2013深孔钻发展到巅峰
深井超深井钻井技术

深井、超深井钻井技术(一)90年代以来,国内外深井、超深井钻井技术的发展方向和趋势深井、超深井钻井技术是一个国家综合钻井技术水平高低的标志之一。
深井钻井技术发展方向是围绕加快钻井速度这一目标,进行深井配套技术、工具的研究,主要包括:钻机、钻头、井下工具、钻井泥浆等方面。
深井钻井技术将向深水平井钻井技术发展。
在国外已完成的深井中,大约有一半的井是探井。
井深已从4500m提高到现在的12000m,世界纪录是苏联科拉半岛上的SG-3井,井深为12200m。
目前,美国、前苏联、德国的超深井钻井技术装备和综合技术处于国际领先地位,其中美国是世界上钻深井历史最长、工作量最大和技术水平最高的国家。
近年来,国外深井钻井技术发展主要集中在钻机、钻头、井下工具、钻井泥浆等方面。
深井钻机功率大、性能好、自动化程度高、配套设备性能可靠,从而在装备上为快速打好深井提供了物质上的准备。
钻头质量好,品种全,选型合理,可获得钻头耗用数少、钻井进尺多、钻井速度快的好效果。
钻井液具有良好的热稳定性、润滑性和剪切稀释特性、固相含量低、高压失水量低、可抗各种可溶性盐类和酸性气的污染。
另外,运用井下动力钻具提高钻速、井身结构设计灵活、高强度钻杆等工具配套齐全,使得国外深井钻井速度快、事故少、成本低。
90年代,美国在复杂地质条件下所钻成的5口7500m左右的深探井,其完井周期最短的不到1年,最长的不超过2年。
目前,北海地区测量井深8000m左右的大位移井,其钻井周期一般只是90d左右。
如钻一口5000m的井,平均使用钻头15~20只,钻井周期约需45~70d:6000m的井用45~70只钻头,约125~150d;7000m的井用60~70只钻头,约175~200d。
美国的深井平均单井成本要比世界其他地区的少40%~50%,其钻井技术特点如表4-1所示。
表4-1美国钻井主要技术数据归纳起来说,深井快速钻井技术国外一般从三个方面考虑:选择大功率、高性能、自动化程度高的钻机,选用先进的钻头,采用其他先进设备和井下工具,装备上要有优势;在工艺上实施实时监控,优化钻井参数,用优质钻井液进行平衡或近平衡钻井,实现科学化钻井作业;加强管理,尽量减少钻井事故。
国内外深井钻井技术比较分析
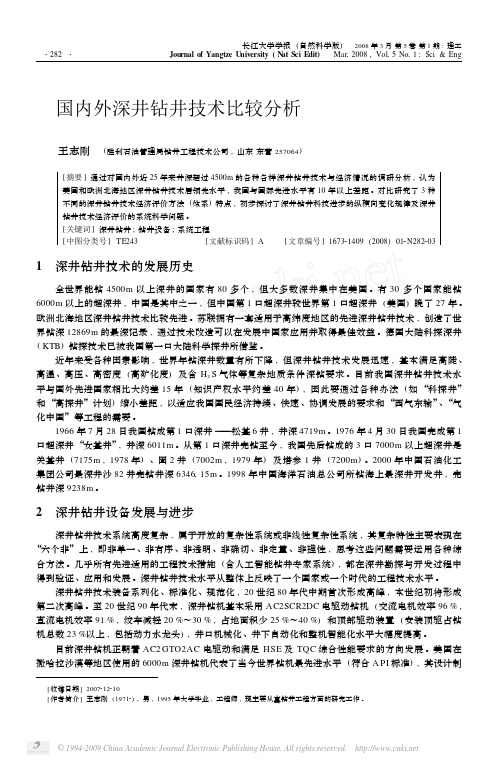
[收稿日期]2007212210 [作者简介]王志刚(19712),男,1995年大学毕业,工程师,现主要从事钻井工程方面的研究工作。
国内外深井钻井技术比较分析 王志刚 (胜利石油管理局钻井工程技术公司,山东东营257064)[摘要]通过对国内外近25年来井深超过4500m 的各种各样深井钻井技术与经济情况的调研分析,认为美国和欧洲北海地区深井钻井技术居领先水平,我国与国际先进水平有10年以上差距。
对比研究了3种不同的深井钻井技术经济评价方法(体系)特点,初步探讨了深井钻井科技进步的纵横向变化规律及深井钻井技术经济评价的系统科学问题。
[关键词]深井钻井;钻井设备;系统工程[中图分类号]TE243[文献标识码]A [文章编号]167321409(2008)012N2822031 深井钻井技术的发展历史全世界能钻4500m 以上深井的国家有80多个,但大多数深井集中在美国。
有30多个国家能钻6000m 以上的超深井,中国是其中之一,但中国第1口超深井较世界第口超深井(美国)晚了27年。
欧洲北海地区深井钻井技术比较先进。
苏联拥有一套适用于高纬度地区的先进深井钻井技术,创造了世界钻深12869m 的最深记录,通过技术改造可以在发展中国家应用并取得最佳效益。
德国大陆科探深井(KTB )钻探技术已被我国第一口大陆科学探井所借鉴。
近年来受各种因素影响,世界年钻深井数量有所下降,但深井钻井技术发展迅速,基本满足高陡、高温、高压、高密度(高矿化度)及含H 2S 气体等复杂地质条件深钻要求。
目前我国深井钻井技术水平与国外先进国家相比大约差15年(知识产权水平约差40年),因此要通过各种办法(如“科探井”和“高探井”计划)缩小差距,以适应我国国民经济持续、快速、协调发展的要求和“西气东输”、“气化中国”等工程的需要。
1966年7月28日我国钻成第1口深井———松基6井,井深4719m 。
1976年4月30日我国完成第1口超深井“女基井”,井深6011m 。
国内掘进技术发展历程

国内掘进技术发展历程
掘进技术是一种专门用于地下采矿或隧道工程的技术。
随着经济的发展和工程建设的需求增加,国内掘进技术经历了长足的发展,取得了显著的成就。
本文将从不同阶段对国内掘进技术的发展历程进行简要介绍。
20世纪50年代至70年代初期,我国开始独立开展掘进技术的研究和应用。
在这一时期,国内掘进技术主要以人工掘进和动力机械爆破掘进为主,并且以煤矿掘进为主要应用领域。
主要的掘进设备包括手持式钻机、露天钻机和小型动力机械掘进设备。
由于技术水平限制和设备性能限制,这一时期的掘进技术在效率和质量上存在一定的问题。
70年代中期至80年代初期,我国开始引进国外先进的掘进技术和设备。
这一时期,国外的隧道掘进机和液压钻机等设备逐渐引入国内,为国内掘进技术的改进和发展提供了新的技术支持。
我国还开始在掘进技术方面进行自主研发,加大了对掘进设备和工艺的改进力度。
这一阶段是国内掘进技术发展的转折点,标志着国内掘进技术开始向现代化、智能化方向迈进。
21世纪初期至今,国内掘进技术持续迎来了新的发展机遇和挑战。
随着科技的不断进步和工程建设的需求不断增加,国内掘进技术仍然面临着一系列新的技术和市场挑战。
在这一新的发展阶段,国内掘进技术需要在保持技术领先的基础上,加大对掘进技术的创新研发力度,提高技术创新能力和核心竞争力,为国内地下工程建设提供更加高效、安全、可持续的技术支持。
国内掘进技术经过了长期的发展和积累,取得了显著的成就。
随着科技的不断进步和社会的不断发展,国内掘进技术仍然面临着许多新的挑战和机遇。
相信在国内政府、企业和社会的共同努力下,国内掘进技术一定会迎来更加美好的未来。
深孔钻床发展简史

1 绪论1.1 机床在国民经济的地位及其发展简史现代社会中,人们为了高效、经济地生产各种高质量产品,日益广泛的使用各种机器、仪器和工具等技术设备与装备。
为制造这些技术设备与装备,又必须具备各种加工金属零件的设备,诸如铸造、锻造、焊接、冲压和切削加工设备等。
由于机械零件的形状精度、尺寸精度和表面粗糙度,目前主要靠切削加工的方法来达到,特别是形状复杂、精度要求高和表面粗糙度要求小的零件,往往需要在机床上经过几道甚至几十道切削加工工艺才能完成。
因此,机床是现代机械制造业中最重要的加工设备。
在一般机械制造厂中,机床所担负的加工工作量,约占机械制造总工作量的40%~60%,机床的技术性能直接影响机械产品的质量及其制造的经济性,进而决定着国民经济的发展水平。
可以这样说,如果没有机床的发展,如果不具备今天这样品种繁多、结构完善和性能精良的各种机床,现代社会目前所达到的高度物质文明将是不可想象的。
一个国家要繁荣富强,必须实现工业、农业、国防和科学技术的现代化,这就需要一个强大的机械制造业为国民经济各部门提供现代化的先进技术设备与装备,即各种机器、仪器和工具等。
然而,一个现代化的机械制造业必须要有一个现代化的机床制造业做后盾。
机床工业是机械制造业的“装备部”、“总工艺师”,对国民经济发展起着重大作用。
因此,许多国家都十分重视本国机床工业的发展和机床技术水平的提高,使本国国民经济的发展建立在坚实可靠的基础上。
机床是人类在长期生产实践中,不断改进生产工具的基础上生产的,并随着社会生产的发展和科学技术的进步而渐趋完善。
最原始的机床是木制的,所有运动都是由人力或畜力驱动,主要用于加工木料、石料和陶瓷制品的泥坯,它们实际上并不是一种完整的机器。
现代意义上的用于加工金属机械零件的机床,是在18世纪中叶才开始发展起来的。
当时,欧美一些工业最发达的国家,开始了从工场手工业向资本主义机器大工业生产方式的过度,需要越来越多的各种机器,这就推动了机床的迅速发展。
钻孔机发展历史论文

钻孔机发展历史论文钻孔机作为一种重要的施工设备,在工程建设中发挥着不可替代的作用。
它的发展历史可以追溯到古代,但直到工业革命以来,钻孔机才逐渐迎来了快速发展。
19世纪初期,最早的钻孔机是由人力或动物力驱动的,用于挖掘地基或挖矿。
随着蒸汽机的发明和应用,钻孔机的动力系统得到了显著改善,工作效率也大大提高。
20世纪初,内燃机和电动机的问世使得钻孔机的动力来源更加多样化,从而满足了不同工程环境的需求。
随着工程技术的不断进步,钻孔机的结构和工作原理也得到了革新和提升。
在20世纪中期,液压技术的应用让钻孔机的操作更加精准和可控,同时减少了运行噪音和振动。
而近年来,随着数字化技术的迅猛发展,智能钻孔机正逐渐走入施工领域,提高了钻孔机的自动化程度和作业精度。
钻孔机在工程建设中的应用也越来越广泛,从地基处理到矿山开采再到环境监测,都有着它的身影。
不断创新的技术和设计让钻孔机的功能得到了拓展和提升,同时也为人们的生产生活带来了诸多便利。
总的来看,钻孔机的发展历程是技术不断革新和应用场景不断扩大的过程。
随着科技的不断发展和社会的不断进步,相信钻孔机将会在未来的施工领域中发挥更加重要的作用。
钻孔机作为一种关键的机械设备,有助于工程建设、基础设施建设和矿业开采等领域的发展。
随着建筑工程的不断发展,对钻孔机的需求也在不断增加,这推动了钻孔机技术的迅速进步。
在过去的几十年里,钻孔机经历了重大的技术革新。
例如,钻头材料的提升、机械结构的优化和自动化控制系统的引入都为提高钻孔机的性能和效率做出了重要贡献。
此外,钻孔机在工程领域的广泛应用也催生了各种各样的专用钻头和附件,以满足不同的工程需求。
随着矿产资源的日益枯竭,对于更深更复杂矿藏的开采需求也不断增加,这种情况推动了钻孔机技术的进一步发展。
现代钻孔机通过雷达、红外线和其他先进技术,不仅能够准确地确定矿藏位置,还可进行远程操控和自动化操作,从而大大提高了采矿效率和安全性。
另外,随着对地下水资源的重视,钻孔机在环境科学和地质勘探中的应用也显著增加。
国外数控钻床发展历程
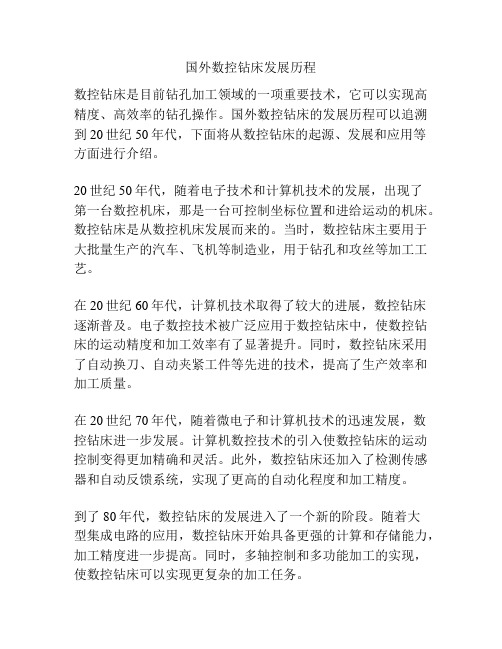
国外数控钻床发展历程数控钻床是目前钻孔加工领域的一项重要技术,它可以实现高精度、高效率的钻孔操作。
国外数控钻床的发展历程可以追溯到20世纪50年代,下面将从数控钻床的起源、发展和应用等方面进行介绍。
20世纪50年代,随着电子技术和计算机技术的发展,出现了第一台数控机床,那是一台可控制坐标位置和进给运动的机床。
数控钻床是从数控机床发展而来的。
当时,数控钻床主要用于大批量生产的汽车、飞机等制造业,用于钻孔和攻丝等加工工艺。
在20世纪60年代,计算机技术取得了较大的进展,数控钻床逐渐普及。
电子数控技术被广泛应用于数控钻床中,使数控钻床的运动精度和加工效率有了显著提升。
同时,数控钻床采用了自动换刀、自动夹紧工件等先进的技术,提高了生产效率和加工质量。
在20世纪70年代,随着微电子和计算机技术的迅速发展,数控钻床进一步发展。
计算机数控技术的引入使数控钻床的运动控制变得更加精确和灵活。
此外,数控钻床还加入了检测传感器和自动反馈系统,实现了更高的自动化程度和加工精度。
到了80年代,数控钻床的发展进入了一个新的阶段。
随着大型集成电路的应用,数控钻床开始具备更强的计算和存储能力,加工精度进一步提高。
同时,多轴控制和多功能加工的实现,使数控钻床可以实现更复杂的加工任务。
进入21世纪,数控钻床在精密加工和高速加工方面取得了重要的突破。
先进的传感器和反馈系统,使得数控钻床的运动控制更加精确和稳定。
同时,高速切削技术的应用,使得数控钻床的工作效率大幅提高。
国外数控钻床的发展历程证明了技术的进步和应用的推动力。
数控钻床的广泛应用使得生产效率大大提升,同时也推动了制造业的发展。
如今,数控钻床已经成为现代制造业中不可或缺的一部分,它不仅在汽车、航空航天等制造业中得到广泛应用,还在电子、光电等高科技领域有着重要的地位。
总的来说,国外数控钻床的发展经历了多个阶段,从最初的电子数控到计算机数控再到现在的高精密和高速加工,每一次的技术革新都为数控钻床的发展带来了新的突破。
国内深井超深井钻井技术的发展趋势
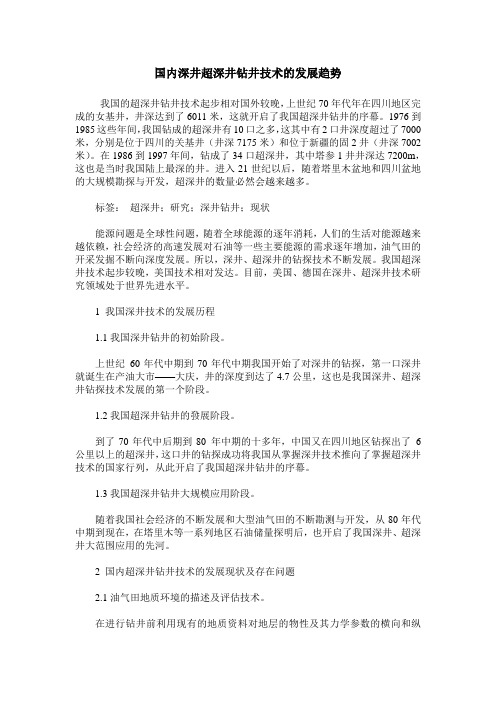
国内深井超深井钻井技术的发展趋势我国的超深井钻井技术起步相对国外较晚,上世纪70年代年在四川地区完成的女基井,井深达到了6011米,这就开启了我国超深井钻井的序幕。
1976到1985这些年间,我国钻成的超深井有10口之多,这其中有2口井深度超过了7000米,分别是位于四川的关基井(井深7175米)和位于新疆的固2井(井深7002米)。
在1986到1997年间,钻成了34口超深井,其中塔参1井井深达7200m,这也是当时我国陆上最深的井。
进入21世纪以后,随着塔里木盆地和四川盆地的大规模勘探与开发,超深井的数量必然会越来越多。
标签:超深井;研究;深井钻井;现状能源问题是全球性问题,随着全球能源的逐年消耗,人们的生活对能源越来越依赖,社会经济的高速发展对石油等一些主要能源的需求逐年增加,油气田的开采发掘不断向深度发展。
所以,深井、超深井的钻探技术不断发展。
我国超深井技术起步较晚,美国技术相对发达。
目前,美国、德国在深井、超深井技术研究领域处于世界先进水平。
1 我国深井技术的发展历程1.1我国深井钻井的初始阶段。
上世纪60年代中期到70年代中期我国开始了对深井的钻探,第一口深井就诞生在产油大市——大庆,井的深度到达了4.7公里,这也是我国深井、超深井钻探技术发展的第一个阶段。
1.2我国超深井钻井的發展阶段。
到了70年代中后期到80 年中期的十多年,中国又在四川地区钻探出了6公里以上的超深井,这口井的钻探成功将我国从掌握深井技术推向了掌握超深井技术的国家行列,从此开启了我国超深井钻井的序幕。
1.3我国超深井钻井大规模应用阶段。
随着我国社会经济的不断发展和大型油气田的不断勘测与开发,从80年代中期到现在,在塔里木等一系列地区石油储量探明后,也开启了我国深井、超深井大范围应用的先河。
2 国内超深井钻井技术的发展现状及存在问题2.1油气田地质环境的描述及评估技术。
在进行钻井前利用现有的地质资料对地层的物性及其力学参数的横向和纵向的分布进行有效的模拟评估,并且通过评估结果来判断地质环境是否适合钻井作业。
我国石油工业史上各类首台钻机

石油之最 MOST OF THE OIL
我国石油工业史上
各类首台钻机
■ 王小波
特深井石油钻机2007年11月研制成功于
我国首台具有自主知识产权的 12000米特深井石油钻机在中国石油宝 鸡石油机械有限责任公司于2007年11 月研制成功。这台钻机是国内外第一 台陆地用12000米交流变频电驱动钻 机,也是当时全球技术最先进的特深 井陆地石油钻机。在此之前,仅美国 在上世纪80年代生产过一台12000米模 拟控制的直流电驱动钻机。
这是国内首次研制成功的DQ40Y液压 顶部驱动钻井装置,填补了我国较大 功率液压顶驱研制方面的空白。
北京石油机械厂DQ40Y液压顶 部驱动钻井装置的基本性能参数与 DQ40BC交流变频顶部驱动钻井装置基 本相当,其主动力机由液压马达取代 交流变频电机,整机结构更加紧凑, 空间尺寸整体缩小,较好地满足了我 国中小型钻机的需要。
- 1、下载文档前请自行甄别文档内容的完整性,平台不提供额外的编辑、内容补充、找答案等附加服务。
- 2、"仅部分预览"的文档,不可在线预览部分如存在完整性等问题,可反馈申请退款(可完整预览的文档不适用该条件!)。
- 3、如文档侵犯您的权益,请联系客服反馈,我们会尽快为您处理(人工客服工作时间:9:00-18:30)。
深孔钻按排屑方式分为外排屑和内排屑两类。
外排屑的有枪钻、深孔扁钻和深孔麻花钻等;内排屑的因所用的加工系统不同,分BTA深孔钻、喷射钻和DF深孔钻3种。
深孔钻已被扩展到小批量加工及大批量生产上,应用范围包括只加工一个孔的零件或有数百多个孔的工件等。
如这套深孔钻系统能适当地配合数控机床应用,其准确度及精密度更能发挥至顶点。
深孔这个需求,早在一百多年前已被人重视及应用,但直至近三十年,这个技术才逐渐被发挥及普遍应用,它能解决麻花钻不能解决的高精度孔和深孔,但直至现在,钻深孔这个技术才更进一步,它已可完全脱离及不再依赖专业深孔钻机器的限制,用户只需购置一套深孔钻系统,再配合其厂里现有的指定机床,便可解决钻深孔的困难。
今天,市场,已普遍被各行各业使用,不管用户要解决深孔、浅孔、高精度孔、大孔径或小孔径的圆孔等,都毫不疑虑地采用这套高技术设计的深孔钻系统如汽车制造业,模具行业,飞机工程,拖拉机厂,军工厂,核电厂和仪表厂等等,他们都能充分发挥这套系统及解决现时所需的精、准、深、误差少及孔径小的圆孔。
材料加工方面,它可解决从碳钢到高温合金以至塑料及木材,最重要的是这套设备能在最短的时间,以最低的成本,钻出一个误差度极低,光滑度高及没有毛刺的圆孔,同时更能从90度以外的角度钻入及内孔交接加工等。
深孔钻工序之重要特点是其高度重复性,用户只需一台稳固的机床或动力头,一件设计正确的夹具,一套完善的深孔钻系统和一支高质量的钻头,便可在整个生产过程中提供一致的表现,一旦固定所有因素:如主轴转速、进给速度和冷却液压力后,深孔钻这个工序便成为一个简易的“控制”工序,不受操作员技术的影响。
枪钻的独具优点解决了传统制造业小直径深孔加工的难题,极大地提高了生产效率,突破了一向影响生产品质、阻碍生产进度的瓶颈,取得十分可喜的效果,至今已被广泛应用於汽车工业、航太工业、医疗器材工业、模具和刀具等制造业领域。
枪钻的书面名称为单刃外排屑深孔钻。
由於最早应用于加工枪管,故通常称为“枪钻”。
枪钻由带有V形切削刃和一个能通切削液的钻头,月牙形的钻杆及夹持所用的钻柄组成。
主要适合於孔深度与孔直径比大於100倍的深孔加工,特别是φ2~φ6的深孔加工。
其工作原理是枪钻柄部被夹持在机床主轴上,钻头通过导引孔或导套进入工件表面,进入後,钻头圆弧面的2-3条刃带起导向作用和挤压孔作用。
这时高压切削液通过钻头中的小孔送到切削区域内,进行冷却、润滑并帮助排屑;切屑和切削液顺著钻头的V形槽排出。
与传统的麻花钻相比,枪钻具有加工精度高、加工时间短、钻头寿命高、排屑好的特点。
而传统的麻花钻每加工大约1~2倍直径的深度必须退刀排屑,加工精度低、表面粗糙度差,加工效率低、操作劳动强度大,质量难以保证。
1. 钻头∶采用硬质合金材料制作;
2. 钻杆∶由专用异型优质钢管制作;
3. 钻柄∶采用优质中碳结构钢制作。
了解详情:/qzdcm.html
官方网站:东莞市曦信模具配件有限公司()。