锚杆支护煤巷冒顶事故类型及对策武星春
锚杆支护巷道冒顶事故原因分析及防范措施
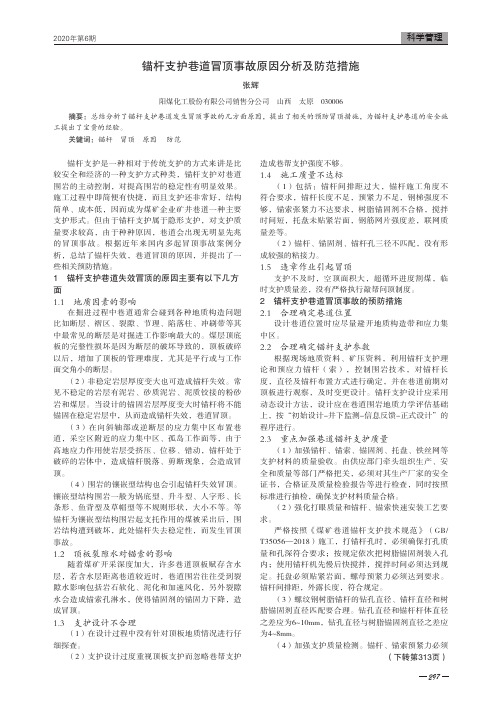
锚杆支护是一种相对于传统支护的方式来讲是比较安全和经济的一种支护方式种类,锚杆支护对巷道围岩的主动控制,对提高围岩的稳定性有明显效果。
施工过程中即简便有快捷,而且支护还非常好,结构简单、成本低,因而成为煤矿企业矿井巷道一种主要支护形式。
但由于锚杆支护属于隐形支护,对支护质量要求较高,由于种种原因,巷道会出现无明显先兆的冒顶事故。
根据近年来国内多起冒顶事故案例分析,总结了锚杆失效,巷道冒顶的原因,并提出了一些相关预防措施。
1 锚杆支护巷道失效冒顶的原因主要有以下几方面1.1 地质因素的影响在掘进过程中巷道通常会碰到各种地质构造问题比如断层、褶区、裂隙、节理、陷落柱、冲刷带等其中最常见的断层是对掘进工作影响最大的。
煤层顶底板的完整性损坏是因为断层的破坏导致的,顶板破碎以后,增加了顶板的管理难度,尤其是平行或与工作面交角小的断层。
(2)非稳定岩层厚度变大也可造成锚杆失效。
常见不稳定的岩层有泥岩、砂质泥岩、泥质铰接的粉砂岩和煤层。
当设计的锚固岩层厚度变大时锚杆将不能锚固在稳定岩层中,从而造成锚杆失效,巷道冒顶。
(3)在向斜轴部或逆断层的应力集中区布置巷道,采空区附近的应力集中区、孤岛工作面等,由于高地应力作用使岩层受挤压、位移、错动,锚杆处于破碎的岩体中,造成锚杆脱落、剪断现象,会造成冒顶。
(4)围岩的镶嵌型结构也会引起锚杆失效冒顶。
镶嵌型结构围岩一般为锅底型、升斗型、人字形、长条形、鱼背型及草帽型等不规则形状,大小不等。
等锚杆为镶嵌型结构围岩起支托作用的煤被采出后,围岩结构遭到破坏,此处锚杆失去稳定性,而发生冒顶事故。
1.2 顶板裂隙水对锚索的影响随着煤矿开采深度加大,许多巷道顶板赋存含水层,若含水层距离巷道较近时,巷道围岩往往受到裂隙水影响包括岩石软化、泥化和加速风化,另外裂隙水会造成锚索孔淋水,使得锚固剂的锚固力下降,造成冒顶。
1.3 支护设计不合理(1)在设计过程中没有针对顶板地质情况进行仔细探查。
煤巷锚杆支护巷道迎头区冒顶原因及预防措施

煤巷锚杆支护巷道迎头区冒顶原因及预防措施作者:郭爱生来源:《科技创新导报》 2011年第29期郭爱生(山西焦煤集团煤炭销售总公司山西太原 030013)摘要:针对煤巷锚杆支护巷道迎头区冒顶事故,阐述了冒顶事故的特点、原因,指出了预防锚杆支护巷道迎头区冒顶的关键,提出了预防迎头区冒顶的措施。
关键词:煤巷锚杆支护迎头区预防措施中图分类号:TQ54 文献标识码:A 文章编号:1674-098X(2011)10(b)-0073-01煤巷锚杆支护具有施工简单,易于提高机械化程度,降低工人劳动强度,成本较低,改善作业环境,掘进单进水平高等诸多优点,已成为煤巷的主要支护形式。
由于锚杆支护设计方法的不断完善,高强度锚杆、锚索、树脂锚固剂的普遍应用,以及对顶板离层监测的重视等,大范围顶板冒落事故已经得到了有效的控制。
但在应用过程中,也发生了一些严重的冒顶事故,而在巷道迎头区则成为冒顶事故的多发区。
1 冒顶的特点煤巷锚杆支护巷道迎头区冒顶具有如下特点:(1)随机性大,呈突发性,冒顶前无明显预兆。
(2)地质条件发生变化的地点,如有小断层、岩石破碎、顶板裂隙发育或近距离煤层的层间距变小、顶锚杆锚固点附近有煤线或有明显的极易离层的岩层弱面存在。
(3)顶板岩体的完整性已受到破坏,已散离为松散的岩块,或者顶板存在“人字形”、“锅底形”、“楔形”、“倒梯形”等镶嵌式构造。
冒顶的高度超过了锚杆长度,冒顶时连带锚杆整体垮落。
(4)冒顶的危害性大,易造成重大伤亡事故。
2 冒顶原因分析煤巷锚杆支护巷道迎头区冒顶的原因,主要有以下三个方面:(1)地质原因。
由于地质构造区附近,岩体的完整性已受到破坏,甚至岩体已散离为大小不等的岩块。
在坚硬的节理发育的岩体中,岩体已被各种各样的结构面切割成各类型的空间镶嵌块体。
开掘巷道后,岩块之间裂隙会迅速扩大,很容易出现局部冒顶事故。
(2)诱发因素。
根据我矿煤巷锚杆支护巷道的矿压观测表明,掘进影响剧烈的时间为1~3天,掘进影响距离为35m左右,其中第一天的变形速度最为显著,距迎头约10m。
煤巷冒顶事故的原因分析和防范对策
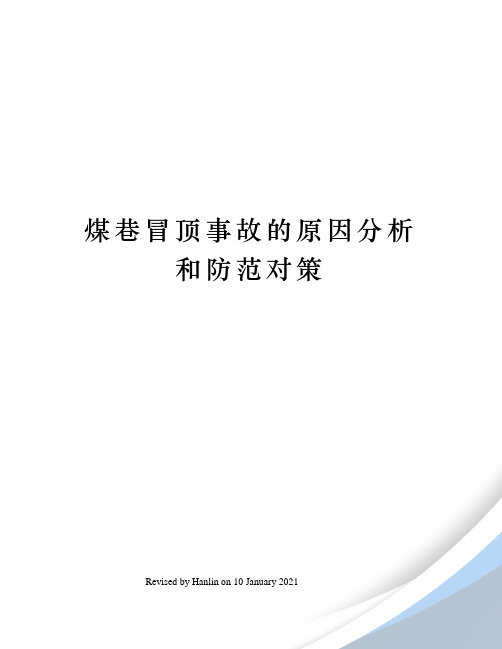
煤巷冒顶事故的原因分析和防范对策Revised by Hanlin on 10 January 2021煤巷冒顶事故的原因分析和防范对策1 概况付村煤业公司井田位于滕南煤田南部,设计生产能力为120万t/a,主采3上和3下煤层,以综采为主。
三层煤直接顶板和底板为砂质泥岩,F=4~6;老顶为细砂岩,F=8~10。
三层煤平均埋藏深度500m左右,煤体硬度F=1.0~2.0。
自1998年矿井试生产以来,在回采巷道中广泛采用了煤巷锚网支护技术,巷道一般设计为矩形,轨顺和运顺一般宽为4.2m,高为3.2m;切眼宽为7.2m,高为2.6m。
其主要支护参数为:顶支护为挂菱形金属网,铺钢梯,安装大螺纹树脂锚杆,钢梯排距800~1000mm;锚杆间距760mm,排距800~1000mm,顶锚杆规格Φ20×2200mm。
帮支护为挂菱形金属网,安装普通钢筋锚杆,锚杆间距800mm,排距800~1000mm,锚杆规格Φ14×1600mm。
自采用锚网支护技术以来,曾发生过两次较大型冒顶事故,一是东二辅助采区皮带巷道冒顶事故,二是3上205切眼冒顶事故。
其中:在3上205切眼冒顶事故中死亡一人,对公司的安全生产工作造成不良影响。
因此,我们对煤巷锚网支护技术结合付煤矿井实际进行研究、总结,对各项支护参数加以修正,使顶板隐患消灭在萌芽之中。
2 冒顶原因分析2.1 冒顶特点从矿井发生的冒顶事故来看,煤巷锚网支护巷道的冒顶具有四个显着特点,一是在进行巷道施工时,由于围岩裂隙发育,出现局部片帮掉顶,顶帮不平整,造成部分锚杆托盘不能密贴壁面,支护质量明显下降。
二是冒顶前巷道围岩显示不稳定状态的一些特征,如:煤炮频率、巷道收敛变形速度不减等。
三是冒顶的厚度及面积较大,两起冒顶事故的冒顶面积皆在20m2以上,巷道冒顶长度皆在5m以上,冒顶厚度皆在2m以上,没有出现锚杆被拉断的现象。
四是冒顶事故皆发生在一些特殊地点,如:断层及围岩破碎带(3上205切眼,东二辅助采区皮带巷)应力集中区、穿层巷道(东二辅助采区皮带巷),巷道宽度较大(3上205切眼)。
锚网巷道冒顶事故的原因和对策

锚网巷道冒顶事故的原因和对策王海云【摘要】通过对事故案例的分析,论述了锚网巷道的冒顶原因,并提出了主要防范措施.【期刊名称】《煤》【年(卷),期】2009(018)009【总页数】3页(P77-78,85)【关键词】锚网巷道;冒顶事故;分析;预防【作者】王海云【作者单位】阳泉煤业集团公司一矿,山西,阳泉,045008【正文语种】中文【中图分类】TD77+1自1998年以来,基本形式为锚杆+W钢带+金属网+补强锚索的锚网支护以其显著的技术、经济优越性成为阳煤集团煤巷的主要支护方式。
但由于锚杆支护为隐蔽工程,煤巷锚网支护的安全可靠性仍较低,冒顶事故时有发生。
下面通过对两起典型事故案例的分析,探讨煤巷锚网支护事故发生的原因,以利于今后防范此类事故的发生。
1.1 某矿15#煤工作面进风巷冒顶事故阳煤集团主采的15#煤层赋存于太原组下部,厚度一般在5~8 m,普氏系数f=2.5~3。
煤层直接顶为黑色泥岩,厚度0~3 m,基本顶为K2石灰岩,厚度7.8~13.3 m。
2006年元月,某矿掘五队在K8111进风巷沿15#煤底层掘进。
该巷采用锚网锚索支护,净宽4.5 m,净高3.0 m,锚杆采用D22 mm×2.4 m螺纹钢锚杆,钢带为4.5 m长7孔W钢带,补强锚索采用D17.8 mm×7.3 m钢绞线,托梁为29U型钢托梁,钢带排距0.9 m。
2006年元月15日晚六点班出勤14人,煤头有5人作业。
由于当班煤头顶板较破碎,塌顶0.8 m,有3排钢带已打起,锚索滞后。
队里安排当班不打进尺,出煤、掼钎包顶。
2006年元月16日0时20分,正在作业时煤头的三排钢带冒顶,造成两人死亡。
1.2 某矿8809工作面尾巷冒顶事故2008年9月,某矿掘二队在8809工作面尾巷沿15#煤层顶板掘进。
该工作面煤层直接顶为黑色泥岩,厚度0.95 m,基本顶为K2石灰岩,厚度10.52 m。
巷道断面为矩形,净宽3.3 m,净高2.3 m,支护方式为锚杆、金属网加锚索联合支护,顶部每排布置5根D20 mm×2 000 mm普通螺纹钢锚杆,间距0.8 m,排距0.8 m,托板规格为D150 mm×8 mm圆形铸钢托板;每4排顶锚杆打两根D15.24 mm×5 200 mm锚索,锚索托板为长1 m的14#槽钢。
煤矿掘进支护技术问题探究武星春

煤矿掘进支护技术问题探究武星春发布时间:2023-06-03T09:53:11.424Z 来源:《中国科技信息》2023年6期作者:武星春[导读] 支护施工对煤矿掘进工作的安全性有着十分重要的影响,支护施工的质量在一定程度上影响着煤矿掘进的效率。
为了优化煤矿掘进支护施工,提高支护效率,本文展开了相关研究,首先介绍煤矿掘进支护施工的特点,之后分析当前煤矿掘进支护所存在的问题,最后提出对策,以此促进煤矿掘进支护施工的发展与完善。
山西保利裕丰煤业有限公司 042199摘要支护施工对煤矿掘进工作的安全性有着十分重要的影响,支护施工的质量在一定程度上影响着煤矿掘进的效率。
为了优化煤矿掘进支护施工,提高支护效率,本文展开了相关研究,首先介绍煤矿掘进支护施工的特点,之后分析当前煤矿掘进支护所存在的问题,最后提出对策,以此促进煤矿掘进支护施工的发展与完善。
关键词煤矿掘进;支护技术;问题;措施引言在煤矿井下开采时,需要掘进大量的巷道以服务于煤矿开采。
在巷道施工过程中,为了保证安全性,需要对巷道进行支护。
掘进巷道的支护不仅要保证效率,还要使得生产的成本处于可控范围内。
由于煤矿地质条件的复杂性,煤矿掘进支护技术还存在着一些问题,例如支护参数不合理、支护速度慢等。
为此,需要对现有的支护技术进行完善,以保证煤矿巷道掘进的安全高效。
一、煤矿掘进支护施工的特征(一)复杂性煤矿掘进支护施工的复杂性主要体现在内部与外部两个方面。
首先在支护施工内部方面,煤矿掘进本身就是一项极其复杂的工作,工序繁多并且难度较大,给相关施工人员在施工工程中造成了较大阻碍;其次在外部方面,支护施工的工作环境也比较复杂,存在较多的不确定因素,经常会出现施工进程与施工设计存在偏差的问题。
由于煤矿掘进支护施工具有较强的复杂性且不可消除,因此支护施工人员必须要采用科学的方法设计施工方案,尽可能多地考虑各种不确定性因素,使施工方案更加全面。
(二)地域性我国幅员辽阔,南北与东西两向跨度极广,并且不同地区的气候环境以及地质条件也有着较大的不同,而这些都是影响支护施工的重要要素,使得支护施工具备很强的地域性特点。
煤巷冒顶事故的原因分析和防范对策

煤巷冒顶事故的原因分析和防范对策1 概况付村煤业公司井田位于滕南煤田南部, 制定生产能力为120万t/a, 主采3上和3下煤层, 以综采为主。
三层煤直接顶板和底板为砂质泥岩, F=4~6;老顶为细砂岩, F=8~10。
三层煤平均埋藏深度500m左右, 煤体硬度F=1.0~2.0。
自1998年矿井试生产以来, 在回采巷道中广泛采纳了煤巷锚网支护技术, 巷道一般制定为矩形, 轨顺和运顺一般宽为4.2m, 高为3.2m;切眼宽为7.2m, 高为2.6m。
其主要支护参数为:顶支护为挂菱形金属网, 铺钢梯, 安装大螺纹树脂锚杆, 钢梯排距800~1000mm;锚杆间距760mm, 排距800~1000mm, 顶锚杆规格Φ20×2200mm。
帮支护为挂菱形金属网, 安装一般钢筋锚杆, 锚杆间距800mm, 排距800~1000mm, 锚杆规格Φ14×1600mm。
自采纳锚网支护技术以来, 曾发生过两次较大型冒顶事故, 一是东二辅助采区皮带巷道冒顶事故, 二是3上205切眼冒顶事故。
其中:在3上205切眼冒顶事故中死亡一人, 对公司的安全生产工作造成不良影响。
因此, 我们对煤巷锚网支护技术结合付煤矿井实际进行研究、总结, 对各项支护参数加以修正, 使顶板隐患消灭在萌芽之中。
2 冒顶原因分析2.1 冒顶特点从矿井发生的冒顶事故来看, 煤巷锚网支护巷道的冒顶具有四个显著特点, 一是在进行巷道施工时, 由于围岩裂隙发育, 出现局部片帮掉顶, 顶帮不平整, 造成部分锚杆托盘不能密贴壁面, 支护质量显然下降。
二是冒顶前巷道围岩显示不稳定状态的一些特征, 如: 煤炮频率、巷道收敛变形速度不减等。
三是冒顶的厚度及面积较大, 两起冒顶事故的冒顶面积皆在20m2以上, 巷道冒顶长度皆在5m 以上, 冒顶厚度皆在2m以上, 没有出现锚杆被拉断的现象。
四是冒顶事故皆发生在一些特别地点, 如: 断层及围岩破碎带〔3上205切眼, 东二辅助采区皮带巷〕应力集中区、穿层巷道〔东二辅助采区皮带巷〕, 巷道宽度较大〔3上205切眼〕。
锚杆支护巷道顶板事故控制措施

锚杆支护巷道顶板事故控制措施一、锚杆支护巷道冒顶事故的原因锚杆支护巷道的冒顶事故的发生除地质因素外,主要是锚杆支护系统的锚固力不足引起的。
巷道成巷后,在原岩应力和次生应力的作用下,巷道围岩产生变形,如果岩石不能自稳,且锚杆支护系统的锚固力不足,这种变形就得不到有效的控制,就会不断发展,最终导致围岩冒落和冒顶。
锚杆间排距过大、锚杆支护材料选择不当、锚杆支护系统的匹配不合理、施工质量差等都会产生这一恶果。
二、巷道交叉处冒顶事故的原因及防治巷道交叉处冒顶事故往往发生在巷道开岔的时候。
因为开岔口需要架设抬棚替换原巷道棚子的棚腿,如果开岔处巷道顶部存在与岩体失去联系的岩块,并且围岩正向巷道挤压,而新支设抬棚或强度不够,或稳定性不够,就可能造成冒顶事故。
当巷道围岩强度不是很大时,顶部存在与岩体失去联系的岩块以及围岩向巷道挤压就在所难免,如果开岔处正好是掘巷时的冒顶处,则情况更为严重。
三、冒顶发生前的预兆:在大多数情况下,在冒顶之前,由于压力增大,顶板岩石开始下沉,使支架开始发出断裂声,而后逐渐折断。
与此同时,还能听到顶板岩石发出啪、啪的破裂声。
随着顶板岩石进一步破碎,在冒落前几秒钟就会发现顶板掉落小碎石块,涌水量也逐渐增大,而后便开始冒落。
顶板冒落之前,岩石在矿山压力作用下开始破坏的初期,其破碎的响声和频率都很低,常常在井下工作人员还没有听到之前,老鼠已有感应。
所以在井下岩层大破坏或大冒落之前,有时会看到老鼠搬家。
在井下工作的人员,当听到或者看到上述冒落预兆时,必须立即停止工作,马上从危险区撤到安全地点。
必须注意的是,有些顶板本来节理发育裂隙就较多,有可能发生突然冒落,而且在冒落前没有任何预兆。
顶板冒落的观测方法有木楔法、标记法、信号柱法等。
木楔法就是在顶板裂隙中钉入一块小木楔(或小金属楔),如果顶板变形、裂隙增大,小木楔会自动落下或松动,说明顶板有冒落危险。
标记法是将黄泥、油漆、水泥砂浆抹在顶板裂隙上,观察其变化,也能反映出顶板变形情况。
锚杆支护掘进工作面常见冒顶事故原因及防治措施

统计资料表明,煤矿顶板事故占总事故数量的40%,而掘进工作面冒顶事故占顶板死亡事故的20%左右,在煤矿事故中占有很大比重。
因此分析煤矿掘进工作面冒顶事故的原因,研究预测预防措施,做好对冒顶事故的预防,对保护煤矿职工的生命和安全至关重要。
1掘进工作面常见冒顶事故的原因分析1.1敲帮问顶制度执行不严格、不彻底,临时支护措施执行不到位,造成危岩突然坠落产生伤亡事故。
如煤矿综掘队2012年10月9日中班在Ⅱ020205工作面机巷进行掘进作业,工作面顶板压力大,采取短掘短支,掘进一片支护一片,截割完第二片网,综掘机断电造成前探梁无法正常使用,现场人员未进行敲帮问顶工作,打设了3根超前锚杆,在挂网作业过程中,突然顶板发出煤炮声,工作面迎头掌子面和顶板跨落下来大量浮煤,顶板冒落300mm,迎头掌子面垮落,一名员工迎面埋倒在综掘机伸缩油缸处,造成左手小臂骨裂。
1.2锚杆、锚索施工质量不合格,原有支护不能很好的控制顶板,日常顶板观测监管不到位。
如某矿综掘队4月8日夜班在120207机巷掘进过程中,当班验收员进入工作面将迎头验收完毕后,行至后巷1130m架棚处发现行人侧顶板异常,有掉渣现象,立即通知迎头人员迅速撤出,随后巷道1130-1140m段顶板冒落,巷道被堵死,外面能看到十几架钢棚完好。
人员安全无伤亡。
后经事故原因分析认为该段巷道为巷道过断层段,断层层理发育、围岩松软破碎,原有支护设计不能较好的控制顶板。
区队安全技术措施执行不到位。
巷道过断层处锚网索支护、锚索安装质量,架棚支护质量不符合安全技术措施要求。
断层处“一梁二柱”棚不能满足支护要求,未及时补打中柱及锚索桁架。
1.3顶板岩性发生变化,非稳定岩层变厚超过支护厚度。
如金凤煤矿2013年8月24日中班,011805工作面机巷在掘进过程中发生一起冒顶事故。
巷道1870-1876m处顶板发生冒顶。
冒落长度6m,冒落高度约3m。
冒顶的主要原因有该段巷道顶部泥岩变厚,厚度超过3m,泥岩遇顶板水膨胀、自重增加、强度降低,且该段巷道前后32m 锚索未及时施工,顶部支护所采用的φ20×2500mm螺纹钢锚杆未能锚入稳定岩层中,造成支护失效。
- 1、下载文档前请自行甄别文档内容的完整性,平台不提供额外的编辑、内容补充、找答案等附加服务。
- 2、"仅部分预览"的文档,不可在线预览部分如存在完整性等问题,可反馈申请退款(可完整预览的文档不适用该条件!)。
- 3、如文档侵犯您的权益,请联系客服反馈,我们会尽快为您处理(人工客服工作时间:9:00-18:30)。
锚杆支护煤巷冒顶事故类型及对策武星春,王恩众,宁小宁(徐州矿务集团旗山煤矿,江苏徐州221132)摘要我国煤巷锚杆支护技术近年来得到飞速发展,煤巷锚杆支护作为巷道支护的先进技术,以其显著的技术、经济优越性已逐渐成为煤矿巷道的重要支护形式。
本文对锚杆支护煤巷冒顶事故类型进行了分析,并提出了应对措施。
关键词锚杆支护煤巷冒顶类型对策中图分类号TD327.2文献标识码A近年来,我国大部分矿区基本实现了煤巷锚杆支护,但是煤巷锚杆支护的安全可靠性仍较低,尤其值得高度关注的是煤巷锚杆支护冒顶比架棚支护冒顶显现出不同的特征,多表现为突发性和结构性失稳,从而导致大范围冒顶。
1冒顶事故类型及分析1.1岩层组合结构恶化(1)非稳定岩层变厚超过锚杆(索)长度。
非稳定岩层是指对顶板岩层变形破坏起控制作用的软岩(煤)及中硬岩层。
由此原因导致的事故占总事故数的29.63%,其中直接顶板泥岩层厚变大,超过锚杆(索)长度的发生冒顶事故占总事故数的20.04%;常见的非稳定岩层有泥岩、砂质泥岩、泥质胶结的粉砂岩和煤层。
当支护不当时,极易导致顶板垮落。
例如:某矿20308运输巷于2008年3月6日发生一起长7.8m、宽3.6m、高4.5 5.0m的大规模冒顶事故,垮落带直接顶板泥岩厚度由设计时的4.4m变为6.3m,锚杆、锚索均未锚入稳定岩层中。
(2)稳定岩层变薄。
稳定岩层是指对顶板岩层稳定起控制作用的硬岩层。
例如:某矿93240切眼于2009年11月20日发生一起长60m、宽6m、高6.5m的大规模冒顶事故,从垮落现场来看,9、10号煤层间粉砂岩厚度由设计时的7 9m变为垮落时的4.06m,稳定岩层变薄,使锚索锚固段位于10号煤层中,大大降低了锚索的锚固承载作用。
事故巷道原支护参数、顶板岩层结构及冒顶特征如图1所示。
(3)顶板一定范围内出现软弱夹层。
软弱夹层层厚一般在几mm至几十mm,而普通锚杆无法将其纳入锚固范围之内,此类顶板条件极易诱发顶板垮落。
因顶板一定范围内出现软弱夹层而导致的事故占总事故数的19.75%。
如2002年04月23日,某矿34206回风巷在掘进过程中,掘进工作面直接顶板泥岩与基本顶砂岩间存在厚50mm的一层煤线,掘后7天(距掘进*收稿日期:2011-07-06作者简介:武星春(1983-),男,江苏徐州人,助理工程师,2006年毕业于阳泉职业技术学院采矿工程专业,现任旗山煤矿安监科助理工程师。
图1稳定岩层变薄导致巷道冒顶工作面29m),发生长9.4m、宽4.2m、高2.35m的大规模冒顶。
(4)地下水的影响。
水可使岩石或裂隙间的摩擦因数和变形模量下降。
地下水压力还有水楔作用,使裂隙内产生张力作用,对岩体稳定性极为不利,此类事故占总事故数的3.7%。
(5)空气中的水分对顶板的软化。
煤矿空气中水分对顶板的影响主要使泥质岩类顶板岩石逐步软化或潮解,逐渐崩解,最后形成软泥状非固结的状态。
此类事故多发生在夏季,具有“季节效应”,调查收集到此类大规模冒顶事故占总事故数的1.2%。
1.2顶板岩层出现构造(1)因对已揭露出的小断层支护不当导致的冒顶事故占总事故数的9.26%。
(2)因巷道附近一定范围内的隐含小断层直接导致的冒顶事故占总事故数的6.17%。
(3)由于地质构造运动的作用,岩层节理发育,多组节理互相切割,破坏了岩体的完整性。
在支护不当时,极易导致大规模的楔形垮落。
因节理导致的冒顶事故占总事故数的4.32%。
(4)围岩出现镶嵌型结构。
镶嵌型围岩结构多为锅底型、人字型、鱼背型、升斗型、长条型及草帽型等不规则形状.因此原因引起的冒顶事故占调查事故总数的2.5%。
1.3高应力环境(1)高应力导致的冒顶事故占总事故数的2.5%。
(2)次生应力引起的冒顶几乎总会与上部或下部邻近面(层)的二次采动有关,或与未充分垮落的盘区产生的挤压或压力过载有关。
由多煤层开采引起的次生应力或压力过载会造成底鼓、煤柱压入底板和顶板及切割顶板等各种形式的配合作用,支护不当时极易导致冒顶。
由此原因导致的冒顶事故占总事故数的3.7%。
1.4施工质量(1)未及时支护。
在巷道施工遇到构造带或巷道两帮片帮严重时,未及时采取加强支护,导致冒顶事故。
此类大规模冒顶事故占总事故数的3.1%。
(2)“三径”匹配不合理。
“三径”匹配不合理指锚索或锚杆直径、孔径、锚固剂直径“三径”匹配不合理,尤其是孔径远大于锚索直径时,锚固剂未送至孔底、多半在孔深的一半处锚固,锚索张拉时初锚力也可达到设计要求,但锚索的深锚悬吊作用已大打折扣,由此导致的冒顶事故具有很大的隐蔽性,只有冒顶后才被发现。
此类大规模冒顶事故占总事故数的1.2%。
(3)施工中“偷工减料”。
如少装树脂药卷,将设计的3支树脂药卷改为1支,造成锚固力不足;或截短锚杆,将2.2m锚杆截短为1.6m,正好该处有一弱面,引起冒顶。
此类大规模冒顶事故占总事故数的1.2%。
(4)因锚固剂本身质量问题,造成不凝固或因安装过程中搅拌时间不足或过长造成锚固能力降低,从而导致锚杆支护失效。
此类原因造成的冒顶事故收集到1起。
2基本对策(1)合理选择巷道位置。
巷道设计时应尽量避开应力集中区、地质构造带,避免因地质构造区内存在的构造应力平衡状态由于开掘过程而遭到破坏,引起构造应力释放而发生冒顶事故。
(2)选择合适的支护设计方案。
支护设计必须建立在对顶板和煤层条件有清晰认识和判断的基础之上。
支护设计完成后,必须进行支护效果的观测,支护形式必须随施工条件的变化而改变。
(3)加强施工支护质量控制。
首先确保支护材料质量达到要求,对锚杆、锚索、树脂药卷、网片等进行严格的验收,确保产品合格。
其次,严格按照安全技术操作规程对巷道及时支护,并检验支护的可靠性,使支护质量自始至终得到保证。
(4)加强对煤巷锚杆支护效果监测。
建立支护台账,健全班组自检、区队日检和矿定期抽检的监测制度,掘进工作面迎头配备扭力扳手及锚杆拉力计等监测仪器,并要求现场专人监测记录备案。
巷道设立测站,安装顶板离层仪定期监测顶板稳定情况。
通过对监测数据反馈、分析,有效地掌握锚杆的支护效果,出现顶板下沉等情况及时采取针对性加固措施。
(上接第181页)2.2.2走向爆破回风道内沿巷道顶板走向使用ZY-300型钻机进行顶板预裂爆破钻孔,第1号钻孔终孔为切眼切顶线铅垂方向上方23m,法线方向距顶板19.7m,依次由上出口向回风道外的顺序进行施工,走向间距5m,终孔间距进入老顶,垂直于直接顶10m,孔径75mm,装药方式与倾斜预裂一致,使老顶沿回风道走向形成断裂面,减小上段采空区的悬臂梁长度,减小工作面老顶垮落的面积,降低顶板冒落对工作面的冲击强度,具体参数见表3。
表3技术参数表孔深(m)钻杆数(根)方位角水平角35.849158ʎ(初投173ʎ)40ʎ2.2.3爆破参数(1)顶板卸压爆破每孔装药量为钻孔深度的一半,使用特制火药,规格为:Φ45ˑ400mm,雷管8发。
(2)走向、倾斜方向顶板预裂爆破采用裂缝法的方式(裂缝法是指人为地形成一个弱面,将能量聚集在一个方向上,当爆破时能够有效地形成一个切顶面,从而达到更好地预裂效果)。
将火药装入塑料管中,塑料管装药部位两侧用刀锯割出5mm裂缝,每5管火药用一个引药,向孔内装药时,每个孔内塑料管裂缝相对,构成爆破面(裂缝法),正向装药,塑料管尾部用黄泥封严,装至孔底,封孔使用4个水炮泥,其外用黄泥封严封实。
2.4煤层卸压爆破卸压孔位置:风道下帮,工作面硬帮,机道上帮。
上、下两道垂直于煤壁并沿煤层倾斜方向在有冲击地压危险的区域均匀布置钻孔。
工作面垂直煤壁均匀布置钻孔。
卸压孔在距离底板0.5 0.8m处开孔,孔距8 10m,眼深10m,每孔装药量为3 5kg,每5个火药用一个引药,孔内并联,空间串联,一次起爆3 5个孔,封孔时使用3个水炮泥,水炮泥以外用粘土或黄土炮泥封实封满,并对爆破孔上图标注、现场挂牌管理。
3结论兴安煤矿采用冲击矿压分级预测技术体系,即采用SOS微震系统进行区域预测、电磁辐射法进行局部预测,再采用钻屑法进行点测,对该矿冲击矿压趋势进行预测,在此基础上采取积极有效防冲措施,减少灾害事故的发生。
关于底板承压水对工作面安全回采影响程度的研究刘国利,邓新刚,于国强(枣矿集团柴里煤矿,山东滕州277519)摘要该文对工作面开采过程中底板裂隙岩层在裂隙水压力作用下的损伤演化进行定量描述,归纳煤层采动后对岩层破坏的机理,确定底板承压水对工作面回采安全的影响程度。
关键词底板承压水采动安全破坏深度影响程度中图分类号TD163+.1文献标识码B1柴里矿232、234采区概况及开采现状(1)采区概况:232、234采区地面相对位于马庙村西和西南,小丁庄南、东、西,二龙岗村北、东北。
区内地形平坦,地面标高35.64 37.94m,东北高、西南低,坡度约为1.5%。
两采区由于受南北向田岗断层和东西向程楼断层、半阁向斜的影响,使两采区内受到东西和南北向的张扭和挤压作用,故使断裂和褶曲构造较发育。
总观二采区断裂构造较发育,四采区褶曲构造较发育。
(2)开采现状:234采区23403、23405南工作面仅回采一分层,剩余工作面均已回采完毕。
232采区现回采工作面有23上205高档工作面、23下208工作面。
23上205高档工作面位于开拓新区,北为程楼断层,西为二龙岗断层,处于两断层交汇处,伴生、次生构造发育。
工作面开采期间主要受3煤顶板砂岩水、断层裂隙带导水、封闭不良钻孔导水三类水害因素影响及威胁。
23下208工作面周边23407、23409工作面老空水在掘进时通过探放水钻孔已基本疏放完毕。
23408南工作面为积水区,有稳定的补给水源,正常补给量为4m3/h,对23下208工作面的开采有一定影响。
该工作面直接充水水源为3煤顶板砂岩水,3煤顶板砂岩含水层水虽经上分层23上408及周边23407、23409工作*收稿日期:2011-05-30作者简介:刘国利(1971-),男,2009年毕业于山东科技大学采矿工程专业,工程师,现任柴里煤矿科技科科长。
面的开采受到一定的疏放,但上部3煤顶板砂岩含水层仍有部分滞水。
上述两工作面采掘活动产生的涌水经232集运或泄水孔泄入-500m轨道、运输巷,对采区涌水量有较大影响。
2232、234采区水文地质情况2.1主要含水层2.1.1侏罗系砾岩岩性由粉砂岩、砂质泥岩、中、细粒砂岩互层、砂砾岩及砾岩组成,不整合于煤系之上,属洞穴裂隙承压水,中等矿化度。
上部为粉砂岩和砂质泥岩,为相对隔水层段,中下部富水性相对增强,是工作面开采的间接充水水源之一。
侏罗系砾岩为强含水层之一,含水不均,局部溶洞发育。
该层距3煤顶板160 270m,3煤开采不受威胁。
2.1.23煤及其顶板砂岩为弱含水层,3煤属裂隙水,顶板砂岩属裂隙-孔隙水,是煤矿直接充水含水层。