航空发动机用涂层残余应力的产生及测试方法
各类涂层的检测技术介绍及对比分析

复合涂层阻抗谱检测可以分为两种,即高温干燥环境中应用的阻抗谱法 (IS) 和电解液中测量使用的电化学阻抗谱法 (EIS)。两者在复合涂层无损检测方面各 具优势,如 EIS 在测量过程中,电解液能够渗入复合涂层 的孔洞、微裂纹等缺 陷,EIS 在检测复合涂层的孔隙率、孔的尺寸和形状、甚至机械性能等方面具有 很大的优势。Sohn[8]等采用 EIS 技术测量 复合涂层 中液体电解质的阻抗变化, 确定了 复合涂层 微观结构演化与电化学阻抗响应之间的关系。Gómez-García 等[9]采用 EIS 技术将恒温氧化后 复合涂层 阻抗谱响应与其机械性能相关联, 证明该技术有能力评估 复合涂层 的微观结构的退化和机械性能的衰减。IS 在 表征 YSZ、TGO 以及两者界面处微观结构和组成成分的演变方面具有优势。 Ogawa 等首次应用 IS 技术研究了大气等离子喷涂 复合涂层 退化过程中反应层 的形成和 YSZ 陶瓷层中裂纹的检测。在此基础上,Xiao 等应用 IS 技术监测了 恒温氧化下 TGO 的演化、YSZ 面层的烧结和相变、TGO 和粘结层的界面裂纹 扩展,为预测服役期间复合涂层剩余寿命奠定了基础。
2.3 红外热成像技术(IRT)
红外热成像技术 (IRT) 是一种基于瞬态热传导的无损检测方法。样品内部 缺陷会影响热量传递,导致表面温度分布不均,IRT 技术通过红外热像仪记录表 面的热像图,识别出样品损伤,其原理如图 2-3 所示。根据红外辐射来源,红外 热成像分为两类:主动式红外热成像 (外部加载产生热激励) 和被动式红外热成 像 (试样本身的红外辐射)。主动式红外热成像根据加热方式的不同,分为脉冲 热成像、调制热成像、阶跃热成像、辐射热成像等,其中最常用的是脉冲热成像 和调制热成像。
残余应力测试方法综述

工 业 技 术65科技资讯 S CI EN CE & T EC HNO LO GY I NF OR MA TI ON 机械零部件中存在的残余应力近年来日益受到人们的关注,尤其是一些成形小的结构件中的残余应力在实际使用中会产生一些有害影响,如微机械、微机电系统中由于制备的原因,残余应力是结构件破坏的主要因素之一。
目前,比较成熟的残余应力检测和评价方法主要限于一些比较大的结构件中。
较大型的机械零部件在加工成形中由于需要较大的变形如挤压、焊接变形,从而容易形成残余应力。
例如:大型铸焊件在热处理或焊接过程中由于热影响而引起的残余变形所导致的残余应力尤为突出。
残余应力对工程构件,特别是对压力容器等焊接结构的危害是显而已见的;反之,也有采取某种特殊工艺措施,使零部件表面形成正压力(如喷丸、碾压等)以增强零部件的抗疲劳能力,提高其使用寿命。
随着断裂力学分析方法的不断发展,迫切要求定量了解或确定零部件内存在的残余应力大小。
由于产生残余应力的机理极其复杂,单纯采用理论分析以及计算方法求解,往往不能满足实际需要,同时现有的一些理论模型还不能完全反映实际情况从而达到寿命预测的目的,因此,实验仍是直接测试零部件的残余应力必不可少的工作方法。
1 残余应力的测量方法1.1物理式残余应力测试方法物理式残余应力测试方法主要有射线法、磁测法及超声法。
这种方法是无损式测量方法,其中射线法使用较多,而且比较成熟;但设备较复杂,携带到现场并在实物上测量有一定的困难,操作技术较复杂。
超声法和磁测法能够测量表面下的应力,是一种较新的测试方法。
1.2机械式残余应力测试方法机械式残余应力测试方法主要采用电阻应变测量技术,通过分段切割、套孔或钻小孔等方法,将残余应力全部或部分释放,获得零部件内的残余应力。
其中套孔法是在应变片周围切一环形槽(如图1(a)所示),将环槽中心工件部分完全孤立,释放孤立区域的残余应力(约释放90%以上),并由应变片检测出释放应变。
纳米压痕法测量航空发动机关键材料残余应力的研究进展

纳米压痕法测量航空发动机关键材料残余应力的研究进展
罗军;李楠;王曦;刘昌奎
【期刊名称】《材料导报》
【年(卷),期】2024(38)11
【摘要】随着航空发动机的需求日益增加,人们对合金性能的要求也越来越高。
在制造和加工过程中引入的残余拉应力会严重影响合金的力学性能,从而缩短发动机
的服役寿命。
因此,残余应力的测量对发动机的可靠性和安全性起着关键性作用。
本文系统归纳了纳米压痕技术的测量原理,包括接触深度、接触刚度、接触面积、
硬度以及弹性模量的计算,介绍了纳米压痕测量残余应力计算模型(如Suresh、Lee、Xu、Wang、Kim以及Peng等模型)的分析过程,对比了计算模型之间的优缺点,详细综述了纳米压痕理论在航空发动机关键材料(如不锈钢、铝合金、钛合金、镍基
高温合金)残余应力测量中的最新研究进展,总结了残余应力计算模型存在的不足,同时展望了纳米压痕法测量残余应力的发展方向。
【总页数】13页(P216-228)
【作者】罗军;李楠;王曦;刘昌奎
【作者单位】中国航发北京航空材料研究院;航空工业失效分析中心;航空材料检测
与评价北京市重点实验室;中国航空发动机集团材料检测与评价重点实验室
【正文语种】中文
【中图分类】TG133
【相关文献】
1.纳米压痕法测量残余应力的研究现状
2.应用纳米压痕法测量电沉积镍镀层残余应力的研究
3.SiC/Al2O3纳米复合材料压痕残余应力压谱法测量研究
4.纳米压痕法测量电沉积镍镀层的残余应力
5.纳米压痕法测量等离子喷涂铁基涂层表面的残余应力
因版权原因,仅展示原文概要,查看原文内容请购买。
盘件轮廓法残余应力测试【推荐】

盘件轮廓法残余应力测试【推荐】一、引言残余应力是材料在加工、热处理或使用过程中,由于内部组织不均匀或外部约束作用而产生的内应力。
残余应力对材料的使用性能和结构安全具有很大影响,因此对其进行测试和分析具有重要意义。
盘件轮廓法残余应力测试是一种常用的测试方法,具有操作简便、测试速度快、精度高等优点。
二、盘件轮廓法残余应力测试原理1. 基本原理盘件轮廓法残余应力测试是基于弹性力学原理,通过测量盘件在不同方向上的轮廓变化,计算得到残余应力的大小。
测试时,将盘件置于专用的测试装置中,通过加载和卸载,使盘件产生弹性变形。
通过测量盘件的轮廓变化,可以计算出残余应力的大小。
2. 应力分布假设在进行盘件轮廓法残余应力测试时,通常假设应力分布满足以下条件:(1)残余应力在盘件截面上呈均匀分布;(2)残余应力在盘件径向方向上不变;(3)残余应力在盘件周向上呈线性分布。
三、盘件轮廓法残余应力测试设备1. 测试装置盘件轮廓法残余应力测试装置主要包括以下部分:(1)加载装置:用于对盘件施加加载和卸载力,使盘件产生弹性变形;(2)测量装置:用于测量盘件的轮廓变化,包括线性测量仪、光学测量仪等;(3)数据采集和处理系统:用于记录和处理测试数据。
2. 辅助设备辅助设备包括:(1)盘件加热装置:用于加热盘件,使其达到测试温度;(2)冷却装置:用于冷却盘件,使其达到测试温度;(3)防护装置:用于保护测试装置和操作人员的安全。
四、盘件轮廓法残余应力测试操作步骤1. 测试前准备(1)检查测试装置是否正常工作;(2)将盘件清洗干净,去除表面污垢和氧化层;(3)对盘件进行加热或冷却,使其达到测试温度;(4)将盘件安装在测试装置上。
2. 加载和卸载(1)施加加载力,使盘件产生弹性变形;(2)记录加载过程中的应力应变数据;(3)卸载力,使盘件恢复到初始状态;(4)记录卸载过程中的应力应变数据。
3. 测量轮廓变化(1)在加载和卸载过程中,测量盘件的轮廓变化;(2)将测量结果输入数据采集和处理系统。
热喷涂过程中热障涂层残余应力分析
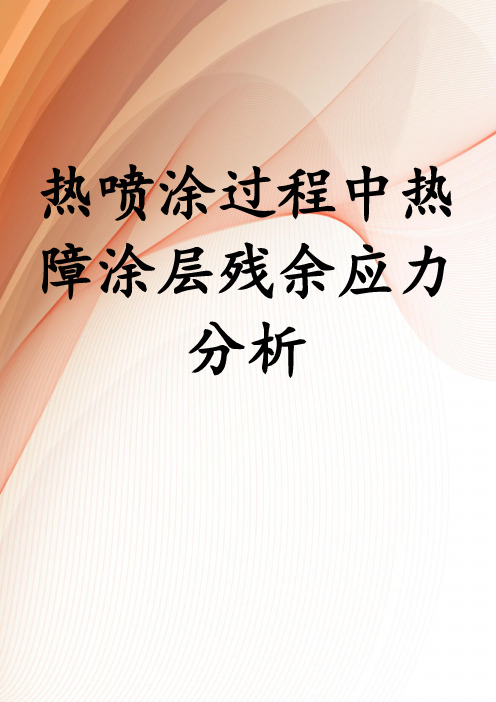
热喷涂过程中热障涂层残余应力分析热喷涂过程中热障涂层残余应力分析热喷涂是一种常用的表面涂层技术,可以提供材料的保护性能和功能增强。
然而,热喷涂过程中会产生残余应力,这可能导致涂层的破裂、剥离或变形,从而影响涂层的性能和寿命。
因此,对热喷涂过程中的残余应力进行分析和控制非常重要。
首先,热喷涂过程中的残余应力主要来源于两个方面:热应力和冷却收缩应力。
热喷涂技术通常需要在高温下进行,涂层材料在熔化和喷涂后迅速冷却,这导致涂层表面和内部产生温度梯度和热应力。
同时,冷却过程中,涂层材料由于收缩而产生冷却收缩应力。
这两种应力的叠加可能导致涂层产生各种应力状况。
其次,为了分析热喷涂过程中的残余应力,可以采用数值模拟方法。
首先,需要将热喷涂过程建模,包括涂层材料的物理特性、热传导、热辐射和流体力学等。
然后,根据实际情况设置边界条件和初始条件,并考虑喷涂参数的影响。
通过数值模拟,可以计算出涂层在热喷涂过程中的温度场和应力场。
然后,可以通过实验方法验证数值模拟结果。
可以在实际热喷涂过程中安装应变计等测量设备,实时监测涂层的应变情况。
同时,还可以采用X射线衍射等非破坏性测试方法,对涂层的晶体结构和残余应力进行测量。
通过实验数据的对比分析,可以验证数值模拟结果的准确性。
最后,根据分析结果,可以采取一些措施来控制热喷涂过程中的残余应力。
例如,可以优化喷涂参数,调整涂层的厚度和成分,以减小残余应力的产生。
此外,还可以采用后续热处理或机械加工等方法,对涂层进行应力释放或改变其应力状态,从而提高涂层的性能和寿命。
总之,热喷涂过程中的残余应力分析对于提高涂层质量和性能至关重要。
通过数值模拟和实验方法的结合,可以获得准确的应力分布信息,并采取相应的控制措施,从而实现涂层的有效保护和性能增强。
大型发电机转轴残余应力测试方法

大型发电机转轴残余应力测试方法大型汽轮发电机的转轴是发电机中*大的转动部件,运行时转速一般为3000r/min或3600r/min,对其的力学性能有较高的要求,尤其是残余应力。
残余应力过高,转轴在长期运行过程中极有可能显现翘曲变形或者尺寸上的变化,并将有可能影响到转轴本身的固有频率,这对服役长达十几年的发电机来说具有很大的风险,目前的技术条件一般要求转轴的残余应力≤60MPa。
当前,国内对汽轮发电机转子锻件的残余应力测试大多采纳切环法。
由于切环法需要在转轴上保留较大的试环区,且在测试的时候需要占用大型机床,在时间与成本上不符合现代生产管理的要求。
因此,环芯法就诞生了,其凭借取样位置小、试验时间短、效率高、成本低等优势,受到广泛应用。
环芯法测试原理在被测表面上粘贴电阻应变片,以电阻应变片为中心,加工一个直径为d的环槽。
环芯边界上的残余应力得到释放,电阻应变片就能够记录到应力释放前后的应变变化,通过胡克定律就可以计算出残余应力的大小。
环芯法残余应力测试过程采纳的仪器仪器采纳聚航科技生产的JHHX环芯法残余应力测试系统,是由JHYC静态应变仪和JHHX精密开槽装置构成,全程软件式操作,自动实时计算残余应力,并实时显示和保存应力应变数值,仪器精度高、操作简单。
前期处理在试验前,应在转轴表面选好测试部位,并对测试部位进行预处理。
预处理的重要目的是清洁表面,为粘贴应变片做好准备,并对测试位置进行定位。
首先,在转轴的表面选取测试部位,一般的原则是两个测试点之间的距离以及测试点与转轴端部的距离均大于500MM,避开测试点之间相互影响。
另外,由于转轴的外圆是圆弧面,在选定测试部位之后需要将测试部位尽量打磨平整,重要是为了去除表面的氧化层和取得一个较为平整的平面,以便于更好的粘贴应变片和校调钻头的位置。
在完成打磨之后,还需用专用的清洗剂对打磨部位进行清洗,为后续粘贴应变片做好准备。
应变片粘贴做好前期准备后,首先需用环芯钻机的机座进行定位,在测试部位布置好机座后,用专用的刀具对试验的部位进行定位和划线。
热喷涂过程中热障涂层残余应力的来源

热喷涂过程中热障涂层残余应力的来源热喷涂过程中热障涂层残余应力的来源热喷涂是一种常用于表面修复和防护的技术,通过将材料以高温喷射在基体表面上,形成一层具有优异性能的涂层。
然而,在热喷涂过程中,涂层与基体之间会产生残余应力,这些残余应力可能会对涂层的性能和寿命产生负面影响。
因此,了解热障涂层残余应力的来源是非常重要的。
首先,热喷涂过程中的热应力是主要的残余应力来源之一。
在喷涂过程中,涂层材料会被加热到非常高的温度,然后迅速冷却。
这种快速的热循环过程会导致涂层材料发生收缩和膨胀,从而产生热应力。
热应力的大小取决于喷涂材料的热膨胀系数、喷涂温度和冷却速率等因素。
一般来说,热膨胀系数较大的材料和高温喷涂会导致更大的热应力。
其次,机械应力也是热障涂层残余应力的来源之一。
在热喷涂过程中,涂层材料被快速喷射到基体表面上,与基体形成粘结。
这个过程中,喷涂材料会受到机械应力的作用,从而导致残余应力的产生。
机械应力的大小取决于喷涂材料的粘结强度、喷涂速度和喷涂厚度等因素。
一般来说,粘结强度较高、喷涂速度较快和喷涂厚度较大会导致更大的机械应力。
此外,冷却过程中的相变也会引起热障涂层的残余应力。
在热喷涂过程中,涂层材料会经历从高温到室温的冷却过程。
在这个过程中,涂层材料可能会发生相变,例如晶体的相变或者玻璃转变。
这些相变会导致涂层材料的结构产生变化,从而产生残余应力。
最后,材料本身的性质也会对热障涂层的残余应力产生影响。
不同的材料具有不同的力学性能和热性能,这些性能会影响热喷涂过程中的应力分布和残余应力的大小。
例如,硬度较高的材料通常会导致较大的残余应力。
综上所述,热喷涂过程中热障涂层残余应力的来源主要包括热应力、机械应力、相变和材料本身的性质。
了解这些来源可以帮助我们更好地理解和控制热障涂层的残余应力,从而提高涂层的性能和寿命。
残余应力基本知识
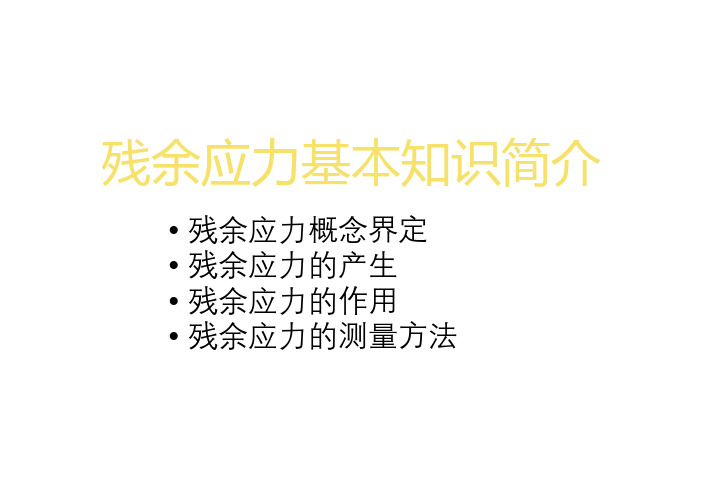
拉伸作用引起凸出效应
垂直于表面的塑性“凸出”, 按照波松比关系,必然会产生 平行于表面的塑性收缩,而表 面之下未收缩,所以,
在被切削平面产生残余拉 应力
耕犁阶段
材料塑性滑移阶段
即“塑性凸出”,表面塑性收缩阶段
表一 残余应力峰值与喷丸预应力的关系
p(Kgf/mm2) +100 +75 +50 0 -98 rp(Kgf/mm2) -91 -88 -83 -63 +5
rp 51.30.5p(Kgf/mm2) (1)
上式的线性回归相关系数为0.973。
然后,对施加不同预应力喷丸,得到不 同残余应力的的钢板弹簧进行疲劳试验, 得到了这样的S—N曲线
残余应力基本知识简介
• 残余应力概念界定 • 残余应力的产生 • 残余应力的作用 • 残余应力的测量方法
一、残余应力的基本概念
定义
• 内应力:没有外力或外力矩作用而在物体内部存在并自身保持平衡的应力。
•历史回顾 1860年 Woehler 指出火车轴的断裂有内应力作用这个因素 1925年 Masing 首次提出将内应力分为三类。 1935年 Давиденков依据各类内应力对晶体的X射线衍射
内
外
残余 应力 (MPa)
实际测试得到的分布曲线却是这样的
400
300
200
100
剥层深度 (mm)
0
10
8
6
4
2
0
-100
-200
实测曲线与理论分析所得曲线 形状相似,区别在于表层及其 以下区间多了显著的拉应力。
实际情况是:钢板弯折 并没有达到90度,焊接 时施加外力,强制焊接 成型,于是把弹性变形 固定下来。
- 1、下载文档前请自行甄别文档内容的完整性,平台不提供额外的编辑、内容补充、找答案等附加服务。
- 2、"仅部分预览"的文档,不可在线预览部分如存在完整性等问题,可反馈申请退款(可完整预览的文档不适用该条件!)。
- 3、如文档侵犯您的权益,请联系客服反馈,我们会尽快为您处理(人工客服工作时间:9:00-18:30)。
航空发动机用涂层残余应力的产生及测试方法 发布时间:2014-5-8 8:47:29 热喷涂是国内外航空发动机公司使用最广泛的一种涂层制备技术,主要被用于耐磨、抗氧化、抗腐蚀、可磨耗封严、热障、防粘接、抗微振磨损、阻燃以及零件尺寸修复涂层的生产。物理气相沉积技术则用于发动机热端涡轮工作叶片和导向叶片部件的优质高温防护涂层制备。在国内,空心阴极电弧离子镀技术被用于MCrAlY和AlSiY抗氧化涂层的制造,电子束物理气相沉积技术用于热障涂层的生产。
在制备涂层的材料熔融、沉积过程中,由于粉末颗粒本身的淬火应力、其对已沉积涂层的冲击应力以及涂层与基体材料在热-机械性能方面差异造成的失配应变和热梯度效应,某些情况下还有后续加工和服役环境的作用,都会使涂层内不可避免地出现或大或小的残余应力。已有研究表明,残余应力的大小和分布严重影响着涂层零件整个体系的主要性能,如基体疲劳寿命[1]、涂层结合强度[2]、耐剥落以及硬度、耐磨、抗热冲击、热循环疲劳等性能,导致涂层开裂[3]、翘起[4]、剥落[5-6]和分层[7-8],因此残余应力对涂层质量、使用性能、涂层构件精度和尺寸稳定性等都有重要影响,甚至导致涂层零件过早失效。
形成涂层应力的影响因素 理论认为当残余应力超过涂层弹性极限时,拉伸应力会在垂直方向导致涂层开裂;一定的压应力对于金属涂层是有利的,因其能使涂层裂纹闭合,改善疲劳性能,但压应力过大会导致涂层粘附性失效。在实际涂层生产中,残余应力的产生及其影响非常复杂。对于热喷涂涂层,其残余应力与喷涂气体流速、基体温度、涂层/基体体系的温度梯度、涂层材料性能、送粉速率、零件尺寸和几何形状、夹具、冷却、喷枪相对于零件的表面速率、走枪路径、涂层与基体厚度、弹性模量、热膨胀系数、热导率等诸多因素密切相关。
基体预处理、涂层后续加工及其服役工况对残余应力也有很大影响。例如表面粗糙化预处理可以提高界面结合强度,然而粗糙界面复杂形貌容易出现垂直于界面的残余拉应力,导致涂层破裂和剥离[9-10]。精密磨削时,砂轮磨粒钝化导致小平面磨钝,使磨粒产生垂直于涂层表面的作用力,该力和摩擦力同时对涂层表面产生挤光作用,使涂层表面形成压应力。砂轮粘结剂对残余应力也有影响[11]。
残余应力还与涂层零件的结构和喷涂区域有关。圆周喷涂的轴类零件或环形件,涂层结合强度足够大时,涂层破坏以开裂形式为主,其裂纹走向为圆周方向,也有轴向裂纹扩展的现象。小型零件内孔表面喷涂涂层,在喷涂、加工或试车考核等阶段都会出现整体涂层剥落的严重质量问题。对于薄壁件,涂层应力导致零件变形,对涂层零件尺寸精度造成影响,严重时会使零件超差报废。 机械式应力检测技术 1 曲率检测技术 曲率检测技术最初是由Hobson和Reiter提出来的[12],其优点是试验设备简单,可以直接测定涂层残余应力,其原理是在基体上生成涂层时产生的残余应力导致曲率变化,通过曲率变化可以计算残余应力大小,一般采用Stoney方程计算残余应力。Stoney方程的优点在于只使用基体弹性模量,不使用涂层弹性模量,从而解决了涂层弹性模量受各种喷涂参数的影响而比较难以准确测量的问题[13]。Gill和Clyne对曲率法做了较大改进,其一是将摄像进行曲率远程监测的方法用于真空等离子喷涂涂层的过程控制;其二是开发出数值计算程序,可以对不同曲率形状产生的残余应力进行计算,并区分喷涂粉末颗粒淬火应力和热膨胀系数差异导致的失配应力[14]。
曲率检测技术可以分为接触和非接触2种方法。接触方法主要有应变仪和轮廓测定法,非接触方法主要有光学、激光扫描、栅格和双晶衍射拓扑法。应变仪法就是用电阻应变片测量喷涂前后试样的曲率变化,通过曲率变化计算涂层残余应力分布及大小。将试样制备成窄条状,以避免产生多轴向曲率和力学不稳定性。但是如果涂层相对基体过薄就不能反映出正应力的变化梯度[3],因此该方法主要适用于比较薄基体表面涂层的情况。
曲率法测试的结果是平均应力,精度比较低(±30MPa),只能粗略测量厚度方向的平均残余应力,并且对试样形状和尺寸限制很严。如果可以对基体表面涂层进行逐层剥离测量,则可以测定整个涂层厚度范围内的残余应力详细数据,但是对于多层或者较厚的涂层则非常困难[15]。另外单纯使用传统曲率检测技术时,难以测量小曲率试样,需要对测量技术和计算方法进行改进。
2 钻孔检测技术 又称盲孔法和套孔法[16],是目前应用广泛的涂层面内残余应力测量方法[17-18]。钻孔检测的原理是将特制箔式应变花粘贴在涂层表面上,在应变花中心钻一直径和深度接近的小孔,产生局部应力释放,释放的应变可由连接各个应变片的应变仪测读出来。通过修正的Kirsch弹性力学公式则可得到在孔深范围内的平均主应力和主应力方向角[19-20],反映厚度大于0.3mm涂层的各向异性。该技术测量手段简单,成本低,测量精度高,已成为一种标准测试方法,并在工程实际中广泛采用。美国ASTM E 837《钻孔应变仪测量残余应力》标准规定了残余应力测试方法、要求及其相应的钻孔程序。
钻孔检测技术的缺点是被测涂层表面遭到钻孔破坏,且钻孔常引起材料损伤和屈服,改变局部应力状态,另外涂层去除均匀困难[15],以至于影响残余应力的测量效果[21]。 3 逐层剥离检测技术 该方法是先在方形试片上喷涂涂层,然后对在涂层抛光剥离前、数次剥离过程和剥离后的试样进行应变测量得到涂层的残余应力。美国金属学会(ASM)所属的热喷涂学会负责编制了《逐层剥离修正法评价热喷涂涂层残余应力》作为喷涂行业使用的涂层机械性能测试标准。该文件给出了试样制备、需要的设备、使用应变规的程序、逐层磨除涂层的程序以及为了计算残余应力而进行数据处理的方法。
光学式应力检测技术 1 X射线衍射检测技术 X射线衍射法“sin2ψ”是测定涂层残余应力最可靠和最实用的一种检测方法。自1971年美国汽车工程师学会颁布X射线衍射残余应力测定的行业标准SAE J784a-1971“Residential Stress Measurement by X-Ray Diffraction”和1973年日本材料学会颁布国家标准JSMS-SD-10-1973“Standard Method for X-ray Stress Measurement”以来,作为一种无损检测技术,测定残余应力的X射线衍射检测技术得到了越来越广泛的应用,技术手段也日渐成熟。为反映最新的技术进步和成熟的测定方法,欧盟标准委员会(CEN)于2008年7月批准使用新的X射线衍射残余应力测定标准EN 15305-2008“Non-destructive Testing: Test Method for Residual Stress Analysis by X-ray Diffraction”, 该标准于2009年2月底在所有欧盟成员国正式实施。与之相呼应,美国试验材料学会(ASTM)也在2010年7月发布了最新X射线衍射残余应力测定标准ASTM E915-2010“Standard Test Method for Verifying the Alignment of X-Ray Diffraction Instrumentation for Residual Stress Measurement”。EN 15305-2008欧盟标准对涂层材料和薄层等被测材料的特性进行了详细说明。
我国于1987年发布并实施《X射线应力测定方法》(GB/T 7704-1987)标准,2009年则实施《无损检测 X射线应力测定方法》(GB/T 7704-2008)新标准,但该标准没有针对涂层特殊结构材料测定残余应力的相关规定,而在国外,X射线衍射技术在20世纪80年代初就被用于喷涂涂层残余应力的检测[22]。
X射线衍射测量应力的基本原理是由于残余应力的存在引起晶格畸变,使得晶格常数发生变化,根据Bragg衍射公式确定涂层材料的晶面间距后,再通过材料的弹性特征参数按下列方程式求得残余应力[23]:
X射线衍射检测技术对涂层表面应力敏感,是一种无损的测试方法,对试样尺寸和形状要求不严格,且可以直接对零件测量,加上测量手段简单,准确度较高,因此在热喷涂涂层研制和生产中得到了广泛的应用。其独到之处是能够同时测量涂层中不同相的残余应力,如WC-Co涂层表面应力表现为压应力,且涂层中各相的残余应力水平及状态不同,WC和W2C相为压应力,W2C相残余压应力水平大于WC相;而Co6W6C相则表现为拉应力[24]。使用掠入射XRD方法还可以测量薄涂层或者厚涂层表面浅层的应力,即其检测深度可以为1μm的薄层。
XRD方法一般适用于具有良好晶体结构的材料,当晶粒尺寸很小时会导致衍射峰值变宽,影响测试结果的精度。EN 15305-2008欧盟标准对涂层材料和薄层特性的说明认为,在测试薄层时可能会遇到衍射强度低和/或晶粒数量不足、由多层材料导致的额外衍射、与基体材料的衍射峰重叠、陡的应力梯度以及强烈的织构等问题,同时涂层材料的X射线弹性常数值可能会与大块材料不同[25]。另外,由于X射线的穿透能力较低,测量深度一般约为10~50μm,因此仅能测试样品表面较薄一层的残余应力,涂层增厚会造成测试结果误差[26]。
2 中子衍射检测技术 该技术是以中子流为入射束,照射涂层表面产生衍射峰。其原理与X射线衍射基本相同,即根据衍射峰位置的变化,利用布拉格方程式计算晶格应变量并算出残余应力值。与X衍射相比,中子衍射检测技术由于中子穿透的深度较大,可测量涂层深处的残余应力,在一定程度上弥补了X射线衍射穿透能力的不足。然而由于中子射线散射强度较低,收集信息速率慢,另外可利用的中子源较少,这些不利因素成为中子衍射检测技术在涂层残余应力研究中应用的障碍[27]。
3 散斑干涉检测技术 散斑干涉记录随机分布的散斑场,定量分析散斑场的变化。要求被测量的物体表面是漫反射表面。相干光照射到漫反射表面后的反射光干涉形成散斑,记录散斑场就可得出位移的变化值[28]。Habib利用错位散斑干涉检测技术测量了温度变化造成金属与涂层之间变形的差异[29]。
4 光激发荧光谱(PLPS)技术 光激发荧光谱技术是利用Al2O3内痕量Cr3+在光激发态的d3电子衰减发出荧光,这种谱线称为光激发荧光谱。不同的Al2O3相结构,其Cr3+离子占据的空间位置不同,相应的荧光谱线也不同,d3电子衰减发出的荧光产生双峰型特征荧光谱R1和R2,在无应力状态下其频率位置分别为14402cm-1和14432cm-1。热生长α-Al2O3膜中存在应力会造成谱线频率位置的偏移,根据这些偏移值可以计算膜内应力。光激发荧光谱技术适合于对热障涂层局部的热生长氧化物(TGO)(见图1)内残余应力进行分析。该技术的优势在