镁及镁合金燃点的测试
Ca和Ce对工业纯镁阻燃性能和表面张力的影响

Ca和Ce对工业纯镁阻燃性能和表面张力的影响秦林;丁俭;方正;赵维民【摘要】镁合金在熔炼过程中容易产生氧化燃烧,因此必须采取有效的措施对其加以保护,合金化是一种理想的阻燃方法.本文研究了添加不同Ce含量对Mg-1.2Ca 镁合金的阻燃性能和熔体表面张力的影响.结果表明:随着Ce的质量分数从0增加到1.5%时,Mg-1.2Ca合金的燃点大幅度提高,表面张力不断下降.当Ce含量提高到1.2%时,镁合金的燃点达到780℃.随着Ce元素的添加,由MgO,CaO和Ce2O3组成的复合氧化膜非常致密,从而可以很好的阻止Mg-1.2Ca镁合金的氧化燃烧.对Mg-1.2 Ca-1.2Ce镁合金氧化膜的SEM和EDS进行了综合分析,结果表明氧化膜最外层主要是MgO,中间层主要是CaO,而Ce2O3主要集中在氧化膜和基体的交界处.【期刊名称】《河北工业大学学报》【年(卷),期】2013(042)005【总页数】6页(P40-44,98)【关键词】镁合金;钙;铈;阻燃;表面张力;氧化膜【作者】秦林;丁俭;方正;赵维民【作者单位】河北工业大学材料科学与工程学院,天津300130;河北工业大学材料科学与工程学院,天津300130;河北工业大学材料科学与工程学院,天津300130;河北工业大学材料科学与工程学院,天津300130【正文语种】中文【中图分类】TG146.220 前言镁合金具有密度小、比强度和比刚度高、良好减震性和消磁性,并且易于切削、成型,因此在航空航天、汽车工业、电子科技等领域得到广泛的应用.但是镁合金在熔炼、浇注过程容易氧化和燃烧,因此必须采取一定的保护措施.现在最常用的阻燃方法是熔剂覆盖法和气体保护法,但这两种阻燃方法都不可免的存在熔剂夹杂、环境污染、设备和工艺复杂等缺点.20世纪50年代,国内外提出阻燃镁合金的研究开发,其主要原理在于向镁合金中添加适量的低氧位合金元素(即其与氧的亲和力大于镁与氧的亲和力),使镁合金在熔炼、浇注过程中自动生成一层致密的复合氧化膜,从而阻止镁合金的进一步的氧化燃烧.日本九州国家工业研究所的Sakamoto和九州大学的Fukuoka等人[1]较早研究了Ca对于合金阻镁燃性能的影响.在镁合金中单独加入Ca元素后,其总体趋势是含Ca量越高其阻燃性越好,但大量实验证明Ca含量的增加,晶界上会出现富Ca的金属间化合物,使合金的力学性能降低,从而阻碍了含Ca阻燃镁合金的进一步推广应用.黄晓锋等[2-3]的研究发现,Ce元素的加入对提高AZ91D 合金在固态下的起燃温度有着重要的作用,随着合金中Ce的加入量的提高,镁合金的起燃温度逐渐升高.Ce元素为表面活性元素,Ce元素的添加对镁合金的阻燃性能和氧化膜结构产生很大的影响,而合金表面氧化膜结构的改变必然同时改变熔体表面张力的大小.表面张力作为高温熔体重要的物理性质之一,是冶金和材料科学与工程中的重要物理参数.它对材料在铸造、焊接等加工过程中表面热力学行为起着十分重要的作用.研究Ce元素对镁合金表面张力的影响对于揭示其阻燃机理具有重要意义.本论文通过添加Ca、Ce到工业纯镁中,探讨其对工业纯镁阻燃性能与熔体表面张力的影响,为新型阻燃镁合金材料的研发提供依据.1 试样的制备及检测方法1.1 试样的制备本实验以工业纯Mg、Mg-30%Ca中间合金、Mg-30%Ce中间合金为原材料,利用坩埚式节能电阻炉进行熔炼,并通入体积百分比为99.5%CO2+0.5%SF6的混合气体作为保护气体.原材料化学成分如表1所示.表1 原材料化学成分(质量百分数) %Tab.1 Main compositionsof experimentalalloys序号 1 2 3 4 5 6成分 Mg-1.2Ca Mg-1.2Ca-0.2Ce Mg-1.2Ca-0.5Ce Mg-1.2Ca-0.8Ce Mg-1.2Ca-1.2Ce Mg-1.2Ca-1.5Ce1.2 燃点检测方法燃点测试设备采用型号为SG2-1.5-12型的小电阻炉进行加热升温,升温速率可通过编程自行设置;温度控制装置使用TCW-32B型程序温度控制器,如图1所示;选用WRE型热电偶进行温度的测定,将试样(12mm×15mm)放在内表面光滑的陶瓷小坩埚中,燃后一同放入节能的小电阻炉中进行测试,整个测试过程不添加任何保护在大气中直接测量[4].本实验采用的燃点测试原理为:用温度采集卡采集到电脑的是一个时间和温度的-坐标系,横坐标为时间,纵坐标为温度 .温度随着电阻炉的升温而缓慢上升,当到达镁合金燃点时,由于镁合金燃烧时大量放热,其表面温度急剧升高,在加热温度和时间曲线上会出现一个拐点,其拐点相应的纵坐标就是合金的燃点 [5-6].1.3 表面张力检测方法本研究采用“最大气泡压力法”测量阻燃镁合金熔体的表面张力.实验装置见图如图2所示.采用高纯度氩气作为工作气体,干燥瓶中装有CaCl2用于干燥气体,毛细石英管直径为2.86mm,端口经过抛光、清洗处理,U形压力计工作液体为纯净水.图1 燃点测试设备简图Fig.1 Theequipmentdiagram of ignition point test图2 最大气泡压力法测试表面张力装置简图Fig.2 BMPSurface tension testing schematic工业纯Mg熔化后在750℃左右加入Mg-30%Ca和Mg-30%Ce中间合金,待金属完全熔化后搅拌均匀,去除表面熔渣,保温10 m in后进行表面张力的测量.测量时首先打开氩气瓶,通过一系列的量程装置、U形管两边液面波动情况和熔体中产生气泡的速度来调节气体流量大小,以阻燃镁合金熔体表面每分钟产生8~10个气泡为准[7-9].记录下毛细石英管插入到熔体内部的深度和U形管两端的最大液面差值.根据胡福增等人研究 [10],表面张力的计算公式为 max=2 /2.记录毛细管下插入熔体深度 1和U形压力计两端最大高度差为 2,则可得式中: =2.86mm;水为水的密度;为阻燃镁合金熔体的密度,镁合金的密度按照质量比进行计算.1.4 氧化膜检测方法将熔炼好的阻燃镁合金取一部分打磨后放入陶瓷坩埚中重新熔炼,待合金熔化完全后进行搅拌以除去表面的夹杂物并使合金混合均匀,将坩埚取出后放入空气中自然冷却,则会在合金表面形成一层自然的氧化膜.通过配备有能谱分析仪的 Hitachi S4800扫描电镜对氧化膜的表面形貌及氧化镁截面的元素分布进行检测,并且通过X射线对氧化膜表面的相组成进行分析.2 实验结果及分析2.1 阻燃性能结果及分析本实验保持Ca含量不变,通过加入不同的Ce含量,探讨Ce含量对镁合金阻燃性的影响,结果表明:在一定范围内随着Ce含量的增加,镁合金燃点不断提高,当Ce含量达到1.2%时,镁合金的燃点达到780℃,而Ce含量再提高到时,镁合金的燃点增长比较缓慢,如图3所示.2.2 氧化膜检测结果及分析图4为合金在液态下自然冷却条件下产生的氧化膜结构,其中a)、b)分别为Mg-1.2Ca的100倍、2 000倍放大倍数的形貌图,c)、d)分别为Mg-1.2Ca-1.2Ce的100倍、2000倍放大倍数的形貌图.通过对比可以看出,Mg-1.2Ca合金的氧化膜疏松多孔,并且在局部区域已经有“菜花状”的氧化产物;而Mg-1.2Ca-1.2Ce合金的氧化膜光滑、致密,在一定程度上可以起到隔绝空气、阻止氧化和燃烧的效果.图 5为Mg-1.2Ca-1.2Ce阻燃镁合金氧化膜表面的物相分析,从图中可以看出其氧化膜表面主要有基体Mg、MgO、CaO和Ce2O3.图4 Ce加入对Mg-1.2Ca合金氧化膜形貌的影响Fig.4 Theeffectof Ceaddition on oxide film morphology ofMg-1.2Caalloy这种氧化膜结构的明显不同可以很好的解释阻燃效果之间的差异.归其原因,主要是由于,在没有添加任何Ce元素的情况下,不论形成的MgO薄膜还是CaO薄膜,由于其致密度较低,因此不能够完全阻止氧的进一步扩散;相反,在添加了较多元素的Ce后,不但可以形成更加致密的复合的氧化膜,而且Ce2O3比较致密,不但可以很好的隔绝氧的进一步扩散,而且还能够添补许多裂纹,因此,具有很好的阻燃效果.图6为Mg-1.2Ca-1.2Ce氧化膜截面的形貌和元素分布线扫描分析.从图中可以看出,氧化膜的厚度差不多有2 m,Ca元素主要分布在氧化膜的中间部分,而Ce元素主要分布在氧化膜与镁基体的交界处.根据先扫描结果可以将Mg-1.2Ca-1.2Ce氧化膜结构分为三层,最外面主要为MgO,中间层主要为CaO,最内层主要为Ce2O3.图5 Mg-1.2Ca-1.2Ce镁合金氧化膜表面的XRD分析Fig.5 XRD analysisofMg-1.2Ca-1.2Ceoxide film图6 Mg-1.2Ca-1.2Ce氧化膜截面形貌及能谱分析Fig.6 The SEM and EDSof oxide film of Mg-1.2Ca-1.2Ce2.3 表面张力测量结果及分析稀土元素Ce是表面活性元素,很容易富集到镁合金熔体表面,这种表面富集现象极大地影响了镁合金熔体氧化膜结构及其阻燃性能.表面张力是一个重要的高温熔体物理属性,可以很好地反映Ce元素在阻燃镁合金熔体表面的富集状况,从而为研究阻燃镁合金机理提供了另外一种直观的理论依据.本研究测量了不同Ce含量对Mg-1.2Ca镁合金熔体表面张力的影响.熔体表面张力的测量在730℃、大气压下进行,采用最大气泡压力法.其测试结果如图7所示,可以看出随着Ce含量的增加,Mg-1.2Ca-xCe熔体表面张力不断下降.这与Ce含量在镁合金熔体表面富集,提高熔体表面表面活性有直接关系.图7 Ce加入量对Mg-1.2Ca合金熔体表面张力的影响Fig.7 Effectof Ce contenton the surface tension ofMg-1.2 Camelt2.4 阻燃镁合金的热力学分析Mg-1.2Ca-1.2Ce氧化膜表面的物相分析表明含有MgO、CaO、Ce2O3,据此推断,合金熔体表面可能发生了以下反应热力学计算中以固态纯物质为标准态,所以取固态物质的活度,镁合金熔炼在750℃左右进行,取为 1 023 K.从式 ( 9)、(12)、(15)可知,从热力学上讲,在氧化开始时Mg、Ca和Ce3种元素均有可能发生氧化;从式 ( 16)、(17)、(18)可以看出,由于活度的影响,式 ( 4)、(5)、(6)所述的置换反应在元素分布均匀的情况下不可能发生;从式 ( 8)、(11)、(14)各氧化物分解压的计算,MgO、CaO 和分解压的大小顺序为:.此外,对氧化膜进行X射线衍射结果表明(图5),氧化膜中并未出现新的复杂氧化物,可见MgO、CaO和是互不固溶的.按热力学规律,此时合金将分层氧化,即氧化膜外层氧压高生成的氧化物其分解压也大,氧化膜内层氧压低生成的氧化物其分解压也小[ 5-6].所以 M g-1.2Ca-1.2Ce来说,将按照这样的顺序来氧化:最外层是MgO,其次是CaO,最内层是.至此,初始的保护性氧化膜形成.但由于Ce元素在合金熔体中是分布不均匀的,如图6所示的点能谱分析可以看出,Ca和Ce在此处的相对原子分数分别达到了2.50%和3.34%.按照此处的原子活度计算得到:△G4(1 023 K)=12 885.19 kJ/mollt;0,△G5(1 023K)=17 418.58kJ/molgt;0,△G6(1 023K)=56 138.14 kJ/molgt;0,在此处式(4)中的反应可以自发地进行.由此可知,式 ( 4)、(5)、(6)的反应在局部元素分布不均匀的区域有可能发生置换反应.3 结论1)在一定范围内,随着Ce含量的增加,合金的燃点也随之提高,当Ce含量达到1.2%时,合金的燃点能达到780℃.2)Mg-1.2Ca合金的氧化膜疏松多孔,并且在局部区域有“菜花状”的氧化产物;当Ce含量加入1.2%后,合金形成的复合氧化膜非常致密、光滑,能有效阻止氧化、燃烧.3)在温度一定的情况内,随着Ce含量的增加,提高了Mg-1.2 Ca-xCe合金表面活性,熔体表面张力不断下降.熔体表面张力的下降可以反映Ce元素在熔体表面的富集状况,从另一个角度表明了Ce元素的添加对氧化膜结构以及阻燃性能的影响. 4)通过氧化膜的截面检测和热力学计算分析得出Mg-1.2Ca-1.2Ce的形成的氧化膜大致分为3层:外层是MgO,中间层是CaO,内层是Ce2O3.参考文献:[1]Sakamoto M.Suppression of ignition and burning ofmolten Mg alloysby Ca bearing stable oxide film [J].Journal of Materials Science Letters,1997,16(12):1048-1050.[2]黄晓锋,周宏,何镇明.富铈稀土对镁合金起燃温度的影响 [J].中国有色金属学报,2001,11(4):638-641.[3]黄晓锋,周宏,何镇明.AZ91D加铈阻燃镁合金氧化膜结构分析 [J].中国稀土学报,2002,20(1):49-52.[4]曾小勤,王渠东,丁文江.镁合金熔炼方法及进展 [J].轻合金加工技术,1999,27(9):5-8.[5]Suling Cheng, Gencang Yang. Effect of Ca and Y additions on oxidation behavior of AZ91 alloy at elevated temperatures[J].Transactionsof NonferrousMetaals Society of China,2009,19(2):299-304.[6]Zhou Hong,WangM ingxing. EffectofCeadditionon ignition pointofAM 50alloy powders[J].Materials Letters,2006,60(27):3238-3240.[7]李华基,刘华堂,杨志远.混合稀土阻燃ZM 5镁合金的表面张力研究 [J].材料热处理技术,2010,39(24):83-85.[8]Jha N,M ishra A K.Thermodynam ic and surface propertiesof liquidMg-Zn alloys[J].A lloysand Compounds,2001,329(1):224-229.[9]Garcia-CordovillaC,LouisE.Surface tensionofbinaryand ternaryaluminium alloysof thesystemsAl-Si-Mgand A l-Zn-Mg[J].MaterialsScience,1992,27(19):5247-5252.[10]胡福增,陈国荣,杜永娟.材料表界面 [M].上海:华东理工大学出版社,2007.。
最新文档-镁及镁合金ppt课件-PPT精品文档
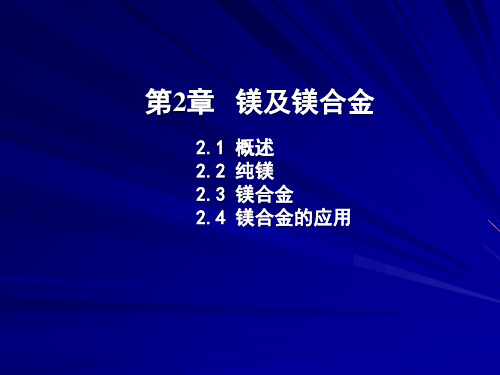
11.5 20.0
2.5 9.0
45 45
8 11.5
9 12.5
30 36
2.2 纯镁-纯镁的ຫໍສະໝຸດ 性物理性能单位 g/cm3
W/m· k μm/m· k %35MPa J/l· k kJ/l
AZ91 1.81
AM 60
A380 压铸 合金 320 160
A356 T6 262 185 186 205 90
尼龙 195 170
ABS 45 40
钢 ~330 ~200
220
0.1%蠕变强度
无缺口冲击强度 有缺口冲击强度 延伸率 弹性模量 剪切模量 布氏硬度
MPa
J J % GPa GPa
125℃
34
6 1.5 3
51
AM60 1.79
61
A380 DC
A356 T6
镁物理性能的优点
尼龙 1.4
0.33
ABS 1.05
0.28
钢 7.8
14
比重
传热系数
2.74
96
2.69
159
膨胀系数
减振性能 比热 熔化潜热 凝固范围 腐蚀失重 3天5% NaCl
26
29 1900 673 470-595 0.02
25.6
52
34
22 3.2 8-15 45
135
3.5 11
4 72 27
5 73 28 80
8 8.9
17 2.1
30-50 207 83 140
Ambient Ambient
45 14 65
镁粉尘云最低着火温度的实验测试

第29卷 第4期爆炸与冲击Vol.29,No.4 2009年7月EXPLOSION AND SHOC K WAV ES J ul.,2009 文章编号:100121455(2009)0420429205镁粉尘云最低着火温度的实验测试3钟英鹏,徐 冬,李 刚,苑春苗,陈宝智(东北大学火灾爆炸防治实验室,辽宁沈阳110004) 摘要:采用标准装置G odbert2Greenwald恒温炉测试了不同条件下镁粉尘云最低着火温度。
实验测试结果显示:D50为6、47、104、173μm时镁粉尘云最低着火温度分别为480、520、620、>700℃;选取D50为6μm 的镁粉,在分散压力恒定为0.1MPa时,镁粉浓度由424g/m3变化到5085g/m3,粉尘云最低着火温度由600℃降低到480℃;而粉尘质量恒定为0.3g时,分散压力从0.1MPa增加到0.2MPa,粉尘云最低着火温度由540℃升高到580℃。
还分析了镁粉粒径、浓度及分散压力对粉尘云最低着火温度的影响。
关键词:爆炸力学;粉尘云最低着火温度;G2G恒温炉;镁粉;粒径;浓度;分散压力 中图分类号:O381;X932 国标学科代码:130・3510 文献标志码:A 金属镁化学性质比较活泼,容易与氧化剂发生剧烈的氧化还原反应。
在镁粉加工、输送和储存过程中,镁粉经常处于悬浮的粉尘云状态,此时,如果粉尘云遇到温度足够高的热源,就可能被点着,从而引发火灾爆炸[1]。
粉尘云最低着火温度(minimum ignition temperature of dust cloud,MITC)是粉尘爆炸中的一个非常重要的特征参数,是对粉尘爆炸敏感度进行相对评价的重要指标,也是进行防爆工艺设计和防爆设备选型的重要依据。
有效点火源是粉尘爆炸发生的必备条件之一,镁粉生产场所选择防爆电气设备,可有效避免电气火花和设备过热成为粉尘爆炸的着火源。
测试镁粉尘云最低着火温度的目的是为了正确选择防爆电气设备,同时可用来评价镁粉着火爆炸危险性,为保证安全生产提供实验依据[2]。
镁合金压铸过程中的防火安全(2篇)

镁合金压铸过程中的防火安全镁合金是一种具有轻量化、高强度、良好的刚性和优异的导热性能的金属材料,广泛应用于汽车、航空航天、电子等行业。
然而,由于镁合金具有较低的点燃温度和快速燃烧的特点,使得镁合金在加工过程中存在着较大的火灾风险。
因此,在镁合金压铸过程中,必须严格遵守防火安全措施,确保工作环境的安全,预防火灾事故的发生。
一、火灾危险性分析1. 镁合金的燃烧性能:镁合金具有较低的点燃温度(约650℃),并且在空气中燃烧时,释放出大量的热量。
同时,镁合金燃烧时还会产生刺激性的烟雾和高温的火焰,给人员和设备带来巨大的危险。
2. 美国质量监督管理局(MIL)对镁合金所进行的失火实验表明,镁合金压铸产品在火灾发生后,燃烧温度可迅速升至2000℃以上。
这种高温下的火焰和火灾热辐射对设备和人员造成的危害极大,且难以控制。
3. 镁合金压铸企业线材、切削工具、干粉涂料等常规的防火设施,不能很好地应对镁合金燃烧产生的高温火势和剧烈反应的影响。
以上分析表明,镁合金压铸过程中的火灾风险较高,对防火安全的要求必须高于其他金属材料的加工过程。
二、镁合金压铸过程中的防火安全措施1. 安全意识教育培训:加强对员工的安全意识教育和防火知识培训,提高员工的安全意识和火灾应急处置能力。
加强对新员工的入职培训和实际操作指导,确保员工具备应对火灾的基本知识和操作技能。
2. 对设备进行定期维护:保持设备的良好状态和正常运行,确保设备不会因为故障导致火灾的发生。
对各种设备、管道和阀门进行定期维护,定期检查是否存在泄漏、松动等现象,及时进行排除。
3. 建立有效的防火检查制度:制定防火检查计划,对生产车间、仓库、设备区域等进行定期检查,发现问题及时整改,确保生产环境的清洁、整齐、无积尘、杂物。
4. 清除易燃物:对生产车间及周边环境进行定期清理,清除易燃物、杂物和积尘,保持生产环境的整洁干净。
5. 设置消防设备:根据工艺流程和压铸设备的特点,设置合适的消防设备,如灭火器、消防栓、喷淋系统等。
【国家标准】DB22T 2362-2015 镁合金中钠含量的测定火焰原子吸收光谱法

国家标准、行业标准编制说明《中华人民共和国标准化法》将中国标准分为国家标准、行业标准、地方标准(DB)、企业标准(Q/)四级。
国际标准由国际标准化组织(ISO)理事会审查,ISO理事会接纳国际标准并由中央秘书处颁布;国家标准在中国由国务院标准化行政主管部门制定,行业标准由国务院有关行政主管部门制定,企业生产的产品没有国家标准和行业标准的,应当制定企业标准,作为组织生产的依据,并报有关部门备案。
法律对标准的制定另有规定,依照法律的规定执行。
制定标准应当有利于合理利用国家资源,推广科学技术成果,提高经济效益,保障安全和人民身体健康,保护消费者的利益,保护环境,有利于产品的通用互换及标准的协调配套等。
中国标准按内容划分有基础标准(一般包括名词术语、符号、代号、机械制图、公差与配合等)、产品标准、辅助产品标准(工具、模具、量具、夹具等)、原材料标准、方法标准(包括工艺要求、过程、要素、工艺说明等);按成熟程度划分有法定标准、推荐标准、试行标准、标准草案。
一份国标通常有封面、前言、正文三部分组成。
标准号:标准号至少由标准的代号、编号、发布年代三部分组成。
标准状态:自标准实施之日起,至标准复审重新确认、修订或废止的时间,称为标准的有效期;又称标龄。
归口单位:实际上就是指按国家赋予该部门的权利和承担的责任、各司其责,按特定的管理渠道对标准实施管理。
替代情况:替代情况在标准文献里就是新的标准替代原来的旧标准。
即在新标准发布即日起,原替代的旧标准作废。
另外有种情况是某项标准废止了,而没有新的标准替代的。
实施日期:标准实施日期是有关行政部门对标准批准发布后生效的时间。
提出单位:指提出建议实行某条标准的部门。
起草单位:负责编写某项标准的部门。
ICS 77.120.01H 12 备案号:48375-2016 DB22吉林省地方标准DB 22/T 2362—2015吉林省质量技术监督局 发布本标准仅本标准仅供内部使用 不得翻印本标准仅供内部使用不得翻印DB22/T 2362—2015 I前 言本标准按照 GB/T 1.1—2009 给出的规则起草。
镁合金使用寿命以及性能特点

如何提高镁合金的耐高温性能?镁合金在汽车制造、航空工业等方面的应用要求具有一定的高温性能和抗蠕变性能,稀土镁合金(AE系列)能提高合金的高温强度和蠕变强度。
研究表明,加入一定量的锡可改善合金的高温强度;加人硅可改善合金的蟠变强度;加人鳃可提高合金的高温(超过300℃)性能;加入银可提高合金的高温强度和蠕变强度。
在Mg-5Al-1 Zn-1 Si合金中加人0.5%(质量分数)的锑,使合金在150℃时的强度从168 MPa上升到178MPa,屈服强度也从81 MP。
上升到90MPa,抗冲击韧性值从21J上升到30J。
稀土会使镁合金的室温性能变差,为此,加人一些短纤维、晶须、颗粒等复合材料,以改善合金的室温和高温性能。
在Mg-/Li合金中加人一定的Mg0/Mg2Si颗粒,使合金的高温抗蠕变。
性能在温度达210℃前得到显著改善,而且随着温度的升高,改善效果更为明显。
笔记本电脑和手机外壳等在一定的工作温度范围内,要求其尺寸稳定性(抗蠕变性能)要好。
与现有的工程塑料相比,不会因环境改变而改变的镁基耐高温复合材料的性能优势可得到充分施展。
镁基复合材料的制备方法主要有真空(或保护性气氛)浸渗法、粉末冶金法、薄膜冶金法、搅拌铸造法。
提高镁合金材料使用寿命有何技术措施?镁是活泼的金属元素,标准电极电位为负值,且绝对值很大,导致镁及镁合金的耐腐蚀性很差,这阻碍了镁合金产品在应用中发挥优势,限制了其应用范围。
镁合金腐蚀的直接原因是合金元素及杂质元素的引入导致镁合金中出现第二相。
镁合金的腐蚀形态有:电偶腐蚀、点蚀、应力腐蚀开裂、晶间腐蚀和丝状腐蚀以及高温氧化。
镁合金发生电化学腐蚀与溶液的pH值、溶液的性质、合金的成分及所处的环境有关。
为提高镁合金材料的使用寿命,应控制冶金因素以提高镁合金的耐腐蚀性,具体包括合金元素、杂质元素、相组成和微结构。
表面处理技术的研究,如镁合金的化学转化处理、阳极氧化、等离子微弧阳极氧化、金属镀层和物理气相沉积涂层技术等,为等离子技术提高镁合金的耐腐蚀性带来了新的生机。
上海交通大学科技成果——阻燃镁合金
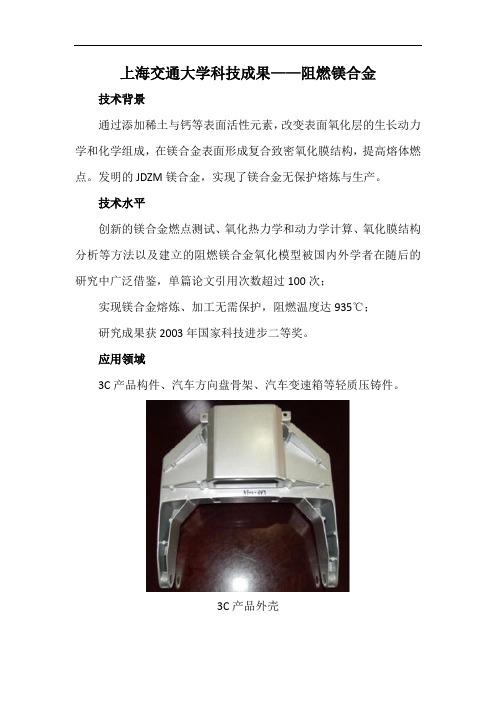
上海交通大学科技成果——阻燃镁合金技术背景
通过添加稀土与钙等表面活性元素,改变表面氧化层的生长动力学和化学组成,在镁合金表面形成复合致密氧化膜结构,提高熔体燃点。
发明的JDZM镁合金,实现了镁合金无保护熔炼与生产。
技术水平
创新的镁合金燃点测试、氧化热力学和动力学计算、氧化膜结构分析等方法以及建立的阻燃镁合金氧化模型被国内外学者在随后的研究中广泛借鉴,单篇论文引用次数超过100次;
实现镁合金熔炼、加工无需保护,阻燃温度达935℃;
研究成果获2003年国家科技进步二等奖。
应用领域
3C产品构件、汽车方向盘骨架、汽车变速箱等轻质压铸件。
3C产品外壳
汽车变速箱壳体
汽车方向盘骨架
汽车副车架。
易燃固体的燃烧实验报告(3篇)

第1篇一、实验目的1. 了解易燃固体的燃烧特性。
2. 观察易燃固体在不同条件下的燃烧现象。
3. 分析影响易燃固体燃烧速度和火焰特性的因素。
4. 增强消防安全意识,提高防火和灭火技能。
二、实验原理易燃固体是指燃点低,对热、撞击、摩擦敏感,易被外部火源点燃,燃烧迅速,并可能散发出有毒烟雾或有毒气体的固体物质。
本实验通过控制变量法,观察不同易燃固体的燃烧现象,分析其燃烧速度、火焰特性以及与外界条件的关系。
三、实验材料与仪器1. 实验材料:易燃固体(如镁粉、硫粉、磷粉等),酒精灯,火柴,镊子,剪刀,计时器,温度计,实验台,记录本。
2. 实验仪器:酒精灯,火柴,剪刀,计时器,温度计,实验台。
四、实验步骤1. 准备实验材料:将不同种类的易燃固体分别用剪刀剪成粉末状,并分别放在实验台上。
2. 设置实验环境:确保实验室内通风良好,避免可燃气体积聚。
3. 进行燃烧实验:a. 将酒精灯点燃,调整火焰大小。
b. 用镊子夹取少量易燃固体粉末,置于酒精灯火焰上方。
c. 观察并记录易燃固体的燃烧现象,包括燃烧速度、火焰颜色、烟雾产生情况等。
d. 用计时器记录燃烧时间,并观察火焰熄灭后的余烬情况。
4. 分析实验结果:比较不同易燃固体的燃烧特性,分析影响燃烧速度和火焰特性的因素。
五、实验结果与分析1. 镁粉燃烧实验:镁粉燃烧速度较快,火焰颜色为白光,产生大量白烟,燃烧时间约为5秒。
2. 硫粉燃烧实验:硫粉燃烧速度较慢,火焰颜色为蓝色,产生刺激性气味,燃烧时间约为10秒。
3. 磷粉燃烧实验:磷粉燃烧速度较快,火焰颜色为黄色,产生大量白烟,燃烧时间约为3秒。
通过实验观察,我们可以得出以下结论:1. 易燃固体的燃烧速度与其化学成分有关,不同种类的易燃固体具有不同的燃烧特性。
2. 燃烧速度受外界条件(如温度、压力、氧气浓度等)的影响,实验中火焰大小和燃烧速度存在一定关系。
3. 燃烧过程中产生的烟雾和气味对环境和人体健康有一定危害,实验时应注意通风和安全。