料分子吸附到纤维(如棉、麻、羊毛等)表面。
② 水洗:初步去除未吸附的浮色,减少后续固色过程中的杂质干扰。
③ 固色处理:加入碱剂(如碳酸钠)和催化剂(如尿素),提升体系pH值,促进染料与纤维发生化学反应,形成共价键结合。
此过程常伴随温度控制,以加速反应速率。
④ 保温反应:在适宜温度下(一般60℃至90℃),保持一段时间,确保染料与纤维充分反应,达到最大固色效果。
⑤ 后水洗:彻底清洗织物,除去未反应的染料、碱剂及其它水溶性杂质,防止后续使用中继续褪色。
⑥ 皂洗:使用洗涤剂进行深度清洁,进一步提高染色牢度,确保色彩鲜艳度和耐洗性。
⑦ 干燥定型:将清洗后的织物干燥并进行热定型处理,固定织物形态,同时完成染料与纤维的最终结合。
⑧ 检验包装:对成品进行质量检验,包括色牢度、颜色一致性等,合格后进行包装入库。
此流程确保了活性染料染色的稳定性和持久性,是纺织行业中广泛应用的染色技术之一。
活性染料皂洗粉DN165的应用
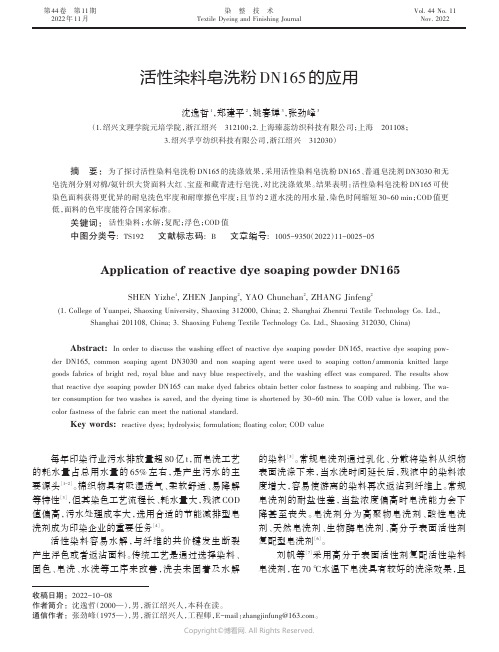
每年印染行业污水排放量超80亿t ,而皂洗工艺的耗水量占总用水量的65%左右,是产生污水的主要源头[1-2]。
棉织物具有吸湿透气、柔软舒适、易降解等特性[3],但其染色工艺流程长、耗水量大,残液COD 值偏高,污水处理成本大,选用合适的节能减排型皂洗剂成为印染企业的重要任务[4]。
活性染料容易水解,与纤维的共价键发生断裂产生浮色或者返沾面料。
传统工艺是通过选择染料、固色、皂洗、水洗等工序来改善,洗去未固着及水解的染料[5]。
常规皂洗剂通过乳化、分散将染料从织物表面洗涤下来,当水洗时间延长后,残液中的染料浓度增大,容易使游离的染料再次返沾到纤维上。
常规皂洗剂的耐盐性差,当盐浓度偏高时皂洗能力会下降甚至丧失。
皂洗剂分为高聚物皂洗剂、酸性皂洗剂、天然皂洗剂、生物酶皂洗剂、高分子表面活性剂复配型皂洗剂[6]。
刘帆等[7]采用高分子表面活性剂复配活性染料皂洗剂,在70℃水温下皂洗具有较好的洗涤效果,且活性染料皂洗粉DN165的应用摘要:为了探讨活性染料皂洗粉DN165的洗涤效果,采用活性染料皂洗粉DN165、普通皂洗剂DN3030和无皂洗剂分别对棉/氨针织大货面料大红、宝蓝和藏青进行皂洗,对比洗涤效果。
结果表明:活性染料皂洗粉DN165可使染色面料获得更优异的耐皂洗色牢度和耐摩擦色牢度;且节约2道水洗的用水量,染色时间缩短30~60min ;COD 值更低,面料的色牢度能符合国家标准。
关键词:活性染料;水解;复配;浮色;COD 值中图分类号:TS192文献标志码:B 文章编号:1005-9350(2022)11-0025-05Abstract:In order to discuss the washing effect of reactive dye soaping powder DN165,reactive dye soaping pow⁃der DN165,common soaping agent DN3030and non soaping agent were used to soaping cotton /ammonia knitted largegoods fabrics of bright red,royal blue and navy blue respectively,and the washing effect was compared.The results showthat reactive dye soaping powder DN165can make dyed fabrics obtain better color fastness to soaping and rubbing.The wa⁃ter consumption for two washes is saved,and the dyeing time is shortened by 30~60min.The COD value is lower,and the color fastness of the fabric can meet the national standard.Key words:reactive dyes;hydrolysis;formulation;floating color;COD valueApplication of reactive dye soaping powder DN165收稿日期:2022-10-08作者简介:沈逸哲(2000—),男,浙江绍兴人,本科在读。
活性染料的染后洗涤和固色处理_二_
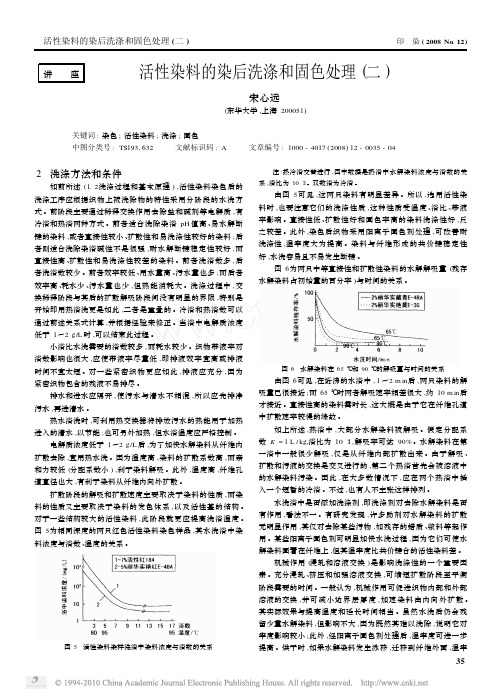
对于中深色品种 ,大多数厂家在皂洗前先经过三次排 /进液 洗涤 ,有的还需经过二次排 /进液皂洗 ,然后热水洗 ,再冷水洗 。
皂洗时 ,为防止水解染料再吸附纤维 ,或与硬水中的金属离 子形成沉淀而沉积在纤维表面 ,通常要加分散剂 、螯合剂 ,或表面 活性剂作洗涤剂 。过去 ,应用较多的是磷酸盐或多磷酸盐 。近年 来 ,为了减少磷污染 ,有用低黏度的聚丙烯酸盐作分散螯合剂 ,它 们可以减弱硬水的影响 ,不会形成大量泡沫 。但是 ,随着活性染 料的应用浓度愈来愈高 ,水解染料对纤维的直接性愈来愈大 ,这 些助剂的效果已无法满足要求 。为此 ,一些公司开发了不少效能 更好的助剂 。例如 , BASF公司的 Cyclanon XC2W ,还有其它类似 产品如 Dekol SN[3 ]和 Sandopur RSKI等专用洗涤剂 。
2 洗涤方法和条件
如前所述 (1. 2洗涤过程和基本原理 ) ,活性染料染色后的 洗涤工序应根据织物上被洗除物的特性采用分阶段的水洗方 式 。前阶段主要通过稀释交换作用去除盐和碱剂等电解质 ,有 冷浴和热浴两种方式 。前者适合洗除染浴 pH 值高 、易水解断 键的染料 ,或者直接性较小 、扩散性和易洗涤性较好的染料 ;后 者则适合洗除染浴碱性不是很强 ,耐水解断键稳定性较好 ,而 直接性高 、扩散性和易洗涤性较差的染料 。前者洗浴数多 ,后 者洗浴数较少 。前者效率较低 、用水量高 、污水量也多 ;而后者 效率高 、耗水少 、污水量也少 ,但热能消耗大 。洗涤过程中 ,交 换稀释阶段与其后的扩散解吸阶段间没有明显的界限 ,特别是 开始即用热浴洗更是如此 ,二者是重叠的 。冷浴和热浴数可以 通过前述关系式计算 ,并根据经验来修正 。当浴中电解质浓度 低于 1~2 g/L 时 ,可以结束此过程 。
皂洗的目的与原理
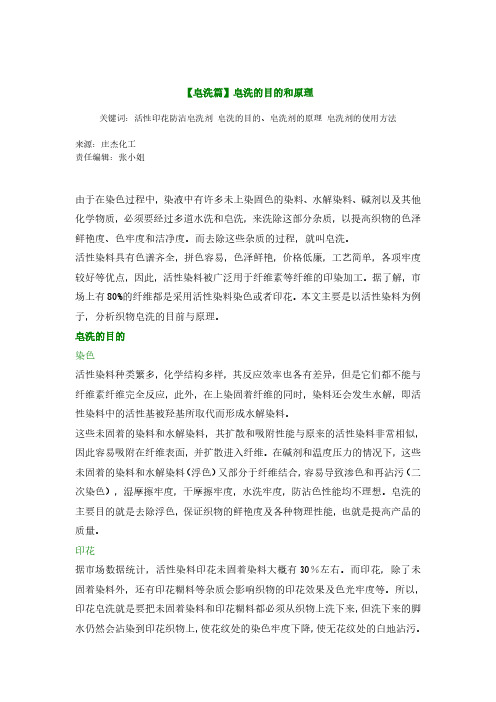
【皂洗篇】皂洗的目的和原理关键词:活性印花防沾皂洗剂皂洗的目的、皂洗剂的原理皂洗剂的使用方法来源:庄杰化工责任编辑:张小姐由于在染色过程中,染液中有许多未上染固色的染料、水解染料、碱剂以及其他化学物质,必须要经过多道水洗和皂洗,来洗除这部分杂质,以提高织物的色泽鲜艳度、色牢度和洁净度。
而去除这些杂质的过程,就叫皂洗。
活性染料具有色谱齐全,拼色容易,色泽鲜艳,价格低廉,工艺简单,各项牢度较好等优点,因此,活性染料被广泛用于纤维素等纤维的印染加工。
据了解,市场上有80%的纤维都是采用活性染料染色或者印花。
本文主要是以活性染料为例子,分析织物皂洗的目前与原理。
皂洗的目的染色活性染料种类繁多,化学结构多样,其反应效率也各有差异,但是它们都不能与纤维素纤维完全反应,此外,在上染固着纤维的同时,染料还会发生水解,即活性染料中的活性基被羟基所取代而形成水解染料。
这些未固着的染料和水解染料,其扩散和吸附性能与原来的活性染料非常相似,因此容易吸附在纤维表面,并扩散进入纤维。
在碱剂和温度压力的情况下,这些未固着的染料和水解染料(浮色)又部分于纤维结合,容易导致渗色和再沾污(二次染色),湿摩擦牢度,干摩擦牢度,水洗牢度,防沾色性能均不理想。
皂洗的主要目的就是去除浮色,保证织物的鲜艳度及各种物理性能,也就是提高产品的质量。
印花据市场数据统计,活性染料印花未固着染料大概有30%左右。
而印花,除了未固着染料外,还有印花糊料等杂质会影响织物的印花效果及色光牢度等。
所以,印花皂洗就是要把未固着染料和印花糊料都必须从织物上洗下来,但洗下来的脚水仍然会沾染到印花织物上,使花纹处的染色牢度下降,使无花纹处的白地沾污。
因此印花皂洗一般都采取防沾色皂洗,以保证能将脏物彻底洗下来,并使洗下来的所有脏物都不再沾染到织物上去。
所以,印花皂洗比染色皂洗要求更高,也可以换句话来说,印花能用的皂洗剂,对应织物的染色都是可以用的。
皂洗的工艺原理目前市场上的皂洗剂主要是表面活性剂型、化学型及聚合物型,但随着科技的发展,很多皂洗剂的具体类型都是融合性的。
活性染料的水洗后处理

活性染料的水洗后处理
目的是去除未固着的染料、盐及碱,使染色织物的pH接近中性,是整个染色工艺过程的重
要环节
所有活性染料都存在着固着不充分、在纤维上留下大量水解染料的缺点
活性染料的亲和性影响了其易洗涤性,低亲和性可用冷水去除,而高亲和性的染料需要高温洗涤
水洗处理时间一般是染料的上染及固着过程的二倍多,大量的水和热用于水洗后处理
水洗过程:冷水洗、热水洗、皂洗、热水洗、冷水洗等
冷水洗、热水洗(40~50℃),稀释阶段,尽可能去除盐、碱及未固着的染料,提高皂洗效
率
皂洗前最好在醋酸浴中进行中和,防止染料在皂洗过程中水解,避免碱剂去除不干净
残留的电解质影响织物耐洗牢度,残碱影响色光
皂洗过程促使纤维内部未固着的水解染料扩散到纤维表面,同时解吸到洗涤液中
提高温度——提高水解染料扩散速率,降低水解染料的亲和性,提高染料的解吸效率
常规使用的皂类洗涤剂及非离子表面活性剂并不能加速水解染料的扩散
皂洗后热水洗(70℃,<10min),进一步去除粘附在纤维上的染料溶液
水洗后处理的染色物耐水色牢度(水渍牢度)良好,耐洗色牢度较差——检查电解质、金属离子、皂洗温度,可进行二次皂洗
耐洗色牢度好、水渍牢度差——提高净洗效果。
消色皂洗剂之应用探讨
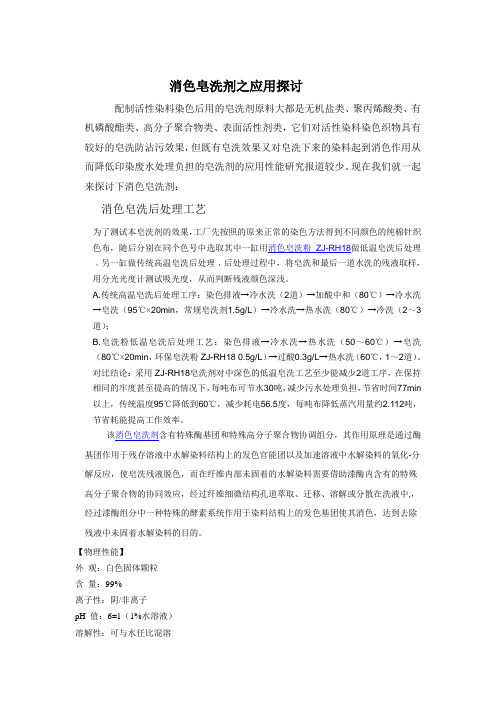
消色皂洗剂之应用探讨配制活性染料染色后用的皂洗剂原料大都是无机盐类、聚丙烯酸类、有机磷酸酯类、高分子聚合物类、表面活性剂类,它们对活性染料染色织物具有较好的皂洗防沾污效果,但既有皂洗效果又对皂洗下来的染料起到消色作用从而降低印染废水处理负担的皂洗剂的应用性能研究报道较少。
现在我们就一起来探讨下消色皂洗剂:消色皂洗后处理工艺为了测试本皂洗剂的效果,工厂先按照的原来正常的染色方法得到不同颜色的纯棉针织色布,随后分别在同个色号中选取其中一缸用消色皂洗粉ZJ-RH18做低温皂洗后处理﹐另一缸做传统高温皂洗后处理﹐后处理过程中,将皂洗和最后一道水洗的残液取样,用分光光度计测试吸光度,从而判断残液颜色深浅。
A.传统高温皂洗后处理工序:染色排液→冷水洗(2道)→加酸中和(80℃)→冷水洗→皂洗(95℃×20min,常规皂洗剂1.5g/L)→冷水洗→热水洗(80℃)→冷洗(2~3道);B.皂洗粉低温皂洗后处理工艺:染色排液→冷水洗→热水洗(50~60℃)→皂洗(80℃×20min,环保皂洗粉ZJ-RH18 0.5g/L)→过酸0.3g/L→热水洗(60℃,1~2道)。
对比结论:采用ZJ-RH18皂洗剂对中深色的低温皂洗工艺至少能减少2道工序,在保持相同的牢度甚至提高的情况下,每吨布可节水30吨,减少污水处理负担,节省时间77min 以上,传统温度95℃降低到60℃,减少耗电56.5度,每吨布降低蒸汽用量约2.112吨,节省耗能提高工作效率。
该消色皂洗剂含有特殊酶基团和特殊高分子聚合物协调组分,其作用原理是通过酶基团作用于残存溶液中水解染料结构上的发色官能团以及加速溶液中水解染料的氧化-分解反应,使皂洗残液脱色,而在纤维内部未固着的水解染料需要借助漆酶内含有的特殊高分子聚合物的协同效应,经过纤维细微结构孔道萃取、迁移、溶解或分散在洗液中,,经过漆酶组分中一种特殊的酵素系统作用于染料结构上的发色基团使其消色,达到去除残液中未固着水解染料的目的。
解决印花沾色问题的新型活性皂洗剂

材料与设备解决印花沾色问题的新型活性皂洗剂□顺德;金亿纺织科技有限公司洗剂是印染加工中活性印花后处理一^必备助剂之一,目前市场中皂洗剂品种繁多,本文罗列了国内外较为常用的几个品种,通过实验比较及印染企业生产实际反馈意见,对于活性染料皂洗工艺总结以下经验,仅供参考。
—.宅洗工艺26*特点1.皂洗剂的发展何为皂洗剂?即传统纺织品在染色或印花后使用的洗涤剂,最早使用的是肥皂,皂洗也就由此而得名。
因为肥皂不耐硬水,且容易产生沾色问题,所以逐渐被经筛选的洗涤剂或其他的表面活性剂的复配物所取代。
这些由表面活性剂组成的净洗剂,在纺织印染工业中使用,洗涤效果有了比较大的提高,但对防沾污效果仍不够理想,特别在对织物进行皂洗时,易发生白底或浅色部分的沾色问题,影响产品质量,因此也就出现了比较专业的皂洗剂。
这些专用的皂洗剂,--般由对染料亲和力较大的表面活性剂和防再沾污剂、无机盐组戍。
由于聚氧乙烯型非离子表面活性剂对染料的亲和力较大,所以染色时才会有缓染作用,在皂洗剂中的表面活性剂也就应以这类表面活性剂为主体;防再沾污剂大多是高分子纺织助剂,如聚乙烯毗咯酮或聚丙烯酸衍生物等,无机盐,如硅酸盐、磷酸盐则起到增效剂作用。
2.皂洗的特点据市场数据统计,活性染料印花未固着染料大概有30%左右,活性染料印花除了未固着染料外,还有印花糊料等杂质会影响织物的印花效果及色光牢度等,所以,印花皂洗就是要把未固着染料和印花糊料都必须从织物上洗下来。
30丝mOEDSU2019.12材料与设备然而,洗下来的残液仍然会沾染到印花织物上,使花纹处的染色牢度下降,使无花纹处的白地沾污。
因此,印花皀洗一般都采取防沾色皂洗,以保证能将脏物彻底洗下来,并使洗下来的所有脏物都不再沾染到织物上去;所以,印花皂洗比染色皂洗要求更高。
可以换句话来说,印花能用的皂洗剂,对应织物的染色都是可以用的。
3.皂洗的原理目前市场上的皀洗剂主要是表面活性剂型、化学型及聚合物型,随着科技的发展,很多皂洗剂的具体类型都是融合性的。
毛用活性染料羊毛低温染色工艺的研究
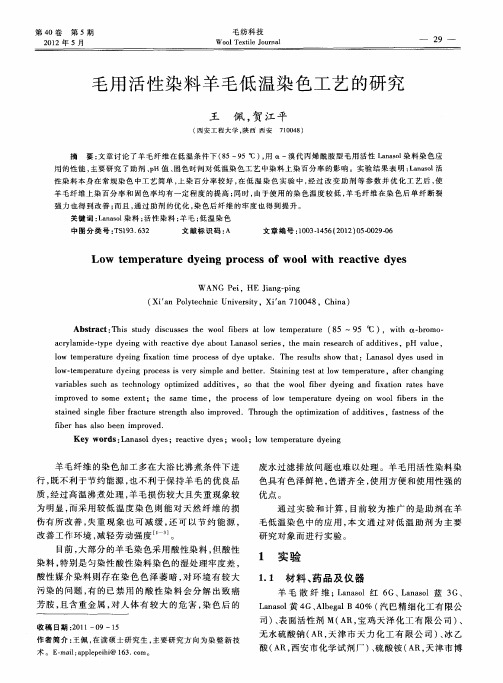
染 色 试 样 进 行 比较 。
入
染
图 1 常 规 染 色 工 艺 曲线
后处 理 工 艺 : 固色 水 洗 ( 碱 质 量 浓 度 2 gL, 纯 / 8 O℃ X 1 n 一 皂 洗 ( 洗 剂 用 量 1 ( w ) 5mi) 皂 % of,
7 5℃ ×1 i)_ 水 洗 (0 o ×1 n 。 0mn + 7 C 0mi)
后 处理 工 艺 : 固色 水 洗 ( 碱 质 量 浓 度 2 g L 纯 / , 8 C×1 i ) 皂 洗 ( 洗 剂 用 量 1 ( w ) Oq 5 mn 一 皂 % of , 7 5℃ ×1 i)_ 水 洗 ( 0℃ ×1 i) 0m n ÷ 7 0mn 。
选 择 L nsl 6 a ao 红 G染 料 得 出优 化 工 艺 的各 参 数用量 , 后推广 至三原 色 , 然 与常规 工艺 染色 后试 样
科伟 永 兴 仪 器 有 限公 司 ) 7 2型 光 栅 分 光 光 度 计 、2
( 海 精 密 科 学 仪 器 制 造 厂 ) S 3 0测 色 配 色 仪 上 、F0
( 维士 电脑 科 技 公 司 ) Y 0 4 思 、 G 0 E型 单 纤 拉伸 断 裂
仪 ( 波纺 织 仪 器 厂 ) Y 7 8型 摩 擦 测试 仪 ( 州 宁 、51 温
配, 作为新 的低 温 染 色 助剂 。将 其 用 于低 温 染 色 试
样, 和常规 染 色 试 样 做 对 比, 出助 剂 最 佳 配 比为 得 4 % A b gl 表 面 活 性 剂 M 为 2 1 用 量 为 1 0 lea B: :, %
羊 毛纤维 的染 色加 工多在 大浴 比沸煮 条件 下进
废 水过 滤排放 问题 也难 以处理 。羊 毛用活 性染 料染
- 1、下载文档前请自行甄别文档内容的完整性,平台不提供额外的编辑、内容补充、找答案等附加服务。
- 2、"仅部分预览"的文档,不可在线预览部分如存在完整性等问题,可反馈申请退款(可完整预览的文档不适用该条件!)。
- 3、如文档侵犯您的权益,请联系客服反馈,我们会尽快为您处理(人工客服工作时间:9:00-18:30)。
助剂 用量等对 皂洗后纱线牢 度性 能及 皂洗残液色度 的影 响, 出了最佳 低温皂洗工艺 : 洗剂 L 3gL 得 皂 S1~ / , 助洗 酶 0 1 0 3g L 8 皂 洗 1 n 。 . ~ . / ,0 5rn i 关键 词 : 染色 ; 活性染料 ; 低温 ; 皂洗 ; 棉纱
活 性染 料 染o 进 14 皂洗 工艺 0 C下 .
行 , 皂煮后 水 洗 次数 多 , 能 耗 水 较 大 , 洗 液 色度 且 耗 皂 高 , 环境 污染严 重 … 。低 温皂 洗 剂 L 对 S主要 组分 为高 分子 表面活 性 剂 , 与 其 它 助 剂 复 配 , 阴/ 离 子混 并 属 非
合 型 , 有泣 湿 、 具 渗透 、 扩散 、 化 、 洗 、 再沉 淀 等优 乳 净 抗 良性 能 , 而且 耐 酸 、 碱 、 耐 耐硬 水 稳 定 性 良好 。它 可 将 皂洗 温度 降 至 7 8 O一 0℃ , 且 还 能 改 善水 质 , 而减 而 从
14 1 皂 洗处方 和 工 艺条 件 . .
0 3 g L。s a i g a 0 o f r1 i . . / o p n t8 c o 5 r n a Ke r s y ig;r a t e d e;lw e p r t r y wo d :d en e ci y v o t m e a u e;s a ig;c to a n o pn o tn y r
c l fs a ig r sdu r s u s d oor o p n e i e we e dic s e .T e o t u p o e s w a b an d:s a ig a e t1~3 g L。wa hn n y o h p i m r c s s o t i e m o pn g n / s i g e z me 0. 1—
温 度/ ℃
时 间/ i a rn 14 2 皂 洗步骤 ..
9 5
1 5
用, 以期提高皂洗效果并降低生产成本。
1 5
1 试 验
1 1 材料 .
染 色后 棉纱按 14 1 皂 洗处 方 和工 艺条 件进 行 .. 节 皂 洗 , 后取 出纱线 , 复 冷水 洗 , 于 热 定形 机 中 以 然 反 再
常规工 艺
低 温工艺
1 ~3 0. 1~0. 2
皂洗 剂/ gL (/ )
助洗 ( / ) gL
浴 比
2— 3
一
1: 0 2
p H值 ( 用烧 碱 调节 ) 6~ 7
1: O 2 8 0
少沾 污现象 。试 验 将 低 温 皂 洗 剂 L S与 生 物 酶 拼 混使
印
染 (0 0N . 8 2 1 o 1 )
活 性 染 料 低 温 皂 洗 工 艺
胡啸 林
( 南通大 学染整技术研 究所 , 苏 南通 2 6 1 ) 江 20 9 摘 要:应用低温皂洗剂 L S与生 物酶拼混 , 对纯棉纱线 活性染 料染 色后进行 低温皂 洗 , 讨论 了温度 、 时间 、
1 C烘干 , 测试 色牢 度 等相关 指 标 。 活性染料染色后 的棉纱( 82t , 1 . x 黑色 和深蓝色 , 10o e 1 5 测 试 . 未皂 洗 , 厂 取样 ) 染 。 () 1 耐摩 擦 色牢 度 1 2 药 品 . 按 G / 90 19 ( B T32 - 9 7 纺织 品 色牢度 试验 耐摩 擦 低温 皂洗 剂 L 助 洗 酶 E 普 通 皂 洗 剂 ( 通 朝 S, N, 南 色牢 度》 G / 5- 20 ( 织 品 色牢 度试验 评定 和 B T2 1 08 纺 日实业 有限公 司 ) 。
中 图 分 类 号 : S9 . 1 T 13 7 文献标识码 : B 文 章 编 号 :10 4 1 (00)8— 0 5—0 0 0— 0 7 2 1 1 0 2 3
Lo t m p r t r o pi g i e c i e dy i w e e a u e s a n n r a tv eng
沾色用灰色样卡》 进行试验和评定 。 () 2 耐皂 洗 色牢度 U I一 0 NC1 0型 紫 外 分 光 光 度 仪 ( 海 尤 尼 柯 仪 器 5 上 按 G / 9 1 2 0 ( B T3 2 - 0 8 纺织 品 色牢 度试验 耐 皂洗 有 限公 司 ) C lr y 10 测 色 配 色 仪 ( rtg c , o lE e30 o— Ge Ma— a 和 B T2 1 0 8 纺 bt 司 ) Y 7 B摩 擦 牢 度 仪 ( 州 第 二 纺 织 机 械 色牢 度》 G / 5- 20 ( 织 品 色 牢度试验 评定 e h公 ,51 常 沾色用灰色样卡》 进行试验和评定。 厂 )热 定形 机 。 , ( ) 液 吸光度 3皂 采用 U I.50型紫 外分 光光 度仪 在染 料最 大 吸 NC 10 收 稿 日期 :0 0—0 21 8—1 0 收波 长 ( ) 0 m 处 测定 皂 洗 后 皂 液 的 吸光 度 , A 6 0n 并 作者简介 : 胡啸林 (9 3一) 男 , 16 , 江苏镇 江人 , 士 , 硕 副教授 , 主要从 事纺
HU a —i Xio ln
( 啦 o y i n ii igTcnl y N  ̄og U i r tI a n 2 0 9 hn ) j fD e gadFn hn ehoo , a n n e i  ̄og2 6 1 。C ia n s g v sy N
Ab t a t omb n d l w— e p r t r o p n g n S w i n yme。s a i g a t rr a t e d eig o o t n y r t lw e - s r c :C ie o t m e a u e s a i g a e tL t e z h o p n fe e c i y n fc to a n a v o tr n p a u e w a a r d o t h n l e c s o e p r t r ert r s c ri u .T e if n e ft m e a u e。t n o a e o d t e n f s n s r p ris a t rs a ig a d e u i me a d d s g fa div s o a t e s p o e t fe o p n n i e